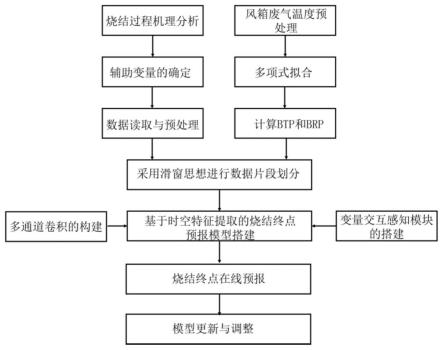
1.本发明属于烧结过程烧结终点提前预报的软测量方法,具体涉及一种基于时空特征提取的烧结终点预报方法。
背景技术:2.钢铁行业作为衡量国家综合实力和经济发展水平的重要产业,不但是国家生存和发展的保障,而且是国民经济的支柱。目前我国长流程的高炉炼钢生产仍占钢铁生成的主导地位,在高炉炼铁过程中,主要原料为烧结矿,它的入炉比重高达70%左右,铁水的质量与其产量和质量息息相关,烧结矿的稳定和优质生产也保证了炼铁过程的顺利进行。因此,作为获取烧结矿的主要途径,烧结过程是高炉炼铁流程中的关键环节。
3.随着“双碳”目标的提出,我国的发展战略中也正式包含了减少碳排放这一工作。而冶金行业作为高能耗、高排放的重工业,其结构的改造和转型已经是刻不容缓。如今,钢铁企业的改革正在快步进行,而高炉炼铁生产技术的提高和进步,主要取决于入炉原料性能的改善,所以改善烧结矿的生产已经是不可逆转的趋势。
4.烧结过程(包括配料、点火、燃烧和冷却四大部分)是一项涉及传质、传热和物理化学反应的复杂工业过程。烧结终点(burning through point,btp)为烧结材料层从上到下烧穿时对应的风箱所在位置。烧结终点反映了当前烧结过程的质量,烧结终点偏离预设值,会出现未烧透和过烧的情况,这不仅会影响到烧结矿的产量,还会造成烧结机的损坏,这就增加了维护成本,同时还会减少烧结机的运行效率。烧结过程的控制,实际就是对烧结终点进行控制,使烧结终点稳定在倒数第二个风箱位置处。但由于受到反应过程中各类物质的影响,导致参数变化多端,而且很难预测随机干扰因素,这也使得烧结终点的预测控制成为了烧结过程的一大难点。如今国内烧结厂对烧结终点的把控依旧离不开人工看火,但是人工操作过度依赖于个人的工作经验,员工的调换等都容易出现问题,且个人操作带有较大盲目性,很容易导致烧结终点控制的效果不理想。
5.因此开发一套烧结专家系统的烧结终点预测模型,用于对烧结终点的预测控制有重大意义。实现对烧结终点位置的精确预测不但可以保证烧结过程各环节的稳定运行,使前后工序互不干扰、高效运作,还能确保有效地利用烧结面积,提高烧结矿的产量、节约能耗。
6.因此,根据烧结过程的实时过程参数、状态参数及操作参数,合理判断烧结过程,并准确预报烧结终点位置,以调整烧结机台车速度,达到稳定烧结终点,减少烧终点位置波动,提高烧结矿产量、质量的控制目的。及时预报烧结终点对于合理利用现有烧结设备,稳定烧结生产,促进烧结控制水平的提离化及提高烧结厂经济效益具有十分重要的意义。
技术实现要素:7.本发明针对烧结过程终点难以提前预报的问题,创新性地将深度学习框架编码解码网络引入烧结领域,提出了基于时空特征提取的烧结终点预报方法。主要包括以下四个
步骤:首先,通过机理分析和专家知识,选取与烧结终点相关的变量,并从数据库里面读取和预处理;然后,读取风箱废弃温度,并对温度数据进行预处理,采用多项式拟合法计算btp;随后,采用滑窗思想构建数据集,搭建时空特征提取网络捕获数据的隐藏特征,并将得到的时空特征输入到解码网络中,实现对烧结终点的多步提前预测;最后,对模型结果进行调试,并在实际工业现场检验。
8.本发明采用以下技术方案实现:
9.本发明首先提供了一种基于时空特征提取的烧结终点预报方法,其包括如下步骤:
10.1)从时序数据库中读取辅助变量数据,并对数据的异常值和空值进行预处理;此外,从时序数据库中读取烧结机的风箱废气的温度,并利用多项式拟合法求出烧结终点和温度上升点的位置;将辅助变量和温度上升点的位置作为输入特征,将烧结终点作为标签;
11.2)根据已经处理的输入特征和计算得到标签,利用滑窗思想对数据进行片段划分,以此构造训练集、验证集和测试集;滑窗的历史时间片段长度为th,未来时间片段的长度为tf;
12.3)搭建基于时空特征提取的烧结终点预报模型
13.4)假设当前时刻为t0,实时读取t
