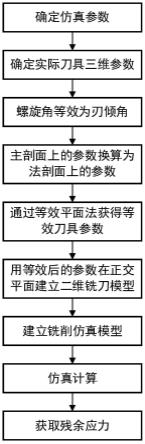
1.本发明属于金属切削加工过程中残余应力仿真的技术领域,具体涉及一种考虑螺旋角的二维连续铣削残余应力仿真方法,适用于各类材料的已加工表面铣削残余应力仿真。
背景技术:2.对于原发失效将会导致灾难性事故的发动机寿命限制件,适航条款far 33.70要求执行“三大计划”来保证其在寿命期内的完整性。其中,工程计划提出了完备的安全性评估流程,是制造计划制定和批准的基础,而制造计划保证了工程计划要求的属性和假设持续有效。然而,如何通过工程计划与制造计划的关联,确定关键的制造工艺参数,获得工艺参数及其控制的零部件属性对限寿件安全性的影响,缺乏必要的研究,制约着民用航空发动机的适航取证。
3.33.70条款的咨询通告中明确提出残余应力场影响着零部件的寿命,是制造过程中需要控制的零部件属性。而金属切削在加工过程中会引入加工残余应力,加工残余应力是衡量工件加工表面质量的一项重要指标,并对工件的材料静态强度和疲劳强度、脆性破坏和腐蚀开裂有严重影响,进而影响工件的疲劳寿命。另外,残余应力还对零件的尺寸精度及稳定性有影响,当零件受到外力、振动等外力作用时,或者环境的温度等其他因素发生变化时,由于作用应力与残余应力的相互作用,使零件的某些局部发生塑性变形,截面内的残余应力将重新分布,当外作用去除或者环境稳定时零件就要发生变形。零件在使用的过程中残余应力将发生松弛,所以残余应力影响着仪器仪表元件以及传感器等精密零件的尺寸稳定性,直接影响到零件的使用性能。鉴于残余应力的形式、大小、分布对零件的性能有重要影响,所以对加工后零件表面的残余应力分布规律进行定量分析具有重要意义。然而现有的研究主要集中在车削磨削残余应力,研究铣削残余应力的多数将铣削简化为单齿切削后的残余应力,实际研究工程应用中所需的铣削已加工完成面残余应力的较少,考虑到铣削加工的特性,有限元三维仿真时间成本巨大,迫切的需要建立一种考虑螺旋角的二维连续铣削残余应力仿真方法。
4.目前现有主流的铣削仿真过程主要有三维和二维仿真,其中三维仿真时间成本过高,迭代时间长,浪费计算资源;现有的二维铣削仿真方法,主要有三种方式:第一类是通过将变厚度的切削层简化为等效厚度后进行正交切削仿真,有等效均匀厚度切削模型、等效斜面工件切削模型、等效刀具斜向切削模型等,这类方式没有考虑到铣削过程是一种间歇多次切削的过程,也没有考虑到铣刀螺旋角对切削的影响,该类方法获得的已加工表面的残余应力与真实的切削机理存在较大差别;第二类是取平行于进给方向的铣刀主剖面(正交平面)来进行二维铣削仿真,该方法考虑了铣削的变厚度连续铣削,可以获得已加工表面残余应力,但该类方法忽略了螺旋角的影响;第三类是建立了考虑螺旋角的变厚度单齿切削模型,该方法考虑了螺旋角的同时考虑了变厚度切削,但未考虑铣削是个多齿连续切削的过程,所获取的残余应力不能描述实际加工后加工完成面的残余应力情况。
技术实现要素:5.鉴于上述方法不足以满足现有科研需要,本发明考虑到铣削的工艺特性,结合斜角切削的等效换算,提出了一种考虑螺旋角的二维连续铣削残余应力仿真方法,结合铣削特性,考虑铣削过程的三个本质特征:变厚度切削过程;斜角切削过程;周期性(切削—卸载冷却—切削)间歇切削过程,将刀具角度通过斜角切削模型等效到由切削方向和流屑方向组成的等效平面中,获取等效参数后,将等效参数代入二维多齿铣刀模型中,以满足考虑螺旋角的二维多齿连续铣削。本发明采用如下技术方案:
6.一种考虑螺旋角的二维连续铣削残余应力仿真方法,包括以下步骤:
7.s1:根据铣削加工实际情况确定仿真参数,包括实际刀具三维参数、加工参数、工件材料参数,其中实际刀具三维参数包括铣刀直径、铣刀螺旋角、前角、后角、铣刀刃口钝圆;
8.s2:通过铣刀的旋转和平动运动将螺旋切削刃的螺旋线展开为直线,螺旋线的螺旋角等于展开后直线与主剖面法向方向的夹角,即螺旋角等于斜角切削中的刃倾角;
