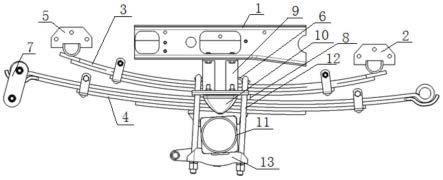
1.本发明属于汽车cae研究领域,具体涉及一种带限位块的钢板弹簧疲劳耐久分析方法,该方法可应用于带副簧的钢板弹簧、不带副簧的钢板弹簧的疲劳耐久分析以及带钢板弹簧的整车cae分析。
背景技术:2.相对于其它弹性元件,钢板弹簧不仅能够起着基本的弹性元件功能,还能起到导向元件的功能,同时,钢板弹簧的簧片件的接触和摩擦在弹簧振动时也能起到阻尼的作用,减小了振动的传递。基于上述有点,钢板弹簧被广泛用于商用车悬架上。
3.针对承载大的车辆,在垂向冲击工况及其它较为恶劣的工况,车辆钢板弹簧及限位块软垫都起到相当重要的作用。而当前的钢板弹簧疲劳耐久试验标准及仿真分析方法皆未考虑限位块对钢板弹簧疲劳寿命的影响,造成疲劳耐久仿真结果不精确,无法与实车进行准确对标。
技术实现要素:4.本发明的目的是针对现有技术存在的上述问题,提供一种能够有效提高仿真精度的带限位块的钢板弹簧疲劳耐久分析方法。
5.为实现以上目的,本发明的技术方案如下:一种带限位块的钢板弹簧疲劳耐久分析方法,依次包括以下步骤:步骤a、基于hyperworks,先建立钢板弹簧有限元模型,然后采用bush单元模拟钢板弹簧上的限位块软垫;步骤b、在钢板弹簧与上压板之间施加u型螺栓预紧力,并进行接触设置;步骤c、在满载比利时路路谱下对钢板弹簧的下表面施加随机位移,利用非线性瞬态分析计算得出op2文件;步骤d、基于得到的op2文件,对钢板弹簧进行变幅值疲劳分析,得到最大损伤点及对应的损伤值,从而确定钢板弹簧的疲劳寿命。
6.步骤a中,所述采用bush单元模拟钢板弹簧上的限位块软垫包括:先将钢板弹簧上的限位块支架与限位块软垫的连接处采用rbe2刚性单元连接,限位块软垫的下表面采用rbe2刚性单元连接,然后在上述两个连接的rbe2刚性单元中心点之间建立bush单元,其中,bush单元的长度由限位块软垫的长度确定,bush单元的刚度通过限位块软垫台架试验确定。
7.步骤a所述的钢板弹簧有限元模型中,对于厚度超过8mm且截面不等厚的零件,采用六面体单元模拟,其它零件则采用四边形壳单元模拟,其中,所述六面体单元模拟包括:先将零件的端面划分为规整的四边形壳单元,然后将划分的四边形壳单元用该零件几何的多条带特征的边界线拉伸出六面体单元。
8.步骤b中,所述在钢板弹簧与上压板之间施加u型螺栓预紧力的实现方式为:
先在钢板弹簧与上压板之间创建beam梁单元,beam梁单元的两端通过刚性单元连接在上压板与主簧中最下方的簧片所在位置,然后通过beam梁单元施加u型螺栓预紧力。
9.步骤b中,所述接触设置包括:分别在限位块软垫的下表面与后桥桥壳的上表面之间、相邻的簧片之间进行接触设置。
10.所述接触的类型为slide。
11.所述步骤b还包括创建边界条件,所述创建边界条件包括:在车架纵梁的断面处创建spc约束:1、2、3、4、5、6自由度;在后桥桥壳上表面周边创建spc约束:2、4、6自由度;在主簧的后端卷耳与摆臂的上端之间创建轴向转动副;在主簧前端的卷耳中心点处、摆臂下端中心点处创建spc约束:1、2、3、4、6自由度。
12.步骤c中,所述施加随机位移的位置为主簧下表面中央部位创建的rbe2刚性单元的中心点处。
13.步骤d中,所述变幅值疲劳分析采用ncode软件、time step载荷类型。
