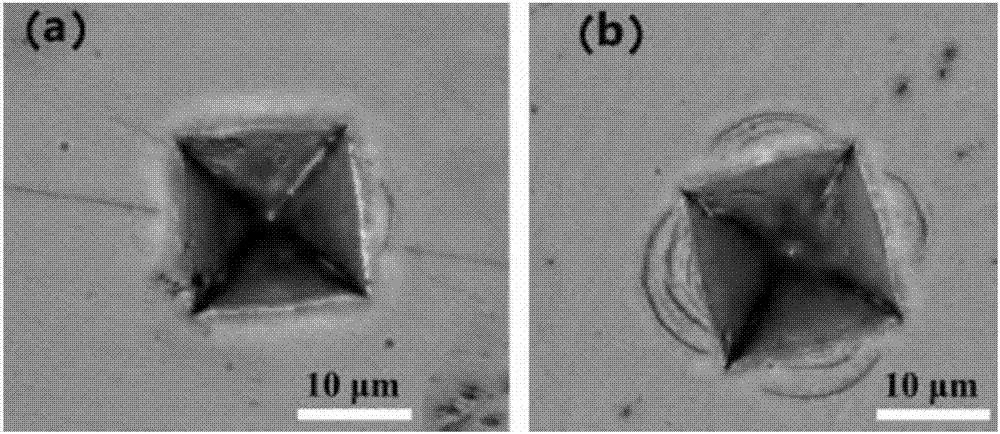
本发明涉及一种韧性增强的铁基块体非晶软磁合金及其制备方法,属于磁性功能材料领域。
背景技术:铁磁性块体非晶合金结构均匀,没有晶界和磁晶各向异性,没有沉淀相和杂质,对磁畴壁运动的钉扎作用很小,而且电阻率高,因而具有低损耗、高磁导率以及高饱和磁化强度等优点,同时铁基非晶原材料丰富、制备流程短、产品节能环保,使得一些Fe基非晶合金条带在电力转换(如变压器)等领域得到了广泛的应用。随着科学技术的迅速发展,要求电磁元件制备简单化和体积小型化,然而,由于非晶形成能力的限制,一定程度上阻碍了其更广泛的应用,所以迫切需要开发出具有强非晶形成能力和高饱和磁化强度的Fe基块体非晶合金。日本专利4044531公布了一种超高强度Fe-Co基块体金属玻璃合金,化学成分为[(Fe1-aCoa)0.75SiXB0.25-X]100-YMY,M为Nb,Zr,W,Cr,Mo,Hf,V和Ti中一种或几种,具体原子百分含量为0.1≤a≤0.6,0.03≤X≤0.07,1≤Y≤4(at.%)。其最大非晶形成能力为5.0mm,但文献报道其饱和磁感应强度只有0.84T;非晶形成能力最小为2.0mm样品的饱和磁感应强度最高也只有1.13T。可以看出该体系虽有较高非晶形成能力但是饱和磁感较低,由于添加了战略资源Co,极大的提高了原料成本。日本专利4319206公开了一种软磁Fe基金属玻璃合金,其组分为Fe79-xMoxP10C4B4Si3(x=2~5at.%),非晶形成能力为1.5~4.0mm,但其饱和磁感应强度也只有1.14~1.39T。日本专利WO2008/068899A1的PCT申请公开了一种非晶合金组合物,其可以在空气中制备,不需要高纯氩气的环境,能大大缩短生产周期和降低成本。其组分为FeaBbSicPxCuy,73≤a≤85at.%,9.65≤b≤22at.%,9.65≤b+c≤24.75at.%,0.25≤x≤5at.%,0≤y≤0.35at.%,且0≤y/x≤0.5。其中成分为Fe76Si9B10P5的合金,饱和磁感应强度高达1.51T,具有0.8A/m的极低矫顽力,但是非晶形成能力仅为2.5mm。此申请中还公开了成分为Fe75Si9B10P5Mo1和Fe75Si9B10P5Nb1的块体非晶合金,前者饱和磁感应强度1.43T,但其最大直径为2.5mm;后者饱和磁感应强度为1.45T,其最大直径也只有3.0mm。综上所述,为了获得强非晶形成能力的Fe基非晶合金通常需要在合金中添加大量的非铁磁性元素,然而非磁性元素的加入,会大大降低其饱和磁化强度或者恶化其它软磁性能,同时提高了原材料成本。非晶合金本身独特的无序化原子结构,合金内部缺少位错、孪晶等晶体缺陷,通常在室温以及低于室温的条件下,不能像晶态材料那样,发生持续的塑性变形,变形只发生在高度局域化的剪切带,从而产生脆性断裂,严重制约了块体非晶合金的工业化应用。因此本领域需要开发兼具强非晶形成能力、韧性良好的高饱和磁感应强度铁基块体非晶软磁合金,从而大幅突破铁磁性块体非晶在生产工艺及应用方面的限制与困难度。
