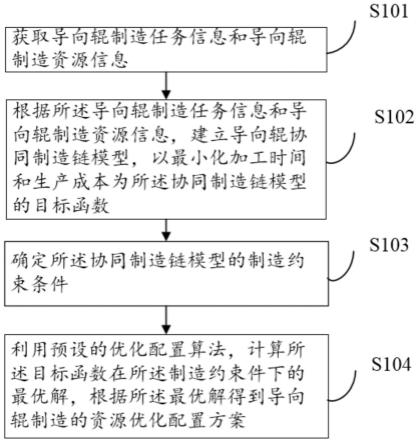
1.本发明涉及印刷机械零件制造技术领域,具体涉及一种导向辊制 造资源优化配置方法、装置、电子设备和计算机可读存储介质。
背景技术:2.印刷业作为我国实体经济的重要组成部分,推进其智能化进程, 对加快建设印刷强国、引领产业高质量发展具有重要意义。印刷机械 结构复杂,制造精密,安装难度大,导向辊作为印刷机械的关键零部 件之一,加工质量要求极高,为保证导向辊加工的效率和质量稳定性, 同时兼顾加工的经济性,需要将导向辊制造资源整合到产品周期中进 行组织和管理,对制造资源进行合理的优化配置。
3.导向辊的制造资源优化配置类似于混合流水车间调度问题,对于 这种np(non-deterministic polynomial,非确定多项式)问题,目前 多采用启发式算法和元启发式算法进行求解,如改进ils算法,通过 引入禁忌表的方式来平衡全局搜索和局部搜索,同时优化了车间能耗、 完工时间和机器负荷三个目标;再如有学者提出了ig算法,通过执 行多次插入操作,将工件分配各工厂最佳位置。但现有的研究多集中 于特定背景下的理论与应用,现有技术所构建的模型和算法并不适用 于导向辊实际制造车间,无法有效优化导向辊的制造和生产。
4.因此,有必要针对印刷机械导向辊制造车间的真实情况,建立更 贴合实际的导向辊协同制造链模型,并采用智能寻优算法寻找到模型 的最优解,从而实现导向辊生产效率与生产成本的协同优化。
技术实现要素:5.有鉴于此,有必要提供一种导向辊制造资源优化配置方法、装置、 设备及介质,用以解决现有印刷机械导向辊制造资源优化方法不能契 合实际导向辊制造车间的真实情况,无法对导向辊的制造和生产进行 有效优化的问题。
6.为了解决上述问题,本发明提供一种导向辊制造资源优化配置方 法,包括:
7.获取导向辊制造任务信息和导向辊制造资源信息;
8.根据所述导向辊制造任务信息和导向辊制造资源信息,建立导向 辊协同制造链模型,以最小化加工时间和生产成本为所述协同制造链 模型的目标函数;
9.确定所述协同制造链模型的制造约束条件;
10.利用预设的优化配置算法,计算所述目标函数在所述制造约束件 下的最优解,根据所述最优解得到导向辊制造的资源优化配置方案。
11.进一步的,所述导向辊制造任务信息包括具有时序性的工序级协 同制造子任务集合;所述导向辊制造资源信息包括导向辊生产车间的 制造资源集合。
12.进一步的,所述协同制造链模型的目标函数中,所述最小化加工 时间包括最小化工件加工的最大完成时间;所述最小化生产成本包括 最小化工件加工的总成本;
13.其中,所述工件加工的最大完成时间为时序上排在最后的制造子 任务的加工结束时间;所述工件加工的总成本包括制造资源加工成本 和制造过程中工件储运成本。
14.进一步的,所述制造约束条件包括:导向辊加工工艺约束、制造 加工时间约束和制造资源状态约束。
15.进一步的,利用预设的优化配置算法,计算所述目标函数在所述 制造约束件下的最优解,包括:
16.生成所述集成调度模型在所述约束条件下的初始解集;
17.计算所述初始解集的适应度,根据所述适应度确定最优个体和最 差个体;
18.根据所述最优个体、最差个体和预设的迭代规则,对所述初始解 集进行更新,得到候选解集;
19.利用预设的局部搜索方法确定所述候选解集的最优个体,当满足 预设的终止条件时,将所述最优个体作为所述目标函数在所述制造约 束件下的最优解。
20.进一步的,计算所述初始解集的适应度,根据所述适应度确定最 优个体和最差个体,包括:
21.计算所述初始解集的非支配等级和拥挤度;
22.所述非支配度等级越高则个体越优;当个体拥有相同的非支配度 等级时,拥挤度高则个体更优。
23.进一步的,所述预设的迭代规则为:对种群中的个体进行交换变 换和移位变换,得到变换个体;
24.根据所述最优个体、最差个体和预设的迭代规则,对所述初始解 集进行更新,得到候选解集,包括:
25.根据所述最优个体、最差个体和jaya算法迭代公式,对所述变 换个体进行更新,得到更新个体;
