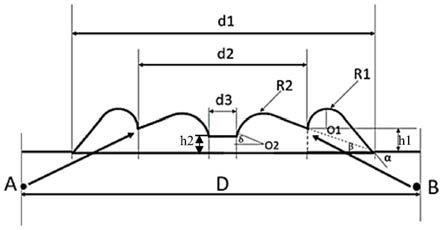
1.本发明属于发动机技术领域,具体涉及一种对置活塞双碰壁喷油燃烧室参数化设计方法。
背景技术:2.增程型插电混合动力车的电动机直接驱动车轮,发动机则用来驱动发电机给电池进行充电,因为发动机并不直接驱动车轮,因此也不需要变速箱,就相当于在普通的电动车上装上了一台汽油发动机(主要应用在普通乘用车上)或柴油发动机(主要用在重载车辆上)。对置式活塞柴油发动机相比传统的直列式发动机,在相同的缸数下,体积更小,结构更为紧凑,与此同时,对置式发动机结构对称,可以巧妙抵消发动机工作时产生的非平衡激振力,从而降低工作噪声,平衡载荷。将对置式活塞柴油发动机应用到增程型插电混合动力车,对于未来的增程型插电混合动力车的长远发展具有重要的现实意义。
3.对置式活塞柴油发动机燃烧室的形状对进气挤流、涡流的生成以及燃油喷雾的油气匹配都有很大的影响,因此对其进行合理地参数化设计,成为了提升对置式活塞柴油发动机性能的重要方式。
4.然而,对置式活塞柴油发动机燃烧室的现有参数化方式只能确定燃烧室的外室与内室的直径等相关线性尺寸的范围,以至于无法系统地构建燃烧室结构并提升燃烧室的油气混合性能与燃烧性能。
技术实现要素:5.有鉴于此,本发明提供了一种对置活塞双碰壁喷油燃烧室参数化设计方法,该方法根据对置活塞双碰壁喷油燃烧室各参数之间的关系,构建燃烧室的结构,并对决定该燃烧室设定的性能指标最关键的变量进行优化,提升燃烧室的油气混合性能与燃烧性能。
6.本发明采用以下技术方案:
7.一种对置活塞双碰壁喷油燃烧室参数化设计方法,所述设计方法包括:
8.步骤一:依据设计任务,给定燃烧室直径d、凸台顶面宽度d3以及内室轮廓角β;
9.步骤二:根据经验值,给定外室喉口直径d1、外室凹坑圆弧半径r1、内室凹坑圆弧半径r2、第一弧脊深度h1、内室喉口直径d2、内室出口角δ;
10.步骤三:基于步骤一至步骤二所确定的参数,保证所述外室的圆弧段在与所述内室的直线段接口处的圆弧切线与水平方向垂直,由此确定外廓角α与第二弧脊高度h2;
11.步骤四:基于步骤一至步骤三所确定的参数,构造所述燃烧室的三维结构;
12.步骤五:从所述外室喉口直径d1、所述内室轮廓角β、所述第一弧脊深度h1、所述内室出口角δ、所述外室凹坑圆弧半径r1、所述内室凹坑圆弧半径r2中选取一个以上对所述燃烧室设定的性能指标相关的参数作为优化参数;
13.步骤六:按照对所述燃烧室设定的性能指标影响程度从大到小的顺序,对所述优化参数进行排序;
14.步骤七:按照步骤六中的排序,依次对所述优化参数进行优化。
15.进一步地,步骤六中设定的性能指标为燃烧室放热率。
16.进一步地,选取所述外室喉口直径d1、所述内室出口角δ、所述外室凹坑圆弧半径r1以及所述内室凹坑圆弧半径r2作为优化参数,其中所述外室凹坑圆弧半径r1与所述内室凹坑圆弧半径r2共同作为一组优化参数,同时进行优化。
17.进一步地,步骤六中所述优化参数的排序是:内室出口角δ、外室喉口直径d1、外室凹坑圆弧半径r1与内室凹坑圆弧半径r2。
