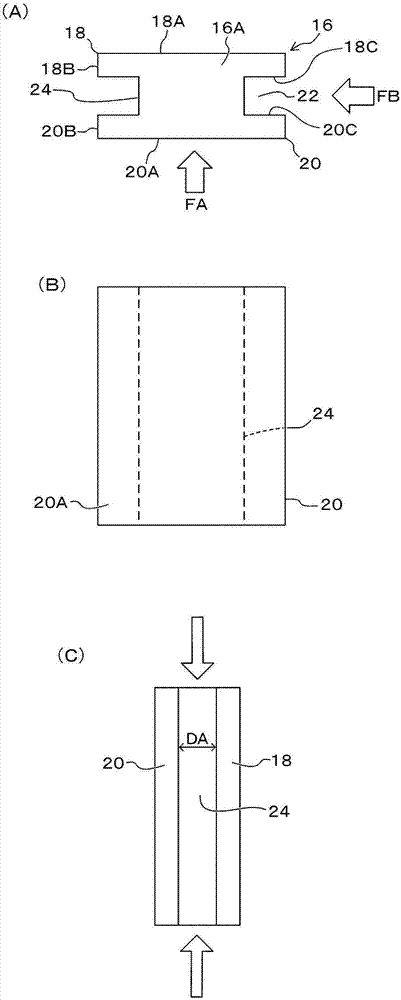
本发明涉及卷绕导线的类型的绕组型电子部件中所使用的磁性体之一,对在两端部具有檐部的轴部卷绕导线的称为鼓形的芯的制造方法,更具体而言,涉及用于芯的高密度化、防止绕组的断线、卷绕不整齐,提高绕线效率的鼓芯。
背景技术:
:由于便携设备的多功能化和汽车的电子化的作用,即使在称为芯片式的小型部件中,也大多使用利用了绕组的部件。特别是在功率类的线圈部件中,从容易对应低电阻化的观点出发,使用在被卷绕绕组的轴部的两端具有檐部的鼓芯,也为了进一步对应于薄型化,正在寻求兼具高性能和尺寸精度的鼓芯。作为上述鼓芯的制造方法,具有例如下述专利文献1所公开的电感芯的制造方法。该技术是为了得到电感特性的称为鼓芯的芯的制造方法,是目前所使用的基于磨削加工的方法。但是,在目前的磨削加工中,以相当于檐部的外周面为基准使工件(成形体)旋转来形成芯部,所以芯部的外周形状成为大致与檐部的外周形状相同的形状。因此,在上述专利文献1记载的制造方法中,通过在对应于檐部的部分的外侧设置旋转基准部,将该旋转基准部的形状形成为椭圆,来将芯部的形状制成椭圆。在该方法中,为了得到鼓芯的形状,需要进行成形、磨削加工、抛光(研磨)。另外,下述专利文献2公开的是通过冲压成形来形成芯片线圈的芯的方法。在利用冲压成形的情况下,需要进行模具的设计,但在该技术中,通过在形成卷芯部的模具中设置圆弧面和冲压承受面,来减少模具的损伤。通过在这样形成的芯上卷绕绕组,能够形成比现有的四边形或多边形的卷芯部的情况更密接于卷芯部的绕组。现有技术文献专利文献专利文献1:特开2014-058007号公报专利文献2:特开平10-294232号公报发明概要发明所要解决的课题但是,在上述专利文献1记载的技术中,组合磨削加工和抛光加工,来形成多种形状的(鼓)芯,能够提高容易进行卷绕的轴的形状的自由度。但是,另一方面,因为需要很多工时数,还有大部分都要通过加工来形成,所以与利用成形来形成芯形状的情况相比,往往会导致尺寸精度变差。另外,为了实现部件的薄型化,需要减小芯的檐的厚度,但在该技术中,因为檐部分也要通过磨削加工和抛光加工来形成,所以容易产生碎屑(chipping),另外,在形成较薄的檐的情况下,具有檐容易产生缺陷之类的课题。进而,因为需要有余量的材料用以进行抛光加工,还有工时数较多,所以也具有导致成本升高之类的课题。另一方面,在上述专利文献2记载的技术中,因为大部分仅通过成形来形成磁性体,所以与利用磨削加工的情况相比,容易确保尺寸精度。但是,因为模具会变成复杂的形状,所以容易损坏,特别是会成为成形时的压力的制约,不能得到高填充的成形体。进而,因为要组合模具,所以容易在使模具组合的部分产生成形毛刺,特别是越薄型化,越难以去除成形毛刺,该成形毛刺会成为作为线圈部件时的导线的断线或缺陷、卷绕不整齐的原因。如上所述,因为至今都没有能够对应于容易卷绕的轴形状和磁性体的高填充化的绕组型线圈部件中所使用的磁鼓,所以希望开发一种称为芯片式的也能够对应于小型部件的绕组型线圈部件中所使用的磁性体。技术实现要素:本发明是着眼于如上所述的那些方面而完成的,其目的在于,提供一种容易卷绕和确保尺寸精度以及能够对应于磁性体的高填充化,防止绕组的断线、卷绕不整齐,可提高绕线效率的绕组型线圈部件中所使用的磁性体的制造方法和线圈部件的制造方法。用于解决课题的技术方案本发明的磁性体的制造方法的特征在于,包括如下工序:成形工序,对磁性材料进行加压成形,形成由相对的一对凸缘部和连接该一对凸缘部的连结部构成的h型钢形状的成形体;磨削工序,以从上述一对凸缘部的一个凸缘部向另一个凸缘部去穿过上述连结部的轴为旋转轴,以上述旋转轴为中心使上述成形体旋转,对上述连结部进行磨削加工,形成在轴部的两端具有一对檐部的鼓形的磨削体;热处理工序,对上述磨削体进行热处理而得到鼓形的磁性体。主要的方式之一的特征在于,上述轴部的与上述磨削工序中的旋转轴正交的方向的截面的外周由相对的一对直线部和将该一对直线部的端部彼此连接的一对弧形部形成,上述檐部具有与上述旋转轴正交的外侧的主面,上述一对直线部与和上述旋转轴正交的面中的上述檐部的主面的长度方向平行。