9.s3:利用实际刀具三维参数,由铣刀主剖面和法剖面的几何关系计算获取铣刀在法剖面上的前后角及刃口钝圆参数;
10.s4:采用等效平面法,将铣刀在法剖面上的前后角及刃口钝圆参数等效到由流屑方向和进给方向组成的等效平面中,得到等效前后角和等效刃口钝圆参数;
11.s5:利用等效前后角和等效刃口钝圆参数,结合铣刀直径在主剖面内建立二维多齿铣刀模型;赋予工件和刀具材料属性,设置分离断裂模型和摩擦模型,根据加工参数设置铣刀和工件的相对位置和边界条件,建立二维连续铣削残余应力有限元仿真模型,进行有限元仿真获得工件加工完成表面的残余应力。
12.进一步,所述加工参数包括铣削深度、进给速度、铣刀主轴转速,所述工件材料参数包括本构模型、密度、热导率、杨氏模量、热容、泊松比。
13.进一步,所述步骤s3,所述铣刀在法剖面上的前后角及刃口钝圆参数具体为:
14.tanγn=tanγ0cosλs15.tanαn=tanα0cosλs[0016][0017]
其中,γ0为主剖面上的前角;α0为主剖面上的后角;r0为主剖面上的刃口钝圆半径;γn为法向前角;αn为法向后角;rn为法剖面上的刃口钝圆半径。
[0018]
进一步,所述步骤s4具体为:
[0019]
通过主剖面、法剖面、等效平面和前刀面及其法向方向构成的四个坐标系之间的几何关系,将铣刀在法剖面上的前后角及刃口钝圆参数等效到由流屑方向和进给方向组成的等效平面中,得到等效前角、等效后角及等效刃口钝圆参数。
[0020]
进一步,所述步骤s4,所述等效前后角和等效刃口钝圆参数具体为:
[0021]
sinγe=sin2λs+cos2λssinγn[0022]
[0023][0024]
其中,γe为等效前角;αe为等效后角;re为等效刃口钝圆半径;γn为法向前角;αn为法向后角;rn为法剖面上的刃口钝圆半径;λs为刃倾角。
[0025]
本发明与现有技术相比的有益效果是:
[0026]
首先,与其他铣削数值计算的方法相比,本发明采用有限元仿真进行计算,使用难度低,不需要很强的理论基础,适用于各种复杂的铣削条件。其次,本发明考虑了螺旋角对铣削的影响,使残余应力结果更加精确,建立的是多齿连续铣削模型,可以准确的描述铣削过程中有规律的间歇性的切削-卸载冷却-切削的过程,相比其他采用单齿单次切削获得的残余应力,更加符合铣削特性和机理。最后,相比于其他三维仿真方法来说,本发明极大提高了计算效率,节省了计算资源。
附图说明
[0027]
图1为本发明的一种考虑螺旋角的二维连续铣削残余应力仿真方法流程图;
[0028]
图2为螺旋线展开为直线,螺旋角等效为刃倾角的示意图;
[0029]
图3为法剖面、主剖面、等效平面和前刀面及其法向向量组成的四个坐标系之间的几何关系示意图;
[0030]
图4(a)为现有技术中单齿切削模型示意图;图4(b)为本发明中采用等效参数在铣刀主剖面建立的二维多齿连续铣削仿真模型示意图。
[0031]
图5(a)和5(b)为建立二维多齿模型的示意图。
具体实施方式
[0032]
下面将结合本发明实施方式中的附图,对本发明实施方式中的技术方案进行清楚、完整的描述,显然,所描述的实施方式仅仅是作为例示,并非用于限制本发明。
[0033]
本发明提供一种考虑螺旋角的二维连续铣削残余应力仿真方法,如图1所示,包括以下步骤:
[0034]
s1:根据铣削加工实际情况确定所需仿真参数,包括实际刀具三维参数、加工参数、工件材料参数;
[0035]
具体地,根据实际铣削情况,确定仿真参数,需要确定的实际刀具三维参数包括铣刀直径φ、铣刀螺旋角λs、前角γ、后角α、铣刀刃口钝圆半径r,加工参数包括铣削深度ae(mm)、进给速度f(mm/s)、铣刀主轴转速vc(rpm),工件材料参数包括本构模型、密度、热导率、杨氏模量、热容、泊松比等材料特性。
