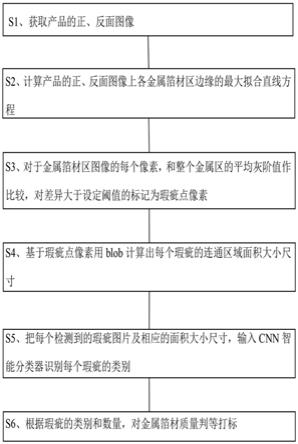
1.本发明涉及一种金属箔材制造中基于机器视觉的质量分析方法。适用于产品质量检测领域。
背景技术:2.金属箔材广泛应用于包装,锂电池基材等行业,对产品的质量要去日益增长,其质量控制涉及表面平整均匀性,还涉及针孔、压印、起皱、脏污、暗斑等瑕疵的检测控制。
3.目前,传统量测方式是需要产线低速运行,用人眼的方式检测各种缺陷,检测精度低,速度慢;而且由于金属箔材高亮反光,人眼易疲劳导致漏检误检,影响产品质量。
技术实现要素:4.本发明要解决的技术问题是:针对上述存在的问题,提供一种金属箔材制造中基于机器视觉的质量分析方法。
5.本发明所采用的技术方案是:一种金属箔材制造中基于机器视觉的质量分析方法,其特征在于:
6.s1、获取产品的正、反面图像;
7.s2、计算产品的正、反面图像上各金属箔材区边缘的最大拟合直线方程;
8.s3、对于金属箔材区内的每个像素,将其与整个金属区的平均灰阶值作比较,对差异大于设定阈值的标记为瑕疵点像素;
9.s4、基于瑕疵点像素计算出每个瑕疵的连通区域面积大小尺寸;
10.s5、把每个检测到的瑕疵图片及相应的面积大小尺寸,输入cnn智能分类器识别每个瑕疵的类别;
11.s6、根据瑕疵的类别和数量,对金属箔材质量判等打标。
12.步骤s2包括:
13.s21、通过图像金字塔算法找到产品正、反面图像上金属箔材区两边大概位置区域;
14.s22、在大概位置区域内,做一次中值滤波,去除噪声信号;
15.s23、使用prewitt算子计算出金属区x和y方向的边缘图像;
16.s24、用x和y方向边缘值计算出每个像素点的梯度方向及导数;
17.s25、根据梯度方向及导数,剔除边缘响应小的像素,留下连续的边缘响应最大的骨架线;
18.s26、基于骨架线采用hough变换计算出边缘点的最大拟合直线方程。
19.还包括:
20.根据金属箔材区两边的直线方程计算出产品的宽度,并与标准值比较,给出尺寸判等结果。
21.一种金属箔材制造中基于机器视觉的质量分析装置,其特征在于,包括:
22.图像获取模块,用于获取产品的正、反面图像;
23.边缘拟合模块,用于计算产品的正、反面图像上各金属箔材区边缘的最大拟合直线方程;
24.瑕疵点识别模块,用于对于金属箔材区内的每个像素,将其与整个金属区的平均灰阶值作比较,对差异大于设定阈值的标记为瑕疵点像素;
25.瑕疵尺寸计算模块,用于基于瑕疵点像素计算出每个瑕疵的连通区域面积大小尺寸;
26.瑕疵分类模块,用于把每个检测到的瑕疵图片及相应的面积大小尺寸,输入cnn智能分类器识别每个瑕疵的类别;
27.质量判等模块,用于根据瑕疵的类别和数量,对金属箔材质量判等打标。
28.所述边缘拟合模块,包括:
29.区域查找模块,用于通过图像金字塔算法找到产品正、反面图像上金属箔材区两边大概位置区域;
30.去噪模块,用于在大概位置区域内,做一次中值滤波,去除噪声信号;
31.边缘图像计算模块,用于使用prewitt算子计算出金属区x和y方向的边缘图像;
32.梯度及导数计算模块,用于利用x和y方向边缘值计算出每个像素点的梯度方向及导数;
33.像素剔除模块,用于根据梯度方向及导数,剔除边缘响应小的像素,留下连续的边缘响应最大的骨架线;
34.边缘点拟合模块,用于基于骨架线采用hough变换计算出边缘点的最大拟合直线方程。
35.还包括:
36.宽度判等模块,用于根据金属箔材区两边的直线方程计算出产品的宽度,并与标准值比较,给出尺寸判等结果。
37.一种存储介质,其上存储有能被处理器执行的计算机程序,其特征在于:所述计算机程序被执行时实现所述金属箔材制造中基于机器视觉的质量分析方法的步骤。
38.一种数据处理设备,具有存储器和处理器,存储器上存储有能被处理器执行的计算机程序,其特征在于:所述计算机程序被执行时实现所述金属箔材制造中基于机器视觉的质量分析方法的步骤。
39.一种基于机器视觉的产品质量检测系统,其特征在于,包括:
40.工业相机ⅰ,用于采集产品正面图像;
41.工业相机ⅱ,用于采集产品反面图像;
42.编码器,该编码器与产品接触,用于获取产品的传送距离,并在产品每传送一定距离后为相机ⅰ、ⅱ提供图像采集触发信号;
43.光源,用于照亮所述工业相机下放的金属箔材产品;
44.数据处理设备,具有存储器和处理器,存储器上存储有能被处理器执行的计算机程序,所述计算机程序被执行时实现所述金属箔材制造中基于机器视觉的质量分析方法的步骤。
