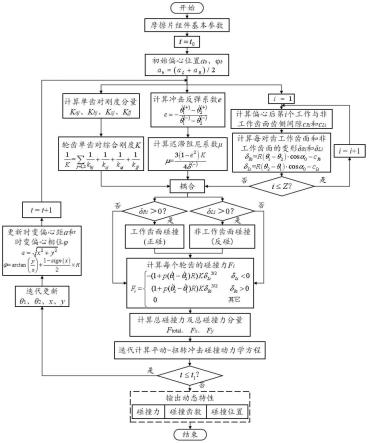
1.本发明涉及摩擦片技术领域,特别涉及一种考虑随机齿向误差的离合器摩擦片冲击力计算方法。
背景技术:2.摩擦片与内毂轮齿在加工过程中不可避免的会使各轮齿间的齿侧间隙呈随机性分布,受摩擦片重力作用的影响摩擦片与内毂会存在一定的偏心距。摩擦片组件运转过程中,由于变速机构的扭转振动等引起内毂转速表现为高频特征的非平稳性,造成摩擦片与内毂发生冲击碰撞,使摩擦片部分齿的齿面受到较大的冲击载荷,引起摩擦片轮齿的齿面与齿根发生疲劳损坏。
3.现有技术对具有齿侧间隙的传动件的冲击动载的研究很少考虑齿形制造误差引起的随机齿向误差的影响,尚未考虑随机齿向误差在重力作用下引起的偏心作用,使最终计算结果与实际值发生较大偏差。同时,考虑随机齿向误差的影响,研究浮动齿圈摩擦片组件的冲击载荷也未发现相关研究。
技术实现要素:4.针对现有技术中未考虑随机齿向误差在重力作用下引起的偏心作用,使获取的摩擦片冲击力与实际值发生较大偏差的问题,本发明提出一种考虑随机齿向误差的离合器摩擦片冲击力计算方法,充分考虑了摩擦片组件轮齿的制造误差引起的随机齿向误差对浮动齿圈摩擦片组件冲击载荷的影响,保证较高计算效率的同时使获取的摩擦片冲击力与实际值误差较小,提高精准性。
5.为了实现上述目的,本发明提供以下技术方案:
6.一种考虑随机齿向误差的离合器摩擦片冲击力计算方法,具体包括以下步骤:
7.s1:获取待计算的浮动支撑摩擦片组件参数,所述摩擦片组件参数包括基本参数和随机齿形制造误差量,所述摩擦片组件包括摩擦片和内毂;
8.s2、基于摩擦片组件的基本参数,利用势能法计算摩擦片与内毂单齿接触的综合刚度;
9.s3、基于摩擦片组件的基本参数和随机齿形制造误差量,计算摩擦片在重力作用下引起的偏心距,以及每时刻摩擦片的时变偏心距和时变偏心相位;
10.s4、根据所述摩擦片与内毂的随机齿侧间隙和相对位置关系,判断摩擦片与内毂是否发生碰撞,确定内毂与摩擦片碰撞齿数和随机碰撞齿位置;
11.s5、基于能量平衡理论和内毂与摩擦片的相对运动关系,计算摩擦片与内毂轮齿间碰撞的冲击反弹系数和迟滞阻尼系数;
12.s6、根据s1中确定的随机齿形制造误差量、s2中确定的摩擦片单齿综合刚度、s3中确定的摩擦片与内毂的时变偏心距和时变偏心相位、s4中确定的内毂与摩擦片碰撞齿数和s5中确定的摩擦片与内毂轮齿间的冲击反弹系数和迟滞阻尼系数,计算摩擦片与内毂每个
接触齿的碰撞力;
13.s7、根据s6中确定的内毂与摩擦片每个轮齿的碰撞力,构建内毂与摩擦片平动-扭转多自由度冲击动载动力学模型,输出每时刻内毂与摩擦片的冲击动载。
14.优选地,所述s1中,摩擦片组件的基本参数包括:摩擦片与内毂的齿数、模数、齿宽、分度圆压力角、弹性模量、泊松比、摩擦片与内毂质量、转动惯量、齿侧间隙、内毂的转速、转速波动频率和幅值。
15.优选地,所述s2包括以下步骤:
16.s201、根据摩擦片组件的参数,利用势能法分别计算内毂或摩擦片的轮齿单齿对的弯曲刚度k
bj
、剪切刚度k
sj
和轴向压缩刚度k
aj
,对应的关系式如下:
[0017][0018][0019][0020]
公式(1)中,j=1时代表内毂;j=2时代表摩擦片;u
aj
、u
bj
和u
sj
分别为内毂轮齿或摩擦片轮齿的轴向压缩、弯曲和剪切变形存储的弹性势能;fj表示内毂轮齿或摩擦片轮齿的啮合点接触载荷;f
aj
为内毂轮齿或摩擦片轮齿的啮合力在水平方向的分量;ej表示内毂轮齿或摩擦片轮齿的弹性模量;a
xj
