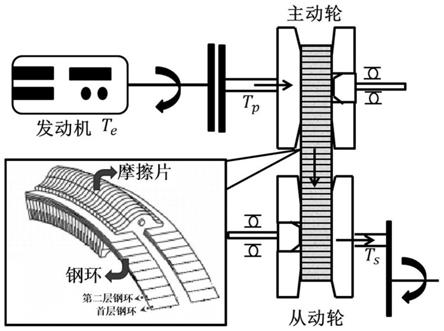
cvt钢环摩擦副磨损深度、安全裕度计算、评估方法及装置
技术领域
1.本发明涉及cvt(continuously variable transmission,金属带式无级变速器)技术领域,特别是关于一种cvt钢环摩擦副磨损深度、安全裕度计算、评估方法及装置。
背景技术:2.cvt作为汽车变速装置的核心部件,其能使变速器的动力传递持续在最优工况点,已在各类型汽车中得到广泛应用。但变速器的传动工况是复杂的多变的,期间产生的损耗不可忽视,这直接影响到cvt的传动效率及其自身寿命]。cvt钢环在热-力-液等多场耦合的作用下,摩擦片的相对运动下各层钢环接触特性、润滑状态会逐步形成具有应力、应变和温度规律分布的表面损伤。随着载荷的变化,钢环配合面之间会产生微动滑移并磨损,通过摩擦片传递导致带与带轮间的接触特性、相对运动等也随之改变,造成金属带滑移、带轮偏转、轴承蠕变同时产生噪音。因此,充分认识多场耦合作用下钢环微动现象及钢环配合面之间的润滑状态,对变速器整体应用效能的影响以及使用寿命的影响是必不可少的。
3.近年来,汽车应用效能的提升研究已日渐成熟,但微动频率及宏观参数对机械系统应用效能以及使用寿命的影响却鲜有人问津。有学者研究了690tt合金管与405不锈钢板在高温高压水中的微动腐蚀影响,最终得出随着微振频率的增加,690tt管的磨损体积先增大后减小,而405不锈钢板的磨损体积和逐渐增大的结论,并提出了相应的寿命预测模型。碎屑类型对微动磨损也有一定的影响。a.m.kirk等通过研究位移幅值对频率范围内微动磨损的影响,对频率效应提出了新的见解。最终得出振动频率的增加会导致氧化为主的磨损机制转变为不能形成氧化碎屑层的机制,而氧化碎屑会隔绝接触面的直接接触,导致严重的地下损伤。l.xin等研究了在高温高压水中,频率对690tt合金对304型不锈钢微动腐蚀行为的影响及其机理。结果表明,磨损主位的要源于分层磨损、材料传递磨损以及氧化磨损。频率的增加加速了磨损碎片的逃逸,这不仅源于tts层的损伤,也源于接触面之间氧化颗粒的破碎。温度对微动磨损的影响不容忽视。温度不仅会影响摩擦副的几何形状变化,还会影响摩擦面之间的接触特性。nsrivastava等提出基于有限元的压合轴微动磨损和微动疲劳预测方法,该方法将磨损模型与微动疲劳分析相结合,定量预测微动磨损引起的应力重分布影响,结果表明接触边缘应力最为显著。傅兵等针对现有cvt传动效率低的问题,通过推导相应钢环压力模型及钢环运动学模型构建钢环摩擦损失计算模型,分析得到了转矩、转速、速比对钢环摩擦损失的影响,并通过台架试验验证其结论。最后通过改善金属带结构的方法,提供了一种优化传动效率的设计思路。综上所述,cvt输入的转矩、转速以及钢环部微振频率都对微动磨损产生极大的影响,探究其间存在的联系,提升cvt的应用效能及使用寿命是非常必要的。
4.机械系统服役下润滑状态引起科研领域的广泛关注,学者们对润滑油膜特性的研究越来越深入。wang等对点接触的螺旋锥齿轮(sbg)在周期性波动载荷和速度下的润滑动态接触油膜刚度进行了全面研究,得到动载荷和接触面积之间存在竞争关系的结论,在一定的波动幅值下会出现正负刚度翻转的现象,这会导致极低刚度或极高刚度。w.h.b基于点
接触混合ehl中冠状双斜齿轮,通过archard理论扩展到润滑情况来评估点接触混合ehl的磨损率,最后得到表面粗糙度对磨损寿命的影响。提出磨损寿命预测模型,通过合理匹配润滑、修整和工作参数提高冠状双斜齿轮的磨损寿命。有学者研究扭矩、转速、粗糙度等因素对摩擦副表面瞬态混合润滑状态的影响,得到其间的内在联系。通过优化改善方法,提高了机械系统的稳定性及使用寿命。chun等提出了一种热混合润滑模型,研究了温度对涂层的机械性能以及摩擦学性能的影响。综上所述,学者们应用诸多手段对不同机械系统的润滑特性进行了研究。
技术实现要素:5.本发明的目的在于提供一种cvt钢环摩擦副磨损深度、安全裕度计算、评估方法及装置来克服或至少减轻现有技术的上述缺陷中的至少一个。
6.为实现上述目的,本发明提供一种cvt钢环摩擦副磨损深度计算方法,其包括:
7.利用式(15)表示的钢环磨损深度模型,计算cvt钢环摩擦副的磨损深度;
[0008][0009]
