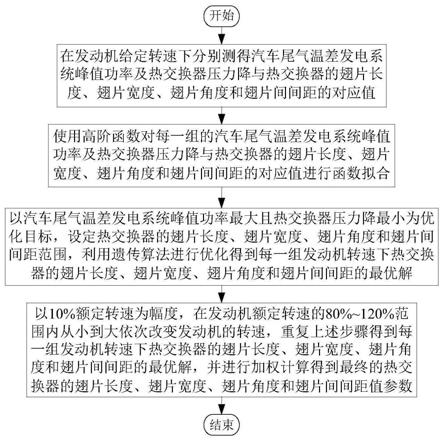
1.本发明属于汽车发电系统技术领域,具体涉及一种汽车尾气温差发电系统的车载兼容性优化方法。
背景技术:2.传统汽车内燃机的效率却普遍低下,大约30%~40%的燃油能量以尾气的形式排入大气,造成了极大的能源浪费与环境污染。温差发电技术由于其具有模块小、无运动部件、寿命长等优点,可以有效回收汽车尾气废热进行发电并用于车载系统,从而提高传统发动机的燃料利用率,降低其污染。然而,在构建汽车尾气温差发电系统时,为了尽可能回收和储存尾气废热进行发电,需要再热交换器内部设计不同流场结构的翅片,由于翅片会造成发动机的背压变化从而影响发动机的排气气流,特别是明显增大的背压会急剧恶化发动机的原有动力性、燃油经济和排放性能,这种一方面热交换器回收尾气废热实现了发电但另一方面发动机影响会降低的此消彼长现象造成了汽车尾气温差发电系统的车载兼容性差,制约了汽车尾气温差发电系统的节能与减排功效。因此,如何优化设计热交换内部翅片和流场结构,在提高热交换器表面温度、汽车尾气温差发电系统的发电功率同时降低发动机的进出口压力损失是十分必要的,也是汽车尾气温差发电技术追求的终极目标。
技术实现要素:3.根据背景技术存在的问题,本发明提供一种汽车尾气温差发电系统的车载兼容性优化方法,获得发动机特定工作条件下热交换器的最优尺寸参数,提高汽车尾气温差发电系统的车载兼容性。
4.为解决上述技术问题,本发明采用如下技术方案:
5.本发明系统的技术方案为汽车尾气温差发电系统,包括:测功机操作台、测功机、发动机、n个热电模块、热交换器、入口压力计、出口压力计、n个冷却水箱、可调电子负载;
6.所述测功机操作台与所述测功机通过导线相连;所述测功机通过机械方式与所述发动机的输出轴相连;所述发动机的排气管与所述热交换器的尾气入口相连;所述热交换器的尾气入口与所述入口压力计相连;所述热交换器的尾气出口与所述出口压力计相连;
7.所述热交换器内腔为圆筒形结构,外部为正多边形表面,每个表面上对应的热电模块d的热端与所述热交换器外表面相贴连,所述热交换器表面的数量为n;
8.所述热电模块由多个热电器件依次串联级联构成;
9.所述热电器件的冷端通过机械方式压紧固定于所述冷却水箱,多个冷却水箱通过水路进行串联,可与外部冷却系统构成环路进而给热电器件进行冷端冷却,从而构建温差实现发电;
10.所述多个热电模块依次串联连接;所述多个热电模块串联后构成总输出端与可调电子负载相连;
11.所述测功机操作台通过人工操作方式在所述测功机操作台的控制界面设置发动
机的目标转速,通过测功机操作台导线发送给测功机内部控制器控制命令,调节所述测功机的运行状况最终实现发动机的给定转速反馈控制;
12.所述热交换器为外表面为正多边形,内腔为圆筒式结构,其外部全长为500mm~600mm、壁厚为3mm~5mm、内径为55mm~70mm、有效换热段总长度为400mm~500mm。
13.本发明方法的技术方案为车载兼容性优化方法,其特征在于,包括以下步骤:
14.步骤1:选取热交换器的翅片长度、翅片宽度、翅片角度和翅片间间距为自变量,以汽车尾气温差发电系统峰值功率及热交换器压力降作为因变量,通过调节可调电子负载和测功机,在发动机给定转速下测得汽车尾气温差发电系统峰值功率及热交换器压力降与热交换器的翅片长度、翅片宽度、翅片角和翅片间间距的对应值;
15.步骤1所述热交换器的翅片长度定义为:l,l为自变量;
16.步骤1所述翅片宽度定义为:w,w为自变量;
17.步骤1所述翅片角度定义为:a,a为自变量;
18.步骤1所述翅片间间距定义为:s,s为自变量;
19.步骤1所述汽车尾气温差发电系统峰值功率定义为:p
max
,p
max
为因变量;
20.步骤1所述热交换器压力降定义为:p
drop
,p
drop