26.根据所述更新个体的适应度判断所述更新个体是否优于更新前 的变换个体;若是,则将所述更新个体作为保留个体;若否,则将所 述变换个体作为保留个体;
27.根据所述保留个体得到候选解集。
28.本发明还提供一种导向辊制造资源优化配置装置,包括:
29.信息获取模块,用于获取导向辊制造任务信息和导向辊制造资源 信息;
30.目标建立模块,用于根据所述导向辊制造任务信息和导向辊制造 资源信息,建立导向辊协同制造链模型,以最小化加工时间和生产成 本为所述协同制造链模型的目标函数;
31.约束条件确定模块,用于确定所述协同制造链模型的制造约束条 件;
32.配置方案输出模块,用于利用预设的优化配置算法,计算所述目 标函数在所述制造约束件下的最优解,根据所述最优解得到导向辊制 造的资源优化配置方案。
33.本发明还提供一种电子设备,包括处理器以及存储器,所述存储 器上存储有计算机程序,所述计算机程序被所述处理器执行时,实现 上述技术方案中任一所述的一种导向辊制造资源优化配置方法。
34.本发明还提供一种计算机可读存储介质,所述计算机可读存储介 质存储有计算机指令,所述指令被处理器执行上述技术方案中任一技 术方案所述的一种导向辊制造资
源优化配置方法。
35.现有技术相比,本发明的有益效果包括:首先,获取导向辊制造 任务信息和导向辊制造资源信息;其次,根据所述导向辊制造任务信 息和导向辊制造资源信息,建立导向辊协同制造链模型,并确定模型 的目标函数和制造约束条件;最后,利用预设的优化配置算法,计算 所述目标函数在所述制造约束件下的最优解,根据所述最优解得到导 向辊制造的资源优化配置方案。本发明面向印刷机械导向辊加工过程, 对导向辊生产车间的协同制造资源配置问题进行研究,建立了更契合 实际生产情况的导向辊协同制造链模型,将导向辊生产车间制造资源 配置问题归结为多目标优化问题,并设计了一种优化配置算法对模型 问题进行求解,能够快速对协同制造链模型进行求解,提高了配置策 略的制定速度,使配置方案的制定更加高效。
附图说明
36.图1为本发明提供的一种导向辊制造资源优化配置方法一实施 例的流程示意图;
37.图2为本发明提供的导向辊协同制造链模型一实施例的示意图;
38.图3为本发明提供的个体拥挤度一实施例的示意图;
39.图4为本发明提供的交换变换一实施例的变换示意图;
40.图5为本发明提供的移位变换一实施例的变换示意图;
41.图6为本发明提供的插入操作一实施例的变换示意图;
42.图7本发明提供的对称变换操作一实施例的变换示意图;
43.图8本发明提供的混合jaya算法一实施例的流程示意图;
44.图9本发明提供的导向辊生产线布局一实施例的结构示意图;
45.图10(a)本发明提供的导向辊制造资源按传统模式配置一实施 例的加工完成时间甘特图;
46.图10(b)本发明提供的导向辊制造资源按ga算法配置一实施 例的加工完成时间甘特图;
47.图10(c)本发明提供的导向辊制造资源按混合jaya算法配置一 实施例的加工完成时间甘特图;
48.图11为本发明提供的一种导向辊制造资源优化配置装置一实施 例的结构示意图;
49.图12为本发明提供的电子设备一实施例的结构示意图。
具体实施方式
50.下面结合附图来具体描述本发明的优选实施例,其中,附图构成 本技术一部分,并与本发明的实施例一起用于阐释本发明的原理,并 非用于限定本发明的范围。
51.在实施例描述之前,首先对目前印刷机械导向辊的生产车间实际 情况进行介绍。
52.成品导向辊需要依次通过下料、粗车、半精车、热装、精车、氧 化、动平衡等工艺,其中,粗车包含车钢轴、车成铝堵以及车辊筒。 对于导向辊的协同制造,需要同时考虑待加工导向辊的制造顺序以及 各加工子任务间加工设备的分配情况。
53.本发明根据实际的导向辊生产车间资源和任务情况,以加工时间 最小化和生产
成本最低化为目标,构建导向辊制造资源与制造任务的 协同制造链模型,将导向辊制造资源配置归结为多目标优化问题,并 且设计了一种优化配置算法,在实际生产的约束条件下对模型进行求 解,得到导向辊生产车间制造资源的最优配置,达到生产效率与生产 成本的协同优化。