式中,h(x)为cvt钢环摩擦副的钢环局部位置x的磨损深度,x轴为钢环的轴向,δk为预设的微动磨损循环加速次数,k为预设的钢环摩擦副磨损循环次数,i为微动磨损次数,k
int
为预设的微动磨损循环连续微动摩擦过程中的增量步,j为磨损增量次数,sf为预设的夹紧力的安全系数,σs为预设的钢环使用的金属材质的屈服极限,υs为预设的钢环摩擦副局部磨损系数,ε为预设的cvt的输入转矩幅值波动系数,α为预设的cvt钢环摩擦副的带轮锥角,r
p
为cvt钢环摩擦副的主动轮的工作半径,kv为cvt运动过程的动载系数,tm为cvt从动带轮的平均输入转矩,ω为钢环摩擦副微振频率,t为微动磨损过程的时间变量,为cvt钢环摩擦副的主动轮与从动轮工作圆公切线与连心线之间的夹角,ds
i,j
(x)为第i次微动摩擦下第j次磨损增量的相对滑移距离,t
p
为cvt钢环摩擦副的从动轮的输入转矩,f为cvt钢环摩擦副的钢环接触表面摩擦系数,f
si
为第i次微动摩擦施加到cvt钢环摩擦副的钢环上的夹紧力,其被描述成式(12);
[0010][0011]
本发明还提供一种cvt钢环摩擦副安全裕度计算方法,其包括:
[0012]
通过比较cvt钢环摩擦副的钢环局部位置x的磨损深度与cvt钢环摩擦副的首层钢环与第二层钢环之间的油膜的厚度,获得cvt钢环摩擦副的安全裕度,其中,x轴为所述钢环的轴向。
[0013]
进一步地,所述cvt钢环摩擦副的安全裕度通过式(26)计算得到:
[0014][0015]
式中,h(x)为如上所述cvt钢环摩擦副的钢环局部位置x的磨损深度,h
l
为cvt钢环摩擦副的首层钢环与第二层钢环之间的油膜的厚度。
[0016]
本发明还提供一种cvt钢环摩擦副评估方法,其包括:
[0017]
步骤1,采集cvt钢环摩擦副的主动轮的工作半径r
p
、cvt从动带轮的平均输入转矩
tm、钢环摩擦副微振频率ω、cvt运动过程的动载系数kv、以及cvt钢环摩擦副的主动轮与从动轮工作圆公切线与连心线之间的夹角
[0018]
步骤2,通过比较cvt钢环摩擦副的钢环局部位置x的磨损深度与cvt钢环摩擦副的首层钢环与第二层钢环之间的油膜的厚度,获得cvt钢环摩擦副的安全裕度,其中,x轴为所述钢环的轴向;
[0019]
步骤3,判断安全裕度是否小于0,如果是,则判定cvt的安全状态良好;否则判定cvt的可靠性差。
[0020]
进一步地,所述cvt钢环摩擦副的安全裕度通过式(26)计算得到:
[0021][0022]
式中,h(x)为权利要求1中所述cvt钢环摩擦副的钢环局部位置x的磨损深度,h
l
为cvt钢环摩擦副的首层钢环与第二层钢环之间的油膜的厚度。
[0023]
本发明还提供一种cvt钢环摩擦副磨损深度计算装置,其包括:
[0024]
钢环磨损深度模型,其被描述成式(15),计算cvt钢环摩擦副的磨损深度;
[0025][0026]
式中,h(x)为cvt钢环摩擦副的钢环局部位置x的磨损深度,x轴为钢环的轴向,δk为预设的微动磨损循环加速次数,k为预设的钢环摩擦副磨损循环次数,i为微动磨损次数,k
int
为预设的微动磨损循环连续微动摩擦过程中的增量步,j为磨损增量次数,sf为预设的夹紧力的安全系数,σs为预设的钢环使用的金属材质的屈服极限,υs为预设的钢环摩擦副局部磨损系数,ε为预设的cvt的输入转矩幅值波动系数,α为预设的cvt钢环摩擦副的带轮锥角,r
p
为cvt钢环摩擦副的主动轮的工作半径,kv为cvt运动过程的动载系数,tm为cvt从动带轮的平均输入转矩,ω为钢环摩擦副微振频率,t为微动磨损过程的时间变量,为cvt钢环摩擦副的主动轮与从动轮工作圆公切线与连心线之间的夹角,ds
i,j
(x)为第i次微动摩擦下第j次磨损增量的相对滑移距离,t
p
为cvt钢环摩擦副的从动轮的输入转矩,f为cvt钢环摩擦副的钢环接触表面摩擦系数,f
si
为第i次微动摩擦施加到cvt钢环摩擦副的钢环上的夹紧力,其被描述成式(12);
[0027][0028]
本发明还提供一种cvt钢环摩擦副安全裕度计算装置,其包括:
[0029]
安全裕度模型,其用于通过比较cvt钢环摩擦副的钢环局部位置x的磨损深度与cvt钢环摩擦副的首层钢环与第二层钢环之间的油膜的厚度,获得cvt钢环摩擦副的安全裕度,其中,x轴为所述钢环的轴向。
[0030]
进一步地,所述cvt钢环摩擦副的安全裕度通过式(26)计算得到:
[0031][0032]
