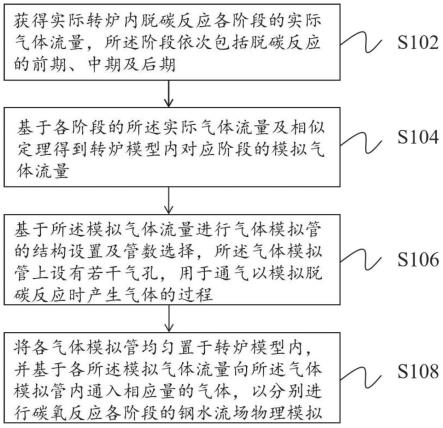
1.本发明涉及炼钢技术领域,具体涉及一种炼钢过程碳氧反应气泡动力学水模型实验方法及装置。
背景技术:2.钢铁主要由氧气转炉和电炉生产。炼钢过程熔池的搅拌对钢水的成分、温度的均匀,排除夹杂物以及提升熔池反应速率等具有重要影响。炼钢过程的熔池搅拌是由其内顶吹、底吹及炼钢过程碳氧反应沸腾三者引起,炼钢过程碳氧反应中产生大量的气体为炼钢过程熔池内的流场变化提供绝大部分动力。
3.受炼钢时高温熔融等现场环境的限制,熔池内部的各相流动很难形成直接的观测和检测。冷态物理模拟(水力学模拟)由于其可视性、可操作性、可检测性具优的方法可为实际转炉生产工艺优化提供更为直接、科学的方案。
4.现有的转炉水学模拟是通过顶吹供气、底吹供气相配合的方式来研究熔池内流场搅拌,仅针对顶吹、底吹两者所引起的流场变化进行,尚无针对炼钢过程碳氧反应影响的物理模拟。而忽略炼钢过程碳氧反应的影响将导致对炼钢过程熔池内熔池内流场分布的了解及后期控制与实际情况间存在较大的差距,进而导致最终的出钢质量及出钢率等均较低。
技术实现要素:5.本发明目的在于提供一种炼钢过程碳氧反应气泡动力学水模型实验方法及装置,用于解决现有对炼钢过程熔池内流场物理模拟研究中忽略炼钢过程碳氧反应而对出钢质量及出钢率造成不良影响的技术问题。
6.为达成上述目的,本发明提出如下技术方案:
7.一种炼钢过程碳氧反应气泡动力学水模型实验方法,包括:
8.获得实际转炉内脱碳反应各阶段的实际气体流量,所述阶段依次包括脱碳反应的前期、中期及后期;
9.基于各阶段的所述实际气体流量及相似定理得到模型内对应阶段的模拟气体流量;
10.基于所述模拟气体流量进行气体模拟管的结构设置及管数选择,所述气体模拟管上设有若干气孔,用于通气以模拟脱碳反应时产生气体的过程;
11.将各气体模拟管均匀置于模型内,并基于各所述模拟气体流量向所述气体模拟管内通入相应量的气体,以分别进行碳氧反应各阶段的钢水流场物理模拟。
12.进一步的,所述获得实际转炉内脱碳反应各阶段的实际气体流量,包括:
13.获取各阶段的脱碳速度及实际转炉内的金属装入重量t;
14.通过得到实际转炉内的气体流量,其中,12为碳的相
对原子质量,22.4
×
10-3
为一摩尔气体体积,单位为m3/mol;α有效利用系数。
15.进一步的,所述得到模型内对应阶段的模拟气体流量,包括:
16.通过得到各阶段的模拟气体流量;其中λ为相似比,β为模拟实验系数。
17.进一步的,所述获得实际转炉内脱碳反应各阶段的实际气体流量,包括:
18.对各阶段的脱碳速度进行积分以得到对应的碳含量变换函数;
19.基于各阶段的碳含量变换函数,及相邻阶段的转折碳浓度得到各阶段的碳氧化量及吹炼时长;
20.基于各阶段的所述碳氧化量、所述吹炼时长,及有效利用系数得到对应的实际气体流量。
21.进一步的,所述基于所述模拟气体流量进行气体模拟管的结构设置及管数选择,包括:
22.选定一型号的软管,所述软管的管壁上间隔设有若干气孔;
23.向所述软管内通入与其管径相应的最大气量,并截取此时均匀出气的若干连续气孔对应的一段软管,并以该段软管作为一根气体模拟管;
24.基于与所述气体模拟管相应的最大气体流量,及脱碳反应中期的模拟气体流量得到所述气体模拟管的管数。
25.进一步的,所述将各气体模拟管均匀置于模型之后,还包括:
26.向所述模型内进行顶吹、底吹或复吹以得到第一均混时长;
