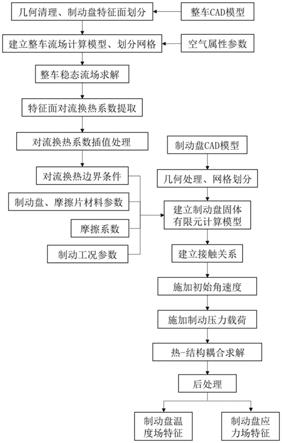
一种汽车制动盘热
‑
结构耦合分析方法
技术领域
1.本发明涉及汽车制动盘性能评估,具体涉及汽车制动盘热
‑
结构耦合分析方法。
背景技术:2.对盘式制动器而言,在汽车的制动过程中,随着动能不断转换为热量,制动盘的温度会不断升高,由此会带来一些危害。一方面,高温会降低制动盘与摩擦片之间的摩擦系数,产生制动热衰退现象。另一方面,盘面摩擦区域与其他区域的温差过大会使制动盘产生热变形,引发制动抖动、制动热疲劳等现象,影响用户体验感及行驶安全性。因此,在整车开发过程中,有必要采取措施来获取制动盘在制动过程中的温度、热应力及热变形等热性能,从而保障车辆的行驶安全及舒适。
3.通常,整车厂都会采用台架试验或整车试验的方式来测试制动盘在制动过程中的热性能。由于台架试验的工况难以和真实驾驶工况保持一致(尤其在制动盘外部流场方面),因此往往出现即使台架试验通过,但实车路试仍然出问题的情况。因此,在整车上对制动盘开展热性能试验仍然是必不可少的。整车试验虽然结果可靠,但成本较高,而且只能在整车开发后期进行,只有验证性,不具有预测性,是一种不经济、不高效的手段。相较这两种试验手段而言,采用cae的方式在整车开发前期对制动盘进行热性能仿真分析,在降低成本、提升效率、规避质量问题等方面具有明显的优势。
4.当前,采用cae仿真手段来获取制动盘热性能的主要途径为基于有限元法的热
‑
结构耦合分析。这种方法虽然计算效率高,但往往在计算精度方面难以保障,主要体现在两个方面:
①
5.不能准确考虑制动盘与外部环境的外部对流换热边界条件,致使计算得到的温度场有较大误差;
②
采用将车辆的动能转换为热量的思维来处理制动热源,与真实的摩擦现象有较大区别,使得计算得到的温度场和应力场特征与实际情况不符。
技术实现要素:6.本发明的目的是提供一种汽车制动盘热
‑
结构耦合分析方法,其能够在保证计算效率的同时提高计算精度,使得计算得到的温度场和应力场特征与实际情况相符,利于预测制动盘的热性能。
7.本发明所述的汽车制动盘热
‑
结构耦合分析方法,其包括如下步骤:
8.s1,将整车三维模型导入处理软件中,建立整车外部流场域;
9.s2,对不同车速条件下的整车进行稳态流场分析,得到制动过程中制动盘的特征面上随时间变化的对流换热系数;
10.s3,将制动盘和摩擦片的三维模型导入有限元分析软件中,根据s2得到的对流换热系数设定制动盘与外界的对流换热边界条件;
11.s4,建立多分析步,模拟制动盘的旋转运动、摩擦片在活塞缸推动下贴紧制动盘的瞬时动作以及制动减速过程,进行热
‑
结构耦合求解及结果后处理。
12.进一步,所述s3中将制动盘和摩擦片的三维模型导入有限元分析软件后,设置制动盘和摩擦片的材料属性,划分网格,设定制动盘与摩擦片之间的摩擦系数,然后设定制动盘与外界的对流换热边界条件。
13.进一步,按照gb5763
‑
2018获取不同温度条件下制动盘与摩擦片之间的摩擦系数。
14.进一步,所述s3中根据s2得到的制动盘的特征面上的对流换热系数,以传热膜系数的形式设定制动盘与外界的对流换热边界条件,设定制动盘与摩擦片的初始温度与环境温度相同。
15.进一步,所述s4中根据实际制动工况建立多分析步,具体为:
16.a.建立制动盘与摩擦片的接触关系,制动盘上的摩擦面为主面,摩擦片上的摩擦面为从面,接触类型为硬接触;
17.b.对制动盘施加初始角速度,模拟制动盘的旋转运动;
18.c.加载制动压力载荷,模拟摩擦片在活塞缸推动下贴紧制动盘的瞬时动作;
19.d.模拟车辆的制动减速过程,时间周期为制动时长;
20.e.建立分析任务,进行热
‑
结构耦合求解。
21.进一步,所述s4中的后处理包括对热
‑
结构耦合求解结果进行分析,得到制动盘温度场特征和制动盘应力场特征。
22.本发明通过联合整车稳态流场分析来获得精确的制动盘与外界的对流换热边界条件,并且对摩擦生热过程进行直接仿真,在此基础上进行热
‑
结构耦合仿真分析和结果后处理,进而在保证计算效率的同时得到了高精度的制动盘温度场特征和制动盘应力场特征,为预测汽车制动盘的热性能提供了一种精准、可靠的新方法。
附图说明
23.图1是本发明的流程示意图;
24.图2是本发明制动盘表面划分及编号示意图;
25.图3是本发明整车流场计算域示意图;
26.图4是本发明制动盘特征面上的对流换热系数随时间变化曲线图;
