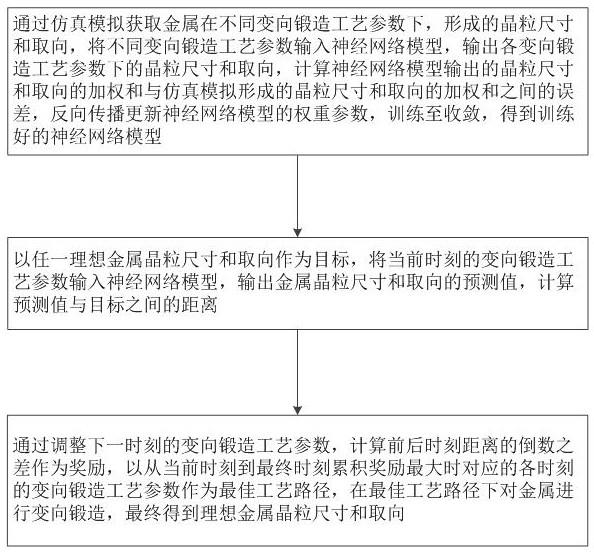
1.本发明属于金属智能制造领域,更具体地,涉及一种变向锻造成形的金属晶粒尺寸和取向的智能协同调控方法。
背景技术:2.制造业是国民经济的主体,也是“创新驱动,转型升级”的主战场,发展金属智能塑性成形工艺及方法,对于推动我国新时期的经济发展尤为重要。航空航天等关键零部件的加工对材料的服役性能有较高要求,根据性能导向定制化加工工艺,获得金属理想的微观组织特征具有重要应用前景。受加工路径、变形温度、应变速率等加工参数的影响,金属材料会经历复杂的微观组织演变过程,晶粒尺寸和取向特征均会发生改变。如何通过设计变形工艺及参数,调控材料在变形过程中的理想晶粒尺寸和取向特征,是当前研究的难点。
3.目前关于金属材料晶粒尺寸和取向调控的研究多是采用挤压、轧制或多向锻造等大变形工艺。申请号为202111155892.9,名称为“一种镁及镁合金无缝管材螺旋挤压装置及挤压工艺”的发明专利,其设计的装置通过在模具和螺旋内芯间形成坯料非均匀切变区,实现镁合金坯料在挤压过程中的螺旋流动,细化了晶粒尺寸并对镁及镁合金沿挤压方向的丝织构进行连续弱化以减小材料的拉压各向异性。该方法存在的问题是,只能单一的实现沿挤压方向的晶粒尺寸和取向改变的功能,而不能针对所需材料的性能,对材料任意的晶粒尺寸和取向特征进行智能调控。申请号为202111560971.8,名称为“一种大型饼类锻件的变向锻造工艺”的发明专利,其通过镦粗、横向压扁、压方倒角、滚圆后旋转镦粗四个步骤,实现改善锻件内部疏松,破碎夹杂物等缺陷,提高产品质量的目的。该方法存在的问题是,加工参数的选择依赖于人工经验和实验试错,成本较高,且无法实现对材料微观织构的有效调控。
4.由此可见,现有技术存在依赖于人工经验和实验试错、成本较高、难以对材料任意的晶粒尺寸和取向特征进行智能调控的技术问题。
技术实现要素:5.针对现有技术的以上缺陷或改进需求,本发明提供了一种变向锻造成形的金属晶粒尺寸和取向的智能协同调控方法,由此解决通过设计工艺参数对金属进行塑性变形优化微观组织的现有技术存在依赖于人工经验和实验试错、成本较高、难以对材料任意的晶粒尺寸和取向特征进行智能调控的技术问题。
6.为实现上述目的,按照本发明的一个方面,提供了一种变向锻造成形的金属晶粒尺寸和取向的智能协同调控方法,包括:以任一理想金属晶粒尺寸和取向作为目标,将当前时刻的变向锻造工艺参数输入神经网络模型,输出金属晶粒尺寸和取向的预测值,计算预测值与目标之间的距离;通过调整下一时刻的变向锻造工艺参数,计算前后时刻距离的倒数之差作为奖励,以从当前时刻到最终时刻累积奖励最大时对应的各时刻的变向锻造工艺参数作为最佳
工艺路径,在最佳工艺路径下对金属进行变向锻造,最终得到理想金属晶粒尺寸和取向;所述神经网络模型通过如下方式训练得到:通过仿真模拟获取金属在不同变向锻造工艺参数下,形成的晶粒尺寸和取向,将不同变向锻造工艺参数输入神经网络模型,输出各变向锻造工艺参数下的晶粒尺寸和取向,计算神经网络模型输出的晶粒尺寸和取向的加权和与仿真模拟形成的晶粒尺寸和取向的加权和之间的误差,反向传播更新神经网络模型的权重参数,训练至收敛,得到训练好的神经网络模型。
