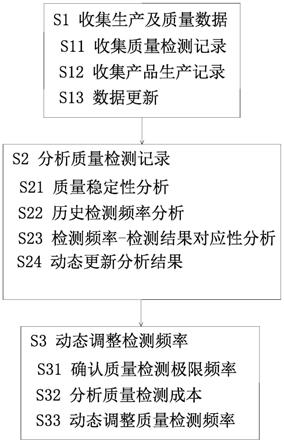
1.本技术涉及品质安全的领域,尤其是涉及一种自动化生产过程的品质安全识别方法及系统。
背景技术:2.cn201610273640.9公开了一种板材质量检测实时计算系统及其方法,其技术方案为:设定质量检测时机:定时器启动多线程计算任务,定时器在指定时间周期 启动计算任务。按热轧卷生产节奏,定时器每3分钟运行一次;检索待计算产品:由业务数据中获取到可以进行指标计算的产品信息。包 括:钢卷号、钢种、送达时间、钢卷开始时间、钢卷结束时间、要计算指标的过程参数开始时 间和结束时间,要计算指标的目标值;检索待计算指标规则:根据钢种检索该钢卷需要计算的指标规则。包括: 指标名称、去头尾、是否要与目标值比较、允许的上下偏差、小数位数和目标要求;将指标和参数项进行整合:利用步骤二中的产品信息及步骤三中的指标 信息进行匹配,将钢卷号与需要计算的指标匹配好;检索该卷指标曲线:依据步骤二中要计算指标的开始和结束时间获取指 标项涉及到的曲线数值。包括时间、位置标签、位置的值和时间、指标曲线名称、指标曲线值;将指标曲线匹配至位置:根据位置信息匹配得到钢卷位置指标项曲线集,匹配后为位置、时间、指标曲线值;识别截取要求:基于步骤三中指标规则的“去头尾”,按位置要求截取。留 下需要计算的数据;指标计算;评价指标计算结果:将指标计算的结果w与业务规则库中“目标要求”对 比,数值大于等于“目标要求”的值,表示该指标在质量检测中符合要求,否则不符合,不予 放行包装,交于质量工程师进行再评估。
3.该板材质量检测实时计算系统及其方法具有以下优点:指标计算及时,为保证产品在当前工序完成后,在符合标准的情况下进入下一工序,由此需要在产品完成后且在进入下一工序前,必须完成质量检测的所有需要指标的计算,由于钢铁行业在生产过程中具有持续性、连续性,在每个工序之间不可能具有稳定的时间间隔,因此采用每个工序各自加工时长作为可允许最长计算时长,可以确保每个钢卷的质量检测指标完全可以在可允许最长计算时长内完成;全面覆盖的质量检测,普通生产中针对质量检测往往采用抽检方式进行,由于抽检方式采用随机抽样进行,本系统采用的原则是:每一个钢卷均进行指标计算,由此避免抽样方式的随机抽取问题,保证了产品的质量检测指标完整,从而实现质量检测中信息的完 整,进而可以由质检信息进行质检分析;采用标准化规则,按钢种预先设定指标计算规则,并在计算过程中获取此 规则,从而保证每个产品的每一个指标采用标准化方式进行,从而实现质检指标计算的规则的稳定,保证质量检测指标的可衡量比较。
4.但是,该板材质量检测实时计算系统及其方法也具有以下缺点:质量检测频率相对固定,无法根据生产实际质量跳动情况动态调整质量检测频率,对生产实际情况的适应性较差。
5.因此,需要一种能根据生产实际情况动态调整质量检测频率的方法或系统。
技术实现要素:6.为了解决质量检测频率相对固定、对生产实际情况的适应性较差的问题,本技术提供一种自动化生产过程的品质安全识别方法及系统。
7.本技术提供一种自动化生产过程的品质安全识别方法,其特征在于,包括以下步骤:步骤s1,收集生产及质量数据,分别收集生产记录和质量检测数据,并持续更新;步骤s2,分析质量检测记录,从质量参数稳定性,结合历史检测频率,对质量检测数据进行分析;步骤s3,动态调整检测频率,根据产品质量分析情况,对质量检测频率进行动态调整。
8.进一步的,所述步骤s1包括:步骤s11,收集质量检测记录,收集历史生产过程中的质量检测记录,提取质量检测记录中的质量参数并标记质量检测时间后上传至品质安全管理平台的质量参数数据库中,提取质量检测记录中的质量检测频率并标记质量检测时间后上传至品质安全管理平台的检测频率数据库中;步骤s12,收集产品生产记录,收集历史生产过程中的产品生产记录,标记生产时间和生产间隔,并上传至品质安全管理平台的生产记录数据库中;步骤s13,数据更新,持续收集质量检测数据和生产记录数据,并上传至品质安全管理平台。
