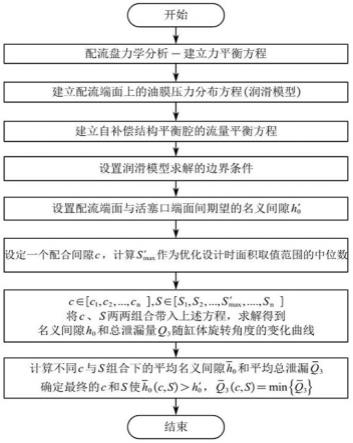
1.本发明属于液压马达零件的结构优化设计领域,尤其涉及一种多作用液压马达盘配流系统自补偿结构设计方法。
背景技术:2.多作用液压马达主要的特点就是马达旋转一周的过程中,活塞在活塞腔内往复工作多次。而多作用的特点使得这类马达具有功率密度大、效率高、脉动小、低速稳定性好等优点。也正因此,无论是在军用领域还是民用领域,多作用马达都有着十分广阔的应用,比如军工领域的驱逐舰、科考船等的绞车系统;民用领域的盾构机、风力发电、打桩船、挖泥船、破碎机、双轮铣、trd工法机械、掘进机、轧钢传输线、卷板机、注塑机等大型装备的旋转驱动系统。
3.多作用液压马达中的配流系统是保证其正常工作的核心部件,主要功能是周期性地将马达的高、低压油口与相应的活塞腔连通,实现油液分配。同时保证活塞在缩回和伸出过程之间切换时,将活塞腔与马达的高、低压油口隔断。
4.目前多作用液压马达中的配流系统主要有三种形式:第一种是阀配流,结构复杂,一般用于水、高水基介质的马达;第二种是轴配流,其结构简单,但需要很高的加工和装配精度来保证正常运转、密封和配油效果,并且它对液压油的"热冲击"(冷马达启动时,输入热油导致配流轴膨胀卡死)非常敏感,同时随工作过程中的磨损,泄漏逐渐增加、容积效率逐渐下降,应用相对较少;第三种是盘配流(端面配流),结构简单紧凑,承压能力高,可设计成带有自补偿结构的形式,以实现配流副磨损自动补偿,提高多作用马达容积效率和启动可靠性。这种自补偿的配流盘目前具有广泛的应用。
5.盘配流系统的自补偿结构将配流盘配流端面压在马达的缸体活塞口端面上,缸体的活塞口端面分布有多个油口与缸体上的活塞腔连通,且各个油口的压力作用在配流盘的配流端面上,形成使配流盘与缸体分离的液压支撑力。随着马达旋转(缸体相对配流盘旋转),活塞口端面上的各个油口的压力在高、低压间交替变换,使配流盘与缸体分离的液压支撑力也在不断变化;如果配流系统中负责压紧的自补偿结构尺寸设计不合理,很有可能导致压紧力不足、配流盘与缸体分离,泄漏增加;亦或是压紧力太大,导致配流盘严重磨损(“烧盘”)。因此,自补偿结构尺寸的合理设计是保证自补偿配流盘以及多作用马达工作品质的重要前提。然而,目前还没有自补偿结构最优尺寸的设计方法。
技术实现要素:6.本发明目的在于针对现有技术的不足,本发明提供一种多作用液压马达盘配流系统自补偿结构设计方法,提高自补偿配流盘的效率和使用寿命。
7.本发明的目的是通过以下技术方案来实现的:一种多作用液压马达盘配流系统自补偿结构设计方法,该方法包括以下步骤:步骤1:对配流盘进行力学分析,得到配流盘两侧的受力平衡方程;
步骤2:建立配流盘配流端面上的油膜压力分布方程;步骤3:对自补偿结构的平衡腔建立流量平衡方程;步骤4:结合步骤3的流量平衡方程为步骤2中的压力分布方程设置求解的边界条件;步骤5:设置配流盘配流端面与缸体活塞口端面间期望的名义间隙;步骤6:根据需求设定自补偿结构与配流盘的配合间隙取值集合,选取集合中的最小配合间隙,结合期望的名义间隙和边界条件,求解油膜压力分布方程和流量平衡方程,得到缸体相对于配流盘旋转不同角度时的油膜压力和平衡腔压力,进而求解受力平衡方程,得到缸体相对于配流盘旋转不同角度时面积s的一组解,以这组解中的最大值为中位数,设定优化设计时的面积取值集合;步骤7:将配合间隙取值集合中的取值与面积取值集合中的取值两两组合,结合边界条件,求解油膜压力分布方程和流量平衡方程,仿真模拟缸体相对于配流盘旋转于不同角度时,配流端面上油膜压力以及平衡腔压力的变化,得到配流端面的名义间隙和配流系统的总泄漏量随缸体旋转角度的变化曲线;步骤8:根据步骤7中计算得到的每条曲线取配流盘工作平稳后的平均值,选择最佳的配合间隙与面积组合作为最终的优化结果,根据最终的优化结果设计完成自补偿结构。