[0036]
s2:通过铣刀的旋转和平动运动将螺旋切削刃的螺旋线展开为直线,螺旋线的螺旋角等于展开后直线与主剖面法向方向的夹角,如图2所示,即认为螺旋角等于刃倾角;
[0037]
具体地,将铣刀某一螺旋切削刃的切削过程展开为其运动轨迹,其展开后的直线与主剖面法向方向的夹角等于螺旋角,即螺旋角等于斜角切削中的刃倾角,满足
[0038]
dhf=λsꢀꢀꢀ
(1)
[0039]
式中,dhf为螺旋角,λs为刃倾角。
[0040]
s3:步骤s1中获取的实际刀具三维参数为刃口在主剖面上的投影参数,由主剖面和法剖面的几何关系计算获取法剖面上的前后角及刃口钝圆;
[0041]
具体地,通过刀具厂商或实测刀具获得主剖面上的刀具参数,法剖面上的刀具参数通过式(2)、(3)、(4)获取:
[0042]
tanγn=tanγ0cosλsꢀꢀꢀ
(2)
[0043]
tanαn=tanα0cosλsꢀꢀꢀ
(3)
[0044][0045]
其中,γ0为主剖面上的前角(
°
);α0为主剖面上的后角(
°
);r0为主剖面上的刃口钝圆半径(μm);γn为法向前角(
°
);αn为法向后角(
°
);rn为法剖面上的刃口钝圆半径(μm)。
[0046]
s4:通过主剖面、法剖面、等效平面和前刀面及其法向方向构成的四个坐标系之间的几何关系,将法剖面上的前后角及刃口钝圆投影到等效平面上,计算获取等效参数;
[0047]
具体地,采用等效平面法,将铣刀的前后角及刃口钝圆等效到由流屑方向和进给方向组成的等效平面中,通过由主剖面、法剖面、前刀面、等效平面四个面及其法向方向构成的四个坐标系之间的换算关系获得等效前角、等效后角及等效刃口钝圆同法向前后角、正交刃口钝圆之间的关系式。
[0048]
如图2和图3所示,y
ar
轴为前刀面内的主切削刃的法线方向;主切削刃方向所在直线为x
ar
轴,x轴与x
ar
轴重合;z
ar
轴垂直于前刀面;z1轴和z2轴与切削速度方向v重合;y轴与y1轴重合。坐标系o-x
aryarzar
由前刀面及其法线方向构成;o-x1y1z1由主剖面及其法线方向构成;o-xyz由法剖面及其法线方向构成;o-x2y2z2由等效平面及其法线方向构成。其中,前刀面(平面x
ar
oy
ar
—p
ar
)为直接作用于被切削的金属层,并控制切屑沿其排出的刀面。切削平面(z1ox
ar
)为切削刃与切削速度方向构成的平面,x1在切削平面内。基面(x1oy1)为过切削刃选定点,垂直于主运动方向的平面。主剖面(y1oz1)过主切削刃选定点,垂直于切削平面和基面。法剖面(yoz)过主切削刃选定点,垂直于主切削刃。等效平面(y2oz2)过主切削刃选定点,由切削方向和流屑方向构成的平面。
[0049]
坐标系o-x
aryarzar
与坐标系o-xyz之间通过绕x
ar
轴旋转角γn转换;坐标系o-xyz与坐标系o-x1y1z1之间通过绕y轴旋转角λs转换;坐标系o-xyz与坐标系o-x2y2z2之间通过绕z1轴旋转角η转换。其中,vc为流屑沿前刀面流出速度;γn为法向前角;γ0为主剖面上的前角;γe为等效前角;λs为刃倾角;ηc为流屑角;η为等效平面主方向角。
[0050]
等效前角、等效后角、等效刃口钝圆半径由如下公式计算获得:
[0051]
sinγe=sin2λs+cos2λssinγnꢀꢀꢀ
(5)
[0052][0053][0054]
其中,γe为等效前角(
°
);αe为等效后角(
°
);re为等效刃口钝圆半径(μm);γn为法向前角(
°
);αn为法向后角(
°
);rn为法剖面上的刃口钝圆半径(μm);λs为刃倾角(
°
)。
[0055]
s5:采用等效后刀具参数建立多齿铣刀模型,用等效后的参数在建模软件中对单齿进行建模,然后根据实际铣刀几何构型进行阵列,按照实际铣削要求装配刀具和工件的相对位置,建立二维连续铣削残余应力有限元仿真模型,进行有限元仿真以获取工件加工完成表面的残余应力。
