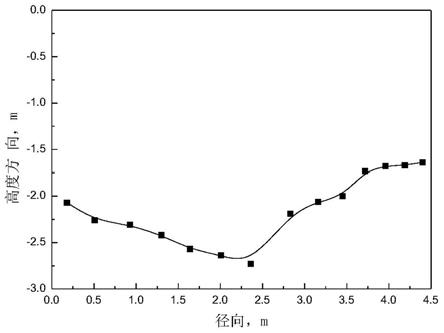
1.本发明涉及高炉炼铁技术领域,具体涉及一种高炉上部炉料径向下降速度分布的确定方法。
背景技术:2.高炉是公认的“黑匣子”和最复杂反应器之一,冶炼过程复杂,内部的状态难以直接监测,对其内部状态的判断一直是高炉冶炼工艺研究的重点和难点,高炉的运行仍然需要依靠经验进行操作,通过科学的方法和量化的检测数据对高炉冶炼过程状态进行分析和计算对于指导高炉生产操作十分重要。
3.高炉要实现稳定顺行,需要根据高炉的运行状态的变化及时对高炉进行调整,高炉操作的主要内容是高炉的上、下部调剂,下部调剂主要是指调节高炉送风制度和出铁制度,上部调剂主要是指调节高炉布料制度。高炉上部炉料料速是高炉控制布料制度的重要参考依据,高炉上部炉料周向下降速度均匀和径向下降速度分布合理是稳定运行的基础。
4.目前高炉操作人员判断上部炉料下降速度一般是通过高炉布料制度和炉顶安装的探尺测得料线位置估算,例如公开号为“cn111274523a”的专利“高炉料速的计算方法和计算系统”就是根据高炉探尺检测数据和布料过程中的信号计算料速。这种方法数据可靠准确,但是由于高炉一般炉顶只在靠近炉墙处周向均匀安装2个或3个探尺,也就是这种方法只能得到料面边缘位置处的2个或3个位置的下料速度,可以根据下料量估算平均下料速度,也可以大致判断高炉周向料速的均匀性,但无法计算高炉径向料速分布。
5.有的高炉技术人员根据布料制度和炉顶红外测温成像系统估算炉顶料面形状和料速,认为温度越低的区域料层越厚,这是方法有一定的道理,但误差太大,不够准确。要计算高炉径向上部炉料下降速度分布可以首先通过测距,得到高炉料面形状,再采取一定的方法由料面形状计算炉料下降速度。目前正要研究和应用的测量高炉料面的手段有激光检测、扫描雷达检测和可见光检测,由于高炉料面上方粉尘较多,而且高炉料面面积大,测距不需要很大的精度,所以扫描雷达检测更具有优势。但扫描雷达检测一次得到是料面的测距信号,可以由此得到料面形状,并不能直接得到炉料下降速度。根据扫描雷达检测的料面形状计算炉料下降速度还需要一定的方法,例如2017年北京科大大学关心的博士论文中根据料面形状和数学算法模拟和预测下料速度,该方法是基于数据统计计算,存在一定的假设,预测的准确性和可靠性不好把控。
6.因此,有必要提供一种准确可靠的方法,计算高炉上部炉料下径向降速度分布,为高炉上部调剂提供帮助。
技术实现要素:7.本发明的目的在于克服现有技术的不足,提供了一种高炉上部炉料径向下降速度分布的确定方法,该方法是在高炉炉顶安装扫描雷达,根据探尺信号和料罐下料阀信号控制雷达进行连续两次监测高炉料面,并进行料面数据筛选,得到料面基准点坐标,再由基准
点坐标计算得到炉料沿径向的下降速度分布,用于指导高炉布料操作。
8.为实现上述目的,本发明所设计一种高炉上部炉料径向下降速度分布的确定方法,包括以下步骤:
9.步骤一:在高炉炉顶上安装扫描雷达,并将扫描雷达的上位机(上位机为高炉控制室安装的计算机)与高炉现场plc系统连接,每次雷达扫描结束后,得到监测信号(信号超过1万个),监测信号输到上位机中,上位机软件系统对上述信号进行识别;
10.步骤二:布完一次料后,雷达对高炉料面进行扫描;
11.步骤三:计算布料后的高炉料面的形状;
12.步骤四:下一次布料前雷达再次对高炉料面进行扫描,
13.步骤五:并计算下一次布料前的高炉料面的形状;
14.步骤六:计算炉料沿径向下降速度分布;
15.进一步地,所述步骤一中,雷达安装高度与高炉炉顶探尺安装孔的高度相同(可以实现沿高炉径向线扫描)。
16.再进一步地,所述步骤二中,雷达对料面进行扫描具体步骤如下:
17.步骤2.1将雷达上位机连接现场plc系统中的高炉两个料罐的下料闸信号,每1秒读取两个下料闸信号一次(解决每次布料完成后炉顶会产生大量粉尘,此时监测雷达受粉尘影响监测结果误差较大的缺陷),
