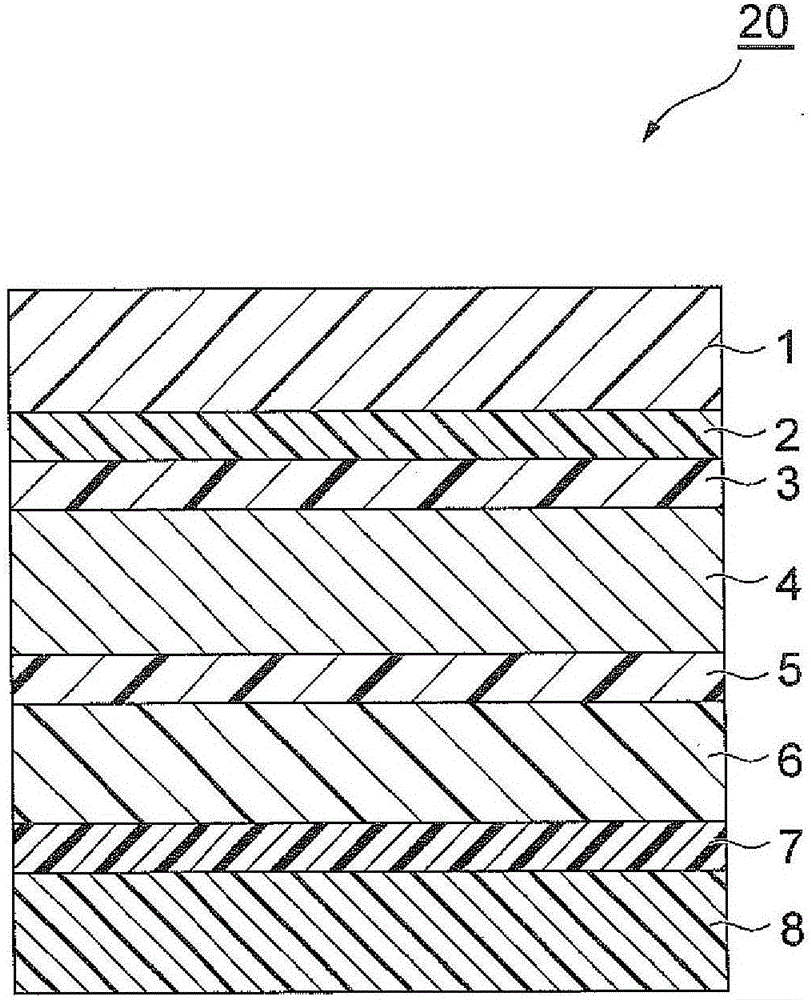
本实用新型涉及二次电池用外包装材料及二次电池。
背景技术:
:近年来,作为个人电脑、手机等便携终端装置、摄像机、卫星及车辆等中使用的蓄电装置,大力开发了能够超薄型化或小型化的二次电池。作为这种电池中使用的外包装材料,由多层膜构成的层压外包装材料(例如具有基材层/第1粘接层/金属箔层/第2粘接层/热熔融粘合树脂层等层叠构成的外包装材料)备受关注。由多层膜构成的层压外包装材料与作为电池要素的容器使用的以往的金属制罐不同,在重量轻、放热性高、可自由地选择形状的方面很优异。二次电池例如通过以下方法制造:通过冷成型在多层膜的二次电池用外包装材料的一部分上形成凹部,在该凹部内收容电池内容物(正极、隔膜、负极及电解液等),将未形成有凹部的剩余部分折回,将边缘部分在夹着从上述正极及负极延伸的电极端子的情况下进行热熔融粘合来实施密封,由此制得(以下也记为“单侧成型加工电池”)。近年来,为了有效地收容更多的内容物以提高能量密度,还制造了在相贴合的二次电池用外包装材料的两侧形成有凹部的二次电池(以下也记为“两侧成型加工电池”)。这种二次电池中,为了获得高的能量密度,要求形成更深的凹部。但是,当加深凹部时,在利用金属模具的成型加工时,容易在拉伸率高的部位即凹部的边或角的部分上产生针孔或断裂。为了抑制在对凹部加深成型(深拉深成型)时的针孔或者断裂,例如在日本专利3567230号公报中,在二次电池用外包装材料的基材层中使用拉伸聚酰胺膜或拉伸聚酯膜等膜来对金属箔进行保护。技术实现要素:实用新型要解决的技术问题但是,根据日本专利3567230号公报中记载的技术虽然能够获得成型性,但在电池制造时相对于金属箔层成为内侧的未拉伸膜在热熔融粘合时会发生熔融而变薄,正极及负极等电池要素或电极端子与金属箔层容易产生电连接,因此有时会产生绝缘性降低的问题。另外,在日本专利3567230号公报记载的构成中,成型加工后有时外包装材料会翘曲。成型加工后的翘曲成为外包装材料的性能降低或加工性降低的原因。而另一方面,当相对于金属箔层成为内侧的层变得过厚时,有时水分会浸入到电池内部与电池内容物等发生反应、产生氢氟酸等物质而将电池要素或金属箔层腐蚀。本实用新型鉴于上述问题而作出,其目的在于提供在确保成型性及水蒸汽阻隔性的同时可抑制绝缘性降低、能够减少成型后的翘曲的二次电池用外包装材料及使用了该材料的二次电池。用于解决技术问题的方法本实用新型提供一种二次电池用外包装材料,其为在第1基材层的一个面上依次层叠至少金属箔层、第2基材层及热熔融粘合树脂层而成的二次电池用外包装材料,其中,上述第2基材层直接层叠在上述金属箔层上或者隔着防腐蚀处理层层叠在上述金属箔层上,上述第1基材层由含有热固化性树脂或热塑性树脂的树脂组合物形成,上述第2基材层由含有热固化性树脂的树脂组合物形成。根据上述二次电池用外包装材料,可以在确保成型性及水蒸汽阻隔性的同时抑制绝缘性的降低、可以减少成型后的翘曲。上述二次电池用外包装材料中,优选上述金属箔层直接层叠在上述第1基材层的一个面上。二次电池用外包装材料通过具备上述构成,可以进一步减少自外包装材料端部的水蒸汽浸入量,另外能够进一步减薄整个外包装材料,能够使二次电池进一步薄型化及小型化。上述二次电池用外包装材料中,优选上述第1基材层的厚度为5μm以上且30μm以下、上述第2基材层的厚度为5μm以上且30μm以下。另外,优选上述第1基材层及第2基材层的厚度之差为15μm以下。上述二次电池用外包装材料中,优选上述第1基材层及上述第2基材层由相互间同种的树脂材料形成。二次电池用外包装材料通过具备上述构成,可以进一步减少成型加工后的翘曲量。上述二次电池用外包装材料中,优选上述金属箔层的厚度为20μm以上且80μm以下。通过金属箔层的厚度为上述范围内,可以更为平衡性良好地获得成型性及能量密度。上述二次电池用外包装材料中,优选在上述第1基材层的另一个面上形成有含有由脂肪酰胺构成的润滑剂的涂布层、或者在上述热熔融粘合树脂层上形成有含有由脂肪酰胺构成的润滑剂的涂布层。二次电池用外包装材料通过具备上述构成,可以进一步提高成型性。本实用新型另外还提供一种二次电池,其具备电池要素和上述二次电池用外包装材料。实用新型效果根据本实用新型,能够提供在确保成型性及水蒸汽阻隔性的同时可抑制绝缘性降低、能够减少成型后的翘曲的二次电池用外包装材料及二次电池。附图说明图1为本实用新型一个实施方式的二次电池用外包装材料的概略截面图。