0-th至t0时刻的辅助变量数据,并进行异常值和空值的预处理;同时读取t
0-th至t0时刻的风箱废气温度数据,利用多项式拟合法计算烧结终点和温度上升点;然后将输入特征和标签进行匹配,利用滑窗思想对数据实时处理,构造t
0-th至t0时刻的历史数据集;并将该数据集输入建立的终点预报模型进行训练,最后将训练完成的模型用于预测未来时间长度tf内的烧结终点的位置。
14.作为本发明的优选方案,所述的步骤1)中,辅助变量选取为:中和矿配比、生石灰配比、石灰石配比、白云水配比、二混含水量、料厚、点火温度、主抽负压、台车速度、大烟道废气温度和温度上升点的位置;其中,除温度上升点的位置外的其余辅助变量均从数据库中存储的烧结过程数据中获取。然后通过编码解码网络建立以辅助变量为输入,烧结终点位置为输出的映射关系,用于烧结终点的预报。
15.作为本发明的优选方案,步骤1)中,所述从数据库中读取风箱废气的温度,并利用多项式拟合法求出烧结终点和温度上升点的位置,具体为:
16.并利用多项式拟合法求出烧结终点和温度上升点的位置,具体计算流程为:
17.在烧结终点附近风箱废气温度与风箱位置(风箱号)呈二次函数关系,因此可根据包括最高温度在内的三个点拟合二次曲线来求得btp值。风箱位置xi与风箱废气温度ti满足的二次函数关系即如式(1)所示(其中a、b、c为系数)。
18.ti=ax
i2
+bxi+c
ꢀꢀꢀ
(1)
19.代入包含温度最高点的相邻三个风箱温度值(x1,t1),(x2,t2),(x3,t3),其中(x2,t2)为温度最高点,于是可以得出式(2)的关系。
[0020][0021]
将等式(2)中的等式一和等式二代入二次函数关系中简化,可得式(3)。
[0022][0023]
由公式(3)中后式减前式,整理可得式(4)。
[0024][0025]
将式(4)中两式相减,得式(5)。
[0026][0027]
将式(5)代入式(4)中第一个等式,得式(6)。
[0028][0029]
为求式(1)的极值,令式(7)成立。
[0030][0031]
于是可以得到:
[0032][0033]
在烧结现场,由于烧结机机尾风箱的密封措施不完善,存在漏风现象,使得风箱废气温度的测量值小于真实值。为了保证烧结终点计算的准确性,引入一个修正系数,大烟道反馈系数,如下公式:
[0034]
btpm=btp
′‑
αδt
ꢀꢀꢀ
(9)
[0035]
该式中,btpm为btp的修正值,btp
′
为烧结终点的计算值,即式(8)中得到的btp,δt为废气温度的测量值与真实值之间的温度偏差,α为修正系数,一般取0.02。
[0036]
温度上升点(brp)是指沿烧结机长度方向废气温度上升的位置,废气温度为180℃时(tk=180),对应的位置xk;根据下列公式求解:
[0037][0038]
作为本发明的优选方案,步骤2)中,采用滑动时间窗片段方法进行采样,每个样本片段可以表示成矩阵:
[0039]
[0040]
其中,th是观测段片段帧数;tf是未来预测片段数目;m代表辅助变量的个数;对于每个输入样本x,对应了一个输出样本y:
[0041][0042]
优选的,步骤3)中,所述的搭建基于时空特征提取的烧结终点预报模型,具体为:采用encoder-decoder框架进行建模,其中编码网络主要用于时空特征的抽取,包括两个模块:多通道时间卷积mtcn和变量交互感知模块vaim。多通道时间卷积通过堆叠多个一维因果扩张卷积,用于提取样本内部的时序特征;变量交互感知模块vaim通过计算每个变量的耦合度,提取变量之间的空间特征;然后对这两种提取的特征进行融合。在解码网络中,采用高效的门控循环网络gru进行搭建,然后将编码网络提取的时空特征输入到解码中,进而实现烧结终点的多步预测。
[0043]
优选的,根据烧结过程中的实时数据,烧结终点预报模型的参数实时调整,不断优化迭代,使得模型具有较强的鲁棒性。