27.将所述第一均混时长与原均混时长进行对比,所述原均混时长为未放置所述初始软管时向所述模型内进行顶吹、底吹或复吹时的均匀混合的时长;
28.当所述第一均混时长与所述原均混时长的时长差值大于预设的差值阈值时,增加各所述气体模拟管的管径,或者减小其管壁上所述气孔间距,或者增加其管壁上所述气孔的直径。
29.一种炼钢过程碳氧反应气泡动力学水模型实验装置,包括模型、气体模拟管及管道支架;
30.所述模型用于模拟实际转炉,所述模型内容纳有液体用于模拟钢水;
31.所述气体模拟管设于所述模型内,用于通气以执行所述的方法;
32.所述管道支架设于所述模型内,用于支撑所述气体模拟管;
33.所述管道支架为一沿所述模型高度方向设置的多层结构,且每层均为与所述模型的横截面相适配的圆形篦子结构,以使所述气体模拟管均匀设于所述模型内。
34.进一步的,所述气体模拟管为硅胶软管。
35.进一步的,每层所述圆形篦子结构的网格间距为2~6cm,相邻层间的间距为3~10cm。
36.进一步的,包括气动分气器,所述气动分气器与各所述气体模拟管相连,用于向各所述气体模拟管均匀通气。
37.有益效果:
38.由以上技术方案可知,本发明的技术方案提供了一种炼钢过程碳氧反应气泡动力
学水模型实验方法,用于对转炉内由碳氧反应引起的流场变化进行研究。
39.碳氧反应对转炉内钢水流场的影响主要由铁液与氧气间化学反应而产生的气体导致。而碳氧反应的前期、中期及后期的气体的产生量及产生速度受反应速度及反应进程影响而存在较大差异。因此本技术方案分别对碳氧反应各阶段造成的流场变化进行对应研究。
40.受实际转炉炼钢时的客观环境影响,本技术方案中采用了方法对其进行研究。为了提高该物理模拟研究结果的准确性及可靠性,以实际转炉及其内的碳氧反应为基础,进行物理模型设置并开展对应物理模拟研究。基于此,首先获得了实际转炉内脱碳反应各阶段的实际气体流量。其次,基于相似定理,通过各阶段的实际气体流量换算得到了对应的物理模型内各阶段的模拟气体流量。
41.由于实际转炉内的脱碳反应布满内熔池,为了在模型内模拟该过程,本技术方案通过均匀设于模型内的气体模拟管构建了气泡发生装置,具体的以通过气体模拟管管壁上气孔处的稳定气体输出对气泡搅动内熔池而引起的流场变换进行物理模拟。基于此,继续进行如下步骤:基于所述模拟气体流量进行气体模拟管的结构设置及管数选择,所述气体模拟管上设有若干气孔。此时,将各气体模拟管均匀置于模型内,并基于各所述模拟气体流量向所述气体模拟管内通入相应量的气体,即可分别进行碳氧反应各阶段的钢水流场模拟。
42.通过上述过程即实现了对转炉内脱碳反应引起的钢水流场变化的物理模拟,并可进行脱碳反应各阶段引起的流场模拟,及脱碳反应各阶段与顶吹、底吹或复吹共同作用的流场模拟。并以其为指导实现对实际转炉炼钢时流场分布、冶炼稳定等的精准控制,进而达到提高冶炼质量及出钢率的效果。
43.本发明的技术方案还提供了一种炼钢过程碳氧反应气泡动力学水模型实验装置。所述装置基于所述方法搭建,包括用于模拟实际转炉的模型,用于执行所述方法的气体模拟管,及用于支撑所述气体模拟管的管道支架。在具体结构设置上,为了达到所述气体模拟管均匀设于所述模型内的目的,进而准确的模拟在整个内熔池内产生的气体。将所述管道支架设为一沿所述模型高度方向设置的多层结构,且每层均为与所述模型的横截面相适配的圆形篦子结构,以使所述气体模拟管均匀设于所述模型内。
44.基于所述装置即可实现对脱碳反应造成的流场变化的模拟研究,进而为优化实际转炉炼钢时的参数控制提供更加可靠的指导。
