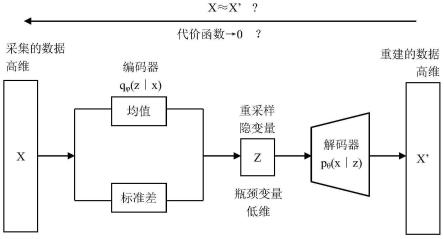
1.本发明涉及工业大数据领域,特别涉及半导体加工过程传感器数据异常检测的方法。
背景技术:2.在集成电路制造产业中现有技术的错误检测分类(fault detection classification, fdc)分析系统对加工过程传感器数据的分析均是基于统计过程控制(statisticalprocess control,spc)的方法进行管控。
3.工程师需要分机台(equipment)/腔室(chamber)/工步(step)/参数(parameter),依据其历史作业曲线,分门别类的手动进行设置目标(target)线/规格(spec)线/ 控制(control)线,同时需要设置一系列管控规则。
4.当机台、腔体进行维护维修(preventive maintenance、productive maintenance, pm)或者更换导致工况变化后,管控线需要重新设置。
5.现有技术存在的问题如下。
6.第一,需要分机台/腔室/工步/参数进行设置,不同类型逻辑规则不统一,维护管控较复杂,效率低下。
7.第二,过程传感器数据为多变量时间序列数据,按照不同加工阶段由体现出不同特点,传统spc方法难以管控。
8.因此,亟需一种更加准确智能的方法对传感器数据进行异常数据的检测。
技术实现要素:9.本发明需要解决的技术问题是:如何自动检测异常传感器数据,并能够输出汇总结果,减少人力付出。
10.为了解决以上技术问题,本发明提供一种半导体加工过程传感器数据异常检测的方法,其目的在于建立整套数据处理方法,可自动检测传感器数据异常,并输出汇总结果,为线上机台/产品管控及优化提供参考,保持产品质量稳定,同时大大减少人力付出。
11.为了达到上述目的,本发明提供了一种半导体加工过程传感器数据异常检测的方法,以实体制程为分析对象,包含:
12.s1:获取该实体制程的历史传感器数据作为历史数据;
13.s2:利用历史数据建立标准数据模型;
14.s3:将新产生的传感器数据与标准数据模型进行比对,据此,检测出异常。
15.优选地,在步骤s2中,采用神经网络算法,进行无监督学习,提高标准数据模型的泛化性能。
16.优选地,在步骤s2中,包含:
17.以采集的历史数据为输入,采用自动编码器进行降维,至低维度瓶颈变量,再对低维度瓶颈变量采用自动解码器进行升维还原输出为重建的历史数据,重建的历史数据和采
集的历史数据之间的代价函数值接近于0,则建立了标准数据模型,标准数据模型包含在代价函数值接近于0时的自动编码器中的降维函数和自动解码器中的升维函数。
18.优选地,在步骤s3中,包含:
19.对采集的新产生的传感器数据,采用标准数据模型中的降维函数进行降维,采用标准数据模型中的升维函数进行升维,计算还原后的重建的新产生的传感器数据和采集的新产生的传感器数据之间的代价函数值,代价函数值表征出数据的异常程度。
20.优选地,对采集的历史数据由编码器生成瓶颈变量的均值和标准差,再由均值和标准差进行重采样形成隐变量,再对隐变量解码放大形成重建的历史数据。
21.优选地,在进行标准数据模型无监督自主学习过程中,随机过程地增加数据的噪音。
22.优选地,所述半导体加工过程传感器数据异常检测的方法,还包含,对传感器数据进行预处理时,采用主成分分析的方法,将个数小于原始传感器数据维度的主成分维度筛选出来,将原始的高维的数据向低维的主主成分维度空间映射,获得低维的数据。
23.优选地,所述半导体加工过程传感器数据异常检测的方法,还包含,对传感器数据进行预处理时,采用动态时间规整,对两个时间序列的数据进行逐个时间点缩放,对缩放后两个时间序列趋近于相互对应,比对缩放后的时间点的数据值。
24.优选地,新产生的传感器数据成为历史数据,进行标准数据模型的测试,并与实体制程的进一步测试异常点的实际是否错误、错误情况进行比较,反馈优化标准数据模型,再进行异常点检测测试,循环优化该标准数据模型。
