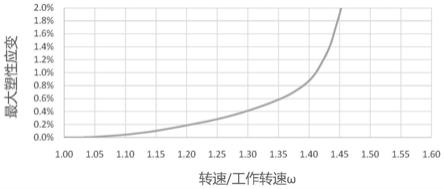
1.本发明涉及一种离心叶轮强度安全性校核方法,具体涉及一种离心叶轮强度安全系数的获取方法。
背景技术:2.离心压缩机是工程上重要的能量转换装置,它被广泛地应用于能源、动力及化工等工程领域。叶轮作为离心压缩机的核心零部件,它的安全运行是离心压缩机整体可靠性的重要保障,因此在设计阶段必须计算叶轮强度,确保其安全性。
3.目前叶轮强度计算普遍采用有限元方法,根据叶轮最大应力与叶轮材料屈服强度的关系,叶轮强度有限元计算分弹性和弹塑性两类。叶轮弹性计算方法适用于最大应力小于材料屈服强度的情况,此时应力、应变与外载荷成线性比例关系,求解速度快,且以应力值评价叶轮强度。而叶轮弹塑性计算方法适用于最大应力超过材料屈服强度的情况,此时叶轮局部出现塑性变形,应力、应变与外载荷成非线性关系,求解器需反复迭代求解应力、应变,且以塑性应变值评价叶轮强度。
4.弹性计算方法适用于低线速度、低应力的叶轮,而随着工程应用需求的变化,叶轮直径趋于大型化,线速度普遍较高,局部应力超过材料屈服强度,出现塑性变形,此情况通常采用弹塑性计算方法获取叶轮塑性应变,进而评价叶轮强度,而弹塑性计算方法耗时长,占用计算资源多,在设计过程中不能快速获知叶轮强度,影响叶轮设计效率。
技术实现要素:5.本发明提供了一种离心叶轮强度安全系数的获取方法,解决现有离心叶轮强度有限元计算方法不统一,分弹性和弹塑性两种的问题,解决在采用弹塑性方法进行计算时,求解器反复迭代,耗时长,占用计算资源多,不能快速获知叶轮强度的安全性,影响叶轮设计效率的问题。
6.本发明的基本构思是:通过弹塑性有限元法计算叶轮在不同转速下的最大塑性应变,统计叶轮的计算数据,确定叶轮塑性应变极限值,再结合理论计算公式,将极限塑性应变等效转换至弹性有限元法的弹性应力值,即将叶轮弹塑性有限元计算转换为弹性有限元计算,使弹性和弹塑性两类有限元计算法统一为弹性有限元计算法,达到使用弹性有限元法计算叶轮强度,快速获知叶轮的安全性,高效完成叶轮设计的目的。
7.本发明所采用的技术方案是:
8.一种离心叶轮强度安全系数的获取方法,其特殊之处在于,包括以下步骤:
9.1)建立叶轮弹塑性有限元计算模型
10.1.1)在三维cad软件中建立叶轮三维模型,模型包含叶片与轮盘、轮盖连接处的倒角,然后将模型导入有限元分析软件;
11.1.2)设置叶轮材料的弹塑性参数,包括密度、泊松比、弹性模量、屈服强度、应力应变关系,应力应变关系采用双线性随动强化模型,切线模量为e1;
12.1.3)考虑离心力作用,对叶轮施加绕旋转轴的工作转速ω;
13.1.4)设置叶轮轴孔径向自由,周向和轴向固定;
14.1.5)设置合理网格尺寸将叶轮划分为四面体单元;
15.1.6)设置弹塑性非线性求解参数,包括求解器类型、时间步长、收敛准则,开启大变形功能;
16.1.7)设置结果输出塑性应变后进行求解;
17.2)统计分析塑性应变极限值
18.2.1)按照步骤1.1至步骤1.7进行叶轮弹塑性计算,分别对1.1ω~2.0ω多个转速进行弹塑性计算,转速间隔可取0.1ω,处理计算结果得到叶轮的最大塑性应变,拟合数据绘制最大塑性应变与转速的关系曲线;
19.2.2)根据叶轮最大塑性应变与转速的关系曲线,确定此类离心叶轮塑性应变极限值ε
p
;
20.3)建立塑性应变与弹性应力的关系
21.利用neuber公式(1),在已知局部塑性应力应变时,将局部应力应变转换到弹性应力应变,转换关系如下:
[0022][0023][0024][0025]
将公式(2)、(3)代入公式(1)中,得
[0026][0027][0028][0029]
其中,k
t
为弹性应力集中系数,k
σ
为应力集中系数,k
ε
为应变集中系数,σ为局部应力,σ
nom
为弹性名义应力,ε为局部总应变,ε
nom
为名义应变,e为弹性模量;
[0030]
4)计算叶轮弹性应力极限值σ
lim
[0031]
局部应力根据公式(7)计算,
[0032]
σ=σs+e1·
ε
p
ꢀꢀꢀ
(7)
[0033]
根据公式(6)和(7),可得弹性应力极限值:
[0034][0035]
其中:
[0036]
σs为屈服强度;
[0037]
e为弹性模量;
[0038]
e1为切线模量;
[0039]
ε
p
为步骤2.2)确定的塑性应变极限值;
[0040]kt