图2为本实用新型另一实施方式的二次电池用外包装材料的概略截面图。图3为本实用新型又一实施方式的二次电池用外包装材料的概略截面图。图4为表示使用本实用新型一个实施方式的二次电池用外包装材料制造二次电池的工序的立体图,(a)表示准备二次电池用外包装材料的状态、(b)表示准备加工成压花型的二次电池用外包装材料和电池要素的状态、(c)表示折回二次电池用外包装材料的一部分并将端部熔融的状态、(d)表示将折回的部分的两侧向上方折回的状态。符号说明1第1基材层、2第1粘接剂层、3、5防腐蚀处理层、4金属箔层、6第2基材层、7粘接树脂层、8热熔融粘合树脂层、10、20、30(二次电池用)外包装材料、50压花型外包装材料、52成型加工区域(凹部)、54盖部、56电池要素、58导线(金属端子)、60二次电池。具体实施方式以下对本实用新型的实施方式详细地进行说明。但本实用新型并非限定于以下的实施方式。本实用新型的外包装材料作为基本构成具备第1基材层、金属箔层、第2基材层及热熔融粘合树脂层,具体地说具备在第1基材层的一个面上依次层叠至少金属箔层、第2基材层及热熔融粘合树脂层而成的结构。[二次电池用外包装材料10]首先,对本实用新型一个实施方式的二次电池用外包装材料10(以下也仅记为“外包装材料10”)进行说明。外包装材料10如图1所示,具有依次层叠第1基材层1、第1粘接剂层2、金属箔层4、防腐蚀处理层5、第2基材层6、粘接树脂层7及热熔融粘合树脂层8而成的层叠结构。外包装材料10例如通过如下方法制造:在金属箔的一个面上形成防腐蚀处理层5,在金属箔的另一个面上介由第1粘接剂粘合第1基材材料,在防腐蚀处理层5上形成第2基材层6,在第2基材层6上介由粘接树脂形成热熔融粘合树脂层8。其中,当第2基材层6由能够赋予防腐蚀功能的后述的含有特定热固化性树脂的树脂组合物形成时,外包装材料10也可不具备防腐蚀处理层5。(第1基材层1)第1基材层1起到将制造电池时的加压热熔融粘合工序(后述的工序S3)中的耐热性赋予外包装材料、抑制在加工或流通时可能产生的针孔的作用。另外,第1基材层1起到防止压花成型工序(后述的工序S2)中的金属箔层4的断裂或防止金属箔层4与其他金属的接触以确保绝缘性的作用。在外包装材料10的制造中,在金属箔的一个面上介由后述的第1粘接剂粘合第1基材材料,上述第1基材材料变为第1基材层1,上述第1粘接剂变为第1粘接剂层2,上述金属箔变为金属箔层4。粘合第1基材材料时,为了促进粘接性,可以在室温~100℃的范围内进行熟化(保养)处理。熟化时间例如为3~10日。外包装材料10的制造中的上述第1基材材料为含有热固化性树脂或热塑性树脂的树脂膜,作为上述树脂膜中含有的热固化性树脂或热塑性树脂,例如可举出聚酯树脂、聚氨酯树脂、聚酰胺树脂、聚酰亚胺系树脂、氟系树脂、聚偏氯乙烯树脂及丙烯酸树脂。构成上述树脂膜的树脂可以单独使用1种或者并用2种以上。作为聚酰亚胺系树脂,可举出聚酰亚胺树脂、聚酰胺酰亚胺树脂及聚醚酰亚胺树脂等。作为氟系树脂,可举出聚四氟乙烯、聚氯三氟乙烯、聚偏氟乙烯、聚氟化乙烯、全氟烷氧基氟树脂、四氟化乙烯-六氟化丙烯共聚物、乙烯-四氟化乙烯共聚物及乙烯-氯三氟乙烯共聚物等。第1基材材料含有热固化性树脂时,树脂膜还可以进一步含有固化剂。作为固化剂,可举出异氰酸酯树脂、环氧树脂及三聚氰胺树脂等。第1基材材料含有热固化性树脂时,第1基材层1可以称作第1基材材料的固化物。上述树脂膜从成型性、耐热性、耐刺穿性、绝缘性及耐化学试剂性等的观点出发,优选是聚酯树脂膜或聚酰胺树脂膜,更优选是二轴拉伸聚酯树脂膜或二轴拉伸聚酰胺树脂膜。第1基材材料可以是由1张膜构成的单一膜,也可以是利用干式层压粘接剂将2张以上的膜粘合在一起的复合膜。上述树脂膜中还可在内部分散有阻燃剂、润滑剂、防粘附剂、抗氧化剂、光稳定剂、粘合赋予剂及防静电剂等添加材料,含有这些添加剂(优选润滑材料)的涂布层还可以形成在上述树脂膜的表面上(即第1基材层1的另一个面上)。作为润滑剂,例如可举出油酰胺、芥酰胺、硬脂酰胺、山嵛酰胺、乙烯双油酰胺及乙烯双芥酰胺等脂肪酰胺。通过润滑剂分散在上述树脂膜的内部或者上述涂布层形成在上述树脂膜的表面上,有外包装材料10的成型性提高的倾向。作为防粘附剂,可举出二氧化硅等各种填料。添加剂可单独使用1种,也可并用2种以上。第1基材层1的厚度与作为第1基材材料的树脂膜大致相同,从耐刺穿性、绝缘性及压花加工性等的观点出发,优选为5μm以上且30μm以下、更优选为8μm以上且25μm以下。