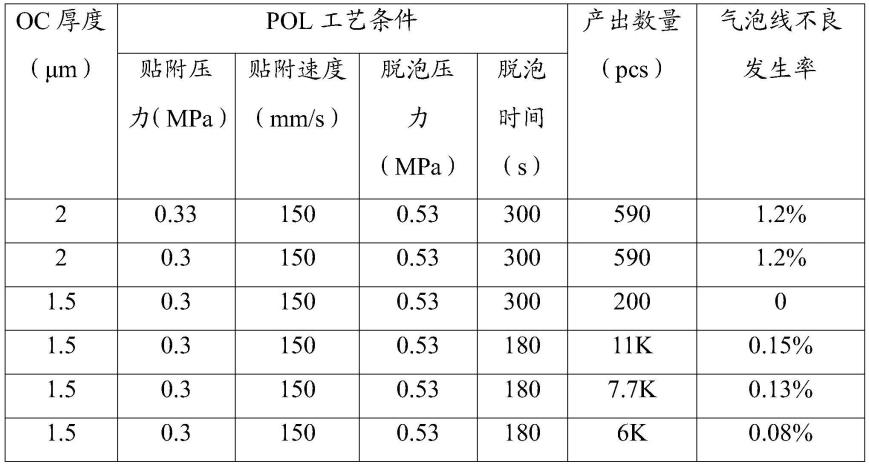
1.本发明涉及显示设备技术领域,特别涉及一种触控显示面板、其制作方法及显示装置。
背景技术:2.目前液晶显示行业技术已发展成熟,缩减成本和增加产品附加值为另一种发展趋势,而且随着消费者对触控技术的需求,mloc(多层外挂式)、sloc(单层外挂式)、touch in cell(内嵌式)等技术应运而生,mloc(mutli layer on cell)为多层结构,每一层均需要相应的掩膜板(mask),成本较高,且整体厚度较厚,不满足窄、薄等要求;touch in cell良率低制约了其发展前景,sloc技术不仅成本低,且良率较高,为目前的主要发展方向。
3.但sloc产品需要一层有机保护层(oc)来保护实现触控感应功能的触控感应(sensor ito)走线不被因外界水汽接触而引起的腐蚀,显示区域(aa区)的有机保护层因影响透过率而被显影掉,仅保留触控扇出区(fanout区)的oc,在触控显示模组贴附偏光片(pol)时容易在oc的边缘(气泡积聚处)出现一条笔直的白线,严重影响产品的外观品质。
技术实现要素:4.本发明提供了一种触控显示面板、其制作方法及显示装置,上述触控显示面板能够降低气泡线不良的发生概率。
5.为达到上述目的,本发明提供以下技术方案:
6.一种触控显示面板,包括:
7.显示面板,所述显示面板包括相对设置的第一显示基板和第二显示基板,所述第二显示基板包括显示区和位于所述显示区一侧的第一非显示区,所述第一非显示区包括触控扇出区;
8.触控感应层,所述触控感应层位于所述第二显示基板背离所述第一显示基板的一侧;
9.有机保护层,所述有机保护层位于所述触控感应层背离所述第二显示基板的一侧,且所述有机保护层在所述第二显示基板上的正投影覆盖于所述触控扇出区上;
10.偏光片,所述偏光片位于所述有机保护层背离所述触控感应层的一侧,所述偏光片位于所述第二显示基板上的正投影与所述有机保护层位于所述第二显示基板上的正投影存在第一交叠区域,且所述第一交叠区域沿第一方向的宽度小于等于900μm,所述第一方向为所述显示区与所述触控扇出区的排列方向。
11.上述触控显示面板中,包括显示面板、触控感应层、有机保护层以及偏光片,其中,显示面板中的第二显示基板包括显示区和位于显示区一侧的第一非显示区,第一非显示区包括触控扇出区,触控感应层位于第二显示基板背离第一显示基板的一侧,有机保护层位于触控感应层背离第二显示基板的一侧,且有机保护层在第二显示基板上的正投影覆盖触控扇出区上,对位于触控扇出区的触控感应层进行保护,偏光片位于有机保护层背离触控
感应层的一侧,由于偏光片位于第二显示基板上的正投影与有机保护层位于第二显示基板上的正投影存在第一交叠区域,且第一交叠区域沿第一方向的宽度小于等于900μm,第一方向为显示区与触控扇出区的排列方向,能够使得偏光片与有机保护层重叠的区域较小,即有机保护层具有段差的位置更靠近偏光片的边缘位置,能够使得在对触控显示面板进行脱泡工艺时,残留在触控显示面板内的气泡更容易被挤压出去,能够降低气泡线不良的发生概率。
12.可选地,所述第二显示基板背离所述触控感应层的一侧形成有遮光层,所述遮光层与所述显示区对应的区域形成有呈阵列分布的开口区,所述遮光层位于所述第一非显示区的正投影与所述偏光片位于所述第一非显示区的正投影存在第二交叠区域;其中,
13.当所述第二交叠区域沿所述第一方向的宽度大于1.5mm时,所述第一交叠区域沿所述第一方向的宽度为0.6mm至0.8mm;
