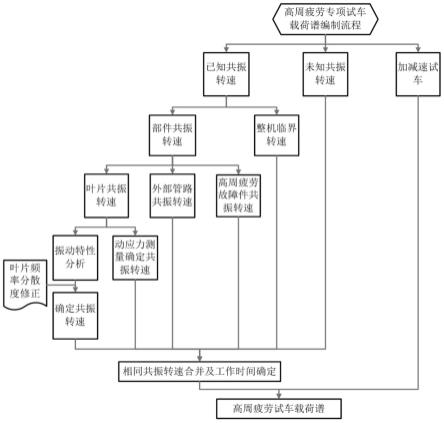
1.本技术属于航空发动机技术领域,特别涉及一种航空发动机整机高循环疲劳试车载荷谱设计方法。
背景技术:2.航空发动机寿命设计需要考虑多方面的影响因素,其中抗高循环疲劳设计是保证航空发动机安全可靠使用的关键技术之一。
3.目前几乎所有的航空发动机研制通用规范,对于高循环疲劳(107及以上)都提出了明确的要求,根据材料不同要求发动机零部件具备足够的高循环疲劳寿命,以验证相关零部件(转、静子叶片,外部管路等)在实际使用条件的结构可靠性。
4.在现有技术中,一般采用无限寿命设计结合材料级或零部件级的高循环疲劳试验的方式开展研制工作。例如,首先在零部件层级,主要是基于坎贝尔图、古德曼图等理论依据,设计零部件在发动机工作范围内不发生有害振动或振动具备足够的裕度。这种方式能够解决高循环疲劳设计的大部分问题,但是不能完全模拟发动机复杂的工作环境,存在设计验证不充分的风险。其次在整机层级,虽然以往在持久试车中采用台阶试车谱进行高循环疲劳验证,但上述台阶试车谱均采用大转速间隔、等时长的方式,导致这种无法达到充分、完整考核,不能在规定时间内达到预期的考核效果;此外,等时长的设计也可能在某些转速段存在过考核的问题,造成时间和资源的浪费。
技术实现要素:5.本技术的目的是提供了一种航空发动机整机高循环疲劳试车载荷谱设计方法,以解决或减轻背景技术中的至少一个问题。
6.本技术的技术方案是:一种航空发动机整机高循环疲劳试车载荷谱设计方法,所述设计方法包括:
7.根据航空发动机工作原理及各零部件结构特点,确定航空发动机整机高循环疲劳试车的考核对象,所述考核对象的试车载荷根据已知共振转速、未知共振转速和加减速次数对振动的影响确定;
8.确定发动机在工作转速范围内的考核转速及其对应的考核时间,包括:
9.根据零部件已知振动数据进行共振转速分析,结合振动特性分散性进行修正得到已知共振转速分析结果;
10.根据航空发动机工作转速区间范围及地面试车条件,确定高循环疲劳试车考核转速的上限和下限,同时根据航空发动机试车实际转速控制精度,确定转速子区间跨度,结合所述考核转速的上限、下限确定考核转速及其区间范围;
11.在考核转速的基础上,对已知共振转速、未知共振转速、整机临界转速进行数据整合,确定每个转速子区间的考核时间;
12.在完成试车载荷要求的基础上,结合加减速次数要求,完成高循环疲劳试车载荷
谱设计。
13.进一步的,所述考核对象包括转子叶片、静子叶片、外部管路、机匣薄壁件。
14.进一步的,所述已知共振转速包括零部件共振转速和整机振动临界转速。
15.进一步的,所述零部件已知共振转速根据零部件的振动特性分析及动应力测试结果确定。
16.进一步的,所述整机振动临界转速依据被试发动机实际的动力特性情况确定。
17.进一步的,每个转速子区间的考核时间为共振转速、未知共振转速、整机临界转速中停留时间的最大值。
18.本技术的方法通过采用整机环境进行考核,且针对不同的零部件、不同的振动特性分别制定载荷要求,保证高循环疲劳考核的有效性、完整性和充分性,为整机高循环疲劳试车载荷谱设计建立了科学、系统、有效的方法和操作流程,提高工作效率,保证飞行安全。
附图说明
19.为了更清楚地说明本技术提供的技术方案,下面将对附图作简单地介绍。显而易见地,下面描述的附图仅仅是本技术的一些实施例。
20.图1为本技术的整高周疲劳试车载荷谱设置方法流程图。
具体实施方式
21.为使本技术实施的目的、技术方案和优点更加清楚,下面将结合本技术实施例中的附图,对本技术实施例中的技术方案进行更加详细的描述。
22.为了克服现有技术中所提出的问题,本技术中通过梳理航空发动机高循环疲劳设计关注点,明确试车载荷确定原则及方法,建立整机高循环疲劳试车载荷谱编制流程,从而形成了整机高循环疲劳试车载荷谱设计方法,通过整机高循环疲劳试车,达到完整、充分考核航空发动机零部件抗高循环疲劳能力的目的。
23.如图1所示,本技术的航空发动机整机高循环疲劳试车载荷谱设计方法包括如下步骤:
24.1、高循环疲劳载荷确定原则