18.步骤2.2当有两个信号由一个开和一个关变为两个关时,开始计时料罐中料已空,开始计时,计时至15秒时,上位机软件系统控制雷达进行扫描,其中,雷达扫描范围覆盖从高炉中心线到炉墙。
19.再进一步地,所述步骤三中,计算布料后的料面形状具体步骤如下:
20.步骤3.1雷达扫描结束,上位机软件系统对雷达信号进行识别,以零料线与高炉中心线的交点为坐标原点,从高炉中心线向炉墙水平方向为横坐标,以高炉中心线从下向上为纵坐标,计算出所有信号对应的坐标点,
21.步骤3.2按照雷达扫描等角度从高炉中心线到炉墙水平方向划分为n个区域(考虑到精确和计算方便,10≤n≤20),其中,10≤n≤20;
22.步骤3.3根据信号分布特点,计算出每个区域信号集中位置中心坐标作为该区域基准点坐标;连接各区域的基准点坐标,得到了计算布料后的料面形状。
23.再进一步地,所述步骤3.3中,计算出每个区域信号集中位置中心坐标具体计算方法为:
24.首先计算该区域所有信号的中心坐标,计算所有信号坐标与该中心坐标的距离,选出距离小的一半信号,再计算这一半信号的中心坐标,即该区域基准点坐标。
25.再进一步地,所述步骤四中,上次布料后雷达扫描料面之后,同时满足以下两个条件则控制雷达对下一次布料前的高炉料面进行扫描:
26.步骤4.1与上次布料后雷达扫描完开始计时,计时超过30秒,且不超过300秒;
27.步骤4.2上位机连接每秒实时现场的plc系统监测到高炉机械探尺信号变为代表提尺的信号。
28.再进一步地,所述步骤五中,计算下一次布料前的高炉料面形状具体步骤:
29.步骤5.1首先按步骤三方法计算得到下一次布料前的初始各区域基准点坐标,
30.步骤5.2再利用差值方法计算得到与步骤三中基准点横坐标对应的点作为下一次布料前的各区域基准点,连接各区域的基准点坐标,得到了下一次布料前的料面形状。
31.再进一步地,所述步骤六中,计算炉料沿径向下降速度分布具体步骤如下:
32.步骤6.1将步骤五中下一次布料前的各区域基准点与步骤三中布料后各区域的基准点纵坐标相减后除以两次扫描记录的时间差,得到炉料沿径向下降速度分布的基准点(由于步骤三和步骤五得到各基准点横坐标一致);
33.步骤6.2再根据步骤6.1得到基准点坐标,采用最小二乘法拟合得到炉料沿径向下降速度分布。
34.结合每个高炉的实际情况,根据计算得到的高炉炉料沿径向下降速度分布情况,从而在后续工作中,帮助工作人员判断布料情况和调整布料方案:
35.收集过去半年内上部炉料沿径向的平均下降速度分布,与当前下降速度分布对比,分析高炉中心与边缘炉料下降是否过快或过慢,综合考虑高炉设备状态、煤气利用率等情况,判断布料情况和调整布料方法:
36.当煤气利用率较低且高炉设备状态较好,相比于半年内上部炉料沿径向的平均下降速度分布,连续出现高炉上部炉料沿径向中心下降过快时,说明中心气流过强,可以通过适当减少中心焦炭量或减少边缘矿石量调整布料。
37.或,当高炉冷却设备状态不好,相比于半年内上部炉料沿径向的平均下降速度分布,连续出现高炉上部炉料沿径向边缘下降过快时,说明边缘气流强,为减少炉料对高炉炉墙的磨损和气流对高炉炉墙的冲刷,保护高炉冷却设备,可以通过适当增加中心焦炭量或增加边缘矿石量调整布料。
38.本发明的有益效果:
39.本发明提供的方法计算和判断及时准确,有利于及时调整高炉布料,减少高炉炉况波动,提高高炉操作水平和节约生产成本。
附图说明
40.图1为某3000m3级高炉布完一次焦炭后雷达扫描得到的料面。
41.图2为图1对应的布料后下一次布料前雷达扫描得到的料面。
42.图3为由图1的料面和图2的料面计算得到的径向下降速度分布。
43.图4为过去半年内上部炉料沿径向的平均下降速度分布。
具体实施方式
44.下面结合具体实施例对本发明作进一步的详细描述,以便本领域技术人员理解。