为因变量;
21.步骤1所述在发动机给定转速下测得热交换器压力降,具体为:
22.通过人工读取所入口压力计和所述出口压力计值进行差值计算得到该条件下的热交换器压力差;
23.步骤1所述在发动机给定转速下测得汽车尾气温差发电系统峰值功率,具体为:
24.通过人工方式从小到大控制所述可调电子负载的给定电流进而任意设置多个热电器件的输出电流值,通过人工方式读取记录所述可调电子负载的显示屏信息测试多个热电器件在每一种输出电流情况下的输出电压和输出功率,从而得到不同输出电流条件下多个热电器件的功率、电压、电流数据集,其中一组功率最大的值作为该发动机转速条件下多个热电器件的峰值功率;
25.步骤2:使用高阶函数分别对步骤1中每一组发动机转速测取的汽车尾气温差发电系统峰值功率与热交换器的翅片长度、翅片宽度、翅片角度、翅片间间距的对应值进行曲线拟合,以构建汽车尾气温差发电系统峰值功率与热交换器的翅片长度、翅片宽度、翅片角度、翅片间间距之间的函数关系模型,使用高阶函数分别对步骤1中每一组发动机转速测取的热交换器压力降与热交换器的翅片长度、翅片宽度、翅片角度、翅片间间距的对应值进行曲线拟合,以构建热交换器压力降与热交换器的翅片长度、翅片宽度、翅片角度、翅片间间距之间的函数关系模型;
26.步骤2所述汽车尾气温差发电系统峰值功率与热交换器的翅片长度、翅片宽度、翅片角度、翅片间间距之间的函数关系模型为:
27.p
max
=(a0+a1l+a2l2+
…
+amlm)+(b0+b1w+b2w2+
…
+bnwn)+(c0+c1a+c2a2+
…
+c
jaj
)+(d0+d1s+d2s2+
…
+dksk)
28.步骤2所述热交换器压力降与热交换器的翅片长度、翅片宽度、翅片角度、翅片间间距之间的函数关系模型为:
29.p
drop
=(a0+a1l+a2l2+
…
+amlm)+(b0+b1w+b2w2+
…
+bnwn)+(c0+c1a+c2a2+
…
+c
jaj
)+(d0+d1s+d2s2+
…
+dksk)
30.其中,ai为峰值功率函数关系模型的翅片长度的i次项系数,ai为压力降函数关系模型的翅片长度的i次项系数,i=0,1,2,
…
,m,b
x
为峰值功率函数关系模型的翅片宽度的x次项系数,b
x
为压力降函数关系模型的翅片宽度的x次项系数,x=0,1,2,
…
,n,cy为峰值功率函数关系模型的翅片角度的y次项系数,cy为压力降函数关系模型的翅片角度的y次项系数,y=0,1,2,
…
,j,dz为峰值功率函数关系模型的的翅片间间距的z次项系数,dz为压力降函数关系模型的的翅片间间距的z次项系数,z=0,1,2,
…
,k;
31.步骤3:以汽车尾气温差发电系统峰值功率最大化且热交换器压力降最小化为优化目标,设定热交换器的翅片长度的取值范围、翅片宽度的取值范围、翅片角度的取值范围、翅片间间距的取值范围,通过二进制编码,设定种群个体数、交叉概率、变异概率和最大迭代数值,利用遗传算法进行优化得到最优化的翅片长度、最优化的翅片宽度、最优化的翅片角度、最优化的翅片间间距;
32.作为优选,步骤3所述汽车尾气温差发电系统峰值功率最大化且热交换器压力降化最小为优化目标为:
33.f=min(p
drop
/p
max
)
34.其中,p
max
为汽车尾气温差发电系统峰值功率,p
drop
为热交换器压力降;
35.步骤3所述热交换器的翅片长度的取值范围为:[l
min
,l
max
];
[0036]
其中,l
min
为热交换器的翅片长度的最小值,l
max
为交换器的翅片长度的最大值;
[0037]
步骤3所述翅片宽度的取值范围为:[w
min
,w
max
];
[0038]
其中,w
min
为翅片宽度的最小值,w
max
为翅片宽度的最大值;
[0039]
步骤3所述翅片角度的取值范围为:[a
