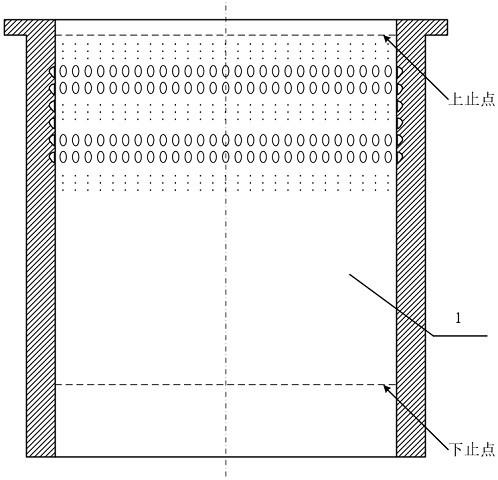
1.本发明涉及工程机械领域,具体而言,涉及一种特形微织构缸套及其优化设计方法。
背景技术:2.随着发动机强化指标的不断提高,发动机的摩擦学问题更加突出,因此需要采用合理的结构设计来增强发动机缸套的摩擦磨损性能,延长缸套的工作寿命和可靠性。
3.自20世纪80年代,表面织构技术便应用于缸套表面且被证明能够显著改善活塞环/缸套摩擦副的摩擦学性能,但由于发动机缸套工作条件的复杂性使得对于缸套表面微织构的研究不应仅仅是微织构的特征类型和几何形状,还应包括缸套的工作条件、纹理形状、分布、多参数优化等。
4.本发明提供了一种特形微织构缸套及其优化设计方法,在缸套内表面上设置有椭圆开口偏置类抛物线微织构,且椭圆开口偏置类抛物线微织构的尺寸和空间分布参数可根据稳定发动机转速下缸套位置的不同而变化;结合响应面和模拟退火算法对缸套表面微织构的长半轴、短半轴、偏置量、深度和面积占有率进行优化设计,得到摩擦系数最小、承载压强最大的最优微织构参数;同时,缸套表面的微织构能够储存一部分润滑油,提高油膜承载力,改善摩擦副润滑减摩性能,延长发动机的工作寿命。
技术实现要素:5.一种特形微织构缸套及其优化设计方法,包括缸套本体(1),所述缸套本体(1)内表面上设置有椭圆开口偏置类抛物线微织构,且椭圆开口偏置类抛物线微织构的尺寸和空间分布参数可根据稳定发动机转速下缸套位置的不同而变化,以满足发动机运行过程中对不同缸套位置摩擦磨损性能的差异性要求,包括如下步骤:步骤1:cfd仿真边界条件的确定:根据所要织构区域在发动机缸套中的位置,选取用于cfd分析的压力和速度;步骤2:未织构缸套cfd仿真:为了与最优微织构参数模型的摩擦磨损性能对比,建立相应未织构缸套模型进行cfd仿真分析并得到其摩擦系数和承载压强;步骤3:试验设计:采用中心复合试验设计方法得到后续优化设计的试验设计表;步骤4:带织构缸套cfd仿真:按照试验设计表依次进行cfd仿真分析并得到各试验组的摩擦系数和承载压强;步骤5:建立优化数学模型:根据试验设计表建立以摩擦系数最小、承载压强最大为目标的缸套表面微织构优化数学模型;步骤6:表面最优微织构参数的确定:根据建立的优化数学模型并结合模拟退火算法进行优化设计,得到最优微织构的长半轴、短半轴、偏置量、深度和面积占有率。
6.作为本发明优选的,所述的一种特形微织构缸套及其优化设计方法,椭圆开口偏置类抛物线微织构长半轴a的取值范围为200~400;短半轴b的取值范围为40~
200;偏置量c的取值范围为0~75;深度d的取值范围为15~60;面积占有率e的取值范围为0.1~0.7。
7.作为本发明优选的,所述的一种特形微织构缸套及其优化设计方法,采用cfd方法对微织构缸套进行分析能更准确的模拟缸套工作环境,从而得到基于服役条件的缸套本体(1)表面微织构参数。
8.作为本发明优选的,所述步骤2取内径d为102mm的未织构缸套本体(1)、外径为101.99mm的活塞环(2)沿圆周方向以进行切分建模,轴向长度为1.8mm;进行cfd仿真分析得到其摩擦系数和承载压强。
9.作为本发明优选的,所述步骤3采用中心复合试验设计方法得到包含椭圆开口偏置类抛物线微织构长半轴a、短半轴b、偏置量c、深度d和面积占有率e的五因素五水平实验设计表;微织构的面积占有率e如下公式所示:(1)其中:e为微织构的面积占有率,%;w为微织构控制体的宽度,单位;h为微织构控制体的高度,单位。
10.作为本发明优选的,所述步骤4取内径d为102mm的缸套本体(1)和外径为101.99mm的活塞环(2)沿圆周方向以能够保证完整微织构的角度进行切分建模,轴向长度为1.8mm;依次进行cfd仿真分析得到各组摩擦系数和承载压强。
11.作为本发明优选的,所述步骤5建立的椭圆开口偏置类抛物线微织构的优化数学模型为:(2)其中:为微织构缸套的摩擦系数;为微织构缸套的承载压强,pa;为未织构缸套的摩擦系数;为微织构缸套的承载压强,pa。
12.本发明有益效果在于:本发明提供了一种特形微织构缸套及其优化设计方法,在缸套内表面上设置有椭圆开口偏置类抛物线微织构,且椭圆开口偏置类抛物线微织构的尺寸和空间分布参数可根据稳定发动机转速下缸套位置的不同而变化;结合响应面和模拟退火算法对缸套表面微织
构的长半轴、短半轴、偏置量、深度和面积占有率进行优化设计,得到摩擦系数最小、承载压强最大的最优微织构参数;同时,缸套表面的微织构能够储存一部分润滑油,提高油膜承载力,改善摩擦副润滑减摩性能,延长发动机的工作寿命。
