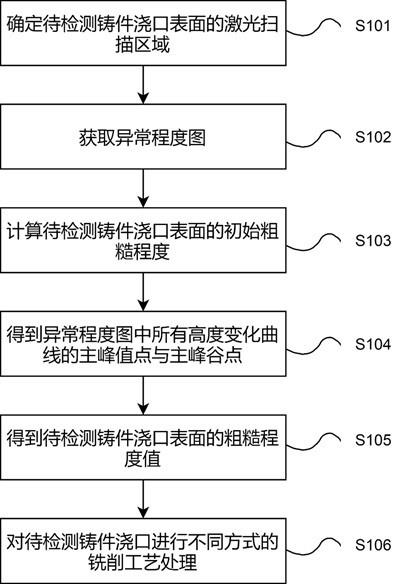
1.本技术涉及人工智能领域,具体涉及一种用于铸件浇口铣削加工的工艺方法。
背景技术:2.随着机械工业的发展,用户对产品的要求愈来愈高。铸造生产作为提供毛坯的重要环节,正面临着实现优质、精化的重要任务。其中铸件浇口的铣削、切割加工是一道必不可少的生产工序。
3.在铸件的实际生产过程中,要求铸件浇口表面平整,表面磨光,当浇口表面的粗糙程度较高时,会对铸件的耐磨性,抗疲劳强度以及抗腐蚀能力产生较大影响,因此对铸件浇口表面的粗糙度的检测是非常重要的。
4.目前常用的表面粗糙度测量方法大概可分为接触式和非接触式两种。接触式的测量方法在测量过程中测量装置会与被测表面接触,不仅容易受到针头直径的影响,且容易对待测浇口表面造成损伤。非接触式的测量方法大致可分为视觉检测法、声发射检测法和光学方法等,不会对被测表面产生二次损伤,而且测量精度比接触式高,但是声发射检测法很容易受到外界环境噪声干扰;视觉检测容易受到自然光照的影响。
技术实现要素:5.针对上述技术问题,本发明提供了一种用于铸件浇口铣削加工的工艺方法,包括:采集激光扫描的待检测铸件浇口表面的激光扫描图;提取激光扫描图中每个像素点对应的发射光强以及反射时间,根据每个像素点处的发射光强与接收光强得到每个像素点处的光强损失值;利用每个像素点处的光强损失值作为该像素点的异常程度值进行图像重构,获得重构的异常程度图;根据异常程度图中各像素点的异常程度值构建灰度共生矩阵,根据异常程度图的灰度共生矩阵中的元素值计算待检测铸件浇口表面的初始粗糙程度;利用异常程度图中每一行像素点的异常程度值获取每一行的高度变化曲线,利用分水岭算法获取每一行高度变化曲线的所有局部极小值点,将获取的局部极小值点作为异常程度图中每一行高度变化曲线的疑似峰值点;利用异常程度图中每一行高度变化曲线上所有疑似峰值点所对应的像素点的反射时间对行高度变化曲线上的疑似峰值点进行分类,得到每一行高度变化曲线上的主峰值点和主峰谷点;根据异常程度图中每一行高度变化曲线上各主峰值点与其相邻主峰值点之间的距离,及该主峰值点与相邻主峰值点之间的主峰谷点对应像素点的反射时间计算该主峰值点的粗糙度,获取所有主峰值点的粗糙度;根据异常程度图中所有主峰值点的粗糙度对待检测铸件浇口表面的初始粗糙程度进行修正得到待检测铸件浇口表面的粗糙程度值;
利用得到的待检测铸件浇口表面的粗糙程度值对待检测铸件浇口进行不同方式的铣削工艺处理。
6.根据异常程度图中所有主峰值点的粗糙度对待检测铸件浇口表面的初始粗糙程度进行修正得到待检测铸件浇口表面的粗糙程度值的方法为:其中:为待检测铸件浇口表面的粗糙程度值,为待检测铸件浇口表面的初始粗糙程度,为异常程度图的像素行数,为异常程度图的像素行数的序号,为第行像素中主峰值点的数量,为第行像素中主峰值点的序号,为第行第个主峰值点的粗糙度。
7.主峰值点的粗糙度的计算方法如下:获取异常程度图中主峰值点的坐标,根据该主峰值点及其相邻两个主峰值点的坐标计算相邻两主峰值点的距离,根据该主峰值点所在行上与该主峰值点相邻主峰值点之间的距离和该主峰值点与相邻主峰值点之间的主峰谷点的反射时间计算该主峰值点的粗糙度,计算公式如下:式中:为第行像素点中第个主峰值点的粗糙度,为光速,表示相邻两个主峰值点之间的主峰谷点对应的像素点的反射时间,为主峰值点对应像素点的反射时间,表示相邻两主峰值点之间的波动程度,为第行像素点中主峰值点的序号。