式中,h(x)为如上所述cvt钢环摩擦副的钢环局部位置x的磨损深度,h
l
为cvt钢环摩擦副的首层钢环与第二层钢环之间的油膜的厚度。
[0033]
本发明还提供一种cvt钢环摩擦副评估评估装置,其包括:
[0034]
采集单元,其用于采集cvt钢环摩擦副的主动轮的工作半径r
p
、cvt从动带轮的平均输入转矩tm、钢环摩擦副微振频率ω、cvt运动过程的动载系数kv、以及cvt钢环摩擦副的主动轮与从动轮工作圆公切线与连心线之间的夹角
[0035]
安全裕度模型,其用于通过比较cvt钢环摩擦副的钢环局部位置x的磨损深度与cvt钢环摩擦副的首层钢环与第二层钢环之间的油膜的厚度,获得cvt钢环摩擦副的安全裕度,其中,x轴为所述钢环的轴向;
[0036]
判断单元,其用于判断安全裕度是否小于0,如果是,则判定cvt的安全状态良好;否则判定cvt的可靠性差。
[0037]
进一步地,所述cvt钢环摩擦副的安全裕度通过式(26)计算得到:
[0038][0039]
式中,h(x)为如上所述cvt钢环摩擦副的钢环局部位置x的磨损深度,h
l
为cvt钢环摩擦副的首层钢环与第二层钢环之间的油膜的厚度。
[0040]
本发明由于采取以上技术方案,其具有以下优点:
[0041]
本发明通过建立磨损深度与宏微观因素相关联的钢环磨损深度模型,并将所求得获得cvt钢环摩擦副的磨损深度及油膜厚度结果,得到cvt工作范围内钢环摩擦副的安全裕度,从而利用该安全裕度评估cvt的可靠性及使用寿命。
[0042]
说明书附图
[0043]
图1为cvt传动及结构示意图。
[0044]
图2为cvt钢环表面磨损观测图。
[0045]
图3为cvt钢环组织形貌及接触模型图。
[0046]
图4为cvt钢环组织温度仿真图。
[0047]
图5为cvt钢环配合面轮廓仿真结果。
[0048]
图6为不同转矩作用下为cvt钢环不同位置处磨损深度,其中:(a)为cvt钢环摩擦副首层外侧磨损深度,(b)为cvt钢环摩擦副首层内测磨损深度,(c)为cvt钢环摩擦副第二层外侧磨损深度。
[0049]
图7为不同转速作用下cvt钢环不同位置处磨损深度,其中:(a)为cvt钢环摩擦副首层外侧磨损深度,(b)为cvt钢环摩擦副首层内测磨损深度,(c)为cvt钢环摩擦副第二层外侧磨损深度。
[0050]
图8为不同频率下cvt钢环表面粗糙度观测图
[0051]
图9为不同微振频率作用下cvt钢环不同位置处磨损深度,其中:(a)为cvt钢环摩擦副首层外侧磨损深度,(b)为cvt钢环摩擦副首层内测磨损深度,(c)为cvt钢环摩擦副第二层外侧磨损深度。
[0052]
图10为cvt钢环的三维粗糙度表面。
[0053]
图11为cvt油膜特性仿真图,其中:(a)为cvt油膜压力变化图,(b)为cvt油膜厚度变化图,(c)为cvt油膜温升变化图。
具体实施方式
[0054]
下面结合附图和实施例对本发明进行详细的描述。
[0055]
cvt金属带由数百个金属摩擦片和6~12层钢环组成,其传动及结构图如图1所示。钢环组在金属带轮夹紧力的作用下张紧,将摩擦片撑起进行转矩传递。cvt运行时钢环与钢环之间,钢环与摩擦片鞍面之间的相对滑动及振动等影响使得钢环之间产生磨损。由于首层钢环的损失占钢环总摩擦功率损失的70%,第二到九层钢环损失仅为6%到0.008%,首层钢环的损失占比远大于其它钢环损失占比,因此本发明实施例的研究对象选取首层钢环与第二层钢环,图2为钢环表面磨损观测图。
[0056]
现有技术中的计算磨损的模型大概有100多种,其适应的范围状态不同。目前工程上应用较为广泛的磨损模型是archard相关的黏着磨损模型。
[0057][0058]
式中,k为磨损系数;p为接触法向载荷;s为滑动距离;h为材料硬度。
[0059]
archard模型计算磨损时,只能应用于摩擦因数恒定的情况。考虑到cvt钢环摩擦副表面材料磨损过程中的复杂性和多变性,需进行变载荷条件下的摩擦磨损建模,从能量的观点可将此过程视为能量消耗和转化的结果,即摩擦副在摩擦过程中由于能量消耗产生材料表面的磨损。
[0060]
在耗散理论中,假定微动磨损量与耗散能量之间存在线性关系,即:
[0061][0062]
式中,υ为能量磨损系数;e
di
为给定滑移幅值下的单次微动循环的耗散能量;k为磨损循环次数。
[0063]
耗散能量为剪切力所做的摩擦功被描述成式(3):