另一方式之一的特征为,在上述磨削工序中,以比上述一对凸缘部的相对面的外缘部之间的间隔窄的宽度对上述连结部进行磨削加工。再另一方式之一的特征为,在上述成形体的上述一对凸缘部的相对面与上述连结部交叉的部分设置有锥面,在上述磨削工序中,上述磨削宽度的两边缘位于上述锥面上。再另一方式之一的特征为,在上述成形体的上述一对凸缘部的相对面上,设置有随着从上述连结部一侧向上述凸缘部的外缘部去该凸缘部的厚度变薄的锥面,在上述磨削工序中,上述磨削宽度的两边缘位于上述锥面上。再另一方式之一的特征为,在上述成形体的上述一对凸缘部的外缘部与上述连结部的端面交叉的部分,设置有上述连结部一侧凹进的锥面,在上述磨削工序中,上述磨削宽度的两边缘位于上述锥面上。本发明的线圈部件的制造方法的特征在于,在通过上述制造方法所形成的磁性体卷绕带覆膜导线。本发明的上述及其他目的、特征、优点从下面的详细说明及附图中即可看明白。发明效果根据本发明,通过形成为上述h型钢形状的成形体,能够施加较高的压力,另外,通过对上述连结部进行磨削加工,能够得到残留有一部分连结部的轴形状。因而,磁性体成为高填充化且容易卷绕的鼓芯。附图说明图1是表示本发明实施例1的鼓芯的制造方法的图。图2是表示上述实施例1的成形体的图,(a)是俯视图,(b)是从箭头fa方向看上述(a)所得的侧视图,(c)是从箭头fb方向看上述(a)所得的侧视图。图3是表示上述实施例1和通过现有的制造方法形成的鼓芯的轴部形状的立体图。图4是表示磨削刀具的宽度比成形体的凸缘部间的槽窄时的磨削体的构造的图,(a)是俯视图,(b)是从箭头fa方向看上述(a)所得的侧视图,(c)是从箭头fb方向看上述(a)所得的侧视图,(d)是外观立体图。图5是表示磨削刀具的宽度比成形体的凸缘部间的槽宽时的磨削体的构造的图,(a)是侧视图,(b)是外观立体图。图6是表示本发明实施例2的鼓芯形成用的成形体的图,(a)是俯视图,(b)是从箭头fa方向看上述(a)所得的侧视图,(c)是从箭头fb方向看上述(a)所得的侧视图。图7是表示上述实施例2的磨削体的图,(a)是俯视图,(b)是从箭头fa方向看上述(a)所得的侧视图,(c)是从箭头fb方向看上述(a)所得的侧视图,(d)是外观立体图。图8是表示本发明实施例3的鼓芯形成用的成形体的图,(a)是俯视图,(b)是从箭头fa方向看上述(a)所得的侧视图,(c)是从箭头fb方向看上述(a)所得的侧视图。图9是表示上述实施例3的磨削体的图,(a)是俯视图,(b)是从箭头fa方向看上述(a)所得的侧视图,(c)是从箭头fb方向看上述(a)所得的侧视图,(d)是外观立体图。图10是表示本发明实施例4的鼓芯形成用的成形体的图,(a)是俯视图,(b)是从箭头fa方向看上述(a)所得的侧视图,(c)是从箭头fb方向看上述(a)所得的侧视图。图11是表示上述实施例4的磨削体的图,(a)是俯视图,(b)是从箭头fa方向看上述(a)所得的侧视图,(c)是从箭头fb方向看上述(a)所得的侧视图,(d)是外观立体图。图12是表示本发明实施例5的成形体及磨削体的俯视图及侧视图。图13是表示本发明的其他实施例的图。符号说明10模具10a凸模10b凹模16成形体16a、16b加压面18、20凸缘部18a、20a主面18b、20b外缘部18c、20c内面22槽24连结部28磨削刀具30磨削体32、34檐部33、36’轴部36a、36b成形面36c、36d磨削面38a、38b直线部38c、38d弧状部40、40’鼓芯(磁性体)42带覆膜导线44a、44b端子电极46封装部50线圈部件60a、60b磨削体62、66台阶部70成形体72、74凸缘部72a、72b、74a、74b内面76连结部76a、76b侧面78锥面80磨削刀具90磨削体92、94檐部96轴部98台阶部150成形体152、154凸缘部152a、152b、154a、154b内面(锥面)156连结部156a、156b侧面160磨削体162、164檐部166轴部168台阶部170倒角200成形体202、204凸缘部202a、202b、204a、204b内面203、205外缘部206连结部206a、206b端面206c、206d侧面208锥面210磨削体212、214檐部216轴部218台阶部250成形体252、254凸缘部256连结部260磨削体262、264檐部266轴部x旋转轴具体实施方式下面,基于实施例对用于实施本发明的最佳方式进行详细说明。