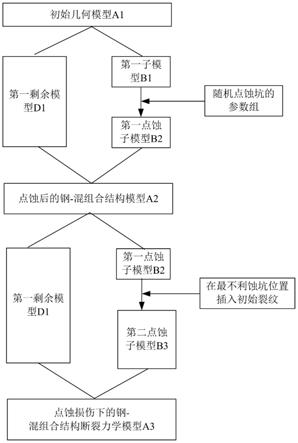
1.本发明涉及桥梁工程技术领域,特别是一种随机点蚀损伤下钢-混组合结构的寿命计算方法。
背景技术:2.近年来,钢-混组合结构(钢-混凝土组合结构)在国内外得到迅速发展,广泛运用于桥梁、民用建筑领域,取得了显著的经济效益。随着时间的推移,由于混凝土桥面板开裂,泄水管损坏等原因,在此基础上钢结构会受到雨水、温度、湿度等多重因素影响,从而产生腐蚀效应,而腐蚀导致的点蚀坑引起的应力集中严重危害结构的耐久性,受到腐蚀影响下钢结构的疲劳性能发生了较大的变化,受力模式较为复杂,对腐蚀损伤下疲劳性能的有效评估方法尤为重要。
3.目前点蚀对船舶、海洋结构构件等的不利影响现在得到广泛的关注,但对于钢结构桥梁腐蚀的方面尚不完善,由于钢-混组合结构的钢梁中材料的不均匀性和周围环境的复杂影响,点蚀的产生位置具有明显的不确定性。同时受到腐蚀影响疲劳破坏可能不发生在疲劳易损伤细节上,而是点蚀位置由于应力集中产生疲劳裂纹发生破坏,组合结构桥产生了新的疲劳易损细节,其点蚀损伤下疲劳失效模式发生了迁移。且目前的研究通常只针对焊接位置的缺陷引起的结构疲劳破坏,而腐蚀损伤会大大减少结构的疲劳寿命。
4.随着桥梁结构健康监测、人工检测及无损检测等其他现代化检测手段的发展,对钢-混组合结构的钢梁腐蚀形态能有较好的识别,同时基于该检测信息,对其腐蚀损伤下的疲劳寿命评估显得尤为重要。就能够广泛的钢-混组合结构性能评估而言,通过建立子模型,考虑相应因素下结构应力集中部分插入随机分布的点蚀坑,来研究点蚀下钢-混组合结构的疲劳性能具有现实意义和工程应用价值。(王春生,张静雯,段兰,谭晨欣.长寿命高性能耐候钢桥研究进展与工程应用[j].交通运输工程学报)
[0005]
公开号为cn113378432a的中国专利公开了一种基于扩展有限元的rpv管点蚀坑上裂纹扩展数值模拟方法,通过考虑点蚀样貌和尺寸对裂纹位置萌生的影响,且该专利采用的裂纹应力为固定均匀的应拉力。而现实中,点蚀区的位置不固定,且桥梁结构所面临的较为常见且重要的疲劳问题多为车辆荷载或风荷载等引起,其特点为应拉力的大小不确定且循环往复,直至造成结构的破坏。
技术实现要素:[0006]
本发明所要解决的技术问题是,针对现有技术不足,提供一种随机点蚀损伤下钢-混组合结构的寿命计算方法,在钢-混组合结构模型中随机生成点蚀,结合断裂力学方法进行疲劳裂纹扩展分析并计算剩余疲劳寿命,以对点蚀损伤的钢桥结构疲劳性能进行评估。
[0007]
为解决上述技术问题,本发明所采用的技术方案是:一种随机点蚀损伤下钢-混组合结构的寿命计算方法,包括以下步骤:
[0008]
s1,在有限元软件中建立钢-混组合结构的初始几何模型,在模型中选取待点蚀区
域部分,生成随机点蚀坑的参数组并装配至所述待点蚀区域,获取点蚀后的钢-混组合结构模型;生成随机点蚀坑的参数组的方法包括:
[0009]
s101,基于实际点蚀统计数据,获取点蚀坑的半径范围及半径所服从的第一分布函数,点蚀坑的深度范围以及深度所服从的第二分布函数;
[0010]
s102,每一次随机生成一个服从所述第一分布函数的随机半径数据,并判断所述随机半径数据是否在点蚀坑的半径范围内;每一次随机生成一个服从所述第一分布函数的随机深度数据,并判断所述随机深度数据是否在点蚀坑的深度范围内;每一次随机生成一个点蚀坐标;
[0011]
s103,重复步骤s102,直至获取n个在半径范围内的随机半径数据,以及n个在深度范围内的随机深度数据;n个点蚀坐标;
[0012]
s104,随机选取1个点蚀的坐标、1个在半径范围内的随机半径数据以及1个在深度范围内的随机深度数据,形成1个随机点蚀坑的参数组;获取n个随机点蚀坑的参数组;