54.本发明实施例提供了一种导向辊制造资源优化配置方法,图1为 本发明提供的一种导向辊制造资源优化配置方法一实施例的流程示 意图,包括:
55.步骤s101:获取导向辊制造任务信息和导向辊制造资源信息;
56.步骤s102:根据所述导向辊制造任务信息和导向辊制造资源信 息,建立导向辊协同制造链模型,以最小化加工时间和生产成本为所 述协同制造链模型的目标函数;
57.步骤s103:确定所述协同制造链模型的制造约束条件;
58.步骤s104:利用预设的优化配置算法,计算所述目标函数在所 述制造约束件下的最优解,根据所述最优解得到导向辊制造的资源优 化配置方案。
59.本实施例提供的一种导向辊制造资源优化配置方法,首先,获取 导向辊制造任务信息和导向辊制造资源信息;其次,根据所述导向辊 制造任务信息和导向辊制造资源信息,建立导向辊协同制造链模型, 并确定模型的目标函数和制造约束条件;最后,利用预设的优化配置 算法,计算所述目标函数在所述制造约束件下的最优解,根据所述最 优解得到导向辊制造的资源优化配置方案。本实施例面向印刷机械导 向辊加工过程,对导向辊生产车间的协同制造资源配置问题进行研究, 建立了更契合实际生产情况的导向辊协同制造链模型,将导向辊生产 车间制造资源配置问题归结为多目标优化问题,并设计了一种优化配 置算法对模型问题进行求解,能够快速对协同制造链模型进行求解, 提高了配置策略的制定速度,使配置方案的制定更加高效。
60.作为优选的实施例,在步骤s101中,所述导向辊制造任务信息 包括具有时序性的工序级协同制造子任务集合;所述导向辊制造资源 信息包括导向辊生产车间的制造资源集合。
61.作为一个具体的实施例,将导向辊制造任务分解为具有时序性的 工序级协同制造子任务,所有制造子任务的集合可表示为: ms={ms1,ms2,
…
,msi,
…
,msn},式中msi为第i个协同制造 子任务,n为制造子任务的总数。
62.所述导向辊制造资源包括单刀架车削中心、双端面数控车床、动 平衡机等设备,将导向辊生产车间的所有制造资源集合为协同制造资 源集:mr={mr1,mr2,
…
,mrj,
…
,mrk},式中mrj为第j个协 同制造资源,k为制造资源的总数。
63.根据所述导向辊制造任务信息和导向辊制造资源信息,建立导向 辊协同制造链模型如图2所示。
64.作为优选的实施例,在步骤s102中,所述协同制造链模型的目 标函数中,所述最小化加工时间包括最小化工件加工的最大完成时间; 所述最小化生产成本包括最小化工件加工的总成本;
65.其中,所述工件加工的最大完成时间为时序上排在最后的制造子 任务的加工结束时间;所述工件加工的总成本包括制造资源加工成本 和制造过程中工件储运成本。
66.作为一个具体的实施例,以所有导向辊加工时间和生产成本最小 为目标,建立导向辊协同制造链模型的目标函数可用数学式表达为:
67.f={min t
max
,min c
ost
}
ꢀꢀ
(1)
68.t
max
=ft
nj
ꢀꢀ
(2)
[0069][0070]
式(1)表示最小化最大完工时间和最小化加工成本,其中,t
max
表示工件加工最大完成时间,c
ost
表示工件加工总成本;
[0071]
式(2)表示工件加工最大完成时间为最后制造子任务的加工结 束时间;其中,ft
ij
表示第i个协同制造子任务在制造资源j上加工 结束时间,n表示协同制造子任务总数;
[0072]
式(3)表示导向辊工件加工总成本为装置加工成本与储运成本 之和,其中,制造资源加工成本为加工时间与单位时间制造资源加工 成本之积,储运成本为工件储运时间与单位时间储运成本之积;cm表示制造资源加工成本,cr表示制造过程中工件储运成本;y
ij
表示第 i个制造子任务在第j个制造资源上加工时为1,否则为0;t
ij
表示第 i个协同制造任务在制造资源j上的加工时间;f
ij
表示第i个协同制 造任务在制造资源j上的加工单位时间加工成本;l
ij
表示第i个协同 制造任务在制造资源j上的工件储运时间(包含工件运输及等待时间 等);l
ij
表第i个协同制造任务在制造资源j上的工件单位时间储运 成本。