9.进一步的,所述步骤s2包括:步骤s21,质量稳定性分析,统计质量参数数据库中的质量参数数值,对产品质量稳定性进行判断;步骤s22,历史检测频率分析,统计质量检测记录,标记质量检测时间和质量检测频率;步骤s23,检测频率-检测结果对应性分析,绘制产品质量检测差异性和检测频率对应性关系曲线,并进行曲线拟合;步骤s24,动态更新分析结果,实时提取品质安全管理平台的质量参数数据库中的质量参数,并持续更新分析结果。
10.进一步的,所述步骤s21中,质量稳定性分析方法为:,其中,u表示为待分析生产过程的质量跳动指数,待分析生产过程的质量跳动指数u越大则待分析生产过程的生产质量的稳定性越差,待分析生产过程的质量跳动指数u越小则待分析生产过程的生产质量的稳定性越好;n表示为质量参数数据库中待分析生产过程的质量检测样本的总数量;i表示为质量参数数据库中待分析生产过程的质量检测样本的样本编号;xi表示为质量参数数据库中待分析生产过程的编号为i的质量检测样本的质量参数值;`x表示为质量参数数据库中待分析生产过程的所有质量检测样本的质量参数平均值。
11.通过采用上述技术方案,分析得出质量跳动情况,由数据跳动情况判断生产质量是否需要进行质量检测频率调整,提高了对品质安全的控制能力。
12.进一步的,所述步骤s22中,质量检测差异性的分析方法为:
,其中,k
p
表示为质量检测差异指数,质量检测差异指数k
p
越大则质量检测结果的差异性越大,质量检测差异指数k
p
越小则质量检测结果的差异性越小;n表示为质量参数数据库中待分析生产过程的质量检测样本的总数量;i表示为质量参数数据库中待分析生产过程的质量检测样本的样本编号;xi表示为质量参数数据库中待分析生产过程的编号为i的质量检测样本的质量参数值;p表示为检测频率变更因子,p=1,2,3...;x
i-p
表示为待分析生产过程中,在编号为i的质量检测样本前第p个质量检测样本的质量参数值;;x
i-2p
表示为待分析生产过程中,在编号为i的质量检测样本前第2p个质量检测样本的质量参数值;(t
i-t
i-2p
)表示为编号为i的质量检测样本和在编号为i的质量检测样本前第2p个质量检测样本的生产时间间隔;所述检测频率差异指数的计算方法为:,其中,s
p
表示为检测频率差异指数;p表示为检测频率变更因子,p=1,2,3...;所述步骤s23中,对应性分析方法为:不断提高p的数值,提取对应参数值导入计算,得出对应的质量检测差异指数k
p
的指数值和检测频率差异指数s
p
的指数值,并以k
p
为纵坐标,s
p
为横坐标,绘制k
p-s
p
曲线,并进行曲线拟合。
13.通过采用上述技术方案,得出了不同检测频率对检测结果的影响能力以及检测结果的差异性情况,判断生产过程对检测频率的需求情况,生产过程的质量检测差异性较大则需要更高的检测频率评价品质安全,生产过程的质量检测差异性较小则需要更高的检测频率评价品质安全,提高了评价品质安全的灵活性以及对生产实际情况的适应能力。
14.进一步的,所述步骤s3包括:步骤s31,确认质量检测极限频率,根据生产要求确定质量检测的最低频率为质量检测极限频率;步骤s32,分析质量检测成本,统计质量检测样本的检测破坏性程度,并结合质量检测样本的检测破坏性程度判断质量检测物料成本,以及检测单个质量检测样本的时间成本;步骤s33,动态调整质量检测频率,先以质量检测极限频率进行产品质量检测,并收集质量检测数据,计算实时质量检测差异指数k,并导入k