45.应当理解,前述构思以及在下面更加详细地描述的额外构思的所有组合只要在这样的构思不相互矛盾的情况下都可以被视为本公开的发明主题的一部分。
46.结合附图从下面的描述中可以更加全面地理解本发明教导的前述和其他方面、实施例和特征。本发明的其他附加方面例如示例性实施方式的特征和/或有益效果将在下面的描述中显见,或通过根据本发明教导的具体实施方式的实践中得知。
附图说明
47.附图不意在按比例绘制。在附图中,在各个图中示出的每个相同或近似相同的组成部分可以用相同的标号表示。为了清晰起见,在每个图中,并非每个组成部分均被标记。现在,将通过例子并参考附图来描述本发明的各个方面的实施例,其中:
48.图1为本发明实施例所述的炼钢过程碳氧反应气泡动力学水模型实验方法的流程图;
49.图2为图1中获得所述各阶段的实际气体流量的流程图;
50.图3为图1中获得所述各阶段的实际气体流量的另一种流程图;
51.图4为与图3方法相应的获得模型内各阶段的模拟气体流量的流程图;
52.图5为图1中进行气体模拟管的结构设置及管数选择的流程图;
53.图6为本发明实施例所述的验证气体模拟管对模型内流场影响的流程图。
54.图7为本发明实施例所述的炼钢过程碳氧反应气泡动力学水模型实验装置的结构图;
55.图8为图7中所述气体模拟管与管道支架的底视图;
56.图9为一组具体的模拟结果图。
57.图中附图标记为:1为模型,2为气体模拟管,3为管道支架,4为支架,5为气动分气器,6为导气管,7为流量计,8为压力计,9为储气罐,10为空气压缩机,11为顶吹管,12为底吹管,13为计算机模块,14为电导率仪,15为电导率探头,16为示踪剂点位。
具体实施方式
58.为使本发明实施例的目的、技术方案和优点更加清楚,下面将结合本发明实施例的附图,对本发明实施例的技术方案进行清楚、完整地描述。显然,所描述的实施例是本发明的一部分实施例,而不是全部的实施例。基于所描述的本发明的实施例,本领域普通技术人员在无需创造性劳动的前提下所获得的所有其他实施例,都属于本发明保护的范围。除非另作定义,此处使用的技术术语或者科学术语应当为本发明所属领域内具有一般技能的人士所理解的通常意义。
59.本发明专利申请说明书以及权利要求书中使用的“第一”、“第二”以及类似的词语并不表示任何顺序、数量或者重要性,而只是用来区分不同的组成部分。同样,除非上下文清楚地指明其它情况,否则单数形式的“一个”“一”或者“该”等类似词语也不表示数量限制,而是表示存在至少一个。“包括”或者“包含”等类似的词语意指出现在“包括”或者“包含”前面的元件或者物件涵盖出现在“包括”或者“包含”后面列举的特征、整体、步骤、操作、元素和/或组件,并不排除一个或多个其它特征、整体、步骤、操作、元素、组件和/或其集合的存在或添加。“上”“下”“左”“右”等仅用于表示相对位置关系,当被描述对象的绝对位置改变后,则该相对位置关系也可能相应地改变。
60.本发明实施例提供了一种炼钢过程碳氧反应气泡动力学水模型实验方法,所述方法以实际转炉各阶段的气体流量为基础,并基于相似定理对模型内的各阶段的模拟气体流量进行了换算,然后基于所述模拟气体流量进行了气体模拟管的设置;最终基于所述模型及气体模拟管即实现了由碳氧反应中气体导致的流场变化的物理模拟研究。
61.本发明实施例还提供了一种炼钢过程碳氧反应气泡动力学水模型实验装置,所述装置基于所述方法搭建,包括模型、气体模拟管及用于支撑气体模拟管的管道支架。并将所述管道支架设为多层的圆形篦子结构,此时所述气体模拟管即均匀排布于模型内,从而更准确的对充满内熔池的碳氧反应过程进行模拟。