第1基材层1的厚度为5μm以上时,有成型性、耐针孔性及绝缘性提高的倾向。另一方面,当第1基材层1的厚度为30μm以下时,易于抑制成本的增加及能量密度降低、与第2基材层6的平衡易于达成。第1基材层1为了耐擦伤性及润滑性改善等,可以在表面具有凹凸。(第1粘接剂层2)外包装材料10中,第1粘接剂层2形成在第1基材层1与金属箔层4之间。即,外包装材料10中,第1基材层1隔着第1粘接剂层2形成在金属箔层4的另一个面(与形成有防腐蚀处理层5的一侧相反侧的面)上。第1粘接剂层2是将第1基材层1与金属箔层4粘接的层,从利用第1基材层1保护压花成型时的金属箔层4的断裂的观点出发,优选具有随动性。作为形成第1粘接剂层2的材料的第1粘接剂,可以使用以聚酯多元醇、聚醚多元醇或丙烯酸多元醇等为主剂、以芳香族系或脂肪族系异氰酸酯等为固化剂的双组分固化型粘接剂。上述第1粘接剂优选固化剂的NCO基与主剂的OH基的摩尔比[NCO/OH]为1以上且10以下、更优选为2以上且5以下。[NCO/OH]为1以上时,可获得更为优异的粘接性。另外,[NCO/OH]为10以下时,具有可抑制过剩的交联反应、防止第1粘接剂层2变脆、变硬或者无法确保伸长量而无法获得成型性等不良情况的倾向。第1粘接剂中还可进一步添加热塑性弹性体、粘合赋予剂、填料、颜料及染料等。第1粘接剂层2的厚度从粘接强度、随动性及加工性等方面出发,优选为0.5μm以上且10μm以下、更优选为1μm以上且5μm以下。此外,第1粘接剂层2的厚度与涂布第1粘接剂并干燥后的干燥厚度基本相同。(金属箔层4)金属箔层4起到防止水分向电池内浸入的作用(即具有水蒸汽阻隔性)。外包装材料10中,金属箔层4配置在第1粘接剂层2与第2基材层6之间。另外,金属箔层4为了进行深拉深成型而具有延展性。在外包装材料的制造中,作为成为金属箔层4的金属箔,可以使用铝及不锈钢等各种金属箔,从重量(比重)、防湿性、加工性或成本的观点出发,优选铝箔。作为成为金属箔层4的铝箔,可以使用公知的软质铝箔,从耐针孔性及成型时的延展性的方面出发,优选含铁的铝箔。铝箔(100质量%)中的铁的含量优选为0.1质量%以上且9.0质量%以下、更优选为0.5质量%以上且2.0质量%以下。铁的含量为上述下限值以上时,耐针孔性及延展性进一步提高。铁的含量为上述上限值以下时,柔软性进一步提高。金属箔层4的厚度与上述金属箔的厚度基本相同,优选为20μm以上且80μm以下、更优选为25μm以上且60μm以下。金属箔层4的厚度为20μm以上时,成型时难以发生针孔或断裂。另一方面,当金属箔层4的厚度为80μm以下时,易于在维持各种性能的同时抑制成本的增加或者能量密度降低。(防腐蚀处理层5)防腐蚀处理层5例如为锂离子二次电池的情况下起到抑制因电解液与水分的反应所产生的氢氟酸对金属箔层4表面的腐蚀的作用。另外,防腐蚀处理层5具有作为针对金属箔层4和第2基材层6的锚定层的功能。防腐蚀处理层5例如通过在金属箔层4的一个面上涂布防腐蚀处理剂并进行干燥、从而形成在金属箔层4的一个面上。防腐蚀处理剂的涂布方法并无特别限定,可以采用凹版涂布、逆涂、辊涂或棒涂等各种方法。防腐蚀处理层5例如可通过使用了由铬酸盐和磷酸盐和氟化物和各种热固化性树脂构成的防腐蚀处理剂的镀铬处理、使用了由稀土类元素氧化物(例如氧化铈等)和磷酸盐和各种热固化性树脂构成的防腐蚀处理剂的二氧化铈溶胶处理等形成。防腐蚀处理层5只要是起到上述作用的层,则并不限定于通过上述处理形成的层,例如也可以通过磷酸盐处理及勃姆石处理等形成。另外,防腐蚀处理层5可以是单层也可以是多层。例如防腐蚀处理层5还可以具有在使用上述防腐蚀处理剂形成的层上涂布作为顶涂剂的树脂(顶涂层)而成的2层以上的结构。防腐蚀处理层5的厚度与防腐蚀处理剂的涂布层(及顶涂层)的干燥厚度大致相同,从防腐蚀功能和作为锚定层的功能的观点出发,优选为5nm以上且1μm以下、更优选为10nm以上且200nm以下。(第2基材层6)第2基材层6起到防止压花成型时的金属箔层4的断裂或针孔发生、并防止金属箔层4与电池要素或导线(金属端子)的接触以易于获得两者的电绝缘性的作用。进而,外包装材料通过在金属箔层4的两侧分别具备第1基材层1和第2基材层6,可以减少成型加工时的翘曲。第2基材层6仅隔着防腐蚀处理层5层叠在金属箔层4上。外包装材料10不具备防腐蚀处理层5时,将第2基材层6直接层叠在金属箔层4上。即,第2基材层6不介由粘接剂层地形成在金属箔层4或防腐蚀处理层5上。