【实施例1】首先,参照图1~图3对本发明的实施例1进行说明。本实施例表示的是本发明的鼓芯的基本构造及其制造方法。图1是表示本实施例的鼓芯的制造方法的图。图2是表示磨削为上述鼓芯的形状之前的成形体的图,(a)是俯视图,(b)是从箭头fa方向看上述(a)所得的侧视图,(c)是从箭头fb方向看上述(a)所得的侧视图。图3是表示本实施例和利用现有制造方法形成的鼓芯的轴形状的立体图。根据本发明,通过磁性材料的加压形成,来形成由相对的一对凸缘部和连接该一对凸缘部的连结部构成的相当于h形钢的成形体。此外,上述“相当于h形钢”这一表述不是一定要由钢材形成的意思,而是为容易根据通常建材等所使用的h形钢想起上述成形体的形状而使用的。即,相当于h形钢的成形体是如下的成形体:在从h形的方向看时,从一个凸缘部向另一个凸缘部具有厚度方向的尺寸,且具有与厚度方向垂直方向的宽度方向的尺寸,在从h形槽的某个侧面看时,具有与厚度方向垂直方向的长度方向的尺寸。然后,一边使上述成形体旋转,一边磨削上述连结部,形成在轴部的两端具有一对檐部的鼓形的磨削体,对所得到的磨削体进行热处理,得到鼓形的磁性体,即,鼓芯。如图1(e)所示,本实施例的鼓芯40构成为在卷绕带覆膜导线42的轴部36的两端设有相对的一对檐部32、34的结构。在图示的例子中,上述檐部32、34是宽度w为1.6mm、长度l为2.0mm的长方形。另外,在本实施例中,如图3(a)所示,与上述轴部36的轴正交的截面成为由一对直线部38a、38b和连接这两个直线部38a、38b的端部彼此的一对弧状部38c、38d构成的长圆型。长圆型是由弧分别连接两个平行的直线的两端而成的形状,轴截面的外周如椭圆型那样由连续的线形成。在图示的例子中,轴部36的短边wl为0.8mm,长边l1为1.0mm,上述檐部32、34的宽度w和长度l之比与上述轴部36的短边w1和长边l1的比率相同。这样,通过与檐部32、34的外形相匹配地来设计轴部36的截面尺寸,不管檐部的外形形状如何,都能够使轴截面积按现有比例计比图3(b)所示的截面形状为圆形的轴部36’的现有鼓芯30’提高约30%,能够抑制绕组(卷绕、绕线)时的导线的张力变化,因此能够实现稳定的绕组。上述的形状的轴部36通过利用磨削加工来形成上述圆弧状部38c、38d,能够与上述檐部32、34的外形尺寸相匹配地进行尺寸调节。下面,具体地说明鼓芯40的制造方法。首先,在准备工序中,将磁性颗粒与粘合剂混合,得到成形材料。接着,如图1(a)所示,利用由凸模10a和凹模10b构成的h形的模具10,对上述磁性材料进行加压成形,形成图1(b)所示的h形的成形体16。该成形体16具备一对大致长方形的凸缘部18、20和连接这两个凸缘部18、20的连结部24。如图2(a)所示,上述凸缘部18、20具有:各自的凸缘部18、20的外侧的主面18a、20a;与各自的上述主面18a、20a连接的各自的凸缘部18、20的外缘部18b、20b;与各自的上述外缘部18b、20b和上述连结部16连接的各自的凸缘部18、20的内面18c、20c。图2(a)表示的是从图1(a)所示的加压方向f1看上述成形体16时的俯视图,加压面16a、16b成为h形面。另外,图2(b)表示的是从箭头fa方向看上述图2(a)看到的侧面,凸缘部18、20的外侧的主面整个面都成为平面。图2(b)所示的凸缘部18、20的主面的外形为具有相对的一对长边和相对的一对短边的长方形。或者,凸缘部18、20的主面的外形也存在例如实施了倒角的形状等,在这种情况下,凸缘部18、20的主面的长度方向变成加压方向。进而,图2(c)表示的是从箭头fb方向看图2(a)看到的侧面,成为在中央具有槽22的面。因为上述加压面16a、16b优选整个面为平面,所以即使是存在凹凸的情况下,相对于成形体18的全长也限制在15%以内。