[0013]
s2,对点蚀后的钢-混组合结构模型进行静力计算,得到应力最大的最不利蚀坑位置,在所述最不利点蚀坑中插入初始裂纹,得到点蚀损伤下的钢-混组合结构断裂力学模型;
[0014]
s3,进行点蚀坑内的初始裂纹应力强度因子与疲劳裂纹扩展参数的计算,进行疲劳裂纹扩展;
[0015]
s4,获取每次疲劳裂纹扩展对应的疲劳作用次数,累加得到随机点蚀损伤下钢-混组合结构剩余疲劳寿命值。
[0016]
上述方案中,n可根据材料的特点以及实际场景进行设定。所述实际点蚀统计数据,可根据试验或者实测获取,试验方法可参考“任松波.点蚀坑演化过程及其对锈蚀钢材疲劳性能影响研究[d].西安建筑科技大学,2016.”中记录的方法,实测方法可参考“代菲.热铆残余应力下铆接构件疲劳性能的点蚀劣化效应[d].西南交通大学,2020.”中记录的方法。
[0017]
具体地,步骤s1中,将随机点蚀坑的参数组装配置所述待点蚀区域的实现方式包括:将所述初始几何模型切分为第一剩余模型与第一子模型,将所述待点蚀区域对应所述第一子模型,基于所述随机点蚀坑的参数组,进行参数化建模并生成几何点蚀体,将所述几何点蚀体与所述第一子模型进行差集布尔运算,得到第一点蚀子模型,将所述第一点蚀子模型与所述第一剩余模型组合为点蚀后的钢-混组合结构模型。
[0018]
具体地,步骤s2的具体实现方式包括:对点蚀后的钢-混组合结构模型进行静力计算,获取整个所述点蚀后的钢-混组合结构模型的应力最大的最不利蚀坑位置,并在最不利点蚀坑位置插入初始裂纹,形成第二点蚀子模型,将所述第二点蚀子模型重新划分网格后与所述第一剩余模型合并,得到点蚀损伤下的钢-混组合结构断裂力学模型。
[0019]
具体地,所述初始裂纹的插入方法包括:采用franc 3d软件,导入第一点蚀子模型,选取半椭圆形的初始裂纹,设定所述半椭圆形的长半轴长度、短半轴长度以及尖端的尺寸后,进行网格划分,在所述初始裂纹的尖端生成两个单元环,分别为15节点奇异楔形单元的内环以及20节点的六面体单元外环。
[0020]
具体地,步骤s3的具体实现方式包括:
[0021]
s301,由公式计算张开型裂纹的应力强度因子值ki、滑开型裂纹的应力强度因子值k
ii
与撕开型裂纹的应力强度因子值k
iii
,g为剪切弹性模量,r及θ为裂纹尖端局部柱坐标系中的两个坐标分量,u,v,ω分别为裂纹尖端任一点的径向位移、法向位移和切向位移;
[0022]
s302,设定第一疲劳裂纹扩展速率参数m以及裂纹前端中心点的扩展步长δa
median
,根据公式计算裂纹前端其他点的扩展步长δai,δk
eq,i
为裂纹尖端点的有效应力强度因子幅值,其计算公式为为裂纹尖端点的有效应力强度因子幅值,其计算公式为为裂纹尖端中心点的有效应力强度因子幅值;v
*
为材料的泊松比;
[0023]
由公式计算裂纹尖端点扩展的角度θi,i为扩展步数,i=1,2,
…
,t,t为裂纹扩展到穿透底板或形成宏观可见的裂纹为止的扩展步数;
[0024]
s303,设定疲劳荷载比r,基于扩展步长δai、裂纹尖端点扩展的角度θi,在franc3d中对所述点蚀损伤下的钢-混组合结构断裂力学模型进行疲劳裂纹的扩展。
[0025]
具体地,步骤s4的具体实现方式包括:设定第二疲劳裂纹扩展速率参数c,由公式计算点蚀损伤下钢-混组合结构的剩余疲劳寿命ni,同时得到疲劳裂纹的最终扩展形态,给定n0=0。
[0026]