为弹性应力集中系数;
[0041]
εe为弹性应变;
[0042]
5)叶轮弹性应力计算
[0043]
5.1)在三维cad软件中建立叶轮三维模型,模型包含叶片与轮盘、轮盖连接处的倒角,然后将模型导入有限元分析软件;
[0044]
5.2)设置叶轮材料的弹性参数,包括密度、泊松比、弹性模量;
[0045]
5.3)仅考虑离心力作用,在叶轮弹塑性模型中添加叶轮绕旋转轴的最大转速ω
max
;
[0046]
5.4)要求叶轮轴孔径向自由,周向和轴向固定约束;
[0047]
5.5)设置合理网格尺寸将叶轮划分为四面体单元;
[0048]
5.6)设置求解器类型,结果输出冯米塞斯应力,求解计算后得到最大冯米塞斯应力σ
mises
及其位置;
[0049]
6)计算安全系数n:
[0050][0051]
其中:
[0052]
σ
lim
为步骤4)得到的叶轮弹性应力极限值;
[0053]
σ
mises
为步骤5)得到的叶轮冯米塞斯应力最大值;
[0054]
7)若安全系数n大于预设值,则叶轮强度满足设计要求;若安全系数n小于预设值,则叶轮强度不满足设计要求,对叶轮结构需做优化改进,改进后再转至步骤5)。
[0055]
进一步地,所述步骤2.2)中,塑性应变极限值ε
p
取0.01~0.015;
[0056]
所述步骤4)中,弹性应力集中系数k
t
取0.95~1.05。
[0057]
进一步地,所述步骤2.2)中,塑性应变极限值ε
p
取0.01;
[0058]
所述步骤4)中,弹性应力集中系数k
t
取1。
[0059]
进一步地,所述设置合理网格类型将叶轮划分为10节点四面体单元;
[0060]
进一步地,步骤1.5)中,所述设置合理网格尺寸将叶轮划分为10节点四面体单元具体为:
[0061]
设置叶轮总体网格尺寸为叶片厚度值,所有叶片表面网格尺寸为厚度值的一半,叶片与轮盘、轮盖连接处的过渡圆角至少分3排单元。
[0062]
本发明相比现有技术的有益效果是:
[0063]
本发明提供的离心叶轮强度安全系数获取方法,通过对离心叶轮进行弹塑性有限元计算,统计分析确定了叶轮塑性应变极限值,再结合理论计算公式,将极限塑性应变等效转换至弹性有限元法的弹性应力值,即将弹塑性计算转换为弹性计算,使叶轮强度计算合并为一类计算,有效解决了弹塑性有限元法耗时长,占用计算资源多的问题,从而提高叶轮的设计效率。
附图说明
[0064]
图1是本发明一个实施例中的叶轮最大塑性应变与转速的关系曲线图;
[0065]
图2是本发明实施例中的叶轮塑性应变-弹性应力转换关系曲线图;
[0066]
图3是本发明实施例中的叶轮总体网格尺寸示意图。
具体实施方式
[0067]
下面结合附图和具体实施方式对本发明进行详细说明。
[0068]
一种离心叶轮强度安全系数的获取方法,具体如下:
[0069]
1)建立叶轮弹塑性有限元计算模型
[0070]
1.1)在三维cad软件中建立叶轮三维模型,模型包含叶片与轮盘、轮盖连接处的倒角,然后将模型导入有限元分析软件。
[0071]
1.2)设置叶轮材料的弹塑性参数,包括密度、泊松比、弹性模量、屈服强度、应力应变关系,应力应变关系采用双线性随动强化模型,切线模量为e1。
[0072]
1.3)考虑离心力作用,对叶轮施加绕旋转轴的工作转速ω。
[0073]
1.4)设置叶轮轴孔径向自由,周向和轴向固定。
[0074]
1.5)设置合理网格尺寸将叶轮划分为10节点四面体单元,具体为:如图3所示,设置叶轮总体网格尺寸为叶片厚度值,所有叶片表面网格尺寸为厚度值的一半,叶片与轮盘、轮盖连接处的过渡圆角至少分3排单元。
[0075]
1.6)设置弹塑性非线性求解参数,包括求解器类型、时间步长、收敛准则,开启大变形功能。
[0076]
1.7)设置结果输出塑性应变后进行求解。
[0077]
2)统计分析塑性应变极限值
[0078]
按照步骤1.1至步骤1.7进行叶轮弹塑性计算,分别对1.1ω~2.0ω多个转速进行弹塑性计算,转速间隔可取0.1ω,处理计算结果得到叶轮的最大塑性应变,拟合数据绘制最大塑性应变与转速的关系曲线,经统计分析,叶轮最大塑性应变为1%~1.5%时,塑性应变快速增加,如图1所示,叶轮表面塑性区逐渐扩大,开始萌生裂纹,并逐渐扩展至破裂失效,由于叶轮安全性对压缩机至关重要,保守考虑此类离心叶轮塑性应变极限值取ε
p
=1%。
[0079]
3)建立塑性应变与弹性应力的关系