min
,a
max
];
[0040]
其中,a
min
为翅片角度的最小值,a
max
为翅片角度的最大值;
[0041]
步骤3所述翅片间间距的取值范围为:[s
min
,s
max
];
[0042]
其中,s
min
为翅片间间距的最小值,s
max
为翅片间间距的最大值;
[0043]
步骤3所述最优化的翅片长度为:l*;
[0044]
步骤3所述最优化的翅片宽度为:w*;
[0045]
步骤3所述最优化的翅片角度为:a*;
[0046]
步骤3所述最优化的翅片间间距为:s*;
[0047]
步骤4:通过测功机操作台界面在发动机额定转速的80%~120%范围内分别以80%发动机额定转速、90%发动机额定转速、100%发动机额定转速、110%发动机额定转速和120%发动机额定转速设定发动机的目标转速,通过导线给测功机内部的控制器发送控制命令调节测功机的运行,进而拖动发动机实现其目标转速的反馈控制,重复上述步骤2、3,得到每组发动机转速条件下最优化的翅片长度、每组发动机转速条件下最优化的翅片宽度、每组发动机转速条件下最优化的翅片角度、每组发动机转速条件下最优化的翅片间间距值,进一步分别进行加权计算作为热交换器的最优尺寸;
[0048]
步骤4所述每组发动机转速条件下最优化的翅片长度为:
[0049]
l
opt
=al1*+bl2*+(1-a-b-c-d)l3*+cl4*+dl5*
[0050]
步骤4所述每组发动机转速条件下最优化的翅片宽度为:
[0051]wopt
=aw1*+bw2*+(1-a-b-c-d)w3*+cw4*+dw4*
[0052]
步骤4所述每组发动机转速条件下最优化的翅片角度为:
[0053]aopt
=aa1*+ba2*+(1-a-b-c-d)a3*+ca4*+da4*
[0054]
步骤4所述每组发动机转速条件下最优化的翅片间间距值为:
[0055]sopt
=as1*+bs2*+(1-a-b-c-d)s3*+cs4*+ds4*
[0056]
式中,l
opt
为最终的翅片长度优化值,w
opt
为最终的翅片宽度优化值,a
opt
为最终的翅片角度优化值,s
opt
为最终的翅片间间距优化值,l
x
*表示第x组发动机转速条件下最优化的翅片长度,w
x
*表示第x组发动机转速条件下最优化的翅片宽度,a
x
*表示第x组发动机转速条件下最优化的的翅片角度,s
x
*表示第x组发动机转速条件下最优化的翅片间间距值,a为在0和1之前取值的第1组发动机转速条件下加权系数,b为在0和1之前取值的第2组发动机转速条件下加权系数,c为在0和1之前取值的第4组发动机转速条件下加权系数,d为在0和1之前取值的第5组发动机转速条件下加权系数,且a+b+c+d≤1,x=1,2,3,4,5;其中,x=1表示发动机转速为80%发动机额定转速,x=2表示发动机转速为90%发动机额定转速,x=3表示发动机转速为100%发动机额定转速,x=4表示发动机转速为110%发动机额定转速,x=5表示发动机转速为120%发动机额定转速。
[0057]
本发明充分考虑了不同发动机转速下汽车尾气温差发电系统车载兼容性评价参数与热交换器翅片长度、翅片宽度、翅片角度和翅片间间距值之间的耦合关系,利用先进优化算法得到各组发动机转速下热交换器翅片长度、翅片宽度、翅片角度和翅片间间距优化值,最后将各组优化值进行加权计算得到最终的热交换器优化参数进行加工制造,从而在提高热交换器表面温度和汽车尾气温差发电系统的发电功率同时降低发动机的进出口压力损失。
附图说明
[0058]
图1:为汽车尾气温差发电系统车载兼容性优化设计流程示意图。
[0059]
图2:为汽车尾气温差发电系统结构示意图。
[0060]
图3:为热交换器优化变量及尺寸示意图。
具体实施方式
[0061]
