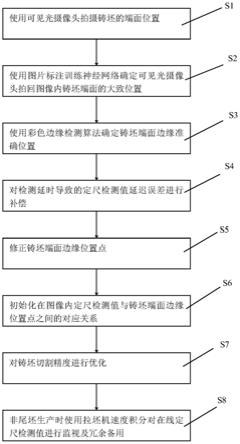
1.本发明涉及炼钢领域,具体地涉及一种连铸坯智能切割定尺方法。
背景技术:2.炼钢厂冶炼的钢水经连铸机连续浇铸为钢坯,钢坯根据下工序的需要切割为一定长度的铸坯,即在连铸钢坯生产线上,往往需要对连铸机生产出的连续坯流按成品钢坯长度要求进行在线定尺检测和切割。前者是通过连铸机后拉坯机速度积分计算或成像识别技术获得坯流端面位置相对于火焰切割机起始切割点的在线长度作为钢坯在线检测长度。后者是当钢坯在线检测长度到达要求的成品钢坯长度附近时,启动火焰切割机对坯流进行夹紧及同步切割,以使钢坯长度获得要求的成品钢坯长度。铸坯切割定尺能否达到标准要求(即定尺合格率)关系到连铸机能否向下一道工序提供合格产品。铸坯定尺长于标准定尺,则浪费坯料,短则成为废品,因此,铸坯定尺合格率成为合格连铸坯的一项重要指标。而钢坯在线检测长度即钢坯在线定尺值的精度是影响切割出的成品钢坯长度是否达到要求精度的一个关键因素。
3.通过连铸机后拉坯机速度积分计算钢坯在线定尺值的缺点在于,一是当拉坯机与坯流之间有滑动时,钢坯定尺值精度会较低,二是在生产尾坯时,由于坯流已经与拉坯机脱离接触,将无法通过拉坯机速度积分计算出钢坯定尺值,即拉尾坯时,拉矫机与铸坯不接触,此时由操作人员通过操作台对尾坯进行手动处理。手动定尺切割铸坯存在着五个方面的问题:一是定尺合格率低,最高仅为7o%;二是燃气长期燃放浪费严重;三是切割后运坯辊道切损严重,更换频繁;四是一、二组运坯辊道电机因辊道积渣太多,过载烧损严重;五是切割工人劳动强度大,劳动生产率低。
4.通过红外成像识别技术获得坯流端面位置相对于火焰切割机起始切割点的在线长度作为钢坯在线检测长度是传统常用的钢坯在线定尺值检测方法。该方法虽然在生产尾坯时也可以得到钢坯定尺值,但仅适用于连铸坯表面温度足够高的工况,对于由于连铸坯断面规格大或火焰切割机离连铸机较远导致连铸坯表面低温的工况,这种传统的红外定尺方法将无法继续使用。
5.针对由于连铸坯断面规格大或火焰切割机离连铸机较远导致连铸坯表面低温,从而无法使用传统红外定尺方法对钢坯进行在线定尺,而如果只使用拉坯机速度积分计算钢坯在线定尺值时钢坯在线定尺值精度会较低且无法在生产尾坯时使用该方法计算钢坯在线定尺值的工况。
技术实现要素:6.本发明旨在提供一种连铸坯智能切割定尺方法,以解决上述问题。为此,本发明采用的具体技术方案如下:
7.一种连铸坯智能切割定尺方法,其可包括以下步骤:
8.s1.使用可见光摄像头拍摄铸坯的端面位置;
9.s2.使用图片标注训练神经网络确定可见光摄像头拍回图像内铸坯端面的大致位置;
10.s3.使用彩色边缘检测方法确定铸坯端面边缘准确位置;
11.s4.对检测延时导致的定尺检测值延迟误差进行补偿;
12.s5.修正铸坯端面边缘位置点;
13.s6.初始化在图像内定尺检测值与铸坯端面边缘位置点之间的对应关系;
14.s7.对铸坯切割精度进行优化;
15.s8.非尾坯生产时使用拉坯机速度积分对在线定尺检测值进行监视及冗余备用。
16.进一步地,s2的具体过程为:
17.s21.使用图片标注工具标注可见光摄像头拍回图片内铸坯端面大致位置;
18.s22.使用标注图片训练可识别铸坯端面大致位置的神经网络;
19.s23.使用训练后的神经网络识别出铸坯端面大致位置。