62.下面结合附图所示的实施例,对公开的炼钢过程碳氧反应气泡动力学水模型实验
方法及装置作进一步具体介绍。
63.实施例1
64.如图1所示,所述方法包括:
65.步骤s102、获得实际转炉内脱碳反应各阶段的实际气体流量,所述阶段依次包括脱碳反应的前期、中期及后期;
66.由于碳氧反应各阶段的气体流量均不相同,若对整个碳氧反应中的各阶段进行宏观的无差别模拟,将导致物理模拟的结果与实际转炉内的物理过程间存在较大的差异。因此本实施例以碳氧反应进程进行划分,分布对脱碳反应的前期、中期及后期进行物理模拟。
67.基于此,并为了使对碳氧反应各阶段的模拟有效可靠。本实施例中首先通过步骤s102获得各阶段的实际气体流量作为本此物理模拟的数据基础。
68.如图2所示,所述步骤s102的中各实际气体流量的获得包括:
69.步骤s102.2、对各阶段的脱碳速度进行积分以得到对应的碳含量变换函数;
70.本步骤中,前期的脱碳速度为其中k1为受总硅含量、熔池温度等影响的非固定常数;中期的脱碳速度为其中k2为由氧流量确定的常数;后期的脱碳速度为其中k3为由供氧强度和枪高决定的常数。
71.具体对各脱碳速度进行积分,得到的脱碳反应前期的碳含量变化函数为其中,[%c]0为铁水初始碳含量。中期的碳含量变化函数为[%c]=-k2t+a,其中,a为常数。后期的碳含量变化函数为ln[%c]=-k3t+b,其中,b为常数。
[0072]
步骤s102.4、基于各阶段的碳含量变换函数,及相邻阶段的转折碳浓度得到各阶段的碳氧化量及吹炼时长。
[0073]
具体计算时,前中转折点(前期与中期的转折碳浓度)[%c]a一般为3%左右;中后期转折点(中期与后期的转折碳浓度)[%c]b为0.1%~1.2%。此时将[%c]a代入前期碳含量变换函数即可求得前期吹炼时长t1;将t1和[%c]a带入中期碳含量变换函数可得中期吹炼时长t2;同理可得中期吹炼时长t3。
[0074]
步骤s102.6、基于各阶段的所述碳氧化量及所述吹炼时长得到对应的实际气体流量。
[0075]
本步骤中,对各阶段的所述碳氧化量在相应的吹炼时长内进行积分,即可得到对应的实际气体流量。
[0076]
作为一种可以选择的实施方式,所述步骤s102的中各实际气体流量的获得也可由以下步骤进行:
[0077]
步骤s102.2’、获取各阶段的脱碳速度及实际转炉内的金属装入重量t。
[0078]
本步骤中所述金属装入重量为铁水重量与废钢重量之和。
[0079]
步骤s102.4’、通过得到实际转炉内的气体流量,其中,12为碳的相对原子质量,22.4
×
10-3
为一摩尔气体体积,α有效利用系数。
[0080]
由于碳氧化气体流量摩尔数等于碳的氧化量摩尔数,因此单位时间气体流量为钢液量与碳浓度的单位氧化量的乘积即为碳的单位时间氧化量。此时利用步骤s102.4’中所述的公式即可快速准确的求得实际转炉内的气体流量。其中有效利用系数指总气体流量中用于实现搅拌作用的占比,为了便于模拟进行,本实施例设定其为75%~85%。
[0081]
步骤s104、基于各阶段的所述实际气体流量及相似定理得到模型内对应阶段的模拟气体流量;
[0082]
本步骤中,以所述步骤s102获得的各阶段的实际气体流量为依据,并通过相似定理即可换算得到各阶段的模拟气体流量。
[0083]
