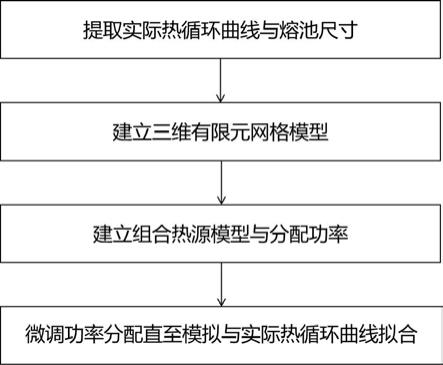
1.本发明属于电弧增材制造数值模拟热源模型技术领域,具体涉及一种电弧增材制造热源模型的建模方法。
背景技术:2.目前,电弧增材制造数值模拟常采用双椭球热源模型,该模型与焊接电弧的热源功率密度分布相符,但未考虑焊丝与基板的实际功率分配,同时焊接与增材制造所造成的熔池形貌差异较大,常常导致采用双椭球热源模型的增材制造数值模拟熔池尺寸小于实际熔池尺寸,不符合真实的熔覆过程。
3.现有专利技术中,如cn107066700b提出的一种电弧增材制造有限元建模方法,通过有限元建模方法以期准确预测增材区域生死单元的宽度和深度,其中仍使用了传统的单一双椭球热源模型,存在如上记载的熔覆过程存在误差的问题。
技术实现要素:4.本发明针对电弧增材制造数值模拟中存在的模拟熔池与实际熔池尺寸差异较大的问题,提供一种电弧增材制造热源模型的建模方法,考虑到热源实际功率分配与熔池形貌,保证了数值模拟的准确性与可靠性,同时该组合热源实现形式简易,参数调节方便,拥有很好的可控性。
5.一种电弧增材制造热源模型的建模方法,包括如下步骤:
6.步骤1:提取实际热循环曲线与熔池尺寸;
7.步骤2:建立三维有限元网格模型;
8.步骤3:建立组合热源模型与分配功率,该组合热源模型包括由双椭球热源与瞬间热源;
9.步骤4:微调功率分配直至模拟与实际热循环曲线拟合,即完成参数的调整,得到的最终的模拟熔池建模。
10.进一步地,所述步骤1中,所述实际热循环曲线为熔池与基板固定点采用测温仪器测得,并记录热循环曲线峰值。
11.进一步地,所述步骤1中,所述熔池尺寸取至熔池横截面图形,该图形以基板上顶面为分割面划分为焊丝与基板两个子图形,熔池尺寸包括熔宽w、熔深d、余高h以及两个子图形的面积。
12.进一步地,所述步骤2中,所述的三维有限元网格模型参考实际熔池尺寸参数建模,进行六面体网格划分,依据热源移动方向规划网格扫描路径和网格编号,利用生死单元法在分析步内以一定规律加载网格。
13.进一步地,所述步骤3中,组合热源由双椭球热源与瞬间热源组成,热流密度分布函数为:
[0014][0015]
式中,f1,f2为热源前后热量分布系数,满足f1+f2=2;qj为基板实际获得热量;a,b,c为热源模型几何参数;qh为焊丝实际热功率;vh为送丝速度;r为焊丝半径;δt为分析步步长;vh为每分析步激活的焊道体积,z为三维建模的z坐标轴参数。
[0016]
进一步地,所述步骤3中,热源模型的初始功率分配与熔池横截面面积有关,具体关系为:
[0017][0018]
式中,q为热源总热功率;η,ηj,ηh为热源热效率、基板热吸收效率和焊丝熔化效率,其中ηj+ηh=1;u为焊接电压;i为焊接电流;sj,sh为步骤1熔池横截面以基板上顶面为分割面划分出来的两个子图形的面积。
[0019]
进一步地,将两个子图形的轮廓曲线近似看作抛物线,两个子图形共用熔宽,由抛物线面积特征得到两个子图形的面积比值即为余高与熔宽的比值。
[0020]
进一步地,所述步骤4中,以热源热效率η和焊丝熔化效率ηh为自变量,以熔池与基板固定点模拟温度峰值为因变量,微调热源热效率η和焊丝熔化效率ηh,对比熔池与基板固定点实际温度峰值,使模拟温度峰值与实际温度峰值的相对误差小于预定误差范围。
[0021]
本发明达到的有益效果为:得到的热源功率分配接近实际功率分配,基本只需要再对功率分配进行很小的微调就能得到精确的模拟结果,本方法可获取的不同工艺下的高精度电弧增材制造组合热源模型,保证了数值模拟的准确性与可靠性,同时该组合热源实现形式简易,参数调节方便,拥有很好的可控性,对研究金属材料电弧增材制造数值模拟和工程实际应用提供技术支持。
附图说明
[0022]
图1为本发明公开的一种电弧增材制造热源模型的建模方法的具体实施方式的流程图。
[0023]
图2为本发明实施例中焊道熔池横截面轮廓示意图。
[0024]
图3为本发明实施例中焊道有限元模型的网格划分示意图。
[0025]
图4为本发明实施例中作用于焊丝的瞬间热源模型示意图。
[0026]
图5为本发明实施例中作用于基板的双椭球热源模型示意图。
[0027]
图6为本发明实施例中模拟熔池与实际熔池尺寸对比图。
具体实施方式
[0028]
下面结合说明书附图对本发明的技术方案做进一步的详细说明。
[0029]
在本次实例中,增材制造有限元模拟软件选用abaqus,热源模型使用fortran语言进行编写并以子程序形式加载入模型,为提高建模效率采用python语言对该模型进行二次开发,材料热物理性能参数可参考相关文献或者通过jmatpro软件计算获取。