45.本发明的有益效果是:本发明通过将金属箔材区内像素点与整个金属区的平均灰
阶值作比较,将差异大于设定阈值的标记为瑕疵点像素,通过瑕疵点像素计算瑕疵面积,基于瑕疵图像及瑕疵面积进行瑕疵分类,根据瑕疵的类别和数量对金属箔材质量判等打标,可自动实现产品质量检测,提高整体效率,保障产品质量。
附图说明
46.图1为实施例一种金属箔材制造中基于机器视觉的质量分析方法的步骤流程示意图。
47.图2为实施例一种金属箔材制造中基于机器视觉的质量分析装置的模块框图。
具体实施方式
48.本实施例为一种金属箔材制造中基于机器视觉的质量分析方法,具体包括以下步骤:
49.s1、获取产品的正、反面图像;
50.s2、计算产品的正、反面图像上各金属箔材区边缘的最大拟合直线方程;
51.s3、对于金属箔材区图像的每个像素,和整个金属区的平均灰阶值作比较,对差异大于设定阈值的标记为瑕疵点像素;
52.s4、基于瑕疵点像素用blob计算出每个瑕疵的连通区域面积大小尺寸。
53.s5、把每个检测到的瑕疵图片及相应的面积大小尺寸,输入cnn智能分类器识别每个瑕疵的类别;
54.s6、根据瑕疵的类别和数量,对金属箔材质量判等打标。
55.本实施例中计算产品的正、反面图像上各金属箔材区边缘的最大拟合直线方程,包括:
56.s21、通过图像金字塔算法找到产品正、反面图像上金属箔材两边大概位置区域;
57.s22、在大概位置区域内,做一次中值滤波,去除噪声信号;
58.s23、使用prewitt算子计算出金属箔材区x和y方向的边缘图像;
59.s24、用x和y方向边缘值计算出每个像素点的梯度方向及导数;
60.s25、根据梯度方向及导数,剔除边缘响应小的像素,留下连续的边缘响应最大的骨架线;
61.s26、基于骨架线采用hough变换计算出边缘点的最大拟合直线方程。
62.本实施例中金属箔材制造中基于机器视觉的质量分析方法,还包括:根据金属箔材两边的边缘直线方程计算出产品的宽度,并与标准值比较,给出尺寸判等结果。
63.本实施例还提供一种金属箔材制造中基于机器视觉的质量分析装置,包括:图像获取模块、边缘拟合模块、宽度判等模块、瑕疵点识别模块、瑕疵尺寸计算模块、瑕疵分类模块和质量判等模块等。
64.本例中图像获取模块用于获取产品的正、反面图像;边缘拟合模块用于计算产品的正、反面图像上各金属箔材区边缘的最大拟合直线方程;宽度判等模块用于根据金属箔材区两边的直线方程计算出产品的宽度,并与标准值比较,给出尺寸判等结果;瑕疵点识别模块用于对于金属箔材区内的每个像素,将其与整个金属区的平均灰阶值作比较,对差异大于设定阈值的标记为瑕疵点像素;瑕疵尺寸计算模块用于基于瑕疵点像素计算出每个瑕
疵的连通区域面积大小尺寸;瑕疵分类模块用于把每个检测到的瑕疵图片及相应的面积大小尺寸,输入cnn智能分类器识别每个瑕疵的类别;质量判等模块,用于根据瑕疵的类别和数量,对金属箔材质量判等打标。
65.本实施例中边缘拟合模块,包括:区域查找模块、去噪模块、边缘图像计算模块、梯度及导数计算模块、像素剔除模块和边缘点拟合模块。
66.本例中区域查找模块用于通过图像金字塔算法找到产品正、反面图像上金属箔材区两边大概位置区域;去噪模块用于在大概位置区域内,做一次中值滤波,去除噪声信号;边缘图像计算模块用于使用prewitt算子计算出金属区x和y方向的边缘图像;梯度及导数计算模块用于利用x和y方向边缘值计算出每个像素点的梯度方向及导数;像素剔除模块用于根据梯度方向及导数,剔除边缘响应小的像素,留下连续的边缘响应最大的骨架线;边缘点拟合模块用于基于骨架线采用hough变换计算出边缘点的最大拟合直线方程。
67.本实施例还提供一种存储介质,其上存储有能被处理器执行的计算机程序,该计算机程序被执行时实现本实施例中金属箔材制造中基于机器视觉的质量分析方法的步骤。
68.本实施例还提供一种基于机器视觉的产品质量检测系统,包括:工业相机ⅰ、工业相机ⅱ、编码器、光源和数据处理设备等。
69.本例中工业相机ⅰ用于采集产品正面图像;工业相机ⅱ用于采集产品反面图像;编码器该编码器与产品接触,用于获取产品的传送距离,并在产品每传送一定距离后为相机ⅰ、ⅱ提供图像采集触发信号;光源用于照亮所述工业相机下放的金属箔材产品;数据处理设备具有存储器和处理器,存储器上存储有能被处理器执行的计算机程序,该计算机程序被执行时实现本实施例中金属箔材制造中基于机器视觉的质量分析方法的步骤。