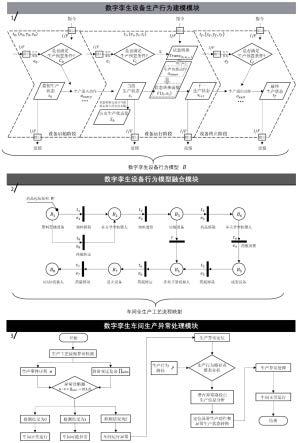
1.本发明属于电子工程和计算机科学领域,具体涉及一种基于模型融合的数字孪生异常处理方法。
背景技术:2.数字孪生车间是一种新的制造范式,由信息和制造技术的深度融合驱动。数字孪生车间的构建被认为是信息和物理世界之间双向映射和互动的潜在有效方法。同时数字孪生模型是数字孪生车间功能实现基础。然而,目前的数字孪生模型未能准确描述设备在整个生产生命周期中的生产行为和生产状态之间的演变过程;同时,在数字孪生建模中没有充分考虑设备生产行为之间基于生产逻辑的相互联系;这导致在全生产生命周期内,数字孪生车间无法对物理设备生产行为进行精准描述和对物理车间进行全生产工艺流程的高保真映射。同时,基于生产工艺流程映射,可以检测生产异常是否发生。再通过对设备行为模型的异常生产动作和异常生产状态转换的定位,从而明确异常源头。为此,本发明提出了一种基于模型融合的数字孪生异常处理方法,即首先构建设备行为模型,然后利用标签petri网技术融合设备行为模型。因此,除了在生产全生命周期内准确描述设备生产行为外,数字孪生车间还实现了对物理车间的全生产工艺流程映射。这个映射包括了从设备到车间的多层级映射和从生产行为到生产规则的多维度映射。再基于多层级和多维度映射,实现对生产异常的检测和定位。
技术实现要素:3.为解决上述技术问题,本发明提供一种基于模型融合的数字孪生异常处理方法,该方法涵盖了数字孪生设备生产行为建模模块设计、数字孪生设备行为模型融合模块设计和数字孪生车间生产异常处理模块设计,能够实现数字孪生车间对设备生产行为的精准描述、数字孪生车间对物理车间全生产工艺流程映射和数字孪生车间生产异常处理。
4.本发明解决其技术问题采取的技术方案为:基于模型融合的数字孪生异常处理方法,包括如下步骤:
5.步骤一、设计数字孪生设备生产行为建模模块,所述数字孪生车间设备生产行为建模模块包括设备生产动作构建功能、设备生产状态构建和设备行为模型通信接口构建功能;该模块依次按照这三个功能的构建流程完成设备行为模型建模;设备生产动作和生产状态共同构成了设备的生产行为路径,用于描述设备在其生产全生命周期内的生产动作和状态的交替演进过程;对于设备内部生产,设备行为模型通信接口用于生产事件的传递;对于设备外部,设备在生产过程中通过通信接口与其他设备进行通信、接受上层生产系统的指令并做出反馈;行为路径和通信接口共同构成了设备的行为模型,用于精准描述设备的生产行为;
6.步骤二、设计数字孪生设备行为模型融合模块,通过标签petri网技术,将车间生产设备的行为模型按照生产逻辑规则进行融合,用于实现数字孪生车间在全生产工艺流程
上对物理车间的高保真虚拟映射;
7.步骤三、设计数字孪生车间生产异常处理模块,所述数字孪生车间生产异常处理模块包括异常检测功能和异常定位功能;该模块依次按照这两个功能的执行流程完成车间生产异常处理,首先利用标签petri网检测是否出现异常,再通过聚类分析生产路径点和分析潜在异常生产路径点所包含的生产信息,定位设备行为模型的异常生产动作和异常生产状态转换,之后采取相应异常处理方法使得车间生产恢复正常。
8.所述步骤一,设计数字孪生设备生产行为建模模块,具体实现如下:
9.(1.1)构建设备生产动作:
10.在公式(1)中,a表示从a
entry
,
…
,am到a
exit
的连续生产动作的集合;公式(2)对生产动作ai,i∈(1,m),进行了详细表达;<si,s
i+1
>表示从生产状态si到s
i+1
的生产状态转换;ty表示生产动作类型,ty={entry,inner,exit},其中entry是生产进入动作a
entry
的标识符,其激活设备生产并使其进入运行阶段;inner是内部生产动作的标识符,设备内部生产动作包括a1,a2,
…
,am,为在设备运行时执行的动作;exit是生产退出动作a