例如,如上所述,如果凸缘部18、20的长度l为2.0mm,则通过使长度方向的凹凸的尺寸在加压面16a、16b中分别为0.15mm,或者一方为0.1mm而另一方为0.2mm、最大不超过0.2mm的大小,就不会造成模具的应力集中或影响成形体的均匀性。作为连结部16的长度,可以达到1.7mm。接着,对上述成形体16进行加热,形成固化体。这里的热处理例如在150℃下进行,使混合于上述磁性颗粒中的粘合剂固化。接着,对上述固化体进行磨削加工,形成磨削体30。如图1(c)所示,磨削加工通过以穿过上述凸缘部18、20的主面18a、20a的中央部的轴为旋转轴x使上述固化体旋转,从与旋转方向平行的方向接触磨削刀具28来进行。上述磨削刀具28使用宽度db比上述凸缘部18、20的外缘部的间隔da稍窄的磨削刀具,设置在不从上述槽22突出的位置进行磨削。此外,在实际的切削加工中,因尺寸精度的误差在磨削加工中残留的部分往往会作为台阶(高低差)而残留下来。因此,在以后的实施例中,进行该上述台阶的说明及更理想地进行磨削的方法的说明。此外,也可以使用对上述磨削刀具28或上述模具10的各个角实施了r0.05mm左右的r倒角(chamfering)的磨削刀具28或上述模具10,可防止微小的毛边或缺陷。通过上述磨削工序,可得到图1(d)所示的磨削体30。磨削体30具备:通过上述连结部24的磨削而形成的轴部36;和相对配置于其两端的一对檐部32、34。就上述轴部36而言,轴向截面为长圆型,具有通过上述成形工序而形成的平面状的成形面36a、36b和通过上述磨削工序而形成的曲面状的磨削面36c、36d。上述檐部32、34对应于上述凸缘部18、20。接着,对上述磨削体30进行热处理,形成磁性体。例如,在要求高绝缘的情况下,作为磁性材料,使用ni-zn铁氧体,在要求电流特性的情况下,使用mn-zn系铁氧体,进而在提高电流特性的情况下,使用金属材料。各个磁性材料在与磁性材料相应的最佳温度下进行热处理,通过考虑由热处理引起的收缩,来确定成形体的尺寸。如图1(e)所示,在以上那样得到的鼓芯40中,从檐部34的外侧的主面到侧面形成端子电极44a、44b,在轴部36卷绕带覆膜导线42,将带覆膜导线42的两端与端子电极44a、44b连接,在卷绕完成以后,利用含有磁性粉末等的树脂形成封装部46,由此形成线圈部件50。这样,根据实施例1,对磁性材料进行加压成形,形成由相对的一对凸缘部18、20和连接该一对凸缘部18、20的连结部24构成的截面h形的成形体16。接下来,以穿过上述凸缘部18、20的主面18a、20a的中央部的轴为旋转轴x使上述成形体16的固化体旋转来对上述连结部24进行磨削加工,形成在轴部36的两端具有相对的一对檐部32、34的鼓形的磨削体30。上述檐部32、34具有与上述旋转轴正交的外侧的主面,与旋转轴正交的方向的上述轴部36的截面的外周,由相对的一对直线部和连接该一对直线部的端部彼此的一对弧状部形成。这样得到的磨削体30中,上述一对直线部与上述檐部32、34的主面的长度方向平行。并且,由于通过对上述磨削体30进行热处理得到磁性体即鼓芯40,因此具有如下那样的效果。(1)因为使用的是简单的h形形状的模具10,所以能够减小由加压引起的对模具10的应力集中,能够施以较高的压力。由此,能够提高磁性材料的填充率。因此,上述加压面16a、16b在整个面都是平面的,或即使在带有凹凸的情况下,通过相对于成形体16的全长限制在15%以内,就由此能够得到该效果。根据该方法,例如,即使在对应于檐部厚度0.2mm的厚度的情况下,也能够不损坏模具地得到成形体。(2)因为能够使磁性材料高密度化,所以能够确保檐部32、34的强度。(3)因为通过加压成形时的密度的均匀性,能够抑制烧制时的变形,所以能够改善鼓芯40彼此的啮入(咬入)。(4)因为轴部36的与轴向正交的截面为长圆型,所以能够抑制卷绕时的带覆膜导线42的张力的变化,能够得到稳定的绕组。(5)通过利用磨削加工来形成截面长圆型的轴部36的圆弧状部38c、38d,能够进行上述檐部32、34的尺寸调节。