14.与现有技术相比,本发明的有益效果为:1、本发明一种带限位块的钢板弹簧疲劳耐久分析方法基于hyperworks,先建立钢板弹簧有限元模型,采用bush单元模拟钢板弹簧上的限位块软垫,然后在钢板弹簧与上压板之间施加u型螺栓预紧力,并进行接触设置,接着在满载比利时路路谱下对钢板弹簧的下表面施加随机位移,利用非线性瞬态分析计算得出op2文件,再对钢板弹簧进行变幅值疲劳分析,得到最大损伤点及对应的损伤值,从而确定钢板弹簧的疲劳寿命,该方法利用bush单元来模拟钢板弹簧的限位块软垫,并以此来进行钢板弹簧疲劳耐久分析,有效提高了疲劳耐久结果的仿真精度,有利于实现仿真结果与实车准确对标。因此,本发明有效提高了疲劳耐久仿真的精度。
15.2、本发明一种带限位块的钢板弹簧疲劳耐久分析方法在建立钢板弹簧有限元模型的过程中,对于厚度超过8mm且截面不等厚的零件采用六面体单元模拟,其它零件则采用四边形壳单元模拟,基于该方法可有效提高网格计算精度,进而提高建模的精确度。因此,本发明提高了建模的精确度。
附图说明
16.图1为实施例1采用的钢板弹簧的cad模型图。
17.图2为实施例1的bush单元模拟图。
18.图3为实施例1中u型螺栓预紧力的创建示意图。
19.图中,车架纵梁1、副簧前支架2、副簧3、主簧4、副簧后支架5、上压板6、摆臂7、垫板8、限位块支架9、限位块软垫10、后桥桥壳11、u型螺栓12、下压板13。
具体实施方式
20.下面结合附图以及具体实施方式对本发明作进一步详细的说明。
21.一种带限位块的钢板弹簧疲劳耐久分析方法,依次包括以下步骤:步骤a、基于hyperworks,先建立钢板弹簧有限元模型,然后采用bush单元模拟钢板弹簧上的限位块软垫;
步骤b、在钢板弹簧与上压板之间施加u型螺栓预紧力,并进行接触设置;步骤c、在满载比利时路路谱下对钢板弹簧的下表面施加随机位移,利用非线性瞬态分析计算得出op2文件;步骤d、基于得到的op2文件,对钢板弹簧进行变幅值疲劳分析,得到最大损伤点及对应的损伤值,从而确定钢板弹簧的疲劳寿命。
22.步骤a中,所述采用bush单元模拟钢板弹簧上的限位块软垫包括:先将钢板弹簧上的限位块支架与限位块软垫的连接处采用rbe2刚性单元连接,限位块软垫的下表面采用rbe2刚性单元连接,然后在上述两个连接的rbe2刚性单元中心点之间建立bush单元,其中,bush单元的长度由限位块软垫的长度确定,bush单元的刚度通过限位块软垫台架试验确定。
23.步骤a所述的钢板弹簧有限元模型中,对于厚度超过8mm且截面不等厚的零件,采用六面体单元模拟,其它零件则采用四边形壳单元模拟,其中,所述六面体单元模拟包括:先将零件的端面划分为规整的四边形壳单元,然后将划分的四边形壳单元用该零件几何的多条带特征的边界线拉伸出六面体单元。
24.步骤b中,所述在钢板弹簧与上压板之间施加u型螺栓预紧力的实现方式为:先在钢板弹簧与上压板之间创建beam梁单元,beam梁单元的两端通过刚性单元连接在上压板与主簧中最下方的簧片所在位置,然后通过beam梁单元施加u型螺栓预紧力。
25.步骤b中,所述接触设置包括:分别在限位块软垫的下表面与后桥桥壳的上表面之间、相邻的簧片之间进行接触设置。
26.所述接触的类型为slide。
27.所述步骤b还包括创建边界条件,所述创建边界条件包括:在车架纵梁的断面处创建spc约束:1、2、3、4、5、6自由度;在后桥桥壳上表面周边创建spc约束:2、4、6自由度;在主簧的后端卷耳与摆臂的上端之间创建轴向转动副;在主簧前端的卷耳中心点处、摆臂下端中心点处创建spc约束:1、2、3、4、6自由度。
