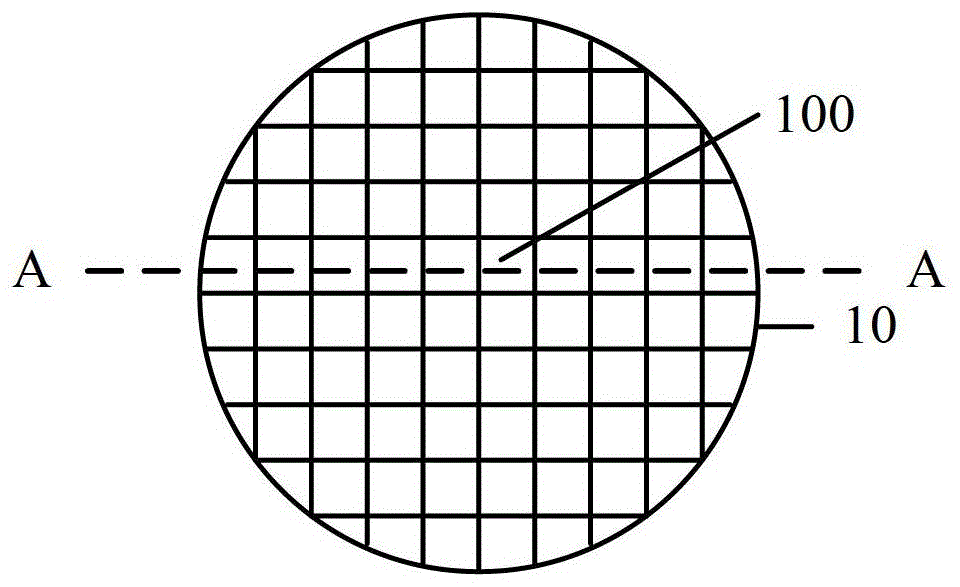
本发明涉及半导体制造技术领域,尤其涉及一种晶圆刻蚀后的清洗方法。
背景技术:在半导体制造过程中,晶圆的清洗是非常重要的一个环节。在执行晶圆的前段工艺过程(FEOL)和后段工艺过程(BEOL)时,晶圆需要经过无数次的清洗步骤,清洗的次数取决于晶圆的设计和互连的层数。在过去十几年中,主要通过批式处理技术对晶圆进行清洗(即在一个处理仓中利用浸泡方法或者喷淋法同时清洗多片晶圆),该方法虽产量较高但效果差、良率低。且随着半导体器件的特征尺寸(CD,CriticalDimension)不断减小,晶圆中半导体器件的数量增加,半导体材料变得越来越脆弱,清洗效果和材料损失的要求变得越来越严格,对晶圆清洗的要求也越来越高,批式处理技术逐渐无法满足晶圆清洗的要求。此外,批式处理技术无法满足如快速热处理(RTP)等工艺的关键扩散和CVD技术。而单个晶圆清洗方法由于对每一片晶圆单独加工,其具有清洗质量高、化学试剂用量少、循环周期块等优点,大大改进了生产力,降低了生产成本。而且,单个晶圆清洗方法也为整个制造周期提供了实现更好的工艺过程控制的机会,改善了单个晶圆以及晶圆对晶圆的均一性,进而提高了良率。因此,单个晶圆清洗方法逐渐替代批式处理技术,成为晶圆清洗工艺的主流方法。现有工艺中,在干法刻蚀之后,通常利用单个晶圆清洗方法对表面介质层中形成有刻蚀图案的晶圆进行清洗,以去除刻蚀残留的聚合物。以在晶圆表面低k或者超低k介质层中形成金属互连线或者插塞为例,在形成金属互连线或者插塞之前,需先对晶圆上的低k或者超低k介质层进行干法刻蚀,形成用于填充金属互连线或者插塞的通孔;再利用单个晶圆清洗方法进行清洗,去除干法刻蚀形成通孔过程中残留于低k或者超低k介质层上表面以及通孔侧壁上的聚合物;然后对清洗后的晶圆进行检测,确定清洗后残留的聚合物是否在设定范围之内;当其在设定范围内时,在低k或者超低k介质层中的通孔内填充金属,形成金属互连线或者插塞,当其超出设定范围内时,需要对晶圆重新进行清洗。然而,在对清洗后的晶圆进行检测后发现,上述晶圆清洗方法的效果不明显,返工几率大,良率低。更多晶圆清洗方法请参考公开号为CN101529559A的中国专利申请。
技术实现要素:本发明解决的问题是提供一种晶圆刻蚀后的清洗方法,提高晶圆清洗的效果,进而提高晶圆清洗的良率。为解决上述问题,本发明提供了一种晶圆刻蚀后的清洗方法,包括:提供晶圆;在晶圆上形成介质层,并于所述介质层中形成贯穿其厚度的通孔,所述介质层为疏水性;进行氨气等离子体处理,使所述介质层的上表面以及通孔的侧壁由疏水性转化为亲水性;进行清洗工艺。可选的,所述氨气等离子体处理的压强为5mTorr~200mTorr,电源功率为100W~1000W,时间为5s~60s,气体为NH3、He和Ar的混合气体,所述混合气体中NH3的流量为10sccm~500sccm,He的流量为10sccm~200sccm,Ar的流量为10sccm~200sccm。与现有技术相比,本发明技术方案具有以下优点:在晶圆表面介质层中形成贯穿介质层厚度的通孔之后,进行氨气等离子体处理,在不影响介质层孔隙率的前提下,增加位于介质层上表面以及通孔侧壁上氢键的数目,使所述介质层的上表面以及通孔的侧壁由疏水性转化为亲水性,进而在晶圆清洗过程中使介质层的上表面以及通孔的侧壁更易与清洗溶液接触,使晶圆刻蚀后残留的聚合物和污染物随清洗溶液去除,提高了晶圆清洗的效果以及良率。