8.相邻两主峰值点之间的波动程度的计算公式如下:式中:表示第个主峰值点与第个主峰值点之间的波动程度,表示第个主峰值点与第个主峰值点之间局部极小值点的数量,表示第个主峰值点与第个主峰值点之间的距离,表示第个主峰值点与第个主峰值点之间局部极小值点的序号,为相邻两主峰值点之间第个局部极小值点对应像素点的反射时间。
9.待检测铸件浇口表面的初始粗糙程度的计算方法为:获取异常程度图像的灰度共生矩阵中的元素值,根据异常程度图的灰度共生矩阵中的元素值计算待检测铸件浇口表面的初始粗糙程度,计算公式如下:式中:为待检测铸件浇口表面的初始粗糙程度,为异常程度图像的灰度共生矩阵的尺寸,即异常程度图中灰度值的数量,,为异常程度图像的灰度共生矩阵尺寸的序号,表示异常程度图像的灰度共生矩阵第行第列的元素值,即第行第列像素对出现的概率,表示异常程度图像的灰度共生矩阵中概率最大的元素值,,为出现概率最大
的像素对所对应的像素对的灰度值。
10.根据每个像素点处的发射光强与接收光强得到每个像素点处的光强损失值的方法为:获取待检测铸件浇口表面的激光扫描图上每个像素点的发射光强与接收光强,对每个像素点的发射光强与接收光强作差得到差值,将该差值作为每个像素点的光强损失值。
11.根据待检测铸件浇口表面的粗糙程度值对待检测铸件浇口进行不同方式的铣削工艺处理的过程如下:当待检测铸件浇口表面的粗糙程度值时,对待检测铸件浇口进行粗铣;当待检测铸件浇口表面的粗糙程度值时,对待检测铸件浇口进行精铣;当待检测铸件浇口表面的粗糙程度值时,认为该待检测浇口的粗糙度达到生产要求,不需要对待检测铸件浇口进行处理;其中,为待检测铸件浇口表面的粗糙程度值,,为粗糙度阈值。
12.得到每一行高度变化曲线上峰值点和主峰谷点的方法如下:根据异常程度图中每一行像素点的像素值绘制异常程度图中每一行像素值的高度变化曲线,利用分水岭分割算法获取异常程度图中每一行像素值的高度变化曲线所有的局部极值点;获取激光反射的理论时间值,当局部极值点的反射时间小于理论时间值时,该局部极值点为该行像素的高度变化曲线中的峰值点,当局部极值点的反射时间大于等于理论时间值时,该局部极值点为该行像素的高度变化曲线中的峰谷点;将该行像素的高度变化曲线中的峰值点中反射时间最小的峰值点作为主峰值点,将该行像素的高度变化曲线中的波谷点中反射时间最大的波谷点作为主峰谷点;根据上述方法得到每一行像素的高度变化曲线中的主峰值点和主峰谷点,得到异常程度图中所有的主峰值点和主峰谷点。
13.相比于现有技术,本发明实施例的有益效果在于:在众多非接触式方法中,由于声发射检测法很容易受到外界环境噪声干扰;视觉检测容易受到自然光照的影响;而激光光源为密闭式,不易受环境的影响。
14.本发明使用激光对浇口表面进行扫描,根据浇口表面的发射光强度的变化情况确定浇口表面不平整的位置以及异常程度,得到异常程度图,根据异常程度图中灰度混乱程度初步计算浇口表面粗糙度,由于异常程度图丢失了浇口表面的高度信息,因此结合各个峰值点的高度差异情况对浇口表面粗糙度进行修正,根据最终所得金属表面粗糙度确定相应的铣削加工方式。
附图说明
15.为了更清楚地说明本发明实施例或现有技术中的技术方案,下面将对实施例或现有技术描述中所需要使用的附图作简单地介绍,显而易见地,下面描述中的附图仅仅是本发明的一些实施例,对于本领域普通技术人员来讲,在不付出创造性劳动性的前提下,还可以根据这些附图获得其他的附图。