14.当所述第二交叠区域沿所述第一方向的宽度小于等于1.5mm时,所述第一交叠区域沿所述第一方向的宽度为所述第二交叠区域沿所述第一方向的宽度的0.4倍至0.6倍。
15.可选地,当所述第二交叠区域沿所述第一方向的宽度大于1.5mm时,所述第一交叠区域沿所述第一方向的宽度为0.75mm;
16.当所述第二交叠区域沿所述第一方向的宽度小于等于1.5mm时,所述第一交叠区域沿所述第一方向的宽度为所述第二交叠区域沿所述第一方向的宽度的0.5倍。
17.可选地,所述有机保护层的厚度1.5μm至3μm。
18.可选地,所述有机保护层的厚度为1.5μm至2μm。
19.可选地,所述有机保护层临近所述第二显示基板的底面与所述有机保护层临近所述显示区的侧面之间的夹角大于等于5
°
且小于等于75
°
。
20.可选地,所述有机保护层临近所述第二显示基板的底面与所述有机保护层临近所述显示区的侧面之间的夹角大于等于9
°
且小于等于16
°
。
21.可选地,所述偏光片的黏性层的厚度为8μm至27μm。
22.可选地,所述偏光片的硬度为3h至6h。
23.本发明实施例还提供一种显示装置,包括上述技术方案中提供的任意一种触控显示面板。
24.本发明实施例还提供一种触控显示面板的制作方法,包括:
25.形成显示面板,所述显示面板包括相对设置的第一显示基板和第二显示基板,所述第二显示基板包括显示区和位于所述显示区一侧的第一非显示区,所述第一非显示区包括触控扇出区;
26.在所述第二显示基板背离所述第一显示基板的一侧形成触控感应层;
27.在所述触控感应层背离所述第二显示基板的一侧形成有机保护层,所述有机保护层在所述第二显示基板上的正投影覆盖于所述触控扇出区上;
28.在所述有机保护层背离所述触控感应层的一侧贴附偏光片,所述偏光片位于所述第二显示基板上的正投影与所述有机保护层位于所述第二显示基板上的正投影存在第一交叠区域,且所述第一交叠区域沿第一方向的宽度小于等于900μm,所述第一方向为所述显示区与所述触控扇出区的排列方向;
29.对偏光片进行脱泡工艺处理。
30.可选地,所述偏光片的贴附速度为100mm/s至350mm/s,所述偏光片的贴附压力为0mpa至0.4mpa。
31.可选地,所述偏光片的贴附速度为100mm/s至250mm/s,所述偏光片的贴附压力为0.22mpa至0.36mpa。
32.可选地,所述脱泡工艺的脱泡压力为0mpa至0.53mpa,所述脱泡工艺的脱泡时间为0s至300s。
33.可选地,所述脱泡工艺的脱泡压力为0.5mpa至0.53mpa,所述脱泡工艺的脱泡时间为100s至300s。
附图说明
34.图1为本发明实施例提供的一种触控显示装置的结构示意图;
35.图2为本发明实施例提供的另一种触控显示装置的结构示意图;
36.图3为图2对应的投影视图;
37.图4为本发明实施例提供的一种触控显示面板的制作方法的流程图。
38.图标:
39.1-显示面板;11-第一显示基板;12-第二显示基板;2-触控感应层;3-有机保护层;4-偏光片;aa-显示区;bb-第一非显示区。
具体实施方式
40.下面将结合本发明实施例中的附图,对本发明实施例中的技术方案进行清楚、完整地描述,显然,所描述的实施例仅仅是本发明一部分实施例,而不是全部的实施例。基于本发明中的实施例,本领域普通技术人员在没有做出创造性劳动前提下所获得的所有其他实施例,都属于本发明保护的范围。
41.请参考图1、图2和图3,本发明提供一种触控显示面板,包括:
42.显示面板1,显示面板1包括相对设置的第一显示基板11和第二显示基板12,第二显示基板12包括显示区aa和位于显示区aa一侧的第一非显示区bb,第一非显示区bb包括触控扇出区cc;