表示距离内毂轮齿或摩擦片轮齿的固定端x处截面的面积;dj表示内毂轮齿或摩擦片轮齿啮合位置距齿根圆距离;mj为距离内毂轮齿或摩擦片轮齿的固定端x处的弯矩;i
xj
表示距离内毂轮齿或摩擦片轮齿的固定端x处截面的惯性矩;f
bj
为内毂轮齿或摩擦片轮齿的啮合力在竖直方向的分量;gj表示内毂轮齿或摩擦片轮齿的剪切模量;
[0021]
s202、根据摩擦片组件的参数,利用o’donnell变形理论计算轮齿单齿对的基体刚度k
fj
,表达式如下:
[0022][0023]
公式(2)中,j=1时代表内毂;j=2时代表摩擦片;θ
fj
为内毂或摩擦片的轮齿基体的变形;m
fj
为距离内毂轮齿或摩擦片轮齿的固定端x处的单位弯矩;vj表示距离内毂轮齿或摩擦片轮齿的固定端x处的单位剪切力;ej表示内毂轮齿或摩擦片轮齿的弹性模量;υj表示内毂轮齿或摩擦片轮齿的泊松比;h
j’表示距离内毂轮齿或摩擦片轮齿固定端x处截面;fj表示内毂轮齿或摩擦片轮齿的啮合点接触载荷;
[0024]
s203、根据s201中内毂和摩擦片轮齿的弯曲刚度k
bj
、剪切刚度k
sj
、轴向压缩刚度k
aj
和s202中基体刚度k
fj
,获取摩擦片组件轮齿单齿对接触的综合刚度k,计算如下:
[0025]
[0026]
公式(3)中,k表示摩擦片组件轮齿单齿对接触的综合刚度。
[0027]
优选地,所述s3包括以下步骤:
[0028]
s301、内毂与摩擦片之间存在随机齿侧间隙且服从高斯分布,形式如下:
[0029]ci
=normrnd(μ,σ2)
ꢀꢀꢀꢀꢀꢀꢀꢀꢀꢀ
(4)
[0030]
公式(4)中,ci表示不偏心状态第i个齿的齿侧间隙;μ表示齿侧间隙理论值;σ2表示齿侧间隙的离散程度,齿侧间隙的范围在(μ-3σ,μ+3σ)之间分布;
[0031]
s302、重力作用下摩擦片工作齿面先接触产生的偏心距计算如下:
[0032][0033]
公式(5)中,ar表示重力作用下摩擦片工作齿面接触引起的偏心距;abs(
…
)表示绝对值;min(
…
)表示最小值;ci表示不偏心状态第i个齿的齿侧间隙;α0表示压力角;z为摩擦片和内毂的齿数,i为第i个齿的齿序号;
[0034]
重力作用下摩擦片非工作齿面先接触产生的偏心距计算如下:
[0035][0036]
公式(6)中,a
l
表示重力作用下摩擦片非工作齿面接触引起的偏心距;abs(
…
)表示绝对值;min(
…
)表示最小值;ci表示不偏心状态第i个齿的齿侧间隙;α0表示压力角;z为摩擦片和内毂的齿数,i为第i个齿的齿序号;
[0037]
则重力作用下摩擦片产生的初始自偏心距表示为:
[0038]ab
=(a
l
+ar)/2;
[0039]
s303、内毂与摩擦片在转速作用下产生相对位移,摩擦片与内毂形成任意位置的偏心,则任意时刻的偏心距a及偏心相位表示为:
[0040][0041]
公式(7)中,a表示任意时刻摩擦片与内毂的偏心距;表示偏心相位;x为每时刻摩擦片的质心相对于内毂质心在水平方向(x方向)的位移;y为每时刻摩擦片的质心相对于内毂质心在竖直方向(y方向)的位移;sign(x)表示为符号函数。
[0042]
优选地,所述s4包括以下步骤:
[0043]
s401、利用s1所述的内毂与摩擦片的基本参数,计算任一时刻第i个齿的工作齿面与非工作齿面的齿侧间隙,计算形式如下:
[0044][0045]
公式(8)中,c
ri
表示自偏心状态第i个齿的工作齿面的齿侧间隙;c
li
表示自偏心状态第i个齿的非工作齿面的齿侧间隙;ci表示不偏心状态第i个齿的齿侧间隙;a表示任意时刻摩擦片与内毂的偏心距;α0表示压力角;z为摩擦片和内毂的齿数;i为第i个齿的齿序号;