7.进一步地,所述变向锻造工艺参数包括变形方向和变形参数,所述神经网络模型的训练数据通过如下方式构造:通过金属在不同变形方向和不同变形参数下进行压缩的力学响应和微观表征数据,拟合晶体塑性模型和微观组织状态方程;对金属进行有限元模拟,提取不同变形方向和不同变形参数下锻造形成的金属心部有限单元上积分点的变形梯度,将变形梯度代入晶体塑性模型,计算金属各个晶粒的位错滑移、变形孪晶,得到应力应变分布和位错密度;将应力应变分布和位错密度代入金属的微观组织状态方程,计算再结晶分数和晶粒尺寸,将位错密度减去用于再结晶的位错密度,得到新的位错密度,将新的位错密度带入晶体塑性模型,得到取向;将不同变形方向、不同变形参数作为训练数据,将不同变形方向、不同变形参数下锻造金属,形成的晶粒尺寸和取向作为训练数据的模拟输出,用于与神经网络模型的输出进行对比。
8.进一步地,所述将新的位错密度带入晶体塑性模型,得到用于描述取向的欧拉角,所述取向通过如下方式描述:其中,为对称广义谐波函数,是对称广义谐波函数的系数,为阶数,为晶体坐标系中的水平方向,为晶体坐标系中的垂直方向,m(l)和n(l)描述了晶体对称性和金属对称性的线性独立谐波数,为晶体坐标系中的欧拉角,分别表示章动角,进动角,自转角。
9.进一步地,所述变形方向包括:轧向、横向和厚度方向,所述变形参数包括:应变量、应变速率和变形温度,所述训练数据以及训练数据的模拟输出均进行归一化处理。
10.进一步地,所述晶粒尺寸和取向的加权和为:归一化后的晶粒尺寸
×
权重系数+归一化后的取向
×
(1-权重系数),其中,权重系数的取值范围是0.4-0.6。
11.进一步地,所述距离通过如下方式计算:
其中,f为t时刻的预测值,为目标,为预测值与目标之间的距离,f
t
为通过神经网络模型预测的t时刻的变向锻造工艺参数对应的金属晶粒尺寸和取向的预测值。
12.进一步地,所述奖励通过如下方式计算:其中,t为当前时刻,为折扣因子,取值范围为[0,1],r为奖励,和分别为t+1和t时刻的预测值。
[0013]
按照本发明的另一方面,提供了一种变向锻造成形的金属晶粒尺寸和取向的智能协同调控系统,包括:训练模块,用于通过仿真模拟获取金属在不同变向锻造工艺参数下,形成的晶粒尺寸和取向,将不同变向锻造工艺参数输入神经网络模型,输出各变向锻造工艺参数下的晶粒尺寸和取向,计算神经网络模型输出的晶粒尺寸和取向的加权和与仿真模拟形成的晶粒尺寸和取向的加权和之间的误差,反向传播更新神经网络模型的权重参数,训练至收敛,得到训练好的神经网络模型;调控模块,用于以任一理想金属晶粒尺寸和取向作为目标,将当前时刻的变向锻造工艺参数输入神经网络模型,输出金属晶粒尺寸和取向的预测值,计算预测值与目标之间的距离;通过调整下一时刻的变向锻造工艺参数,计算前后时刻距离的倒数之差作为奖励,以从当前时刻到最终时刻累积奖励最大时对应的各时刻的变向锻造工艺参数作为最佳工艺路径,在最佳工艺路径下对金属进行变向锻造,最终得到理想金属晶粒尺寸和取向。
[0014]
进一步地,所述变向锻造工艺参数包括变形方向和变形参数,所述训练模块,用于通过金属在不同变形方向和不同变形参数下进行压缩的力学响应和微观表征数据,拟合晶体塑性模型和微观组织状态方程;对金属进行有限元模拟,提取不同变形方向和不同变形参数下锻造形成的金属心部有限单元上积分点的变形梯度,将变形梯度代入晶体塑性模型,计算金属各个晶粒的位错滑移、变形孪晶,得到应力应变分布和位错密度;将应力应变分布和位错密度代入金属的微观组织状态方程,计算再结晶分数和晶粒尺寸,将位错密度减去用于再结晶的位错密度,得到新的位错密度,将新的位错密度带入晶体塑性模型,得到取向;将不同变形方向、不同变形参数作为训练数据,将不同变形方向、不同变形参数下锻造金属,形成的晶粒尺寸和取向作为训练数据的模拟输出,用于与神经网络模型的输出进行对比。