进一步的,在晶圆上形成介质层之前,先在晶圆表面形成停止层,在贯穿介质层厚度的通孔形成后,进行氨气等离子体处理时,所述停止层能够有效保护晶圆,避免氨气等离子体处理对晶圆表面以及形成于晶圆中的半导体器件造成损伤。附图说明图1为本发明晶圆刻蚀后的清洗方法一个实施方式的流程示意图;图2~图6为本发明晶圆刻蚀后的清洗方法一个实施例的结构示意图。具体实施方式为使本发明的上述目的、特征和优点能够更加明显易懂,下面结合附图对本发明的具体实施方式做详细的说明。在下面的描述中阐述了很多具体细节以便于充分理解本发明,但是本发明还可以采用其它不同于在此描述的其它方式来实施,因此本发明不受下面公开的具体实施例的限制。正如背景技术部分所述,现有工艺在干法刻蚀之后,通常利用单个晶圆清洗方法对表面低k或者超低k介质层中形成有刻蚀图案的晶圆进行清洗,以去除刻蚀残留的聚合物,使清洗后残留的聚合物在设定范围之内,利于后续工艺(如:在通孔内进行的金属填充工艺)的进行。但是,在对清洗后的晶圆进行检测后发现,现有晶圆清洗方法的效果不明显,良率低。发明人经过研究发现,单个晶圆清洗方法对表面低k或者超低k介质层中形成有通孔的晶圆清洗效果不明显、良率低,是由以下原因造成的:低k或者超低k介质层表面为疏水性,通过单个晶圆清洗方法对低k或者超低k介质层表面进行清洗时,清洗溶液难以浸润其表面,附着于低k或者超低k介质层表面的聚合物和污染物难以随清洗溶液一起脱离低k或者超低k介质层表面。基于上述分析可知:可在不损害低k或者超低k介质层的前提下,采用使低k或者超低k介质层表面由疏水性转化为亲水性的方法解决现有效果不明显、良率低的问题。发明人经过进一步研究发现:在通过氦气和/或氢气等离子对低k介质层表面的掩膜层进行灰化处理时,由于氦气和/或氢气不包含氧原子,其不会对低k或者超低k介质层造成损害,但是,灰化处理后的低k或者超低k介质层表面仍为疏水性;若通过氦气和/或氢气等离子对低k或者超低k介质层进一步进行过刻蚀,低k或者超低k介质层表面仍不能从疏水性转变为亲水性,而且过刻蚀还可能导致低k或者超低k介质层的孔隙率提高,降低了低k或者超低k介质层的k值,影响其性能。而通过氨气等离子对低k或者超低k介质层表面进行处理时,氨气等离子不会影响低k或者超低k介质层的k值,且氨气等离子体中的氢键会附着于低k或者超低k介质层表面,使低k或者超低k介质层表面由疏水性转化为亲水性,使低k或者超低k介质层表面易于与清洗溶液接触,进而使残留于低k或者超低k介质层表面的聚合物和污染物随清洗溶液一起去除,提高晶圆清洗的效果。针对上述分析,本发明提供了一种晶圆刻蚀后的清洗方法,在晶圆表面介质层中形成通孔后,对介质层上表面以及通孔的侧壁进行氨气等离子体处理,使介质层的上表面以及通孔的侧壁由疏水性转化为亲水性,最后再进行清洗工艺,去除残留于介质层上表面以及通孔侧壁上的聚合物和污染物。本发明晶圆刻蚀后的清洗方法的清洗效果好、良率高。下面结合附图进行详细说明。参考图1,为本发明晶圆刻蚀后的清洗方法一个实施方式的流程示意图,包括:步骤S1,提供晶圆,并在晶圆上由下至上依次形成停止层和介质层;步骤S2,在所述介质层上形成掩膜层,所述掩膜层中形成有与通孔形状对应的掩膜图形;步骤S3,沿掩膜图形刻蚀所述介质层,形成贯穿所述介质层厚度的通孔,在形成通孔的同时去除介质层上部分厚度的掩膜层;步骤S4,去除介质层上剩余的掩膜层;步骤S5,进行氨气等离子体处理,使所述介质层的上表面以及通孔的侧壁由疏水性转化为亲水性;步骤S6,进行清洗工艺。