18.进一步地,在步骤七中对所述优化参数进行优化时,先保持外室喉口直径d1、外室凹坑圆弧半径r1、内室凹坑圆弧半径r2以及内室轮廓角β不变,优化内室出口角δ,使燃烧室放热率达到最优;在优化完内室出口角δ的基础上,保证外室凹坑圆弧半径r1、内室凹坑圆弧半径r2不变以及内室出口角δ不变,优化外室喉口直径d1,使燃烧室放热率达到最优;在优化完内室出口角δ与外室喉口直径d1的基础上,保证内室出口角δ与外室喉口直径d1不变,优化外室凹坑圆弧半径r1与内室凹坑圆弧半径r2,使燃烧室的放热率达到最优。
19.进一步地,对所述优化参数进行优化时保证燃烧室的总容积不变。
20.有益效果:
21.1、本发明的对置活塞双碰壁喷油燃烧室参数化设计方法,通过燃烧室结构各参数之间的关系,既能确定外室与内室直径等相关线性尺寸,也能确定外室凹坑圆弧半径以及内室凹坑圆弧半径等相关非线性尺寸,从而能够系统性地高效地设计构建满足油气混合性能与燃烧性能的燃烧室结构。且在对参数进行优化时,先按照对燃烧室设定的性能指标影响程度从大到小的顺序对优化参数进行排序,然后再按照排序依次分别对选定的优化参数进行优化,相比较只是对优化参数进行优化而没有先进行排序的方式,这种先排序再优化的方式可以提高优化效率。
22.2、本发明的对置活塞双碰壁喷油燃烧室参数化设计方法,侧重分析通过调整燃烧室的哪几组参数可以真正有效地进行油气匹配,具体给出了外室喉口直径d1、内室出口角δ、外室凹坑圆弧半径r1以及内室凹坑圆弧半径r2是影响燃烧室放热率的最关键的参数,便于对燃烧室放热率性能的研究。
23.3、本发明的对置活塞双碰壁喷油燃烧室参数化设计方法,给出了外室喉口直径d1、内室出口角δ、外室凹坑圆弧半径r1以及内室凹坑圆弧半径r2对燃烧室放热率影响程度的排序,便于对燃烧室放热率进行更高效的优化。
24.4、本发明的对置活塞双碰壁喷油燃烧室参数化设计方法,通过对内室出口角δ的优化,使燃烧室的结构充分有利于燃油卷流的形成,从而使燃油与空气在燃烧室内迅速形成可燃混合气,保证燃油的充分燃烧,提升燃烧室的油气混合性能与燃烧性能;在对内室出口角δ优化基础上,通过对外室喉口直径d1进行优化,使燃油既可以充分地扩散到整个燃烧室,又不会过度增加弧脊附近燃烧室的热负荷,进一步提升燃烧室的油气混合性能与燃烧性能;在对外室喉口直径d1优化的基础上,选择外室凹坑圆弧半径r1以及内室凹坑圆弧半径r2作为优化对象,这两个参数与燃烧室的内外室的容积之间具有较强的相关性,通过这两个参数反映燃烧室的内外室容积能够避免寻找内外室容积复杂的函数表达式,简化燃烧室内外室容积的研究,而且通过对外室凹坑圆弧半径r1以及内室凹坑圆弧半径r2的优化,改变燃烧室的内外室容积比,能够改变内室与外室燃油分配的情况,进一步提升燃烧室的
油气混合性能与燃烧性能。
附图说明
25.图1为本发明实施例的对置活塞双碰壁喷油燃烧室简图;
26.图2为本发明实施例的对置活塞双碰壁喷油燃烧室的结构示意图;
27.图3为本发明实施例的不同内室出口角度与燃烧室放热率关系的示意图;横坐标为曲轴转角,纵坐标为放热率;
28.图4为本发明实施例的不同外室喉口直径与燃烧室放热率关系的示意图;横坐标为曲轴转角,纵坐标为放热率;
29.图5为本发明实施例的不同内外室容积比与燃烧室放热率关系的示意图;横坐标为曲轴转角,纵坐标为放热率。
具体实施方式
30.下面结合附图并举实施例,对本发明进行详细描述。