[0015]
总体而言,通过本发明所构思的以上技术方案与现有技术相比,能够取得下列有益效果:(1)本发明提出的一种变向锻造成形的金属晶粒尺寸和取向的智能协同调控方法,该方法可以通过调整变向锻造工艺参数,对金属材料任意的晶粒尺寸和取向进行智能调控,定制和优化材料的力学性能。引入神经网络,可以准确快速的进行预测,由此提高效
率,降低成本。引入强化学习的方法,可以针对金属理想的晶粒尺寸和取向,智能优化变向锻造工艺参数,找到通向目标结构的最佳工艺路径,准确性高,可靠性强。
[0016]
(2)本发明在获取训练数据时,通过宏微观跨尺度模拟方法,将宏观有限元模型与晶体塑性模型、材料微观组织状态方程进行迭代耦合,可以实现金属在变向锻造过程中宏观应力应变,微观再结晶分数、晶粒尺寸和取向特征的协同预测,由此获取的数据集进行训练,得到预测结果准确可靠的神经网络。
[0017]
(3)晶体塑性模型中滑移系和孪晶系的schmid因子反映了多晶体中滑移系和孪晶系的激活程度,由此改变晶体取向的欧拉角。基于此,采用欧拉角作为对称广义谐波函数的输入,通过广义球谐(gsh)矢量对金属的取向分布函数进行逼近,来表示金属的取向特征,可以降低数据维度以提高训练效率。对训练数据进行归一化处理是为了提高模型精度和泛化能力。
[0018]
(4)本发明可以在金属的不同方向进行变形,通过调整合适的工艺参数,包括变形方向、应变速率、应变量和变形温度,从而促进金属的晶体取向在变形过程中发生指定方向的旋转和指定滑移系、孪晶系的激活,并有效细化晶粒,实现理想晶粒尺寸和取向特征的调控。
[0019]
(5)本发明设计了晶粒尺寸和取向的加权和表达,可以实现晶粒尺寸和取向的多目标协同优化。本发明在计算距离的时候计算的是初始时刻至某个时刻的累计距离,这样充分考虑了当前时刻和之前时刻的误差,有助于寻找最佳工艺路径。本发明设计的奖励函数,由于充分考虑了前后时刻的误差,得到一个更密集的学习奖励信息,有助于强化学习的准确寻优。
附图说明
[0020]
图1是本发明实施例提供的方法流程图。
[0021]
图2中(a)是本发明实施例提供的厚度方向nd锻造示意图。
[0022]
图2中(b)是本发明实施例提供的轧向rd锻造示意图。
[0023]
图2中(c)是本发明实施例提供的横向td锻造示意图。
具体实施方式
[0024]
为了使本发明的目的、技术方案及优点更加清楚明白,以下结合附图及实施例,对本发明进行进一步详细说明。应当理解,此处所描述的具体实施例仅仅用以解释本发明,并不用于限定本发明。此外,下面所描述的本发明各个实施方式中所涉及到的技术特征只要彼此之间未构成冲突就可以相互组合。
[0025]
针对现有技术在对金属进行塑性变形优化微观组织时,工艺参数的设计多依赖经验和实验试错的方法,实验和人力成本较高,同时面临无法实现对金属任意的晶粒尺寸和取向进行智能化、协同化、精准化调控的技术瓶颈。本发明提供了一种变向锻造成形的金属晶粒尺寸和取向的智能协同调控方法,如图1所示,包括:以任一理想金属晶粒尺寸和取向作为目标,将当前时刻的变向锻造工艺参数输入神经网络模型,输出金属晶粒尺寸和取向的预测值,计算预测值与目标之间的距离;通过调整下一时刻的变向锻造工艺参数,计算前后时刻距离的倒数之差作为奖