20.进一步地,图片标注工具为labelimg,以及神经网络为yolo。
21.进一步地,s3的具体过程为:
22.s31.在可见光摄像机拍摄回的每个彩色rgb图像内,沿着铸坯端面运行的轨迹设置一条直线,直线方向与铸坯运行方向一致;
23.s32.沿着该直线设置两个相邻的矩形框,使左矩形框右边线的中点与右矩形框左边线的中点重合,通过保持重合中点在该直线上并从直线起点沿着铸坯运行方向移动重合中点来移动这两个矩形框并计算这两个矩形框内各自所有像素点的r、g、b平均值;
24.s33.假设两个矩形框内各自所有像素点的r、g、b平均值分别为r11、g11、b11、r12、g12、b12,再通过归一化公式计算这两个相邻矩形框的相似度xsd1=1
‑
(|r11
‑
r12|+|g11
‑
g12|+|b11
‑
b12|)/(255*3),当相似度xsd1首次低于设置的阀值fz1时,即认为这两个相邻矩形框公共边与直线的交点为检测到的铸坯端面边缘位置点。
25.进一步地,s4的具体过程为:在可见光摄像机拍摄回的每个彩色rgb图像内,计算铸坯端面边缘位置点移动速度v,设置定尺检测值检测延迟时间dt1,得到检测延时导致的定尺检测值延迟误差e1=v*dt1。
26.进一步地,s5的具体过程为:记录末次图像处理完成的时刻ts,记录末次图像处理并对检测延时导致的定尺检测值延迟误差进行补偿后得到的定尺检测值vs,设当前时刻为ta,则当前时刻图像处理修正后的铸坯端面边缘位置点xb=vs+(ta
‑
ts)*v,式中v为铸坯端面边缘位置点移动速度。
27.进一步地,s6的具体过程为:初始化期间,先令图像内定尺检测值yb=通过拉坯机速度积分计算得到的在线定尺检测值p,再记录下铸坯端面在不同位置时的图像内定尺检测值yb与铸坯端面边缘位置点xb,作为它们之间初始化时的对应关系。
28.进一步地,s7的具体过程为:
29.s71.对于每种长度尺寸的铸坯定尺值,设置好铸坯切割长度目标值ps,在铸坯定尺检测值达到切割长度目标值ps附近时发出切割命令来切割出铸坯;
30.s72.实际量出切割出铸坯的实际长度a,得出该种长度尺寸的铸坯定尺值切割精度优化误差=a
‑
t;
31.s73.将该种长度尺寸的铸坯定尺值切割精度优化误差=a
‑
t输入定尺系统作为该
种长度尺寸的铸坯定尺值切割精度优化误差叠加到在线定尺检测值上得到该种长度尺寸的新的在线定尺检测值;
32.s74.在新的在线定尺检测值达到切割长度目标值ps附近时发出切割命令来切割出铸坯。
33.进一步地,s8的具体过程为:在非尾坯生产时,实时比较通过拉坯机速度积分计算得到的在线定尺检测值pf与通过图像分析得到的在线定尺检测值ybs之间的差异,当差异小于等于预设阀值时,自动选择在线定尺检测值ybs作为在线定尺检测值,当差异大于预设阀值时,产生告警信息,并按预设选择选择在线定尺检测值pf或在线定尺检测值ybs作为在线定尺检测值。
34.本发明采用上述技术方案,具有的有益效果是:本发明可以有效克服传统红外定尺方法无法应用于连铸坯表面低温工况的缺陷、传统通过拉坯机速度积分计算钢坯在线定尺值方法无法应用于连铸坯尾坯生产工况的缺陷、以及传统通过拉坯机速度积分计算钢坯在线定尺值方法精度较低的缺陷,此外通过本方法,可以轻松实现对连铸坯切割精度的优化,即通过使用更高像素可见光摄像头拍摄连铸坯端面位置将可获得更高的连铸坯切割精度,同时使用可见光摄像头拍摄连铸坯端面位置,较传统红外切割定尺方法使用红外摄像头拍摄连铸坯端面位置,具有设备成本更低的优势。