43.触控感应层2,触控感应层2位于第二显示基板12背离第一显示基板11的一侧;
44.有机保护层3,有机保护层3位于触控感应层2背离第二显示基板12的一侧,且有机保护层3在第二显示基板12上的正投影覆盖于触控扇出区cc上;
45.偏光片4,偏光片4位于有机保护层3背离触控感应层2的一侧,偏光片4位于第二显示基板12上的正投影41与有机保护层3位于第二显示基板12上的正投影31存在第一交叠区域,且第一交叠区域沿第一方向的宽度l1小于等于900μm,第一方向为显示区aa与触控扇出区cc的排列方向。
46.上述发明实施例提供的触控显示面板中,包括显示面板1、触控感应层2、有机保护层3以及偏光片4,其中,显示面板1中的第二显示基板12包括显示区aa和位于显示区aa一侧的第一非显示区bb,第一非显示区bb包括触控扇出区cc,触控感应层2位于第二显示基板12背离第一显示基板11的一侧,有机保护层3位于触控感应层2背离第二显示基板12的一侧,且有机保护层3在第二显示基板12上的正投影覆盖触控扇出区cc上,对位于触控扇出区cc
的触控感应层2进行保护,偏光片4位于有机保护层3背离触控感应层2的一侧,由于偏光片4位于第二显示基板12上的正投影与有机保护层3位于第二显示基板12上的正投影存在第一交叠区域,且第一交叠区域沿第一方向的宽度l1小于等于900μm,第一方向为显示区aa与触控扇出区cc的排列方向,能够使得偏光片4与有机保护层3重叠的区域较小,即有机保护层3具有段差的位置q更靠近偏光片4的边缘位置,能够使得在对触控显示面板进行脱泡工艺时,残留在触控显示面板内的气泡更容易被挤压出去,能够降低气泡线不良的发生概率。
47.上述显示面板可以是液晶显示面板或者是有机电致发光显示面板,在这里不做限制。其中,如果上述显示面板为液晶显示面板,第一显示基板为阵列基板,第二显示基板为彩膜基板,或者第一显示基板为彩膜基板,第二显示面板为阵列基板。
48.上述触控感应层2可以为与显示区aa相对的区域具有触控感应线,与触控扇出区cc相对的区域具有触控扇出走线,触控感应线通过触控扇出走线与触控驱动芯片相连接。
49.上述发明实施例提供的触控显示装置中,如图2所示,第二显示基板12背离触控感应层2的一侧形成有遮光层121,遮光层121与显示区aa对应的区域形成有呈阵列分布的开口区,遮光层121可以为黑矩阵,黑矩阵的开口区设置有色阻层,也可以为其它遮光结构,在这里不做限制;具体地,遮光层121能够对第一非显示区bb进行遮光,有机保护层3的正投影31和偏光片4的正投影41形成的第一交叠区域位于遮光层121对应的区域,能够使得在显示区aa不形成气泡线,不影响触控显示面板显示。其中,遮光层121位于第一非显示区bb的正投影1211与偏光片4位于第一非显示区bb的正投影41存在第二交叠区域。
50.为了保证有机保护层3的正投影21和偏光片4的正投影41形成的第一交叠区域与显示区aa之间的距离以及偏光片4与有机保护层3之间的有效贴附距离,如图2和图3所示,当第二交叠区域沿第一方向的宽度l2大于1.5mm时,第一交叠区域沿第一方向的宽度l1可以为0.6mm至0.8mm;而当第二交叠区域沿第一方向的宽度l2小于等于1.5mm时,第一交叠区域沿第一方向的宽度l1可以为第二交叠区域沿第一方向的宽度l2的0.4倍至0.6倍。此种结构既能保证有机保护层3和偏光片4的交叠区远离显示区aa,又保证使得偏光片4能够贴附到有机保护层3上不会翘起,避免水汽进入导致触控感应层2被腐蚀,并且能够解决气泡线不良的问题。