技术实现要素:针对现有技术的不足,本发明的目的在于提供一种韧性增强的铁基块体非晶软磁合金及其制备方法。该合金非晶形成能力强、韧性好、且软磁性能优异。为了实现上述目的,本发明采用了以下技术方案:一种韧性增强的铁基块体非晶软磁合金,该合金的表达式为:FexSiaBbPcCdMoeMf,其中所述表达式中M为Cu、Ag、Au中的至少一种;所述表达式中x、a、b、c、d、e和f分别表示各对应组分的原子百分比含量(原子%),且满足以下条件:0.5≤a≤14,0.5≤b≤15,0.5≤c≤14,0.1≤d≤5,0.1≤e≤5,0.2≤f≤1,72≤x≤85,x+a+b+c+d+e+f=100%。上述合金成分设计思路是:采用拥有大非晶形成能力的FeSiBPCMo系合金作为基础合金,添加与合金主元素铁原子有正混合焓的铜原子,铁原子与铜原子有限固溶,原子之间会相互排斥而拒绝进入铜团簇内部而分布在团簇周围;同时,铜的FCC结构与α-Fe的BCC结构的原子排布很好地匹配,使得α-Fe由原来的均质形核转变为异质形核,大大降低了α-Fe的形核势垒,促进了α-Fe晶相的析出,再通过控制成分及冶炼工艺,最终获得的块体非晶合金基体上均匀弥散分布着α-Fe团簇,该团簇在块体非晶受力变形过程中可有效的促进剪切带的增殖与交割,从而使得该块体非晶的韧性得到明显增强。上述合金中,作为一种优选实施方式,所述Fe的原子百分比含量x取值范围为72≤x≤80。上述合金中,作为一种优选实施方式,所述Si的原子百分比含量a的取值范围为1≤a≤9。上述合金中,作为一种优选实施方式,所述B的原子百分比含量b的取值范围为1≤b≤5。上述合金中,作为一种优选实施方式,所述P的原子百分比含量c的取值范围为1≤c≤6。上述合金中,作为一种优选实施方式,所述C的原子百分比含量d的取值范围为0.1≤d≤3,更优选为1≤d≤3。上述合金中,作为一种优选实施方式,所述Mo的原子百分比含量e的取值范围为0.1≤e≤3,更优选为1≤e≤3。上述合金中,作为一种优选实施方式,所述M的原子百分比含量f的取值范围为0.2≤f≤0.8。下面对上述铁基块体非晶软磁合金的成分设计原理进行说明:在本发明的铁基块体非晶软磁合金中,Si元素的原子%要满足:0.5≤a≤14,优选的范围是1≤a≤9。Si元素是构成非晶态合金的常用元素,Si元素的适量添加,不仅能提高合金的热稳定性和居里温度,提高合金的非晶形成能力,而且还能提高B和P等类金属元素在合金中的溶解度,扩大合金的成分范围;当Si元素原子%含量少于0.5时,Si元素的促进形成非晶态合金的作用很难充分发挥出来,而当Si元素原子%含量大于14时,则会降低铁磁性元素的含量,无法获得高饱和磁感应强度的软磁合金。在本发明的铁基块体非晶软磁合金中,B元素的原子%要满足0.5≤b≤15,优选的范围是1≤b≤5。当B原子%小于0.5时,B元素含量太低,则不易形成非晶态合金。而当B原子%大于15时,则会降低合金中铁磁性元素含量而降低合金的饱和磁感应强度。在本发明的铁基块体非晶软磁合金中,P元素的原子%要满足:0.5≤c≤14,优选的范围是1≤c≤6。P元素是构成非晶态合金的常用元素,P元素的适量添加,P和体系里的其他元素都有较大的负的混合热,P的添加有利于提高过冷液相区的稳定性,不仅可以提高合金的非晶形成能力,而且能提高合金的热稳定性和扩大非晶合金的热处理温区范围。当P元素原子%含量少于0.5时,P元素的促进形成非晶态合金的作用难以发挥出来,而当P元素原子%含量大于14时,则会降低铁磁性元素的含量,无法获得高饱和磁感应强度的软磁合金。在本发明的铁基块体非晶软磁合金中,C元素的原子%要满足:0.1≤d≤5,优选的范围是1≤d≤3。