[0044]
本发明的有益效果在于:
[0045]
1、所提方法将烧结终点预测问题定义为一个多对多地时间序列问题,创新性地利用编码解码网络对烧结终点进行建模,对提高烧结终点的稳点控制,维持烧结过程的正常运行,都具有指导性意义。
[0046]
1、所提方法充分考虑了数据的动态性,采用多通道卷积提取数据的时序特征,可以提高模型预测的准确率。
[0047]
2、该方法还考虑的变量之间的空间位置关系,提出了变量交互感知模块用于提取烧结过程的空间关系,提高模型的鲁棒性。
附图说明
[0048]
图1为基于时空特征提取的烧结终点预报模型构建与应用图;
[0049]
图2为烧结过程变量分类图;
[0050]
图3风箱尾气温度拟合图;
[0051]
图4数据片段划分示意图;
[0052]
图5多通道卷积示意图;
[0053]
图6变量交互感知模块示意图;
[0054]
图7基于时空特征提取的烧结终点预报模型示意图。
具体实施方式
[0055]
下面结合附图和实施例对本发明作进一步详细描述,需要指出的是,以下所述实施例旨在便于对本发明的理解,而对其不起任何限定作用。
[0056]
图1提供了基于时空注意力机制的时空特征提取的烧结终点预报模型的具体构建与应用步骤,
[0057]
1)从时序数据库中读取辅助变量数据,并对数据的异常值和空值进行预处理;此外,从时序数据库中读取烧结机的风箱废气的温度,并利用多项式拟合法求出烧结终点和温度上升点的位置;将辅助变量和温度上升点的位置作为输入特征,将烧结终点作为标签;
[0058]
2)根据已经处理的输入特征和计算得到标签,利用滑窗思想对数据进行片段划
分,以此构造训练集、验证集和测试集;滑窗的历史时间片段长度为th,未来时间片段的长度为tf;
[0059]
3)搭建基于时空特征提取的烧结终点预报模型
[0060]
4)在当前时刻k,通过传感器和数据库实时读取k-th至k时刻的在线历史数据,搜集辅助变量,并进行预处理;同时读取k-th至k时刻的风箱废气温度数据,利用最小二乘法计算烧结终点和温度上升点;使用滑窗方法获得数据片段,构造k-th至k时刻的多对多序列数据集;将多对多序列数据集输入训练后的烧结终点预报模型,得到k时刻起的下一段预测时间长度tf内的烧结终点预报结果。在本发明的一个具体实施例中,k-th至k时刻的时间宽度可以取45min(th=45),时间长度tf可以为10min(tf=10)。
[0061]
以下结合具体案例对本发明做进一步的说明。
[0062]
(1)烧结机理与特点分析
[0063]
本次实验针对中国华南某钢铁集团的360平方米烧结机。烧结过程是将原料制成烧结矿的工序。烧结过程首先将精矿、返矿、焦炭、石灰石等各种粉状含铁原料、燃料和溶剂混合,加入适量的水并预热。接着经过布料器均匀地在烧结机台车上铺开,形成混合料层。下一步在烧结机上通过点火器点燃混合料,混合料不断燃烧且沿着台车缓慢向卸料端移动,同时抽风机抽风使空气进入,帮助混合料燃烧,使物料发生物理化学变化,直至矿粉颗粒黏结成块。最后将烧好的烧结矿卸下冷却后粉碎送入高炉进行下一工序(其中符合要求的烧结矿被返回进行再加工)。烧结过程具体流程见图。
[0064]
烧结过程由于其含有大量复杂的流程步骤,有如下一些特征。
[0065]
(1.1)大滞后性
[0066]
烧结是一个连续生产的工业过程,从配料的混合开始到烧结矿化的整个过程大约需要一个小时左右。在烧结过程的控制中,一个控制参数的变化调整,其导致的效果往往要到半小时甚至几个小时后才能知道。这都导致了烧结过程具有大滞后性。
[0067]
(1.2)强耦合性
[0068]
烧结过程中参数较多,又由于各个流程间的牵制影响,使得混合槽内料位、烧结终点位置、混合料物料成分配比、含水量、透气性等变量都互相干扰。通常,一个操作变量的变化容易同时导致多个控制变量一起变化。例如改变烧结机机速来调整烧结终点位置的操作,就会引起环冷机速度、板式给矿机速度、给料机转速的同时变化,进而同时改变了混合料料槽料位的变化,也就对原料成分参数产