[0046]
s402、考虑摩擦副组件在扭矩作用下的相对位移,计算内毂与摩擦片的工作齿面与非工作齿面的变形量,计算形式如下:
[0047]
δ
ri
=r(θ
1-θ2)cosα
0-c
ri
,δ
li
=r(θ
2-θ1)cosα
0-c
li
ꢀꢀꢀꢀꢀ
(9)
[0048]
公式(9)中,δ
ri
表示内毂与摩擦片第i个齿的工作齿面的变形量;δ
li
表示内毂与摩擦片第i个齿的非工作齿面的变形量;r为分度圆半径;θ1为内毂角位移;θ2为摩擦片角位移;α0为压力角;c
ri
表示自偏心状态第i个齿的工作齿面的齿侧间隙;c
li
表示自偏心状态第i个齿的非工作齿面的齿侧间隙;
[0049]
s403、根据s402的工作齿面变形量δ
ri
和非工作齿面变形量δ
li
的计算结果进行碰撞判断:
[0050]
若δ
ri
>0则摩擦片与内毂的第i个工作齿面发生碰撞(正碰),如图4所示,为正碰接触状态示意图,记c
ri
=1;若δ
li
>0则摩擦片与内毂的第i个非工作齿面发生碰撞(反碰),如图5所示,为反碰接触状态示意图,记c
li
=1;若δ
ri
≤0或δ
li
≤0,则摩擦片与内毂的第i个齿不发生碰撞,记c
ri
=0或c
li
=0;
[0051]
s404、根据s403的计算结果,分别获得内毂与摩擦片正碰和反碰的碰撞齿数,表示为:
[0052][0053]
公式(10)中,z为摩擦片和内毂的齿数;i为第i个齿的齿序号;
[0054]
则内毂与摩擦片轮齿总碰撞齿数为:
[0055]
n=nr+n
l
。
[0056]
优选地,所述s5包括以下步骤:
[0057]
s501、基于赫兹接触理论,非线性冲击碰撞力f表示为:
[0058][0059]
公式(11)中,kδm表示弹性接触力部分;是冲击阻尼力部分,δ为齿部法向相对变形量;为碰撞过程中相对速度;m为非线性指数,m=1.5;μ为迟滞阻尼系数;
[0060]
s502、轮齿碰撞开始接触到碰撞结束分离时的能量损耗δt表示为:
[0061][0062]
公式(12)中,m1为内毂的质量;m2为摩擦片的质量;为碰撞前轮齿的相对速度;e为冲击反弹系数;
[0063]
冲击反弹系数e定义为两物体碰撞前的相对接近速度与碰撞后的相对分离速度的比值,表示为:
[0064][0065]
公式(13)中,为碰撞结束分离时内毂的速度;为碰撞结束分离时摩擦片的速度;为碰撞开始接触时内毂的速度;为碰撞开始接触时摩擦片的速度;
[0066]
s503、当轮齿碰撞以阻尼力形式做功的能量耗散δt表示为:
[0067][0068]
公式(14)中,δ0为轮齿碰撞的最大变形量;k表示摩擦片组件轮齿单齿对接触的综合刚度;
[0069]
s504、根据能量守恒定理,结合式(12)和式(14)得到迟滞阻尼系数μ,表示为:
[0070][0071]
公式(15)中,e为冲击反弹系数;k表示摩擦片组件轮齿单齿对接触的综合刚度;为碰撞前轮齿的相对速度。
[0072]
优选地,所述s6包括以下步骤:
[0073]
s601、轮齿的冲击力合力依靠内毂轮齿与摩擦片轮齿相互碰撞来传递,结合式(3)、式(9)和式(15),任意时刻内毂与摩擦片工作齿面与非工作齿面的碰撞力计算为
[0074][0075]
公式(16)中,fi表示摩擦片与内毂第i个齿的碰撞力;p=μ/k;μ为迟滞阻尼系数;k表示摩擦片组件轮齿单齿对接触的综合刚度;为内毂角速度;为摩擦片角速度;r表示分度圆半径;δ
l
表示内毂与摩擦片轮齿非工作齿面的变形量;δr表示内毂与摩擦片轮齿工作齿面的变形量;
[0076]