45.利用高炉上部炉料径向下降速度分布的确定方法确定某3000m3级高炉(该高炉炉顶安装了料面扫描雷达)上部径向炉料下降速度分布,步骤如下:
46.步骤1:布完一次料后雷达进行扫描料面。高炉焦炭布完后,两个料罐的下料闸信号,由一个开和一个关变为两个关时开始计时,计时达到15秒时,上位机系统控制控制扫描雷达进行扫描。
47.步骤2:计算此次焦炭布料后的各区域基准点坐标。雷达扫描结束时,记录时间为2020年11月27日15点52分18秒。上位机软件系统对雷达信号进行识别,以零料线与高炉中
心线的交点为坐标原点,从高炉中心线向炉墙水平方向为横坐标,以高炉中心线从下向上为纵坐标,计算出所有信号对应的坐标点,按照雷达扫描等角度从高炉中心线到炉墙水平方向划分为14个区域,计算出每个区域信号集中位置中心坐标作为该区域基准点坐标,具体计算方法为首先计算该区域所有信号的中心坐标,计算所有信号坐标与该中心坐标的距离,选出距离小的一半信号,再计算这一半信号的中心坐标,即该区域基准点坐标,各区域基准点坐标见表1。根据表1中各域基准点坐标数据,横坐标为x轴,纵坐标为y轴,进行多项式拟合得到高炉料面形状如图1所示。
48.表1此次焦炭布料后的各区域基准点坐标,m
49.横坐标4.44.193.963.723.453.162.832.362.011.641.30.930.510.18纵坐标
‑
1.64
‑
1.67
‑
1.68
‑
1.73
‑2‑
2.06
‑
2.19
‑
2.73
‑
2.64
‑
2.57
‑
2.42
‑
2.31
‑
2.26
‑
2.07
50.步骤3:下一次布料前雷达进行扫描料面。上次布料后雷达扫描料面之后,同时满足以下两个条件则控制雷达开始扫描料面,(1)与上次布料后雷达扫描完开始计时,计时超过30秒,(2)上位机连接每秒实时现场的plc系统监测到高炉机械探尺信号变为代表提尺的信号。雷达扫描结束时,记录时间为2020年11月27日15点53分 14秒。
51.步骤4:计算下一次布料前的各区域基准点坐标。与步骤2方法相同,得到下一次布料前的初始各区域基准点坐标,再利用差值方法计算得到与步骤2中基准点横坐标对应的点作为下一次布料前的各区域基准点,见表2。根据表2数据,进行多项式拟合得到下一次布料前的料面形状,如图2所示。
52.表2下一次布料前的各区域基准点坐标,m
53.横坐标4.44.193.963.723.453.162.832.362.011.641.30.930.510.18纵坐标
‑
1.79
‑
1.88
‑
1.84
‑
1.89
‑
2.17
‑
2.26
‑
2.28
‑
2.56
‑
2.8
‑
2.67
‑
2.59
‑
2.46
‑
2.37
‑
2.17
54.步骤5:根据表1此次焦炭布料后的各区域基准点坐标和表2下一次布料前的各区域基准点坐标,纵坐标相减后除以两次扫描记录的时间差56秒,得到炉料沿径向下降速度分布的基准点,见表3。
55.表3炉料沿径向下降速度分布的基准点
[0056][0057]
对这些基准点坐标进行多项式拟合得到炉料沿径向下降速度分布图,如图3所示。
[0058]
步骤6:通过统计过去半年内正常高炉炉况下上部炉料沿径向的下降速度数据,计算平均值,得到过去半年内上部炉料沿径向的平均下降速度分布,如图4所示,与当前下降速度分布对比,发现当前高炉上部炉料下降速度稍快,这是因为高炉本身运行时出铁并不是一直连续的,而且正常风量也有变化,所以出现短时间内下降速度稍快或稍慢都是正常现象,前高炉上部炉料没有出现中心或边缘下降过快或过慢的情况。可以判断当前布料制度合理,应当保持当前布料批重和布料矩阵。
[0059]
其它未详细说明的部分均为现有技术。尽管上述实施例对本发明做出了详尽的描述,但它仅仅是本发明一部分实施例,而不是全部实施例,人们还可以根据本实施例在不经创造性前提下获得其他实施例,这些实施例都属于本发明保护范围。