下面结合图1至图3介绍本发明的具体实施方式,本发明具体实施方式包括第一实施例以及第二实施例。
[0062]
本发明系统的技术方案为汽车尾气温差发电系统,包括:测功机操作台、测功机、发动机、n个热电模块、热交换器、入口压力计、出口压力计、n个冷却水箱、可调电子负载;
[0063]
所述测功机操作台与所述测功机通过导线相连;所述测功机通过机械方式与所述发动机的输出轴相连;所述发动机的排气管与所述热交换器的尾气入口相连;所述热交换器的尾气入口与所述入口压力计相连;所述热交换器的尾气出口与所述出口压力计相连;
[0064]
所述热交换器内腔为圆筒形结构,外部为正多边形表面,每个表面上对应的热电模块d的热端与所述热交换器外表面相贴连,所述热交换器表面的数量为n;
[0065]
所述热电模块由多个热电器件依次串联级联构成;
[0066]
所述热电器件的冷端通过机械方式压紧固定于所述冷却水箱,多个冷却水箱通过水路进行串联,可与外部冷却系统构成环路进而给热电器件进行冷端冷却,从而构建温差实现发电;
[0067]
所述多个热电模块依次串联连接;所述多个热电模块串联后构成总输出端与可调电子负载相连;
[0068]
所述测功机操作台通过人工操作方式在所述测功机操作台的控制界面设置发动机的目标转速,通过测功机操作台导线发送给测功机内部控制器控制命令,调节所述测功机的运行状况最终实现发动机的给定转速反馈控制;
[0069]
所述测功机操作台选型为dw160;
[0070]
所述测功机选型为dw160电涡流测功机;
[0071]
所述发动机选型为psa rfn10lh3x;
[0072]
所述n个热电模块选型为bi2te3低温型;
[0073]
所述热交换器选型为5mm厚黄铜;
[0074]
所述入口压力计选型为305idp;
[0075]
所述出口压力计选型为305idp;
[0076]
所述n个冷却水箱选型为3.0mm厚铝合金;
[0077]
所述可调电子负载选型为l280600;
[0078]
本发明方法的技术方案为车载兼容性优化方法,包括以下步骤:
[0079]
步骤1:选取热交换器的翅片长度、翅片宽度、翅片角度和翅片间间距为自变量,以汽车尾气温差发电系统峰值功率及热交换器压力降作为因变量,通过调节可调电子负载和测功机,在发动机给定转速下测得汽车尾气温差发电系统峰值功率及热交换器压力降与热交换器的翅片长度、翅片宽度、翅片角和翅片间间距的对应值;
[0080]
步骤1所述热交换器的翅片长度定义为:l,l为自变量;
[0081]
步骤1所述翅片宽度定义为:w,w为自变量;
[0082]
步骤1所述翅片角度定义为:a,a为自变量;
[0083]
步骤1所述翅片间间距定义为:s,s为自变量;
[0084]
步骤1所述汽车尾气温差发电系统峰值功率定义为:p
max
,p
max
为因变量;
[0085]
步骤1所述热交换器压力降定义为:p
drop
,p
drop
为因变量;
[0086]
步骤1所述在发动机给定转速下测得热交换器压力降,具体为:
[0087]
通过人工读取所入口压力计和所述出口压力计值进行差值计算得到该条件下的热交换器压力差;
[0088]
步骤1所述在发动机给定转速下测得汽车尾气温差发电系统峰值功率,具体为:
[0089]
通过人工方式从小到大控制所述可调电子负载的给定电流进而任意设置多个热电器件的输出电流值,通过人工方式读取记录所述可调电子负载的显示屏信息测试多个热电器件在每一种输出电流情况下的输出电压和输出功率,从而得到不同输出电流条件下多个热电器件的功率、电压、电流数据集,其中一组功率最大的值作为该发动机转速条件下多个热电器件的峰值功率;
[0090]
