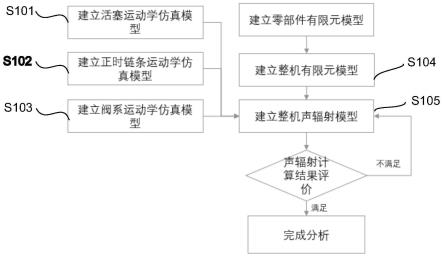
一种混动总成nvh仿真分析评价方法及装置
技术领域
1.本发明涉及nvh技术领域,特别是一种混动总成nvh仿真分析评价方法及装置。
背景技术:2.一般来说,新型混动总成开发项目由于许多数据未明确、未锁定的情况,所以混动总成的传统nvh分析方法,通常是分别对配气组件、曲轴组件、活塞组件和缸体缸盖进行建模分析,而且配气组件多数采用单阀系模型进行分析。这样的优点是模型简单,需求数据相对较少,建模和运算的时间短。缺点是在平台化混动总成改型开发项目中,未能在前期发现由于发动机结构和零部件变更带来的nvh性能问题,进而导致后期出现的问题解决效率低下。目前,对混动总成的评价还是主要依靠后期试验测试,这样在后期出现nvh问题的时候无法有效的溯源,会耗费更多的成本进行优化。混动总成是整车振动的激励源,如何在开发前期对混动总成nvh水平进行合理的预测及评价成为各大主机厂关注的重点。
3.面对日趋激烈的汽车行业竞争,很多企业纷纷开展了平台化建设,以缩短项目开发周期,降低研发成本。混动总成平台化改型是汽车平台化中重要的一部分,如何在保证产品性能和可靠性的同时,缩短开发周期,就显得尤为重要。汽车混动总成nvh分析是混动总成开发的一项重要内容,外在表现为分析和解决对汽车的噪声、振动、不平顺性的过程,其内涵则为在汽车混动总成性能、品质和成本间寻找平衡点的策略。因此如何构建混动总成整机nvh分析体系,成为现代汽车平台化混动总成改型项目nvh分析需要考虑的重要突破点。
4.基于混动总成平台化的性质,在其改型开发项目中,要求在不减弱混动总成动力性能、不变更本体零部件,仅更改外围结构和零部件。所以平台化发混动总成改型开发项目中的混动总成nvh仿真分析应该构建出一种和传统nvh仿真分析不同的思路和方法。这种方法应当在保证混动总成动力性能前提下,能模拟出混动总成结构和零部件变更带来的nvh问题,并提出有效的解决方案。
技术实现要素:5.本部分的目的在于概述本发明的实施例的一些方面以及简要介绍一些较佳实施例。在本部分以及本技术的说明书摘要和发明名称中可能会做些简化或省略以避免使本部分、说明书摘要和发明名称的目的模糊,而这种简化或省略不能用于限制本发明的范围。
6.鉴于上述和/或现有的混动总成中存在的问题,提出了本发明。
7.因此,本发明所要解决的问题在于如何提供一种能在混动总成开发前期就参与的nvh仿真分析评价方法。
8.为解决上述技术问题,本发明提供如下技术方案:
9.第一方面,本发明实施例提供了一种混动总成nvh仿真分析评价方法,其包括,
10.通过活塞运动学分析,建立活塞运动学仿真模型,采用燃烧分析结果作为在和激励,输入到所述活塞运动学仿真模型中,获取活塞运动学结果;
11.通过正时系统分析,建立正时链条运动学仿真模型,通过仿真正时系统的运动,获取正时链条运动学结果;
12.通过阀系运动学分析,建立阀系运动学模型,通过阀系运动学仿真,获取阀系运动学结果;
13.建立零部件模型并搭载为整机有限元模型,实现3d有限元网格划分;
14.将所述活塞运动学结果、正时链条运动学结果和阀系运动学结果作为激励,输入到所述整机有限元模型中,建立整机声辐射模型,预测整机在模拟激励力下的噪声辐射水平。
15.作为本发明所述混动总成nvh仿真分析评价方法的一种优选方案,其中:所述获取活塞运动学结果的具体步骤包括,
16.通过活塞运动学分析,建立活塞有限元模型;
17.对活塞进行分块,对活塞直接进行3d实体有限元网格划分;
18.通过对活塞施加前期燃烧分析得出的缸内爆发力,作为活塞运动的激励力,实现活塞动力学仿真;
19.获得活塞温度场结果和活塞运动学结果,并输出到曲轴运动学分析中。