16.图1为本发明实施例1一种用于铸件浇口铣削加工的工艺方法提供的流程框图;图2为本发明实施例1一种用于铸件浇口铣削加工的工艺方法提供的方法步骤图;图3为本发明实施例2一种用于铸件浇口铣削加工的工艺方法提供的方法步骤图;图4为本发明实施例2一种用于铸件浇口铣削加工的工艺方法提供的铸件浇口表面高度变化曲线示意图。
具体实施方式
17.为了使本发明的目的、技术方案及优点更加清楚明白,以下结合附图及实施例,对本发明进行进一步详细说明。应当理解,此处所描述的具体实施例仅用以解释本发明,并不用于限定本发明。基于本发明中的实施例,本领域普通技术人员在没有做出创造性劳动前提下所获得的所有其他实施例,都属于本发明保护的范围。
18.以下描述中,为了说明而不是为了限定,提出了诸如特定系统结构、技术之类的具体细节,以便透彻理解本技术实施例。然而,本领域的技术人员应当清楚,在没有这些具体细节的其它实施例中也可以实现本技术。在其它情况中,省略对众所周知的系统、装置、电路以及方法的详细说明,以免不必要的细节妨碍本技术的描述。
19.术语“第一”、“第二”仅用于描述目的,而不能理解为指示或暗示相对重要性或者隐含指明所指示的技术特征的数量。由此,限定有“第一”、“第二”的特征可以明示或者隐含地包括一个或者更多个该特征;在本实施例的描述中,除非另有说明,“多个”的含义是两个或两个以上。
20.实施例1本发明实施例提供了一种用于铸件浇口铣削加工的工艺方法,如图1与图2所示,包括:s101、确定待检测铸件浇口表面的激光扫描区域本实施例是利用激光扫描过程中,各个位置激光反射的激光强度确定浇口表面的不平整位置,根据不平整位置的位置分布特征,确定浇口表面的轮廓峰,根据轮廓峰的高度变化情况以及波动程度计算浇口表面粗糙度,根据所得表面粗糙度对铣削质量进行判断,因此需要采集待检测铸件浇口表面图像确定出对待检测铸件浇口表面进行激光扫描的激光扫描区域。
21.s102、获取异常程度图当铸件浇口表面较为平整时,异常程度图像中的灰度值也是较为均匀的,因此以异常程度图像中的灰度混乱程度作为浇口表面整体粗糙度的初始值。所以,根据激光扫描后每个位置的光强损失量来得到待检测铸件浇口表面的异常程度图,便于后续的分析与计算。
22.s103、计算待检测铸件浇口表面的初始粗糙程度构建异常程度图的灰度共生矩阵,根据异常程度图的灰度共生矩阵的灰度熵计算异常程度图的灰度混乱程度,根据得到的灰度混乱程度来反映待检测铸件浇口表面的粗糙程度,得到出检测铸件浇口表面的初始粗糙程度。
23.s104、得到异常程度图中所有高度变化曲线的主峰值点与主峰谷点由于激光反射所需要的反射时间时间与浇口表面的高度成反比,即高度越高,所
需要的时间越短,因此实际反射时间与理论所需反射时间之间的差异值可以作为给极值点相对于中线的高度差异程度。本发明中根据两个波峰之间的距离对波峰点的粗糙度进行评估,但是由于并非所有局部极小值点均为波峰,因此在进行浇口表面粗糙度的计算之前,还需要判断局部极小值的所属类型,得到出异常程度图中每一行的主峰值点与主峰谷点。
24.s105、得到待检测铸件浇口表面的粗糙程度值由于异常程度图中忽略了各个极小值点之间的高度差异,即高度变化曲线相同时,高度差异较大区域与高度差异较小的区域存在相同的异常程度(灰度值),然而实际上高度差异越大,浇口表面的粗糙程度越大,即上述所得的待检测铸件浇口表面的初始粗糙程度的计算结果仍然不准确,因此本实施例需要结合各个位置的时间差进行分析,对待检测铸件浇口表面的初始粗糙程度进行修正得到待检测铸件浇口表面的粗糙程度值。