图2~图6为本发明晶圆刻蚀后的清洗方法一个实施例的结构示意图,结合图2~图6,通过具体实施例对本发明晶圆刻蚀后的清洗方法做进一步说明。首先,参考图2,提供晶圆10。图2为晶圆10的俯视图,所述晶圆10分成若干器件区域。现有工艺中,通常在一片晶圆的各器件区域中制作相同的半导体器件,且各半导体器件同时制作,制作的工艺、流程以及条件完全相同,以简化半导体器件的制作工艺,降低半导体器件的制作成本。因此,可以以对晶圆10中一个器件区域上的介质层进行刻蚀形成通孔,并进行刻蚀后清洗工艺为例,对本发明的晶圆刻蚀后的清洗方法进行说明。本实施例中,以对晶圆10中器件区域100上的介质层中形成通孔,并进行刻蚀后清洗工艺为例,对本发明的晶圆刻蚀后的清洗方法进行说明,晶圆10中其他器件区域上半导体器件的制作工艺与器件区域100上半导体器件的制作工艺相同,在此不再赘述。图3为图2中晶圆10中器件区域100沿AA方向的剖视图。参考图3,在器件区域100上由下至上依次形成停止层102和介质层104。本实施例中,所述器件区域100中还可形成有半导体器件(图未示)。所述停止层102的材料为氮化硅,所述介质层104为疏水性,所述介质层104的材料可为低k材料或者超低k材料。继续参考图3,在所述介质层104上形成掩膜层,所述掩膜层中形成有与通孔形状对应的掩膜图形112。本实施例中,所述掩膜层为多层结构,位于介质层104上的掩膜层由下至上依次包括:图形膜层106a、介质层抗反射层(DielectricAnti-ReflectionCoat简称DARC)108和光刻胶层(photoresist,简称为PR)110。所述掩膜图形112位于掩膜层中的光刻胶层110中,形成掩膜图形112的方法为曝光、显影工艺。之所以选择多层结构的掩膜层,是因为:形成于器件区域100中的半导体器件特征尺寸较小,光刻胶层110的厚度较薄,以包含掩膜图形112的光刻胶层110为掩模对介质层104进行刻蚀时,光刻胶层110易在通孔形成之前被完全去除,而采用图形膜层106a、介质层抗反射层108和光刻胶层110共同作为掩膜层,可以通过包含掩膜图形112的光刻胶层110定义出图形,在之后的刻蚀中图形被转移到介质层反射层108和图形膜层106a,在光刻胶层110被消耗完之后,由介质层抗反射层108做掩模,在介质层抗反射层108被消耗完之后,由图形膜层106a做掩模。以保证在图形膜层106a被完全去除之前,形成通孔。具体的,所述图形膜层106a的材料为无定形碳,形成所述图形膜层106a的方法为化学气相沉积;所述介质层抗反射层108的材料为氮化硅或者氮氧化硅,形成所述介质层抗反射层108的方法为化学气相沉积。在其他实施例中,所述掩膜层还可为单层结构,所述掩膜层的材料为光刻胶。参考图4,沿图3中掩膜图形112刻蚀所述介质层104,形成贯穿所述介质层104厚度的通孔114,在形成通孔114的同时去除介质层104上部分厚度的掩膜层。本实施例中,沿图3中掩膜图形112刻蚀所述介质层104,形成贯穿所述介质层104厚度的通孔114的方法为干法刻蚀,如各向异性干法刻蚀。