励,以从当前时刻到最终时刻累积奖励最大时对应的各时刻的变向锻造工艺参数作为最佳工艺路径,在最佳工艺路径下对金属进行变向锻造,最终得到理想金属晶粒尺寸和取向;所述神经网络模型通过如下方式训练得到:通过仿真模拟获取金属在不同变向锻造工艺参数下,形成的晶粒尺寸和取向,将不同变向锻造工艺参数输入神经网络模型,输出各变向锻造工艺参数下的晶粒尺寸和取向,计算神经网络模型输出的晶粒尺寸和取向的加权和与仿真模拟形成的晶粒尺寸和取向的加权和之间的误差,反向传播更新神经网络模型的权重参数,训练至收敛,得到训练好的神经网络模型。
[0026]
训练过程的金属和智能协同调控时的金属是相同的,金属材料、金属初始织构、初始晶粒尺寸一致。
[0027]
神经网络模型的训练包括:变向锻造工艺参数包括变形方向和变形参数,变形方向(di)包括:轧向(rd)、横向(td)、厚度方向(nd)三个方向,变形参数具体指,应变速率,取值范围为:0.001~1s-1
;变形温度,取值范围为:金属的再结晶温度~金属的熔点以下100℃;应变量,取值范围为:0~1;通过金属在不同变形方向和不同变形参数下进行压缩的力学响应和微观表征,拟合晶体塑性模型和微观组织状态方程;金属在不同变形方向压缩的力学响应具体指金属分别沿轧向(rd)、横向(td)、厚度方向(nd)三个方向进行切取试样(使得试样满足基础实验要求),并进行单轴压缩实验,从而可以保证和变向锻造过程中材料在不同方向变形的真实力学响应保持一致。
[0028]
晶体塑性模型可以为平均场也可以为全场形式的晶体塑性模型。
[0029]
晶体塑性模型的表达形式有多种,本发明以其中一种为例进行介绍:其中,f表示变形梯度,fe为弹性应变梯度,f
p
为塑性应变梯度,l
p
为速度梯度,为塑性应变梯度随时间的变化率,和分别为滑移系和孪晶系的塑性应变率,和分别为滑移系和孪晶系的schmid因子,为孪晶分数随时间的变化率,ns和n
tw
分别为金属中滑移系a和孪晶系β的总数;其中,q、kb和t分别为热激活能、玻尔兹曼常数和温度,为滑移系剪切应力,分别为滑移系的热无关和热相关应力,
其中,为初始滑移阻力,c1为材料常数,g为剪切模量,b为伯式矢量,为位错密度,其中,为孪晶剪切应变,为孪晶体积分数,为孪晶体积,n
tw
为孪晶系数量,为初始孪晶形核率,为第一孪晶临界应力拟合材料常数,为第二孪晶临界应力拟合材料常数,r为拟合指数,其中,表示滑移系或孪晶系的剪切应力,te为piola-kirchhoff应力张量,与材料弹性应变存储能有关,表示滑移系或孪晶系的schmid因子,待拟合的模型参数;滑移系和孪晶系的schmid因子反映了多晶体中滑移系和孪晶的激活程度,会改变晶体取向的欧拉角。
[0030]
拟合前设置初始模型参数以及模型参数的范围,拟合时,以晶体塑性模型的应力预测值与力学响应的应力之间的残差最小且晶体塑性模型的滑移系和孪晶系的schmid因子对应的欧拉角与微观表征所得欧拉角之间的误差最小为目标,对晶体塑性模型的待拟合的模型参数迭代寻优,得到最优模型参数。
[0031]
微观组织状态方程:其中,x为再结晶分数,为再结晶分数随时间的变化率,为位错密度,为再结晶形核的临界位错密度,为塑性应变随时间的变化率(即晶体塑性模型计算的滑移系和孪晶系的塑性应变率的加权和,通过damask软件计算),分别为微观组织状态方程中再结晶模型待拟合的第一、第二、第三材料常数,上式表示了在再结晶之后,位错密度的更新值,为新的位错密度,kr、r分别为微观组织状态方程中更新位错密度模型待拟合的第一、第二材料常数。
[0032]ddrx
为再结晶晶粒尺寸,z为热激活参数,与变形温度、应变速率相关,a0和a1分别为微观组织状态方程中再结晶晶粒尺寸模型待拟合的第一、第二材料常数。
[0033]
