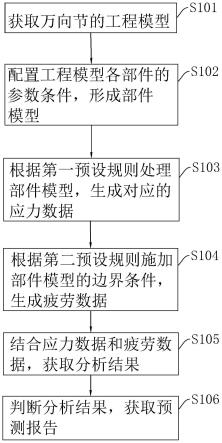
1.本技术涉及轴承检测技术领域,尤其涉及一种万向节寿命预测方法及系统。
背景技术:2.万向节即万向接头,是实现变角度动力传递的机件,用于需要改变传动轴线方向的位置,它是汽车驱动系统的万向传动装置的“关节”部件。
3.等速万向节是汽车驱动轴的关键部件之一,常见的等速万向节有球式,球笼式等,球笼式等速万向节作为旋转轴之间连接的关键部件,可以克服普通十字轴万向节所存在的不等速问题,同时自身也具备较强的刚度。
4.在动力传递过程中,万向节各个部件具有复杂的接触力学关系,较难进行直接受力分析,因此难以通过仿真试验对其寿命预测、结构特点以及构件间的相互作用进行直接测定,再者寿命实验的周期过长,代价较大,不利于产品开发阶段的反复迭代和优化。
技术实现要素:5.为了提升万向节寿命的预测效果,本技术提供一种万向节寿命预测方法及系统。
6.第一方面,本技术提供一种万向节寿命预测方法,包括以下步骤:获取万向节的工程模型;配置所述工程模型各部件的参数条件,形成部件模型;根据第一预设规则处理所述部件模型,生成对应的应力数据;根据第二预设规则施加所述部件模型的边界条件,生成疲劳数据;结合所述应力数据和所述疲劳数据,获取分析结果;解析所述分析结果,获取预测报告。
7.通过采用上述技术方案,根据万向节的工程模型配置其各部件对应的参数条件,进而形成赋予参数值部件模型,然后根据第一预设规则对部件模型进行相应处理,获取各个部件模型对应的应力数据,同时根据第二预设规则施加各部件模型的边界条件,获取对应的疲劳数据,以便于结合应力数据和疲劳数据进行仿真,得到较为准确的分析结果,进一步结合相关数据对获取的分析结果进行解析判断,形成最终的预测报告,从而提升了万向节寿命的预测效果。
8.可选的,所述根据第一预设规则处理所述部件模型,生成对应的应力数据包括以下步骤:根据所述第一预设规则,获取所述部件模型的接触应力位置;根据所述接触应力位置,获取对应的最大接触应力和整体接触应力;将所述最大接触应力和所述整体接触应力作为所述应力数据。
9.通过采用上述技术方案,根据第一预设规则获取并确定部件模型的接触应力位置,便于获取对应的最大接触应力和整体接触应力,从而根据最大接触应力和整体接触应力可以更准确地分析并获取部件模型对应的应力数据。
10.可选的,所述根据第二预设规则施加所述部件模型的边界条件,生成疲劳数据包括以下步骤:根据所述第二预设规则,获取所述部件模型的接触碰撞模型;根据所述边界条件,施加所述接触碰撞模型的转动参数,并生成所述疲劳数据。
11.通过采用上述技术方案,根据第二预设规则获取部件模型的接触碰撞模型,并根据边界条件施加接触碰撞模型的转动参数,可以更准确地生成接触碰撞模型中部件模型的疲劳数据。
12.可选的,所述结合所述应力数据和所述疲劳数据,获取分析结果包括以下步骤:分析所述应力数据,获取所述部件模型的接触应力分布图;分析所述疲劳数据,获取所述部件模型的疲劳寿命云图;结合所述接触应力分布图和所述疲劳寿命云图,获取所述分析结果。
13.通过采用上述技术方案,结合接触应力分布图和所述疲劳寿命云图对万向节的寿命进行综合分析,从而可以提升分析结果的准确性。
14.可选的,所述分析所述疲劳数据,获取所述部件模型的疲劳寿命云图包括以下步骤:加载所述疲劳数据,获取所述部件模型的特征信息;根据预设运算规则处理所述特征信息,生成所述部件模型的所述疲劳寿命云图。
15.通过采用上述技术方案,根据预设运算规则对部件模型的特征信息进行运算,可过滤掉无意义的信号分量,进一步提升了获取部件模型疲劳寿命云图中信息的准确性。
16.可选的,所述结合所述接触应力分布图和所述疲劳寿命云图,获取所述分析结果包括以下步骤:判断所述部件模型的所述参数条件是否符合预设工艺条件;若符合所述预设工艺条件,则根据所述预设工艺条件获取对应的工艺属性信息,并结合所述工艺属性信息、所述接触应力分布图和所述疲劳寿命云图进行分析,获取所述分析结果。