51.在此基础上,还可以通过同步调整有机保护层3的厚度/工艺条件、偏光片4的工艺参数等,可以解决气泡线的问题,提升产品品质。
52.在一种具体地实施方式中,当第二交叠区域沿第一方向的宽度l2大于1.5mm时,第一交叠区域沿第一方向的宽度l1可以为0.75mm;当第二交叠区域沿第一方向的宽度l2小于等于1.5mm时,第一交叠区域沿第一方向的宽度l1可以为第二交叠区域沿第一方向的宽度的0.5倍。
53.上述发明实施例中,有机保护层3的厚度可以为1.5μm至3μm,能够对触控扇出区的触控扇出走线进行保护,避免触控扇出走线因与外界水汽接触而引起的腐蚀。
54.为了更好的降低气泡线发生的概率,有机保护膜层的厚度可以降低到1.5μm至2.0μm。有机保护层3的厚度降低,则其自身的段差降低,能够使得偏光片4贴附时在有机保护层3的段差处压入量增大,有机保护层3段差处气泡积聚总量降低,在对触控显示面板进行脱泡工艺时气泡更容易被挤压出去,从而降低气泡线不良发生率。并且,有机保护层3减薄也可以节约成本,且有机保护层3也不能无限制减薄,否则容易在成膜过程中出现破膜,影响
对触控感应层2的保护。
55.如表1所示,具有不同厚度的有机保护层3条件下气泡线不良发生率的验证结果。其中,表中验证的触控面板的尺寸均为15.6英寸,从表1可以看出在相同的pol工艺条件下,有机保护层3的厚度越小,气泡线不良发生率越低。
56.表1
[0057][0058]
上述发明实施例中,有机保护层3临近第二显示基板12的底面与有机保护层3临近显示区aa的侧面之间的夹角θ可以大于等于5
°
且小于等于75
°
。其中,θ的数值越小,偏光片4与有机保护层3的接触性越好,偏光片4与有机保护层3的边缘交叠处残留的气泡更小,脱泡时气泡也更容易被挤压出去。
[0059]
在一种具体地实施方式中,为了更好的减小气泡线不良发生率,有机保护层3临近第二显示基板12的底面与有机保护层3临近显示区aa的侧面之间的夹角θ可以大于等于9
°
且小于等于16
°
。
[0060]
上述发明实施例中,偏光片4靠近有机保护层3一侧具有黏性层,偏光片4的黏性层的厚度可以为8μm至27μm。偏光片4与有机保护层3之间主要靠黏性层进行连接,黏性层厚度越厚,脱泡前气泡线现象越轻微。
[0061]
上述发明实施例中,偏光片4的硬度可以为3h至6h。在黏性层厚度相同前提下,偏光片4硬度越大,脱泡前气泡线不良现象越重,偏光片4在有机保护层3的段差处更不容易变形弯曲和折叠,脱泡工艺时不容易将有机保护层3的段差处残留气泡挤压出去。而同步脱泡前在偏光片4边缘处涂覆可剥蓝胶(tuffy胶)进行密封,然后再进行脱泡工艺,发现未涂覆tuffy胶样品无气泡线,而涂覆tuffy胶样品气泡线不良发生率较高。
[0062]
如表2所示,为不同偏光片4下气泡线不良发生情况的验证结果。由表2可以看出,脱泡前,在偏光片4硬度相同的情况下,偏光片4黏性层越厚,脱泡前气泡线现象越轻微,在偏光片4边缘处未涂覆tuffy胶的情况下,脱泡后可实现无气泡线。而脱泡后,在偏光片4的黏性层厚度相同的情况选,偏光片4边缘处未涂覆tuffy胶时,触控显示面板样品无气泡线,偏光片4边缘处涂覆tuffy胶时,样品气泡线不良发生率较高,这是因为tuffy胶对偏光片4边缘进行了密封,在脱泡时,不能很好的将气泡挤压出来。
[0063]
表2
[0064][0065]
基于同一发明构思,本发明实施例还提供一种显示装置,包括上述技术方案中提供的任意一种触控显示面板。
[0066]
本发明实施例还提供一种触控显示面板的制作方法,应用于上述技术方案中提出的任意一种触控显示面板,如图4所示,具体包括以下步骤:
