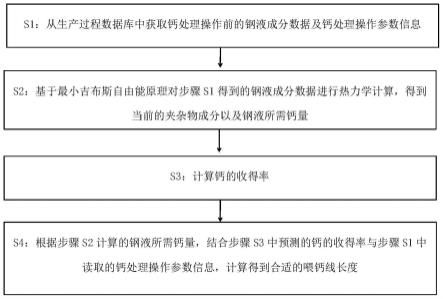
1.本发明属于钢铁冶金钢液精炼领域,具体涉及一种基于最小吉布斯自由能法计算钢液钙线喂入量的方法。
背景技术:2.在钢液的冶炼过程中,铝作为一种强脱氧剂可以有效地将钢液中的氧降低至较低水平。但铝的加入会生成大量的氧化铝夹杂物,导致水口结瘤,影响连铸过程的顺行以及导致产品质量的下降。因此,在大多数使用铝脱氧的钢种中,将比铝活泼的金属钙加入到钢液中以将钢液中的氧化铝夹杂物改性为液态的钙铝酸盐,减少水口结瘤及堵塞问题,保证连铸顺行,提高产品质量。同时,钢中钙的存在也可以控制钢凝固、冷却及加热过程中mns夹杂物的形态及数量。然而,钢中的需钙量存在一个合理的范围,不能过高也不能过低。
3.钢液中合理的需钙量与钢液温度、钢液成分以及钢种等条件有关,不同的生产炉次钢液的需钙量有所不同,目前几乎所有企业钙处理操作都是根据经验进行,缺乏一个科学合理的指导,因此钢中钙含量控制不稳定。因此,基于最小吉布斯自由能原理计算当前钢液中的夹杂物成分以及合适的钙含量,最终得到合适的喂钙线长度,实现钙处理操作的精准控制,对降低企业生产及运行成本、提高产品质量及合金利用效率具有重要的研究价值及意义。
技术实现要素:4.为了解决上述现有技术的不足,本发明提供一种基于最小吉布斯自由能法计算钢液钙线喂入量的方法,实现对钙处理操作的精准控制。
5.具体地,本发明提供一种基于最小吉布斯自由能法计算钢液钙线喂入量的方法,其包括以下步骤:
6.s1:从生产过程数据库中获取钙处理操作前的钢液成分数据及钙处理操作参数信息;
7.s2:基于最小吉布斯自由能原理对步骤s1得到的钢液成分数据进行热力学计算,得到当前的夹杂物成分以及钢液所需钙量,具体包括如下步骤:
8.s21:基于最小吉布斯自由能原理计算钢液中非金属夹杂物的成分,使用的公式如下:
[0009][0010]
式中,min.gs为体系的最小吉布斯自由能,为组分i的标准摩尔吉布斯自由能,ai为组分i的活度,组分i包括固体夹杂物相,液体夹杂物相以及钢液相,m为钢液中的组分,r为气体常数,t为钢液温度,slag为钢液中的液体夹杂物,solid为钢液中的固体夹杂物;
[0011]
s22:计算固体夹杂物相、液体夹杂物相以及铁液相中的吉布斯自由能,其中,计算
固体相中吉布斯自由能的公式如下:
[0012][0013]
计算液体相夹杂物中吉布斯自由能的公式如下:
[0014][0015]
计算铁液相中吉布斯自由能的公式如下:
[0016][0017]
式中,c为钢-夹杂物体系中的组分数,x为钢液中元素的摩尔分数,γ为钢液中元素的活度系数;
[0018]
s23:计算固体夹杂物相中夹杂物的活度值以及液体夹杂物相中夹杂物的活度值,固体夹杂物相中夹杂物的活度值为1,液体夹杂物相中夹杂物的活度值根据如下公式计算:
[0019][0020][0021]
式中:为液相夹杂物中al2o3的活度,a
cao
为液相夹杂物中cao的活度,为液相夹杂物中al2o3的质量分数;
[0022]
s24:计算钢液中夹杂物的成分和含量,将公式(2)~(6)代入到公式(1)中,并添加约束条件,约束条件中计算当前夹杂物的成分时输入的变量为钢液的成分,通过求公式(1)的解,求解得到当前钢液中夹杂物的成分及含量,并以将夹杂物控制在液相区为条件计算钢液所需钙量;
[0023]
s3:计算钙的收得率:对钙处理过程中钙的收得率进行预测或计算得到钙的收得率;
[0024]
s4:根据步骤s2计算的钢液所需钙量,结合步骤s3中预测的钙的收得率与步骤s1中读取的钙处理操作参数信息,计算得到合适的喂钙线长度;
[0025]
计算喂钙线长度的公式如下:
[0026][0027]
式中:l为喂钙线长度,单位为m;w为钢水重量,单位为t;n[ca]
t
为根据步骤s2计算的钢液所需钙量,单位为%;n[ca]o为钙处理前钢液中钙含量,单位为%;m