25.s106、对待检测铸件浇口进行不同方式的铣削工艺处理根据得到的待检测铸件浇口表面的粗糙程度值确定待检测铸件浇口表面的铣削工艺。
26.实施例2本发明实施例提供了一种用于铸件浇口铣削加工的工艺方法,如图1与图3所示,具体内容包括:s201、确定待检测铸件浇口表面的激光扫面区域本实施例是利用激光扫描过程中,各个位置激光反射的激光强度确定浇口表面的不平整位置,根据不平整位置的位置分布特征,确定浇口表面的轮廓峰,根据轮廓峰的高度变化情况以及波动程度计算浇口表面粗糙度,根据所得表面粗糙度对铣削质量进行判断,因此需要采集待检测铸件浇口表面图像确定出对待检测铸件浇口表面进行激光扫描的激光扫描区域。
27.1.获取待检测铸件浇口表面图像由于铸件表面较为复杂,为减少不必要的计算,首先需要对待检测的铸件浇口进行定位,因此本发明采用dnn语义分割的方式来识别分割图像中的铸件浇口图像。具体过程如下:输入相机采集的图像,使用dnn网络对其进行语义分割;网络结构为encoder-decoder结构,数据集为铸件浇口图像;标签分为两类,浇口区域和背景。该方式为像素级分类,即需要给图像中所有像素标注上对应的标签。属于浇口区域的像素,其值标注为1;属于背景的像素,其值标注为0;网络所用的loss函数为交叉熵损失函数。
28.2.确定待检测铸件浇口表面的激光扫描区域由此得到铸件浇口与相机的相对位置,结合激光传感器与相机的相对位置,调节激光传感器的位置,从而确定待检测铸件浇口表面的激光扫描区域。
29.也可以直接利用激光对待检测铸件浇口表面进行扫描得到待检测铸件浇口表面的激光扫描图,根据激光扫描图获取待检测铸件浇口的反射信息。
30.s202、获取异常程度图当铸件浇口表面较为平整时,异常程度图像中的灰度值也是较为均匀的,因此以异常程度图像中的灰度混乱程度作为浇口表面整体粗糙度的初始值。所以,根据激光扫描
后每个位置的光强损失量来得到待检测铸件浇口表面的异常程度图,便于后续的分析与计算。
31.1. 使用激光垂直入射,并从左向右地对待测浇口表面进行横向点扫描,记录各个位置的发射光强以及反射所需时间;2. 由于激光光束存在一定大小,激光束范围内的浇口表面较为粗糙时,浇口表面发生漫反射,导致激光的部分或完全损失,使得传感器接收到的激光强度降低,因此本实施例以各个光束扫描区域的光强损失量,即发射光强与接收光强之间的差值大小为各个光束扫描区域中各个位置的异常程度值;此时当反射的激光强度越接近激光发射强度时,对应的光强损失量越小,即发射出的激光大部分都被反射回来,此时浇口表面越平整;反之,则说明该处的浇口表面越不平整。
32.3. 重复上述步骤,得到浇口表面每个位置的异常程度值,根据各个位置的异常程度值得到异常程度图,图中的每个像素点的像素值即为该点对应位置的异常程度值。
33.s203、构建异常程度图的灰度共生矩阵构建异常程度图的灰度共生矩阵,灰度熵是图像所具有的信息量的度量,纹理信息也属于图像的信息,是一个随机性的度量,当共生矩阵中所有元素有最大的随机性、空间共生矩阵中所有值近乎相等时,共生矩阵中元素分散分布时,灰度熵较大。它表示了图像中纹理的非均匀程度或复杂程度。利用灰度共生矩阵的灰度熵来反映异常程度图的灰度复杂程度,即灰度混乱程度。
34.获取异常程度图像中的灰度共生矩阵,该矩阵为矩阵,为图像中灰度值的总数量,矩阵中的每个元素用于表征不同灰度值的像素对出现的概率,其中第行第列的元素记为。