(6)通过形成上述轴部36的截面的外周的直线部与上述檐部32、34的主面的长度方向成为平行的位置关系,能够根据上述檐部32、34的长度方向的长度,调节要磨削的量,从而得到需要的轴截面积。(7)并且,在作为芯片式的部件的典型、具有长度不同的边的部件中使用的、长度比凸缘部18、20的宽度大的部件中,能够更有效地形成轴截面积。这通过将轴截面的外周的直线部的长度设为与凸缘部18、20的长度和宽度的大小之差相应的长度,能够减少要卷绕的区域的浪费。(8)根据本实施例的方法,不容易受到磨削加工的旋转轴x的位置偏离的影响。图13(a)及(b)是表示旋转轴的位置的例子的图,且是对应于上述图1(c)和(d)的工序的侧视图。此外,下面的说明中的“凸缘部”对应于磨削加工后的“檐部”。图13(a)是表示旋转轴向凸缘部20的短边方向偏离了的例子的图。用虚线表示以凸缘部20的中心c为旋转轴进行了磨削时的轴部36,用实线表示以从上述中心c向凸缘部20的短边方向偏离了该短边的长度的10%的位置ca为旋转中心进行了磨削的情况下的轴部36’。即使在这种情况下,也不会减少上述轴部36’的轴截面积,不会对特性产生影响。另外,也不会产生卷绕带覆膜导线42时的影响。直线部38a、38b优选以凸缘部20的长边的40~70%的长度、且分别为相同的长度。但是,如上所述,在旋转轴向该短边方向偏离后的情况下,即使直线部38a、38b的长度不同,如果存在直线部38a、38b,也能够以同样的方式确保上述的效果即要卷绕的区域,不会导致要卷绕的带覆膜导线在比檐部32、34的外周面突出到靠外侧。进而,只要直线部38a、38b的合计的长度为凸缘部的长边的60~140%即可。这即使在此后形成封装部46的情况下,也不需要考虑封装部46的露出等,能够稳定地形成必要量的封装部46。另外,图13(b)是表示旋转轴向凸缘部20的长边方向偏离后的例子的图。在同图中,用虚线表示以凸缘部20的中心c为旋转轴进行了磨削的情况下的轴部36,用实线表示以从上述中心c向凸缘部20的长边方向偏离了该长边的长度的10%的位置cb为旋转中心,进行了磨削时的轴部36’。这样,即使在旋转轴向凸缘部20的长边方向偏离后的情况下,轴截面积也不减少,不会产生对特性的影响。也不会产生卷绕带覆膜导线42时的影响。【实施例2】接着,参照图4~图7对本发明的实施例2进行说明。此外,在与上述的实施例1相同或对应的构成元件上使用同一符号(下面的实施例也同样)。本实施例的制造方法与上述的实施例1同样,通过使用模具对磁性材料进行加压,形成相当于h形钢的成形体,通过对该成形体的连结部进行磨削加工,形成鼓芯的轴部,该方法成为进一步考虑了尺寸精度的方法。图5表示的是使用刀具的宽度db比凸缘部间的间隔da宽的刀具进行了磨削加工时的磨削体60b。图5(a)是磨削体60b的侧视图,图5(b)是外观立体图。在这种情况下,如图5(a)及(b)所示,在轴部36的周围残留有圆形的台阶部66。因此,这里,从檐部32、34沿厚度方向看到的台阶部66的大小设为此后使用的带覆膜导线的粗细度的一半以下。由此,能够防止导线在卷绕时挂在(钩挂、搁浅)该台阶部66的情况。进而,作为与上述相反的例子,图4表示的是使用磨削刀具的宽度db比一对凸缘部的外缘部的间隔da窄的刀具进行了磨削加工时的磨削体60a。图4(a)是从成形体的加压方向看到的俯视图,图4(b)是从箭头fa方向看上述(a)看到的侧视图,图4(c)是从箭头fb方向看上述(a)看到的侧视图,图4(d)是立体图。如这些图4(a)~(d)所示,在磨削刀具28的宽度db比凸缘部间的间隔da窄的情况下,在磨削加工时,磨削刀具28与凸缘部18、20不接触,但在轴部36的上下将残留台阶部62。因此,这里,从檐部32、34在厚度方向上看到的台阶部62的大小设为之后使用的带覆膜导线的粗细度的一半以下。由此,能够防止导线在卷绕时挂在该台阶部62。另外,在使用磨削刀具的宽度db比一对凸缘部的外缘部的间隔da窄的刀具进行了磨削加工的情况下,除具有上述的实施例1的效果以外,还具有如下所述的效果。即,通过磨削刀具28不与凸缘部18、20接触,(1)不管磨削时的负荷与凸缘部18、20无关,都能够得到具有较薄的檐部32、34的磁性体即鼓芯40。