C元素是构成非晶态合金的常用元素,C元素的适量添加,有利于提高过冷液相区的稳定性,不仅可以提高合金的非晶形成能力,而且能改善软磁性能。当C元素原子%含量少于0.1时,P元素的促进形成非晶态合金的作用难以发挥出来,而当C元素原子%含量大于5时,则会降低铁磁性元素的含量,无法获得高饱和磁感应强度的软磁合金。在本发明的铁基块体非晶软磁合金中,Mo元素的原子%要满足:0.1≤e≤5,优选的范围是1≤e≤3。Mo元素是大原子元素,Mo元素的适量添加,不仅可以提高合金的非晶形成能力,而且能提高非晶合金的耐腐蚀性能。当Mo元素原子%含量少于0.1时,Mo元素的促进形成非晶态合金的作用难以发挥出来,而当Mo元素原子%含量大于3时,因为Mo是非铁磁性元素,无法获得高饱和磁感应强度的软磁合金。在本发明的铁基块体非晶软磁合金中,M元素因其不溶于Fe,铸造过程中,通过控制熔体的粘度、表面张力,α-Fe团簇从熔体中均匀析出,在块体非晶基底上生成大量的α-Fe团簇,从而达到同时提高饱和磁感强度及塑性变形能力的效果。M元素的原子%要满足:0.2≤f≤1,优选的范围是0.2≤f≤0.8。当M元素的原子%大于1时,合金的非晶形成能力变差,难以制备块体非晶。而当M元素的原子%小于0.2时,在铸造过程中α-Fe团簇不易析出。在本发明的铁基块体非晶软磁合金中,除上述元素外,余量由Fe构成,Fe为磁性元素,为了获得高饱和磁感应强度,必须保证合金含有较高的Fe含量。然而,Fe含量的升高,必然导致非晶形成元素的减少,非晶形成能力下降,无法获得最佳综合性能。Fe含量为72≤x≤85,且优选为72≤x≤80。上述合金中,作为一种优选实施方式,所述合金的非晶基体上均匀分布着α-Fe团簇,所述α-Fe团簇的粒径为2-10nm(比如3nm、5nm、7nm、9nm),所述α-Fe团簇的体积分数为1-20%(比如2%、5%、10%、15%、20%、25%、28%),大量α-Fe团簇在提高软磁性能的同时提高了塑性变形能力。一种上述韧性增强的铁基块体非晶软磁合金的制备方法,具体包括如下步骤:步骤一,按上述表达式中各组分的原子百分比含量进行配料;步骤二,在抽真空后充入保护气体的气氛下采用感应熔炼炉或电弧熔炼炉将所述步骤一配好的原料熔炼均匀,然后随炉冷却或注入模具冷却成母合金锭;步骤三,将所述步骤二得到的母合金锭进行破碎;步骤四,将破碎后的小块母合金锭熔化成钢液,然后采用铸造法将所述钢液快速冷却以制备出所述铁基块体非晶软磁合金。在上述制备方法中,作为一种优选实施方式,在所述步骤一中,所述配料时使用原料的纯度为99.5%以上。在上述制备方法中,作为一种优选实施方式,在所述步骤二中,所述抽真空的真空度为低于5×10-3Pa(比如2×10-3Pa、1×10-3Pa、8×10-4Pa、3×10-4Pa、5×10-5Pa);所述保护气体的气氛为氮气或氩气气氛。在上述制备方法中,作为一种优选实施方式,在所述步骤二中,所述熔炼的温度为1000-1600℃(比如1050℃、1100℃、1150℃、1200℃、1250℃、1300℃、1350℃、1400℃、1450℃、1500℃、1550℃),时间为30-40min(比如32min、34min、36min、38min);更优选地,在所述步骤二中,在原料熔化后保温一定时间以使合金原料熔炼均匀;进一步地,所述保温的时间为5-30min(比如8min、12min、16min、20min、24min、28min)。