[0073]
作为优选的实施例,在步骤s103中,所述制造约束条件包括: 导向辊加工工艺约束、制造加工时间约束和制造资源状态约束。
[0074]
作为一个具体的实施例,所述约束条件用数学式表达如下:
[0075]
1、所述导向辊加工工艺约束包括:
[0076][0077]
式(4)表示所有待加工导向辊需要经过所有制造任务,且每个 制造任务只能在一个制造资源上加工;其中,y
ij
∈{0,1},y
ij
表示第i个 制造子任务在第j个制造资源上加工时为1,否则为0;n表示协同制 造子任务总数;k表示制造资源总数。
[0078]
2、所述制造加工时间约束包括:
[0079][0080]
式(5)表示导向辊的加工开始时间与结束时间的关系,即工件 加工的连续性;
[0081][0082]
式(6)表示导向辊准备时间为加工完成时间与制造资源加工时 间之差;t
ij
表示第i个协同制造任务在制造资源j上的加工时间;ti表示第i个协同制造子任务的加工完成时间;
[0083][0084]
式(7)表示任一待加工的导向辊在零时刻释放等待加工;f
ij
表 示第i个协同制造
任务在制造资源j上的加工单位时间加工成本。
[0085]
3、所述制造约束条件包括:
[0086][0087]
式(8)表示制造子任务的链式约束,即导向辊某子任务完成时 才能开始下一子任务的加工。
[0088]
作为优选的实施例,在步骤s104中,利用预设的优化配置算法, 计算所述目标函数在所述制造约束件下的最优解,包括:
[0089]
生成所述集成调度模型在所述约束条件下的初始解集;
[0090]
计算所述初始解集的适应度,根据所述适应度确定最优个体和最 差个体;
[0091]
根据所述最优个体、最差个体和预设的迭代规则,对所述初始解 集进行更新,得到候选解集;
[0092]
利用预设的局部搜索方法确定所述候选解集的最优个体,当满足 预设的终止条件时,将所述最优个体作为所述目标函数在所述制造约 束件下的最优解。
[0093]
作为优选的实施例,计算所述初始解集的适应度,根据所述适应 度确定最优个体和最差个体,包括:
[0094]
计算所述初始解集的非支配等级和拥挤度;
[0095]
所述非支配度等级越高则个体越优;当个体拥有相同的非支配度 等级时,拥挤度高则个体更优。
[0096]
作为优选的实施例,所述预设的迭代规则为:对种群中的个体进 行交换变换和移位变换,得到变换个体;
[0097]
根据所述最优个体、最差个体和预设的迭代规则,对所述初始解 集进行更新,得到候选解集,包括:
[0098]
根据所述最优个体、最差个体和jaya算法迭代公式,对所述变 换个体进行更新,得到更新个体;
[0099]
根据所述更新个体的适应度判断所述更新个体是否优于更新前 的变换个体;若是,则将所述更新个体作为保留个体;若否,则将所 述变换个体作为保留个体;
[0100]
根据所述保留个体得到候选解集。
[0101]
下面结合具体的实施例对上述的优化配置算法进行详细说明。
[0102]
本实施例采用基于操作的整数编码方式,具体规则为编码长度只 与待加工工件总数z和协同制造子任务数n相关,编码长度就是z*n, 编码内容是1,2,3,4,5
…
z*n之间的整数值。
[0103]
以待加工工件总数z=4,协同制造子任务数n=3为例,可得编码 和操作o
ji
之间的对应关系如表1所示。
[0104]
表1编码基础对应表
[0105][0106]
解码过程中,要同时考虑待加工导向辊的制造顺序以及各子任务 间加工装置分配情况。本实施例中,在某一子任务先加工完成的导向 辊,在下一制造子任务优先进行加工;在给定子任务最先空闲的装置 优先安排加工;而对于多个导向辊在某一子任务同时完成时,采用随 机原则(random rule,rr)进行求解。
[0107]
针对制造资源等待时间过长问题,本实施例提出一种基于空闲时 间升序的插入机制:如果某个导向辊的加工时长小于某制造装置的空 闲时间,则将该导向辊优先加工,直接插入该装置的空闲时间内完成 加工。
[0108]