25.优选地,该传感器数据异常检测的方法适用于机台级别、腔室级别、工步级别、参数级别的自动异常监控。
26.与现有技术相比,本发明提供了一种半导体加工过程传感器数据异常检测的方法,以实体制程为分析对象,包含:s1:获取该实体制程的历史传感器数据作为历史数据;s2:利用历史数据建立标准数据模型;s3:将新产生的传感器数据与标准数据模型进行比对,据此,检测出异常。据此,本发明能够达到的技术效果在于,该方法适用率高,能够覆盖集成电路制造工厂的74%以上的制程;异常检测率高,可达80%以上;检测效率高,节省人力。
附图说明
27.图1展示了本发明提供的半导体加工过程传感器数据异常检测的方法的一实施例的示意图。
28.图2展示了本发明提供的半导体加工过程传感器数据异常检测的方法的又一实施例的示意图。
29.图3展示了本发明提供的半导体加工过程传感器数据异常检测的方法的再一实施例中增加的动态时间规整方法与欧式距离方法的比较示意图。
30.图4a至图4b展示了本发明提供的半导体加工过程传感器数据异常检测的方法应用在一种实体制程——刻蚀工艺的判断及结果示意图。
31.图4c至图4d展示了本发明提供的半导体加工过程不同传感器的数据。
32.图5展示了本发明提供的半导体加工过程传感器数据异常检测的方法应用在又一
种实体制程——物理气相沉积工艺的结果示意图。
33.图6展示了本发明提供的半导体加工过程传感器数据异常检测的方法应用在再一种实体制程——浅沟道隔离-化学机械抛光工艺的结果示意图。
具体实施方式
34.以下结合附图对本发明的具体实施方式进行详细说明。
35.本发明提供了一种半导体加工过程传感器数据异常检测的方法,以实体制程为分析对象,包含以下步骤。
36.s1:获取该实体制程的历史传感器数据作为历史数据。
37.s2:利用历史数据建立标准数据模型。
38.s3:将新产生的传感器数据与标准数据模型进行比对,据此,检测出异常。
39.实体制程(physical recipe)是集成电路制造工厂中的机台级别、腔室级别、工步级别、参数级别。例如,刻蚀工艺(etch)、物理气相沉积工艺(pvd)、浅沟道隔离-化学机械抛光工艺(sti-cmp)。可以记录的数据的维度包括:制程编号、模式、状态、机台型号、机台编号、晶圆编号、工步编号、起始时间、传感器编号、传感器实时数值等。
40.历史传感器数据是指在过去的某一段时间里(比如,前3个月内或前6个月内等) 所记录存储的传感器数据(包含各个维度)。
41.在步骤s2中,采用神经网络算法,进行无监督学习,提高标准数据模型的泛化性能。
42.参考图1所示,在步骤s2中,包含:以采集的历史数据为输入,采用自动编码器进行降维,至低维度瓶颈变量,再对低维度瓶颈变量采用自动解码器进行升维还原输出为重建的历史数据,重建的历史数据和采集的历史数据之间的代价函数值接近于 0,则建立了标准数据模型,标准数据模型包含在代价函数值接近于0时的自动编码器中的降维函数和自动解码器中的升维函数p
θ
(x|z)。
43.代价函数(cost function)是用来评价重建数据和采集数据之间是否近似的函数。一个具体实施例,采用均方误差来量化,误差是指重建数据与采集数据之间的差值。
44.参考图1所示,在步骤s3中,包含:对采集的新产生的传感器数据,采用标准数据模型中的降维函数进行降维,采用标准数据模型中的升维函数进行升维,计算还原后的重建的新产生的传感器数据和采集的新产生的传感器数据之间的代价函数值,代价函数值表征出数据的异常程度。
45.参考图2所示,对采集的历史数据由编码器生成瓶颈变量的均值和标准差,再由均值和标准差进行重采样(sampled)形成隐变量(latent vector),再对隐变量解码放大形成重建的历史数据。
46.在进行标准数据模型无监督自主学习过程中,随机过程地增加数据的噪音。据此,能够提高编码器的稳定性,减少过拟合。