(2)在大致保持凸缘部18、20的尺寸精度的状态下,能够形成檐部32、34的厚度的尺寸精度。(3)檐部32、34的内面为平滑,毛边、缺陷等少,能够抑制带覆膜导线42的损坏。另外,在将带覆膜导线42与檐部32、34的侧面接合的情况下,可得到与端子电极44a、44b的连接稳定性。因此,带覆膜导线42的粗细度没有限制,细导线也不会断线,粗导线也能够接合。基于上述内容,由于从尺寸精度上不容易进一步消除上述台阶62、66,下面表示的是即使有少许尺寸误差也不会产生带覆膜导线42的断线或卷绕不整齐的方法。具体而言,在以下本实施例2中,通过在利用加压成形而形成的成形体的一对凸缘部的内侧设置锥面,且以磨削刀具28的两端与该锥面接触的方式进行磨削加工,来制作台阶部的角被倒角了的状态,可防止上述的断线或卷绕不整齐。图6是表示实施例2的鼓芯形成用的成形体的图,(a)是俯视图,(b)是从箭头fa方向看上述(a)的侧视图,(c)是从箭头fb方向看上述(a)的侧视图。图7是表示磨削体的图,(a)是俯视图,(b)是从箭头fa方向看上述(a)的侧视图,(c)是从箭头fb方向看上述(a)的侧视图,(d)是外观立体图。在本实施例中,如图6(a)~(c)所示,形成为在加压成形后的成形体70的一对凸缘部72、74的相对面与连结部76交叉的部分设有锥面78的形状。具体而言,在凸缘部72的内面72a与连结部76的侧面76a相交的部分、上述凸缘部72的内面72b与上述连结部76的侧面76b相交的部分、凸缘部74的内面74a与连结部76的侧面76a相交的部分、凸缘部74的内面74b与连结部76的侧面76b相交的部分这四个部位,沿着图6(b)中箭头所示的加压方向设置锥面78。在将上述凸缘部72、74的尺寸设为与上述实施例1相同的情况下,如图6(a)及(c)所示,形成上述锥面78的范围是上述凸缘部72、74的厚度方向的宽度t1为0.05~0.1mm程度的范围。而且,如图6(c)所示,以磨削刀具80的两端都接触到上述锥面78的方式来定位,进行磨削加工。即,以残留上述锥面78的一部分的方式进行磨削加工。此外,这里,用具体数值表示了锥面78的宽度,但为了确保绕组空间,可以设为轴部的长度的1/6以下,在考虑带覆膜导线42的断线等时,设为带覆膜导线42的粗细度的1/4以上。另外,在使用扁线作为带覆膜导线42的情况下,设为带覆膜导线42的角的曲率以上等,根据需要适当设定。当如上那样定位来进行磨削加工时,可得到在轴部96的两侧具有一对檐部92、94的磨削体90。在上述轴部96的上下残留有台阶部98,在该台阶部98与檐部92、94的内面之间残留有上述锥面78,因为该部分作为倒角发挥功能,所以在卷绕带覆膜导线42时不会发生钩挂(搁浅),能够防止卷绕不整齐或断线。另外,因为使得在上述锥面78具有一定程度的宽度,只要磨削刀具80的两端与该宽度的范围内接触即可,所以即使有定位的少许偏离或尺寸精度的误差,也可得到同样的效果。其他基本作用、效果与上述的实施例1同样。【实施例3】接着,参照图8和图9对本发明的实施例3进行说明。本实施例3与上述的实施例2同样,通过在利用加压成形而形成的成形体设置锥面,且以磨削刀具的两端与该锥面接触的方式进行磨削加工,由此制作台阶部的角被倒角了的状态,能够防止上述的断线或卷绕不整齐。图8是表示实施例3的鼓芯形成用的成形体的图,(a)是俯视图,(b)是从箭头fa方向看上述(a)的侧视图,(c)是从箭头fb方向看上述(a)的侧视图。图9是表示磨削体的图,(a)是俯视图,(b)是从箭头fa方向看上述(a)的侧视图,(c)是从箭头fb方向看上述(a)的侧视图,(d)是外观立体图。在本实施例中,如图8(a)~(c)所示,在加压成形后的成形体150的一对凸缘部152、154的相对面,设有该凸缘部152、154的厚度从连结部156侧向上述凸缘部152、154的外缘部去变薄的锥面。具体而言,凸缘部152的内面152a成为以该凸缘部152的厚度从连结部156的侧面156a向凸缘部152的外缘部去逐渐变薄的方式倾斜的锥面。同样,凸缘部内面152b成为以该凸缘部152的厚度从连结部侧面156b向凸缘部152的外缘部去逐渐变薄的方式倾斜的锥面。