[0080]
当弹性计算的局部弹性名义应力超过屈服强度时,可以采用neuber公式将弹性名义应力应变转换为局部应力应变。离心叶轮的最大弹性应力通常出现在叶片与轮盘或轮盖的连接过渡圆角区或附近,属应力集中影响区域,经过仿真计算符合neuber公式的应用条件。本发明反之,利用neuber公式(1),在已知局部塑性应力应变时,将局部应力应变转换到弹性应力应变,由公式(6)可计算出弹性名义应力,转换关系如图2所示,公式之间的转换如下所示:
[0081][0082]
[0083][0084]
将公式(2)、(3)代入公式(1)中,得
[0085][0086][0087][0088]
其中,k
t
为弹性应力集中系数,k
σ
为应力集中系数,k
ε
为应变集中系数,σ为局部应力,σ
nom
为弹性名义应力,ε为局部总应变,ε
nom
为名义应变,e为弹性模量。
[0089]
4)求解叶轮弹性应力极限值
[0090]
通过有限元方法计算的应力,考虑了应力集中影响,因此k
t
=1。在步骤2中已通过大量仿真计算获得塑性应变的极限值ε
p
,其对应的局部应力按公式(7)计算,
[0091]
σ=σs+e1·
ε
p
ꢀꢀꢀ
(7)
[0092]
按公式(6)和(7),可得弹性应力极限值:
[0093][0094]
其中,σ
lim
为弹性应力极限值,εe为弹性应变,ε
p
为塑性应变的极限值,σs为屈服强度,e为弹性模量,e1为切线模量。
[0095]
5)叶轮弹性应力计算
[0096]
5.1)在三维cad软件中建立叶轮三维模型,模型包含叶片与轮盘、轮盖连接处的倒角,然后将模型导入有限元分析软件。
[0097]
5.2)设置叶轮材料的弹性参数,包括密度、泊松比、弹性模量;
[0098]
5.3)仅考虑离心力作用,对叶轮施加绕旋转轴的最大转速ω
max
。
[0099]
5.4)要求叶轮轴孔径向自由,周向和轴向固定约束。
[0100]
5.5)设置合理网格尺寸将叶轮划分为10节点四面体单元,同步骤1.5),设置叶轮总体网格尺寸为叶片厚度值,所有叶片表面网格尺寸为厚度值的一半,叶片与轮盘、轮盖连接处的过渡圆角至少分3排单元。
[0101]
5.6)设置求解器类型,结果输出冯米塞斯应力,求解计算后处理得到冯米塞斯应力最大值σ
mises
及其位置。
[0102]
6)按下式计算安全系数n:
[0103][0104]
由公式(8)可以看出,当材料相同时,由于屈服强度、弹性模量、切线模量不变,因此叶轮弹性极限应力为定值,对于新结构叶轮的安全系数计算,只需进行步骤5)和步骤6)。
[0105]
7)若安全系数n大于预设值(如预设值为1.25),则叶轮可在最大转速ω
max
最大下
安全运行;若安全系数n小于预设值,则叶轮在最大转速ω
max
下运行存在安全风险,需对叶轮结构做优化改进,改进后再转至步骤5)。
[0106]
以具体叶轮设计过程为例:
[0107]
已知某类离心叶轮材料为fv520b,材料密度ρ=7850kg/m3,屈服强度σs=880mpa,泊松比ν=0.3,弹性模量e=2.0e5mpa,切线模量e1=100mpa。
[0108]
1)按步骤1至步骤4,进行弹塑性有限元计算后统计分析得到,此类离心叶轮采用fv520b材料时的塑性应变极限值ε
p
=0.012,再按公式(8)计算得到叶轮弹性应力极限值:
[0109][0110]
对一新设计的叶轮按步骤5)进行叶轮弹性有限元应力计算,转速设置为叶轮的最大转速1241.8rad/s,后处理得到冯米塞斯应力最大值σ
mises
=1161.6mpa。
[0111]
按公式(9)计算安全系数n:
[0112][0113]
安全系数n大于预设值1.25,叶轮可在最大转速1241.8rad/s安全运行。
[0114]
本发明的计算方法可大大缩短叶轮强度计算时间,节约计算资源。对一个叶轮划分10节点四面体单元,节点数3187776、单元数2180016,进行弹性和弹塑性有限元计算,计算时间和占用资源如表1所示。
[0115]
表1弹性与弹塑性有限元计算对比
[0116] 弹性计算弹塑性计算计算时间9分45秒1小时23分53秒磁盘写入总数据4.5gb158.5gb磁盘读取总数据1.7gb150.1gb
[0117]
对大量叶轮进行弹塑性和本发明的弹性有限元计算,经比对分析,本发明的方法可获得与弹塑性有限元一致的安全性评价结果。