[0064][0065]
式中,为第i次微动摩擦金属带总受力;si为第i微动摩擦两钢环摩擦副的相对滑移距离。
[0066]
研究过程将接触区域设定为一极限接触区域da,微动磨损深度dh表示为:
[0067][0068]
式中,υs为局部的磨损系数。
[0069]
由式(3)可得钢环弧段任意一x处的第i次局部磨损耗散能量为:
[0070][0071]
式中,为第i次微动摩擦首层钢环和第二层钢环局部位置的总受力;dsi(x)为第i微动摩擦首层钢环和第二层钢环局部位置x的相对滑移距离。
[0072]
由式(4)和式(5)可得第i次微微动摩擦首层钢环和第二层钢环接触位置的磨损深度为:
[0073][0074]
式中,τi(x)为第i次微动摩擦首层钢环和第二层钢环局部接触位置x处的摩擦切应力。
[0075]
由上式可得此处的微动磨损深度表示为:
[0076]
δhi(x)=υs∫τi(x)dsi(x)
ꢀꢀ
(7)
[0077]
假设在连续的微动摩擦过程中有k
int
个增量步,将第j(j=1,2
…
,k
int
())次的磨损深度进行线性叠加,即得到第i次微动摩擦首层钢环和第二层钢环局部接触位置的磨损深度为:
[0078][0079]
式中,τ
i,j
(x)为第i次微动摩擦下第j次磨损增量的切应力;ds
i,j
(x)为第i次微动摩擦下第j次磨损增量的相对滑移距离。
[0080]
因此,在第k次微动摩擦下钢环局部接触位置x处的磨损深度为:
[0081][0082]
在实际的微动摩擦过程中摩擦次数相当大,若在计算过程依次计算每一次摩擦量将会导致计算成本提升且耗费时间加长。考虑到每一次的微动摩擦所产生的磨损量很小,且对下一次的磨损结果微量的影响。因此,可通过相似性原理适当加大能量磨损系数,同时将一次微动摩擦过程代替δk次摩擦过程,从而大大缩短计算时间。
[0083]
可得到加速次数为δk时,整个微动摩擦过程中钢环局部位置x的磨损深度为:
[0084][0085]
空气中的金属表面都有自然污染的表面膜。摩擦滑动即把膜剪断。令膜的剪切强度为τ
i,j
(x)。如果用金属的剪切强度τb为单位表示τ
i,j
(x),可以写成τ
i,j
(x)=cτb,c为某个常数。
[0086][0087]
式(11)概括了各种表面状态具有普遍性,既包括粘着摩擦,又包括氧化膜、其它反应膜的摩擦。
[0088]
上式中施加在钢环上的夹紧力为:
[0089][0090]
式中,sf为安全系数;t
p
为从动轮的输入转矩;α为带轮锥角;f为摩擦因数;r
p
为主动轮的工作半径。
[0091]
考虑到变速器传动过程中的工况变化是多变的且多激励特征,在传动过程中的传动载荷是变化的。假设传动载荷呈简谐波形式变化,那么钢环摩擦副传递的转矩为:
[0092][0093]
式中,kv为动载系数,与转速有关;tm为平均输入转矩;ε为输入转矩幅值波动系数;ω为微振频率;为主从动轮工作圆公切线与连心线之间的夹角。
[0094]
由上式可得切应力为:
[0095][0096]
因此,本发明实施例提供的cvt钢环摩擦副磨损深度计算方法包括:
[0097]
利用式(15)表示的钢环磨损深度模型,计算cvt钢环摩擦副的磨损深度;
[0098][0099]
金属带通过推力与摩擦力传递转矩,摩擦副间的润滑作用符合热弹流点接触的形式,其中reynolds方程如公式所示:
[0100][0101]
式中,x,y为坐标系方向,y为钢环运动方向;h为油膜厚度;ρ、η分别为考虑温度影响润滑油密度及润滑油黏度,可根据密温密压方程和黏温黏压方程求得。
[0102]
当出口、入口区压力均为0,出口区压力变化率为0时,方程的边界条件为:
[0103]
入口处:p(x1,y)=0;
[0104]
出口处:p(x2,y)=0,
[0105]
式中,x1为入口处x坐标,x2为出口处x坐标。
[0106]
考虑粗糙度的点接触膜厚方程为:
[0107][0108][0109][0110]
式中,h0为中心膜厚;r
x
,ry分别为沿x,y方向上的当量曲率半径;h(x,y)为由压力产生的弹性变形位移;r(x,y)为表面粗糙度函数;e为综合弹性模量;s、g分别为压力点在x、y方向上的坐标。e1和υ1分别代表金属片的弹性模量和泊松比;e2和υ2分别代表带轮的弹性模量和泊松比。
[0111]