13.附图说明:图1是椭圆开口偏置类抛物线微织构周向分布示意图;图2是椭圆开口偏置类抛物线微织构分布区域示意图;图3是椭圆开口偏置类抛物线微织构参数示意图;图4是活塞环和织构化缸套切分示意图;图中:1、缸套;2、活塞环;3、润滑油。
14.具体实施方式:下面结合附图和具体的实施例对本发明做进一步说明。
15.如图1所示,在缸套表面加工椭圆开口偏置类抛物线微织构,且椭圆开口偏置类抛物线微织构的尺寸和空间分布参数可根据稳定发动机转速下缸套位置的不同而变化。
16.为了说明本发明中缸套不同区域微织构参数的确定方法,取如图2所示距上止点为5mm、总长为5mm的区域作为此示例性实施例的织构区域。
17.本实施例中,一种特形微织构缸套及其优化设计方法,包括如下步骤:步骤1:cfd仿真边界条件的确定:根据所要织构区域在发动机缸套中的位置,选取用于cfd分析的压力和速度;由发动机工作特点可知此示例性实施例的微织构区域处于低速低压区,即cfd边界条件可取:进口压力为0.4mpa、出口压力为0.1mpa、发动机转速为1500r/min(此时活塞环移动速度为3.4m/s);润滑油密度和粘度分别为890和0.009。
18.步骤2:未织构缸套cfd仿真:为了与最优微织构参数模型的摩擦磨损性能对比,建立相应未织构缸套模型进行cfd仿真分析并得到其摩擦系数和承载压强;取内径为102mm的未织构缸套本体(1)、外径为101.99mm的活塞环(2)沿圆周方向以进行切分建模,轴向长度为1.8mm;并进行cfd仿真分析,得到其摩擦系数和承载压强分别为0.0081和249000pa。
19.步骤3:试验设计:采取中心复合试验设计方法得到后续优化设计的试验设计表;采用中心复合试验设计得到包含如图3所示的椭圆开口偏置类抛物线微织构长半轴a、短半轴b、偏置量c、深度d和面积占有率e的五因素五水平实验设计表;微织构的面积占有率e如下公式所示:(3)其中:e为微织构的面积占有率,%;w为微织构控制体的宽度,单位;h为微织构控制体的高度,单位;步骤4:带织构缸套cfd仿真:按照试验设计表依次进行cfd仿真分析并得到各试验组的摩擦系数和承载压强;取如图4所示的内径d为102mm的缸套本体(1)和外径为101.99mm的活塞环(2)沿
圆周方向以能够保证完整微织构的角度进行切分建模,轴向长度为1.8mm,并根据不同的实验设计表进行不同微织构参数缸套模型的cfd仿真分析,得到各试验组的摩擦系数和承载压强;步骤5:建立优化数学模型:根据试验设计表建立以摩擦系数最小、承载压强最大为目标的缸套表面微织构优化数学模型;通过试验设计表数据分别建立摩擦系数和承载压强的数学模型如下公式所示:(4)(5)建立以摩擦系数最小、承载压强最大为目标并考虑微织构各因素取值区间为约束条件的优化数学模型如下公式所示:(6)其中:为微织构缸套的摩擦系数;为微织构缸套的承载压强,pa;为未织构缸套的摩擦系数,0.0081;为未织构缸套的承载压强,249000pa。
20.步骤6:表面最优微织构参数的确定:根据建立的优化数学模型并结合模拟退火算法进行优化设计,得到最优微织构的长半轴、短半轴、偏置量、深度和面积占有率。
21.通过模拟退火算法求解优化数学模型后得到摩擦系数最小、承载压强最大的最优微织构参数:长半轴为390、短半轴为108、偏置量为139、深度为42及面积占有率为0.69;最优模型的摩擦系数和承载压强分别为0.0055和255645pa。与未织构缸套相比,在承载压强提升2.67%的基础上,摩擦系数降低了32.1%,即优化后得到的微织构能有效
改善此示例性实施例对应发动机缸套织构区域的摩擦学性能。
22.综上所述,本发明提供了一种特形微织构缸套及其优化设计方法,在缸套内表面上设置有椭圆开口偏置类抛物线微织构,且椭圆开口偏置类抛物线微织构的尺寸和空间分布参数可根据稳定发动机转速下缸套位置的不同而变化;结合响应面和模拟退火算法对缸套表面微织构的长半轴、短半轴、偏置量、深度和面积占有率进行优化设计,得到摩擦系数最小、承载压强最大的最优微织构参数;同时,缸套表面的微织构能够储存一部分润滑油,提高油膜承载力,改善摩擦副润滑减摩性能,延长发动机的工作寿命。
23.尽管已经示出和描述了本发明的具体实施例,但本发明的保护范围并不局限于此,对于任何熟悉本领域的技术人员而言,可理解在不脱离本发明原理和精神的情况下对实施例进行多种变化、修改、替换和变形。因此,本发明的保护范围应以权利要求的保护范围为准。