exit
的标识符,其终止当前设备生产并使其进入终止阶段;tm是生产动作发生时间;posn是生产动作发生在虚拟空间的位置坐标(x,y,z):
11.a={a
entry
,a1,a2,...,am,...,a
exit
}
ꢀꢀ
(1)
12.ai={<si,s
i+1
>,ty,tm,posn}
ꢀꢀ
(2)
13.在公式(3)中,c表示从c0,
…
,cm到cf的预置条件的集合,其中预置条件cf对应于设备的最终生产状态;预置条件由设备生产全生命周期内不同阶段的运行机制、生产规则和制造约束信息等因素决定;ci是c的第i个预置条件,用公式(4)定量表示ci;在公式(4)中,是以属性值atri为自变量的运算函数;atri包括来自传感器的监测值、反馈值和操作面板的输入值;和数值常数β之间的运算关系由关系运算符op表示,op∈{=,≠,>,≥,<,≤};在公式(5)中,e'表示从e0,...,en到ef的生产事件集合,其中ef是设备的最终生产事件;如果atri满足ci,如公式(6)所示,生产事件ei可以触发生产状态转换同时在这个过程中产生相应的生产动作ai:
14.c={c0,c1,c2,...,cm,...,cf}
ꢀꢀ
(3)
[0015][0016]
e'={e0,e1,e2,...,en,...,ef}
ꢀꢀ
(5)
[0017][0018]
(1.2)构建设备生产状态:
[0019]
在公式(7)中,s为设备生产状态的集合;其中,s0、si和s
i+1
分别代表初始生产状态、当前生产状态和下一生产状态;sf为最终生产状态,表示负责当前生产工序的设备已进入终止阶段,负责下一工序的设备准备启动运行;sh为历史状态的集合;如公式(8)所示,当生产状态转换发生时,状态转换函数f(si,ai)被激活以产生s
i+1
;同时,在状态转换完成后,si将结束并记录在sh中;通过回溯设备的生产历史状态,可以对生产过程进行监控和历史数据分析,以便及时进行生产异常检测和定位:
[0020]
s={s0,si,s
i+1
,sf,sh}
ꢀꢀ
(7)
[0021]
f(si,ai)=s
i+1
ꢀꢀ
(8)
[0022]
(1.3)构建数字孪生设备行为模型:
[0023]
公式(9)描述了设备e的生产行为模型b由生产行为路径p和通信接口i/f组成:
[0024]
1)生产行为路径:在设备生产全生命周期中,s和a构成了公式(10)中的生产行为路径p(s,a)。p(s,a)表示了设备生产从启始阶段到终止阶段的完整生命周期中的生产状态和生产动作之间的演变推进过程;
[0025]
2)通信接口:如公式(9)所示,行为模型配备了通信接口i/f;在公式(11)中,通信接口i/f为包含从int1到int
p
的通信接口的集合。
[0026]
b=(e,p,i/f)
ꢀꢀ
(9)
[0027]
p(s,a)={s0,a
entry
,...,si,a
i+1
,s
i+1
,...,a
exit
,sf}
ꢀꢀ
(10)
[0028]
i/f={int1,int2,int3,...,int
p
}
ꢀꢀ
(11)
[0029]
所述步骤二,设计数字孪生设备行为模型融合模块,具体实现如下:
[0030]
为设备行为模型组装所涉及到的元素。是从b1到bm的设备行为模型集合;t为包含从t1到tn的生产变迁集合,其表示不同生产设备之间工件的进给过程;在公式(13)中,t被分为两个不相交子集to和tu;to表示no个可观测的生产变迁集合;tu表示nu个不可观测的生产变迁集合;在公式(14)和(15)中,标签函数ξ:t
→
e'∪{δ}用来把生产事件集e'中的生产事件e分配给生产变迁t,t∈t;不可观测的生产变迁t对应着不可观测事件δ,t∈t;如公式(16)所示,w为包含从w0到w
p