钢环之间的粗糙峰是按照概率密度函数随机分布的,因此,其间的接触峰的数量也应按照概率密度函数来计算。两摩擦副表面粗糙度的均方根值分别为σ1和σ2,其间接触的情况可以转换为一个光滑的刚性表面和一个粗糙弹性表面的接触,粗糙弹性表面的均方根值为
[0112]
摩擦副中心线间的距离为l时,当轮廓高度z大于中心线距离l时,钢环表面才发生接触。在概率密度分布曲线中,两表面发生接触的面积即为表面接触概率为:
[0113]
p(z>x)=∫
l∞
ψ(z)dz
ꢀꢀꢀꢀꢀꢀꢀꢀꢀꢀꢀꢀꢀꢀꢀꢀꢀ
(20)若粗糙表面的峰点数为n,则接触部分的峰点数m为:
[0114]
m=n∫
l∞
ψ(z)dz
ꢀꢀꢀꢀꢀꢀꢀꢀꢀꢀꢀꢀꢀꢀꢀ
(21)接触峰点的法向变形量为z-l,可的实际接触面积a为:
[0115]
a=mπr∫
l∞
(z-l)=nπr(z-l)ψ(z)dz
ꢀꢀꢀꢀꢀ
(22)接触峰点支承的总载荷量w为:
[0116]
[0117]
通常实际表面的轮廓高度按照gauss分布。在gauss分布中,靠近z值较大的部分近似于指数型分布。若令ψ(z)=exp(-z/σ)。计算可得:
[0118][0119]
润滑油膜的传热方式以对流散热为主,沿膜厚方向的热传导可忽略不计,所需能量方程:
[0120][0121]
式中,c
p
为润滑油等压比热容;t为润滑油温度;j为热功当量。
[0122]
温度求解是沿油膜运动方向从入口处到出口处,x方向设定为润滑油流动方向,t0为无量纲化后的初始温度,边界条件设置如下:
[0123]
x方向上:t(x1,y)=t0;
[0124]
y方向上:
[0125]
本实施例选用的cvt为九层钢环,将首层钢环与第二层钢环概念性的分离,方便进行后续有限元计算的网格划分与模拟。使用ansys软件进行仿真计算,网格划分时,为使计算过程精确化,使用多区域网格划分方法(multizone)最小网格长度为1mm,同时限制元素大小为1mm。首层钢环与第二层钢环表面组织形貌分别为图3中的(a)和(b)所示,图3中的(c)为摩擦副接触形式图,摩擦副由两个长度为20.0mm,厚度为0.18mm的马氏体钢环组成。
[0126]
利用所建立的模型设置边界条件后,通过数值方法得到钢环整体在3000cycles循环下的温度分布。图4为温度分布结果图,温升主要集中在摩擦片与钢环接触面附近区域,由于变速器运行过程中摩擦片内测与钢环一侧发生接触且产生相对滑动,摩擦功导致温度有较明显的变化。且鞍面与钢环接触面之间存在润滑油,其间的散热形式通常为传导散热,因此导致温度较明显的向钢环边缘处传导,中部由于产生较微弱摩擦以及润滑油的冷却作用下温度降低较快,且温升不明显。
[0127]
本实施例将cvt作为研究对象,根据上述构建的模型计算首层钢环与第二层钢环间微动磨损与微动参量的关系。对钢环过盈段进行仿真分析时,首先确定微动循环周次k。
[0128]
图5为不同循环周次的钢环配合面轮廓仿真结果,横坐标为钢环任意位置距钢环中心的距离。由于钢环配合面轮廓在边缘处变化最大,因此,选取距钢环中心新0~1.0mm范围内轮廓进行研究,0.9mm处为过盈配合的最边缘,其左边为过盈配合部位。由图5可见,在同一循环周次内当配合面的磨损深度在过盈配合最边缘处达到最大,向钢环中心线方向逐渐减小;图5中,沿着纵向坐标轴,由上至下,曲线对应的循环周次的不断增加,钢环边缘向中心线方向的磨损深度都不断增大,磨损宽度也不断增大。由于首层钢环与第二层钢环间的粗糙度幅值保持在1左右,且振荡幅值不超过1,为了保证结果的准确性,循环周次选取最小的3000以保证配合面轮廓磨损度的精确。
[0129]
为了探究传递转矩对首层钢环与第二层钢环间的磨损深度,选取不同输入转矩的值进行磨损深度的仿真分析。图6为cvt在转矩分别为30n
·
m、90n
·
m、150n
·
m三种情况下
两摩擦副载荷循环3000周期后的钢环面沿轴向的磨损深度变化。图6中的(a)为钢环摩擦副首层外侧磨损深度分布,由钢环内侧(x/l=0)到外侧(x/l=1)磨损深度先变小后变大,在x/l=0.83处磨损深度快速增加,在x/l=1.0处达到最大,当转矩tm=150n
·
m时磨损深度最大为1.54μm。图6中的(b)为钢环摩擦副首层内测磨损深度分布,变化趋势与钢环紧边变化趋势大体相同,但变化趋势较缓。图6中的(c)为钢环摩擦副第二层外侧磨损深度分布,由钢环内侧(x/l=0)到外侧(x/l=1)磨损深度先变小后变大,在x/l=0.86处磨损深度急速增加,在x/l=1.0处达到最大,当转矩tm=150n