ca
为钙的摩尔质量,单位为g/mol;m
fe
为铁的摩尔质量,单位为g/mol;η为钙的收得率,单位为%;β单位为为钙线中钙元素的含量,单位为%;μ为钙线米重,单位为g/m。
[0028]
优选地,步骤s2中计算当前夹杂物的成分时输入的变量为钢液的成分,满足如下约束条件:
[0029]
[0030][0031][0032]
∑ns=n
[s]
+n
cas
ꢀꢀ
(11)
[0033]
式中:∑n
ca
为体系中钙元素的总摩尔数,n
[ca]
为钢液相中溶解钙的摩尔数,n
[al]
为钢液相中溶解铝的摩尔数,n
[o]
为钢液相中溶解氧的摩尔数,n
[s]
为钢液相中溶解硫的摩尔数,n
cao
为夹杂物中cao的摩尔数,n
cas
为夹杂物中cas的摩尔数,为夹杂物中的摩尔数,为夹杂物中cao
·
6al2o3的摩尔数,n
ca2
为夹杂物中cao
·
2al2o3的摩尔数。
[0034]
优选地,步骤s1中所的钙处理操作参数包括钢液c含量、钢液si含量、钢液mn含量、钢液p含量、钢液s含量、钢液ca含量、钢液al含量、钢液氧含量、钢液温度、钙线米重、钙线钙含量和钢液重量。
[0035]
优选地,步骤s3中可以根据当前的钢液[o]含量预测钙的收得率,或者根据神经网络模型进行预测。
[0036]
步骤s3中钙的收得率能够根据神经网络模型进行预测或者根据当前的钢液[o]含量预测,根据氧含量预测的计算公式为:
[0037]
y=50000*xo+10
ꢀꢀ
(12)
[0038]
式中:xo为钢液[o]含量,y为根据氧含量预测的收得率η。
[0039]
优选地,所述神经网络模型为浅层神经网络模型或深层神经网络模型。
[0040]
与现有技术相比,本发明的有益效果:
[0041]
本发明提供的基于最小吉布斯自由能法计算钢液钙线喂入量的方法,通过实时获取每一炉次的钢液成分及钙处理操作参数信息,预测当前钢液中的夹杂物成分以及钢液中合适的需钙量,最终结合钙线钙含量、钙线米重、收得率等操作参数信息得到合适的钙线喂入量。通过本模型中基于吉布斯自由能最小原理计算钢中的夹杂物成分以及计算得到钙处理过程合适的喂钙线长度,能够实现对钙处理操作的科学合理指导,减少由于凭借经验进行喂钙带来的误差,有利于稳定钙处理操作过程,保证企业生产顺行,降低生产成本,提高生产效率以及产品质量。
附图说明
[0042]
图1是本发明的整体流程示意图;
[0043]
图2是根据本发明实施的一种基于最小吉布斯自由能法计算钢液钙线喂入量的方法流程示意图;
[0044]
图3是本发明实施例中最小吉布斯自由能原理计算钢中夹杂物成分的流程示意图;
[0045]
图4是本发明实施例中基于最小吉布斯自由能原理计算的钢中钙含量对夹杂物的影响示意图。
具体实施方式
[0046]
以下将参考附图详细说明本发明的示例性实施例、特征和方面。附图中相同的附
图标记表示功能相同或相似的元件。尽管在附图中示出了实施例的各种方面,但是除非特别指出,不必按比例绘制附图。
[0047]
根据本发明的实施例,提供了一种基于最小吉布斯自由能法计算钢液钙线喂入量的方法
[0048]
其包括以下步骤:
[0049]
s1:从生产过程数据库中获取钙处理操作前的钢液成分数据及钙处理操作参数信息;
[0050]
s2:基于最小吉布斯自由能原理对步骤s1得到的钢液成分数据进行热力学计算,得到当前的夹杂物成分以及钢液所需钙量,具体包括如下步骤:
[0051]
s21:基于最小吉布斯自由能原理计算钢液中非金属夹杂物的成分,使用的公式如下:
[0052][0053]
式中,min.gs为体系的最小吉布斯自由能,为组分i的标准摩尔吉布斯自由能,ai为组分i的活度,组分i包括固体夹杂物相,液体夹杂物相以及钢液相,m为钢液中的组分,r为气体常数,t为钢液温度,slag为钢液中的液体夹杂物,solid为钢液中的固体夹杂物;