8.进一步地,所述配流盘的力平衡方程表示作用在柱塞上的所有力的矢量和为0。
9.进一步地,所述配流盘配流端面压力分布方程通过润滑分析得到,用于求解配流端面各处的油膜压力分布和油液流速分布。
10.进一步地,平衡腔为柱状、均布于配流盘上,且位于配流盘配流端面的对侧,配流端面的油液通过小孔进入平衡腔内。
11.进一步地,所述平衡腔内有自补偿结构,自补偿结构为柱状结构,对平衡腔具有密封作用,且自补偿结构沿平衡腔内壁滑动,但不能完全滑出平衡腔。
12.进一步地,所述自补偿结构平衡腔内的流量平衡方程用于计算处于过渡状态的平衡腔的压力,所述过渡状态为平衡腔不与缸体上的活塞腔油口连通。
13.进一步地,步骤6中,设定配合间隙c取值集合c={c1,c2,c3,
…
,ck},其中c1…ck
逐渐增大。
14.进一步地,步骤6中,缸体相对于配流盘旋转不同角度时面积s的一组解为,将面积中的最大值,设为优化设计时面积s取值范围的中位数,中位数前后的面积s取值根据实际需求设计,即面积s取值集合为ss={s1,s2,s3,
…
,sm,,s
m+2
,
…
,s
2m+1
},其中s1…s2m+1
逐渐增大。
15.进一步地,步骤8中,步骤7中计算得到的每条曲线取配流盘工作平稳后的平均值,得到配合间隙与面积组合下的平均名义间隙和平均泄漏量,在保证大于步骤5中设置的配流盘配流端面与缸体活塞口端面间期望的名义间隙的情况下,选取使平均泄漏流量最小的配合间隙c与面积s组合作为最终的优化结果,根据最终的优化结果设计完成自补偿结构。
16.进一步地,步骤6中,所述面积s是自补偿结构在配流盘配流端面上的投影面积,面
积s乘以对应平衡腔内的压力即可得到该自补偿结构对配流盘端面产生的压紧力,步骤8中,所述配流盘工作平稳是指此时名义间隙随缸体旋转角度呈现周期性波动。
17.本发明的有益之处为:本发明提出的设计方法可实现自补偿结构快速、低成本的优化设计,缩短多作用液压马达盘配流系统的设计周期,并且设计的自补偿结构可以在有效降低配流系统的泄漏量的同时,保证配流盘的配流端面与缸体活塞口端面有良好的润滑。
附图说明
18.图1 自补偿结构设计方法流程图。
19.图2 自补偿配流系统结构原理及受力示意图。
20.图3 配流端面示意图。
21.图4 活塞口端面示意图。
22.图5 配流端面和配合间隙油膜压力分布示意图。
23.图6 当配合间隙为5微米、直径d为16毫米时名义间隙随马达旋转角度的变化曲线。
24.图7 当配合间隙为5微米、直径d为16毫米时总泄漏量随马达旋转角度的变化曲线。
25.图8 当直径为时平均名义间隙随配合间隙c的变化曲线。
26.图9 当直径为时平均总泄漏量随配合间隙c的变化曲线。
27.附图中的标记为:1-缸体、2-活塞腔油口、3-自补偿结构、4-配流盘、5-壳体、6-浮动密封套、7-低压配油窗口、8-平衡腔、9-高压配油窗口、10-弹簧。
具体实施方式
28.为了更清楚地说明本发明实施例,下面结合附图和具体实施例对本发明作进一步阐述。