的向量集合,向量wi表示在不同车间生产阶段中每台设备上正在加工的工件或物料的数量。
[0031]
t={t1,t2,t3,...,tn}
ꢀꢀ
(12)
[0032]
t=t0∪tuꢀꢀ
(13)
[0033][0034][0035]
w={w0,w1,w2,...,w
p
}
ꢀꢀ
(16)
[0036]
所述步骤三,设计数字孪生车间生产异常处理模块,具体实现如下:
[0037]
(3.1)车间生产异常检测:
[0038]
在公式(17-20)中,可观测的生产变迁集合to包括两个子集t
o,reg
和t
o,abn
;与常规可观测变迁集合t
o,reg
不同,与异常可观测变迁集合t
o,abn
中的异常变迁相关的生产事件在特定生产场景下导致生产异常;不可观测的生产变迁集合tu包括两个互不相交的子集t
u,reg
和t
u,abn
;t
u,reg
表示常规的不可观测的变迁集合;t
u,abn
表示异常的不可观测的变迁集合;t
abn
为包含n
abn
个异常变迁的集合,由t
o,abn
和t
u,abn
共同构成。异常的生成行为路径p(s,a)由包含n
abn
个异常变迁的集合t
abn
所反映,具体的生产异常类型由到所表示的不同异常类来表示,异常类归入公式(20)所表示的异常检测集π
abn
:
[0039]
to=t
o,reg
∪t
o,abn
ꢀꢀ
(17)
[0040]
tu=t
u,reg
∪t
u,abn
ꢀꢀ
(18)
[0041]
t
abn
=t
o,abn
∪t
u,abn
ꢀꢀ
(19)
[0042][0043]
在公式(22)和(23)中,σ表示车间生产工艺流程中连续生产事件集e1到er;σ和п
abn
共同构成检测函数δ。基于转化后的标签petri网的路径约束关系,检测函数δ利用路径约束规则检测车间是否发生异常;基于检测函数δ的输出结果的分析,得到车间检测结果如下:
[0044]
σ=e1...erꢀꢀ
(21)
[0045]
δ:σ
×
п
abn
→
{0,1,2}
ꢀꢀ
(22)
[0046]
·
δ(σ,п
abn
)=0。当δ的计算结果为0时,表示车间生产事件流中不存在异常,即数字孪生车间运行正常。
[0047]
·
δ(σ,п
abn
)=1。当δ的计算结果为1时,表示车间生产事件流中可能异常,即数字孪生车间有可能发生异常。
[0048]
·
δ(σ,п
abn
)=2。当δ的计算结果为2时,表示车间生产事件流已经出现了异常,即数字孪生车间出现了生产异常。
[0049]
(3.2)异常定位:
[0050]
在检测到数字孪生车间生产出现异常后,需要通过定位设备行为模型中导致生产行为路径偏移既定正常生产路径的异常生产动作和异常状态转换来确定车间生产异常的源头。
[0051]
首先根据异常生产变迁t
abn
在标签petri网中发生的位置来确定包含潜在异常生产行为路径点的设备行为模型b。通过异常聚类算法聚类分析之前所确定的设备行为模型的生产行为路径点。基于聚类算法的分析结果,比较b的历史行为路径p(s,a),确定异常的生产行为路径点。
[0052]
其次基于异常行为路径点所包含生产信息,对其中的生产事件、生产状态、生产时间和位置坐标之间的生产逻辑关系进行分析,实现对异常生产行为a
abn
和异常生产状态转换trans
abn
的定位。
[0053]
最后在完成对异常生产动作和异常生产状态的定位后,将导致生产异常的生产事件标记为异常生产事件e
abn
,并将其作为历史异常生产事件集合中的一个新元素进行存储记录。如公式(23)所示,历史异常生产事件集合用符号e'
abn
表示,e'
abn
由已标记异常生产事件e
1abn
到e
sabn
组成。如果e
abn
与e'
abn
中的已标记异常生产事件相匹配,历史异常处理经验可以提供相应的参考。基于生产全生命周期内对设备生产行为的描述,通过分析a
abn
