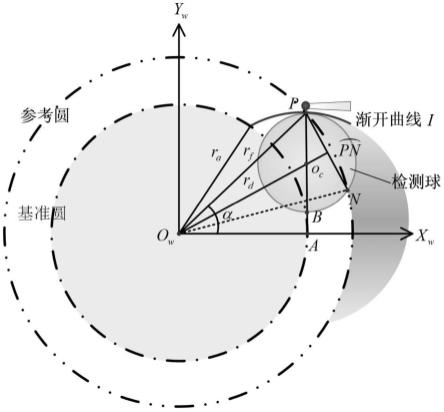
1.本发明属于齿距标准器技术领域,具体涉及一种用于模拟高精度标准齿轮 的齿距模拟标准器及其设计方法,还涉及一种齿距量值标定方法。
背景技术:2.齿距样板是用于数控齿轮测量仪器进行高精度校准和齿距量值传递的标准 器,故又称为齿距标准器。现有技术中采用高精度标准齿轮作为传统齿距样板, 存在如下缺陷:(1)传统齿距样板加工工艺十分复杂,制造价格昂贵,其齿面 容易被测头划伤,并不易修复;(2)传统齿距样板难以加工出大尺寸,因此校 准范围受限制,难以满足较大的齿轮测量中心的要求;(3)针对高精度齿轮测 量仪器,由于加工精度的限制,传统齿距样板的精度往往难以达到设备要求。
技术实现要素:3.本发明的目的在于解决上述现有技术中存在的难题,提供一种齿距模拟标 准器的设计方法,以解决传统齿距样板难以加工制造的技术问题,能够通过标 准球模拟出具有齿距量值的标准器。
4.本发明是通过以下技术方案实现的:一种齿距模拟标准器的设计方法,包 括以下步骤:
5.获取目标齿距样板的参数,包括分度圆半径、压力角、模数与齿数;
6.建立目标齿距样板的坐标系owx
wyw
:以目标齿距样板的中心为坐标原点 ow,沿两个互相垂直的半径方向分别为xw轴、yw轴;
7.在目标齿距样板的坐标系owx
wyw
下,假设采用位于目标齿距样板的渐开线 凹侧的标准球的部分圆弧代替目标齿距样板中单齿的渐开线轮廓:以目标齿距 样板的分度圆与渐开线的交点,作为标准球在坐标系owx
wyw
下的水平投影圆的 切点;
8.根据所述水平投影圆的半径与目标齿距样板的分度圆半径之间的几何关 系,计算出水平投影圆的半径以及水平投影圆到坐标原点的距离;
9.所述水平投影圆的半径作为标准球的设计半径,所述水平投影圆的圆心到 坐标原点的距离作为标准球的球心到高精度旋转台的中心轴线的设计距离,从 而获得齿距模拟标准器的设计参数;
10.通过高精度旋转台的旋转角度对设计齿距角进行模拟,得到模拟齿距角; 设计齿距角θ
′
=2π/z,z表示目标齿距样板的齿数;目标齿距样板的分度圆半径 作为齿距模拟标准器的分度圆半径;所述模拟齿距角在分度圆上所对应的弧长 即为齿距。
11.进一步的,所述标准球的设计半径,即水平投影圆的半径,按如下公式计 算:
[0012][0013]
所述设计距离,即水平投影圆的圆心到坐标原点的距离,按如下公式计算:
[0014][0015]
式中,rc表示标准球的设计半径;rf表示目标齿距样板的分度圆半径;rd表 示标准球的球心到高精度旋转台的中心轴线的设计距离;l
pn
表示目标齿距样板 的齿厚,l
pn
=π
·mn
/2,mn表示模数;α表示目标齿距样板的压力角。
[0016]
本发明还提供一种齿距模拟标准器的制备方法,采用本发明的齿距模拟标 准器的设计方法获取齿距模拟标准器的设计参数;按照所述设计半径选择单个 标准球并按照所述设计距离布置标准球与高精度旋转台的相对位置,从而制备 得到齿距模拟标准器。
[0017]
本发明还提供一种齿距模拟标准器,采用本发明的齿距模拟标准器的制备 方法制备得到。
[0018]
进一步的,标准球按所述设计距离布置在高精旋转台上。
[0019]
进一步的,标准球座布置在高精度旋转台外侧,并通过激光光路确定标准 球与高精度旋转台之间的相对位置。
[0020]
进一步的,激光干涉仪设置在高精度旋转台上,正交分光棱镜设置在高精 度旋转台中央,正交分光棱镜顶部设置全反射镜,标准球通过支撑座固定在高 精度旋转台外,支撑座相对于正交分光棱镜的区域设有测量面镜;测量面镜的 反射表面所在平面为所述标准球的切平面;