31.如图1与图2所示的一种对置活塞双碰壁喷油燃烧室,该对置活塞双碰壁喷油燃烧室为进排气两侧对称的ω型燃烧室,燃烧室由上下两侧活塞体顶部的共有空间构成。燃烧室的直径记作d,外室喉口直径记作d1,内室喉口直径记作d2,在燃烧室的内部设有减少热负荷的凸台(上表面为类似平面的结构),该凸台顶面宽度记作d3,内室出口角(内室与凸台的接口处圆弧径向与水平线的夹角)记作δ,内室轮廓角(内室直线段与水平线的夹角)记作β,外廓角(外室直线段与水平线的夹角)记作α,外室凹坑圆弧半径记作r1,内室凹坑圆弧半径记作r2,内室与外室连接处的第一弧脊高度记作h1,凸台高度即第二弧脊的高度记作h2。
32.具体地,参照图1与图2,燃烧室内壁从两侧供油口开始向内依次形成外室导流凹坑、内室导流凹坑,其中,内室导流凹坑与外室导流凹坑连接处形成第一弧脊(也可以称为第一凸缘),内室与凸台连接处形成第二弧脊(也可以称为第二凸缘),这种燃烧室结构可以产生两股燃油卷流以及两股燃油粒子冲击,即,从喷油口喷出的燃油喷射到第一凸缘后,一部分燃油由于受到撞壁会朝逆喷射方向流动,并在经过外室导流凹坑后,在喷射后方形成燃油涡流;另一部分燃油中,有部分燃油依次经过内室导流凹坑、第二凸缘的碰撞后,与经过第一凸缘改变方向射向燃烧室中心的部分燃油产生冲击。
33.可以看出,该结构的特点是:借助第一凸缘和第二凸缘的相互作用,使得燃烧室两侧不仅有一次卷流,还在第二凸缘的作用下出现另一卷流,同时燃烧室双侧燃油粒子也会在燃烧室中心交汇处产生粒子碰撞,使得燃烧室一侧对另一侧的燃烧产生较强的冲击。具体来说,燃烧室的每一侧均设置碰撞凸缘和导流凹坑,油束喷出后,首先碰撞第一凸缘,第一凸缘是第一侧向壁面油束着壁点,经过喷油孔喷出的燃油在碰撞到侧向壁面油束着壁点后,形成壁面射流剥离,实际上是对自由射流部分的燃油形成扰动,使得自由射流的方向进行偏转,形成的混合射流一侧沿第一凸缘方向到第二凸缘方向向燃烧室中心运动,另一侧沿逆喷射方向向燃烧室边缘运动;同时这种经扰动的混合射流沿燃烧室反射壁壁面进行扩散,最终导致燃烧室中心的广大区域及边缘的大量空气被卷吸,大大增加了燃油与空气的接触面积,使燃油分布更加均匀,燃气混合更加均匀,从而有效的提升了油气混合的速率和效果。
34.更重要的是,该双侧对称的燃烧室结构,在燃烧室对称的两侧均形成相互冲击的大型卷流,从而出现湍动能的交换,与单侧碰壁射流相比,双侧设计使得双侧粒子也会在交汇处产生粒子碰撞,使得一侧对另一侧的燃烧产生较强的冲击,更有效地通过燃油粒子动能的碰撞提升油气混合物的利用率。
35.对图1所示的对置活塞双碰壁喷油燃烧室进行参数化设计时,由于该对置活塞双碰壁喷油燃烧室的喷油器位于垂直于活塞运动方向的径向两侧(图1中的a,b两点),当油束从a,b两处射出后,会撞击第一弧脊形成分裂的两束卷流,这两束卷流分布在燃烧室的内室与外室,而双卷流的燃烧室的结构由多达十几个参数共同决定,且各个参数无法孤立研究,因此通过参数定位分析几个决定型参数。
36.图1所示的对置活塞双碰壁喷油燃烧室的工作过程可以概况成以下四个阶段:
37.(1)燃油射流触脊前为准自由射流段:此阶段内燃油射流通常以空气卷吸原理进行混合,此时处于滞燃期。
38.(2)射流触脊分裂段:燃油射流触脊时刻处于滞燃期末,触脊后产生的飞溅油雾和微涡流影响着火,所以第一弧脊的位置是影响滞燃期的新因素。
39.(3)燃油双卷流形成段:触脊后分裂形成的小股射流沿内室环壁向下沿壁翻卷成内卷流;主股射流进入内室底部沿环壁向上翻卷,出喉口后进入平壁(缸盖底面),部分燃油成平壁射流向燃烧室中心流动,大部分继续卷动成外卷流,避免了燃油在内喉口的扎堆现象,外室卷流则填补了两侧外室空间的缺油。本阶段是以环壁射流空气卷吸机理进行混合与燃烧,燃烧进入了初燃期和主燃期。