在种群初始化时,为保证全局多样性,且导向辊生产车间制造资 源优化配置问题只需考虑加工排序与资源分配,故编码方案根据编码 长度使用完全随机生成策略。
[0109]
为了有效均衡加工效率和加工成本之间的特征,本技术中,个体 适应度评价策略为:利用帕累托寻优进行非支配等级排序及个体拥挤 度结合的机制进行个体选择。具体规则为,
[0110]
min f(x1)=min{f1(x1),f2(x1),
…fn
(x1)},x1∈m,
[0111]
其中fn(x1)表示以最小化为目标的第n个目标函数,x1表示目标 函数的一个解,m表示解集空间。如果存在另外一个解x2∈m,对 于均满足fi(x1)≤fi(x2),且满足 fi(x1)《fi(x2),则有x
1 f x2,即x1支配x2,解x1具有更高的等级。
[0112]
等级越高的解会被认为是更加优秀的解;如果两个解拥有相同的 等级,具有较高拥挤距离的解会被视为优于其他解。
[0113]
其中,拥挤度ds的计算公式如下式所示:
[0114][0115]
式(9)中,n为目标函数的个数,f
imax
与f
imin
分别为种群中第i个目 标函数值的最大值与最小值,fi(s+1)和fi(s-1)分别为待求解相邻两个 位置第i个目标函数值。
[0116]
图3为某一边界集中的个体s的拥挤度示意图。对于边界解(第0 和第r个个体),设定边界距离为无穷大。
[0117]
本实施例预设了迭代规则,对初始解集进行更新,具体为:对种 群个体xk实施两种变换因子,变换后的新个体与原个体构成迭代候选 集isetk,通过轮盘赌的选择策略,从候选集中获取x'k参与jaya迭代, 用于产生候选解x'k的两种变换包括交换变换和移位变换。
[0118]
交换变换具体为:在一个加工序列中随机选取两个序列点,交换 它们的位置,得到新的加工序列,如图4所示。
[0119]
移位变换具体为:在一个加工序列中随机选取两个序列点,将第 一个序列点依次与其后一个序列点交换位置,直至与随机选取的第二 个序列点交换完位置,得到新的序
列,如图5所示。
[0120]
在jaya迭代过程中,最优解为非支配等级最高的解,若存在解 的非支配等级相同,则最优解为拥挤度距离大的解,最劣解的选择与 之相反。jaya算法迭代公式为:
[0121]
a(i+1,j,k)=a(i,j,k)+r(i,j,1)(a(i,j,b)-|a(i,j,k)|)
ꢀ‑
r(i,j,2)(a(i,j,b)-|a(i,j,w)|)
ꢀꢀ
(10)
[0122]
其中,i,j,k分别代表迭代代数,个体的变量,种群中的个体。 例如,a(i,j,k)表示迭代第轮时,种群中第k个个体的第j个变量; a(i,j,b)和a(i,j,w)分别代表i代时种群中的最优个体和最差个体的第j 个变量;r(i,j,1)和r(i,j,2)分别控制缩放大小,取值在[0,1]之间。通过 公式(10)对个体进行更新,得到更新后的个体。
[0123]
为进一步提高算法的搜索性能,本实施例采用变邻域搜索 (variable neighborhood search,vns)对后期优秀个体进行局部优化, 从而提高混合算法的收敛速度以及增大其跳出局部最优的概率。
[0124]
而对于局部搜索策略的邻域结构,选择插入操作和对称变换操作, 在搜索过程中,两种混合结构各有50%的概率被选择参与迭代。
[0125]
插入操作具体规则为:随机选取一个元素插入到序列最开始的位 置,其他子批依次后退,如图6所示。
[0126]
对称变换操作具体规则为:在一个序列中随机产生两个位置连续 的序列对,先将每个序列中序列点反转,然后将序列对交换位置,得 到新的序列,如图7所示。
[0127]
上述过程的完整流程图如图8所示,具体步骤包括:
[0128]
步骤1:初始化种群,并设置最大迭代次数为终止条件。
[0129]
步骤2:寻找x
best
和x
worst
;计算所有个体非支配等级和拥挤度, 确定相对最优解与最差解。
[0130]
步骤3:实施变换因子;对每个个体xk进行交换、移位变换,和 原个体构成候选迭代集isetk。
[0131]