、trans
abn
和e
abn
,可以推断出导致数字孪生车间生产出现异常的原因。因此,可以根据异常的原因采取具体的异常处理方法,使得物理车间生产恢复正常。
[0054][0055]
本发明与现有技术相比的优点在于:传统的数字孪生车间建模中的数字孪生模型未能准确描述设备在整个生产生命周期中的生产行为和生产状态之间的演变过程;在数字孪生车间建模中没有充分考虑设备生产行为之间基于生产逻辑的相互联系;这导致在全生产生命周期内,数字孪生车间无法对物理设备生产行为进行精准描述和对物理车间进行全生产工艺流程的高保真映射。同时,数字孪生异常处理的过程中无法实现对生产异常源头的精准定位,从而无法实现有效的异常处理。本发明借助数字孪生技术并结合车间整个生产生命周期内的生产规则逻辑和具体每个设备的生产动作与状态的演进规律,首先构建设备行为模型,车间生产设备的行为模型由设备生产行为路径和进行内外部的通信接口组成;然后利用标签petri网技术,将设备行为模型融合。同时,基于数字孪生车间对物理车间
的多层级多维度映射,实现了对车间生产异常源头的精准定位。因此,本发明在设备的整个生产生命周期内对其生产行为进行准确描述,保证了数字孪生车间对物理车间全生产工艺流程映射,同时还实现了有效的生产异常处理。
附图说明
[0056]
图1为本发明的一种基于模型融合的数字孪生异常处理方法流程框图。
具体实施方式
[0057]
为了使本发明的目的、技术方案及优点更加清楚明白,以下结合附图及实施例,对本发明进行进一步详细说明。应当理解,此处所描述的具体实施例仅用以解释本发明,并不用于限定本发明。此外,下面所描述的本发明各个实施方式中所涉及到的技术特征只要彼此之间未构成冲突就可以相互组合。
[0058]
本发明涉及一种基于模型融合的数字孪生异常处理方法,设计了数字孪生设备生产行为建模模块、数字孪生设备行为模型融合模块和数字孪生车间异常处理模块,能够对车间生产设备在整个生产生命周期内的生产行为进行准确描述,保证了数字孪生车间对物理车间全生产工艺流程映射,还能实现有效的异常处理。
[0059]
如图1所示,本发明的基于模型融合的数字孪生异常处理方法具体包括如下步骤:
[0060]
步骤一、设计数字孪生设备生产行为建模模块,具体实现如下;
[0061]
①
以药物包装瓶生产车间中的agv(automatic guided vehicle)自动搬运机器人为例,该模块首先对agv自动搬运机器人的在药物包装瓶生产车间中生产动作进行构建。对于agv的某个生产状态转换,如果生产事件满足预置条件,该生产状态转换就会被触发,对应产生相应的生产动作。agv生产动作分为三类,即生产进入动作、生产内部动作和生产退出动作;生产进入动作激活之前处于休眠状态的agv进行运行状态;生产内部动作是agv运行时的生产动作;生产退出动作终止agv运行并进入休眠状态。例如,如果agv的属性值“剩余电量”满足预置条件“大于等于160ah”的要求,那么生产事件“物料搬运”就会触发agv的生产状态从休眠状态转换到运行状态;在这个状态转换的过程中,avg的生产进入动作将会被执行。
[0062]
②
该模块其次对agv的生产状态进行构建。agv的生产状态分为五类,初始生产状态、当前生产状态、下一生产状态、历史生产状态和最终状态;初始生产状态表示agv刚开始运行时的状态;当前生产状态将会在生产状态转换中的状态转换函数的触发下产生下一生成状态,在状态转换完成时设备的当前状态被终止,同时被存储记录在历史状态集中;通过回溯设备的生产历史状态,生产过程监控和数据分析可用于快速纠正agv在生产运行中错误和生产运行过程;终止状态意味着当前agv所负责工序的结束并且agv进入休眠状态,也意味负责下一工序的设备的生产开始。avg的生产进入动作将会被执行,当前agv的休眠状态在转换为运行状态后,其最初的休眠状态将作为历史状态被存储和记录在历史状态集中。最终,在agv负责的生产工序结束后,agv的终止状态将会被触发。