与现有技术相比,本发明所具有的有益效果为:本发明通过在原始几何模型中选取待点蚀区域,并随机生成符合要求的点蚀参数组,以尽可能的模拟实际状况,然后将该参数组进行参数化建模,以差布尔运算的方法形成点蚀后的钢-混组合结构模型,基于所述点蚀后的钢-混组合结构模型,得到应力最大的最不利蚀坑位置,在所述最不利点蚀坑中插入初始裂纹,得到点蚀损伤下的钢-混组合结构断裂力学模型,并在点蚀损伤下的钢-混组合结构断裂力学模型中进行疲劳裂纹扩展,获取每次疲劳裂纹扩展对应的疲劳作用次数,累加得到随机点蚀损伤下钢-混组合结构剩余疲劳寿命值。本发明的所述第一子模型与第一点蚀子模型,结构相同,节约了划分网格的时间,提高了计算效率。
附图说明
[0027]
图1为本发明一实施例的建模方法流程图。
[0028]
图2为本发明一实施例的初始几何模型以及第一子模型的示意图。
[0029]
图3为本发明一实施例的第一点蚀子模型参数化建模后网格划分的立面图。
[0030]
图4为图3中第一点蚀子模型参数化建模后网格划分的俯视图。
[0031]
图5为本发明一实施例的第二点蚀子模型及其初始裂纹的俯视图。
[0032]
图6为图5中初始裂纹的俯视图。
[0033]
图7为图5中初始裂纹的立面图。
[0034]
图8为本发明一实施例的第二点蚀子模型的疲劳裂纹的扩展形态立面图。
[0035]
图9为本发明一实施例的第二点蚀子模型的疲劳裂纹的扩展形态侧视图。
[0036]
图10为本发明一实施例的第二点蚀子模型的剩余疲劳寿命-裂纹深度曲线。
[0037]
其中,a1为初始几何模型,b1为第一子模型。
具体实施方式
[0038]
本发明一实施例的随机点蚀损伤下钢-混组合结构的寿命计算方法包括:
[0039]
如图2所示,在abaqus软件中建立钢-混组合结构的初始几何模型a1,由混凝土板、栓钉连接件及其下方的钢梁组成,钢梁总长度为3200mm,混凝土板长度为3000mm。其中混凝土板宽、厚分别为300mm及80mm,工字钢梁板厚为10mm,顶板及底板宽度分别为120mm和160mm,腹板高150mm。在模型中模拟跨中底板腐蚀的情况,划分出待点蚀区域,将所述初始几何模型a1切分为第一剩余模型d1与所述待点蚀区域对应的第一子模型b1。同时生成随机点蚀坑的参数组:
[0040]
s101,基于试验,试验的方法参考“任松波.点蚀坑演化过程及其对锈蚀钢材疲劳性能影响研究[d].西安建筑科技大学,2016.”,模拟钢-混组合结构在近似大气腐蚀环境下的工作状态,以跨中底板腐蚀为例,获取点蚀坑的半径r平均值为5mm,半径r的范围为1.5mm~6mm,且半径r服从正态分布;获取点蚀坑的深度h的平均值为3mm,深度h的范围为1.5mm~6mm,且深度h服从正态分布;
[0041]
s102,设定点蚀坑数量n=50;使用python语句,以5mm为均值,0.5为标准差,使用函数random.normalvariate(5,0.5):每一次随机生成一个服从正态分布的随机半径数据,并判断所述随机半径数据是否在点蚀坑的半径范围1.5mm~6mm内,当超出范围则剔除该值,重新生成随机半径数据,若在范围内,保留该值;同时,每一次随机生成一个服从正态分布的随机深度数据,并判断所述随机深度数据是否在点蚀坑的深度范围1.5mm~6mm内,当超出范围则剔除该值,重新生成随机深度数据,若在范围内,保留该值;每一次随机生成一个点蚀坐标,并通过两个点蚀坐标之间的距离与半径之和判定是否重合及相交,如果重合或相交则剔除数据,重新生成随机点蚀坐标,若不重也不相交,保留该值;
[0042]
s103,重复步骤s102,直至获取50个在半径范围内的随机半径数据,以及50个在深度范围内的随机深度数据和50个点蚀坐标;
[0043]
s104,随机选取1个点蚀的坐标、1个在半径范围内的随机半径数据以及1个在深度范围内的随机深度数据,形成1个随机点蚀坑的参数组;获取50个随机点蚀坑的参数组。