s602、第i个齿正碰和反碰的法向冲击碰撞力在x方向和y方向上碰撞力分量分别表示为:
[0077][0078]
公式(17)中,f
xi
表示第i个齿的法向冲击碰撞力在x方向上碰撞力分量;f
yi
表示第i个齿的法向冲击碰撞力在y方向上碰撞力分量;fi表示摩擦片与内毂第i个齿的碰撞力;α0为压力角;i为第i个齿;z为齿的总数;ω为浮动齿圈角速度;θ0为分度圆齿厚的半齿角,δ
ri
表示内毂与摩擦片第i个齿的工作齿面的变形量;δ
li
表示内毂与摩擦片第i个齿的非工作齿面的变形量;t表示为时间。
[0079]
优选地,所述s7包括以下步骤:
[0080]
s701、由于内毂扭转振动造成摩擦片的转速波动,内毂输入角速度ω及输入角加速度α表示为
[0081]
ω=ω0+asin(2πft),α=2πfacos(2πft)
ꢀꢀꢀꢀꢀꢀꢀꢀ
(18)
[0082]
公式(18)中,ω表示内毂转速波动,ω0表示恒定转速;a为转速波动幅值;f为转速波动频率;t表示t时刻;α表示内毂输入角加速度;
[0083]
s702、建立内毂平动-扭转动力学方程,其形式如下:
[0084][0085]
公式(19)中,m1表示内毂的质量;表示内毂在x方向的加速度;x1表示内毂在x方向的位移;表示内毂在x方向的速度;表示内毂在y方向的加速度;y1表示内毂在y方向的位移;表示内毂在y方向的速度;k
1x
表示内毂在x方向的支撑刚度;c
1x
表示内毂在x方向的支撑阻尼;f
xi
表示第i个齿的法向冲击碰撞力在x方向上碰撞力分量;f
yi
表示第i个齿的法向冲击碰撞力在y方向上碰撞力分量;j1表示内毂的转动惯量;为内毂角加速度;α表示内毂输入角加速度;fi表示摩擦片与内毂第i个齿的碰撞力;i表示第i个齿;z为轮齿的总数;r为分度圆半径;α0为压力角;
[0086]
s703、建立摩擦片平动-扭转动力学方程,其形式如下
[0087][0088]
公式(20)中,m2表示摩擦片的质量;表示摩擦片在x方向的加速度;x2表示摩擦片在x方向的位移;表示摩擦片在x方向的加速度;表示摩擦片在y方向的加速度;y2表示摩擦片在y方向的位移;表示摩擦片在y方向的速度;k
2x
表示摩擦片在x方向的支撑刚度;c
2x
表示摩擦片在x方向的支撑阻尼;f
xi
表示第i个齿的法向冲击碰撞力在x方向上碰撞力分量;f
yi
表示第i个齿的法向冲击碰撞力在y方向上碰撞力分量;j2表示摩擦片的转动惯量;为摩擦片角加速度;α0为压力角;fi表示摩擦片与内毂第i个齿的碰撞力;i表示第i个齿;z为轮齿的总数;r为分度圆半径;
[0089]
s704、对s702中构建的内毂平动-扭转动力学方程和s703中构建的摩擦片平动-扭转动力学方程时间t内迭代计算,输出每时刻内毂与摩擦片的所有齿的总冲击载荷和单个轮齿的冲击载荷。
[0090]
综上所述,由于采用了上述技术方案,与现有技术相比,本发明至少具有以下有益效果:
[0091]
本发明提供了一种利用能量法求解内毂与摩擦片的单齿接触的综合刚度的方法;
[0092]
本发明还提供了一种摩擦片与内毂在制造过程中引起随机齿向误差的情况下摩擦片在重力作用下产生的初始偏心距计算方法,以及每时刻摩擦片的时变偏心距和时变偏心相位的迭代计算方法。
[0093]
本发明还提供了一种摩擦片与内毂的轮齿间存在随机齿向误差和摩擦片产生时变偏心距和时变偏心相位的情况下,内毂与摩擦片齿面任意时刻发生正碰、反碰的确定方法以及碰撞齿数和随机碰撞齿位置的计算方法;
[0094]
本发明还提供了一种摩擦片与内毂与摩擦片轮齿碰撞前后的冲击反弹系数的确定方法;
[0095]
