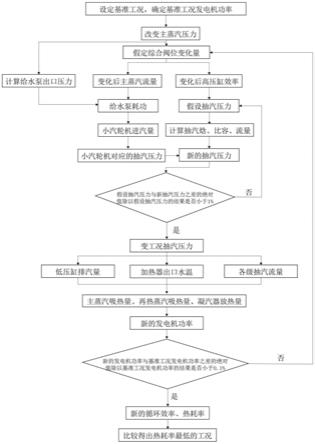
1.本发明涉及一种变工况下汽轮机组主蒸汽压力寻优计算方法,属于火力发电厂汽轮机组运行优化领域。
背景技术:2.汽轮机滑压优化是指在电负荷一定时,改变主蒸汽压力导致蒸汽参数也随之变化,蒸汽参数变化时对应的调门开度也不同,则会有如下影响:1)部分进汽及节流损失发生变化,使调节级焓降偏离设计值,从而改变高压缸效率;2)若汽动给水泵出口压力下降,功耗降低,使拖动给水泵的小汽轮机耗汽减小,经济性提高;3)蒸汽参数降低会使汽轮机焓降减少,循环热效率降低,而机组的绝对内效率是相对内效率与循环热效率的乘积,故机组的绝对内效率降低。综合这些因素即可找出高压缸效率、给水泵耗功与循环热效率三者之间的最优组合,得出不同负荷下的最佳运行主蒸汽压力,提升汽轮机组的经济性能。
3.汽轮机热耗率是综合反映汽轮机组经济性的热力学指标,因此同一工况下对应汽轮机热耗率最低的主蒸汽压力即为最优主蒸汽压力。传统汽轮机滑压优化汽轮机最优主蒸汽压力是通过现场热力性能试验计算得到,通过比较相同负荷,不同主蒸汽压力下的汽轮机热耗率,选择汽轮机热耗率最低的主蒸汽压力作为最优主蒸汽压力,但试验期间,受运行方式改变、入炉煤质变化、给水流量测点精度、系统隔离等因素的影响,现场试验得到的热耗率误差较大,不能真实体现主蒸汽压力的变化对热耗率的影响,且机组的边界参数变化,也会对最优主蒸汽压力产生影响。
技术实现要素:4.针对现有技术的不足,本发明的目的是提供一种变工况下汽轮机组主蒸汽压力寻优计算方法,无需做多次的热力性能试验,便可直接计算得到滑压优化结论。。
5.为了实现上述目的,本发明所采用的技术方案是:
6.一种变工况下汽轮机组主蒸汽压力寻优计算方法,包括以下步骤:
7.步骤1:在汽轮机组确定负荷下,固定主蒸汽压力,进行汽轮机热力性能试验,按照试验标准,采集系统参数并计算汽轮机热耗率,确定发电机功率,以此次试验作为基准工况,然后改变主蒸汽压力;
8.步骤2:改变主蒸汽压力后假定综合阀位变化量,根据改变后的综合阀位变化量计算变化后主蒸汽流量、变化后高压缸效率、给水泵有效功率与新的抽汽压力;
9.步骤3:根据变工况后计算出来的抽汽压力,计算低压缸排汽量、加热器出口水温、各级抽汽流量、主蒸汽吸热量、再热蒸汽吸热量与凝汽器放热量,从而得到新的发电机功率;
10.步骤4:将步骤3中得到的发电机功率与步骤1中的基准工况的发电机功率进行比较,如果二者偏差绝对值除以基准工况的发电机功率的结果小于0.1%,即认为计算结束转到步骤5,否则返回到步骤2;
11.步骤5:将变工况计算得出的不同热耗率相互进行比较,热耗率最小工况下的主蒸汽压力即为最优主蒸汽压力。
12.所述步骤2中变化后主蒸汽流量、变化后高压缸效率、变化后给水泵有效功率与新的抽汽压力的计算由改变后的主蒸汽压力大小与假定的综合阀位进行计算得来。
13.所述变化后主蒸汽流量的计算方法如下:
14.根据弗留格尔公式:
[0015][0016]
式中:g0为基准工况主蒸汽流量,t/h;g1为变工况主蒸汽流量,t/h;p
00
为基准工况主蒸汽压力,mpa;p
01
为变工况主蒸汽压力,mpa;t
00
为基准工况调节级后温度,k;t
01