附图说明
35.为进一步说明各实施例,本发明提供有附图。这些附图为本发明揭露内容的一部分,其主要用以说明实施例,并可配合说明书的相关描述来解释实施例的运作原理。配合参考这些内容,本领域普通技术人员应能理解其他可能的实施方式以及本发明的优点。图中的组件并未按比例绘制,而类似的组件符号通常用来表示类似的组件。
36.图1是本发明的一种连铸坯智能切割定尺方法的流程图;
37.图2是本发明的基于可见光摄像头的智能切割定尺系统的架构图;
38.图3是使用图片标注工具标注可见光摄像头拍回图片内铸坯端面大致位置的示意图;
39.图4是使用训练后的神经网络识别出铸坯端面大致位置的示意图;
40.图5是确定铸坯端面边缘准确位置的示意图;
41.图6是定尺系统发出切割信号前的状态截图;
42.图7是定尺系统发出切割信号时的状态截图。
具体实施方式
43.现结合附图和具体实施方式对本发明进一步说明。
44.如图1和2所示,一种连铸坯智能切割定尺方法可包括以下步骤:
45.s1.使用可见光摄像头拍摄铸坯端面位置。图2示出了基于可见光摄像头的智切割定尺系统架构,其目的在于通过使用可见光摄像头对连铸坯端面位置进行精确定位检测以实现对连铸坯的精确定尺切割。该系统可以根据连铸机的流数可选用1或多个可见光摄像头。操作室安装1台工控机作为铸坯定尺切割主机。可见光摄像头通过电口到光口转换器将摄像头网口转换到光口,再通过光纤连接到操作室的光口到电口转换器,再通过以太网线
连接到定尺切割主机网口。定尺系统主机网口连接到外部连铸机控制系统交换机用于发送定尺检测值及火焰切割机切割命令给外部连铸机控制系统。定尺系统主机配显示器、键鼠用于显示及操作。可见光摄像头与定尺切割系统主机间通过tcp/ip协议通讯。定尺切割系统主机与外部连铸机控制系统通过tcp/ip协议通讯。
46.s2.使用图片标注训练神经网络确定可见光摄像头拍回图像内铸坯端面的大致位置。具体地,先使用图片标注工具(例如labelimg)标注可见光摄像头拍回图片内铸坯端面大致位置,如图3所示;再使用标注图片训练可识别铸坯端面大致位置的神经网络(例如yolo);然后使用训练后的神经网络识别出铸坯端面大致位置,如图4所示。
47.s3.使用彩色边缘检方法确定铸坯端面边缘准确位置。具体地,在可见光摄像机拍摄回的每个彩色rgb图像内,沿着铸坯端面运行的轨迹设置一条直线1(即图5中的白色直线),直线1方向与铸坯运行方向一致,沿着该直线1设置两个相邻的矩形框2r和2l(即图5中两个白色小矩形框),使左矩形框2l的右边线的中点与右矩形框2r的左边线的中点重合,通过保持重合中点在直线1上并从直线1的起点沿着铸坯运行方向(图5中铸坯运行方向为从左向右)移动重合中点来移动这两个矩形框2r和2l。图5中左边大矩形框3l是通过步骤s2获得的铸坯端面大致位置,将该矩形框3l沿铸坯运行方向移动该矩形框3l的半宽距离得到图5中右边大矩形框3r。图5中右边大矩形框3r的左边线与直线1的交点将作为图5中两个小矩形框2r和2l的重合中点的移动起点,图5中右边大矩形框3r的右边线与直线1的交点将作为图5中两个小矩形框2r和2l的重合中点的移动终点,通过在直线1上从重合中点的移动起点开始移动重合中点,至多到重合中点移动到移动终点为止,移动这两个小矩形框2r和2l的重合中点并计算这两个小矩形框2r和2l内各自所有像素点的r、g、b平均值。假设两个小矩形框2r和2l内各自所有像素点的r、g、b平均值分别为r11、g11、b11、r12、g12、b12,通过归一化公式计算这两个相邻小矩形框2r和2l的相似度xsd1=1