25.高循环疲劳载荷确定应全面考虑航空发动机零部件的主要破坏模式,根据航空发动机工作原理及各零部件结构特点,确定航空发动机整机高循环疲劳试车的考核对象,包括但不限于转子叶片、静子叶片、外部管路、机匣薄壁件等。
26.对于这些零部件,试车载荷确定主要考虑已知共振转速、未知共振转速和加减速三部分因素。
27.a)确定已知共振转速
28.已知共振转速中又包括零部件共振转速和整机振动临界转速两部分。
29.零部件的已知共振转速主要根据零部件的振动特性分析、动应力测试结果等进行确定。
30.对于各级转子叶片,由于实际装机叶片存在频率分散度,为达到充分验证的目的,根据各级叶片的频率实测结果对试车转速进行修正,对分散度较大的叶片,频率密集度较高的各分散带均作为共振转速进行验证。
31.例如,对于钛合金零件,由于其超过107次循环后的疲劳寿命仍然会继续下降,寿命要求应为109次循环。但根据jssg-2007要求,“对于钛,应该用材料性能试验,而不是用发动机试验”,因此高循环疲劳试车共振转速的停留时间仍以107或108次循环为主确定。
32.整机振动临界转速主要参照转子动力学分析结果,根据被试发动机实际的动力特性情况确定。由于临界转速为发动机非常用转速,因此停留时间按1
×
106次循环确定。
33.b)确定未知共振转速
34.除上述部件和整机的已知共振转速外,高循环疲劳试车载荷谱还需考虑其他部件及未知共振转速的影响。停留时间参考jssg-2007和国外高周疲劳试车的相关资料,按1
×
106次循环确定,激振因素为转速的3倍频。
35.c)确定加减速试车次数
36.发动机加减速过程中气流的变化会影响主要零部件的振动,因此,本技术在hcf(high cycle fatigue,即高周期疲劳)试车载荷谱编制中添加了发动机加减速对振动的影响。
37.2、确定高循环疲劳试车载荷谱
38.整机高循环疲劳试车载荷谱的目标是在发动机工作转速范围内,确定考核转速及其对应的考核时间,确定载荷谱的具体过程包括:
39.(1)共振转速分析:考虑零部件振动特性、试验测量结果等已知数据进行共振转速分析,同时,视情考虑振动特性分散性进行修正后,得到已知共振转速分析结果。
40.如表1即为本技术一实施例中的已知共振转速分析结果统计表。
41.表1已知共振转速分析结果
[0042][0043]
(2)确定考核转速:综合考虑航空发动机工作转速区间范围、地面试车条件,确定高循环疲劳试车考核转速上、下限;考虑发动机试车实际转速控制精度,确定转速子区间跨度,结合上、下限转速确定考核转速及其区间范围。
[0044]
(3)确定考核时间:在考核转速的基础上,对已知共振转速、未知共振转速、整机临界转速等要求进行数据整合分析,采用最大化原则,确定每个转速子区间的考核时间。
[0045]
如表2所示即为本技术一实施例中的每个转速子区间的考核时间表,从表中可以看到,对于低压相对转速45%这个工况,停留时间最长的为“转子叶片(-1%)振动特性分析”,因此对于该转速子区间的考核时间选取其对应的405min;同样的,对于低压相对转速
46%这个工况,停留时间最长的为“未知共振转速”,因此对于该转速子区间的考核时间选取其对应的83min。其他情况不再赘述。
[0046]
表2转速考核时间表
[0047][0048]
(4)试车载荷谱设计:在上述载荷要求的基础上,充分考虑加减速次数要求,完成高循环疲劳试车载荷谱设计。
[0049]
根据航空发动机零部件高循环疲劳试车载荷确定原则,建立高循环疲劳试车载荷谱,根据相关理论计算和试验数据分析结果,即可在地面台架试车时,实现对航空发动机主要零部件抗高循环疲劳能力的考核。
[0050]
本技术的方法通过采用整机环境进行考核,且针对不同的零部件、不同的振动特性分别制定载荷要求,保证高循环疲劳考核的有效性、完整性和充分性,为整机高循环疲劳试车载荷谱设计建立了科学、系统、有效的方法和操作流程,提高工作效率,保证飞行安全。
[0051]
以上所述,仅为本技术的具体实施方式,但本技术的保护范围并不局限于此,任何熟悉本技术领域的技术人员在本技术揭露的技术范围内,可轻易想到的变化或替换,都应涵盖在本技术的保护范围之内。因此,本技术的保护范围应以所述权利要求的保护范围为准。