[0069]
(1.3)不确定性
[0070]
由于设备和装置的限制,许多烧结过程中的重要参数无法被测量,比如衡量烧结质量的决定性指标btp和透气性等。这导致了烧结过程存在很大的不确定性。再者,烧结过程长时间暴露在空气中,其间的环境因素时刻变化,产生了难以计数的外部扰动,例如风压等高频微弱扰动,这也增加了可测量参数中的不确定性。生了影响。
[0071]
(2)烧结过程变量构建
[0072]
烧结过程是一个机理复杂、影响因素众多、不确定性、强非线性、大滞后性、高耦合性的动态时变过程。为了更好地理解烧结过程与变量的关系,这里对烧结过程变量进行了系统性的归纳,如图2所示。通过机理分析和专家知识,选择与烧结终点btp相关的辅助变量有12个,见表1所示。
[0073]
表1模型输入参数与烧结终点位置
[0074][0075]
(3)数据预处理与btp的计算
[0076]
烧结是一个完全暴露在空气中不断燃烧的过程,其高温、多粉尘等特性导致了烧结过程的复杂性和动态性。其中各种干扰噪声以及检测设备的故障等情况的产生,不可避免地会造成检测数据的异常,这些脏乱的数据若直接拿来运用于软测量模型,定会造成模型精度的下降。因此,在搭建软测量模型之前,需要先对测量得到的风箱废气温度进行数据预处理,用来平滑数据,减小噪声带来的影响。
[0077]
(3.1)限幅滤波
[0078]
根据烧结厂的生产经验,首先确定每次检测风箱废气温度可能产生的最大偏差值,即比较相邻时刻的两个温度采样值。如果两次温度采样值的偏差值超过了可以接受的最大偏差值,则认为该次测量发生了干扰,属于异常值,选择剔除;若没有超过允许的最大偏差值,那么就认为本次采样值是有效值。
[0079]
(3.2)限速滤波
[0080]
为了保证采样值的实时性以及连续性,根据三次采样值来确定采样结果。根据生产经验,先确定下来两次温度采样值之间的可能最大偏差(根据生产状况的不同需实时调整)。然后将本次采样值与之前相邻的两次采样值比较。若前一次的采样值与前两次的采样值差值绝对值小于所设定的最大偏差值δx
max
,那么取上一次的采样值作为滤波器的输出。若前一次采样值与前两次采样值差值绝对值大于设定最大值,则比较当前一次采样值与上一次采样值的差值绝对值。若大于所设最大偏差δx
max
,那么取该次采样值与上一次采样值的平均值作为滤波器的输出,否则取当前采样值作为滤波器输出。
[0081]
从数据库中读取风箱废气温度,利用风箱废气温度与烧结终点之间的数学关系建立软测量模型。在烧结生产过程中废气温度最大值出现在混合料恰好烧透的时候,由机尾部分的风箱废气温度即可找到烧结终点位置。其中风箱废气温度的曲线如图3所示。在烧结终点附近风箱废气温度与风箱位置(风箱号)呈二次函数关系,因此可根据包括最高温度在内的三个点拟合二次曲线来求得btp值。风箱位置xi与风箱废气温度ti满足的二次函数关系即如式(1)所示(其中a、b、c为系数)。
[0082]
ti=ax
i2
+bxi+c
ꢀꢀꢀ
(1)
[0083]
代入包含温度最高点的相邻三个风箱温度值(x1,t1),(x2,t2),(x3,t3),其中(x2,t2)为温度最高点,于是可以得出式(2)的关系。
[0084][0085]
将等式(2)中的等式一和等式二代入二次函数关系中简化,可得式(3)。
[0086][0087]
由公式(3)中后式减前式,整理可得式(4)。
[0088][0089]
将式(4)中两式相减,得式(5)。
[0090][0091]
将式(5)代入式(4)中第一个等式,得式(6)。
[0092][0093]
为求式(1)的极值,令式(7)成立。
[0094][0095]
于是可以得到:
[0096][0097]