‑
(|r11
‑
r12|+|g11
‑
g12|+|b11
‑
b12|)/(255*3),当相似度xsd1首次低于设置的阀值fz1时,即认为这两个相邻小矩形框2r和2l的公共边与直线1的交点(即重合中点)为检测到的铸坯端面边缘位置点。
48.s4.对检测延时导致的定尺检测值延迟误差进行补偿。具体地,设对可见光摄像头拍摄图像分析得到的铸坯端面边缘位置点为xa,在可见光摄像机拍摄回的每个彩色rgb图像内,根据铸坯端面边缘位置点xa定时计算出铸坯端面边缘位置点xa的移动速度va,对va进行过滤及限幅处理得v,即当va小于下限阀值val时,令v=0,当va大于上限阀值vau时,令v=vau,其他情况令v=va。设定尺检测值检测延迟时间为dt1,得到检测延时导致的定尺检测值延迟误差e1=v*dt1,设对检测延时导致的定尺检测值延迟误差进行补偿后得到的铸坯端面边缘位置点为vs,则vs=xa+e1。
49.s5.修正铸坯端面边缘位置点。具体地,记录末次图像处理完成得到铸坯端面边缘位置点vs时的时刻值ts,设当前时刻值为ta,则当前时刻图像处理修正后的铸坯端面边缘位置点xb=vs+(ta
‑
ts)*v,式中v为步骤s4计算所得的铸坯端面边缘位置点xa的移动速度。通过在两次图像处理之间附加对铸坯端面边缘位置点xa的移动速度积分来插值,可以提高当前时刻定尺检测值的精度。
50.s6.初始化在图像内定尺检测值yb与铸坯端面边缘位置点xb之间对应关系。具体地,初始化期间,先令图像内定尺检测值yb=通过拉坯机速度积分计算得到的在线定尺检测值p,其中,通过拉坯机速度积分计算得到的在线定尺检测值p的确定方法为:在每次火焰
切割机开始切割命令的上升沿,p归零,之后通过拉坯机速度积分计算得到在线定尺检测值p。再记录下铸坯端面在不同位置时的图像内定尺检测值yb与铸坯端面边缘位置点xb,作为它们之间初始化时的对应关系。
51.s7.对铸坯切割精度进行优化。具体地,该优化步骤采用两种方法,第一种是通过使用拉坯机速度积分计算得到的在线定尺检测值p进行铸坯切割时无废料损失的铸坯切割精度优化方法:对于每种长度尺寸的铸坯定尺值,设置好铸坯切割长度目标值ps,根据步骤s6所得的在线定尺检测值p在p达到铸坯切割长度目标值ps附近时发出切割命令来切割出铸坯;实际量出切割出铸坯的实际长度a;得出该种长度尺寸的铸坯定尺值切割精度优化误差dyb1=a
‑
ps;将dyb1输入定尺系统作为该种长度尺寸的铸坯定尺值切割精度优化误差叠加到在线定尺检测值p上得到该种长度尺寸通过拉坯机速度积分计算得到的在线定尺检测值pf,即pf=p+dyb1;之后在pf达到铸坯切割长度目标值ps附近时发出切割命令来切割出铸坯。铸坯定尺切割精度优化前铸坯定尺切割按照步骤s6得到的在线定尺检测值p进行切割,铸坯切割精度较低但不会产生废料,在对在线定尺检测值p叠加切割精度优化误差dyb1后,铸坯定尺切割按照pf=p+dyb1进行切割,铸坯切割精度得到提高的同时亦不会产生废料。