因此,可以减薄外包装材料整体的厚度,与介由粘接剂层形成第2基材层6的情况相比、可以削减工序数及制造成本。另外,外包装材料10通过不具备粘接剂层,可以减少自外包装材料端部的水蒸汽浸入量。此时,第2基材层6优选通过将第2基材材料涂布或涂饰在金属箔层4或防腐蚀处理层5上来形成。第2基材材料为含有热固化性树脂的树脂组合物,第2基材层6可以称作第2基材材料的固化物。上述热固化性树脂优选是选自聚酯树脂、聚氨酯树脂、聚酰胺树脂、聚酰亚胺系树脂、氟系树脂、聚偏氯乙烯树脂及丙烯酸树脂中的至少1种树脂。第2基材层6通过由含有上述热固化性树脂的树脂组合物形成,可以抑制在热熔融粘合时第2基材层6变薄。其结果,可以防止金属箔层4与电池要素或导线(金属端子)的接触,可以确保绝缘性。另外,第2基材层6通过由含有上述热固化性树脂的树脂组合物形成,有对外包装材料10进一步赋予防腐蚀功能及耐化学试剂性的倾向。第2基材层6通过具有耐化学试剂性,难以被电解液等溶解、可以抑制强度降低或性能下降。作为聚酰亚胺系树脂,可举出聚酰亚胺树脂、聚酰胺酰亚胺树脂、及聚醚酰亚胺树脂等。作为氟系树脂,可举出聚四氟乙烯、聚氯三氟乙烯、聚偏氟乙烯、聚氟化乙烯、全氟烷氧基氟树脂、四氟化乙烯-六氟化丙烯共聚物、乙烯-四氟化乙烯共聚物、及乙烯-氯三氟乙烯共聚物等。上述树脂材料可以单独使用1种、也可并用2种以上。第2基材材料(树脂组合物)优选和上述树脂材料一起含有固化剂。作为固化剂,可举出异氰酸酯树脂、环氧树脂及三聚氰胺树脂等。第2基材材料通过含有固化剂,可以提高固化后的第2基材层6与防腐蚀处理层5及粘接树脂层7的密合力,由于可以更强地保护成型加工时的金属箔层4,因此可以进一步提高成型性。进而,上述树脂组合物通过含有固化剂,有能够进一步提高防腐蚀功能的倾向。另外,上述树脂材料优选具有能够与上述固化剂反应的官能团。上述树脂材料通过具有能够与固化剂反应的官能团,伴随着不仅是固化剂还包括树脂材料的交联反应的第2基材材料的固化进一步进行,变得易于调整第2基材层6的熔点等特性。作为能够与固化剂反应的官能团,可举出氨基、羧基、羟基及羰基等。通过提高第2基材层6中的交联密度、具有可获得更为优异的电绝缘性的倾向。即,上述树脂组合物含有树脂材料和固化剂,通过使树脂材料与固化剂交联,有可获得更为优异的电绝缘性的倾向。第2基材材料例如作为溶液涂布在金属箔层4或防腐蚀处理层5上并进行加热或干燥,从而变成第2基材层6。另外,当第2基材材料含有固化剂时,优选通过进一步熟化而固化,变成第2基材层6。第2基材层6的熔点优选比热熔融粘合树脂层8的熔点还高40℃以上、更优选高70℃以上。通过使用具有上述范围熔点的第2基材层6对外包装材料进行热熔融粘合,在热熔融粘合时可以进一步抑制第2基材层6变薄。结果,可以防止金属箔层4与电池要素或导线(金属端子)的接触以确保更优异的绝缘性。第2基材层6的熔点与热熔融粘合树脂层8的熔点之差较大时,变得易于兼顾熔融粘合的功能和绝缘性、可以在宽的温度范围内设定热熔融粘合温度。第2基材层6的熔点优选为200℃以上、更优选为230℃以上。通过第2基材层6的熔点为200℃以上,第2基材层6在热熔融粘合时不会变得过薄,可以防止金属箔层4与电池要素或导线(金属端子)的接触、可以更为确实地获得绝缘性。第2基材层6的熔点上限并无特别限定,第2基材层6例如可具有500℃左右的熔点、也可没有熔点。另外,第2基材层6的熔点与热熔融粘合树脂层8的熔点之间的差可以为100℃以下。第2基材层6的熔点与热熔融粘合树脂层8的熔点之差较小时,有第2基材层6的加工性提高的倾向。第2基材层6的熔点例如可通过上述树脂材料的官能团量及固化剂的添加量等控制交联点的数量来进行调整。因此,树脂材料的官能团量及固化剂的添加量等按照熔点达到上述范围内的方式、并一并考虑金属箔层4的保护效果等其他特性来进行适当选择即可。另外,上述第2基材层6通过直接或者仅隔着防腐蚀处理层5层叠在金属箔层4上,可以在维持成型性及水蒸汽阻隔性的同时抑制成型时的翘曲、并提高绝缘性。另外,本说明书中熔点表示使用DSC(差示扫描热量计)以5℃/分钟加热试样时的伴随试样熔解的吸热峰顶的温度。形成第2基材层6的第2基材材料优选是与构成第1基材层1的第1基材材料同种的树脂材料。即,例如第1基材材料为聚酯树脂膜时,第2基材材料优选为聚酯树脂。第2基材材料通过为与第1基材材料同种的树脂材料,易于进一步减少成型加工后的翘曲量。