35.s204、计算待检测铸件浇口表面的初始粗糙程度根据异常程度图的灰度共生矩阵的灰度熵计算异常程度图的灰度混乱程度,根据得到的灰度混乱程度来反映待检测铸件浇口表面的粗糙程度,得到出检测铸件浇口表面的初始粗糙程度。
36.计算该灰度共生矩阵的灰度熵,所得熵值越大,表示图像中的灰度混乱程度越高,对应浇口表面的粗糙度越高;由于激光是垂直入射的,可能会存在大面积的无法进行激光反射的区域,在这种情况下,使得灰度值(异常程度)较高的像素点出现的概率较高,使用传统的灰度熵计算方法会出现熵值较小的情况,由此会导致得到表面粗糙度较小的错误结论,因此本实施例不仅需要考虑灰度熵的值,还需要根据灰度熵的大小进一步判断灰度的混乱程度,则铸件浇口表面的初始粗糙程度的计算方法为:获取异常程度图像的灰度共生矩阵中的元素值,根据异常程度图的灰度共生矩阵中的元素值计算待检测铸件浇口表面的初始粗糙程度,计算公式如下:式中:为待检测铸件浇口表面的初始粗糙程度,为异常程度图像的灰度共生矩
阵的尺寸,即异常程度图中灰度值的数量,,为异常程度图像的灰度共生矩阵尺寸的序号,表示异常程度图像的灰度共生矩阵第行第列的元素值,即第行第列像素对出现的概率,表示异常程度图像的灰度共生矩阵中概率最大的元素值,,为出现概率最大的像素对所对应的像素对的灰度值。
37.s205、得到异常程度图中所有高度变化曲线的主峰值点与主峰谷点当相邻的两个铸件浇口表面轮廓峰值点之间的距离越短,且高度差异越小时,铸件浇口表面越光滑,此时浇口表面粗糙度越低,因此浇口表面粗糙度与峰值点之间的距离以及峰值点之间的高度差异程度均成正比。因此需要确定出异常程度图中每一行像素的高度变化曲线中的主峰值点与主峰谷点,用以对待检测铸件浇口表面的初始粗糙程度进行修正。
38.由于激光反射所需要的时间与浇口表面的高度成反比,即高度越高,所需要的时间越短,因此实际反射时间与理论所需反射时间之间的差异值可以作为极值点相对于中线的高度差异程度。本实施例中根据两个波峰之间的距离对波峰点的粗糙度进行评估,但是由于并非所有局部极小值点均为波峰,因此在进行浇口表面粗糙度的计算之前,还需要判断局部极小值的所属类型。
39.1.当激光光束垂直照射到待检测铸件浇口表面时,光线在待检测铸件浇口表面波峰以及波谷处会大部分会发生反射或者是全反射,而在波峰与波谷之间的坡带上基本无法反射,从而形成轮廓峰本身异常程度较低,而两侧异常程度较高的现象。因此轮廓峰可以看作为局部极小值点。
40.因此,使用分水岭分割算法获取异常程度图像的所有局部极小值点;2.对异常程度图中的每一行像素点中各个局部极小值点的反射时间进行分析,则第行像素点中各个局部极小值点的反射时间序列记为;3.由于两个峰值点之间的坡带不一定是光滑的,坡带上可能存在微小突起,激光反射时间反映了铸件浇口表面的相对高度,铸件浇口表面高度变化曲线如图4所示,因此本实施例以铸件浇口表面高度最高的峰值点为进行粗糙度评估的主峰值点,根据两个主峰值点之间的高度变化情况计算该峰值点处的波动程度;4.以为激光反射的理论时间值,当局部极小值点的反射时间小于理论时间值时,认为该局部极小值点为峰值点;否则认为该局部极小值点为峰谷点;5.将中相邻的峰值点划分为一组,以每组峰值点中反射所需时间最小的点为主峰值点。将中相邻的峰谷点划分为一组,以每组峰谷点中反射所需时间最大的点为主峰谷点。
41.至此,确定出异常程度图中每一行像素的高度变化曲线的主峰值点与主峰谷点。