本发明还提供了一种内毂与摩擦片的任意时刻每个轮齿发生正碰、反碰的齿部碰撞力的计算方法;
[0096]
本发明还提供了一种内毂与摩擦片的平动-扭转多自由度冲击动载动力学模型迭代计算方法,确定每时刻内毂与摩擦片的冲击载荷,保证较高计算效率的同时使获取的摩擦片冲击力与实际值误差较小,提高获取的摩擦片冲击力精准性。
附图说明:
[0097]
图1为根据本发明示例性实施例的一种考虑随机齿向误差的离合器摩擦片冲击力计算方法示意图。
[0098]
图2为根据本发明示例性实施例的不偏心随机齿侧间隙初始状态示意图。
[0099]
图3为根据本发明示例性实施例的重力作用下初始偏心距状态示意图。
[0100]
图4为根据本发明示例性实施例的正碰接触状态示意图。
[0101]
图5为根据本发明示例性实施例的反碰接触状态示意图。
具体实施方式
[0102]
下面结合实施例及具体实施方式对本发明作进一步的详细描述。但不应将此理解为本发明上述主题的范围仅限于以下的实施例,凡基于本发明内容所实现的技术均属于本发明的范围。
[0103]
在本发明的描述中,需要理解的是,术语“纵向”、“横向”、“上”、“下”、“前”、“后”、“左”、“右”、“竖直”、“水平”、“顶”、“底”“内”、“外”等指示的方位或位置关系为基于附图所示的方位或位置关系,仅是为了便于描述本发明和简化描述,而不是指示或暗示所指的装置或元件必须具有特定的方位、以特定的方位构造和操作,因此不能理解为对本发明的限制。
[0104]
如图1所示,本发明提供一种考虑随机齿向误差的离合器摩擦片冲击力计算方法,包括以下步骤:
[0105]
s1、获取待计算的浮动支撑摩擦片组件参数,所述摩擦片组件参数包括基本参数和随机齿形制造误差量,所述摩擦片组件包括摩擦片和内毂。
[0106]
本实施例中,浮动支撑摩擦片组件的基本参数包括:摩擦片与内毂的齿数、模数、齿宽、分度圆压力角、弹性模量、泊松比、摩擦片与内毂质量、转动惯量、齿侧间隙、内毂的转速、转速波动频率和幅值等。
[0107]
s2、基于摩擦片组件的基本参数,利用势能法计算摩擦片与内毂单齿接触的综合刚度。
[0108]
s201、根据摩擦片组件的参数,利用势能法分别计算内毂或摩擦片的轮齿单齿对的弯曲刚度k
bj
、剪切刚度k
sj
和轴向压缩刚度k
aj
,对应的关系式如下:
[0109][0110][0111][0112]
公式(1)中,j=1时代表内毂;j=2时代表摩擦片;u
aj
、u
bj
和u
sj
分别为内毂轮齿或摩擦片轮齿的轴向压缩、弯曲和剪切变形存储的弹性势能;fj表示内毂轮齿或摩擦片轮齿的啮合点接触载荷;f
aj
为内毂轮齿或摩擦片轮齿的啮合力在水平方向的分量;ej表示内毂轮齿或摩擦片轮齿的弹性模量;a
xj
表示距离内毂轮齿或摩擦片轮齿的固定端x处截面的面积;dj表示内毂轮齿或摩擦片轮齿啮合位置距齿根圆距离;mj为距离内毂轮齿或摩擦片轮齿的固定端x处的弯矩;i
xj
表示距离内毂轮齿或摩擦片轮齿的固定端x处截面的惯性矩;f
bj
为内毂轮齿或摩擦片轮齿的啮合力在竖直方向的分量;gj表示内毂轮齿或摩擦片轮齿的剪切模量;
[0113]
s202、根据摩擦片组件的参数,利用o’donnell变形理论计算轮齿单齿对的基体刚度k
fj
,表达式如下:
[0114][0115]
公式(2)中,j=1时代表内毂;j=2时代表摩擦片;θ
fj
为内毂或摩擦片的轮齿基体的变形;m
fj
为距离内毂轮齿或摩擦片轮齿的固定端x处的单位弯矩;vj表示距离内毂轮齿或摩擦片轮齿的固定端x处的单位剪切力;ej表示内毂轮齿或摩擦片轮齿的弹性模量;υj表示内毂轮齿或摩擦片轮齿的泊松比;h