28.步骤c中,所述施加随机位移的位置为主簧下表面中央部位创建的rbe2刚性单元的中心点处。
29.步骤d中,所述变幅值疲劳分析采用ncode软件、time step载荷类型。
30.实施例1:一种带限位块的钢板弹簧疲劳耐久分析方法,本实施例以整车坐标系下位于车架左侧的带副簧的后钢板弹簧为研究对象(其cad模型图参见图1),依次按照以下步骤进行:1、基于hyperworks,建立钢板弹簧有限元模型,其中,对于副簧3、主簧4、副簧后支架5、摆臂7,其厚度均超过8mm且截面不等厚,采用六面体单元模拟,其它零件则采用四边形壳单元模拟,且所述六面体单元模拟为:先在hypermesh-2d-automesh面板下,将副簧3和主簧4的端面划分为规整的5mm四边形壳单元,然后在hypermesh-3d-solidmap-line drag面板下,将划分的四边形壳单元用该零件几何的多条带特征的边界线拉伸出六面体单元,垫板7区域的副簧3和主簧4的簧片之间采用节点融合。
31.2、参见图2,先将限位块支架9与限位块软垫10的连接处采用rbe2刚性单元连接,
限位块软垫10的下表面采用rbe2刚性单元连接,然后在上述两个连接的rbe2刚性单元中心点之间建立bush单元,其中,bush单元的长度由限位块软垫的长度确定,bush单元的刚度通过限位块软垫台架试验确定。
32.3、参见图3,先在主簧4与上压板6之间需要施加预紧力的位置创建beam梁单元,beam梁单元的两端通过刚性单元连接在上压板6与主簧4中最下方的簧片所在位置,然后通过beam梁单元施加u型螺栓预紧力。
33.4、创建边界条件,包括:在车架纵梁1的断面处、副簧前支架2和副簧后支架5的安装孔处创建spc约束:1、2、3、4、5、6自由度;在后桥桥壳11的上表面周边创建spc约束:2、4、6自由度;在主簧4的后端卷耳与摆臂7的上端之间创建轴向转动副;在主簧4前端的卷耳中心点处、摆臂7下端中心点处创建spc约束:1、2、3、4、6自由度。
34.5、接触设置,包括:分别在限位块软垫10的下表面与后桥桥壳11的上表面之间、副簧3和主簧4的簧片之间、副簧3与前副簧支架2之间、副簧3与后副簧支架5之间设置接触,其中,所述接触的类型为slide。
35.6、在满载比利时路路谱下对钢板弹簧的下表面施加随机位移,利用非线性瞬态分析计算得出op2文件,其中,所述施加随机位移的位置为主簧4下表面中央部位创建的rbe2刚性单元的中心点处,所述非线性瞬态分析设置如下:工况设定分为两步连续工况:工况1、设定预紧力工况;工况2、在预紧力工况基础上添加满载比利时路路谱的强制位移。
36.工况1非线性瞬态分析(non-linear transient):勾选:spc约束;nlstat(lgdisp) 非线性大变形准静态;pretension预紧力;nlout。
37.工况2非线性瞬态分析(non-linear transient):勾选:spc约束;nlstat(lgdisp) 非线性大变形准静态;rload强制位移;statsub(pretens)预紧力工况;nlout;在subcase options中勾选cntnlsub连续工况。
38.本实施例计算得出的最大应力值位于副簧第二片板簧上,应力值为608.3mpa。
39.7、对钢板弹簧进行变幅值疲劳分析,得到最大损伤点位于副簧第二片板簧上,对应的损伤值为2.174e-6
,从而确定钢板弹簧的疲劳寿命为46万次,其中,所述变幅值疲劳分析采用ncode软件、time step载荷类型。