为变工况调节级后温度,k;a0为基准工况汽轮机进汽面积,m2;a1为变工况汽轮机进汽面积,m2;
[0017]
由于主蒸汽流量与调节级压力呈正比关系,于是用调节级压力代表主蒸汽流量,同时忽略温度的变化,对式(1)变换得到式(2);
[0018][0019]
式中:ψ为综合阀位,%;k1为调节级压力与主蒸汽流量的线性系数,通过试验获取;p
10
为基准工况调节级压力,mpa;p
11
为变工况调节级压力,mpa;
[0020]
当主蒸汽压力改变后,为维持发电机功率不变,综合阀位会发生改变,进而改变主蒸汽流量,对式(2)进一步化简得到式(3);
[0021]
δg1=k2δψp
01
ꢀꢀꢀꢀꢀꢀꢀꢀꢀꢀꢀꢀꢀꢀꢀꢀꢀꢀꢀꢀꢀꢀꢀꢀꢀꢀꢀ
(3)
[0022]
式中δg1:主蒸汽流量变化量,t/h;δψ:综合阀位变化量,%;p
01
:变工况主蒸汽压力,mpa;k2:线性系数,由运行数据计算得到。
[0023]
所述变化后高压缸效率计算方法如下:
[0024]
针对试验机组进行现场试验,得出综合阀位与高压缸效率之间的关系曲线,拟合得到高压缸效率的计算公式:
[0025]
η
gyg
=aψ+b
ꢀꢀꢀꢀꢀꢀꢀꢀꢀꢀꢀꢀꢀ
(4)
[0026]
式中η
gyg
:高压缸效率,%;ψ:综合阀位,%;a、b为线性系数,由现场试验拟合关系曲线得到。
[0027]
所述给水泵有效功率计算方法如下:
[0028]
首先计算得到给水泵出口压力,主蒸汽压力改变之后,利用给水管道压降,以基准工况给水泵出口压力加上工况改变后的给水压降得出变工况给水泵出口压力;给水管道的压降与给水流量近似呈正比关系,计算公式如下:
[0029][0030]
式中下标1:变工况,下标0:基准工况,δp:给水压降,mpa;d
gs
:给水流量,t/h;k
gs
:压降系数,通过试验获取;
[0031]
给水泵扬程计算公式如式(6):
[0032][0033]
给水泵有效功率计算公式如式(7):
[0034][0035]
给水泵效率计算公式如式(8):
[0036][0037]
小汽轮机输出功率计算公式如式(9):
[0038][0039]
小汽轮机进汽量计算公式如式(10):
[0040][0041]
泵组效率计算公式如式(11):
[0042]
η
bz
=η
xj
·
η
sb
·
η
lzq
ꢀꢀꢀꢀꢀꢀꢀꢀꢀꢀꢀꢀꢀꢀꢀꢀꢀꢀꢀꢀꢀꢀꢀ
(11)
[0043]
式(6)至式(11)中,h:给水泵扬程,m;p
jk
、p
ck
:给水泵进、出口压力,mpa;ρ:给水泵平均密度,kg/m3;v
jk
、v
ck
:给水泵进、出口流速,m/s;g:重力加速度,取9.81m/s2;δz:给水泵进出口高度差,m;d
gs
:给水流量,t/h;η
sb
:给水泵效率,%;η
lzq
:联轴器效率,%;η
xj
:小汽轮机效率,%;η
bz
:泵组效率,%;pe:给水泵有效功率,kw;p
xj
:小汽轮机输出功率,kw;δh
sb
:给水泵焓升,kj/kwh;δh
xj
:小汽轮机理想焓降,kj/kwh;d
xj
:小汽轮机进汽量,t/h。
[0044]
所述新的抽气压力计算方法如下:
[0045]
对于中间各级组,在计算抽汽压力时,参照《asme ptc6-2004汽轮机性能试验规程》中一类修正的处理方法,通过计算抽汽口后的蒸汽流量,再间接计算得到新的抽汽压力,计算公式如式(12);