[0054]
s22:计算固体夹杂物相、液体夹杂物相以及铁液相中的吉布斯自由能,其中,计算固体相中吉布斯自由能的公式如下:
[0055][0056]
计算液体相夹杂物中吉布斯自由能的公式如下:
[0057][0058]
计算铁液相中吉布斯自由能的公式如下:
[0059][0060]
式中,c为钢-夹杂物体系中的组分数,x为钢液中元素的摩尔分数,γ为钢液中元素的活度系数;
[0061]
s23:计算固体夹杂物相中夹杂物的活度值以及液体夹杂物相中夹杂物的活度值,固体夹杂物相中夹杂物的活度值为1,液体夹杂物相中夹杂物的活度值根据如下公式计算:
[0062][0063][0064]
式中:为液相夹杂物中al2o3的活度,a
cao
为液相夹杂物中cao的活度,为液相夹杂物中al2o3的质量分数;
[0065]
s24:计算钢液中夹杂物的成分和含量,将公式(2)~(6)代入到公式(1)中,并添加
约束条件,约束条件中计算当前夹杂物的成分时输入的变量为钢液的成分,通过求公式(1)的解,求解得到当前钢液中夹杂物的成分及含量,并以将夹杂物控制在液相区为条件计算钢液所需钙量;
[0066]
s3:计算钙的收得率:对钙处理过程中钙的收得率进行预测或计算得到钙的收得率;
[0067]
s4:根据步骤s2计算的钢液所需钙量,结合步骤s3中预测的钙的收得率与步骤s1中读取的钙处理操作参数信息,计算得到合适的喂钙线长度;
[0068]
计算喂钙线长度的公式如下:
[0069][0070]
式中:l为喂钙线长度,单位为m;w为钢水重量,单位为t;n[ca]
t
为根据步骤s2计算的钢液所需钙量,单位为%;n[ca]o为钙处理前钢液中钙含量,单位为%;m
ca
为钙的摩尔质量,单位为g/mol;m
fe
为铁的摩尔质量,单位为g/mol;η为钙的收得率,单位为%;β单位为为钙线中钙元素的含量,单位为%;μ为钙线米重,单位为g/m。
[0071]
优选地,步骤s2中计算当前夹杂物的成分时输入的变量为钢液的成分,满足如下约束条件:
[0072][0073][0074][0075]
∑ns=n
[s]
+n
cas
ꢀꢀ
(11)
[0076]
式中:∑n
ca
为体系中钙元素的总摩尔数,n
[ca]
为钢液相中溶解钙的摩尔数,n
[al]
为钢液相中溶解铝的摩尔数,n
[o]
为钢液相中溶解氧的摩尔数,n
[s]
为钢液相中溶解硫的摩尔数,n
cao
为夹杂物中cao的摩尔数,n
cas
为夹杂物中cas的摩尔数,为夹杂物中al2o3的摩尔数,为夹杂物中cao
·
6al2o3的摩尔数,n
ca2
为夹杂物中cao
·
2al2o3的摩尔数。
[0077]
优选地,步骤s1中所钢液成分信息及操作参数包括钢液c含量、钢液si含量、钢液mn含量、钢液p含量、钢液s含量、钢液ca含量、钢液al含量、钢液氧含量、钢液温度、钙线米重、钙线钙含量、钢液重量。
[0078]
优选地,步骤s3中对钙处理过程中钙的收得率进行预测需要的参数包括钢液c含量、钢液si含量、钢液mn含量、钢液p含量、钢液s含量、钢液ca含量、钢液al含量、钢液温度、喂线速度、吹氩流量。
[0079]
钙的收得率η可以通过浅层神经网络或深层神经网络预测计算得到,或者通过当前的钢液[o]含量预测钙的收得率。
[0080]
在一个实施例中,可以根据当前的钢液[o]含量预测钙的收得率,钙的收得率可以直接通过如下公式计算:
[0081]
y=50000*xo+10
[0082]
式中:xo为钢液[o]含量,y为根据氧含量预测的收得率η。
[0083]
在实际计算过程中,也可以通过申请人之前申请的基于深度神经网络的钙处理过程中钙的收得率的预测方法来预测计算钙的收得率,在此不再赘述。
[0084]
具体实施例1
[0085]