[0021]
通过激光光路确定标准球与高精度旋转台之间的相对位置:所述激光干涉 仪沿水平方向发射的激光光束到达正交分光棱镜后,分成水平光束与竖向光束; 竖向光束与高精度旋转台的中心轴线重合;所述竖向光束到达所述全反射镜后 被反射回正交分光棱镜,再被正交分光棱镜反射回激光干涉仪;所述水平光束 到达所述测量面镜后,被反射回激光干涉仪;
[0022]
通过调节所述支撑座的位置,使得两路反射光束的距离差加上标准球的半 径等于所述设计距离。
[0023]
进一步的,标准球通过磁定位装置固定在支撑座上。
[0024]
本发明还提供一种齿距量值标定方法,采用三坐标测量机对本发明所提供 的齿距模拟标准器的齿距量值进行标定:
[0025]
根据齿数z确定高精度旋转台在同一初始位置下的旋转次数n=z-1,以所 述设计齿距角作为每次旋转的目标角度;
[0026]
对初始位置的标准球进行采样,然后标准球与高精度旋转台同步旋转,每 旋转一次就对标准球进行采样,通过采样点拟合出标准球在各个位置的球心坐 标;
[0027]
通过各个位置的标准球的球心坐标拟合出齿距模拟标准器的中心坐标;
[0028]
计算齿距模拟标准器的中心坐标分别与两相邻位置的球心坐标的连线的夹 角作为模拟齿距角;
[0029]
计算各个模拟齿距角在分度圆上对应的弧长,从而实现齿距量值的标定。
[0030]
进一步的,对齿距量值进行误差修正:
[0031]
设置至少两个不同的初始位置,测量每个初始位置下各个模拟齿距角所对 应的齿距量值;第j个初始位置下的第i个齿距量值表示为第j个初始位置 下的第i个齿距量值的仪器测量误差表示为量值的仪器测量误差表示为l表示理论齿距值, l=πmn,由此建立误差修正矩阵m:
[0032][0033]
根据误差修正矩阵m计算各齿距量值的修正值:
[0034][0035]
式中,表示误差修正矩阵m中第i行第j列元素,i∈{1,2,.....,z},z表示齿 数,j∈{1,2,......,n},n表示初始位置的总个数。
[0036]
与现有技术相比,本发明的有益效果包括:
[0037]
1、本发明的齿轮模拟标准器所需要设计的参数仅需标准球的设计半径与标 准球的球心到高精度旋转台的中心轴线的设计距离,不仅使得设计过程简洁高 效,而且设计参数越少,那么制备标准器所引入的制备误差就会越少,有利于 提高标准器的精度。
[0038]
2、本发明十分巧妙的通过高精度旋转台的旋转角度对设计齿距角进行模 拟,再通过模拟齿距角在分度圆上所对应的弧长就模拟得到齿距,因此不再需 要加工出高精度的实体齿轮来提供齿距量值。
[0039]
3、本发明的齿距模拟标准器的制备方法十分简便:高精度旋转台可以通过 购买现成品获得,标准球可以通过购买现成品或加工制造获得,而且仅需要一 个标准球,大大节省了成本,同时与采样多个标准球相比,减少了加工误差的 累计。
[0040]
4、对于尺寸较小的目标齿轮样板的模拟,将标准器布置在高精度旋转台上 即可;对于尺寸较大的目标齿轮样板的模拟,标准球座布置在高精度旋转台外 侧,并通过激光光路确定标准球与高精度旋转台之间的相对位置。总之,通过 调整标准球与高精度选择台之间的距离,就能调整对目标齿轮样板的尺寸的模 拟。
[0041]
5、激光干涉仪属于高精度仪器,通过激光干涉仪的光路确定出的标准球与 高精度旋转台之间的距离具有极高的精度,能够满足设计距离。
[0042]
6、本发明通过设置不同的初始位置来测量不同初始位置下各个模拟齿距角 所对应的齿距量值,再求平均值,不同方位的测量误差可形成相互抵消之势, 形成了误差自闭环修正,提高误差等级。