[0046][0047]
式中c
jz
:流量系数,d
jz
:抽汽口后的蒸汽流量,t/h;p
cq
:新的抽汽压力,mpa,v
cq
:抽汽比容,m3/kg;
[0048]
级段压力变工况计算采用迭代方法进行,步骤如下:首先假设抽汽压力,然后根据变化后高压缸效率与抽汽蒸汽参数,求出抽汽焓、比容与流量,再对加热器进行热平衡计算,得到抽汽流量和抽汽口后蒸汽流量,然后利用式(12)计算得到新的抽汽压力,将新的抽汽压力与假设的抽汽压力进行对比,直至假设抽气压力与新的抽汽压力之差的绝对值除以假设的抽汽压力得到的结果小于1%,便结束迭代计算。
[0049]
所述步骤3中根据变工况后计算出来的抽汽压力,根据汽轮机性能试验标准计算低压缸排汽量、加热器出口水温、各级抽汽流量、主蒸汽吸热量、再热蒸汽吸热量与凝汽器放热量,从而得到新的发电机功率,这一计算过程中为提高计算模型的准确性,模型中的其他参数设置如下:
[0050]
(1)抽汽压损、加热器端差取基准工况值,变工况计算时与基准工况值相近,假定
参数值不变;
[0051]
(2)凝汽器的过冷度取基准工况值,变工况计算时保持不变;
[0052]
(3)再热器压损取基准工况值,变工况计算时保持不变;
[0053]
(4)由于中调阀维持全开,中压缸效率、低压缸elep效率取基准工况值,变工况计算时与基准工况值相近,假定参数值不变;
[0054]
(5)低压缸排汽容积损失由变工况下的低压缸排汽流量计算得到;
[0055]
(6)主蒸汽温度、再热蒸汽温度、排汽压力取基准工况值,变工况计算时保持不变。
[0056]
所述步骤5中当需要计算某个负荷点的最优运行主蒸汽压力时,采用“穷举法”,在步骤1中以0.5mpa为步长改变主蒸汽压力,遍历所有压力区间,选择其中对应热耗率最小的主蒸汽压力作为该负荷点的最优主蒸汽压力。
[0057]
本发明有益效果:
[0058]
本发明提供一种变工况下汽轮机组主蒸汽压力寻优计算方法,可以准确计算出汽轮机组对应负荷下的最优主蒸汽压力,无需进行多次重复的热力性能试验,减少相对于传统滑压优化试验过程中边界参数变化、运行方式改变、系统隔离等因素的影响,为后续的汽轮机组滑压优化提供新的思路。
附图说明
[0059]
图1为综合阀位与高缸效率的关系曲线图。
[0060]
图2为给水压降与主给水流量的关系曲线图。
[0061]
其中,δp1/δp0:变工况给水压降/基准工况给水压降,mpa;d
gs1
/d
gs0
:变工况给水流量/基准工况给水流量。
[0062]
图3为最优主蒸汽压力变工况计算流程图。
具体实施方式
[0063]
以下结合实施例对本发明的具体实施方式作进一步详细说明。
[0064]
实施例
[0065]
一种变工况下汽轮机组主蒸汽压力寻优计算方法,包括以下步骤:
[0066]
步骤1:在机组确定负荷下,固定主蒸汽压力,进行汽轮机热力性能试验,按照试验标准,采集系统参数并计算汽轮机热耗率,确定发电机功率,以此次试验作为基准工况,然后改变主蒸汽压力。
[0067]
步骤2:改变主蒸汽压力后假定综合阀位变化量,根据改变后的综合阀位变化量计算变化后主蒸汽流量、变化后高压缸效率、给水泵耗功与新的抽汽压力。