[0063]
③
该模块在完成对agv的生产全生命周期的生产动作和状态构建后,就可以得到agv的生产行为路径,它精准描述了agv在其整个生产生命周期内生产动作和生产状态的交替演进规律。在完成了agv生产行为模型的生产行为路径的构建后,就是为其行为模型配置
通信接口。在agv行为模型内部,接口被部署用来传递生产事件。在agv行为模型外部,接口响应药物包装生产车间上层生产指令并提供相应的反馈,从而使agv行为模型与其他设备行为模型相互连接。agv生产行为路径和通信接口共同组成了可以用于agv全生产生命周期精准描述的生产行为模型。
[0064]
步骤二、设计数字孪生设备行为模型融合模块,具体实现如下:
[0065]
在药品包装生产车间的生产工艺流程中,b1、b3、b5和b7分别为原料存储设备、切削设备、成型设备和退火设备的数字孪生行为模型。b1、b3、b5和b7主要负责完成药品包装加工的各种加工处理工艺。物料w为药品包装的原料。w在各药品包装加工、处理设备之间的流转由agv、多关节型机器人和选择顺应性装配机器手臂(selective compliance assembly robot arm,scara)完成。加工完成的药品包装将被scara移入托盘中等待后续处理。多关节型机器人的行为模型分别由b2、b4、b6表示。scara的行为模型由b8表示。同时b1与b3之间的物料转运可以直接由agv完成。车间中各设备间的物料转运过程与生产变迁t1到t8相对应,每个生产变迁都对应着e1到e8中的一个具体的生产事件,如物料抓取、物料进给等等。异常不可观变迁ε对应着agv将物料由切削设备b3转运到多关节型机器人b6的异常生产事件。物料将会在基于标签petri网所构建的车间生产工艺流程中进行流转,通过生产变迁对应的生产事件驱动负责相应生产工艺的设备相继进行生产加工。负责上一生产工艺的设备完成其生产全生命周期的生产任务后,相应的生产变迁将会触发。该生产变迁对应的生产事件会驱动负责下一生产工艺的设备生产全生命周期的开始。
[0066]
步骤三、设计数字孪生车间生产异常处理模块,具体实现如下;
[0067]
(3.1)首先确定转化后标签petri网的子网,并基于路径约束关系对子网的特定路径之间约束关系进行分析,可以推导出在生产事件流作用下的检测函数δ的计算结果。当δ的计算结果为2时,说明常不可观变迁ε被触发了,即车间生产出现了异常。
[0068]
(3.2)在检测到异常发生后,对agv设备行为模型的生产行为路径点进行聚类分析。确定潜在异常路径点。通过对agv行为模型异常路径点所包含的生产信息进行分析,可以确定异常物料转运动作和相应的异常生产状态转换。在定位异常源头后,可以采取相应的异常处理方法使得车间恢复正常生产。
[0069]
综上所述,本发明公开了一种基于模型融合的数字孪生异常处理方法,包括对以下模块的设计:数字孪生设备生产行为建模模块,数字孪生设备行为模型融合模块和数字孪生车间生产异常处理模块。建模和融合模块能够在一定程度上对车间生产设备在整个生产生命周期内的生产行为进行准确描述外,还保证了数字孪生车间对物理车间全生产工艺流程映射,这个映射包括了从设备到车间的多层级映射和从生产行为到生产规则的多维度映射。异常处理模块先通过标签petri网检测车间是否出现异常,再通过分析生产路径点信息定位异常生产动作和异常生产状态转换,最后采取相应异常处理方法使得车间生产恢复正常。
[0070]
本发明说明书中未作详细描述的内容属于本领域专业技术人员公知的现有技术。
[0071]
以上所述仅是本发明的优选实施方式,应当指出,对于本技术领域的普通技术人员来说,在不脱离本发明原理的前提下,还可以做出若干改进和润饰,这些改进和润饰也应视为本发明的保护范围。