17.通过采用上述技术方案,判断部件模型的参数条件是否符合对应预设工艺条件,可减少最终分析结果与实际严重不符情况的发生,从而提升了分析结果的准确性。
18.可选的,所述判断所述分析结果,获取预测报告包括以下步骤:加载所述分析结果,生成对应的仿真结果;判断所述仿真结果是否符合预设测试结果;若符合所述预设测试结果,则根据所述仿真结果生成正常预测数据作为所述预测报告;若不符合所述预设测试结果,则根据所述预设测试结果对所述仿真结果进行分析,获取异常预测数据作为所述预测报告。
19.通过采用上述技术方案,根据预设测试结果对生成的仿真结果进行分析判断,进一步获取到对应正常预测数据或异常预测数据的预测报告,从而提升了预测效果,且便于后续对异常预测数据进行反馈。
20.可选的,所述若不符合所述预设测试结果,则根据所述预设测试结果对所述仿真结果进行分析,获取异常预测数据作为所述预测报告包括以下步骤:
根据预设测试结果,获取目标测试数据;根据所述目标测试数据的类型,匹配所述仿真结果中的仿真数据;分析所述目标测试数据和所述仿真数据,获取所述异常预测数据,并生成所述预测报告。
21.通过采用上述技术方案,根据目标测试数据匹配仿真结果中的仿真数据,从而可以准确获取仿真结果中的异常预测数据。
22.可选的,所述分析所述目标测试数据和所述仿真数据,获取所述异常预测数据,并生成所述预测报告包括以下步骤:获取所述仿真数据中不符合所述目标测试数据的异常仿真数据;判断所述异常仿真数据的数量;若存在单项所述异常仿真数据,则将单项所述异常仿真数据作为所述异常预测数据,并生成所述预测报告;若存在多项所述异常仿真数据,则获取各个所述异常仿真数据的目标权重;选取最大所述目标权重的所述异常仿真数据作为所述异常预测数据,并生成所述预测报告。
23.通过采用上述技术方案,判断异常仿真数据的数量,进而根据实际的数量情况和所占目标权重选取异常预测数据,进一步生成对应的预测报告,可提升后续对异常仿真数据的分析效率。
24.第二方面,本技术还提供一种万向节寿命预测系统,包括:获取模块,用于获取万向节的工程模型;配置模块,用于配置所述工程模型各部件的参数条件,形成部件模型;第一预设规则模块,用于根据第一预设规则处理所述部件模型,生成对应的应力数据;第二预设规则模块,用于根据第二预设规则施加所述部件模型的边界条件,生成疲劳数据;结合模块,用于结合所述应力数据和所述疲劳数据,获取分析结果;解析模块,用于解析所述分析结果,获取预测报告。
25.通过采用上述技术方案,根据获取模块获取的万向节的工程模型,通过配置模块配置其各部件对应的参数条件,进而形成赋予参数值部件模型,以便于第一预设规则模块根据第一预设规则对部件模型进行相应处理,获取各个部件模型对应的应力数据,同时结合第二预设规则模块根据第二预设规则施加各部件模型的边界条件,获取对应的疲劳数据,随即通过结合模块结合应力数据和疲劳数据进行仿真,进而可得到较为准确的分析结果,最后通过的解析模块调用相关数据对获取的分析结果进行解析判断,形成最终的预测报告,从而提升了万向节寿命的预测效果。
26.综上所述,本技术包括以下有益技术效果:根据万向节的工程模型配置其各部件对应的参数条件,进而形成赋予参数值部件模型,然后根据第一预设规则对部件模型进行相应处理,获取各个部件模型对应的应力数据,同时根据第二预设规则施加各部件模型的边界条件,获取对应的疲劳数据,以便于结合应力数据和疲劳数据进行仿真,得到较为准确的分析结果,进一步结合相关数据对获取的分析结果进行解析判断,形成最终的预测报告,
从而提升了万向节寿命的预测效果。
附图说明
27.图1是本技术一种万向节寿命预测方法中步骤s101至步骤s106的流程示意图。
28.图2是本技术一种万向节寿命预测方法中的万向节结构图。
29.图3是本技术一种万向节寿命预测方法中万向节的材料参数图。
30.图4是本技术一种万向节寿命预测方法中步骤s201至步骤s203的流程示意图。