27.图5是本发明制动盘的有限元分析模型示意图;
28.图6是本发明制动盘与摩擦片之间的摩擦系数随温度变化情况示意图;
29.图7是本发明制动盘表面温度分布云图;
30.图8是本发明制动盘表面节点位置示意图;
31.图9是本发明制动盘表面节点的温升曲线示意图;
32.图10是本发明制动盘表面应力分布云图。
具体实施方式
33.下面结合附图对本发明作详细说明。
34.参见图1,所示的汽车制动盘热
‑
结构耦合分析方法,其包括如下步骤:
35.s1,将整车三维cad模型导入处理软件中,该处理软件为star
‑
ccm+,在完成几何清理后,根据几何特征对制动盘表面进行划分并编号,参见图2,fi为内侧端面,f2为外侧端面,f3为通风孔内侧端面,f4为通风孔外侧端面,f5为通风孔柱面,f6为外缘面,f7为中心柱
面,f8为鹅颈内表面,f9为鹅颈外表面。
36.建立整车外部流场域,参见图3,l为车长,w为车宽,h为车高,x、y、z分别为车长、车宽、车高方向,由于在实际情况下,有气流经发动机舱流向制动盘,会影响制动盘的冷却效果。因此为了提高仿真精度,应考虑发动机舱内部的流场,体现在以多孔介质的方法来处理散热器、冷凝器及中冷器,以mrf的方法来处理风扇。进行网格划分,需要说明的是,对边界层和制动盘周边流场的网格进行加密处理。对整车外部流场赋予空气属性,设置流场入口为速度边界条件,出口为压力边界条件,采用mrf即多重参考系的方法来处理制动盘及车轮的旋转。
37.s2,设置湍流参数和求解参数,分别在0km/h、10km/h、20km/h、40km/h、60km/h、80km/h、100km/h七个的车速条件下来进行稳态流场求解。对不同车速条件下的整车稳态流场计算结果进行处理,提取制动盘各特征面的对流换热系数。插值处理后,参见图4,得到整个制动过程中,制动盘各特征面上随时间变化的对流换热系数。
38.s3,将制动盘和摩擦片的三维cad模型导入abaqus有限元分析软件中,设置制动盘和摩擦片的材料属性。参见图5,划分网格,网格类型为c3d8rt。设定制动盘与摩擦片之间的摩擦系数,为了提高仿真精度,参见图6,按照gb5763
‑
2018获取不同温度条件下制动盘与摩擦片之间的摩擦系数。然后根据s2得到的制动盘的特征面上的对流换热系数,以传热膜系数的形式设定制动盘与外界的对流换热边界条件,设定制动盘与摩擦片的初始温度与环境温度相同。
39.s4,根据实际制动工况建立多分析步,具体为:
40.a.建立初始分析步,即建立制动盘与摩擦片的接触关系,制动盘上的摩擦面为主面,摩擦片上的摩擦面为从面,接触类型为硬接触。
41.b.建立分析步1,类型为static general,对制动盘施加初始角速度,模拟制动盘的旋转运动。
42.c.建立分析步2,类型为static general,加载制动压力载荷,模拟摩擦片在活塞缸推动下贴紧制动盘的瞬时动作。
43.制动压力由公式计算得到,其中,n为夹钳活塞缸数量,p
f
为活塞缸内部制动液的压力,d
p
为活塞缸内径,a为摩擦片与制动盘的摩擦面积。
44.d.建立分析步3,模拟车辆的制动减速过程,分析步类型为coupled temp
‑
displacement,时间周期为制动时长;
45.e.建立分析任务,进行热
‑
结构耦合求解。
46.后处理具体是对热
‑
结构耦合求解结果进行分析,得到整个制动过程中制动盘温度场特征和制动盘应力场特征。参见图7,得到整个制动过程中制动盘表面的温度分布特征,参见图8和图9,在划分网格时得到节点1至节点8,对热
‑
结构耦合求解结果进行分析得到制动盘上各个节点的温升情况,参见图10得到制动盘在制动过程中的应力场分布特征以及制动盘变形情况。进而能够根据制动盘温度场特征和制动盘应力场特征对汽车制动盘的热性能进行准确预测,相较于传统的热
‑
结构耦合分析方法,本发明通过联合整车稳态流场分析来获得精确的制动盘与外界的对流换热边界条件,并且对摩擦生热过程进行直接仿
真,在此基础上进行热
‑
结构耦合仿真分析和结果后处理,进而在保证计算效率的同时得到了高精度的制动盘温度场特征和制动盘应力场特征,为预测汽车制动盘的热性能提供了一种精准、可靠的新方法。
47.以上所述仅为本发明的较佳实施例而已,并不用以限制本发明,凡在本发明的精神和原则之内所作的任何修改、等同替换和改进等,均应包含在本发明的保护范围之内。