附图说明
[0043]
图1为设计过程中用标准球的部分圆弧代替渐开线轮廓的理论模型图;
[0044]
图2为实施例1中的齿距模拟标准器的结构示意图;
[0045]
图3为基准圆心偏心引起的球心轨迹偏离理想位置的示意图;
[0046]
图4为第一个初始位置的示意图;
[0047]
图5为第二初始位置的示意图;
[0048]
图6为齿距量值修正前的误差等级图;
[0049]
图7为齿距量值修正后的误差等级图。
[0050]
图8为实施例2中的齿距模拟标准器的结构示意图。
具体实施方式
[0051]
下面结合附图对本发明作进一步详细描述:
[0052]
一种齿距模拟标准器的设计方法,包括以下步骤:
[0053]
获取目标齿距样板的参数,包括分度圆半径rf、压力角α、模数mn与齿数z;
[0054]
参考图1所示,建立目标齿距样板的坐标系owx
wyw
:以目标齿距样板的中 心为坐标原点ow,沿两个互相垂直的半径方向分别为xw轴、yw轴;
[0055]
在目标齿距样板的坐标系owx
wyw
下,假设采用位于目标齿距样板的渐开线 凹侧的标准球的部分圆弧代替目标齿距样板中单齿的渐开线轮廓:以目标齿距 样板的分度圆与渐开线的交点p,作为标准球在坐标系owx
wyw
下的水平投影圆 的切点;
[0056]
根据所述水平投影圆的半径与目标齿距样板的分度圆半径之间的几何关 系,计算出水平投影圆的半径以及水平投影圆到坐标原点的距离;
[0057]
所述标准球的设计半径,即水平投影圆的半径,按如下公式计算:
[0058][0059]
所述设计距离,即水平投影圆的圆心到坐标原点的距离,按如下公式计算:
[0060][0061]
式中,rc表示标准球的设计半径;rf表示目标齿距样板的分度圆半径;rd表 示标准球的球心到高精度旋转台的中心轴线的设计距离;l
pn
表示目标齿距样板 的齿厚,l
pn
=π
·mn
/2,mn表示模数;α表示目标齿距样板的压力角。
[0062]
所述水平投影圆的半径作为标准球的设计半径rc,所述水平投影圆的圆心 oc到坐标原点ow的距离作为标准球的球心到高精度旋转台的中心轴线的设计距 离rd,从而获得齿距模拟标准器的设计参数;
[0063]
参考图2所示,通过高精度旋转台的旋转角度θ对设计齿距角进行模拟, 得到模拟齿距角;设计齿距角θ
′
=2π/z,z表示目标齿距样板的齿数;目标齿距 样板的分度圆半径rf作为齿距模拟标准器的分度圆半径;所述模拟齿距角在分 度圆上所对应的弧长即为齿距。
[0064]
计算出齿距模拟标准器的设计参数后,按照所述设计半径选择或制备单个 标准球并按照所述设计距离rd布置标准球与高精度旋转台的相对位置,从而制 备得到齿距模拟标准器。
[0065]
采用三坐标测量机对齿距模拟标准器的齿距量值进行标定:
[0066]
根据齿数z确定高精度旋转台在同一初始位置下的旋转次数n=z-1,以所 述设计齿距角作为每次旋转的目标角度;
[0067]
对初始位置的标准球进行采样,然后标准球与高精度旋转台同步旋转,每 旋转一次就对标准球进行采样,通过采样点拟合出标准球在各个位置的球心坐 标;
[0068]
通过各个位置的标准球的球心坐标拟合出齿距模拟标准器的中心坐标;
[0069]
计算齿距模拟标准器的中心坐标分别与两相邻位置的球心坐标的连线的夹 角作为模拟齿距角;
[0070]
计算各个模拟齿距角在分度圆上对应的弧长,从而实现齿距量值的标定。
[0071]
对齿距量值进行误差修正:
[0072]