·
m时磨损深度最大可达3.1μm。这是由于在摩擦副过盈处金属片通过挤推力传递转矩时,对钢环的压力变大,导致微动面的接触压力和剪切力增大,从而导致此处磨损深度变大。由于此处的压力堆积,导致接触压力和剪切力出现应力集中现象,从而出现过盈处的磨损深度剧增的现象。
[0130]
cvt转速是影响钢环磨损深度的一个重要因素,在仿真过程中避开变速器输入的最高及最低转速,将转速的输入值分别设定为1400、2100、2800r/min。如图7分别为钢环摩擦副首层外侧、首层内测以及第二层外侧钢环表面磨损深度随输入转速的变化图。由图7中的(a)可以看出钢环在轴向上的磨损深度先减小后变大,且转速越大,磨损深度越大。在x/l=0.9处磨损深度快速增加,因为此处为磨损边缘处,变速器金属片对钢环的挤压力相对较大,导致磨损深度的变化。钢环首层内测磨损深度变化与紧边的变化趋势相似,但由于金属片给予钢环的挤推力较紧边小,所以磨损深度相对较小且幅值变化较小。图7中的(c)为钢环第二层外侧磨损深度变化,其变化趋势先变小,后再x/l=0.5左右有快速增长,随后在x/l=0.9左右又有较快增长。这是由于在上述两处分别为金属片进入和离开金属带轮的位置,由于在金属片的挤推力作用下,钢环夹带金属片一起移动,在进入和离开金属带轮位置处会产生相对较高的加压力,因此,此处的磨损频率相对较快,导致钢环的磨损深度有较快速的增长。
[0131]
本发明实施例中使用的变速器钢环摩擦副的材料为18%ni屈服极限为175级的马氏体时效刚,其成分中添加各种时效硬化的合金元素,表1为马氏体钢环的化学成分。其弹性模量为192gpa,泊松比为0.30,密度为7800kg/m3。试验前,标本均在乙醇中清洗且在烘干机中进行处理。
[0132]
表1马氏体时效刚成分表
[0133][0134]
cvt服役时金属带钢环紧配合结构由微振动致使微动磨损,微振频率会影响钢环摩擦副之间的表面粗糙度的变化,在考虑表面粗糙度对磨损深度的影响时,必须先探讨微振频率对表面粗糙度的影响。采用电镜扫描试验来观测微振频率对表面粗糙度的影响。本实施例使用的是hitachi regulus8100冷场发射扫描电镜,此电镜保留了su8100易维护、易操作等优点,进一步提高了性能。
[0135]
借助振动试验台逐步设置微振频率分别为30、60、90、120hz,得到3000周期循环周
次下的钢环样品,分别对首层钢环与第二层钢环进行制样,将钢环样品依次放入电镜进行观测,选取表面状态良好的结果图。由图8可见,随着微振频率的增加,摩擦副表面粗糙度也随之增加。微振频率不仅提高磨损量,而且加速了摩擦表面的机械破碎,促进了表面破碎物的清除,导致磨屑保护效果降低。当微振频率从30hz增加到90hz时粗糙度加剧增大,此时磨损量也加大。当频率超过90hz时,表面粗糙度及磨损量反而减小。这是因为过大的频率会对钢环表面裂纹扩展速率产生较大影响,裂纹萌生的深度较浅,其产生的速率较慢,导致摩擦副之间的分层效率降低,表面粗糙度随着频率的增加而减小。
[0136]
随着微振频率的变化,钢环摩擦副之间的磨损深度也有着显著的变化。如图9分别为钢环摩擦副首层外侧、首层内测以及第二层外侧钢环表面磨损深度随微振频率的变化图。磨损深度在轴向上总体呈先增多后减少的趋势,这是因为微振频率升高,磨损量升高导致摩擦表面的机械破碎速率加快,表面破碎物的清除速率加快,因此磨损深度增大。当频率超过90hz,摩擦副之间的分层效率降低,磨损深度随着频率的增加而减小。由图9中的(a)可得当频率由30hz增加到90hz时,钢环摩擦副的最大磨损深度由0.72μm增加到1.44μm;钢环首层内测频率由30hz增加到90hz时,摩擦副的最大磨损深度由0.78μm增加到1.18μm;图9中的(c)可得,频率为30、60、90、120hz时,在x/l=0.80、x/l=0.72、x/l=0.52、x/l=0.56处磨损深度便有较快增长。在过盈处当频率由30hz增加到90hz时,钢环摩擦副的最大磨损深度由1.24μm增加到1.73μm。
[0137]