在烧结现场,由于烧结机机尾风箱的密封措施不完善,存在漏风现象,使得风箱废气温度的测量值小于真实值。为了保证烧结终点计算的准确性,引入一个修正系数,大烟道反馈系数,如下公式:
[0098]
btpm=btp
′‑
αδt
ꢀꢀꢀ
(9)
[0099]
该式中,btpm为btp的修正值,btp
′
为烧结终点的计算值,即式(8)中得到的btp;δt为废气温度的测量值与真实值之间的温度偏差,α为修正系数,一般取0.02。
[0100]
温度上升点(brp)是指沿烧结机长度方向废气温度上升的位置,废气温度为180℃时(tk=180),对应的位置xk;根据下列公式求解:
[0101][0102]
(4)数据片段的划分
[0103]
采用滑动时间窗片段方法进行采样,如图4所示。采用滑动窗口的思想进行片段划分采样有两个作用:(1)直接解决了数据文件少,采集时间短的问题;(2)缩小了个别坐标数据误差对运动模式判断的影响。每个样本片段可以表示成矩阵:
[0104][0105]
其中,th是观测段片段帧数;tf是未来预测片段数目;m代表辅助变量的个数;对于每个输入样本x,对应了一个输出样本y:
[0106][0107]
这样就构建了一个序列数据集,用于后面的模型输入。
[0108]
(5)基于时空特征提取的烧结终点预报模型
[0109]
步骤1:离线建模;
[0110]
步骤1.1:通过对烧结机理分析,可以确定12个关键变量作为模型的输入特征,比如原料配比、台车速度、料层透气性和温度上升点brp等关键变量。然后从数据库中实时读取数据,并进行数据滤波处理、数据平滑处理、数据归一化处理等预处理。
[0111]
步骤1.2:从数据库中读取风箱废气的温度,并利用多项式拟合法求出烧结终点和温度上升点brp的位置。利用已有的输入特征,采用滑窗方法对数据进行片段划分,构建训练样本、验证样本和测试样本。
[0112]
步骤1.3:图5为基本循环网络以及典型的预测任务,由于烧结终点是多对多的序列预测模型,这里将使用encoder-decoder框架进行建模。首先,搭建多通道时间卷积,用于提取烧结数据的时序特征,具体如图6所示。由于烧结数据具有较强的时序性,tcn能够更好地获取时序数据的因果关系,但原始tcn只能处理一维数据,无法处理多维问题。这里,使用多个通道的卷积核组成一个卷积网,用于处理多维时序问题。多通道tcn包括因果卷积、空洞卷积和残差连接。
[0113]
因果卷积:在时间维度,因为在时序数据的处理过程中,理论上任意时刻t的输出ty实际上仅与当前时刻t以及之前输入有关,即其具有因果性(causality)。因此网络结构也应具有因果性。为了避免未来信息泄露,因果卷积采用如图所示结构,因果卷积核只对现时间点之前的输入作出相应,这样可以减少未来输入数据对计算产生的干扰。
[0114][0115]
扩张卷积:扩大卷积核意味着单个卷积核所含权重参数增多,甚至会引起模型训练难以收敛。对于其中一个维度的输入序列x和卷积核f:{0,1,2,
…
n-1},空洞卷积的计算可以定义为:
[0116][0117]
其中f(s)表示在经过一次空洞卷积计算后,新的序列在s位置上的计算结果。n表示一维卷积核的尺寸,d表示扩张因子,d=1,2,4,
…
,以2的指数幂增加,在不同卷积层空洞间隔不同。那么,新的感受野的计算公式为:
[0118]
field=(n-1)*d
ꢀꢀꢀ
(15)
[0119]
残差连接:随着网络的不断加深,会带来一些问题:(1)网络过拟合;(2)梯度消失或梯度爆炸。因此,这里引入残差网络,如图所示。假设经过第i层的输出为ai,初始输入为xi,扩张卷积层为fi(s),多通道卷积为ci,那么有:
[0120]ai
=cixi+relu(fi(s)
·
(relu(fi(s)
·
xi)))
ꢀꢀꢀ
(16)
[0121]
设mtcn的隐藏层单数数目为d
model
,那么提取的时间特征可以表示为如下矩阵:
[0122][0123]