20.作为本发明所述混动总成nvh仿真分析评价方法的一种优选方案,其中:所述获取正时链条运动学结果的具体步骤包括,
21.通过曲轴运动学中的曲轴运动,带动正时链条转动;
22.将正时链条的运动作为输入,完成正时系统运动学仿真模型的搭建;
23.对附件进行3d实体有限元网格划分;
24.获得正时链条运动学结果。
25.作为本发明所述混动总成nvh仿真分析评价方法的一种优选方案,其中:所述获取阀系运动学结果的具体步骤包括,
26.考虑气门落座力对振动噪声的贡献,建立阀系运动学模型;
27.通过阀系运动学仿真获取阀系激励,输入到所述阀系运动学模型;
28.获取阀系运动学结果。
29.作为本发明所述混动总成nvh仿真分析评价方法的一种优选方案,其中:所述网格划分包括:将模型导入有限元分析前处理软件,进行区域划分。
30.作为本发明所述混动总成nvh仿真分析评价方法的一种优选方案,其中:所述预测整机在模拟激励力下的噪声辐射水平包括,
31.对零部件进行网格划分,并进行模态计算;
32.将所述模态计算结果与实际测试获得的模态结果对标;
33.若仿真结果误差在5%以内,则认为零部件模态计算结果准确,实现模型校核。
34.作为本发明所述混动总成nvh仿真分析评价方法的一种优选方案,其中:所述预测整机在模拟激励力下的噪声辐射水平还包括,
35.结合所有关键零部件的有限元模型,搭载整机有限元模型;
36.对整机进行网格划分,并进行模态计算;
37.将所述模态计算结果与实际测试获得的模态结果对标;
38.若误差在10%以内,则认为整机模态计算结果准确,实现模型校核。
39.作为本发明所述混动总成nvh仿真分析评价方法的一种优选方案,其中:所述预测整机在模拟激励力下的噪声辐射水平还包括,根据iso标准,建立场点网络,在样机标定还未成型时仿真出声压级,评价整机的振动噪声水平。
40.第二方面,本发明实施例提供了一种混动总成nvh仿真分析评价系统,基于上述的混动总成nvh仿真分析评价方法,包括,
41.活塞运动学仿真模型建立模块,用于通过活塞运动学分析,建立活塞运动学仿真模型,采用燃烧分析结果作为在和激励,输入到所述活塞运动学仿真模型中,获取活塞运动学结果;
42.正时运动学仿真模型建立模块,用于通过正时系统分析,建立正时链条运动学仿真模型,通过仿真正时系统的运动,获取正时链条运动学结果;
43.阀系运动学仿真模型建立模块,用于通过阀系运动学分析,建立阀系运动学模型,通过阀系运动学仿真,获取阀系运动学结果;
44.整机有限元模型建立模块,用于建立零部件模型并搭载为整机有限元模型,实现3d有限元网格划分;
45.整机声辐射模型建立模块,用于将所述活塞运动学结果、正时链条运动学结果和阀系运动学结果作为激励,输入到所述整机有限元模型中,建立整机声辐射模型,预测整机在模拟激励力下的噪声辐射水平。
46.第三方面,本发明实施例提供了一种计算机设备,包括存储器和处理器,所述存储器存储有计算机程序,其中:所述处理器执行所述计算机程序时实现上述任一方法的步骤。
47.第四方面,本发明实施例提供了一种计算机可读存储介质,其上存储有计算机程序,其中:所述计算机程序被处理器执行时实现权利要上述任一方法的步骤。
48.本发明有益效果为:
49.1、一般的nvh测试需要在样机制造完成并完成40%标定的时候才可以进行,本发明可以在只有前期设计参数及数模的前提下,就较为精确的预测到整机噪声辐射水平,相比于等待样机出来后再进行噪声测试,更具有前瞻预判性,更能对混动总成的nvh进行有效控制;
50.2、现有技术多采用单阀系进行仿真分析,本发明采用了考虑凸轮轴不同轴段的多阀系仿真分析;现有技术是分别对配气组件、活塞组件、曲轴组件进行独立的nvh仿真分析,本发明为对上述三大组件及其相互连接的轮系、缸体缸盖及其附带的进排气歧管,考虑组件间载荷传递以及由于结构和零部件变更的整机集成nvh仿真分析,并且依靠活塞运动学、曲轴运动学、阀系运动学和正时运动学将发动机上大部分激励涵盖进去,可以使nvh仿真预测更加接近实际水平。