作为一种可以选择的实施方式,当选择步骤s102.2’~步骤s102.4’中的方法进行实际气体流量计算时,如图4所示,各模拟气体流量具体通过如下获得:
[0084]
步骤s104.2’、通过公式得到各阶段的模拟气体流量;其中,λ为相似比,β为模拟实验系数;本实施例中所述模拟气体为空气,因此所述实验模拟系数具体为空气实验模拟系数,具体数值为342。
[0085]
通过上述步骤即可获得模型内各阶段的准确的模拟气体流量,从而为后需的物理模拟过程提供准确的物理模拟数值。
[0086]
步骤s106、基于所述模拟气体流量进行气体模拟管的结构设置及管数选择,所述气体模拟管上设有若干气孔,用于通气以模拟脱碳反应时产生气体的过程;
[0087]
实际转炉内的碳氧反应发生于整个内熔池内,其产生的气体存在亦存在于整个内熔池内,从而对整个内熔池的流场变化产生着影响。而在模型内复刻碳氧反应的整个过程不但无法实现,且没有必要(因为对流场的影响仅与其产生的气体引起的搅拌作用有关,而与碳氧反应的内部化学过程无关)。因此本实施例在模型内引入了均匀排布的气体模拟管,并对其进行通气以构建气泡模拟装置,进而实现对碳氧反应中气体产生对流场影响的模拟。
[0088]
由于所述气体模拟管直接模拟了碳氧反应的气体产生过程,因此气体模拟管的设置直接影响了最终物理模拟的准确性。
[0089]
本实施例中,如图5所示,气体模拟管的结构设置及管数选择包括:
[0090]
步骤s106.2、选定一型号的软管,所述软管的管壁上间隔设有若干气孔;
[0091]
本步骤中,选择软管的目的在于便于实现其在模型内的排布,且不会由于弯曲而对出气的均匀性造成影响,以最大程度上模拟实际碳氧反应的气体产生过程。
[0092]
由于每种管径的软管均有一个最大流速限制,若管径太小则流量不能达到单根软管需求的流量要求。若管径太大,虽然流量能满足要求,但软管的体积则会过大,从而对流场变化造成干扰。基于此,本步骤在选定所述软管时,还应参考步骤s104中的模拟气体流量进行。
[0093]
步骤s106.4、向所述软管内通入与其管径相应的最大气量,并截取此时均匀出气的若干连续气孔对应的一段软管,并以该段软管作为一根气体模拟管;
[0094]
由于软管上各气孔的出气流量会随着软管长度增加不断减少,而当软管长至一定长度时即使有气孔也不会进行出气。因此本步骤中引入了通入最大气量时的稳定出气的一段软管作为有效软管,并以其作为一气体模拟管。
[0095]
步骤s106.6、基于与所述气体模拟管相应的最大气体流量,及脱碳反应中期的模拟气体流量得到所述气体模拟管的管数。
[0096]
基于公知常识可得,碳氧反应中期的气体流量大于前期的气体流量,也大于后期的气体流量。因此为了便于所述气体模拟管的设置可同时满足对碳氧反应前期、中期及后期的气体产生过程模拟,此处以中期的模拟气体流量为依据进行所述气体模拟管的管数选择。
[0097]
具体的,脱碳反应中期的模拟气体流量与单根气体模拟管最大流量间的商值即为对应的管数。
[0098]
步骤s108、将各气体模拟管均匀置于模型内,并基于各所述模拟气体流量向所述气体模拟管内通入相应量的气体,以分别进行碳氧反应各阶段的钢水流场物理模拟。
[0099]
本步骤中,由于脱碳中期的模拟气体流量相对稳定,因此选择1个具体数值的中期模拟气体流量进行实验即可;而脱碳前期及后期的模拟气体流量变换较大,因此选择2~3个具体数值的前期模拟气体流量、后期模拟气体流量进行实验。
[0100]