j’表示距离内毂轮齿或摩擦片轮齿固定端x处截面;fj表示内毂轮齿或摩擦片轮齿的啮合点接触载荷;
[0116]
s203、根据s201中内毂和摩擦片轮齿的弯曲刚度k
bj
、剪切刚度k
sj
、轴向压缩刚度k
aj
和s202中基体刚度k
fj
,获取摩擦片组件轮齿单齿对接触的综合刚度k,计算如下:
[0117][0118]
s3、基于摩擦片组件的基本参数和随机齿形制造误差量,计算摩擦片在重力作用下引起的偏心距,以及每时刻摩擦片的时变偏心距和时变偏心相位。
[0119]
s301、内毂与摩擦片在加工过程中存在误差,会产生随机齿侧间隙,如图2所示,不偏心状态下摩擦片与内毂的轮齿之间存在多个单侧齿侧间隙c1、c2、ci、cn,假设单侧齿侧间隙服从高斯分布,计算形式如下
[0120]ci
=normrnd(μ,σ2)
ꢀꢀꢀꢀꢀꢀꢀꢀꢀ
(4)
[0121]
公式(4)中,ci表示不偏心状态第i个齿的齿侧间隙;μ表示齿侧间隙理论值;σ2表示齿侧间隙的离散程度;齿侧间隙的范围在(μ-3σ,μ+3σ)之间分布。
[0122]
s302、如图3所示,因此重力作用下摩擦片会产生初始自偏心距ab;
[0123]
本实施例中,重力作用下摩擦片右侧齿(工作齿面)先接触产生的偏心距计算如下:
[0124][0125]
公式(5)中,ar表示重力作用下摩擦片右侧齿(工作齿面)接触引起的偏心距;abs(
…
)表示绝对值;min(
…
)表示最小值;ci表示不偏心状态第i个齿的齿侧间隙;α0表示压力角;z为摩擦片和内毂的齿数,i为第i个齿的齿序号;
[0126]
重力作用下摩擦片左侧齿(非工作齿面)先接触产生的偏心距计算如下:
[0127][0128]
公式(6)中,a
l
表示重力作用下摩擦片左侧齿(工作齿面)接触引起的偏心距;abs(
…
)表示绝对值;min(
…
)表示最小值;ci表示不偏心状态第i个齿的齿侧间隙;α0表示压力角;z为摩擦片和内毂的齿数,i为第i个齿的齿序号;
[0129]
重力作用下摩擦片产生的初始自偏心距ab可表示为:
[0130]ab
=(a
l
+ar)/2。
[0131]
s303、内毂与摩擦片在转速作用下会产生相对位移,使摩擦片与内毂形成任意位置的偏心,任意时刻的偏心距a及偏心相位(与x轴正方向的夹角)可表示为
[0132][0133]
公式(7)中,a表示任意时刻摩擦片与内毂的偏心距;表示偏心相位;x为每时刻摩擦片的质心相对于内毂质心在水平方向(x方向)的位移;y为每时刻摩擦片的质心相对于内毂质心在竖直方向(y方向)的位移;sign(x)表示为符号函数。
[0134]
s4、根据所述摩擦片与内毂的随机齿侧间隙和相对位置关系,判断摩擦片与内毂是否发生碰撞,确定内毂与摩擦片碰撞齿数和随机碰撞齿位置。
[0135]
s401、利用s1所述的内毂与摩擦片的基本参数,计算任一时刻第i个齿的工作齿面与非工作齿面的齿侧间隙,计算形式如下:
[0136][0137]
公式(8)中,c
ri
表示自偏心状态第i个齿的工作齿面的齿侧间隙;c
li
表示自偏心状态第i个齿的非工作齿面的齿侧间隙;ci表示不偏心状态第i个齿的齿侧间隙;a表示任意时刻摩擦片与内毂的偏心距;α0表示压力角;z为摩擦片和内毂的齿数;i为第i个齿的齿序号;表示偏心相位。
[0138]
s402、考虑摩擦副组件在扭矩作用下的相对位移,计算内毂与摩擦片的工作齿面与非工作齿面的变形量,计算形式如下:
[0139]
δ
ri
=r(θ
1-θ2)cosα
0-c
ri
,δ
li
=r(θ
2-θ1)cosα
0-c
li
ꢀꢀꢀꢀꢀ
(9)
[0140]
公式(9)中,δ