步骤2:使用高阶函数分别对步骤1中每一组发动机转速测取的汽车尾气温差发电系统峰值功率与热交换器的翅片长度、翅片宽度、翅片角度、翅片间间距的对应值进行曲线拟合,以构建汽车尾气温差发电系统峰值功率与热交换器的翅片长度、翅片宽度、翅片角度、翅片间间距之间的函数关系模型,使用高阶函数分别对步骤1中每一组发动机转速测取的热交换器压力降与热交换器的翅片长度、翅片宽度、翅片角度、翅片间间距的对应值进行
曲线拟合,以构建热交换器压力降与热交换器的翅片长度、翅片宽度、翅片角度、翅片间间距之间的函数关系模型;
[0091]
步骤2所述汽车尾气温差发电系统峰值功率与热交换器的翅片长度、翅片宽度、翅片角度、翅片间间距之间的函数关系模型为:
[0092]
p
max
=(a0+a1l+a2l2+
…
+amlm)+(b0+b1w+b2w2+
…
+bnwn)+(c0+c1a+c2a2+
…
+c
jaj
)+(d0+d1s+d2s2+
…
+dksk)
[0093]
步骤2所述热交换器压力降与热交换器的翅片长度、翅片宽度、翅片角度、翅片间间距之间的函数关系模型为:
[0094]
p
drop
=(a0+a1l+a2l2+
…
+amlm)+(b0+b1w+b2w2+
…
+bnwn)+(c0+c1a+c2a2+
…
+c
jaj
)+(d0+d1s+d2s2+
…
+dksk)
[0095]
其中,ai为峰值功率函数关系模型的翅片长度的i次项系数,ai为压力降函数关系模型的翅片长度的i次项系数,i=0,1,2,
…
,m,b
x
为峰值功率函数关系模型的翅片宽度的x次项系数,b
x
为压力降函数关系模型的翅片宽度的x次项系数,x=0,1,2,
…
,n,cy为峰值功率函数关系模型的翅片角度的y次项系数,cy为压力降函数关系模型的翅片角度的y次项系数,y=0,1,2,
…
,j,dz为峰值功率函数关系模型的的翅片间间距的z次项系数,dz为压力降函数关系模型的的翅片间间距的z次项系数,z=0,1,2,
…
,k;m=4,n=5,j=6,k=7。
[0096]
步骤3:以汽车尾气温差发电系统峰值功率最大化且热交换器压力降最小化为优化目标,设定热交换器的翅片长度的取值范围、翅片宽度的取值范围、翅片角度的取值范围、翅片间间距的取值范围,通过二进制编码,设定种群个体数、交叉概率、变异概率和最大迭代数值,利用遗传算法进行优化得到最优化的翅片长度、最优化的翅片宽度、最优化的翅片角度、最优化的翅片间间距;
[0097]
步骤3所述汽车尾气温差发电系统峰值功率最大化且热交换器压力降化最小为优化目标为:
[0098]
f=min(p
drop
/p
max
)
[0099]
其中,p
max
为汽车尾气温差发电系统峰值功率,p
drop
为热交换器压力降;
[0100]
步骤3所述热交换器的翅片长度的取值范围为:[l
min
,l
max
];
[0101]
其中,l
min
为热交换器的翅片长度的最小值,l
max
为交换器的翅片长度的最大值;
[0102]
步骤3所述翅片宽度的取值范围为:[w
min
,w
max
];
[0103]
其中,w
min
为翅片宽度的最小值,w
max
为翅片宽度的最大值;
[0104]
步骤3所述翅片角度的取值范围为:[a
min
,a
max
];
[0105]
其中,a
min
为翅片角度的最小值,a
max
为翅片角度的最大值;
[0106]
步骤3所述翅片间间距的取值范围为:[s
min
,s
max
];
[0107]
其中,s
min
为翅片间间距的最小值,s
max
为翅片间间距的最大值;
[0108]
步骤3所述最优化的翅片长度为:l*;
[0109]
步骤3所述最优化的翅片宽度为:w*;
[0110]
步骤3所述最优化的翅片角度为:a*;
[0111]
步骤3所述最优化的翅片间间距为:s*;
[0112]
步骤4:通过测功机操作台界面在发动机额定转速的80%~120%范围内分别以80%发动机额定转速、90%发动机额定转速、100%发动机额定转速、110%发动机额定转速