附图说明
51.为了更清楚地说明本发明实施例的技术方案,下面将对实施例描述中所需要使用的附图作简单地介绍,显而易见地,下面描述中的附图仅仅是本发明的一些实施例,对于本领域普通技术人员来讲,在不付出创造性劳动性的前提下,还可以根据这些附图获得其它的附图。其中:
52.图1为混动总成nvh仿真分析评价方法的流程图。
53.图2为不带vvt的凸轮轴各缸不同轴段的变形量。
54.图3为多阀系仿真分析模型图。
55.图4为各缸凸轮轴对气门挺柱的作用力。
56.图5为各缸气门对阀座的冲击力。
57.图6为凸轮轴各轴段对轴承座的垂向载荷。
58.图7为凸轮轴各轴段对轴承座的横向载荷。
59.图8为样机1#第四缸异常磨损的挺柱。
60.图9为优化后的挺柱受力。
61.图10为样机2#第四缸未异常磨损的挺柱。
62.图11为混动专用发动机整机nvh集成仿真分析模型。
63.图12为优化前的整机振动加速度云图。
64.图13为优化后的整机振动加速度云图。
65.图14为优化前的曲轴前端扭振。
66.图15为优化后的曲轴前端扭振。
67.图16为样机1#前端声压功率曲线。
68.图17为样机2#前端声压功率曲线。
具体实施方式
69.为使本发明的上述目的、特征和优点能够更加明显易懂,下面结合说明书附图对本发明的具体实施方式做详细的说明。
70.在下面的描述中阐述了很多具体细节以便于充分理解本发明,但是本发明还可以采用其他不同于在此描述的其它方式来实施,本领域技术人员可以在不违背本发明内涵的情况下做类似推广,因此本发明不受下面公开的具体实施例的限制。
71.其次,此处所称的“一个实施例”或“实施例”是指可包含于本发明至少一个实现方式中的特定特征、结构或特性。在本说明书中不同地方出现的“在一个实施例中”并非均指同一个实施例,也不是单独的或选择性的与其他实施例互相排斥的实施例。
72.实施例1
73.参照图1,为本发明第一个实施例,该实施例提供了一种混动总成nvh仿真分析评价方法,在只有前期设计参数及数模的前提下,就可以较为精确的预测到整机噪声辐射水平,具体步骤包括:
74.s101:通过活塞运动学分析,建立活塞运动学仿真模型,采用燃烧分析结果作为在和激励,输入到所述活塞运动学仿真模型中,获取活塞运动学结果。
75.应说明的是,在对某混动专用发动机的性能开发过程中,首先通过活塞运动学分析,建立活塞有限元模型,对活塞进行分块,对活塞直接进行3d实体有限元网格划分。
76.其中网格划分包括:将活塞模型导入有限元分析前处理软件,对活塞进行分区域划分。直接3d网格划分可以保证后续活塞应力计算的精度。
77.进一步的,通过给活塞施加前期燃烧分析得出的缸内爆发压力,作为活塞运动的激励,实现活塞运动学仿真,最终获得活塞温度场结果及活塞运动学输出给到曲轴运动学分析中。
78.s102:通过正时系统分析,建立正时链条运动学仿真模型,通过仿真正时系统的运动,获取正时链条运动学结果。
79.应说明的是,在正时系统分析中,通过曲轴运动学中的曲轴运动,带动正时链条转动,以此作为正时链条的输入,对正时系统进行模型搭建,对链条及导板等附件进行3d网格划分,最终仿真出正时链条的运动学结果。
80.s103:通过阀系运动学分析,建立阀系运动学模型,通过阀系运动学仿真,获取阀系运动学结果。
81.应说明的是,同样在阀系仿真中,也能通过阀系运动学仿真获得阀系激励力。
82.s104:建立零部件模型并搭载为整机有限元模型,实现3d有限元网格划分。
83.应说明的是,同时混动专用发动零部件进行网格划分,并进行模态计算,与实际测试获得的模态结果对标。确保仿真结果误差在5%以内,则认为零部件模态计算结果准确,实现模型校核。