[0056]
现有技术中多采用单齿单次切削,如图4(a)所示,其描述的为铣刀中的单个刀齿对工件切削行为,其切削完成后的已加工表面在实际铣削过程中会被下一步切削切除,因此用此表面的残余用力来代表实际加工中加工完成面的残余应力同实际机理有所区别。本发明采用的是多齿连续铣削,如图4(b)所示,其运动轨迹(包括旋转和进给,其轨迹为次摆线)和切削机理均与实际铣削过程相符,实际铣削过程中,周期性的加载和冷却导致每个齿切削后的残余应力会受前一齿形成的残余应力的影响,实际铣削后已加工平面是经过多次切削形成的,该模型获得的加工完成表面残余应力即为实际过程中多次切削形成的已加工表面的残余应力。
[0057]
具体地,如图5(a)和5(b)所示,使用计算获得的等效前后角和等效刃口钝圆参数,结合铣刀实测直径在铣刀主剖面内建立二维多齿铣刀,其中,z为铣刀齿数,φ为铣刀直径。赋予工件和刀具材料属性,设置分离断裂模型和摩擦模型等,根据加工参数设置铣刀和工件的相对位置和边界条件,经过多齿连续有限元切削仿真后,最终获得工件加工完成表面的残余应力。
[0058]
下面通过具体的实施例对本发明提供的上述考虑螺旋角的二维连续铣削残余应力仿真方法的具体实施进行详细说明。
[0059]
实施例1
[0060]
s1:实际测量获得刀具前角为13.5
°
,后角为6
°
,螺旋角为25
°
,刃口钝圆半径为20μm,铣刀直径为10mm;被加工材料为钛合金tc4,其本构模型为:
[0061][0062]
其中,σ为流动应力,ε
p
为材料等效塑性应变,为材料等效塑性应变率,为材料参考应变率,t为材料动态温度。密度、热导率、热容、杨氏模量、泊松比等采用deform软件中自带的材料库中ti6al4v的参数;铣削深度为0.1mm,主轴转速为600rpm,进给速度为0.2mm/r。
[0063]
s2:螺旋角等效为刃倾角:
[0064]
dhf=λs=25
[0065]
s3:由实测的主剖面获得的参数计算获得法剖面的参数:
[0066]
γn=arctan((tan13.5
°
)
×
(cos25
°
))=12.28
[0067]
αn=arctan((tan6
°
)
×
(cos25
°
))=6.62
[0068][0069]
s4:获得铣刀法剖面参数后,通过等效关系式计算等效参数:
[0070]
等效前角:
[0071]
sinγe=(sin25
°
)2+(cos25
°
)2×
(sin12.28
°
)
[0072]
γe=20.69
°
[0073]
等效后角:
[0074][0075]
αe=6.23
°
[0076]
等效刃口钝圆半径:
[0077][0078]
re=34.40
[0079]
s5:用等效后的刀具参数建立铣削仿真模型,建立两齿铣刀,采用顺铣加工方法,铣刀施加600rpm自转,沿x方向2mm/s平动。刀具和工件材料参数如步骤s1中所述;分离准则采用基于压力的物理分离准则,阀值为0.1;断裂准则采用normalized c&l模型,阀值为0.2;工件与铣刀接触的两个面设置为三类边界条件和环境换热,换热系数为0.02n/sec/mm/c;刀具加工过程为接触的面设置为一类边界条件,设置为环境温度20
°
;切削时工件和刀具的换热系数为40n/sec/mm/c;摩擦模型选库伦模型,摩擦系数设为0.25。
[0080]
最终获得等效前的表面残余应力为-200mpa,其残余应力最大值位于表面,残余应力深度为1.5mm;等效后的表面残余应力为-10mpa,在64μm处达到最大-20mpa,残余应力深度为0.8mm。由此可以看出,是否考虑螺旋角所获取的残余应力值及其分布规律不一样,考虑螺旋角的多齿连续铣削仿真获得的残余应力结果更加精确,更符合真实的铣削特性和机理。