[0068]
步骤3:根据变工况后计算出来的抽汽压力,计算低压缸排汽量、加热器出口水温、各级抽汽流量、主蒸汽吸热量、再热蒸汽吸热量与凝汽器放热量,从而得到新的发电机功率。
[0069]
步骤4:将步骤3中得到的发电机功率与步骤1中的基准工况的发电机功率进行比较,如果二者偏差绝对值除以基准工况的发电机功率的结果小于0.1%,即认为计算结束转到步骤5,否则返回到步骤2。
[0070]
步骤5:将变工况计算得出的不同热耗率相互进行比较,热耗率最小工况下的主蒸
汽压力即为最优主蒸汽压力。
[0071]
其中,步骤2中变化后主蒸汽流量、变化后高压缸效率、变化后给水泵耗功与新的抽汽压力指标的计算由改变后的主蒸汽压力大小与假定的综合阀位进行计算得来,
[0072]
(1)变化后主蒸汽流量计算方法如下:
[0073]
根据弗留格尔公式:
[0074][0075]
式中:g0为基准工况主蒸汽流量,t/h;g1为变工况主蒸汽流量,t/h;p
00
为基准工况主蒸汽压力,mpa;p
01
为变工况主蒸汽压力,mpa;t
00
为基准工况调节级后温度,k;t
01
为变工况调节级后温度,k;a0为基准工况汽轮机进汽面积,m2;a1为变工况汽轮机进汽面积,m2。
[0076]
对于高压缸来说,其进汽面积随高调门的开度变化而变化,而高调门开度则由综合阀位指令通过阀门管理函数生成,故可用综合阀位表征高压缸的进汽面积。
[0077]
由于主蒸汽流量与调节级压力呈正比关系,可用调节级压力代表主蒸汽流量,同时忽略温度的变化,对式(1)稍作变换得到式(2)。
[0078][0079]
式中:ψ为综合阀位,%;k1为调节级压力与主蒸汽流量的线性系数,通过试验获取;p
10
为基准工况调节级压力,mpa;p
11
为变工况调节级压力,mpa。
[0080]
当主蒸汽压力改变后,为维持发电机功率不变,综合阀位会发生改变,进而改变主蒸汽流量,对式(2)进一步化简得到式(3)。
[0081]
δg1=k2δψp
01
ꢀꢀꢀꢀꢀꢀꢀꢀꢀꢀꢀꢀꢀꢀꢀꢀꢀꢀꢀꢀꢀꢀꢀꢀꢀꢀꢀ
(3)
[0082]
式中δg1:主蒸汽流量变化量,t/h,δψ:综合阀位变化量,%,p
01
:变工况主蒸汽压力,mpa,k2:线性系数,可由运行数据计算得到。
[0083]
(2)变化后高压缸效率计算方法如下:
[0084]
针对试验机组进行现场试验,可得出综合阀位与高压缸效率之间的关系曲线,拟合得到公式:
[0085]
η
gyg
=aψ+b
ꢀꢀꢀꢀꢀꢀꢀꢀꢀꢀꢀ
(4)
[0086]
式中η
gyg
:高压缸效率,%;ψ:综合阀位,%;a、b:线性系数,由现场试验拟合关系曲线得到。
[0087]
需要注意的是,汽轮机高压缸效率与高调门的重叠度有关,若高调门的重叠度发生了变化,相应的函数关系也将发生变化。
[0088]
(3)计算给水泵耗功需要提前计算得到给水泵出口压力。主蒸汽压力改变之后,可利用给水管道压降,以基准工况给水泵出口压力加上工况改变后的给水压降得出变工况给水泵出口压力。给水管道的压降与给水流量近似呈正比关系,计算公式如下:
[0089][0090]
式中下标1:变工况,下标0:基准工况,δp:给水压降,mpa;d
gs
:给水流量,t/h。k
gs
:压降系数,通过试验获取。
[0091]
