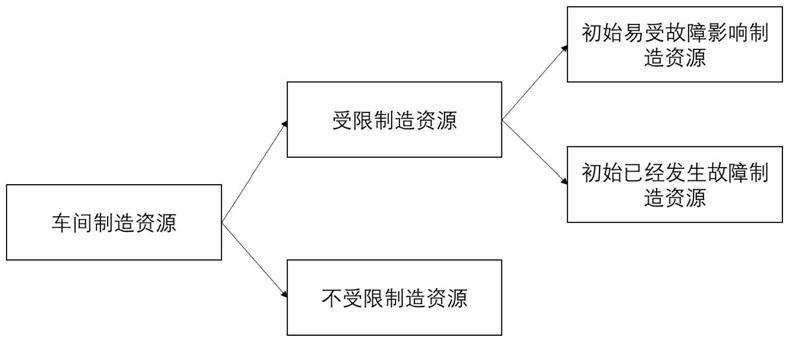
一种面向可逆恢复故障的车间关键制造资源sis识别方法
技术领域
1.本发明涉及生产过程控制技术领域,特别涉及一种面向可逆恢复故障的车间关键制造资源sis识别方法。
背景技术:2.面对来自市场的竞争压力,为了满足不同顾客的需要,越来越多的企业把精力放在了对生产系统以及生产过程的改善和优化中。然而生产系统的高效可控需要与生产活动有关的人员、机器、物料和工件等制造资源,经过有机组合、相互配合才能实现。对生产系统进行科学系统的分析、量化的评价评估,对于增强离散制造车间的稳定性,提高工件的准时完工率,进而提升企业经济效益等方面具有积极的作用。
3.生产系统分析的前提是对离散制造车间的生产环节的充分认识和准确建模,通过设立关键的指标,可以将车间一段生产周期内生产计划的风险点和关键节点识别出来,并为后续有针对性的改善提供准确的数据支持。
技术实现要素:4.针对上述问题,本发明的目的在于提供一种面向可逆恢复故障的车间关键制造资源sis识别方法,首先,通过信息技术和数据库技术,将一段生产周期内所生产的工件,与其生产计划、生产工艺、涉及的制造资源进行自动关联,其次,根据传染病研究理论中的sis模型,假定离散车间制造资源中的初始已发生故障制造资源和未发生故障制造资源,再次,通过sis模型求解初始发生故障制造资源造成其他制造资源发生瓶颈的数量随时间的变化,进而,通过瓶颈资源数量的峰值和达到峰值的时间长短的加权结果来标记初始已经发生故障制造资源的重要度,接着,更改车间制造资源中初始发生故障制造资源和未发生故障制造资源的分组情况,并重新计算重要度,依次不断重复,直到得到所有可能分组情况的重要度,最后,根据所有得到的重要度的大小顺序,得到离散车间制造系统中的关键制造资源节点。
5.为达到上述目的,本发明采用的技术方案是:
6.一种面向可逆恢复故障的车间关键制造资源sis识别方法,包括以下步骤:
7.步骤一、基于物联网rfid技术和关系型sql数据库,将一段生产周期内所生产的工件,与其生产计划、生产工艺、涉及的制造资源进行自动关联,根据传染病研究理论中的sis模型,假定在整个车间的生产周期内制造资源的总数量保持不变,记为u,离散车间制造资源中的初始已发生故障制造资源和未发生故障制造资源,分别记为:x(t0)和y(t0):
8.用关系代数表示x(t0)和y(t0)为:
9.x(t0)={x1(t0),x2(t0),x3(t0),
…
,x
j
(t0)}
10.y(t0)={y1(t0),y2(t0),y3(t0),
…
,y
k
(t0)}
11.其中:
12.x
j
(t0)为开始时刻第j个初始已发生故障制造资源;
13.y
k
(t0)为开始时刻第k个初始未发生故障制造资源;
14.步骤二、基于物联网rfid技术和关系型sql数据库,将制造车间中一定生产周期内的工件、生产计划、生产工艺,和对应的制造资源进行自动关联,关联关系自动转化成车间生产制造系统网络中的连接边,边的权重为工序的加工时间,车间生产过程中机床设备、刀具、夹具、量具和人员所有制造资源最终映射为制造系统网络中节点;
15.步骤三、按照步骤一的分组结果,设定已发生故障制造资源导致未发生故障制造资源最终发生故障的概率、已发生故障制造资源对未发生故障制造资源的单位时间内有效作用数、已发生故障制造资源再次发生故障数量占总发生故障制造资源总数的比率,分别为:β、γ、λ;
16.步骤四、具有连接关系的制造资源之间的故障传播率为连接两者之间边的权重与整个网络中最大权重的比值,β
ij
计算为:
[0017][0018]
其中,δ为两个制造资源的接触概率,当两者之间有连接边时,接触概率为1,没有连接边时,接触概率为0;
[0019]
步骤五、通过sis模型求解初始已发生故障制造资源造成未发生故障制造资源发生瓶颈的数量随时间的变化:
[0020][0021]
其中,i(t)为发生易故障制造资源发生瓶颈数量随时间变化的数量。
[0022]
步骤六、通过将瓶颈资源数量的峰值和达到峰值的时间长短的加权结果用来标记初始已经发生故障制造资源的重要度:
[0023][0024]
其中,zyd(i)为第i组初始发生故障制造资源的重要度,
[0025]
t(i)为第i组发生制造资源瓶颈数量达到峰值的时间;