[0067]
s401:形成显示面板,显示面板包括相对设置的第一显示基板和第二显示基板,第二显示基板包括显示区和位于显示区一侧的第一非显示区,第一非显示区包括触控扇出区;
[0068]
s402:在第二显示基板背离第一显示基板的一侧形成触控感应层;
[0069]
s403:在触控感应层背离第二显示基板的一侧形成有机保护层,有机保护层在第二显示基板上的正投影覆盖于触控扇出区上;
[0070]
s404:在有机保护层背离触控感应层的一侧贴附偏光片,偏光片位于第二显示基板上的正投影与有机保护层位于第二显示基板上的正投影存在第一交叠区域,且第一交叠区域沿第一方向的宽度小于等于900μm,第一方向为显示区与触控扇出区的排列方向;
[0071]
s405:对偏光片进行脱泡工艺处理。
[0072]
上述发明实施例提供的触控显示面板的制作方法中,依次形成显示面板、触控感应层、有机保护层和偏光片贴附,由于偏光片位于第二显示基板上的正投影与有机保护层位于第二显示基板上的正投影存在第一交叠区域,且第一交叠区域沿第一方向的宽度小于等于900μm,第一方向为显示区与触控扇出区的排列方向,能够使得偏光片与有机保护层重叠的区域较小,即有机保护层具有段差的位置更靠近偏光片的边缘位置,能够使得在对偏光片进行脱泡工艺时,残留在触控显示面板内的气泡更容易被挤压出去,能够降低气泡线
的发生概率。
[0073]
上述发明实施例中,偏光片的贴附速度可以为100mm/s至350mm/s,偏光片的贴附压力可以为0mpa至0.4mpa,能够实现偏光片在触控显示面板上的贴附。
[0074]
为了降低气泡线不良的产生率,具体地,还可以降低贴附速率和增大贴附压力。例如,偏光片的贴附速率可以为100mm/s至250mm/s,偏光片的贴附压力可以为0.22mpa至0.36mpa。降低偏光片贴附速度和增大偏光片贴附压力时,偏光片的黏性层压入量增大,脱泡前偏光片与有机保护层段差处残留气泡总量较改善前减少,降低发生率。但偏光片贴附速度也不可能无限降低,否则会影响生产时间,损失产能,偏光片贴附压力因设备极限不可能无限量增加,一般上限为0.4mpa。
[0075]
如表3所示,为偏光片贴附工艺参数调整气泡线不良情况验证。由表3中的内容可知看出,偏光片贴附速度越低,气泡线不良的发生率越低;偏光片的贴附压力越大,气泡线不良的发生率越低。
[0076]
表3
[0077][0078]
上述发明实施例中,脱泡工艺的脱泡压力可以为0mpa至0.6mpa,脱泡时间可以为0s至300s。在贴附完偏光片后,对偏光片进行脱泡工艺处理,能够将偏光片内残留的气泡被挤压排出,降低气泡线不良的产生率。
[0079]
在一种具体实施方式中,为了降低气泡线不良的产生率,还可通过增大脱泡压力和延长脱泡时间来实现。脱泡工艺的脱泡压力可以为0.5mpa至0.53mpa,脱泡时间可以为100s至300s。脱泡压力增大和脱泡时间增加,即更大的脱泡强度和时间可以将有机保护层段差处的残留气泡挤压出去或者变成更小肉眼难以看见的气泡,从而气泡线不良的问题。其中,设备脱泡压力上限为0.53mpa,而更长的脱泡时间对产能有很大影响。
[0080]
如表4所示,为偏光片脱泡工艺参数调整气泡线不良情况验证。由表4可以看出脱泡时间越长,气泡不良的发生率越低。
[0081]
表4
[0082][0083]
显然,本领域的技术人员可以对本发明实施例进行各种改动和变型而不脱离本发明的精神和范围。这样,倘若本发明的这些修改和变型属于本发明权利要求及其等同技术的范围之内,则本发明也意图包含这些改动和变型在内。