在上述制备方法中,作为一种优选实施方式,在所述步骤四中,所述破碎后的小块母合金锭熔化成钢液的熔化温度为1000-1600℃(比如1010℃1050℃、1080℃、1140℃、1190℃、1250℃、1340℃、1430℃、1520℃、1580℃)。在上述制备方法中,作为一种优选实施方式,在所述步骤四中,采用所述铸造法制备的所述铁基块体非晶软磁合金时,气氛为氮气、氩气或空气,更优选为空气,铸造温度为1250-1600℃(比如1260℃、1280℃、1300℃、1340℃、1360℃、1380℃、1420℃、1460℃、1530℃、1570℃),喷铸时表面张力不小于0.5KN/m,喷铸时粘度不小于0.5mPas,通过控制熔体的粘度和表面张力可以控制块体非晶的尺寸及团簇析出;更优选地,所述喷铸时表面张力为0.5-2.5KN/m(比如0.6KN/m、0.8KN/m、1.2KN/m、1.5KN/m、1.8KN/m、2KN/m、2.5KN/m),进一步优选为0.5-1.5KN/m;所述喷铸时粘度为0.5-100mPas(比如0.8mPas、1.5mPas、5mPas、10mPas、20mPas、30mPas、40mPas、50mPas、60mPas、70mPas、80mPas、90mPas、95mPas),进一步优选为0.5-20mPas。在上述制备方法中,作为一种优选实施方式,在所述步骤四中,制备所述铁基块体非晶软磁合金时所需的临界冷却速率为1-103℃/s(比如5℃/s、10℃/s、50℃/s、100℃/s、200℃/s、500℃/s、800℃/s、900℃/s、950℃/s),即所述钢液快速冷却时的冷却速率为1-103℃/s。也就是说,采用铸造法制备Fe基非晶合金材料时可以以极低的冷却速率即1-103℃/s来完成,特别是本发明的冷却速率可以小于100℃/s,从而极大的降低了生产设备和生产工艺的要求。在上述制备方法中,作为一种优选实施方式,制备出的所述铁基块体非晶软磁合金为Fe基非晶合金棒材,所述棒材的直径为0.5-5mm(比如1mm、1.5mm、2mm、2.5mm、3mm、3.5mm、4mm、4.5mm、5mm);更优选地,所述棒材的直径大于3.5mm不大于5mm。上述铁基块体非晶软磁合金在制备电子器件铁芯方面的应用。本发明用X射线衍射仪(XRD)确定非晶合金带材和棒材的非晶结构,完全非晶态的合金的XRD图具有宽化的弥散衍射峰,无明显的晶体结构对应的尖锐衍射峰,经检测发现本发明制备的铁基块体非晶软磁合金为非晶结构。本发明用高分辨透射电镜(HRTEM)测试非晶合金的微观结构,确定团簇的类型为α-Fe团簇。用维氏硬度仪测试材料的韧性,发现本发明制备的铁基块体非晶软磁合金具有良好的韧性。本发明用振动样品磁强计(VSM)测试其饱和磁感应强度Bs,用直流B-H回线测试仪测试矫顽力Hc,用阻抗分析仪测磁导率μ。与现有技术相比,本发明的有益效果是:(1)本发明提供的铁基块体非晶软磁合金具有较高的饱和磁感应强度,饱和磁化强度Bs可达1.5T以上,最高可达1.65T;具有低矫顽力,其矫顽力Hc在0-3A/m之间;1kHz下有效磁导率大于10K;具有非常好的韧性,大量α-Fe团簇在块体非晶受力变形过程中有效的促进剪切带的增殖与交割,从而使得该块体非晶的韧性得到明显增强,极大地提高了该材料在工程方面应用的潜力。