和120%发动机额定转速设定发动机的目标转速,通过导线给测功机内部的控制器发送控制命令调节测功机的运行,进而拖动发动机实现其目标转速的反馈控制,重复上述步骤2、3,得到每组发动机转速条件下最优化的翅片长度、每组发动机转速条件下最优化的翅片宽度、每组发动机转速条件下最优化的翅片角度、每组发动机转速条件下最优化的翅片间间距值,进一步分别进行加权计算作为热交换器的最优尺寸;
[0113]
步骤4所述每组发动机转速条件下最优化的翅片长度为:
[0114]
l
opt
=al1*+bl2*+(1-a-b-c-d)l3*+cl4*+dl5*
[0115]
步骤4所述每组发动机转速条件下最优化的翅片宽度为:
[0116]wopt
=aw1*+bw2*+(1-a-b-c-d)w3*+cw4*+dw4*
[0117]
步骤4所述每组发动机转速条件下最优化的翅片角度为:
[0118]aopt
=aa1*+ba2*+(1-a-b-c-d)a3*+ca4*+da4*
[0119]
步骤4所述每组发动机转速条件下最优化的翅片间间距值为:
[0120]sopt
=as1*+bs2*+(1-a-b-c-d)s3*+cs4*+ds4*
[0121]
式中,l
opt
为最终的翅片长度优化值,w
opt
为最终的翅片宽度优化值,a
opt
为最终的翅片角度优化值,s
opt
为最终的翅片间间距优化值,l
x
*表示第x组发动机转速条件下最优化的翅片长度,w
x
*表示第x组发动机转速条件下最优化的翅片宽度,a
x
*表示第x组发动机转速条件下最优化的的翅片角度,s
x
*表示第x组发动机转速条件下最优化的翅片间间距值,a为在0和1之前取值的第1组发动机转速条件下加权系数,b为在0和1之前取值的第2组发动机转速条件下加权系数,c为在0和1之前取值的第4组发动机转速条件下加权系数,d为在0和1之前取值的第5组发动机转速条件下加权系数,且a+b+c+d≤1,x=1,2,3,4,5;其中,x=1表示发动机转速为80%发动机额定转速,x=2表示发动机转速为90%发动机额定转速,x=3表示发动机转速为100%发动机额定转速,x=4表示发动机转速为110%发动机额定转速,x=5表示发动机转速为120%发动机额定转速;a=0.3,b=0.2,c=0.3,d=0.2。
[0122]
如图1所示,一种汽车尾气温差发电系统车载兼容性优化设计方法,包括以下步骤:
[0123]
步骤1:选取热交换器的翅片长度l、翅片宽度w、翅片角度a和翅片间间距s为自变量,以汽车尾气温差发电系统峰值功率p
max
及热交换器压力降p
drop
作为因变量,通过调节可调电子负载和测功机,在发动机给定转速下测得汽车尾气温差发电系统峰值功率p
max
及热交换器压力降p
drop
与热交换器的翅片长度l、翅片宽度w、翅片角度a和翅片间间距s的对应值;
[0124]
步骤2:使用高阶函数分别对步骤(1)中每一组发动机转速测取的汽车尾气温差发电系统峰值功率p
max
及热交换器压力降p
drop
与热交换器的翅片长度l、翅片宽度w、翅片角度a和翅片间间距s的对应值进行曲线拟合,构建汽车尾气温差发电系统峰值功率p
max
及热交换器压力降p
drop
与热交换器的翅片长度l、翅片宽度w、翅片角度a和翅片间间距s之间的函数关系分别如下:
[0125]
p
max
=(a0+a1l+a2l2+
…
+amlm)+(b0+b1w+b2w2+
…
+bnwn)+(c0+c1a+c2a2+
…
+c
jaj
)+(d0+d1s+d2s2+
…
+dksk)
[0126]
p
drop
=(a0+a1l+a2l2+
…
+amlm)+(b0+b1w+b2w2+
…
+bnwn)+(c0+c1a+c2a2+
…
+c
jaj
)+(d0+d1s+d2s2+
…
+dksk)
[0127]