ri
表示内毂与摩擦片第i个齿的工作齿面的变形量;δ
li
表示内毂与摩擦片第i个齿的非工作齿面的变形量;r为分度圆半径;θ1为内毂角位移;θ2为摩擦片角位移;
α0为压力角;c
ri
表示自偏心状态第i个齿的工作齿面的齿侧间隙;c
li
表示自偏心状态第i个齿的非工作齿面的齿侧间隙。
[0141]
s403、根据s402的工作齿面变形量δ
ri
和非工作齿面变形量δ
li
的计算结果进行碰撞判断:
[0142]
若δ
ri
>0则摩擦片与内毂的第i个工作齿面发生碰撞(正碰),如图4所示,为正碰接触状态示意图,记c
ri
=1;若δ
li
>0则摩擦片与内毂的第i个非工作齿面发生碰撞(反碰),如图5所示,为反碰接触状态示意图,记c
li
=1;若δ
ri
≤0或δ
li
≤0,则摩擦片与内毂的第i个齿不发生碰撞,记c
ri
=0或c
li
=0,通过c
ri
和c
li
可判断碰撞齿位置。
[0143]
s404、根据s403的计算结果,可分别获得内毂与摩擦片正碰和反碰的碰撞齿数,可表示为:
[0144][0145]
公式(10)中,z为摩擦片和内毂的齿数;i为第i个齿的齿序号;
[0146]
则内毂与摩擦片轮齿总碰撞齿数为:
[0147]
n=nr+n
l
。
[0148]
s5、基于能量平衡理论和内毂与摩擦片的相对运动关系,计算摩擦片与内毂轮齿间碰撞的冲击反弹系数和迟滞阻尼系数。
[0149]
s501、基于赫兹接触理论,非线性冲击碰撞力可表示为:
[0150][0151]
公式(11)中,kδm表示弹性接触力部分;是冲击阻尼力部分,δ为齿部法向相对变形量;为碰撞过程中相对速度;m为非线性指数,m=1.5;μ为迟滞阻尼系数;
[0152]
s502、轮齿碰撞开始接触到碰撞结束分离时的能量损耗可表示为:
[0153][0154]
公式(12)中,m1为内毂的质量;m2为摩擦片的质量;为碰撞前轮齿的相对速度;e为冲击反弹系数。
[0155]
冲击反弹系数e定义为两物体碰撞前的相对接近速度与碰撞后的相对分离速度的比值,表示为:
[0156][0157]
公式(13)中,为碰撞结束分离时内毂的速度;为碰撞结束分离时摩擦片的速度;为碰撞开始接触时内毂的速度;为碰撞开始接触时摩擦片的速度。
[0158]
s503、当轮齿碰撞以阻尼力形式做功的能量耗散δt可表示为:
[0159]
[0160]
公式(14)中,δ0为轮齿碰撞的最大变形量。
[0161]
s504、根据能量守恒定理,结合式(12)和式(14)可得到迟滞阻尼系数μ,可表示为:
[0162][0163]
公式(15)中,e为冲击反弹系数;k表示摩擦片组件轮齿单齿对接触的综合刚度;为碰撞前轮齿的相对速度。
[0164]
s6、根据s1中确定的随机齿形制造误差量、s2中确定的摩擦片单齿综合刚度、s3中确定的摩擦片与内毂的时变偏心距和时变偏心相位、s4中确定的内毂与摩擦片碰撞齿数和s5中确定的摩擦片与内毂轮齿间的冲击反弹系数和迟滞阻尼系数,基于hertz接触理论,计算摩擦片与内毂每个接触齿的碰撞力。
[0165]
s601、轮齿的冲击力合力依靠内毂轮齿与摩擦片轮齿相互碰撞来传递,采用hertz接触力学模型可以描述接触面之间的非线性冲击碰撞作用。基于hertz接触理论,结合式(3)、式(9)和式(15),任意时刻内毂与摩擦片工作齿面与非工作齿面的碰撞力可计算为
[0166][0167]
公式(16)中,fi表示摩擦片与内毂第i个齿的碰撞力;p=μ/k;μ为迟滞阻尼系数;k表示摩擦片组件轮齿单齿对接触的综合刚度;为内毂角速度;为摩擦片角速度;r表示分度圆半径;δ
l