第2基材层6的厚度与第2基材材料的涂布层的干燥厚度大致相同,从成型性、绝缘性及水蒸汽阻隔性等观点出发,优选为5μm以上且30μm以下、更优选为8μm以上且25μm以下、进一步为8μm以上且20μm以下、特别优选为8μm以上且15μm以下。第2基材层6的厚度为5μm以上时,具有成型性、耐针孔性及绝缘性提高的倾向。而当第2基材层6的厚度为30μm以下时,有减少在电池制造时自端部浸入的水蒸汽量、水蒸汽阻隔性提高的倾向。第1基材层1与第2基材层6的厚度之差优选为15μm以下、更优选为10μm以下。第1基材层1与第2基材层6的膜厚差为15μm以下时,易于减少成型加工时的翘曲。(粘接树脂层7)粘接树脂层7是将热熔融粘合树脂层8和第2基材层6粘接的层。第2基材层6、粘接树脂层7及热熔融粘合树脂层8的构成与构成粘接树脂层7的粘接树脂一起,大致分类为热层压构成和干式层压构成。热层压构成中,通过挤出层压将粘接树脂导入至第2基材层6上。热层压构成中的上述粘接树脂优选为热塑性树脂。作为热层压构成中的上述粘接树脂,例如可举出聚烯烃树脂、弹性体树脂、将聚烯烃树脂酸改性得到的酸改性聚烯烃树脂。作为聚烯烃树脂,例如可举出低密度、中密度及高密度的聚乙烯;乙烯-α烯烃共聚物;聚丙烯;以及丙烯-α烯烃共聚物等。为共聚物时的聚烯烃树脂可以是嵌段共聚物、也可以是无规共聚物。作为酸改性聚烯烃树脂,例如可举出上述聚烯烃树脂被不饱和羧酸及其衍生物改性(酸改性)了的树脂等。作为不饱和羧酸,例如可举出丙烯酸、甲基丙烯酸、马来酸、富马酸、巴豆酸及衣康酸等。作为不饱和羧酸的衍生物,可举出不饱和羧酸的酸酐、单及二酯、酰胺化物以及酰亚胺化物等。不饱和羧酸及其衍生物优选是丙烯酸、甲基丙烯酸、马来酸或马来酸酐,更优选是马来酸酐。酸改性聚烯烃树脂可以通过共聚不饱和羧酸、其衍生物及其他单体等来获得。上述共聚可以是嵌段共聚、无规共聚及接枝共聚中的任一种。这些不饱和羧酸及其衍生物可以单独使用1种、也可以并用2种以上。聚烯烃系树脂及酸改性聚烯烃系树脂的电解液耐受性优异。作为弹性体树脂,可举出SEBS(苯乙烯/乙烯/丁烯/苯乙烯)共聚物、SBS(苯乙烯/丁二烯/苯乙烯)共聚物、SEPS(苯乙烯/乙烯/丙烯/苯乙烯)共聚物、SEP(苯乙烯/乙烯/丙烯)共聚物及SIS(苯乙烯/异戊二烯/苯乙烯)共聚物等。作为粘接树脂,通过将上述弹性体树脂和酸改性聚烯烃系树脂并用,具有能够改善因冷成型时的裂纹所导致的拉伸白化耐受性、通过提高湿润性来改善密合力、通过降低各向异性来改善成膜性、改善热熔融粘合强度等特性的倾向。在干式层压构成中,将粘接树脂导入(例如涂布)在第2基材层6上。作为干式层压构成中的上述粘接树脂,例如可举出酸改性聚烯烃树脂。作为酸改性聚烯烃树脂,可举出在热层压构成中示例出的酸改性聚烯烃树脂。粘接树脂层7的厚度与粘接树脂的导入层的干燥厚度大致相同。粘接树脂层7的厚度在为热层压构成时优选为8μm以上且30μm以下、更优选为10μm以上且20μm以下。粘接树脂层7的厚度为8μm以上时,易于获得第2基材层6与热熔融粘合树脂层8的充分粘接强度。粘接树脂层7的厚度为30μm以下时,易于减少自外包装材料端面透过至电池内部的水分量。另外,粘接树脂层7的厚度在为干式层压构成时,优选为1μm以上且5μm以下。粘接树脂层7的厚度为1μm以上时,第2基材层6与热熔融粘合树脂层8的密合力提高、易于获得充分的层压强度。而粘接树脂层7的厚度为5μm以下时,易于抑制膜断裂的发生。干式层压构成中的粘接树脂层7的膜厚通过为1μm以上且5μm以下的范围内,可以更为牢固地使热熔融粘合树脂层8与第2基材层6密合。(热熔融粘合树脂层8)热熔融粘合树脂层8隔着粘接树脂层7形成在第2基材层6上。热熔融粘合树脂层8可通过干式层压及夹心层压等进行层叠,也可以与粘接树脂层7一起通过共挤出法进行层叠。在粘接树脂层7上层叠热熔融粘合树脂层8,使2张外包装材料的热熔融粘合树脂层8彼此相向,在热熔融粘合树脂层8的熔解温度(熔点)以上对外包装材料的端部进行加压热熔融粘合,从而可以将电池内容物密封在上述2张外包装材料内。热熔融粘合树脂层8由热熔融粘合树脂形成。作为热熔融粘合树脂,可举出聚烯烃树脂。作为上述聚烯烃树脂,例如可举出低密度、中密度及高密度的聚乙烯以及聚丙烯等。上述聚烯烃树脂可以是共聚物,可以是嵌段共聚物、还可以是无规共聚物。另外,上述聚烯烃树脂还可以是将丙烯酸及甲基丙烯酸等极性单体共聚而成的共聚物,还可以是分散或共聚交联聚烯烃等聚合物等而成的树脂。上述聚烯烃树脂可以单独使用1种、也可并用2种以上。热熔融粘合树脂层8也可以由热熔融粘合树脂膜形成。