本步骤中,由于与实际转炉相比,所述气体模拟管为模型内额外引起的结构,为了防止所述气体模拟管本身对模型内的流场造成影响。如图6所示,在所述将各气体模拟管均匀置于模型之后,还包括:
[0101]
步骤s202、向所述模型内进行顶吹、底吹或复吹以得到第一均混时长;
[0102]
步骤s204、将所述第一均混时长与原均混时长进行对比,所述原均混时长为未放置所述初始软管时,向所述模型内进行顶吹、底吹或复吹时的均匀混合的时长;
[0103]
步骤s206、当所述第一均混时长与所述原均混时长的时长差值大于预设的差值阈值时,增加各所述气体模拟管的管径,或者增加其管壁上所述气孔的直径。
[0104]
本实施例中,所述差值阈值具体为3秒。
[0105]
通过步骤s202~步骤s206即可对所述气体模拟管的引入是否对模型内流场有影响进行验证。当所述第一均混时长与所述原均混时长的时长差值不小于差值阈值时,则表明所述气体模拟管的引入对模型内流场的影响可以忽略不计。而所述时长差值大于所述差值阈值时,则表明所述气体模拟管的引入干扰了模型内的流场。此时,增加气体模拟管的管径,或减小气体模拟管的管壁上气孔间的间距,或增加其管壁上所述气孔的直径的目的在于增加实际的模拟气体流量,以消除气体模拟管带来的消极影响。
[0106]
通过上述步骤即实现了对碳氧反应中气体导致的流场变化的物理模拟。其在对实际转炉炼钢时流场分布、冶炼稳定等的精准控制方面具有实际有效的指导意义。
[0107]
实施例2
[0108]
如图7所示,所述装置包括模型1、气体模拟管2及管道支架3。所述模型1用于模拟实际转炉,所述模型内容纳有液体用于模拟钢液。由于钢液在高温下与水的特性相同,因此此处的液体指的是水。所述气体模拟管2设于所述模型1内,其管壁上设有若干气孔,用于通过导气管6通气以执行实施例1所述的方法。所述管道支架3设于所述模型1内,用于支撑所述气体模拟管2。
[0109]
为了达到所述气体模拟管2均匀设于所述模型1内的目的,进而准确的模拟在整个内熔池内产生的气体。所述管道支架3的具体结构为:所述管道支架3为一沿所述模型1高度方向设置的多层结构,且每层均为与所述模型1的横截面相适配的圆形篦子结构,以使所述气体模拟管2均匀设于所述模型1内。
[0110]
本实施例中,所述模型1依据相似定理,具体为空心的锥球形结构。其材质为有机玻璃。
[0111]
所述气体模拟管2具体为硅胶软管,并捆绑固定于所述管道支架3上。其管壁上的气孔的间距具体为1cm~3cm。
[0112]
对于管道支架3,其每层所述圆形篦子结构的网格间距为2~6cm,相邻层间的间距为3~10cm。
[0113]
为了对所述模型1进行支撑,所述装置还包括支架4。
[0114]
为了使各所述气体模拟管2均匀出气,设置所述装置还包括气动分气器5。所述气动分气器5通过导气管6与各所述气体模拟管2相连,用于向各所述气体模拟管5均匀通气。
[0115]
本实施例中,气体模拟管5内的气体由空气压缩机10和储气罐9提供。且在储气罐9与气动分气器5之间还连有流量计7、压力计8。所述流量计7用于对气体模拟管2的出气流量进行显示,所述压力计8用于对气体模拟管2的出气流量进行调节。
[0116]
实施例3
[0117]
如图7-8所示,基于实施例1所述的方法,及实施例2所述的装置,以顶吹流量为20000nm3/h,铁水碳含量为4%的120吨转炉为例进行转炉碳氧反应的物理模拟。
[0118]