根据上文对首层钢环及二层钢环间润滑情况的建模,进行两摩擦副之间的润滑特性分析。点接触混合润滑常用的求解方式为newton-raphson算法,该方法的求解收敛速度较快,计算结果较为准确,但这个求解过程需要分解解决方程的雅克比矩阵进行一维线性分析,计算过程较为复杂。因此,此仿真过程使用牛顿迭代算法是最好的选择。
[0138]
在计算过程中首先提供了数组rou空间,数组个数与节点数一致。其次为了方便计算,在程序目录下提前计算了粗糙情况,并保存在相应子程序中。在膜厚方程中添加粗糙度函数,计算在粗糙度影响下的油膜厚度变化。最后由于随机粗糙度是不对称的,在计算过程中y方向计算过程全部执行,不进行对称处理。
[0139]
求解输入转矩转矩t
p
=150n
·
m,主动轮转速n
p
=5500r/min,滑转率ε=3%,速比i=1的cvt工况下钢环摩擦副之间的膜厚、压力、温升变化分布的量纲化结果.如图10为根据所建模型生成的三维表面粗糙度表面,由图可见所生成表面的粗糙峰最高不超过1.0μm,且粗糙峰分布随机。
[0140]
如图11所示,x为摩擦片移动方向,y为钢环法线方向的无量纲坐标。
[0141]
在随机粗糙峰的影响下,摩擦副之间的油膜分布也是随机的,当出现较为尖锐的粗糙峰时,此时峰顶处会产生一个压力峰,如图11中的(a)所示期间产生的压力峰值最高可达1.77gpa。随着转矩、转速的增加,峰顶处的压力急剧升高,其周围的润滑方式将向混合润滑变化,将会产生油膜破裂的危险。
[0142]
图11中的(b)为钢环摩擦副之间油膜厚度变化图,由于表面粗糙度的影响得到的油膜厚度结果表面也是粗糙的。当摩擦副之间产生磨损逐渐增多时,钢环两表面之间就会渗透进入润滑油,此时两摩擦副之间形成各种润滑膜组成特性的综合表现,在粗糙峰峰顶处油膜压力迅速上升,由于油膜两侧受到摩擦副施加的压力导致其发生弹性变形,油膜出现第一次压力极值,此时膜厚也会发生骤减现象,此时油膜厚度为0.3μm。润滑油经过粗糙
峰时油膜压力下降,当润滑油到达相邻粗糙峰时出现颈缩现象,油膜压力会再次出现压力极值,此时,油膜厚度也会出现极值,膜厚为0.37μm。
[0143]
图11中的(c)为在表面粗糙度影响下油膜温度的变化图,温度变化与压力变化相似,在较为尖锐的粗糙峰处油膜温度会急速上升。宏观上,尖峰处的摩擦力会导致机械能转换为热能而使得温度升高。在微观方面,由于在粗糙峰顶部油膜内部的剪应变率增大导致剪切力变大,油膜获得较多剪切功致使温度上升。在转矩、转速、微振频率等因素的影响下,粗糙峰顶部的油膜温升最高可达48℃左右。
[0144]
cvt运转过程中,在转矩、转速、微振频率等因素的影响下钢环摩擦副之间的随机粗糙度和随机油膜分布会发生变化。摩擦副之间的润滑状态逐渐向混合润滑转移,混合润滑的整体特征是各种润滑膜组成特性的综合表现,润滑膜在摩擦副接触表面上所占的比例与摩擦界面形态和工况条件有关。在摩擦过程中,润滑膜的厚度、所占比例及和分布状况都在变化之中,当粗糙峰高度大于最大润滑膜的厚度时,此时会形成干摩擦状态,导致表面损伤。随着载荷波动的进行,配合面产生微动滑移并磨损,通过摩擦片传递导致带与带轮间的接触特性、相对运动等也随之改变,造成金属带滑移、带轮偏转、轴承蠕变。
[0145]
因此,本发明实施例提供的cvt钢环摩擦副安全裕度计算方法包括:
[0146]
通过比较cvt钢环摩擦副的钢环局部位置x的磨损深度与cvt钢环摩擦副的首层钢环与第二层钢环之间的油膜的厚度,获得cvt钢环摩擦副的安全裕度,其中,x轴为所述钢环的轴向。
[0147]
在一个具体的实施例中,为了保证变速器传动的可靠性以及延长使用寿命,cvt钢环摩擦副的安全裕度通过式(26)计算得到:
[0148][0149]
当磨损深度大于cvt钢环摩擦副的首层钢环与第二层钢环之间的油膜的厚度,即安全裕度大于0时,钢环磨损情况加重,失效概率及寿命缩减概率加大,此时较差,否则视为安全状态良好。选取rd150型cvt为研究对象,进行安全裕度求解。表2为选取cvt的结构与工作参数:
[0150]
表2cvt的结构与工作参数表
[0151][0152]
设置cvt工作参数范围的最小值为初始值,主动轮转速的步长选取为100r/min,滑转率的步长选取为0.1%,速比步长选取为0.2,转矩步长选取为10n
·
m;其次,结合金属带传动过程的温度变化,计算每个工作点的安全裕度值,并进行插值处理;最后,获得工况条件变化时相对应的安全裕度曲面图。
[0153]