步骤1.4:接下来,利用变量间交互感知模块vaim提取空间特征。针对多变量耦合特性,设计一种变量交互感知模块(variables interaction-aware module,viam)去获取各个变量之间的复杂耦合关系。设输入数据x可以表示为x=[x1,x2,
…
,xm]∈m
×
th,m为变量个数,th为输入时间步长。为了与前面多通道卷积输出维度保持一致,首先对原始数据进行线性映射,计算公式如下:
[0124][0125]
为了使模型在不同的表示子空间里学习到更丰富的相关信息,将原始数据映射到不同的子空间k(num_subspace),每个子空间可以表示为为了避免信息压缩损失,这里采用奇异值分解svd计算子空间的维度dk。将求得的奇异值从大到小排序,δ={δ1,δ2,
…
δu},选择奇异值中占奇异值总和95%的奇异值,即可代表整个矩阵的重要信息。说明dk个维度可以有效地表征整个矩阵的重要信息,于是可以得到子空间的维度,然后在不同的子空间计算变量间的耦合度。利用余弦相似度计算任意两个变量zi,zj之间相似性,计算公式为:
[0126][0127]
定义两个变量zi,zj之间的耦合度为:
[0128][0129]
然后,将各个子空间里面计算的耦合度进行拼接和投影变换,最终的变量间耦合度的计算矩阵为:
[0130][0131]
最后,将提取到的时间特征a和空间特征b(变量间的耦合度)进行融合,并输给解码网络decoder。这样就完成了烧结终点多步预测模型的搭建,具体方法见图7。
[0132]
步骤2:在线检测;
[0133]
步骤2.1:通过传感器和数据库实时读取在线数据,搜集辅助变量,并进行预处理,构造数据集。然后,将建立的预报模型部署在烧结专家系统里面,根据这些实时数据进行在线预报。
[0134]
步骤3:模型更新
[0135]
根据烧结过程中的实时数据,编码解码模型的参数也在实时调整,不断优化迭代,重复步骤1,使得模型具有较强的鲁棒性。
[0136]
(6)模型性能检验
[0137]
为了检验模型的有效性,从某烧结厂里采集10000条样本,采样间隔为1分钟,利用滑窗后获得样本片段后,进数据预处理后,将数据片段划分为6000个训练样本,1000个验证样本和800个测试样本由于深度学习模型调参比较麻烦,通过实验设置模型参数如下表2。
[0138]
表2模型的超参数
[0139]
参数hidden_sizelearning_ratehidden_layerdropoutinput_sizeoutput_size取值200.00310.1405
[0140]
为了比较所建立的模型优劣,这里使用的对比模型为两种传统的机器学习模差分整合移动平均自回归模型arima、长短时记忆循环网络lstm网络,门控gru网络和时间卷积tcn。评价指标为命中率hr、均方根误差rmse和平均绝对误差mae。
[0141]
表3展示了基于时空特征提取的编码解码模型的预测效果。可以看出,传统的机器学习模型arima在多步预测上的效果比较差,说明统计学习模型对于复杂工业过程存在一定的局限性。而三种种深度学习模型门控神经网络gru、长短时记忆网络lstm和时间卷积tcn效果提升了不少,命中超过了80%。不过对于工业现场来说,btp的预报模型还难以应用。对于多对多序列预测来说,编码解码模型取得了较好的效果,命中率在90%以上,提高了终点预报的准确性,为烧结操作工调整工艺参数提供了充足的时间,可以提高烧结矿的产量和质量。对于烧结厂来说,能够实现烧结终点的提前预报,将会给企业带来较大的经济效应。
[0142]
表3模型预测结果对比
[0143][0144]
以上所述实施例仅表达了本发明的几种实施方式,其描述较为具体和详细,但并不能因此而理解为对本发明专利范围的限制。应当指出的是,对于本领域的普通技术人员来说,在不脱离本发明构思的前提下,还可以做出若干变形和改进,这些都属于本发明的保护范围。因此,本发明的保护范围应以所附权利要求为准。