另一凸缘部154侧也同样,凸缘部154的内面154a成为以该凸缘部154的厚度从连结部侧面156a向凸缘部154的外缘部去逐渐变薄的方式倾斜的锥面,凸缘部内面154b成为以该凸缘部154的厚度从连结部侧面156b向凸缘部154的外缘部去逐渐变薄的方式倾斜的锥面。这些锥面(即,凸缘部内面152a、152b、154a、154b)在将上述凸缘部152、154的尺寸设为与上述实施例1相同的情况下,如图8(a)和(c)所示,上述凸缘部152、154的厚度方向的宽度t2成为0.05~0.1mm程度。并且,如图8(c)所示,以磨削刀具80的两端都与上述锥面接触的方式定位,进行磨削加工。此外,这里,用具体数值表示了锥面的宽度,但为了确保檐部的强度,可以设为檐部的厚度的1/3以下,在考虑带覆膜导线42的断线等时,设为带覆膜导线42的粗细度的1/4以上。另外,在使用扁线作为带覆膜导线42的情况下,设为带覆膜导线42的角的曲率以上等,根据需要适当设定。当如上所述那样定位来进行磨削加工时,能够得到在轴部166的两侧具有一对檐部162、164的磨削体160,并且在上述轴部166的周围残留有圆形的台阶部168,因为该台阶部168与檐部162、164的内面通过锥面170连接,所以在向轴部166卷绕带覆膜导线42时,也不会使带覆膜导线42挂在上述台阶部168,能够防止卷绕不整齐或断线。另外,因为在檐部162、164的内面残留有锥面152a、152b、154a、154b,所以带覆膜导线42难以挂在檐部162、164的外缘部。并且,因为将成形体150的凸缘部152、154的内面152a、152b、154a、154b整个面形成为锥面,所以即使偏离一个凸缘部侧地磨削加工或磨削加工的宽度的尺寸精度有误差,也可得到同样的效果。其它基本作用、效果都与上述的实施例1同样。【实施例4】接着,参照图10和图11对本发明的实施例4进行说明。本实施例4与上述的实施例2同样,通过在利用加压成形而形成的成形体设置锥面,以磨削刀具的两端与该锥面接触的方式进行磨削加工,由此制作台阶部的角被倒角了的状态,可防止上述的断线或卷绕不整齐。图10是表示实施例4的鼓芯形成用的成形体的图,(a)是俯视图,(b)是从箭头fa方向看上述(a)的侧视图,(c)是从箭头fb方向看上述(a)的侧视图。图11是表示磨削体的图,(a)是俯视图,(b)是从箭头fa方向看上述(a)的侧视图,(c)是从箭头fb方向看上述(a)的侧视图,(d)是外观立体图。在本实施例中,如图10(a)~(c)所示,在加压成形后的成形体200的一对凸缘部202、204的外缘部203、205与连结部206的端面206a、206b交叉的四个部分,设置有上述连结部206侧凹进的锥面208。具体而言,在连结部206的一个端面206a,以该端面206a的中央侧凹进的方式在与凸缘部202、204的外缘部203、205交叉的部分分别设置锥面208。同样,在连结部206的另一端面206b,以该端面206b的中央侧凹进的方式在与凸缘部202、204的外缘部203、205交叉的部分分别设置锥面208。在共计四个部位设置锥面208。这些锥面208在将上述凸缘部202、204的尺寸设为与上述实施例1相同的情况下,如图10(a)和(c)所示,上述凸缘部202、204的厚度方向的宽度t3成为0.05~0.1mm程度。而且,如图10(c)所示,以磨削刀具80的两端都与上述锥面208接触的方式进行磨削加工。此外,这里,用具体数值表示了锥面208的宽度,但为了确保檐部的强度,可以形成为该檐部的厚度的1/3以下,在考虑带覆膜导线42的断线等时,形成为带覆膜导线42的粗细度的1/4以上。另外,在使用扁线作为带覆膜导线42的情况下,设为带覆膜导线的角的曲率以上等,根据需要适当设定。当如上所述那样定位来进行磨削加工时,可得到在轴部216的两侧具有一对檐部212、214的磨削体210。在上述轴部216的上下残留有台阶部218,在该台阶部218与檐部212、214之间残留有上述锥面208,因为该部分作为倒角发挥功能,所以在卷绕带覆膜导线42时不会发生钩挂,能够防止卷绕不整齐或断线。