本发明主要围绕cvt的应用效能及安全问题展开,基于符合钢环摩擦副的耗散磨损模型,建立了磨损深度与其影响变量相关联的磨损深度模型,同时构建了符合钢环摩擦副的润滑模型。基于所建模型进行特定工况下的仿真实验,得到相应的磨损深度以及油膜特性结果。最后结合宏观参数和微观润滑两方面进行应用效能及安全问题深入剖析。主要结论总结如下:
[0154]
1)钢环摩擦副的磨损深度随转矩、转速的增加会逐渐增大,且在轴向方向上,在x/l=0.8附近时磨损深度会快速增加,且在x/l=1.0时达到最大。磨损深度随微振频率的变化在轴向上总体呈先增多后减少的趋势。微振频率升高,是因为磨损量升高导致摩擦表面的机械破碎速率加快,表面破碎物的清除速率加快。当频率超过90hz,摩擦副之间的分层效率降低,磨损深度随着频率的增加而减小。
[0155]
2)cvt运行下,金属带由摩擦产生的热量会通过热传导的方式耗散,由于摩擦片内测与钢环一侧发生接触且产生相对滑动,摩擦功导致接触部位温度有较明显的升高。且鞍面与钢环接触面之间存在润滑油,导致钢环中部冷却相对较快,因此温度较明显的向钢环边缘处传导。油膜温度由于粗糙峰的影响会呈峰状的随机分布,在表面粗糙尖峰处会产生较高的温度峰,最高温升可达48℃。
[0156]
3)在随机粗糙峰的影响下,摩擦副之间的油膜分布也是随机的,当出现较为尖锐的粗糙峰时,此时峰顶处会产生一个压力峰,期间产生的压力峰值最高可达1.77gpa。在粗糙峰的影响下,在粗糙峰峰顶处油膜压力迅速上升,由于油膜两侧受到摩擦副施加的压力导致其发生弹性变形,膜厚出现第一次骤减现象,膜厚为0.3μm。当润滑油到达相邻粗糙峰时出现颈缩效应,油膜厚度第二次出现骤减现象,膜厚为0.37μm。
[0157]
4)随着转矩和转速的升高,微振频率也逐渐增大,在应用效能和安全性的综合考
虑下,安全裕度随着宏观参数的减小而逐渐降低,当传递转矩大于130n
·
m即安全裕度下降到0以下时,此时安全裕度处于非安全区域,传动效率偏低且安全性失效概率显著增大。
[0158]
本发明实施例还提供的cvt钢环摩擦副评估方法包括:
[0159]
步骤1,采集cvt钢环摩擦副的主动轮的工作半径r
p
、cvt从动带轮的平均输入转矩tm、钢环摩擦副微振频率ω、cvt运动过程的动载系数kv、以及cvt钢环摩擦副的主动轮与从动轮工作圆公切线与连心线之间的夹角
[0160]
步骤2,通过比较cvt钢环摩擦副的钢环局部位置x的磨损深度与cvt钢环摩擦副的首层钢环与第二层钢环之间的油膜的厚度,获得cvt钢环摩擦副的安全裕度,其中,x轴为所述钢环的轴向。
[0161]
步骤3,判断安全裕度是否小于0,如果是,则判定cvt的安全状态良好;否则判定cvt的可靠性差。
[0162]
本发明实施例提供的cvt钢环摩擦副磨损深度计算装置包括钢环磨损深度模型,钢环磨损深度模型被描述成式(15),用于计算cvt钢环摩擦副的磨损深度。
[0163]
本发明实施例另提供的cvt钢环摩擦副安全裕度计算装置包括安全裕度模型,安全裕度模型用于通过比较cvt钢环摩擦副的钢环局部位置x的磨损深度与cvt钢环摩擦副的首层钢环与第二层钢环之间的油膜的厚度,获得cvt钢环摩擦副的安全裕度,其中,x轴为所述钢环的轴向。
[0164]
在一个实施例中,所述cvt钢环摩擦副的安全裕度通过式(26)计算得到。
[0165]
本发明实施例还提供的cvt钢环摩擦副评估装置包括采集单元、安全裕度模型和判断单元,其中:
[0166]
采集单元用于采集cvt钢环摩擦副的主动轮的工作半径r
p
、cvt从动带轮的平均输入转矩tm、钢环摩擦副微振频率ω、cvt运动过程的动载系数kv、以及cvt钢环摩擦副的主动轮与从动轮工作圆公切线与连心线之间的夹角
[0167]
安全裕度模型用于通过比较cvt钢环摩擦副的钢环局部位置x的磨损深度与cvt钢环摩擦副的首层钢环与第二层钢环之间的油膜的厚度,获得cvt钢环摩擦副的安全裕度,其中,x轴为所述钢环的轴向。
[0168]
判断单元用于判断安全裕度是否小于0,如果是,则判定cvt的安全状态良好;否则判定cvt的可靠性差。
[0169]
最后需要指出的是:以上实施例仅用以说明本发明的技术方案,而非对其限制。本领域的普通技术人员应当理解:可以对前述各实施例所记载的技术方案进行修改,或者对其中部分技术特征进行等同替换;这些修改或者替换,并不使相应技术方案的本质脱离本发明各实施例技术方案的精神和范围。