31.图5是本技术一种万向节寿命预测方法中的结果数据图。
32.图6是本技术一种万向节寿命预测方法中步骤s301至步骤s302的流程示意图。
33.图7是本技术一种万向节寿命预测方法中的边界条件图。
34.图8是本技术一种万向节寿命预测方法中的万向节应力寿命曲线图。
35.图9是本技术一种万向节寿命预测方法中步骤s401至步骤s403的流程示意图。
36.图10是本技术一种万向节寿命预测方法中万向节外轮花键部位寿命云图。
37.图11是本技术一种万向节寿命预测方法中步骤s501至步骤s502的流程示意图。
38.图12是本技术一种万向节寿命预测方法中步骤s601至步骤s602的流程示意图。
39.图13是本技术一种万向节寿命预测方法中步骤s701至步骤s704的流程示意图。
40.图14是本技术一种万向节寿命预测方法中步骤s801至步骤s803的流程示意图。
41.图15是本技术一种万向节寿命预测方法中步骤s901至步骤s904的流程示意图。
42.图16是本技术一种万向节寿命预测系统中的模块示意图。
43.附图标记说明:1、获取模块;2、配置模块;3、第一预设规则模块;4、第二预设规则模块;5、结合模块;6、解析模块。
具体实施方式
44.以下结合附图1-16对本技术作进一步详细说明。
45.为了便于对方案进行说明,本实施例以球笼式等速万向节为例,球笼等速万向节作为旋转轴之间连接的关键部件,可以克服普通十字轴万向节所存在的不等速问题,同时自身也具备较强的刚度。
46.本技术实施例公开一种万向节寿命预测方法,参照图1,包括以下步骤:s101、获取万向节的工程模型;s102、配置工程模型各部件的参数条件,形成部件模型;s103、根据第一预设规则处理部件模型,生成对应的应力数据;s104、根据第二预设规则施加部件模型的边界条件,生成疲劳数据;s105、结合应力数据和疲劳数据,获取分析结果;s106、判断分析结果,获取预测报告。
47.步骤s101中的工程模型是指万向节的分析模型建立,其包括结构模型和网格模型。
48.例如,如图2所示,为uf球笼式等速万向节结构图,主要由外轮、内轮、保持轮、钢球组成,保持架上有6窗体容纳钢球,外轮上有6个球道供钢球移动。
49.其中,工程模型在进行几何简化后仍然存在面积较细小区域,如花键齿处、球道细节处等,可采用较小单元划分,其余位置则使用较大单元。
50.步骤s102中的参数条件是指工程模型中万向节各零部件的材料参数以及属性信息。
51.例如,如图3所示,配置了工程模型各部件的材料参数以及对应的属性信息,外轮部件的材料选取为55#钢,弹性模量/gpa为217,泊松比为0.27,密度/kg
·
m-3
为7830;内轮材料选取为20crmntih,弹性模量/gpa为212,弹性模量/gpa为212,泊松比为0.289,密度/kg
·
m-3
为7860;保持架的材料选取为20crmntih,弹性模量/gpa为212,弹性模量/gpa为212,泊松比为0.289,密度/kg
·
m-3
为7860;钢球的材料选取为gcr15,弹性模量/gpa为219,泊松比为0.3,密度/kg
·
m-3
为7830。
52.步骤s103中的第一预设规则是指部件模型的静力学分析方法,根据静力学分析方法施加各部件模型的仿真条件以及约束条件,并生成对应的应力数据。
53.步骤s104中的第二预设规则是指部件模型的动力学分析方法,根据动力学分析方法施加各部件模型的边界条件,并依此生成对应的疲劳数据。
54.步骤s105中的分析结果是指结合各部件的应力数据和疲劳数据综合进行分析的结果,通过使用静力学分析方法和动力学分析方法,将二者结合后用于部件模型的仿真。
55.步骤s106中预测报告是指根据分析结果和相关的实验测试,进而获取到最终有关万向节寿命的预测结果。