另外,因为在上述锥面208具有一定程度的宽度,且只要磨削刀具80的两端与该宽度的范围内接触即可,所以不管定位有些许偏离,还是在尺寸精度上产生了误差,均可得到同样的效果。其他基本作用、效果都与上述的实施例1同样。【实施例5】接着,参照图12对本发明的实施例5进行说明。本实施例表示的是形成本发明的鼓芯的材料和尺寸的具体例。图12(a-1)是从加压方向看本实施例的成形体的俯视图,图12(a-2)是从箭头fa方向看上述(a-1)的侧视图。图12(b-1)和(b-2)是对上述成形体进行了切削加工而成的切削体的俯视图和侧视图。如这些图所示,本实施例的成形体250是与上述实施例4大致同样的结构,且形成为由连结部256连接相对的一对凸缘部252、254的h形形状。另外,磨削体260成为由截面长圆型的轴部266连接一对檐部262、264的形状。下面的表1表示的是对应于以上各部的磁性体的尺寸例。【表1】(单位:mm)c×a×b2.5×2.0×0.92.5×1.6×0.852.0×1.25×0.81.6×0.8×0.6c2.5221.6a21.61.250.8b0.90.850.80.7b10.250.230.20.2b20.250.230.20.2b30.40.390.40.3b40.30.310.350.25a10.90.750.5750.38c11.41.11.2751.15此外,上述表1的尺寸例是使用合金颗粒时的磁性体的尺寸。在合金颗粒的情况下,成形体250和磁性体成为大致相同的尺寸。这是因为即使进行热处理也几乎不产生收缩。与此相对,在铁氧体材料的情况下,考虑分别自成形体250收缩16%左右来设定成形体250的尺寸。作为磁性材料,例如,ni-zn铁氧体、mn-zn铁氧体分别通过在氧气氛1100℃、氮气氛1150℃(范围为1000~1200℃)下进行烧制来形成磁性体。另外,成形时和磨削时的尺寸变成上述表1的各数字另加上16%所得的尺寸。因为要进行收缩,所以成形时的填充率很重要,由于填充率的偏差,会产生变形或微小裂纹,但在本发明中,因为是使用h型的模具进行加压成形而成的均匀的成形体,所以不会产生上述变形或微小裂纹等。另外,作为合金磁性颗粒有fesial或fesicr等,在氧气氛750℃(范围600~900℃)下进行烧制。通过该热处理能够形成氧化膜,得到磁性体。因为不产生收缩,所以没有变形,磁性体尺寸的稳定性良好。此外,这里所示的材料、尺寸只是一个例子,也可以使用其他公知的各种材料,还可以根据线圈部件的用途适当变更尺寸。此外,本发明不局限于上述的实施例,在不脱离本发明主旨的范围内,能够进行各种变更。例如,也包含下面的实施例。(1)上述实施例所示的形状、尺寸只是一个例子,可以根据需要适当变更。另外,鼓芯的轴部的截面形状也是一个例子,在上述实施例1中形成为长圆型,但弧的部分不需要为圆弧,也可以根据需要适当组合曲率不同的弧等进行变更。另外,鼓芯的檐部34的外侧的主面也在上述实施例1中形成为长方形,但可以带有槽或实施倒角等根据需要适当变更。(2)上述实施例1或实施例5所示的尺寸、材料也只是一个例子,可根据线圈部件的用途等,在实现同样效果的范围内适当变更。(3)也可以组合上述实施例2~实施例4而使设置锥面的部位为多个。(4)上述实施2~实施例4所示的锥面的形成范围也只是一个例子,可在实现同样效果的范围内适当变更。(5)上述实施例所示的端子电极也只是一个例子,可适当设计变更来实现同样的效果。(6)由本发明的制造方法形成的鼓芯优选用于例如绕组电感器等绕组部件,但不局限于此,可广泛应用于变压器、共模扼流线圈等。产业上的可利用性根据本发明,通过如下工序来制造鼓芯:成形工序,对磁性材料进行加压成形,形成由相对的一对凸缘部和连接该一对凸缘部的连结部构成的截面h形的成形体;磨削工序,以上述凸缘部的主面的中央部为中心使上述成形体旋转,对上述连结部进行磨削加工,形成在轴部的两端具有一对檐部的鼓形的磨削体;热处理工序,对上述磨削体进行热处理,得到鼓形的磁性体。因此,轴截面形状的自由度高,可应对磁性体的高填充化,可防止绕组的断线、卷绕不整齐,能够提高绕线效率,所以能够应用于线圈部件用的鼓芯的用途。当前第1页12