此处选择图3所示的方法进行实际气体流量计算。首先,根据炼钢经典脱碳理论计算出各阶段脱碳速度,其中前中期碳浓度转折选取3%,中后期碳浓度转折选取0.6%,计算出三阶段脱碳速度分别为0.081t2、0.28、0.47[c%],后期脱碳函数ln[c%]=-0.47t+5.81。
[0119]
其次,基于脱碳速度和后期脱碳函数,按照相似定理的相似比为8:1,金属装入量120吨带入公式得到模拟流量随时间变化函数。函数最大中期流量57m3/h,依据需要对脱碳前后期分划选取实验模拟流量49m3/h,41m3/h,33m3/h,25m3/h,17m3/h。
[0120]
然后,依据最大模拟气体流量,选择管径为2.5mm的软管,并在其管壁上间隔1cm设置直径为1.2mm的气孔。对所述软管通入其许可的最大气量,测出单根软管中均匀出气的一段软管对应的长度为1.5m,此时则以该段软管作为一根气体模拟管,并记录下此时单根气体模拟管最大流量为2.8m3/h。
[0121]
继续根据脱碳反应中期的最大的气量57m3/h计算所需管数至少20根。将选定直径有效长度1.8m的气体模拟管均匀布设于管道支架上。所述管道支架共三层,每两层间距为4cm,每层设有7根气体模拟管,共为21根。
[0122]
继续将排布好气体模拟管的管道支架放入模型内进行底吹进行混匀实验。具体实施时,首先,将底吹管12的一端接入模型1底部,另一端依次通过流量计7、压力计8接入储气罐9;并通过调节压力计8对底吹流量进行预调节,以使流量计7的示数达到预设的底吹流量,且底吹管12可稳定输出即可。然后,将计算机模块13与电导率仪14相连,并将相应的电导率探头13放入所述模型1内,电导率探头13位于最下层的模拟气体管2下方;同时,将示踪
剂也放入所述最下层的模拟气体管2内,并使对应的示踪剂点位16与电导率探头13位于同一深度。最终,依据开始预调节的结果向模型1内进行底吹以进行混匀实验。
[0123]
当混匀实验的结果为时长差值不大于差值阈值3s,则表明所述气体模拟管设置合理。
[0124]
最终,依据各阶段的模拟气体流量,由空气压缩机10和储气罐9,经气动分气器5、导气管6向模拟气体管2内通气进行相应的水模型物理模拟实验。
[0125]
具体实施时,首先,通过底吹管12向模型1内通气,以模拟实际转炉的底吹过程。其次,将电导率探头13放入模型1内且探头处于最下层的模拟气体管2下方,通过调节压力计8使空气压缩机10和储气瓶9按计算得到的模拟气体流量进行稳定供气。然后,吹气一段时间以使模型1内气泡和水溶液达到稳定后,保持模拟气体流量不变,向模型1中加入示踪剂,且对应的示踪剂点位16与电导率探头13位于同一深度。此时,所述示踪剂将引起电导率探头13处水溶液的电导率发生变化,且相应的电导率变化数据将通过电导率仪14同步输出至计算机模块13进行处理。最终,当相应的电导率数据信号平稳时,在计算机模块13内即可得到炼钢过程碳氧反应气泡搅拌的熔池混匀时间。其中一组结果如图9所示,加入碳氧反应模拟后,本实验下较纯底吹最优效果从1.8m3/h提前为1.5m3/h,且较大模拟流量40m3/h下底吹流量0.6m3/h~1.5m3/h降低混匀时间作用不明显,这为实际冶炼存在的约几十秒冶炼误差和优化底吹成本提供有效指导。加入碳氧反应模拟后还可以为其他顶吹、底吹等模拟带来更接近实际的结果。
[0126]
虽然本发明已以较佳实施例揭露如上,然其并非用以限定本发明。本发明所属技术领域中具有通常知识者,在不脱离本发明的精神和范围内,当可作各种的更动与润饰。因此,本发明的保护范围当视权利要求书所界定者为准。