56.本实施例提供的一种万向节寿命预测方法,根据万向节的工程模型配置其各部件对应的参数条件,进而形成赋予参数值部件模型,然后根据第一预设规则对部件模型进行相应处理,获取各个部件模型对应的应力数据,同时根据第二预设规则施加各部件模型的边界条件,获取对应的疲劳数据,以便于结合应力数据和疲劳数据进行仿真,得到较为准确的分析结果,进一步结合相关数据对获取的分析结果进行判断,形成最终的预测报告,从而提升了万向节寿命的预测效果。
57.在本实施例的其中一种实施方式中,如图4所示,步骤s103包括以下步骤:s201、根据第一预设规则,获取部件模型的接触应力位置;s202、根据接触应力位置,获取对应的最大接触应力和整体接触应力;s203、将最大接触应力和整体接触应力作为应力数据。
58.在实际运用中,第一预设规则是指运用静力学分析方法对部件模型设定静力学仿真工况,接触应力位置是指部件模型的接触处。
59.例如,根据静力学仿真工况对部件模型采用6
°
夹角660n
·
m静载荷条件下进行仿真分析计算,载荷加于外轮花键,花键中心处施加除轴向约束外的所有约束,并约束花键非轴向转动,外轮尾部施加轴向约束,保持架与钢球在完全自由运动时,施加任何约束也能达到运动接触平衡。
60.如图5所示,根据部件模型的材料参数以及静力学分析结果可得,外轮内圆及球槽部位表面、杆部及花键部位强度不小于2390mpa,花键轴芯部约为1039mpa,其中,外轮与钢球接触处最大接触应力为1232mpa,整体接触应力为3750mpa,并将部件模型对应的最大接触应力和整体接触应力作为应力数据。
61.本实施方式提供的一种万向节寿命预测方法,根据第一预设规则获取并确定部件
模型的接触应力位置,便于获取对应的最大接触应力和整体接触应力,从而根据最大接触应力和整体接触应力可以更准确地分析并获取部件模型对应的应力数据。
62.在本实施例的其中一种实施方式中,如图6所示,步骤s104包括以下步骤:s301、根据第二预设规则,获取部件模型的接触碰撞模型;s302、根据边界条件,施加接触碰撞模型的转动参数,并生成疲劳数据。
63.在实际运用中,第二预设规则是指运用动力学分析方法对部件模型设定动力学仿真工况,转动参数是指旋转副,也称回转副,旋转副允许两个构件绕公共轴线作相对转动,转角为α,两构件之间的垂直距离l为常数,称为偏距,接触碰撞模型是指分析部件模型运用的计算方法。
64.例如,如图7所示,为动力学仿真工况的边界条件图,其中设定的产品名称为uf3400i号球笼式等速万向节,计算工况为6
°
夹角,计算方法为部件模型的接触碰撞模型,零件选取外轮,无载荷施加,边界条件为外轮出施加与地面之间的旋转副,相互关系为接触,摩擦系数为0.003。
65.如图8所示,为材料s-n曲线图,本零件在外轮花键处采用热处理出淬硬层,由图8可以得出,金属表面淬火可以大幅度提高表面硬度、刚性、耐磨性等,极大提高了表面寿命。动力学分析模型不设置萃硬层,因此得到疲劳数据后结合淬硬层性质来分析外轮。
66.本实施方式提供的一种万向节寿命预测方法,根据第二预设规则获取部件模型的接触碰撞模型,并根据边界条件施加接触碰撞模型的转动参数,可以更准确地生成接触碰撞模型中部件模型的疲劳数据。
67.在本实施例的其中一种实施方式中,如图9所示,步骤s105包括以下步骤:s401、分析应力数据,获取部件模型的接触应力分布图;s402、分析疲劳数据,获取部件模型的疲劳寿命云图;s403、结合接触应力分布图和疲劳寿命云图,获取分析结果。
68.在实际运用中,接触应力分布图是指根据各部件模型的应力数据生成的应力分布图,疲劳寿命云图是指根据各部件模型的应力数据生成的疲劳寿命图。
69.例如,如图10所示,为外轮花键部位寿命云图,在不考虑淬火的情况下,外轮最短寿命出现在外轮内滚道和钢球接触处,其次是外轮花键部位,当外轮滚道对数寿命为约为6.048,即旋转次数为116863次时,外轮滚道路可能出现凹坑或有裂纹萌生。
70.内轮最短寿命出现在内轮和钢球接触的部位,表面材料平均对数寿命约为6.417,即旋转次数约为2612161次时,内轮表面会出现轻微破坏。