84.进一步的,结合所有关键零部件的有限元模型,搭载整机有限元模型,同样与实际测试的模态测试结果对标,误差在10%以内,认为整机模态计算结果准确,实现模型校核。
85.s105:将活塞运动学结果、正时链条运动学结果和阀系运动学结果作为激励,输入到整机有限元模型中,建立整机声辐射模型,预测整机在模拟激励力下的噪声辐射水平。
86.应说明的是,混动总成整机振动和噪声的激励主要来源于燃烧系统、配气组件、活塞组件、曲轴组件四大组件运行产生的振动和噪声。混动总成nvh的表现通常来源于配气组件、活塞组件、曲轴组件在燃烧系统的驱动下的综合表现。并且配气组件、活塞组件、曲轴组件这三大运动组件之间也有着相互传递的载荷。
87.应说明的是,将这些运动学模型激励加载到整机有限元模型上,搭载整机声辐射仿真模型,根据iso标准,建立场点网格,实现在样机标定还未成型的时候模拟整机的声压级的功能,能够更好的评价整机的振动噪声水平,实现前期的预测,避免后期样机锁定后造成的更改风险。
88.进一步的,本实施例还提供一种混动总成nvh仿真分析评价系统,包括:
89.活塞运动学仿真模型建立模块201,用于通过活塞运动学分析,建立活塞运动学仿真模型,采用燃烧分析结果作为在和激励,输入到所述活塞运动学仿真模型中,获取活塞运动学结果;
90.正时运动学仿真模型建立模块202,用于通过正时系统分析,建立正时链条运动学仿真模型,通过仿真正时系统的运动,获取正时链条运动学结果;
91.阀系运动学仿真模型建立模块203,用于通过阀系运动学分析,建立阀系运动学模型,通过阀系运动学仿真,获取阀系运动学结果;
92.整机有限元模型建立模块204,用于建立零部件模型并搭载为整机有限元模型,实现3d有限元网格划分;
93.整机声辐射模型建立模块205,用于将所述活塞运动学结果、正时链条运动学结果和阀系运动学结果作为激励,输入到所述整机有限元模型中,建立整机声辐射模型,预测整机在模拟激励力下的噪声辐射水平。
94.本实施例还提供一种计算机设备,适用于混动总成nvh仿真分析评价方法的情况,包括:存储器和处理器;存储器用于存储计算机可执行指令,处理器用于执行计算机可执行
指令,实现如上述实施例提出的混动总成nvh仿真分析评价方法。
95.该计算机设备可以是终端,该计算机设备包括通过系统总线连接的处理器、存储器、通信接口、显示屏和输入装置。其中,该计算机设备的处理器用于提供计算和控制能力。该计算机设备的存储器包括非易失性存储介质、内存储器。该非易失性存储介质存储有操作系统和计算机程序。该内存储器为非易失性存储介质中的操作系统和计算机程序的运行提供环境。该计算机设备的通信接口用于与外部的终端进行有线或无线方式的通信,无线方式可通过wifi、运营商网络、nfc(近场通信)或其他技术实现。该计算机设备的显示屏可以是液晶显示屏或者电子墨水显示屏,该计算机设备的输入装置可以是显示屏上覆盖的触摸层,也可以是计算机设备外壳上设置的按键、轨迹球或触控板,还可以是外接的键盘、触控板或鼠标等。
96.本实施例还提供一种存储介质,其上存储有计算机程序,该程序被处理器执行时实现如上述实施例提出的实现混动总成nvh仿真分析评价方法。
97.本实施例提出的存储介质与上述实施例提出的数据存储方法属于同一发明构思,未在本实施例中详尽描述的技术细节可参见上述实施例,并且本实施例与上述实施例具有相同的有益效果。
98.实施例2
99.参照图2~17,为本发明第二个实施例,该实施例提供了一种混动总成nvh仿真分析评价方法,为了验证本发明的有益效果,通过仿真实验进行科学论证。
100.以1.5升混动专用发动机平台为例,原机型取消了进排气凸轮轴连接的dvvt、更改了前端轮系的链条、进排气歧管的结构。因此,平台化混动总成整机nvh集成仿真分析的任务,就是要模拟出混动专用发动机在上述发动机结构和零部件变更后,发动机出现的nvh性能问题,并提出有效的解决方案。