形成热熔融粘合树脂层8的热熔融粘合树脂膜可以是混合了上述聚烯烃树脂的膜、优选是无拉伸聚烯烃树脂膜、更优选是无拉伸聚丙烯膜。另外,形成热熔融粘合树脂层8的上述热熔融粘合树脂膜可以是单层膜、也可以是多层膜。热熔融粘合树脂层8可以由与上述热熔融粘合树脂一起还含有润滑剂、防粘附剂、防静电剂、成核剂、颜料及染料等各种添加剂的热熔融粘合树脂组合物形成。上述添加剂可以单独使用1种、也可并用2种以上。另外,含有上述添加剂(优选润滑材料)的涂布层可以形成在热熔融粘合树脂层8(与金属箔层4侧相反侧的表面)上。作为润滑剂,可以使用在第1基材层中举出的润滑剂。通过热熔融粘合树脂层8由含有润滑材料的热熔融粘合树脂组合物形成、或者将含有润滑材料的涂布层涂布在热熔融粘合树脂层8上,有外包装材料10的成型性提高的倾向。热熔融粘合树脂层8的厚度与形成热熔融粘合树脂层8的树脂膜的厚度大致相同,优选为20μm以上且90μm以下。当热熔融粘合树脂层8的厚度为20μm以上时,易于确保充分的层压强度。另外,当热熔融粘合树脂层8的厚度为90μm以下时,易于抑制水蒸汽的透过量增多。[二次电池用外包装材料20]接着,对本实用新型另一实施方式的二次电池用外包装材料20(以下也仅记为“外包装材料20”)进行说明。外包装材料20如图2所示,具有依次层叠第1基材层1、第1粘接剂层2、防腐蚀处理层3、金属箔层4、防腐蚀处理层5、第2基材层6、粘接树脂层7、及热熔融粘合树脂层8而成的层叠结构。外包装材料20与外包装材料10的不同点是在第1粘接剂层2与金属箔层4之间进一步具备防腐蚀处理层3。外包装材料20通过具备防腐蚀处理层3,可以防止金属箔层4的第1基材层1一侧的面的腐蚀。防腐蚀处理层3可以通过与外包装材料10中上述防腐蚀处理层5同样的防腐蚀处理剂、利用相同的方法形成。[二次电池用外包装材料30]接着,对本实用新型又一实施方式的二次电池用外包装材料30(以下也仅记为“外包装材料30”)进行说明。外包装材料30如图3所示,具有依次层叠第1基材层1、金属箔层4、防腐蚀处理层5、第2基材层6、粘接树脂层7及热熔融粘合树脂层8而成的层叠结构。外包装材料30与外包装材料10的不同点是不具有第1粘接剂层2。外包装材料30中,将金属箔层4直接层叠在第1基材层1的一个面上。即,第1基材层1未介由粘接剂层地形成在金属箔层4的未形成有防腐蚀处理层5的一侧的面上。因此,可以减小外包装材料整体的厚度、使二次电池更薄型化及小型化,与介由粘接剂层形成第1基材层1的情况相比,可以削减工序数及制造成本。此时,第1基材层1优选通过将第1基材材料涂布或涂饰在金属箔层4上来形成。此外,当第2基材层6由能够赋予防腐蚀功能的上述的含有特定热固化性树脂的树脂组合物形成时,外包装材料30也可不具备防腐蚀处理层5。外包装材料30的制造中,第1基材材料与外包装材料10中将第2基材材料涂布在防腐蚀处理层5上时同样地涂布在金属箔层4上。外包装材料30的制造中,上述第1基材材料是含有热固化性树脂或热塑性树脂的树脂组合物。第1基材层1可以称作第1基材材料的固化物。作为热固化性树脂或热塑性树脂,例如可举出聚酯树脂、聚氨酯树脂、聚酰胺树脂、聚酰亚胺树脂、氟树脂、聚偏氯乙烯树脂及丙烯酸树脂等。作为外包装材料30的制造中的第1基材材料,更为具体地可以使用作为第2基材材料列举出的材料。上述第1基材材料中还可进一步添加异氰酸酯树脂、三聚氰胺树脂及环氧树脂等固化剂。第1基材层1中使用的树脂材料优选与第2基材层6中使用的树脂材料相同。第1基材层1中使用的树脂材料通过与第2基材层6中使用的树脂材料为同种,易于减少成型加工后的翘曲量。[二次电池60]接着,对具备上述外包装材料的二次电池进行说明。本实施方式的二次电池具备电池要素和上述外包装材料。详细地说,二次电池具备含有电极的电池要素、自上述电极延伸存在的导线(金属端子)和收容电池要素的容器,上述容器由上述外包装材料、按照热熔融粘合树脂层8成为内侧的方式形成。上述容器可以是使热熔融粘合树脂层8彼此相向地将2个外包装材料重叠、将重叠的上述外包装材料的边缘部进行热熔融粘合而获得,另外也可将1个外包装材料折回地进行重叠、同样地将上述外包装材料的边缘部进行热熔融粘合所获得。作为二次电池,例如可举出锂离子电池、镍氢电池及铅蓄电池等。导线58被以热熔融粘合树脂层8为内侧而形成容器的上述外包装材料所夹持并密封。导线58也可介由胶带密封剂被上述外包装材料所夹持。[二次电池的制造方法]接着,对使用上述外包装材料制造二次电池的方法进行说明。