71.本实施方式提供的一种万向节寿命预测方法,结合接触应力分布图和疲劳寿命云图对万向节的寿命进行综合分析,从而可以提升分析结果的准确性。
72.在本实施例的其中一种实施方式中,如图11所示,步骤s402包括以下步骤:s501、加载疲劳数据,获取部件模型的特征信息;s502、根据预设运算规则处理特征信息,生成部件模型疲劳寿命云图。
73.在实际运用中,特征信息是指材料在承受循环加载的过程中其应力应变响应表现出的记忆特征,预设运算规则是指雨流计数法。
74.例如,本实施方式运用仿真分析技术,通过动力学分析得到结构的载荷谱,采用雨流计数法进行疲劳计算并得到疲劳寿命云图。其中,部件模型的材料在承受循环加载的过
程中,其应力应变响应会表现出对应的记忆特征,而雨流计数法能记录材料的应变历程,且删除了无意义的信号分量。
75.本实施方式提供的一种万向节寿命预测方法,根据预设运算规则对部件模型的特征信息进行运算,可过滤掉无意义的信号分量,进一步提升了获取部件模型疲劳寿命云图中信息的准确性。
76.在本实施例的其中一种实施方式中,如图12所示,步骤s403包括以下步骤:s601、判断部件模型的参数条件是否符合预设工艺条件;s602、若符合预设工艺条件,则根据预设工艺条件获取对应的工艺属性信息,并结合工艺属性信息、接触应力分布图和疲劳寿命云图进行分析,获取分析结果。
77.在实际运用中,预设工艺条件是指淬火工艺,淬火工艺可以赋予金属表面更强的刚度并保护内部不会失效,由上述可知金属表面淬火可以大幅度提高表面硬度、刚性、耐磨性等,极大提高了表面寿命,所以在对部件模型的接触应力分布图和疲劳寿命云图进行分析的过程中进一步考虑部件模型是否经过淬火工艺,进行综合分析;工艺属性信息是指部件模型经过淬火工艺而形成的淬硬层的性质。
78.例如,以外轮花键与颈部为例,花键表面淬火后抗拉强度达到了2390mpa,与仿真中未设定淬硬层所得到的结果相比,可以减少花键及内部轴杆的损坏情况的发生,在花键内部完整的情况下,而由于颈部没有经过淬火工艺,失效部位由颈部向外扩散;经过对比发现,淬硬层完整保护了花键及内部材料的完整,提高了的外轮的整体寿命。
79.本实施方式提供的一种万向节寿命预测方法,判断部件模型的参数条件是否符合对应预设工艺条件,可减少最终分析结果与实际严重不符情况的发生,从而提升了分析结果的准确性。
80.在本实施例的其中一种实施方式中,如图13所示,步骤s106包括以下步骤:s701、加载分析结果,生成对应的仿真结果;s702、判断仿真结果是否符合预设测试结果;s703、若符合预设测试结果,则根据仿真结果生成正常预测数据作为预测报告;s704、若不符合预设测试结果,则根据预设测试结果对仿真结果进行分析,获取异常预测数据作为预测报告。
81.在实际运用中,预设测试结果是指根据相应扭转疲劳实验得出的测试结果,正常预测数据是指仿真结果中符合预设测试结果的目标数据,异常预测数据是指仿真结果中不符合预设测试结果的目标数据,预测报告是指包含万向节寿命预测的各项分析数据的报告。
82.例如,将三组uf型球笼式等速万向节样品总成与转向器联接的一端固定,从方向盘一端加正反方向转矩,按照国标方法进行扭转疲劳测试,三组样品均在20万次测以后未发生失效,符合分析结果对应生成的仿真结果,并根据仿真结果生成正常预测数据作为预测报告。
83.又例如,进行扭转疲劳测试后,其中三组样品中的1号组在15万次测以后发生失效,则根据预设测试结果对仿真结果进行分析,获取仿真结果中外轮的疲劳数据对应的预设测试结果,则获取疲劳数据对应的异常预测数据作为预测报告。
84.本实施方式提供的一种万向节寿命预测方法,根据预设测试结果对生成的仿真结
果进行分析判断,进一步获取到对应正常预测数据或异常预测数据的预测报告,从而提升了预测效果,且便于后续对异常预测数据进行反馈。