(2)本发明提供的铁基块体非晶软磁合金具有较强的非晶形成能力,用铸造法将用工业原料配制的合金锭在空气中铸造非晶棒材,其直径可达5mm,足够大的非晶形成能力和低临界冷却速率(<<103℃/s),极大地降低了生产设备和生产工艺的要求,保证了生产过程中质量的稳定性。(3)本发明提供的制备方法能同时提高铁基块体非晶的饱和磁感强度及其塑性变形能力,生产工艺简单、成本低、易于实现工业化,所制得产品具有优异软磁性能及韧性,可作为结构及功能软磁材料,应用于电力、电子、信息、通讯等领域。附图说明图1为本发明制备的Febal.Si9B10P5C1Mo1Cuf(f=0,0.75)合金全非晶棒材HRTEM图片,其中,(a)作为对比,为Febal.Si9B10P5C1Mo1合金全非晶棒材的HRTEM图片,(b)为实施例1中Febal.Si9B10P5C1Mo1Cu0.75合金全非晶棒材的HRTEM图片。图2为本发明经530℃退火10分钟的Febal.Si9B10P5C1Mo1Cuf(f=0,0.75)合金全非晶棒材维氏硬度压痕SEM图片,其中,(a)作为对比,为Febal.Si9B10P5C1Mo1合金全非晶棒材的维氏硬度压痕SEM图片,(b)为实施例1中Febal.Si9B10P5C1Mo1Cu0.75合金全非晶棒材的维氏硬度压痕SEM图片。具体实施方式为了使本发明的内容更容易被清楚的理解,下面根据本发明的具体实施例并结合附图,对本发明作进一步详细的说明。实施例1根据本发明的铁基块体非晶软磁合金的成分范围,我们做了一系列实验。依据本发明的成分和对比例的成分进行配料,具体成分及原子百分比含量参见表1(序号1-22);将配比好的原料放入感应熔炼炉或电弧熔炼炉,抽真空至5×10-3Pa以下,然后充氩气气氛保护,在1400℃下熔炼35min,完全熔化后再保温30min使合金原料熔炼成均匀的钢液,注入模具冷却得到成分均匀的母合金锭;再将母合金锭破碎;然后将破碎后的小块母合金装入石英管内熔化成钢液,熔化温度为1300℃左右,空气中用铜模铸造法将钢液快速冷却,铸造温度为1250℃,喷铸时表面张力1200N/m,喷铸时粘度13mPas,冷却速率为102℃/s,最终制备出直径为0.5~5mm的非晶合金棒材。用X射线衍射仪(XRD)确定非晶棒材的非晶结构。用磁性测试设备测试本发明合金带材的磁性能,用振动样品磁强计(VSM)测试其饱和磁感应强度Bs,用直流B-H回线测试仪测试矫顽力Hc,用阻抗分析仪测磁导率μ,测量得到合金的非晶形成能力、软磁性能见表1。为了对比方便,我们同时也例举多组现有技术的成分合金,具体成分对比的结果均列入表1中。序号1-15为本发明实施例,序号16-17为本发明实施例中序号15的对比例,序号18-22为选取现有技术中性能较好的合金系作为对比例。由表1中的发明例可以看出,本发明的表达式为FexSiaBbPcCdMoeMf的非晶软磁合金,其饱和磁化强度较高,集中在1.5T~1.65T,矫顽力集中在3A/m以下,交流磁导率集中在3.5万至5.8万。本实施例提供的合金的饱和磁化强度明显高于对比例的合金,交流磁导率高于对比例的FeSiB系、硅钢,而合金成本低于对比例。综合比较实施例和对比例可以看出,本发明合金的综合性能优于现有技术的合金。