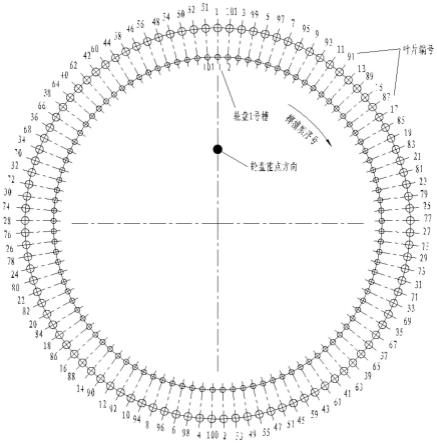
1.本发明涉及航空发动机压气机转子装配领域,尤其涉及一种压气机转子叶片优化排序方法。
背景技术:2.压气机转子的平衡精度对发动机整机的安全工作十分重要,较高的平衡精度可以有效降低整机振动。压气机转子通过动平衡来降低不平衡量,为了减少转子最终动平衡的工作量,提高转子的平衡精度,可在各级压气机转子装配阶段进行单面动平衡,通过轮盘局部去重、增加配重块或优化叶片排序等方法降低单级转子的剩余不平衡量,以降低整个转子动平衡的初始不平衡量。
3.对盘叶分离的单级转子,其剩余不平衡量主要受两方面因素的影响,一方面是轮盘和叶片本身因材料致密性差异和尺寸制造误差导致的质量分布不均,另一方面是不同质量的叶片因排序方法不当导致的转子周向质量分布不均。在实际生产制造过程中,材料致密性差异和制造误差客观存在,不便对其进行优化,但可以通过优化叶片排序,降低叶片对转子的附加不平衡量,或者通过叶片对转子的附加不平衡量与轮盘的剩余不平衡量相互抵消,以降低单级转子的剩余不平衡量。
4.叶片排序的本质是对所有叶片进行排列组合,当叶片数为n片时,共有n!种排列组合方法。理论上必然存在全局最优解,使转子剩余不平衡量在n!种排列组合方法中达到最小。但当叶片数较多时,其排列组合数量级相当庞大,无法通过现有的计算设备在可以接受的时间内获得全局最优解,而且全局最优解下转子剩余不平衡量必然无限接近于0,工程上不需要达到如此的平衡精度。故设计优化排序方法达到满足要求的局部最优解尤其必要。针对叶分离的单级转子叶片排序问题,目前已有
5.公开号为cn113312705a的专利申请公开了一种航空发动机低压风扇转子叶片排序方法,以转子叶片质量矩和转子初始不平衡量为输入,引入退火选择操作,建立了基于退火单亲遗传算法的风扇转子叶片排序模型。此方法在无需人工微调的情况下便可得到优于传统遗传算法的结果,且不易陷入局部收敛,有利于进行高效快速准确的风扇转子叶片排序。
6.又如,公开号为cn111339610a的专利申请公开了一种叶轮机械转子叶片装配优化排序方法,建立安装叶片后单级叶盘考虑叶片重量矩的总不平衡量的力学模型;仿照运筹学整数规划中指派问题的解决思路对力学模型建立叶片配置问题的数学模型;利用遗传算法求解建立的数学模型,获得叶片的优化排列顺序。该专利基于叶轮机械单级叶盘叶片安装问题,通过建立力学模型和数学模型,基于遗传算法通过编制程序/软件实现单级叶盘叶片安装位置的优化配置,能够直接指导工程实际应用。
7.针对盘叶分离的单级转子叶片排序问题,现有技术中将遗传算法用于优化排序,父代通过交叉算子、交异算子进行遗传得到子代个体,子代个体通过适应度函数进行选择,通过迭代计算并控制迭代次数获得最终适应度最优的子代个体输出为最终排序。但是,遗
传算法可以有效解决叶片排序问题,但是其求解过程较为复杂,需要一定的数学功底,才能很好的理解求解思路,建立求解模型。
8.在实际工程中,通常还采用传统的叶片排序方法,对每片叶片进行称重并记录,按质量大小进行编号,继而通过编号进行排序。传统叶片排序方法的目的是使叶片对转子的附加不平衡量尽量小。工厂实际装配时,通过传统叶片排序方法装配叶片后,对转子的不平衡量进行测量,若不平衡量不满足要求,则通过对调叶片,使转子的不平衡量降低;若对调叶片后不平衡量依旧不满足要求,则重复对调叶片,直到转子剩余不平衡量满足要求为止。对调叶片的工作由平衡工人根据经验开展,难以找到最优的叶片对调方法,对调过程中也会有一定的试错,造成平衡工序的效率较低,而且最终不平衡量也仅是满足要求即可,不会考虑是否可以进一步降低不平衡量。
技术实现要素:9.本发明的主要目的是提出一种压气机转子叶片优化排序方法,提高寻优效率高,且使转子的剩余不平衡量满足要求并达到局部最优。
10.为实现上述目的,本发明提出一种压气机转子叶片优化排序方法,包括以下步骤:
11.步骤s1:确定叶片的初始排序,并计算初始排序时的转子不平衡量;
12.步骤s2:对初始排序进行多次对调,并计算出每次对调方案中的转子不平衡量,选取所有对调方案中转子不平衡量最小的对调方案作为新的优化排序;
13.步骤s3:根据步骤s2中得到新的优化排序,重补步骤s2的对调流程,以确定更新的优化排序,直至不能通过对调叶片实现转子不平衡量进一步减小为止,得到局部最优解。