29.如图1所示,本发明提供了一种多作用液压马达盘配流系统自补偿结构设计方法,通过优化自补偿结构在配流端面上的投影面积以及自补偿结构与配流盘的配合间隙来降低配流系统的泄漏和磨损。所述配流系统中,配流盘的一侧为配流端面,另一侧为配流盘的进油口和回油口,随马达旋转过程中油液压力、转速、磨损等的变化,配流盘沿自补偿结构移动,自动调整配流盘配流端面与缸体活塞口端面之间的距离,实现自动补偿,配流盘高压配流窗口和低压配油窗口的油液会周期性的进入自补偿结构的平衡腔内,为配流盘提供压紧力,所述压紧力使配流盘配流端面向与缸体活塞口端面的配合间隙减小,保证配流盘与缸体之间的密封。
30.本发明具体设计步骤如下:以八作用十四柱塞液压马达的自补偿配流系统为例,配流系统的局部剖切图如图2所示,由配流盘4、自补偿结构3、弹簧10、浮动密封套6组成;所述配流盘4的完整的配流端面12如图3所示,所述配流端面12压在缸体1上的活塞口端面13上,所述缸体活塞口端面13如图4所示;
所述自补偿结构3为圆柱盖状结构,实现平衡腔8的密封,保持平衡腔8内部压力,为配流盘4提供向左的压紧力;所述自补偿结构3的右端压在马达的固定壳体11上,所述配流盘4可根据左右两侧的力差沿自补偿结构3移动,实现自补偿功能;由于所述自补偿结构3为圆柱状,其在配流端面的投影面积s可用直径d表示,因此自补偿结构3的两个关键尺寸为其外圆柱直径d以及自补偿结构3与配流盘4的配合间隙c,所述外圆直径d和配合间隙c均会影响配流盘向左的压紧力和泄漏;所述外圆直径d和配合间隙c为本实施例自补偿结构待优化设计的参数。
31.步骤1:对配流盘进行力学分析,如图2所示,配流盘4受到油膜力、活塞腔油口2的液压力、八个高压配油窗口9过渡斜面上的液压力、八个低压配油窗口7过渡斜面上的液压力、十六个平衡腔8的液压力、十六个弹簧10的弹力、八个高压进油口处的浮动密封套6的压紧力、八个低压出油口处的浮动密封套6的压紧力、马达壳体内部压力在配流盘4上的作用力,建立配流盘的力平衡方程,合力f为0:步骤1中所述油膜力通过对配流端面上分布的油膜压力p进行积分得到;所述液压力为十四个活塞腔油口2的油液在配流端面12上产生的总作用力,每个活塞腔油口2的作用力通过该活塞腔的压力与重叠面积相乘计算得到;所述重叠面积是活塞腔油口2与配流端面12的重叠区域面积;所述液压力由平衡腔8内的压力和自补偿结构3的在配流端面12上的投影面积s的乘积;对于本实施例,投影面积s由自补偿结构3的直径d计算得到。
32.步骤2:建立配流端面12上的油膜压力分布方程(润滑模型),用于计算配流盘配流端面与缸体活塞口端面之间的支撑力和配流副泄漏量,所述支撑力使配流盘与缸体分离;其中,p表示配流端面12上某一点的油膜压力,x表示配流端面12上各点在水平方向的坐标,如图3所示,y表配流端面12上各点在垂直方向的坐标,是配流端面上各点的油液密度,t为时间,是油液粘度,h为摩擦副某一点的油膜厚度,u为活塞口端面13某一点相对x轴的速度,v为活塞口端面13某一点相对y轴的速度。
33.所述油膜厚度通过以下方程计算:其中,为配流端面12与活塞口端面13之间的名义间隙,为配流端面12与活塞口端面13的某一点由于压力而产生的形变量。
34.步骤3:对自补偿结构所在的平衡腔建立流量平衡方程,用于计算处于过渡状态的平衡腔8内的压力,平衡腔8的净流量为0:如图2所示,式中,为平衡腔的净流量,为从配流端面流入平衡腔8的流量,