给水泵耗功(即给水泵有效功率)计算方法如下:
[0092]
给水泵扬程可由式(6)计算:
[0093][0094]
给水泵有效功率计算公式如式(7):
[0095][0096]
给水泵效率计算公式如式(8):
[0097][0098]
小汽轮机输出功率计算公式如式(9):
[0099][0100]
小汽轮机进汽量计算公式如式(10):
[0101][0102]
泵组效率计算公式如式(11):
[0103]
η
bz
=η
xj
·
η
sb
·
η
lzq
ꢀꢀꢀꢀꢀꢀꢀꢀꢀꢀꢀꢀꢀꢀꢀꢀꢀꢀꢀꢀꢀꢀꢀ
(11)
[0104]
式(6)至式(11)中,h:给水泵扬程,m;p
jk
、p
ck
:给水泵进、出口压力,mpa;ρ:给水泵平均密度,kg/m3;v
jk
、v
ck
:给水泵进、出口流速,m/s;g:重力加速度,取9.81m/s2;δz:给水泵进出口高度差,m;d
gs
:给水流量,t/h;η
sb
:给水泵效率,%;η
lzq
:联轴器效率,%;η
xj
:小汽轮机效率,%;η
bz
:泵组效率,%;pe:给水泵有效功率,kw;p
xj
:小汽轮机输出功率,kw;δh
sb
:给水泵焓升,kj/kwh;δh
xj
:小汽轮机理想焓降,kj/kwh;d
xj
:小汽轮机进口流量(即小汽轮机进汽量),t/h。
[0105]
(4)级段压力变工况(即新的抽气压力)计算方法如下:
[0106]
对于中间各级组,在计算抽汽压力时,参照《asme ptc6-2004汽轮机性能试验规程》中关于一类修正的处理方法,即通过计算抽汽口后的蒸汽流量,再间接计算得到新的抽汽压力,计算公式如式(12)。
[0107][0108]
式中c
jz
:流量系数,d
jz
:抽汽口后的蒸汽流量,t/h;p
cq
:新的抽汽压力,mpa,v
cq
:抽汽比容,m3/kg。
[0109]cjz
实际上表征了汽轮机各级段的通流面积,其在各个负荷段几乎不变,可根据运行数据预先得到各级段的c
jz
。
[0110]
级段压力变工况计算采用迭代方法进行,步骤如下:首先假设抽汽压力,然后根据变化后高压缸效率与抽汽蒸汽参数(抽汽压力、抽汽温度),求出抽汽焓、比容与流量,再对加热器进行热平衡计算,得到抽汽流量和抽汽口后蒸汽流量,然后利用式(12)计算得到新的抽汽压力,将新的抽汽压力与假设的抽汽压力进行对比,直至假设抽气压力与新的抽汽压力之差的绝对值除以假设的抽汽压力得到的结果小于1%,便结束迭代计算。
[0111]
其中,步骤3中根据变工况后计算出来的抽汽压力,可根据汽轮机性能试验标准计算低压缸排汽量、加热器出口水温、各级抽汽流量、主蒸汽吸热量、再热蒸汽吸热量与凝汽器放热量,从而得到新的发电机功率,这一计算过程中为提高计算模型的准确性,模型中的其他参数设置如下:
[0112]
(1)抽汽压损、加热器端差取基准工况值,变工况计算时与基准工况值近似,假定参数值不变;
[0113]
(2)凝汽器的过冷度取基准工况值,变工况计算时保持不变;
[0114]
(3)再热器压损取基准工况值,变工况计算时保持不变;
[0115]
(4)由于中调阀维持全开,中压缸效率、低压缸elep效率取基准工况值,变工况计算时与基准工况值近似,假定参数值不变;
[0116]
(5)低压缸排汽容积损失由变工况下的低压缸排汽流量计算得到;