表示内毂与摩擦片轮齿非工作齿面的变形量;δr表示内毂与摩擦片轮齿工作齿面的变形量;
[0168]
s602、第i个齿正碰和反碰的法向冲击碰撞力在x方向和y方向上碰撞力分量分别可表示为:
[0169][0170]
公式(17)中,f
xi
表示第i个齿的法向冲击碰撞力在x方向上碰撞力分量;f
yi
表示第i个齿的法向冲击碰撞力在y方向上碰撞力分量;fi表示摩擦片与内毂第i个齿的碰撞力;α0为压力角;i为第i个齿;z为齿的总数;ω为浮动齿圈角速度;θ0为分度圆齿厚的半齿角,δ
ri
表示内毂与摩擦片第i个齿的工作齿面的变形量;δ
li
表示内毂与摩擦片第i个齿的非工作齿面的变形量;t表示为时间。
[0171]
s7、根据s6中确定的内毂与摩擦片每个轮齿的碰撞力,基于牛顿力学理论,构建内毂与摩擦片平动-扭转多自由度冲击动载动力学模型,计算每时刻内毂与摩擦片的冲击动载。
[0172]
s701、由于内毂扭转振动造成摩擦片的转速波动,内毂输入角速度ω及输入角加速度α可表示为
[0173]
ω=ω0+asin(2πft),α=2πfacos(2πft)
ꢀꢀꢀꢀꢀꢀꢀꢀꢀꢀ
(18)
[0174]
公式(18)中,ω表示内毂转速波动,ω0表示恒定转速;a为转速波动幅值;f为转速波动频率;t表示t时刻;α表示内毂输入角加速度。
[0175]
s702、建立内毂平动-扭转动力学方程,其形式如下:
[0176][0177]
公式(19)中,m1表示内毂的质量;表示内毂在x方向(水平方向)的加速度;x1表示内毂在x方向(水平方向)的位移;表示内毂在x方向(水平方向)的速度;表示内毂在y方向(竖直方向)的加速度;y1表示内毂在y方向(竖直方向)的位移;表示内毂在y方向(竖直方向)的速度;k
1x
表示内毂在x方向的支撑刚度;c
1x
表示内毂在x方向的支撑阻尼;f
xi
表示第i个齿的法向冲击碰撞力在x方向上碰撞力分量;f
yi
表示第i个齿的法向冲击碰撞力在y方向上碰撞力分量;j1表示内毂的转动惯量;为内毂角加速度;α表示内毂输入角加速度;fi表示摩擦片与内毂第i个齿的碰撞力;i表示第i个齿;z为齿数(轮齿的总数);r为分度圆半径;α0为压力角;
[0178]
s703、建立摩擦片平动-扭转动力学方程,其形式如下
[0179][0180]
公式(20)中,m2表示摩擦片的质量;表示摩擦片在x方向(水平方向)的加速度;x2表示摩擦片在x方向(水平方向)的位移;表示摩擦片在x方向(水平方向)的加速度;表示摩擦片在y方向(竖直方向)的加速度;y2表示摩擦片在y方向(竖直方向)的位移;表示摩擦片在y方向(竖直方向)的速度;k
2x
表示摩擦片在x方向的支撑刚度;c
2x
表示摩擦片在x方向的支撑阻尼;f
xi
表示第i个齿的法向冲击碰撞力在x方向上碰撞力分量;f
yi
表示第i个齿的法向冲击碰撞力在y方向上碰撞力分量;j2表示摩擦片的转动惯量;为摩擦片角加速度;α0为压力角;fi表示摩擦片与内毂第i个齿的碰撞力;i表示第i个齿;z为齿数(轮齿的总数);r为分度圆半径。
[0181]
s704、利用龙格库塔法对s702中构建的内毂平动-扭转动力学方程和s703中构建的摩擦片平动-扭转动力学方程时间t内迭代计算,若t≤t1,更新θ1、θ2、x、y以及更新时变偏心距和时变偏心相位,并将t+1,重复s2-s6;若t>t1,输出每时刻内毂与摩擦片的所有齿的总冲击载荷和单个轮齿的冲击载荷。
[0182]
本领域的普通技术人员可以理解,上述各实施方式是实现本发明的具体实施例,而在实际应用中,可以在形式上和细节上对其作各种改变,而不偏离本发明的精神和范围。