14.优选的,在步骤s1中,将n片叶片按质量大小进行编号,质量最大为1号,最小为n号;1号叶片与2号叶片圆周相对安装,(n-1)号n号叶片圆周相对安装;1号与n号叶片相邻安装,以此类推,得到叶片的初始排序。
15.优选的,在步骤s2中,对初始排序进行对调的方法为:对初始排序u号位与v号位的叶片进行对调,其中u∈[1,2,
…
,n-1],v∈[u+1,u+2,
…
,n]。
[0016]
优选的,转子不平衡量的计算采用向量计算,在轮盘上标记1号榫槽位置,以发动机逆航向为x轴,径向通过1号槽所装配叶片的理论质心为y轴,z轴按坐标系右手定则确定,得到计算用坐标系。
[0017]
优选的,转子不平衡量的计算方法为:
[0018]
第i片叶片的质量为mi,其装配位置处的叶片理论质心回转半径为则该第i片叶片的质量矩向量为:
[0019][0020]
所有n片叶片对转子的附加不平衡量为:
[0021][0022]
轮盘的初始不平衡量记为则转子的剩余不平衡量为:
[0023][0024]
由于采用了上述技术方案,本发明的有益效果如下:
[0025]
本发明中,通过对初始排序进行多次对调,并计算出每次对调方案中的转子不平衡量,选取所有对调方案中转子不平衡量最小的对调方案作为新的优化排序,直至不能再通过对调叶片实现转子不平衡量进一步减小为止,得到局部最优解,形成了“叶片对调穷举法”。采用本发明所述排序方法,不需要设计交叉算子、变异算子,也不需要设计适应度函数,思路较为简单且易于理解,最终结果自动收敛,不需要人为设计迭代次数,且最终转子不平衡量精度满足工程实际需求。
附图说明
[0026]
为了更清楚地说明本发明实施例或现有技术中的技术方案,下面将对实施例或现有技术描述中所需要使用的附图作简单地介绍,显而易见地,下面描述中的附图仅仅是本发明的一些实施例,对于本领域普通技术人员来讲,在不付出创造性劳动的前提下,还可以根据这些附图示出的结构获得其他的附图。
[0027]
图1为本发明中叶片初始排序示意图;
[0028]
图2为本发明中叶片对调优化排序的仿真优化算法流程图;
[0029]
图3为本发明中计算用坐标系的确定示意图;
[0030]
图4为本发明中每轮叶片对调后转子不平衡量变化;
[0031]
图5为采用本发明实施例中1000种随机初始排序条件下的剩余不平衡量。
具体实施方式
[0032]
下面将结合本发明实施例中的附图,对本发明实施例中的技术方案进行清楚、完整地描述,显然,所描述的实施例仅仅是本发明的一部分实施例,而不是全部的实施例。基于本发明中的实施例,本领域普通技术人员在没有作出创造性劳动前提下所获得的所有其他实施例,都属于本发明保护的范围。
[0033]
一种压气机转子叶片优化排序方法,包括以下步骤:
[0034]
步骤s1:确定叶片的初始排序,并计算初始排序时的转子不平衡量;将n片叶片按质量大小进行编号,质量最大为1号,最小为n号;1号叶片与2号叶片圆周相对安装,(n-1)号n号叶片圆周相对安装;1号与n号叶片相邻安装,以此类推,得到叶片的初始排序;
[0035]
步骤s2:对初始排序进行多次对调,对调的方法为:对初始排序u号位与v号位的叶片进行对调,其中u∈[1,2,
…
,n-1],v∈[u+1,u+2,
…
,n];并计算出每次对调方案中的转子不平衡量,选取所有对调方案中转子不平衡量最小的对调方案作为新的优化排序;
[0036]
步骤s3:根据步骤s2中得到新的优化排序,重补步骤s2的对调流程,以确定更新的优化排序,直至不能通过对调叶片实现转子不平衡量进一步减小为止,得到局部最优解,即获得基于“叶片对调穷举法”的局部最优解。
[0037]
在步骤s2中,转子不平衡量的计算采用向量计算,在轮盘上标记1号榫槽位置,以发动机逆航向为x轴,径向通过1号槽所装配叶片的理论质心为y轴,z轴按坐标系右手定则确定,得到计算用坐标系(如图3所示)。计算时,因单级转子为单面动平衡,故不涉及x方向
的计算,质量矩向量通过分解到y、z方向进行计算。
[0038]
具体地,转子不平衡量的计算方法为:
[0039]
第i片叶片的质量为mi,其装配位置处的叶片理论质心回转半径为则该第i片叶片的质量矩向量为:
[0040][0041]