42.s206、计算异常程度图中每个主峰值点的粗糙度由于灰度共生矩阵中的像素点对的差异情况一般为以下三种情况:1.灰度值均较大(对应两个像素点均为粗糙位置的情况);2.灰度值均较小(两个像素点均为平整位置的情况);3.灰度值一个较小一个较大(两个像素点分别为浇口表面轮廓的平整位置和不平整位置的情况);
对于第三种情况所得灰度熵较大,符合其实际粗糙度,而前两种情况所得灰度熵较小,即灰度共生矩阵中存在出现概率较高的像素点对,但是二者的不同之处在于,前者的高概率像素点对的灰度值均较大,后者的高概率像素点对的灰度值均较小,因此当所得灰度熵较小时,需要进一步结合高概率像素点对的灰度值的大小进行修正。
43.1.计算每个主峰值点的粗糙度获取异常程度图中每一行的主峰值点的坐标,根据相邻两个主峰值点的坐标计算相邻两主峰值点的距离,根据相邻两主峰值点的距离以及相邻两主峰值点之间的反射时间计算相邻两主峰值点序号较大的主峰值点的粗糙度,计算公式如下:式中:为第行像素点中第个主峰值点的粗糙度,为光速,表示相邻两个主峰值点之间的主峰谷点对应的像素点的反射时间,为主峰值点对应像素点的反射时间,表示相邻两主峰值点之间的波动程度,为第行像素点中主峰值点的序号。
44.其中,相邻两主峰值点之间的波动程度的计算公式如下:式中:表示第个主峰值点与第个主峰值点之间的波动程度,表示第个主峰值点与第个主峰值点之间局部极小值点的数量,表示第个主峰值点与第个主峰值点之间的距离,表示第个主峰值点与第个主峰值点之间局部极小值点的序号,为相邻两主峰值点之间第个局部极小值点的反射时间。
45.表示两个主峰值点之间,局部极小值点的高度波动程度;由于是根据两个峰值点之间各个极值点相对于中线的高度差异累加所得,当两个峰值点之间的波动率较高,但是各个位置的整体高度差异较小的情况,在实际中这两个峰值点之间较为平整,但是使用上述方法得到的结果可能较大,即上述所得结果仍然存在误差,因此本实施例引入波峰与波谷之间的高度差为权重对所得结果进行修正,该值表示第个主峰值点与该点及第个主峰值点之间的主峰谷点之间的高度差,该值越小,表示两个主峰值点之间的高度差异较小,表面越平整,故而粗糙度越低,反之亦然。
46.s207、计算待检测铸件浇口表面的粗糙程度值由于异常程度图中忽略了各个极小值点之间的高度差异,即高度变化曲线相同时,高度差异较大区域与高度差异较小的区域存在相同的异常程度(灰度值),然而实际上高度差异越大,浇口表面的粗糙程度越大,即上述所得的待检测铸件浇口表面的初始粗糙程度的计算结果仍然不准确,因此本实施例需要结合各个位置的时间差进行分析,对待检测铸件浇口表面的初始粗糙程度进行修正得到待检测铸件浇口表面的粗糙程度值。
47.其中:为待检测铸件浇口表面的粗糙程度值,为待检测铸件浇口表面的初始粗糙程度,为异常程度图的像素行数,为异常程度图的像素行数的序号,为第行像素中主峰值点的数量,为第行像素中主峰值点的序号,为第行第个主峰值点的粗糙度。
48.s208、对待检测铸件浇口进行不同方式的铣削工艺处理根据得到的待检测铸件浇口表面的粗糙程度值确定待检测铸件浇口表面的铣削工艺。
49.确定粗糙阈值;当待检测铸件浇口表面的粗糙程度值时,认为该铸件浇口的粗糙度较高,对待检测铸件浇口进行粗铣;当待检测铸件浇口表面的粗糙程度值时,认为该铸件浇口的粗糙度较低但未达到生产要求,对待检测铸件浇口进行精铣;当待检测铸件浇口表面的粗糙程度值认为浇口表面粗糙度达到生产要求,不需要对待检测铸件浇口进行处理。
50.以上所述仅为本发明的较佳实施例而已,并不用以限制本发明,凡在本发明的精神和原则之内,所作的任何修改、等同替换、改进等,均应包含在本发明的保护范围之内。