40.(4)射流尾端通过弧脊后的双卷流段:此时内、外室卷流出现明显涡心,外室涡心位置不动,外室除卷流外,部分燃油沿平壁向室中心流动,使燃油分布扩大。内室的卷流涡心向室中心移动,燃油随之向室中心扩张,最终燃油在室中形成较为均匀的分布,由于附壁燃油经翻卷可不断遇到新空气,从而冲破了热束缚。
41.综上,在本实施例中,参数定位如下:
42.(1)外室喉口直径d1取值太大对燃油射流的动能要求较高,燃烧室形状趋于传统的开式燃烧室,使得双卷流流动动能减小,使外室燃油扎堆,内室中心缺油,但增大外室喉口直径d1有利于减小活塞顶和活塞环的热应力,根据双卷流燃烧系统相关设计经验,推荐值为(0.7~0.84)d。
43.(2)内室喉口直径d2的大小会对弧脊(此处指第一弧脊,下文所述弧脊也均指第一弧脊)的位置产生影响,而弧脊位置影响内、外室容积所占的比例。具体来说,内室喉口直径d2过小,则油束触脊后形成的双卷流距离较远,双涡流动界面无干涉,产生的微涡流很小;内室喉口直径d2过大,则触脊后双涡重叠过多,趋于普通直喷式燃烧室,内室中心缺油,四周燃油扎堆,没有双卷流的作用效果。
44.(3)外室凹坑圆弧半径记r1与内室凹坑圆弧半径r2会对卷流尺度有较大影响;此外,外室凹坑圆弧半径r1、内室凹坑圆弧半径r2的大小也影响燃烧室的内、外室容积的比例。外室凹坑圆弧半径r1的推荐值范围为:r1/d1=0.06~0.10,内室凹坑圆弧半径r2的推荐值范围为:r2/d1=0.05~0.08。
45.(4)第一弧脊深度h1决定了燃油在燃烧室的内、外室中分配的比例。当燃油喷孔夹角保持不变,第一弧脊深度h1过小时,内室燃油分配过多;第一弧脊深度h1过大,则使得内
室分配燃油过少,两者均不利于燃烧室内混合气的燃烧;同时,一般情况下,(d1-d2)与h1紧密相关,(d1-d2)增大,第一弧脊深度h1则相应增大,且h1/d1的范围一般在0.06~0.09。
46.另外,双卷流燃烧系统设计的主要经验原则包括:一是内、外室的燃油应符合一定比例;二是双涡相切原则,要求内外室圆弧分别与内外室直线段轮廓相切;三是内、外卷流不能超过燃烧室顶面太多;四是射流入射角应大于零且接近零,同时中心凸台顶面宽度d3对于参数化研究对于燃烧的影响不大,可以取定值。
47.更具体地,在本实施例中,对图1所示的对置活塞双碰壁喷油燃烧室进行参数化设计的步骤包括:
48.步骤一:依据设计任务,给定燃烧室直径d、凸台顶面宽度d3以及内室轮廓角β;
49.步骤二:根据经验值,具体地,是指根据外室喉口直径d1=(0.7~0.84)d,在该数值范围给定外室喉口直径d1;根据外室凹坑圆弧半径r1=(0.06~0.10)d1,在该数值范围给定外室凹坑圆弧半径r1;根据内室凹坑圆弧半径r2=(0.05~0.08)d1,在该数值范围给定内室凹坑圆弧半径r2;根据弧脊深度h1=(0.06~0.09)d1,在该数值范围给定弧脊深度h1;根据内室喉口直径满足h1=(d1-d2)/2
·
tanβ,在该数值范围给定内室喉口直径d2;根据工程经验,给定内室出口角δ;