设置至少两个不同的初始位置,测量每个初始位置下各个模拟齿距角所对 应的齿距量值;第j个初始位置下的第i个齿距量值表示为第j个初始位置 下的第i个齿距量值的仪器测量误差表示为由此建立误差修正矩阵m:
[0073][0074]
误差修正矩阵m中的每一列对应一个初始位置,第一列以为减数,分别按照 第1个齿距量值到第z个齿距量值的闭环顺序取被减数计算差项;第二列以为 减数,分别按照第z个齿距量值到第z-1个齿距量值的闭环顺序取被减数计算 差项;第三列以为减数,分别按照第z-1个齿距量值到第z-2个齿距量值的 闭环顺序取被减数计算差项;以此类推,在闭环中,根据对称特性,一些地方 的测量误差偏大,另一些地方的误差必然偏小,因此累加后能够显著的消除误 差。
[0075]
根据误差修正矩阵计算各齿距量值的修正值:
[0076][0077]
式中,表示第i个齿距量值的修正值;表示误差修正矩阵m中第i行 第j列元素,i∈{1,2,.....,z},z表示齿数,j∈{1,2,......,n},n表示初始位置的总个 数。
[0078]
根据目标齿距样板的尺寸采用不同方式来布置标准球,下面分别以实施例 1与实施例2进行说明。
[0079]
实施例1
[0080]
对于尺寸较小的目标齿距样板的模拟,将标准球布置在高精度旋转台上, 标准球按设计距离布置在高精旋转台上,为了易于更换标准球,标准球通过磁 定位装置吸附固定在高精度旋转台上。标准球在测量过程中受到仪器探针360
°ꢀ
的探测力f',这就要求磁力f1略大于(f'-gb)/μ,其中gb为标准球的重量、μ为 球与磁装置接触面的摩擦系数。
[0081]
磁定位装置的原理参考中国专利(cn1096822852b)中的磁定位装置,在 高精度旋
转台内设置电磁铁与电路,通过调节限流电阻的阻值来改变电流大小, 从而改变磁力大小。
[0082]
磁定位装置还可以永磁铁,永磁铁上下端为磁极的n和s极,永磁铁周边 由绝缘材料包裹,以防对仪器探针产生较大的磁吸附力。
[0083]
标准球由磁定位装置吸附固定在高精度旋转台上,选择高精度旋转台的中 心圆柱中心作为齿距模拟标准器的轴心线,选择旋转台自身的中心圆柱或者其 他参考作为基准,是为了避免齿距模拟标准器的中心轴线与高精度旋转台自身 轴线不重合,以更加准确的确定齿距模拟标准器的中心轴线。
[0084]
通过调节标准球球心与转台轴线的距离(可通过激光光标尺进行测距)来 模拟出目标齿距样板的分度圆半径rf。同时通过高精度旋转台旋转实现对模拟 齿距角度的控制,能够满足不同齿距弧长的要求。
[0085]
为了简化验证过程,本实施例选取能直接购买得到的国际标准中最广泛使 用的标准球,即直径为12.7mm标准球,并且rd=rf,目标齿距样板的参数如下: z=8,mn=26.87925mm,rf=107.51875mm。标准球的直径经校准满足12.7
±
0.0005mm 要求;经在三坐标测量机上的测试,当磁铁吸附力大于5.42n时,球在360
°
受 力情况下不受影响。可得到表1如下。
[0086]
表1齿距模拟标准器的设计参数
[0087][0088][0089]
依据最新国际齿轮标准iso1328-1对齿距测量误差等级进行评价,单个齿 距偏差f
pt
和齿距总偏差等级f
pt
计算公式分别如下:
[0090][0091][0092]
将本实施例中的齿距模拟标准器溯源至中国计量科学研究院的齿轮多参量 计量标准装置,图3给出了单个齿距偏差重复测量结果。从图3中可以看出, 新研制的齿距样板单个齿距偏差均值处于0级至1级,单个齿距偏差的重复性 均小于1.5μm,并且齿距累积总偏差为7.0μm,大于0级6.9492μm,小于1级 9.8278μm,这说明新研制的齿距模拟标准器达到了1级齿距样板水平。