其中,d为晶粒尺寸,d0为初始晶粒尺寸,通过微观表征得到。
[0034]
微观组织状态方程中待拟合的方程参数为:;z通过力学响应数据绘制的应力应变曲线确定,d通过微观表征得到,在已知输入输出的情况下通过最小二乘法拟合方程参数,或者,拟合前设置初始方程参数和方程参数范围,拟合时,以微观组织状态方程计算的再结晶分数与微观表征的再结晶分数之间误差最小且微观组织状态方程计算的晶粒尺寸微观表征的晶粒尺寸之间的误差最小为目标,对微观组织状态方程的待拟合的方程参数迭代寻优,得到最优方程参数。
[0035]
对金属进行有限元模拟,提取变向锻造工艺参数下锻造形成的金属心部有限单元上积分点的变形梯度,将变形梯度代入晶体塑性模型,计算金属各个晶粒的位错滑移、变形孪晶,得到应力应变分布和位错密度;在商用有限元软件(如abaqus)上进行变形锻造工艺的有限元数值模拟。金属的心部指中心位置,目的是金属在变向锻造过程中,应变分布不均匀,在中心位置处的应变与模拟设置的应变量是一致的。有限单元涉及到有限元法的基本原理,是其最小组成单元。有限元法的思路和原理是以结构力学中的位移法为基础,把复杂的结构或连续体看成有限个单元的组合,各单元在节点处彼此连续而组成整体,把连续体分成有限个单元和节点,称为离散化。积分点即为有限元单元上的节点。变形梯度是在有限元软件后处理中可以直接提取的状态变量。
[0036]
将应力应变分布和位错密度代入金属的微观组织状态方程,计算再结晶分数和晶粒尺寸,将位错密度减去用于再结晶的位错密度,得到新的位错密度,将新的位错密度带入晶体塑性模型,得到用于描述取向的欧拉角;取向的表达:输入量:为晶体学坐标系中确定定点转动位置的三个一组角参量(欧拉角),分别表示章动角,进动角,自转角,其中,为对称广义谐波函数,是对称广义谐波函数的系数,l为阶数,u为晶体坐标系中的水平方向,v为晶体坐标系中的垂直方向,m(l)和n(l)描述了晶体对称性和金属对称性的线性独立谐波数。
[0037]
将不同变形方向、不同变形参数作为训练数据,将不同变形方向、不同变形参数下锻造金属,形成的晶粒尺寸和取向作为训练数据的模拟输出,用于与神经网络模型的输出进行对比。
[0038]
模拟出的金属织构采用广义球谐(gsh)矢量对金属的取向分布函数进行逼近,来表示金属的取向特征,可以降低数据维度以提高训练效率。
[0039]
输入集和输出集均需进行归一化处理在-1到1之间。不同的锻造方向di分别取值
为-1,0和1。输入集变量:应变量、应变速率和变形温度t,输出集变量:金属晶粒尺寸d和取向特征t信息均采用如下函数进行归一化:式中,x为上述输入和输出集变量:应变量、应变速率、变形温度、晶粒尺寸和取向特征。
[0040]
搭建神经网络模型为多层前馈全连接神经网络模型(一个输入层,n个隐含层,一个输出层)或递归lstm神经网络。
[0041]
金属晶粒尺寸和取向特征协同调控的多目标函数的表达式为:式中,为归一化后的晶粒尺寸和取向特征,n为权重系数,取值范围为0.4~0.6。
[0042]
采用dqn强化学习算法对金属变向锻造过程的晶粒尺寸和取向特征进行智能协同调控。优化目标动作值为:,其中,为优化空间域,。其中距离函数,具体表示为:其中,f为t时刻的预测值,为目标,为预测值与目标之间的距离,f
t
为通过神经网络模型预测的t时刻的变向锻造工艺参数对应的金属晶粒尺寸和取向的预测值。
[0043]
采用的dqn强化学习算法设置的奖励函数r为:式中,t为当前时刻,为折扣因子,取值范围为[0,1]。该奖励函数可以得到一个更密集的学习奖励信息。