所有n片叶片对转子的附加不平衡量为:
[0042][0043]
轮盘的初始不平衡量记为则转子的剩余不平衡量为:
[0044][0045]
轮盘加工完毕后,其剩余不平衡量值及方向便已确定。叶片对转子的不平衡量影响主要靠叶片质量矩,即叶片质量与叶片质心回转半径的乘积。叶片质量矩需使用专门的设备进行称量,设备投入较大,称量效率较低,而叶片质量可通过天平称量,比较容易获得。考虑到同级叶片的质心回转半径差异较小,故通过称量的叶片质量与理论质心回转半径相乘,获得叶片质量矩。通过该方法计算得到的叶片质量矩与实际的叶片质量矩相差较小,不影响结果的准确性。
[0046]
本发明所提供的压气机转子叶片优化排序方法,仿真优化算法流程见图2所示。首先对叶片进行初始排序方法,并计算得到转子不平衡量,然后通过穷举所有的叶片对调方法,并计算出对调后的转子不平衡量,选取不平衡量最小的那一种对调方法对调叶片,将对调后的排序作为新的优化排序方法。得到新的优化排序方法后,重复前述流程,再次穷举所有的叶片对调方法,以确定更新的优化排序方法,直到再也不能通过对调叶片实现转子不平衡量进一步减小为止,获得基于“叶片对调穷举法”的局部最优解。
[0047]
通过采用上述压气机转子叶片优化排序方法某级压气机转子上进行了仿真计算验证,该级转子共101片叶片,将101片叶片按质量大小进行编号,质量最大为1号,最小为101号。1号叶片与2号叶片圆周相对安装,(n-1)号n号叶片圆周相对安装;1号与n号叶片相邻安装,以此类推,其中n∈[1,2,
…
,101]。叶片初始排序方法如图1所示。
[0048]
通过统计叶片质量平均值为3.121g,标准差为0.074g,叶片理论质心回转半径为187.85mm。通过软件生成一组服从上述正态分布的叶片随机质量。假设轮盘加工完毕后其剩余不平衡量为300g
·
mm,重点方向在y轴处。通过传统排序方法,转子不平衡量为299.5393g
·
mm。依据本发明所提供的压气机转子叶片优化排序方法,经过“叶片对调穷举法”流程(流程图2所示),每经过一轮叶片对调穷举寻优,转子不平衡量一步步减小,直至不能再通过对调叶片减小转子不平衡量为止,每轮叶片对调转子不平衡量逐渐减小(如图4所示),最终转子剩余不平衡量为0.0040g
·
mm。
[0049]
本发明的压气机转子叶片优化排序方法,即“叶片对调穷举法”,其逻辑简单、可编程性强。每轮叶片对调穷举次数因叶片数量n而异,为当叶片数为101时,每轮叶片对调
方法总数为5050,叶片对调一般不超过10轮即可获得局部最优解,故通过“叶片对调穷举法”通常只需要计算最多数万种排列组合方法即可获得局部最优解,可在数秒内计算得到结果,寻优效率极高,对计算设备的要求不高,且局部最优排序下转子不平衡量通常低于0.1g
·
mm,平衡精度极高。
[0050]
本发明所提供的压气机转子叶片优化排序方法形成的“叶片对调穷举法”,其最终优化排序跟初始排序相关,每种初始排序对应一种最终优化排序。图5为随机生成初始排序条件下的剩余不平衡量,随机初始排序共1000种。从计算结果可知,初始排序为传统排序时转子剩余不平衡量0.0040g
·
mm在随机1000种初始排序得到的最终剩余不平衡量中也是较优的结果,可见初始排序确定为传统排序合理,且与初始排序为随机排序相比,初始排序确定为传统排序可以保证每次采用“叶片对调穷举法”计算得到的结果唯一。
[0051]
本发明建立了转子叶片优化排序时的计算模型,确定了相关公式,且公式考虑了轮盘剩余不平衡量,可保证叶片对转子的附加不平衡量与轮盘相互抵消,实现转子不平衡量降低。
[0052]
本发明的转子叶片优化排序方法,即“叶片对调穷举法”,可在数秒内计算得到结果,寻优效率极高,对计算设备的要求不高,且局部最优排序下转子不平衡量通常低于0.1g
·
mm,平衡精度极高。
[0053]
本发明的转子叶片优化排序方法仿真优化算法流程简洁,逻辑简单,可编程性强,可根据该算法流程进行编程或封装成软件,直接应用到相关装配场景中。
[0054]
以上所述仅为本发明的优选实施例,并非因此限制本发明的专利范围,凡是在本发明的发明构思下,利用本发明说明书及附图内容所做的等效结构变换,或直接/间接运用在其他相关的技术领域均包括在本发明的专利保护范围内。