[0093]
新型研制的齿距模拟标准器具备轴对称结构,并且具备闭环特征,利用多 方位自修正技术能够消除使用过程中的系统误差。图4给出了基准圆心偏心引 起的球心轨迹偏离理想位置的情景(如图中虚线轨迹所示),这在实际应用中经 常发生,将引起过大的系统误
差。
[0094]
对本实施例中的齿距模拟标准器进行了系统误差修正处理。设置至少两个 不同的初始位置,测量每个初始位置下各个模拟齿距角所对应的齿距量值;第j 个初始位置下的第i个齿距量值表示为第j个初始位置下的第i个齿距量值 的仪器测量误差表示为的仪器测量误差表示为l表示理论齿距值,l=πmn。如图5所示, 在方第一初始位置中获得一组齿距弧长测量结果旋转齿距模拟 标准器,参考图6所示,变化第一齿的位置到第二初始位置,获得第二组齿距 弧长测量结果再继续旋转变化第一齿的初始位置,直至达到360
°
, 形成闭环。通过n次方位变化,本例中取n=8,建立相应的误差修正矩阵:
[0095][0096]
为了消除仪器测量的系统误差,采用求和平均的方式,根据误差修正矩阵计算 各齿距量值的修正值:
[0097][0098]
式中,表示第i个齿距量值的修正值;表示误差修正矩阵m中第i行 第j列元素,i∈{1,2,.....,z},z表示齿数,j∈{1,2,......,n},n表示初始位置的总个 数。
[0099]
图7显示了齿距模拟标准器经过8次方位修正后的测量结果。相较于图3, 图7中单个齿距测量偏差稳定在0级内,齿距累积偏差为3.2μm,小于0级 6.9492μm,修正后的齿距量值达到0级水平。
[0100]
实施例2
[0101]
对于尺寸较大的目标齿轮样板的模拟,标准球座布置在高精度旋转台外侧, 并通过激光光路确定标准球与高精度旋转台之间的相对位置,参考图8所示, 具体的如下:
[0102]
激光干涉仪3设置在高精度旋转台1上,正交分光棱镜4设置在高精度旋 转台中央,正交分光棱镜4顶部设置全反射镜5,标准球通过支撑座固定在高 精度旋转台外,支撑座内设置磁定位装置以吸附固定标准球,支撑座相对于正 交分光棱镜4的区域设有测量面镜6;测量面镜6的反射表面所在平面为所述 标准球的切平面;
[0103]
通过激光光路确定标准球与高精度旋转台之间的相对位置:所述激光干涉 仪沿水平方向发射的激光光束到达正交分光棱镜后,分成水平光束与竖向光束; 竖向光束与高精度旋转台的中心轴线重合;所述竖向光束到达所述全反射镜后 被反射回正交分光棱镜,再被正交分光棱镜反射回激光干涉仪;所述水平光束 到达所述测量面镜后,被反射回激光干涉仪;
[0104]
通过调节所述支撑座的位置,使得两路反射光束的距离差加上标准球的半 径等于所述设计距离。
[0105]
本实施例的齿距模拟标准器用于齿距量值标定时,所有步骤与实际例1相 同,除
了标准球与高精度旋转台的同步旋转方式与实施例1不同,具体的:每 通过高精度旋转台的旋转模拟一次设计齿距角,就将支撑座移动到使测量面镜 中央与激光水平光束垂直的位置,并且调节支撑座到正交分光棱镜的距离使得 两路反射光束的距离差加上标准球的半径等于所述设计距离。
[0106]
同样的,齿距量值标定后还可以采用实施例1中的多方位自修正技术消除 使用过程中的系统误差。
[0107]
上述技术方案只是本发明的一种实施方式,对于本领域内的技术人员而言, 在本发明公开了原理的基础上,很容易做出各种类型的改进或变形,而不仅限 于本发明上述具体实施例所描述的技术方案,因此前面描述的只是优选的,而 并不具有限制性的意义。