50.步骤三:基于步骤一至二所确定的参数,保证外室圆弧段在与内室直线段接口处的圆弧切线与水平方向垂直,此时在内室出口角β、外室凹坑圆弧半径r1、第一弧脊深度h1、外室喉口直径d1的约束下有唯一确定的外廓角α,并且在内室出口角δ、内室喉口直径d2、凸台顶面宽度d3、内室轮廓角β、内室凹坑圆弧半径r2的约束下,有唯一确定的第二弧脊高度h2;
51.步骤四:基于步骤一至步骤三所确定的参数,可以构造出燃烧室的型线,进而通过拉伸与旋转等三维建模手段可以构造出燃烧室的三维结构(可参照图2),且燃烧室的容积的函数可以表达为:v=f(d1,β,h1,δ,r1,r2,d3);
52.步骤五:因为v=f(d1,β,h1,δ,r1,r2,d3),故对外室喉口直径d1、内室轮廓角β、第一弧脊深度h1、内室出口角δ、外室凹坑圆弧半径r1、内室凹坑圆弧半径r2、凸台顶面宽度d3中的任意一个参数(如内室出口角δ)进行几组改变,都能得到相应的几组唯一确定的燃烧室结构,在本实施例中,从中选取一个以上对燃烧室某个设定的性能指标相关的参数作为优化参数;
53.步骤六:按照对燃烧室设定的性能指标影响程度从大到小的顺序,对步骤五中选取的优化参数进行排序;
54.步骤七:按照步骤六中的排序,依次对优化参数进行优化。
55.具体来说,上述选取的优化参数最好应具有以下特点:一是属于独立变量;二是在理论上可对结果产生较为明显影响。更具体地,本实施例设定的燃烧室性能指标是燃烧室放热率,根据上述对图1与图2所示的对置活塞双碰壁喷油燃烧室工作原理的分析以及上述该对置活塞双碰壁喷油燃烧室的参数化构建过程,本实施例选取内室出口角δ、外室喉口直径d1、外室凹坑圆弧半径r1与内室凹坑圆弧半径r2作为优化参数,对燃烧室的结构进行优化设计。如此,可通过对优化参数的优化,达到对燃烧室结构优化的目的,从而提高燃烧室的放热率。
56.本实施例在传统只是对选取的优化参数进行优化的基础上,先按照对燃烧室放热
率影响程度从大到小的顺序,对优化参数进行排序,然后按照排序依次对优化参数进行了优化。具体来说,根据图3~图5的数据,可知内室出口角δ、外室喉口直径d1、外室凹坑圆弧半径r1与内室凹坑圆弧半径r2(外室凹坑圆弧半径r1与内室凹坑圆弧半径r2共同作为一组优化参数,同时进行优化)对燃烧室放热率的影响程度是依次逐渐降低的,因此按照这种排序依次分别对这三组优化参数进行优化。具体地,在本实施例中,优化时,先保持外室喉口直径d1、外室凹坑圆弧半径r1以及内室凹坑圆弧半径r2与内室轮廓角β不变,通过燃烧室的三维仿真,优化内室出口角δ,使燃烧室放热率达到最优;在优化完内室出口角δ的基础上(即内室出口角δ不变),保证外室凹坑圆弧半径r1与内室凹坑圆弧半径r2不变,,通过燃烧室的三维仿真,优化外室喉口直径d1,使燃烧室放热率达到最优;在优化完内室出口角δ与外室喉口直径d1的基础上(即内室出口角δ与外室喉口直径d1不变),优化外室凹坑圆弧半径r1与内室凹坑圆弧半径r2,使燃烧室的放热率达到最优。这种优化步骤是根据对影响燃烧室放热率程度从高到低进行的,可以提高优化的效率。
57.值得注意的,在本实施中,是根据燃烧室的放热率这一性能指标对选取的参数进行优化,实际上也可以是其它关注的性能指标,如在发动机单次循环下的燃烧室最高缸压与指示功率等;而且在上述参数优化过程中应当维持燃烧室的总容积不变。
58.综上所述,以上仅为本发明的较佳实施例而已,并非用于限定本发明的保护范围。凡在本发明的精神和原则之内,所作的任何修改、等同替换、改进等,均应包含在本发明的保护范围之内。