为平衡腔8从配合间隙c中泄漏的流量,为平衡腔8的容积,为平衡腔8前一时刻的压力,为油液的体积弹性模量;所述平衡腔8的过渡状态为当平衡腔8未与活塞腔油口2连通时的状态,此时平衡腔的压力为未知量,且随时间变化,需根据上述流量平衡方程计算得出,而当平衡腔8与活塞腔油口2连通时,此时平衡腔的压力等于所连通活塞腔油口压力,是已知量,无需通过流量平衡方程计算;步骤4:结合步骤3的流量平衡方程为步骤2中的压力分布方程设置求解的边界条件;所述边界条件为:与高压配流窗口9相连的边界上的压力设为马达的进油压力,与低压配流窗口7相连的边界上的压力设为马达的排油压力,与马达内部腔体相连的边界设为马达的泄油压力,与平衡腔8连接的边界上的压力设为;步骤5:根据配流端面12与活塞口端面13的表面粗糙度,确定配流端面12上希望的名义间隙,本实施例中取,其中和分别为配流端面12与活塞口端面13的表面粗糙度。
35.步骤6:设定配合间隙c的取值集合为c={2,2.5,3,3.5,
…
,21.5,22}微米,本步骤中选取配合间隙c=2微米,结合步骤5中确定的和步骤4中的边界条件求解步骤2和步骤3中的方程,得到缸体相对于配流盘旋转不同角度时面积s的一组解为,将面积中的最大值,设为优化设计时面积s取值范围的中位数,中位数前后的面积s取值根据实际需求设计,即面积s取值集合为ss={s1,s2,s3,
…
,sm,,s
m+2
,
…
,s
2m+1
},其中s1…s2m+1
逐渐增大。而在本实施例中,具体是得到缸体1相对于配流盘4旋转不同角度时的油膜压力p和平衡腔压力,缸体1相对于配流盘4旋转到270度时的结果如图5所示,线条越密集的地方表示压力越大,基于不同角度时的油膜压力p和平衡腔压力求解步骤1中的力平衡方程,得到不同角度时直径d的一组解,中的最大值为=16毫米,设定优化时直径d取值集合为dd={9,10,11,
…
,16,21,22,23}毫米。
36.步骤7:将集合c中的41个配合间隙c的取值与dd集合中的15个直径d的取值两两组合,结合步骤4中的边界条件求解步骤2和步骤3的方程,仿真模拟缸体1相对于配流盘4旋转于不同角度时,配流端面12上油膜压力p以及平衡腔压力的变化;每一个角度的计算结果应保证步骤1中的力平衡方程成立;对仿真结果后处理得到41
×
15个配合间隙c与直径d组合下缸体1相对于配流盘4旋转于不同角度时配流端面12的名义间隙和泄漏量的变化曲线,其中c=5、d=16组合下的名义间隙和泄漏量的变化曲线分别如图6和图7所示;所述泄漏量为配流系统的泄漏量总和,包括配流端面12泄漏流量和自补偿结构3配合间隙泄漏的流量。
37.步骤8:对步骤7中获得的每条曲线取配流盘4工作平稳后的平均值,对于图6和图7中的数据则取175度-270度范围内的数据的平均值,得到平均名义间隙和平均泄漏量随配合间隙c、直径d的变化曲线;直径d=16毫米时,平均名义间隙和平均泄漏量随配合间隙c的变化曲线如图8和图9所示;在保证大于的情况下,选取使泄漏流量最小的配合间隙c=5微米与d=16毫米的组合作为最终的优化结果,根据最终的优化结果完成自补偿结构设计。
38.以上所述的实施例仅仅是对本发明的优选实施方式进行描述,并非对本发明的范
围进行限定,在不脱离本发明设计精神的前提下,本领域普通技术人员对本发明的技术方案做出的各种变形和改进,均应落入本发明权利要求书确定的保护范围内。