这表现在如下四个方面:(1)软磁性能方面,本发明的合金同时拥有1.5T以上的饱和磁感应强度和3A/m以下的矫顽力,3.5万以上的交流磁导率,其各项性能指标都靠前;(2)合金成本方面,本发明的合金所采用的原料大部分都容易获得,价格较低,与对比例(16-22号)合金相比成本大幅降低;(3)非晶形成能力方面,本发明的合金具有较大非晶形成能力,与对比例(16-22号)合金相比非晶形成能力明显提高,基本可以制成棒材;(4)本发明的合金在非晶基体上弥散分布着2-10nm的α-Fe团簇。综合比较表1中的实施例和对比例可以看出,本发明的合金兼具强非晶形成能力、良好的韧性、优异的软磁性能以及价低的原料成本,可以极大的降低对生产工艺及设备的要求,是一种非常有应用前景的铁基块体非晶软磁合金。表1本实施例合金成分及性能表中,下标bal.表示余量。由图1可以看出,制备的合金成分为Febal.Si9B10P5C1Mo1Cuf(f=0,0.75)的全玻璃棒不含Cu元素时是典型的非晶结构(见图1中的(a)),而添加0.75原子百分比Cu元素后制备的块体非晶合金基体上均匀弥散分布着粒径为2-10nm的α-Fe团簇(见图2中的(b))。由图2可以看出,制备的合金成分为Febal.Si9B10P5C1Mo1Cuf(f=0,0.75)的全玻璃棒不含Cu元素时韧性较差(见图2中的(a)),而添加0.75原子百分比Cu元素制备的块体非晶合金基体因其基底上存在大量2-10nm的α-Fe团簇,该团簇在块体非晶受力变形过程中可有效的促进剪切带的增殖与交割,从而使得该块体非晶的韧性得到明显增强(见图2中的(b))。实施例2根据本发明的铁基纳米晶合金的成分范围,我们做了一系列实验。本实施例制备的高饱和磁感应强度的FexSiaBbPcCdMoeMf合金,该合金的M组分在实施例1的合金表达式FexSiaBbPcCdMoeCuf的基础上有所改变,即其Cu被1原子%以下的Ag、Au中的至少一种元素部分或全部替代。依据本发明的成分进行配料,具体成分及原子百分比含量参见表2(序号1-10);将配比好的原料放入感应熔炼炉或电弧熔炼炉,抽真空至5×10-3Pa以下,然后充氮气气氛保护,在1400℃下熔炼35min,熔化后保温30min使合金原料熔炼成均匀的钢液,注入模具冷却得到成分均匀的合金锭;将母合金锭破碎;将破碎后的小块母合金装入石英管内熔化成钢液,熔化温度为1500℃左右,空气中用铜模铸造法将钢液快速冷却,铸造温度为1400℃,喷铸时表面张力1000N/m,喷铸时粘度10mPas,冷却速率为102℃/s,最终制备出直径为0.5~5mm的非晶合金棒材。用X射线衍射仪(XRD)确定非晶棒材的非晶结构;用磁性测试设备测试本发明合金带材的磁性能,用振动样品磁强计(VSM)测试其饱和磁感应强度Bs,用直流B-H回线测试仪测试矫顽力Hc,用阻抗分析仪测磁导率μ,测量得到合金的非晶形成能力、软磁性能见表2。综合本实施例可以看出,Ag/Au取代Cu对材料性能影响较大,这表现在如下两个方面:(1)软磁性能方面,本发明的合金各项性能指标都有明显提升,特别是矫顽力降至3A/m以下,同时拥有1.5T以上的饱和磁感应强度和3A/m以下的矫顽力;(2)非晶形成能力方面,非晶形成能力有较大提高,最大非晶形成能力为5mm棒材。尽管Ag/Au取代Cu后合金成本大幅上升,但本发明的合金兼具强非晶形成能力、大热处理温区、优异的软磁性能,作为特种结构功能软磁材料有广泛的应用前景。表2本实施例合金成分及性能表中,下标bal.