本实施例中,由于光刻胶层110和介质层抗反射层108的厚度远小于图形膜层106a的厚度,在形成通孔114时去除部分厚度的掩膜层为光刻胶层110、介质层抗反射层108和部分厚度的图形膜层106a,剩余的掩膜层为部分厚度的图形膜层106b。在其他实施例中,剩余的掩膜层还可为由部分厚度的光刻胶层、介质层抗反射层和图形膜层构成的多层结构,或者部分厚度的介质层抗反射层和图形膜层构成的多层结构,其与形成通孔114之前掩膜层中光刻胶层110、介质层抗反射层108和图形膜层106a各层的厚度以及形成通孔114的刻蚀工艺有关。在形成通孔114时,所述停止层102能够有效保护位于其下方的器件区域100表面或者器件区域100中的半导体器件。参考图5,去除介质层104上剩余的掩膜层。本实施例中,由于剩余的掩膜层为部分厚度的图形膜层106b,相应的,去除介质层104上剩余的掩膜层的方法为灰化工艺,所述灰化工艺的气体可为氢气或/和氦气,其具体工艺为本领域技术人员所熟知,在此不再赘述。需要说明的是,在去除介质层104上剩余的掩膜层时,需严格控制灰化工艺的时间,在剩余的掩膜层被完全去除后立即停止灰化工艺,避免灰化工艺对介质层104进行过刻蚀,进而避免灰化工艺对介质层104的k值造成影响。继续参考图5,进行氨气等离子体处理,使所述介质层104的上表面以及通孔114的侧壁由疏水性转化为亲水性。本实施例中,所述氨气等离子体处理的压强可为5mTorr~200mTorr,电源功率可为100W~1000W,时间可为5s~60s,气体可为NH3、He和Ar的混合气体,所述混合气体中NH3的流量为10sccm~500sccm,He的流量为10sccm~200sccm,Ar的流量为10sccm~200sccm。由于NH3、He和Ar的混合气体中不包含氧原子,其不会对介质层104的k值造成影响;且氨气等离子体中的氢键会附着于介质层104的上表面以及通孔114的侧壁,使介质层104的上表面以及通孔114的侧壁由疏水性转化为亲水性。在进行氨气等离子处理时,所述通孔114底部的停止层102还能够有效保护位于其下方的器件区域100表面或者器件区域100中的半导体器件。参考图6,去除通孔114底部的停止层102。本实施例中,去除通孔114底部的停止层102的方法为干法刻蚀。具体的,所述干法刻蚀的压强可为5mTorr~200mTorr,电源功率可为100W~1000W,时间为5s~60s,气体可为CH4、CHF3、CH3F、He和Ar的混合气体,所述混合气体中CH4的流量为10sccm~500sccm,CHF3的流量为10sccm~200sccm,CH3F的流量为10sccm~100sccm,He的流量为10sccm~200sccm,Ar的流量为10sccm~200sccm。继续参考图6,进行清洗工艺。本实施例中,所述清洗工艺可为单个晶圆清洗工艺;所述清洗工艺的清洗溶液为水基清洗溶液。由于介质层104的上表面以及通孔114的侧壁为亲水性,其易于与清洗溶液接触,进而使残留于介质层104上表面以及通孔114的侧壁的聚合物和污染物随清洗溶液一起去除,提高晶圆清洗的效果,晶圆清洗的良率高。本发明虽然已以较佳实施例公开如上,但其并不是用来限定本发明,任何本领域技术人员在不脱离本发明的精神和范围内,都可以利用上述揭示的方法和技术内容对本发明技术方案做出可能的变动和修改,因此,凡是未脱离本发明技术方案的内容,依据本发明的技术实质对以上实施例所作的任何简单修改、等同变化及修饰,均属于本发明技术方案的保护范围。