p-s
p
拟合曲线中得出实时检测频率差异指数s,并导入s
p
计算公式得出实时检测频率变更因子p’,并将实时检测频率变更因子p’代入计算得出调整后的检测频率;所述步骤s33中,调整后质量检测频率计算方法为:,其中,λ表示为调整后的质量检测频率;λ0表示为;质量检测极限频率;p’表示为实时检测频率变更因子;c1表示为单个质量检测样本的物料成本,若产品质量检测为破坏性检测且检测后产品不可使用,则c1即为该单个产品的生产成本,若产品质量检测为非破坏性检测且检测后产品可继续使用,则c1即为0;c2表示为单个质量检测样本的质量检测成本,
具体为检测单个质量检测样本所需时间的人工成本、检测耗材成本、设备占用成本;l表示为该产品的单价;所述步骤s33中,质量检测频率始终大于步骤s31中确认的质量检测极限频率。
15.通过采用上述技术方案,结合质量检测差异性和检测成本,对质量检测频率进行动态调整,保证了对生产过程的质量评价能力,同时控制检测成本,提高了质量评价生产实际情况的适应能力。
16.进一步的,所述步骤s33中,若不同生产过程的生产间隔超出设定阈值,则提高对产品质量的检测频率,直至质量检测结果的质量稳定性满足合格区间,则恢复至通过k
p-s
p
拟合曲线确定的检测频率。
17.通过采用上述技术方案,防止了生产间隔过大造成生产设备及生产介质等发生偏差时传统质量检测方法无法识别品质安全问题的情况,提高了对品质安全的控制能力。
18.一种自动化生产过程的品质安全识别系统,包括:品质安全管理平台和与品质安全管理平台连接的自动化生产终端;所述品质安全管理平台包括:存储器;处理器,与处理器连接;生产记录数据库,设置在所述存储器内,用于存储生产记录数据及对应时间信息;质量参数数据库,设置在所述存储器内,用于存储质量参数数据及对应时间信息;检测频率数据库,设置在所述存储器内,用于存储检测频率数据及对应时间信息;所述自动化生产终端用于接收指令信息并控制自动化生产线运行状态,并上传生产记录数据至生产记录数据库。
19.进一步的,还包括:质量分析模块,运行在所述处理器上,与所述质量参数数据库连接,用于运行指定算法对质量稳定性进行分析;检测差异性分析模块,运行在所述处理器上,与所述质量参数数据库和检测频率数据库连接,用于运行指定算法计算不同检测频率下检测结果的差异情况;对应性关系分析模块,运行在所述处理器上,与所述质量参数数据库和检测频率数据库连接,用于提取质量检测差异性数据和检测频率数据并拟合对应性关系曲线。
20.综上所述,本技术包括以下有益技术效果:1.通过分析得出不同检测频率对检测结果的影响能力以及检测结果的差异性情况,判断生产过程对检测频率的需求情况,提高了评价品质安全的灵活性;2.结合质量检测差异性和检测成本,对质量检测频率进行动态调整,保证了对生产过程的质量评价能力,同时控制检测成本,提高了质量评价生产实际情况的适应能力;3.通过把握生产间隔时间,防止了生产间隔过大造成生产设备及生产介质等发生偏差时传统质量检测方法无法识别品质安全问题的情况,提高了对品质安全的控制能力。
附图说明
21.图1是本技术实施例的一种自动化生产过程的品质安全识别方法的步骤图。
22.图2是本技术实施例的一种自动化生产过程的品质安全识别系统的结构图。
23.附图标记说明:1、品质安全管理平台;2、存储器;21、生产记录数据库;22、质量参数数据库;23、检测频率数据库;3、处理器;31、质量分析模块;32、检测差异性分析模块;33、对应性关系分析
模块;4、自动化生产终端。
具体实施方式
24.下面对照附图,通过对实施例的描述,本技术的具体实施方式如所涉及的各构件的形状、构造、各部分之间的相互位置及连接关系、各部分的作用及工作原理、制造工艺及操作使用方法等,作进一步详细的说明,以帮助本领域技术人员对本发明的发明构思、技术方案有更完整、准确和深入的理解。为方便说明,本技术提及方向以附图所示方向为准。