表示余量。实施例3本实施例采用铜模铸造法制备高饱和磁感应强度的Febal.Si12B7P3C1Mo3Cu0.75合金,在不同粘度、表面张力、铸造温度下制备直径为3.5~5mm的非晶合金棒,具体参数参见表3。根据合金成分进行配料;将配比好的原料放入感应熔炼炉或电弧熔炼炉,抽真空至5×10-3Pa以下,然后充氩气气氛保护,在1400℃下熔炼35min,熔化后保温30min使合金原料熔炼成均匀的钢液,注入模具冷却得到成分均匀的合金锭;将母合金锭破碎;将破碎后的小块母合金装入石英管内熔化成钢液,熔化温度为1550℃左右,空气中用铜模铸造法将钢液快速冷却,冷却速率为102℃/s,最终制备出直径为3.5~5mm的非晶合金棒材。用X射线衍射仪(XRD)确定非晶棒材的非晶结构。用磁性测试设备测试本发明合金带材的磁性能,用振动样品磁强计(VSM)测试其饱和磁感应强度Bs,用直流B-H回线测试仪测试矫顽力Hc,用阻抗分析仪测磁导率μ,测量得到合金的非晶形成能力,软磁性能见表3。综合本实施例可以看出,表面张力、粘度、铸造温度对材料性能影响较大。这表现在如下两个方面:(1)软磁性能方面,低粘度及高铸造温度下形成的非晶棒材磁性能优异;(2)非晶形成能力方面,高粘度及低铸造温度有利于形成大块非晶。综合实施例可以看出喷铸过程必须对表面张力、粘度、铸造温度三者进行合理调控。表3实施例3制备的合金及其性能实施例4本实施例采用铜模铸造法制备高饱和磁感应强度的Febal.Si12B7P3C1Mo3Cu0.75合金,在不同冷却速率下制备厚度为0.5~5mm的非晶合金棒,具体参数参见表4。根据合金成分进行配料;将配比好的原料放入感应熔炼炉或电弧熔炼炉,抽真空至5×10-3Pa以下,然后充氩气气氛保护,在1500℃下熔炼20min,熔化后保温20min使合金原料熔炼成均匀的钢液,注入模具冷却得到成分均匀的合金锭;将母合金锭破碎;将破碎后的小块母合金装入石英管内熔化成钢液,熔化温度为1500℃左右,空气中利用铜模铸造法将钢液快速冷却,铸造温度为1400℃,喷铸时表面张力2000N/m,喷铸时粘度10mPas,冷却速率参见表4,利用不同材质的铜模控制冷却速率,最终制备出直径为0.5~5mm的非晶合金棒材。用X射线衍射仪(XRD)确定非晶棒材的非晶结构。用磁性测试设备测试本发明合金带材的磁性能,用振动样品磁强计(VSM)测试其饱和磁感应强度Bs,用直流B-H回线测试仪测试矫顽力Hc,用阻抗分析仪测磁导率μ,测量得到合金的非晶形成能力,软磁性能见表4。综合本实施例可以看出,冷却速率对材料性能影响较大。这表现在如下两个方面:(1)冷却速率降低,α-Fe团簇尺寸及体积分数明显增加,从而达到提升饱和磁感强度的效果,同时大量的α-Fe团簇可以有效阻止剪切带滑移从而达到韧性增强的效果;(2)冷却速率降低,软磁性能仍然优异,且非晶形成能力没有显著降低。综合实施例可以看出该体系可以在较低冷却速率下获得性能优异的块体非晶合金,该通过控制冷却速率调控块体非晶微观结构及性能的方法切实可行。表4实施例4制备的合金及其性能显然,上述实施例仅仅是为清楚地说明所作的举例,而并非对实施方式的限定。对于所属领域的普通技术人员来说,在上述说明的基础上还可以做出其它不同形式的变化或变动。这里无需也无法对所有的实施方式予以穷举。而由此所引伸出的显而易见的变化或变动仍处于本发明创造的保护范围之中。