[0026]
为第i组发生制造资源瓶颈数量达到峰值;
[0027]
k1,k2为达峰时间和峰值的权重;
[0028]
步骤七、更改车间制造资源中初始发生故障制造资源和未发生故障制造资源的分组情况,并按照步骤一到六重新计算重要度,依次不断重复,直到得到所有可能分组情况的重要度;
[0029]
步骤八、根据所有得到的重要度的大小顺序,得到离散车间制造系统中的关键制造资源节点。
[0030]
本发明的有益效果是:
[0031]
1)可以对离散制造车间中在可逆恢复制造资源故障环境下,确定出关键制造资源。
[0032]
2)可以对关键制造资源的重要度通过瓶颈资源数量的达峰时间和峰值的加权进
行量化描述。
[0033]
3)可以准确描述制造资源之间连接关系对可逆恢复故障传播的影响。
[0034]
4)可以通过故障传播速度的排序,梳理出制造车间中生产管理中需要关注的其他关键制造资源,并提前做好预案,提高生产组织的柔性。
附图说明
[0035]
图1是生产车间制造资源的分类。
[0036]
图2是车间制造资源网络构建框架。
[0037]
图3是不同制造资源接触概率的取值。
[0038]
图4是关键制造资源节点识别流程图。
具体实施方式
[0039]
一种面向可逆恢复故障的车间关键制造资源sis识别方法,包括以下步骤:
[0040]
步骤一、参照图1,基于物联网rfid技术和关系型sql数据库,将一段生产周期内所生产的工件,与其生产计划、生产工艺、涉及的制造资源进行自动关联,根据传染病研究理论中的sis模型,假定在整个车间的生产周期内制造资源的总数量保持不变,记为u,离散车间制造资源中的初始已发生故障制造资源和未发生故障制造资源,分别记为:x(t0)和y(t0)。
[0041]
用关系代数表示x(t0)和y(t0)为:
[0042]
x(t0)={x1(t0),x2(t0),x3(t0),
…
,x
j
(t0)}
[0043]
y(t0)={y1(t0),y2(t0),y3(t0),
…
,y
k
(t0)}
[0044]
其中:
[0045]
x
j
(t0)为开始时刻第j个初始已发生故障制造资源;
[0046]
y
k
(t0)为开始时刻第k个初始未发生故障制造资源;
[0047]
步骤二、参照图2,基于物联网rfid技术和关系型sql数据库,将制造车间中一定生产周期内的工件、生产计划、生产工艺,和对应的制造资源进行自动关联,关联关系自动转化成车间生产制造系统网络中的连接边,边的权重为工序的加工时间,车间生产过程中机床设备、刀具、夹具、量具和人员等所有制造资源最终映射为制造系统网络中节点;
[0048]
步骤三、按照步骤一的分组结果,设定已发生故障制造资源导致未发生故障制造资源最终发生故障的概率、已发生故障制造资源对未发生故障制造资源的单位时间内有效作用数、已发生故障制造资源再次发生故障数量占总发生故障制造资源总数的比率,分别为:β、γ、λ;
[0049]
步骤四、参照图3,具有连接关系的制造资源之间的故障传播率为连接两者之间边的权重与整个网络中最大权重的比值,β
ij
计算为:
[0050][0051]
其中,δ为两个制造资源的接触概率,当两者之间有连接边时,接触概率为1,没有连接边时,接触概率为0;
[0052]
步骤五、通过sis模型求解初始已发生故障制造资源造成未发生故障制造资源发生瓶颈的数量随时间的变化:
[0053][0054]
其中,i(t)为发生易故障制造资源发生瓶颈数量随时间变化的数量。
[0055]
步骤六、通过将瓶颈资源数量的峰值和达到峰值的时间长短的加权结果用来标记初始已经发生故障制造资源的重要度。
[0056][0057]
其中,zyd(i)为第i组初始发生故障制造资源的重要度,
[0058]
t(i)为第i组发生制造资源瓶颈数量达到峰值的时间;
[0059]
为第i组发生制造资源瓶颈数量达到峰值;
[0060]
k1,k2为达峰时间和峰值的权重;
[0061]
步骤七、参照图4,更改车间制造资源中初始发生故障制造资源和未发生故障制造资源的分组情况,并按照步骤一到六重新计算重要度,依次不断重复,直到得到所有可能分组情况的重要度;
[0062]
步骤八、根据所有得到的重要度的大小顺序,得到离散车间制造系统中的关键制造资源节点。