25.参照图1-图2所示,一种自动化生产过程的品质安全识别方法,其特征在于,包括以下步骤:步骤s1,收集生产及质量数据,分别收集生产记录和质量检测数据,并持续更新;步骤s2,分析质量检测记录,从质量参数稳定性,结合历史检测频率,对质量检测数据进行分析;步骤s3,动态调整检测频率,根据产品质量分析情况,对质量检测频率进行动态调整。
26.所述步骤s1包括:步骤s11,收集质量检测记录,收集历史生产过程中的质量检测记录,提取质量检测记录中的质量参数并标记质量检测时间后上传至品质安全管理平台1的质量参数数据库22中,提取质量检测记录中的质量检测频率并标记质量检测时间后上传至品质安全管理平台1的检测频率数据库23中;步骤s12,收集产品生产记录,收集历史生产过程中的产品生产记录,标记生产时间和生产间隔,并上传至品质安全管理平台1的生产记录数据库21中;步骤s13,数据更新,持续收集质量检测数据和生产记录数据,并上传至品质安全管理平台1。
27.所述步骤s2包括:步骤s21,质量稳定性分析,统计质量参数数据库22中的质量参数数值,对产品质量稳定性进行判断;步骤s22,历史检测频率分析,统计质量检测记录,标记质量检测时间和质量检测频率;步骤s23,检测频率-检测结果对应性分析,绘制产品质量检测差异性和检测频率对应性关系曲线,并进行曲线拟合;步骤s24,动态更新分析结果,实时提取品质安全管理平台1的质量参数数据库22中的质量参数,并持续更新分析结果。
28.所述步骤s21中,质量稳定性分析方法为:,其中,u表示为待分析生产过程的质量跳动指数,待分析生产过程的质量跳动指数u越大则待分析生产过程的生产质量的稳定性越差,待分析生产过程的质量跳动指数u越小则待分析生产过程的生产质量的稳定性越好;n表示为质量参数数据库22中待分析生产过程的质量检测样本的总数量;i表示为质量参数数据库22中待分析生产过程的质量检测样本的样本编号;xi表示为质量参数数据库22中待分析生产过程的编号为i的质量检测样本的质量参数值;`x表示为质量参数数据库22中待分析生产过程的所有质量检测样本的质量参数平均值。
29.所述步骤s22中,质量检测差异性的分析方法为:,其中,k
p
表示为质量检测差异指数,质量检测差异指数k
p
越大则质量检测结果的差异性越大,质量检测差异指数k
p
越小则质量检测结果的差异性越小;n表示为质量参数数据库22中待分析生产过程的质量检测样本的总数量;i表示为质量参数数据库22中待分析生产过程的质量检测样本的样本编号;xi表示为质量参数数据库22中待分析生产过程的编号为i的质量检测样本的质量参数值;p表示为检测频率变更因子,p=1,2,3...;x
i-p
表示为待分析生产过程中,在编号为i的质量检测样本前第p个质量检测样本的质量参数值;;x
i-2p
表示为待分析生产过程中,在编号为i的质量检测样本前第2p个质量检测样本的质量参数值;(t
i-t
i-2p
)表示为编号为i的质量检测样本和在编号为i的质量检测样本前第2p个质量检测样本的生产时间间隔;所述检测频率差异指数的计算方法为:,其中,s
p
表示为检测频率差异指数;p表示为检测频率变更因子,p=1,2,3...;所述步骤s23中,对应性分析方法为:不断提高p的数值,提取对应参数值导入计算,得出对应的质量检测差异指数k
p
的指数值和检测频率差异指数s
p
的指数值,并以k
p
为纵坐标,s
p
为横坐标,绘制k
p-s
p
曲线,并进行曲线拟合。