此外,这里举例说明使用压花型外包装材料50制造二次电池60的情况。图4是表示上述压花型外包装材料50的图。图4的(a)~(d)是表示使用了上述外包装材料的单侧成型加工电池的制造工序的立体图。作为二次电池60,也可以是设置2个如压花型外包装材料50那样的外包装材料、一边调整对准一边将这种外包装材料彼此粘合而制造的两侧成型加工电池。作为单侧成型加工电池的二次电池60例如可通过以下的工序S1~S5制造。工序S1:准备外包装材料(例如外包装材料10、外包装材料20或外包装材料30)、含有电极的电池要素56以及自上述电极延伸存在的导线58的工序。工序S2:在外包装材料的单面上形成用于配置电池要素56的凹部52的工序(参照图4(a)及图4(b))。工序S3:在压花型外包装材料50的成型加工区域(凹部52)中配置电池要素56、按照盖部将凹部52覆盖的方式将压花型外包装材料50折回重叠、按照将自电池要素56延伸存在的导线58夹持的方式对压花型外包装材料50的一边进行加压热熔融粘合的工序(参照图4(b)及图4(c))。工序S4:残留夹持导线58的边以外的一边、对其他边进行加压热熔融粘合、之后从残留的一边注入电解液、在真空状态下对残留的一边进行加压热熔融粘合的工序(参照图4(c))。工序S5:将夹持导线58的边以外的加压热熔融粘合边端部剪切、向成型加工区域(凹部52)侧弯折的工序(参照图4(d))。(工序S1)工序S1中,准备上述外包装材料、含电极的电池要素56以及自上述电极延伸存在的导线58。上述外包装材料基于上述实施方式进行准备。作为电池要素56及导线58并无特别限定,可以使用公知的电池要素56及导线58。(工序S2)工序S2中,在上述外包装材料的热熔融粘合树脂层8一侧形成用于配置电池要素56的凹部52。作为形成凹部52的方法,可举出使用了金属模具的成型加工(深拉深成型)。作为成型方法,可举出以下方法:使用按照具有上述外包装材料的厚度以上的间距的方式配置的阴模和阳模的金属模具,将阳模的金属模具随上述外包装材料一起按入到阴模的金属模具中的方法。通过调整阳模的金属模具的按入量,可以将凹部52的深度(深拉深量)调整至所希望的量。通过在上述外包装材料中形成凹部52,获得压花型外包装材料50。(工序S3)工序S3中,在压花型外包装材料50的成型加工区域(凹部52)内配置由正极、隔膜及负极等构成的电池要素56。另外,将自电池要素56延伸存在、分别接合于正极和正极的导线58自成型加工区域(凹部52)向外引出。之后,将压花型外包装材料50在长度方向的大致中央处折回,按照热熔融粘合树脂层8彼此变为内侧的方式进行重叠,对压花型外包装材料50的夹持导线58的一边进行加压热熔融粘合。加压热熔融粘合通过温度、压力及时间这3个条件来控制以适当地进行设定。加压热熔融粘合的温度优选是热熔融粘合树脂层8熔解的温度(熔点)以上且低于第2基材层6熔解的温度(熔点)。通过在上述温度范围内进行加压热熔融粘合,可以使热熔融粘合树脂层8充分地熔融,且可以在不使第2基材层6熔融的情况下保持厚度。因此,可以兼顾熔融粘合的功能和绝缘性。另外,热熔融粘合树脂层8的热熔融粘合前的厚度优选相对于导线58的厚度为40%以上且80%以下。通过热熔融粘合树脂层8的厚度为上述下限值以上,有热熔融粘合树脂能够充分地填充导线58端部的倾向,通过为上述上限值以下,可以适度地抑制二次电池60的上述外包装材料端部的厚度,可以减少水分自外包装材料10、外包装材料20或外包装材料30的端部的浸入量。(工序S4)工序S4中,残留夹持导线58的边以外的一边、进行其他边的加压热熔融粘合。之后,从残留的一边注入电解液,在真空状态下对残留的一边进行加压热熔融粘合。加压热熔融粘合的条件与工序S3同样。(工序S5)将夹持导线58的边以外的周边加压热熔融粘合边端部剪切,将从端部挤出的热熔融粘合树脂层8除去。之后,将周边加压热熔融粘合部向成型加工区域52一侧折回,形成折回部62,从而获得二次电池60。[实施例]以下举出实施例具体地说明本实用新型,但本实用新型并非限定于这些。[使用材料]以下示出用于形成实施例及比较例的外包装材料的第1基材层、第1粘接剂层、金属箔层、防腐蚀处理层、第2粘接层、第2基材层、粘接树脂层及热熔融粘合树脂层的材料。(第1基材层)第1基材材料A-1:聚酰胺树脂膜(厚度:15μm)。第1基材材料A-2:具有氨基的聚酰胺树脂及异氰酸酯系固化剂的混合物。第1基材材料A-3:具有羟基的聚酯树脂及异氰酸酯系固化剂的混合物。