85.在本实施例的其中一种实施方式中,如图14所示,步骤s704包括以下步骤:s801、根据预设测试结果,获取目标测试数据;s802、根据目标测试数据的类型,匹配仿真结果中的仿真数据;s803、分析目标测试数据和仿真数据,获取异常预测数据,并生成预测报告。
86.在实际运用中,目标测试数据是指根据仿真结果中各类目标数据进行测试的数据,仿真数据是指仿真过程中与目标测试数据对应的数据。
87.例如,根据接触应力分布图和疲劳寿命云图获取各项仿真过程中需要用到的应力数据和疲劳数据,然后将应力数据和疲劳数据与预设测试结果中对应同类型的目标测试数据做对比,获取外轮的疲劳数据不符合对应的外轮测试数据,则获取外轮的疲劳数据作为异常预测数据,并生成对应的预测报告。
88.本实施方式提供的一种万向节寿命预测方法,根据目标测试数据匹配仿真结果中的仿真数据,从而可以准确获取仿真结果中的异常预测数据。
89.在本实施例的其中一种实施方式中,如图15所示,步骤s803包括以下步骤:s901、获取仿真数据中不符合目标测试数据的异常仿真数据;s902、判断异常仿真数据的数量;s903、若存在单项异常仿真数据,则将单项异常仿真数据作为异常预测数据,并生成预测报告;s904、若存在多项异常仿真数据,则获取多项异常仿真数据的目标权重,并选取最大目标权重的异常仿真数据作为异常预测数据,并生成预测报告。
90.在实际运用中,目标权重是指多项异常仿真数据各自所占的比例。例如,例如,获取仿真数据中不符合目标测试数据的异常仿真数据只有内轮疲劳数据,则直接将内轮疲劳数据作为异常预测数据,并生成对应预测报告。
91.又例如,获取仿真数据中不符合目标测试数据的异常仿真数据有内轮疲劳数据、外轮应力数据和钢球应力数据,其中内轮疲劳数据的目标比重为67%,外轮应力数据的目标比重为20%,钢球应力数据的目标比重为13%,则选取内轮疲劳数据作为异常预测数据,并生成对应的预测报告。
92.其中,多项异常仿真数据各自对应的目标比重计算的方法为:首先,获取仿真数据中所有的异常仿真数据,其次,根据仿真数据对应的预设测试结果对多项异常仿真数据进行识别分类,然后分别算出各项异常仿真数据占所有异常仿真数据的比例,进而得出每项异常仿真数据对应的目标比重。
93.本实施方式提供的一种万向节寿命预测方法,判断异常仿真数据的数量,进而根据实际的数量情况和所占目标权重选取异常预测数据,进一步生成对应的预测报告,可提升后续对异常仿真数据的分析效率。
94.本实施例还公开一种万向节寿命预测系统,如图16所示,包括:获取模块1,用于获取万向节的工程模型;配置模块2,用于配置工程模型各部件的参数条件,形成部件模型;第一预设规则模块3,用于根据第一预设规则处理部件模型,生成对应的应力数
据;第二预设规则模块4,用于根据第二预设规则施加部件模型的边界条件,生成疲劳数据;结合模块5,用于结合应力数据和所述疲劳数据,获取分析结果;解析模块6,用于解析分析结果,获取预测报告。
95.本实施方式提供的一种万向节寿命预测系统,根据获取模块1获取的万向节的工程模型,通过配置模块2配置其各部件对应的参数条件,进而形成赋予参数值部件模型,以便于第一预设规则模块3根据第一预设规则对部件模型进行相应处理,获取各个部件模型对应的应力数据,同时结合第二预设规则模块4根据第二预设规则施加各部件模型的边界条件,获取对应的疲劳数据,随即通过结合模块5结合应力数据和疲劳数据进行仿真,进而可得到较为准确的分析结果,最后通过的解析模块6调用相关数据对获取的分析结果进行解析判断,形成最终的预测报告,从而提升了万向节寿命的预测效果。
96.需要说明的是,本技术实施例所提供的一种万向节寿命预测系统,还包括与上述任一一种万向节寿命预测方法的逻辑功能或逻辑步骤所对应的各个模块和/或对应的子模块,实现与各个逻辑功能或者逻辑步骤相同的效果,具体在此不再累述。
97.以上均为本技术的较佳实施例,并非依此限制本技术的保护范围,故:凡依本技术的结构、形状、原理所做的等效变化,均应涵盖于本技术的保护范围之内。