[0030]
如图1所示,本实施例提供一种电弧增材制造热源模型的建模方法,包括如下步骤:
[0031]
步骤1:提取实际热循环曲线与熔池尺寸:
[0032]
步骤11:确定增材制造工艺,使用电弧tig焊以er49-1焊丝在eh36钢板表面进行堆焊实验,焊丝直径1.2mm,基板尺寸200mm*200mm*20mm,堆积电流为140a,堆积速度为3mm/s,送丝速度为140cm/min。采用红外线、热电偶等测温仪器提取熔池和基板上固定点的热循环曲线及峰值。
[0033]
步骤12:如图2所示,提取第一层熔池横截面图形,以基板上顶面为分割面划分熔池图形为焊丝与基板两个子图形,记录两个子图形尺寸,因两个子图形轮廓曲线近似抛物线,故两个子图形面积之比即为余高h与熔深d之比。熔池宽度6.5mm,熔深1.3mm,余高2.1mm。
[0034]
步骤2:建立三维有限元网格模型:
[0035]
步骤21:参考第一层焊道实际尺寸在三维软件creo中进行几何建模并保存为stp文件,以部件形式导入至abaqus有限元分析软件。
[0036]
步骤22:编辑材料热物理性能参数。通过jmatpro软件计算出材料的热物理性能参数,规范单位后导入至模型中。
[0037]
步骤23:对三维模型进行六面体网格划分,焊缝及附近区域网格近似为1mm,基板边缘区域近似为4mm,中间网格以1∶2形式过渡,如图3所示。对焊缝区域以热源移动路径为扫描方向划分网格,使焊缝网格编号以一定规律排列。
[0038]
步骤24:设置相互作用。通过python语言进行二次开发,采用生死单元法于每一分析步加载固定编号的网格。环境温度取20℃,热辐射系数取0.2,对流换热系数设为分段函数:
[0039][0040]
步骤25:设置载荷。针对两种热源分别设置载荷,作用于基板的热源采用fortran语言进行编写并以子程序形式加载入模型,作用于焊丝的热源以对每一分析步出现的网格设置热通量的形式加载入模型。
[0041]
步骤3:组合热源模型建立与功率分配:
[0042]
组合热源由作用于基板的双椭球热源与作用于焊丝的瞬间热源组成。
[0043]
步骤31:首先建立如图4所示的作用于基板的双椭球热源模型:
[0044][0045]
式中,qj是双椭球热源前后热流密度分布函数;f1,f2为热源前后热量分布系数,满
足f1+f2=2,取f1=0.6,f2=1.4;qj为基板实际获得热量;a,b,c为热源模型几何参数,参考熔池实际形貌取值,取a1=3.5,a2=8,b=3.5,c=1.3。
[0046]
步骤32:其次建立如图5所示的作用于焊丝的瞬间热源模型,该模型尺寸由每分析步内生死单元法加载出的焊道尺寸决定:
[0047][0048]
式中,qh是瞬间热源热流密度分布函数;qh为焊丝实际热功率;vh为送丝速度;r为焊丝半径;δt为分析步步长;vh为每分析步激活的焊道体积。因在单层多道和多层多道中,焊道的形貌复杂且互不相同,故舍弃移动热源模型改用瞬间热源模型对每一分析步的载荷加载热通量,结合python语言二次开发便于随时修改。
[0049]
步骤33:最后对焊丝与基板的实际功率进行分配,焊丝与基板的实际功率分配满足:
[0050][0051]
式中,q为热源总热功率;η,ηj,ηh为热源热效率,基板热吸收效率和焊丝熔化效率,其中ηj+ηh=1;u为焊接电压,i为焊接电流;sj,sh为步骤1熔池横截面以基板上顶面为分割面划分出来的两个子图形的面积,d为熔深,余h为余高,将两个子图形的轮廓曲线近似看作抛物线,两个子图形共用熔宽,由抛物线面积特征可得两个子图形的面积比值即为余高与熔宽的比值。
[0052]
步骤4:微调焊丝与基板的实际功率分配:
[0053]
步骤41:获得模拟结果的温度场,对比熔池与基板固定点的模拟与实际温度峰值,对比模拟与实际熔池横截面尺寸。
[0054]
步骤42:以热源热效率η和焊丝熔化效率ηh为自变量,以熔池与基板固定点模拟温度峰值为因变量,微调热源热效率η和焊丝熔化效率ηh,使模拟温度峰值与实际温度峰值的相对误差小于预定误差范围,同时最终得到的模拟熔池与实际熔池尺寸相近,如图5所示。
[0055]
综上所述,本实施例提供一种电弧增材制造热源模型的建模方法,通过上述的实施步骤,本发明所提供的组合热源考虑到热源实际功率分配与熔池形貌,保证了数值模拟的准确性与可靠性,同时该组合热源实现形式简易,参数调节方便,拥有很好的可控性。
[0056]
以上所述仅为本发明的较佳实施方式,本发明的保护范围并不以上述实施方式为限,但凡本领域普通技术人员根据本发明所揭示内容所作的等效修饰或变化,皆应纳入权利要求书中记载的保护范围内。