47.半导体加工过程传感器数据异常检测的方法,还包含,对传感器数据进行预处理时,采用主成分分析的方法(pca,principal components analysis),将个数小于原始传感器数据维度的主成分维度筛选出来,将原始的高维的数据向低维的主主成分维度空间映射,获得低维的数据。例如,将原本m维度的数据,降低为k(k<m)维度的数据。利用各个数据
之间的关联性,进行分析。
48.参阅图3所示,半导体加工过程传感器数据异常检测的方法,还包含,对传感器数据进行预处理时,采用动态时间规整(dtw,dynamic time warping),对两个时间序列的数据进行逐个时间点缩放,对缩放后两个时间序列趋近于相互对应,比对缩放后的时间点的数据值。比方说,同样的刻蚀过程进行比较,第一组数据,某工步开始时间为t1,结束时间为t1+δ1,第二组数据,某工步开始时间为t2,结束时间为t2+δ2,δ1≠δ2,需要采用dtw将时刻点进行重新分配对应关系,保证对应可比性。欧式距离是基于某一维度(比如时刻点)的单位向量在两组数据中是一致的,而采用动态时间规整,则是基于某一维度的某些特定点,再进行各个数据的各个时刻点的单位向量的重新定义。
49.新产生的半导体加工过程传感器数据成为历史数据,进行标准数据模型的测试,并与实体制程的进一步测试异常点的实际是否错误、错误情况进行比较,反馈优化标准数据模型,再进行异常点检测测试,循环优化该标准数据模型。
50.该半导体加工过程传感器数据异常检测的方法适用于机台级别、腔室级别、工步级别、参数级别的自动异常监控。
51.下面来列举三个应用实例。
52.实体制程为某刻蚀工艺的案例。参阅图4a,为刻蚀工艺中芯片层次,对工步的异常度(dtw距离)进行排序。工步6(step6)最异常。图4b,针对最异常的工步 6(异常度2.5),对传感器的异常度(dtw距离)找出各个传感器异常的晶圆编号。参阅图4c所示,最异常的(异常度5.8)第var87号传感器对应最异常的晶圆编号为 lot058#08(11);参阅图4d所示,第6异常的(异常度1.35)第var130号对应最异常的晶圆编号为lot019#06。再进行数据比较,前后批次(lot)、前后晶圆(waferno.),都正常,属于单个案例(single case),例如,第var130号传感器的数据对应最异常的晶圆编号为lot019#06。
53.实体制程为某物理气相沉积工艺的案例。总采集2295件晶圆的数据。参阅图5,为晶圆的编号为一个维度,工步8、工步12、工步16为一个维度,另外传感器数据也是一个维度。如图5所示,lot097#07号晶圆工步12处发生异常度最高(达到9.92)。
54.实体制程为浅沟道隔离-化学机械抛光工艺的案例。参阅图6,是经过采用本发明提供的方法后检测到的情况,最异常的晶圆号lot096#01,最异常传感器号var19,异常度17.82。
55.针对不同的实体制程,通过本发明提供的方法,能够自动建立不同的标准数据模型,但是评价标准都统一到异常度(代价函数为其一个实施例)的评价上来,可以实时汇总分析集成电路制造工厂中所采集的半导体加工过程传感器数据,并能够及时发现其中的异常。
56.以上即为本发明所提供的半导体加工过程传感器数据异常检测的方法的具体实施例。据此,本发明能够达到的技术效果在于:第一,该方法适用率高:传感器数据异常检测的方法提供的标准数据模型应用经过多月的持续的测试——总结——优化——测试的不断循环,最终达到该方法在某集成电路制造工厂的所有制程中的覆盖率达到74%,使用的实体制程很多,如刻蚀、物理气相沉积、浅沟道隔离-化学机械抛光等;第二,异常检测率高:通过验证,对传感器数据异常检测的检出率可达80%以上;第三,大大提高检测效率,节省人力:属无监督学习,模型检测运行全自动,自动生成汇总报告。
57.上述具体实施例和附图说明仅为例示性说明本发明的技术方案及其技术效果,而非用于限制本发明。任何熟于此项技术的本领域技术人员均可在不违背本发明的技术原理及精神的情况下,在权利要求保护的范围内对上述实施例进行修改或变化,均属于本发明的权利保护范围。