[0044]
通过强化学习更新动作值,并迭代入神经网络模型中进行循环更新,重复以上步骤直到学习出累积奖励r值最大的策略,输出得到理想金属晶粒尺寸和取向特征协同调控目标值的最优工艺参数。
[0045]
实施例1实施例1的材料为轧制态6082铝合金,该合金晶体结构为fcc。初始晶粒尺寸为40μ
m,目标优化晶粒在20μm以下,并弱化轧向《111》的纤维织构。本发明提供的金属变向锻造成形的晶粒尺寸和取向智能协同调控方法的具体步骤如下:步骤1、获取轧制态6082铝合金沿轧制方向,横向、厚度方向压缩的力学响应,应变速率设置为0.001s-1-0.1s-1
,压缩变形量为60%,变形温度范围为350-500℃。并对压缩后的试样进行ebsd(electron backscattered diffraction,电子背散射衍射)表征,获取晶粒尺寸和取向信息,同时利用压缩应力应变曲线和表征数据,对晶体塑性模型进行参数标定,从而可以实现沿不同变形方向不同变形参数下晶体取向的预测。
[0046]
步骤2、构建数据集,基于abaqus有限元平台,对6082铝合金进行不同变形参数交互作用下的金属变向锻造工艺数值模拟,变形参数及取值范围如下:锻造方向(di),可选为轧向(rd)、横向(td)、厚度方向(nd);应变量(),单道次的应变范围为:0-1;应变速率(),取值范围为0.001-0.1 s-1
,变形温度范围为350-500℃。不同锻造变形方向如图2中(a)、图2中(b)和图2中(c)所示,forging direction表示锻造方向,在模拟时主要进行多道次不同变形方向及路径耦合的影响,共计64组模拟。并提取模拟变形后合金心部代表单元的应变梯度。晶体塑性模型根据输入的变形梯度,计算金属各个晶粒的位错滑移、变形孪晶,得到应力应变分布和位错密度等状态变量。同时,将晶体塑性模型得到的状态变量传递给材料的微观组织状态方程用于计算动态再结晶分数、晶粒尺寸,并传回晶体塑性模型中对各个晶粒的状态变量进行更新,获取该变形条件下6082铝合金的晶粒尺寸d和取向特征信息t。建立以不同工艺参数为输入集,6082铝合金的晶粒尺寸和取向特征信息为输出集的对应关系。
[0047]
步骤3、利用步骤2中获取的数据集,搭建三层全连接神经网络模型,分别包含一个输入层,一个隐含层和一个输出层。训练前对数据集进行归一化处理至-1到1之间。隐含层间选择relu作为模型的激活函数,采用随机梯度下降法(adam)来寻找模型参数的最优解,训练得到隐含层节点数为10。并使用该模型预测任意变形条件下6082铝合金的晶粒尺寸d和取向特征信息t。
[0048]
达式为:。式中,为归一化后的晶粒尺寸和取向特征,n为权重系数,取值为0.5。采用基于dqn的强化学习算法,针对细化晶粒尺寸在20μm以下,并弱化轧向《111》的纤维织构为目标, 目标动作值为:,其中,为优化空间域,。其中距离函数,具体表示为:其中,f为t时刻的预测值,为目标,为预测值与目标之间的距离,f
t
为通过神经网络模型预测的t时刻的变向锻造工艺参数对应的6082铝合金晶粒尺寸和取向的预测值。
[0049]
奖励函数r为:
式中,t为当前时刻,折扣因子初始取值为0.96。通过在神经网络中进行迭代循环,自动学习出获取输出得到理想6082铝合金晶粒尺寸和取向特征协同调控目标值的最优工艺参数,并保存模型。
[0050]
步骤5、输出细化6082铝合金晶粒尺寸并弱化沿轧向织构的变向锻造完整工艺路径和参数设置,实现对6082铝合金晶粒尺寸和取向的智能精准调控。