101.对于取消进排气凸轮轴dvvt来说,其影响主要是改变了在缸压作用下,气门开启的相位变化所带来的凸轮轴、挺柱、气门、阀座、轴承相互之间的冲击力变化;对于更改前端轮系的静音链条为非静音链条来说,其影响主要是改变了轮系之间的驱动扭矩振动,该驱动扭矩振动会传递给曲轴前端,进而影响曲轴皮带轮的扭矩振动;对于进排气歧管结构的改变来说,主要是热分布的改变而影响缸体变形量,进而影响活塞运动,活塞运动又反过来影响缸体的振动和敲击。
102.考虑凸轮轴在长度方向上不同轴段刚度、和取消进排气dvvt的影响的情况下,先应用abaqus先对不带vvt的凸轮轴进行仿真分析,得到凸轮轴各缸不同轴段的变形量,转化为刚度,然后代入ricardo的valdyn模型进行无dvvt的仿真分析。通过对n15机型进行多阀系建模仿真分析,得出各缸气门对阀座的不同冲击力、各缸凸轮轴轴承座受到的载荷。
103.如图2~8所示,从结果中可以看出,各缸凸轮轴对气门挺柱的作用力都不同,且第四缸的挺柱受力已经超过了评价指标。从后期样机1#(优化前)的试验结果来看,第四缸的挺柱确实是受到了异常的磨损。其他各缸对气门阀座的冲击力、凸轮轴各轴段对轴承座的垂向和横向载荷也显示出了不同的数值。
104.如图9和图10所示,在保证混动总成动力性能的前提下,通过重新调整气门型线和气门弹簧力的大小后,重新代入多阀系模型进行仿真分析,结果得到各缸挺柱受力得以有效减小,低于评价指标值,后期样机2#(优化后)的实验结果显示,第四缸挺柱没有异常的磨
损。解决了取消dvvt后,凸轮轴对第四缸气门挺柱的过大作用力造成的异常磨损问题。并且能够预见到各缸气门对阀座的不同的冲击力、各轴承座的受力情况。
105.前端轮系的驱动扭矩振动传递到曲轴,与曲轴本身的扭矩振动共同作用于缸体上的曲轴轴承座;进排气歧管的热分布对缸体缸盖的变形量也有影响,进而影响活塞运动,活塞运动又反过来影响缸体的振动和敲击。基于上述原因,利用ricardo的valdyn、fearce、engdyn软件建立了包含进排气多阀系、前端轮系、曲轴、缸体缸盖热变形、悬置系统于一体的整机nvh集成仿真分析模型,使得凸轮轴驱动扭矩经过前端轮系传递到曲轴前端,与曲轴本身的扭矩共同作用,结果输出曲轴皮带轮的扭矩振动。
106.应说明的是,发动机整机nvh评估内容,主要涉及曲轴扭振、整机振动、1米声压级/声功率、声压/声强等。
107.其中发动机整机声压需要满足五个面的评价标准,分析每个面的声压值情况,由声压曲线、1/3倍频程、colormap图得到噪声频率分布及成分大小,对发动机振动峰值频率成分及对应转速进行分析,找出峰值贡献频率范围,从而排查问题零部件解决问题。
108.如图11所示,混动专用发动机nvh集成仿真分析结果中,发现发动机前端盖中下部分在4200rpm附近有比较大的振动加速度。查看曲轴组件仿真分析结果发现发动机在4200rpm 4阶次时曲轴的扭振也有个小波峰,其幅值接近评价指标。因此,基本锁定了问题的症结点——需要反过来调整曲轴组件的参数,以降低曲轴前端扭振,从而使得发动机前端盖在该工况下振动加速度减小。在后期试验中,样机1#(未优化)该测试点的1米声功率曲线在4100~4300rpm范围也出现了一个小波峰,而样机2#(优化后)该测试点的1米声压功率曲线在4100~4300rpm范围的小波峰降低。
109.应说明的是,以上实施例仅用以说明本发明的技术方案而非限制,尽管参照较佳实施例对本发明进行了详细说明,本领域的普通技术人员应当理解,可以对本发明的技术方案进行修改或者等同替换,而不脱离本发明技术方案的精神和范围,其均应涵盖在本发明的权利要求范围当中。