步骤4:选择迭代候选解x'k;对迭代候选集中的解决方案进行轮 盘赌选择,确定参与迭代的候选解x’k
。
[0132]
步骤5:更新种群;根据迭代公式对所有候选解进行更新。
[0133]
步骤6:判断是否替换;计算新解的适应度,若优于旧解,则将 旧解替换,否则保留旧解进入下一次迭代。
[0134]
步骤7:执行局部搜索;开始对种群中前15%的个体进行变邻域 搜索。
[0135]
步骤8:选择最优解;根据适应度评价规则,更新最优个体。
[0136]
步骤9:判断是否达到终止条件;若是跳转到步骤9,否则跳回 步骤3并遵循后续循环。
[0137]
步骤10:输出结果并结束。
[0138]
为了将比较本技术的优化配置方法与常用的优化算法进行分析 对比,本实施例选用常见的遗传算法与本技术的优化配置算法(后面 简称混合jaya算法)进行仿真对比分析,说明本技术算法的实用性 与优越性。
[0139]
以某印刷机械导向辊生产车间的实际订单为例,进行面向导向辊 协同制造资源优化配置问题研究,并与当前加工模式及其他资源优化 配置算法进行对比,导向辊生产线
布局如图9所示。
[0140]
以某时间段12个导向辊加工任务为实例,对导向辊制造过程中 的粗车、半精车、热装、精车、氧化、动平衡六大工序构成的协同制 造链进行优化,12个待加工导向辊毛坯需要依次完成以上6个制造 子任务,其中粗车、半精车、热装、精车、氧化、动平衡的制造资源 数分别为:1、2、2、3、1、2,各工件的制造子任务(msi)在不同 的制造资源(mri)上的加工时间与单位时间加工成本如表3所示, 储运成本为每小时30元。
[0141]
表2各工件制造任务不同制造资源加工时间表(单位:min)
[0142][0143]
表3单位时间各制造资源mri加工成本(单位:元/min)
[0144]
mr1mr2mr3mr4mr5mr62 3 2.5 1.5 1.5 5 mr7mr8mr9mr
10
mr
11
ꢀꢀ
4.5 4 1 2 2.5
ꢀꢀꢀ
[0145]
通过完全试验设计法,取混合jaya算法性能最优的参数组合: popsize为100,gmax为400。同时根据表2、表3所示的导向辊加工 数据,分别使用混合jaya算法,遗传算法(ga)进行模型求解,并 与传统生产方式进行比较,所得结果如图10(a)、图10(b)、图 10(c)及表4所示。图10(a)、(b)、(c)中,图示条形框[z msi] 表示导线辊第z个待加工毛坯的第i个制造子任务在对应纵坐标制造 资源上进行加工,
[0146]
由图10(a)、图10(b)、图10(c)可看出,传统的加工模式 会导致制造资源的空闲等待时间过长,对比条形框长度,可发现存在 并行制造资源时,传统模式不能选择更优的资源路线,而采用混合jaya算法结果的加工模式,可很好的选择制造资源,且总完工时间缩 短,提高了车间的生产效率。
[0147]
通过表4比较三种加工方案的制造周期与检定成本:基于本技术 所提混合jaya算法结果的加工模式,加工完成全部12个导向辊,约 需33小时,总加工成本约21000元,相较于按遗传算法结果的加工 模式所需2176min,总加工成本22836元,可节约9%的加工时间和 7%的加工成本。而在完成相同工作量下,采用传统加工模式,用时 约35小时,总加工成本约23000元,采用本发明所提算法结果模式 加工,可节约4.6%的加工时间,而加工成本可大幅节约7.9%。
[0148]
表4导线辊按不同模式加工结果对比
[0149]
加工方式 装置加工成本 储运成本 总完工时间 总加工成本 传统模式 13915 9101 2087 23016 遗传算法 13084 9752 2176 22836 混合jaya算法 12600 8755 1995 21335 [0150]
可见采用本技术所提混合jaya算法的导向辊协同制造资源优化 配置方案,达到了制造效率与制造成本的协同优化,且和其他智能算 法相比,混合java算法在解决此类问题上更具优势。
[0151]
本发明还提供一种导向辊制造资源优化配置装置,其结构框图如 图11所示,一种导向辊制造资源优化配置装置1100,包括:
[0152]
信息获取模块1101,用于获取导向辊制造任务信息和导向辊制 造资源信息;
[0153]
目标建立模块1102,用于根据所述导向辊制造任务信息和导向 辊制造资源信息,建立导向辊协同制造链模型,以最小化加工时间和 生产成本为所述协同制造链模型的目标函数;
[0154]
约束条件确定模块1103,用于确定所述协同制造链模型的制造 约束条件;
[0155]
配置方案输出模块1104,用于利用预设的优化配置算法,计算 所述目标函数在所述制造约束件下的最优解,根据所述最优解得到导 向辊制造的资源优化配置方案。
[0156]
如图12所示,上述的一种导向辊制造资源优化配置方法,本发 明还相应提供了一种电子设备1200,该电子设备可以是移动终端、 桌上型计算机、笔记本、掌上电脑及服务器等计算设备。该电子设备 包括处理器1201、存储器1202及显示器1203。
[0157]
存储器1202在一些实施例中可以是计算机设备的内部存储单元, 例如计算机设备的硬盘或内存。存储器1202在另一些实施例中也可 以是计算机设备的外部存储设备,例如计算机设备上配备的插接式硬 盘,智能存储卡(smart media card,smc),安全数字(secure digital, sd)卡,闪存卡(flash card)等。进一步地,存储器1202还可以既 包括计算机设备的内部存储单元也包括外部存储设备。存储器1202 用于存储安装于计算机设备的应用软件及各类数据,例如安装计算机 设备的程序代码等。存储器1202还可以用于暂时地存储已经输出或 者将要输出的数据。在一实施例中,存储器1202上存储有一种导向 辊制造资源优化配置方法程序1204,该一种导向辊制造资源优化配 置方法程序1204可被处理器1201所执行,从而实现本发明各实施例 的一种导向辊制造资源优化配置方法。
[0158]
处理器1201在一些实施例中可以是一中央处理器(central processing unit,cpu),微处理器或其他数据处理芯片,用于运行 存储器1202中存储的程序代码或处理数据,例如执行一种导向辊制 造资源优化配置程序等。
[0159]
显示器1203在一些实施例中可以是led显示器、液晶显示器、 触控式液晶显示器以及oled(organic light-emitting diode,有机发 光二极管)触摸器等。显示器1203用于显示在计算机设备的信息以 及用于显示可视化的用户界面。计算机设备的部件1201-1203通过系 统总线相互通信。
[0160]
本实施例还提供了一种计算机可读存储介质,其上存储有一种导 向辊制造资源优化配置方法的程序,处理器执行程序时,实现如上述 任一技术方案所述的一种导向辊制造资源优化配置方法。
[0161]
根据本发明上述实施例提供的计算机可读存储介质和计算设备, 可以参照根据本发明实现如上所述的一种导向辊制造资源优化配置 方法具体描述的内容实现,并具有与如上所述的一种导向辊制造资源 优化配置方法类似的有益效果,在此不再赘述。
[0162]
本发明公开的一种导向辊制造资源优化配置方法、装置、设备及 介质,首先,获取导向辊制造任务信息和导向辊制造资源信息;其次, 根据所述导向辊制造任务信息和导向辊制造资源信息,建立导向辊协 同制造链模型,并确定模型的目标函数和制造约束条件;最后,利用 预设的优化配置算法,计算所述目标函数在所述制造约束件下的最优 解,根据所述最优解得到导向辊制造的资源优化配置方案。
[0163]
本发明面向印刷机械导向辊加工过程,对导向辊生产车间的协同 制造资源配置问题进行研究,建立了更契合实际生产情况的导向辊协 同制造链模型,将导向辊生产车间制造资源配置问题归结为多目标优 化问题,并设计了一种优化配置算法对模型问题进行求解,能够快速 对协同制造链模型进行求解,提高了配置策略的制定速度,使配置方 案的制定更加高效。
[0164]
以上所述,仅为本发明较佳的具体实施方式,但本发明的保护范 围并不局限于此,任何熟悉本技术领域的技术人员在本发明揭露的技 术范围内,可轻易想到的变化或替换,都应涵盖在本发明的保护范围 之内。