如图2及图3所示,根据本发明实施例的基于最小吉布斯自由能法计算钢液钙线喂入量的方法,包括以下步骤:
[0086]
s1:与现场生产过程数据库建立连接,确定钙处理操作前的钢液成分及钙处理操作参数信息:c=0.06%、si=0.08%、mn=1.4%、p=0.002%、s=0.0035%、ca=0.0021%、al=0.083%、t.o=0.007%、[o]=0.0003%、钢液温度t=1873k、钙线米重200g/m,钙线钙含量40%,钢液重量100t。
[0087]
s2:基于最小吉布斯自由能原理对步骤s1得到的钢液成分数据进行热力学计算,计算得到当前的夹杂物成分以及钢中合适的需钙量。
[0088]
s3:对钙处理过程中钙的收得率进行预测。
[0089]
s4:根据步骤s2计算的钢液中合适的需钙量,结合步骤s3中预测的钙的收得率与步骤s1中读取的操作参数信息,计算得到合适的喂钙线长度。
[0090]
进一步的,步骤s2中基于最小吉布斯自由能原理计算钢中非金属夹杂物的成分,使用的公式函数如下:
[0091][0092]
式中,min.gs为体系的最小吉布斯自由能,为组分i的标准摩尔吉布斯自由能,使用的数据如表1所示,ai为组分i的活度,组分i包括固体夹杂物相,液体夹杂物相以及钢液相。
[0093]
表1钢-夹杂物体系中各物质的标准摩尔吉布斯自由能
[0094]
[0095]
计算固体相中吉布斯自由能的公式如下:
[0096][0097]
计算液体相夹杂物中吉布斯自由能的公式如下:
[0098][0099]
计算铁液相中吉布斯自由能的公式如下:
[0100][0101]
进一步的,固体夹杂物相中夹杂物的活度值为1,液体夹杂物相中夹杂物的活度值根据如下公式计算:
[0102][0103][0104]
式中:为液相夹杂物中al2o3的活度,a
cao
为液相夹杂物中cao的活度,为液相夹杂物中al2o3的质量分数。
[0105]
步骤s2中,计算当前夹杂物的成分时输入的变量为钢液的成分,满足如下约束条件:
[0106][0107][0108][0109]
∑ns=n
[s]
+n
cas
ꢀꢀ
(11)
[0110]
式中:∑n
ca
为体系中钙元素的总摩尔数,n
[ca]
为钢液相中溶解钙的摩尔数,n
[al]
为钢液相中溶解铝的摩尔数,n
[o]
为钢液相中溶解氧的摩尔数,n
[s]
为钢液相中溶解硫的摩尔数,n
cao
为夹杂物中cao的摩尔数,n
cas
为夹杂物中cas的摩尔数,为夹杂物中al2o3的摩尔数,为夹杂物中cao
·
6al2o3的摩尔数,n
ca2
为夹杂物中cao
·
2al2o3的摩尔数。
[0111]
将公式(2)~(6)代入到公式(1)中,通过matlab求公式(1)的解,求解得当前钢液中含有0.0021%的cao
·
6al2o3和0.0024%的cao
·
2al2o3,为将夹杂物控制在液相区,钢液的需钙量为0.0018%~0.0027%。
[0112]
进一步的,步骤s3中根据当前的钢液[o]含量预测钙的收得率,钢液含量与钙的收得率通过如下公式计算:
[0113]
y=50000*xo+10
[0114]
式中:xo为钢液[o]含量,y为根据氧含量预测的收得率η。
[0115]
钢液中[o]含量为0.0003%,计算的钙的收得率为25%。
[0116]
进一步的,步骤s2计算的目标钙含量为0.0018%-0.0027%,根据如下公式计算当
前钢液中合适的喂钙线长度:
[0117][0118]
式中:χ为喂钙线长度,m;w为钢水重量,t;ω[ca]
t
为根据步骤s2计算的目标钙含量,%;ω[ca]o为钙处理前钢液中钙含量,%;m
ca
为钙的摩尔质量,g/mol;m
fe
为铁的摩尔质量,g/mol;η为钙收得率,%;β为钙线中钙元素的含量,%;μ为钙线米重,g/m。
[0119]
根据公式计算的当前的合适喂钙线长度为:40-70m.