[0044]
如图3与图4所示,在abaqus软件中,将所述点蚀坑的参数组拉伸成圆柱体,与所述
第一子模型b1装配后进行差集布尔运算,得到第一点蚀子模型b2,将所述第一点蚀子模型b2与所述第一剩余模型d1组合为点蚀后的钢-混组合结构模型a2。
[0045]
对点蚀后的钢-混组合结构模型a2进行静力计算,混凝土材料为c50,钢材为q235b,定义模型材料参数、边界条件以及加载位置,栓钉连接件可通过实体单元或弹簧单元模拟,为简化模型也可通过在混凝土与钢梁之间设置绑定约束进行简化模拟。
[0046]
获取整个所述点蚀后的钢-混组合结构模型a2的应力最大的最不利蚀坑位置,通过franc 3d软件将带有最不利蚀坑位置的所述第一点蚀子模型b2切割出来,如图5所示,在所述最不利点蚀坑位置插入初始裂纹。如图6与图7所示,所述初始裂纹选取半椭圆形,设定所述半椭圆形的长半轴长度为0.5和短半轴长度为0.2,在所述初始裂纹的尖端生成两个单元环,分别为15节点奇异楔形单元的内环以及20节点的六面体单元外环,然后进行网格划分,形成第二点蚀子模型b3。
[0047]
将所述第二点蚀子模型b3重新划分网格后与所述第一剩余模型d1合并,得到点蚀损伤下的钢-混组合结构断裂力学模型a3。
[0048]
基于所述点蚀损伤下的钢-混组合结构断裂力学模型a3,进行疲劳裂纹扩展,具体方法包括:
[0049]
s301,通过m积分,由公式计算张开型裂纹的应力强度因子值ki、滑开型裂纹的应力强度因子值k
ii
与撕开型裂纹的应力强度因子值k
iii
,g为剪切弹性模量,r及θ为裂纹尖端局部柱坐标系中的两个坐标分量,u,v,ω分别为裂纹尖端任一点的径向位移、法向位移和切向位移;
[0050]
s302,以gb/t6398-2000《金属材料疲劳裂纹扩展速率试验方法》进行试验拟合数据得到第一疲劳裂纹扩展速率参数m,bs7910(2005)对于q235b钢材的推荐值是m=3,设定裂纹前端中心点的扩展步长δa
median
,根据公式计算裂纹前端其他点的扩展步长δai;
[0051]
δk
eq,i
为裂纹尖端点的有效应力强度因子幅值,其计算公式为
[0052]
为裂纹尖端中心点的有效应力强度因子幅值;
[0053]v*
为材料的泊松比;
[0054]
由公式计算裂纹尖端点扩展的角度θi;
[0055]
i为扩展步数,i=1,2,
…
,t,t为裂纹扩展到穿透底板或形成宏观可见的裂纹为止的扩展步数,t的设定可参考“fisher j w,albrecht p,yen b t,et al.fatigue strength of steel beams with welded stiffeners and attachments[j].nchrp report,1974(147).”中记录的方法;
[0056]
s303,设定疲劳荷载比r=0.2,基于扩展步长δai、裂纹尖端点扩展的角度θi,在franc 3d中对所述点蚀损伤下的钢-混组合结构断裂力学模型进行疲劳裂纹的扩展。
[0057]
以gb/t6398-2000《金属材料疲劳裂纹扩展速率试验方法》进行试验拟合数据得到第二疲劳裂纹扩展速率参数c,bs7910(2005)对于q235b钢材的推荐值是c=5.21
×
10-13
,根据paris公式a为裂纹扩展步长,n为疲劳扩展次数,可得计算点蚀损伤下钢-混组合结构的剩余疲劳寿命ni,给定n0=0。
[0058]
最终得到如图10所示的点蚀损伤下钢-混组合结构的剩余疲劳寿命ni与疲劳裂纹扩深度之间的曲线,图10中横坐标表示疲劳寿命,单位为次;纵坐标为裂纹深度,单位为mm。同时得到如图8与图9所示的疲劳裂纹的扩展形态图。