30.所述步骤s3包括:步骤s31,确认质量检测极限频率,根据生产要求确定质量检测的最低频率为质量检测极限频率;步骤s32,分析质量检测成本,统计质量检测样本的检测破坏性程度,并结合质量检测样本的检测破坏性程度判断质量检测物料成本,以及检测单个质量检测样本的时间成本;步骤s33,动态调整质量检测频率,先以质量检测极限频率进行产品质量检测,并收集质量检测数据,计算实时质量检测差异指数k,并导入k
p-s
p
拟合曲线中得出实时检测频率差异指数s,并导入s
p
计算公式得出实时检测频率变更因子p’,并将实时检测频率变更因子p’代入计算得出调整后的检测频率;所述步骤s33中,调整后质量检测频率计算方法为:,其中,λ表示为调整后的质量检测频率;λ0表示为;质量检测极限频率;p’表示为实时检测频率变更因子;c1表示为单个质量检测样本的物料成本,若产品质量检测为破坏性检测且检测后产品不可使用,则c1即为该单个产品的生产成本,若产品质量检测为非破坏性检测且检测后产品可继续使用,则c1即为0;c2表示为单个质量检测样本的质量检测成本,具体为检测单个质量检测样本所需时间的人工成本、检测耗材成本、设备占用成本;l表示为该产品的单价;所述步骤s33中,质量检测频率始终大于步骤s31中确认的质量检测极限频率。
31.所述步骤s33中,若不同生产过程的生产间隔超出设定阈值,则提高对产品质量的检测频率,直至质量检测结果的质量稳定性满足合格区间,则恢复至通过k
p-s
p
拟合曲线确定的检测频率。
32.一种自动化生产过程的品质安全识别系统,包括:品质安全管理平台1和与品质安全管理平台1连接的自动化生产终端4;所述品质安全管理平台1包括:存储器2;处理器3,与处理器3连接;生产记录数据库21,设置在所述存储器2内,用于存储生产记录数据及对应时间信息;质量参数数据库22,设置在所述存储器2内,用于存储质量参数数据及对应时间信息;检测频率数据库23,设置在所述存储器2内,用于存储检测频率数据及对应时间信息;所述自动化生产终端4用于接收指令信息并控制自动化生产线运行状态,并上传生产记录数据至生产记录数据库21。
33.还包括:质量分析模块31,运行在所述处理器3上,与所述质量参数数据库22连接,用于运行指定算法对质量稳定性进行分析;检测差异性分析模块32,运行在所述处理器3上,与所述质量参数数据库22和检测频率数据库23连接,用于运行指定算法计算不同检测频率下检测结果的差异情况;对应性关系分析模块33,运行在所述处理器3上,与所述质量参数数据库22和检测频率数据库23连接,用于提取质量检测差异性数据和检测频率数据并拟合对应性关系曲线。
34.本技术实施例,一种自动化生产过程的品质安全识别方法及系统的工作原理为:首先分析得出质量跳动情况,由数据跳动情况判断生产质量是否需要进行质量检测频率调整,再分析得出不同检测频率对检测结果的影响能力以及检测结果的差异性情况,判断生产过程对检测频率的需求情况,生产过程的质量检测差异性较大则需要更高的检测频率评价品质安全,生产过程的质量检测差异性较小则需要更高的检测频率评价品质安全,提高了评价品质安全的灵活;并结合质量检测差异性和检测成本,对质量检测频率进行动态调整,保证了对生产过程的质量评价能力,同时控制检测成本,提高了质量评价生产实际情况的适应能力。
35.本技术实施例中,通过把握生产间隔时间,防止了生产间隔过大造成生产设备及生产介质等发生偏差时传统质量检测方法无法识别品质安全问题的情况,提高了对品质安全的控制能力。
36.以上示意性地对本发明及其实施方式进行了描述,该描述没有限制性,附图所示的也只是本发明的实施方式之一,实际的结构并不局限与此。所以,如果本领域的普通技术人员受其启示,在不脱离本发明创造宗旨的情况下,不创造性地设计出与该技术方案相似的结构方式及实施例,均应属于本发明的保护范围。