[0117]
(6)主蒸汽温度、再热蒸汽温度、排汽压力取基准工况值,变工况计算时保持不变。
[0118]
其中,步骤5中当需要计算某个负荷点的最优运行主蒸汽压力时,采用“穷举法”,在步骤1中以0.5mpa为步长改变主蒸汽压力,遍历所有压力区间,选择其中对应热耗率最小的主蒸汽压力作为该负荷点的最优主蒸汽压力。
[0119]
应用例
[0120]
以实施例所述变工况下汽轮机组主蒸汽压力寻优计算方法,进行如下实验:
[0121]
步骤1:以某超临界600mw机组为例,采用该机组投产后不同发电机功率下得到试验工况作为基准工况。然后选择要进行优化的工况,确定发电机功率,然后改变主蒸汽压力,在原工况压力基础上以0.5mpa为步长,增加或减少3mpa,共进行6次计算。
[0122]
步骤2:改变主蒸汽压力后,假设综合阀位变化量,根据式(3)求出变化后主蒸汽流量;采用现场试验的方法,获取综合阀位与高压缸效率的变化关系如图1所示。拟合得到综合阀位与高压缸效率的函数关系为式(13),根据关系式求出变化后的高压缸效率。
[0123]
η
gyg
=0.2162ψ+69.5
ꢀꢀꢀꢀꢀꢀꢀꢀꢀꢀꢀꢀꢀꢀꢀꢀꢀꢀꢀꢀꢀꢀ
(13)
[0124]
式中η
gyg
:高压缸效率,%;ψ:综合阀位,%;
[0125]
根据机组运行数据得出该机组的给水压降与主给水流量关系曲线如图2所示,由图可求得该机组的压降系数k
gs
为1.139。再根据压降计算公式计算出给水泵的出口压力,各负荷下的给水流量和锅炉压降如表1所示,进一步根据式(6)至式(11)求出给水泵耗功、小汽轮机进汽量。小汽轮机对应的抽汽压力由接下来的级段压力变工况计算得出。
[0126]
表1给水流量与给水压降关系
[0127]
给水流量/t/h17611179838704531给水压降/mpa3.011.851.20.980.67
[0128]
级段压力变工况计算采用迭代方法进行,步骤如下:首先假设抽汽压力,然后根据高压缸效率与抽汽蒸汽参数,求出抽汽焓、比容与流量,再对加热器进行热平衡计算,得到抽汽流量和抽汽口后蒸汽流量,然后利用式(12)计算得到新的抽汽压力,将新的抽汽压力与假设的抽汽压力进行对比,直至假设压力与新的抽汽压力之差的绝对值除以假设的抽汽压力得到的结果小于1%,便结束迭代计算得到变工况下的新抽汽压力。
[0129]
步骤3:根据变工况后计算出来的抽汽压力,计算低压缸排汽量、加热器出口水温、各段抽汽流量、主蒸汽吸热量、再热蒸汽吸热量与凝汽器放热量,从而得到新的发电机功
率。
[0130]
步骤4:将新的发电机功率与原发电机功率对比,当二者偏差绝对值除以基准工况的发电机功率的结果小于0.1%时,即认为计算结束。否则返回到步骤2。
[0131]
步骤5:当需要计算某个负荷点的最优运行主蒸汽压力时,采用“穷举法”,以0.5mpa为步长,遍历所有压力区间,选择其中对应热耗率最小的主蒸汽压力作为该负荷点的最优主蒸汽压力。变工况计算流程如图3所示,各个工况下的计算结果如表2所示:
[0132]
表2某超临界600mw机组最优主蒸汽压力计算结果
[0133][0134]
由表2可知,该超临界机型采用变工况计算得到的最优初压相比设计值普遍要高,在滑压运行时应适当提高主蒸汽压力。