[0051]
实施例2实施例2的材料为轧制ta15钛合金,该合金包含α相和β相。初始晶粒尺寸为30μm,目标优化晶粒在15μm以下,并提高其基面织构。本发明提供的金属变向锻造成形的晶粒尺寸和取向智能协同调控方法的具体步骤如下:步骤1、获取轧制态ta15钛合金沿轧制方向,横向、厚度方向压缩的力学响应,应变速率设置为0.001s-1-0.1s-1
,压缩变形量为60%,变形温度范围为800-950℃。并对压缩后的试样进行ebsd表征,获取两相晶粒尺寸和取向信息,同时利用压缩应力应变曲线和表征数据,对晶体塑性模型进行参数标定,从而可以实现沿不同变形方向不同变形参数下晶体取向的预测。
[0052]
步骤2、构建数据集,基于abaqus有限元平台,对ta15钛合金进行不同变形参数交互作用下的金属变向锻造工艺数值模拟,变形参数及取值范围如下:锻造方向(di),可选为轧向(rd)、横向(td)、厚度方向(nd);应变量(),单道次的应变范围为:0-1;应变速率(),取值范围为0.001-0.1 s-1
,变形温度范围为800-950℃。不同锻造变形方向如图2中(a)、图2中(b)和图2中(c)所示,在模拟时主要进行多道次不同变形方向及路径耦合的影响,共计64组模拟。并提取模拟变形后合金心部代表单元的应变梯度。晶体塑性模型根据输入的变形梯度,计算金属各个晶粒的位错滑移、变形孪晶,得到应力应变分布和位错密度等状态变量。同时,将晶体塑性模型得到的应力应变分布和状态参量传递给材料的微观组织状态方程用于计算动态再结晶分数、晶粒尺寸以及再结晶,并传回晶体塑性模型中对各个晶粒的状态变量进行更新,获取该变形条件下轧制态ta15钛合金的晶粒尺寸d和取向特征信息t。建立以不同工艺参数为输入集,轧制态ta15钛合金的晶粒尺寸和取向特征信息为输出集的对应关系。
[0053]
步骤3、利用步骤2中获取的数据集,搭建三层全连接神经网络模型,分别包含一个输入层,一个隐含层和一个输出层。训练前对数据集进行归一化处理至-1到1之间。隐含层间选择relu作为模型的激活函数,采用随机梯度下降法(adam)来寻找模型参数的最优解,训练得到隐含层节点数为10。并使用该模型预测任意变形条件下轧制态ta15钛合金的两相晶粒尺寸d和取向特征信息t。
[0054]
步骤4、设计轧制态ta15钛合金晶粒尺寸和取向特征协同调控的多目标函数,函数表达式为:。式中,为归一化后的晶粒尺寸和取向特
征,n为权重系数,取值为0.4。采用基于dqn的强化学习算法,针对细化晶粒尺寸在15μm以下,并提高其基面织构为目标, 目标动作值为:,其中, 为优化空间域,。其中距离函数,具体表示为:其中,f为t时刻的预测值,为目标,为预测值与目标之间的距离,f
t
为通过神经网络模型预测的t时刻的变向锻造工艺参数对应的ta15钛合金晶粒尺寸和取向的预测值。
[0055]
奖励函数r为:式中,t为当前时刻,折扣因子初始取值为0.92。通过在神经网络中进行迭代循环,自动学习出获取输出得到理想金属晶粒尺寸和取向特征协同调控目标值的最优工艺参数,并保存模型。
[0056]
步骤5、输出细化ta15钛合金两相晶粒尺寸并提高基面织构的变向锻造完整工艺路径和参数设置,实现对ta15钛合金晶粒尺寸和取向的智能精准调控。
[0057]
本领域的技术人员容易理解,以上所述仅为本发明的较佳实施例而已,并不用以限制本发明,凡在本发明的精神和原则之内所作的任何修改、等同替换和改进等,均应包含在本发明的保护范围之内。