52.第二种是通过使用图像内定尺检测值yb进行铸坯切割时无废料损失的铸坯切割精度优化方法:对于每种长度尺寸的铸坯定尺值,设置好铸坯切割长度目标值ps,根据步骤s7所得铸坯定尺检测值yb与xb之间的初始化对应关系按在线xb插值计算出在线的yb并在yb达到铸坯切割长度目标值ps附近时发出切割命令来切割出铸坯;实际量出切割出铸坯的实际长度a;得出该种长度尺寸的铸坯定尺值切割精度优化误差dyb2=a
‑
ps;将dyb2输入定尺系统作为该种长度尺寸的铸坯定尺值切割精度优化误差叠加到步骤s7得到的在线定尺检测值yb上得到该种长度尺寸图像分析检测到的在线定尺检测值ybs,即ybs=yb+dyb2;之后在ybs达到铸坯切割长度目标值ps附近时发出切割命令来切割出铸坯。按步骤s6所述的yb与xb之间的初始化对应关系,保证了在叠加铸坯切割精度优化误差dyb2前,铸坯定尺切割按照ybs=yb=通过拉坯机速度积分计算得到的在线定尺检测值p进行切割,铸坯切割精度较低但不会产生废料,在叠加铸坯切割精度优化误差dyb2后,铸坯定尺切割按照ybs=yb+dyb2进行切割,铸坯切割精度得到提高的同时亦不会产生废料。
53.s8.非尾坯生产时使用拉坯机速度积分对在线定尺检测值进行监视及冗余备用。具体地,在非尾坯生产时,实时比较通过拉坯机速度积分计算得到的在线定尺检测值pf与通过图像分析得到的在线定尺检测值ybs之间的差异,当差异小于等于预设阀值时,自动选择在线定尺检测值ybs作为在线定尺检测值,当差异大于预设阀值时,产生告警信息,并按预设选择选择备用的在线定尺检测值pf或在线定尺检测值ybs作为在线定尺检测值。通过这种方式,可提高铸坯切割定尺系统在线定尺检测值冗余度及可靠性。
54.实例
55.实车切割验证:武钢csp条材厂一炼钢分厂3号连铸机存在连铸坯断面规格大导致连铸坯表面低温无法使用传统红外定尺方法的问题,通过使用本发明提出的连铸坯智能切割定尺方法对该连铸机的连铸坯的在线实车切割进行实验证明。图6和图7是在线实车切割实验过程截图。在图6和图7中,设定的目标切割长度为ps,定尺系统发出的切割信号为dq,定尺系统检测的铸坯长度为ybs。从图7看到,当铸坯目标切割设定长度ps=5560.0毫米,系
统检测铸坯长度ybs=5557.1毫米,定尺系统开始发出切割信号dq=1。铸坯切割后手动测量确认铸坯实际长度a=5565.0毫米,实际切割精度=a
‑
ps=5.0毫米。由此可见,本发明的方法有效克服了由于连铸坯断面规格大或火焰切割机离连铸机较远导致连铸坯表面低温无法使用传统红外定尺方法的工况,定尺切割精度达到预期精度2厘米,具有良好的铸坯长度检测能力、铸坯精确定尺切割能力以及连铸在线应用能力。此外,通过使用不同分辨率的可见光摄像头及本文提出的连铸坯智能切割定尺方法,可以轻松实现对连铸坯切割精度的优化,例如武钢实车切割实验使用有效分辨率为1600像素可见光摄像头拍摄连铸坯端面位置达到连铸坯切割精度2厘米,通过使用更高像素可见光摄像头拍摄连铸坯端面位置将可达到更高连铸坯切割精度;同时使用可见光摄像头拍摄连铸坯端面位置,较传统方法使用红外摄像头拍摄连铸坯端面位置,具有设备成本上的优势。
56.尽管结合优选实施方案具体展示和介绍了本发明,但所属领域的技术人员应该明白,在不脱离所附权利要求书所限定的本发明的精神和范围内,在形式上和细节上可以对本发明做出各种变化,均为本发明的保护范围。