[0120]
实施例2
[0121]
如图2所示,根据本发明实施例的基于最小吉布斯自由能法计算钢液钙线喂入量的方法,包括以下步骤:
[0122]
s1:与现场生产过程数据库建立连接,确定钙处理操作前的钢液成分及钙处理操作参数信息:c=0.06%、si=0.08%、mn=1.4%、p=0.002%、s=0.0035%、ca=0.0020%、al=0.083%、t.o=0.007%、[o]=0.0003%、钢液温度t=1873k、钙线米重200g/m,钙线钙含量40%,钢液重量100t。
[0123]
s2:基于最小吉布斯自由能原理对步骤s1得到的钢液成分数据进行热力学计算,计算得到当前的夹杂物成分以及钢中合适的需钙量;
[0124]
s3:对钙处理过程中钙的收得率进行预测;
[0125]
s4:根据步骤s2计算的钢液中合适的需钙量,结合步骤s3中预测的钙的收得率与步骤s1中读取的操作参数信息,计算得到合适的喂钙线长度;
[0126]
进一步的,步骤s2中基于最小吉布斯自由能原理计算钢中非金属夹杂物的成分,使用的公式函数如下:
[0127][0128]
式中,min.gs为体系的最小吉布斯自由能,为组分i的标准摩尔吉布斯自由能,使用的数据如表1所示,ai为组分i的活度,组分i包括固体夹杂物相,液体夹杂物相以及钢液相。
[0129]
表2钢-夹杂物体系中各物质的标准摩尔吉布斯自由能
[0130][0131]
计算固体相中吉布斯自由能的公式如下:
[0132][0133]
计算液体相夹杂物中吉布斯自由能的公式如下:
[0134][0135]
计算铁液相中吉布斯自由能的公式如下:
[0136][0137]
进一步的,固体夹杂物相中夹杂物的活度值为1,液体夹杂物相中夹杂物的活度值根据如下公式计算:
[0138][0139][0140]
式中:为液相夹杂物中al2o3的活度,a
cao
为液相夹杂物中cao的活度,为液相夹杂物中al2o3的质量分数。
[0141]
步骤s2中,计算当前夹杂物的成分时输入的变量为钢液的成分,满足如下约束条件:
[0142][0143][0144]
[0145]
∑ns=n
[s]
+n
cas
ꢀꢀ
(11)
[0146]
式中:∑n
ca
为体系中钙元素的总摩尔数,n
[ca]
为钢液相中溶解钙的摩尔数,n
[al]
为钢液相中溶解铝的摩尔数,n
[o]
为钢液相中溶解氧的摩尔数,n
[s]
为钢液相中溶解硫的摩尔数,n
cao
为夹杂物中cao的摩尔数,n
cas
为夹杂物中cas的摩尔数,为夹杂物中al2o3的摩尔数,为夹杂物中cao
·
6al2o3的摩尔数,n
ca2
为夹杂物中cao
·
2al2o3的摩尔数。
[0147]
将公式(2)~(6)代入到公式(1)中,通过matlab求公式(1)的解,求解得当前钢液中夹杂物全部为液态的钙铝酸盐,利用约束条件将夹杂物控制在目标区域内,钢液的需钙量为0.0018%~0.0027%,图4根据吉布斯自由能最小原理计算的钢中钙含量对夹杂物的影响。
[0148]
进一步的,根据实施例1中的计算钙含量的方法计算出当前钢液中的钙含量为0.002%,在0.0018%~0.0027%范围内,因此钢液不需要喂钙,合适的喂钙线长度为:0m。
[0149]
最后应说明的是:以上所述的各实施例仅用于说明本发明的技术方案,而非对其限制;尽管参照前述实施例对本发明进行了详细的说明,本领域的普通技术人员应当理解:其依然可以对前述实施例所记载的技术方案进行修改,或者对其中部分或全部技术特征进行等同替换;而这些修改或替换,并不使相应技术方案的本质脱离本发明各实施例技术方案的范围。