其中,ai和ai为上述两组拟合函数公式中翅片长度l的i次项系数(i=0,1,2,
…
,m),b
x
和b
x
为上述两组拟合函数公式中翅片宽度w的x次项系数(x=0,1,2,
…
,n),cy和cy为上述两组拟合函数公式中翅片角度a的y次项系数(y=0,1,2,
…
,j),dz和dz为上述两组拟合函数公式中翅片间间距s的z次项系数(z=0,1,2,
…
,k);
[0128]
步骤3:以步骤(2)中汽车尾气温差发电系统峰值功率p
max
最大且热交换器压力降p
drop
最小为优化目标,设定热交换器的翅片长度l的取值范围[l
min
,l
max
]、翅片宽度w的取值范围为[w
min
,w
max
]、翅片角度a的取值范围为[a
min
,a
max
]和翅片间间距s的取值范围为[s
min
,s
max
],通过二进制编码,设定种群个体数、交叉概率、变异概率和最大迭代数值,利用遗传算法进行优化得到输出值作为该组发动机转速下最优化的翅片长度l、翅片宽度w、翅片角度a和翅片间间距s值;
[0129]
步骤4:以10%额定转速为幅度,在发动机额定转速的80%~120%范围内分别以80%、90%、100%、110%和120%发动机额定转速,重复上述步骤(2)和(3),得到各组发动机转速条件下最优化的翅片长度l、翅片宽度w、翅片角度a和翅片间间距s值,最后将每组优化的翅片长度l
x
、翅片宽度w
x
、翅片角度a
x
和翅片间间距s
x
值进行加权计算作为热交换器的最优尺寸。
[0130]
如图2所示,一种汽车尾气温差发电系统车载兼容性优化设计方法,其特征在于,所述热交换器为外表面为正多边形,内腔为圆筒式结构,其外部全长为500mm~600mm、壁厚为3mm~5mm、内径为55mm~70mm、有效换热段总长度为400mm~500mm。
[0131]
如图1和2所示,一种汽车尾气温差发电系统车载兼容性优化设计方法,其特征在于,针对每一组发动机转速条件下,设定的优化目标函数f=min(p
drop
/p
max
),设定热交换器的翅片长度20mm≤l≤45mm,热交换器的翅片宽度2mm≤w≤15mm,热交换器的翅片角度30
°
≤a≤90
°
,热交换器的翅片间间距15mm≤s≤40mm。
[0132]
如图2和图3所示,一种汽车尾气温差发电系统车载兼容性优化设计方法,其特征在于,针对每一组发动机转速v
x
条件下得到最优化的翅片长度l
x
、翅片宽度w
x
、翅片角度a
x
和翅片间间距s
x
值,得到热交换器的最优翅片尺寸加权计算方法如下:
[0133]
l
opt
=al1+bl2+(1-a-b-c-d)l3+cl4+dl5[0134]wopt
=aw1+bw2+(1-a-b-c-d)w3+cw4+dw4[0135]aopt
=aa1+ba2+(1-a-b-c-d)a3+ca4+da4[0136]sopt
=as1+bs2+(1-a-b-c-d)s3+cs4+ds4[0137]
式中,l
opt
、w
opt
、a
opt
和s
opt
分别为最终的翅片长度、翅片宽度、翅片角度和翅片间间距的优化值,l
x
、w
x
、a
x
和s
x
(x=1,2,3,4,5)分别对应80%、90%、100%、110%和120%发动机额定转速得到的各组优化的翅片长度、翅片宽度、翅片角度和翅片间间距值,a、b、c和d分别为在0和1之前取值的加权系数,且a+b+c+d≤1。
[0138]
应当理解的是,本说明书未详细阐述的部分均属于现有技术。应当理解的是,上述针对较佳实施例的描述较为详细,并不能因此而认为是对本发明专利保护范围的限制,本领域的普通技术人员在本发明的启示下,在不脱离本发明权利要求所保护的范围情况下,还可以做出替换或变形,均落入本发明的保护范围之内,本发明的请求保护范围应以所附权利要求为准。