第1基材材料A-4:具有羟基的聚氨酯树脂及异氰酸酯系固化剂的混合物。第1基材材料A-5:具有羧基的聚酰胺酰亚胺树脂及环氧系固化剂的混合物。(第1粘接剂层)第1粘接剂B-1:双组分固化型聚酯氨基甲酸酯粘接剂([NCO/OH]=5)。(金属箔层)金属箔C-1:进行了退火处理的软质铝箔8079材料(厚度:40μm)。(防腐蚀处理层)处理剂D-1:以氧化铈、磷酸及丙烯酸系树脂为主体的涂布型二氧化铈溶胶处理剂。(第2粘接剂层)第2粘接剂E-1:双组分固化型聚酯氨基甲酸酯粘接剂。(第2基材层)第2基材材料F-1:具有羟基的聚酯树脂及异氰酸酯系固化剂的混合物(固化后的树脂膜(第2基材层)熔点:230℃)。第2基材材料F-2:具有羟基的聚氨酯树脂及异氰酸酯系固化剂的混合物(固化后的树脂膜熔点:250℃)。第2基材材料F-3:具有羧基的聚酰胺酰亚胺树脂及环氧系固化剂的混合物(固化后的树脂膜熔点:290℃)。第2基材材料F-4:具有羟基的聚酯树脂及异氰酸酯系固化剂的混合物(固化后的树脂膜熔点:200℃)第2基材材料F-5:聚丙烯树脂膜(厚度:10μm、熔点:160℃)。第2基材材料F-6:聚酯树脂膜(厚度:25μm、熔点:240℃)。第2基材材料F-7:具有羟基的聚酯树脂及异氰酸酯系固化剂的混合物(固化后的树脂膜熔点:190℃)(粘接树脂层)粘接树脂G-1:马来酸酐改性聚丙烯系树脂(商品名:Admer、三井化学公司制)。(热熔融粘合树脂层)热熔融粘合树脂H-1:无拉伸聚丙烯膜(厚度:40μm、熔点:160℃)。[外包装材料的制作](实施例1)在金属箔C-1的一个面上涂布处理剂D-1,实施烧结处理,形成干燥厚度为100nm的防腐蚀处理层。接着,在金属箔C-1的形成有防腐蚀处理层的一面的相反面上按照干燥厚度达到4μm的方式涂饰第1粘接剂B-1,在40℃下利用干式层压法粘合第1基材材料A-1。之后,对所得的层叠体进行40℃、7日的熟化。接着,在熟化后的层叠体的防腐蚀处理层一侧的面上按照干燥厚度达到8μm的方式涂饰第2基材材料F-1。之后,通过进行40℃、7日的熟化,使第2基材材料中的固化剂交联。接着,在涂布有第2基材材料F-1的面上按照干燥厚度达到3μm的方式涂饰粘接树脂G-1,在100℃下利用干式层压法粘合热熔融粘合树脂H-1,制作了外包装材料。(实施例2)在金属箔C-1的一个面上涂布处理剂D-1,实施烧结处理,形成干燥厚度为100nm的防腐蚀处理层。接着,在金属箔C-1的形成有防腐蚀处理层的一面的相反面上按照干燥厚度达到8μm的方式涂饰第1基材材料A-2。接着,在防腐蚀处理层上按照干燥厚度达到8μm的方式涂饰第2基材材料F-1。之后,通过进行40℃、7日的熟化,使第2基材材料中的固化剂交联。接着,在涂布有第2基材材料F-1的面上按照干燥厚度达到3μm的方式涂饰粘接树脂G-1,在100℃下利用干式层压法粘合热熔融粘合树脂H-1,制作了外包装材料。(实施例3)除了代替第1基材材料A-2而使用第1基材材料A-3以外,与实施例2同样地制作了外包装材料。(实施例4)除了代替第1基材材料A-2而使用第1基材材料A-4、代替第2基材材料F-1而使用第2基材材料F-2以外,与实施例2同样地制作了外包装材料。(实施例5)除了代替第1基材材料A-2而使用第1基材材料A-5、代替第2基材材料F-1而使用第2基材材料F-3以外,与实施例2同样地制作了外包装材料。(实施例6)除了代替第2基材材料F-1而使用第2基材材料F-4以外,与实施例3同样地制作了外包装材料。(实施例7)除了代替第2基材材料F-1而使用第2基材材料F-7以外,与实施例3同样地制作了外包装材料。(比较例1)在金属箔C-1的一个面上涂布处理剂D-1,实施烧结处理,形成干燥厚度为100nm的防腐蚀处理层。接着,在金属箔C-1的形成有防腐蚀处理层的一面的相反面上按照干燥厚度达到4μm的方式涂饰第1粘接剂B-1,在40℃下利用干式层压法粘合第1基材材料A-1。接着,在防腐蚀处理层上按照干燥厚度达到4μm的方式涂饰第2粘接剂E-1,在40℃下利用干式层压法粘合第2基材材料F-5。之后,进行40℃、7日的熟化。接着,在第2基材材料F-5上按照干燥厚度达到3μm的方式涂饰粘接树脂G-1,在100℃下利用干式层压法粘合热熔融粘合树脂H-1,制作了外包装材料。(比较例2)在金属箔C-1的一个面上涂布处理剂D-1,实施烧结处理,形成干燥厚度为100nm的防腐蚀处理层。接着,在金属箔C-1的形成有防腐蚀处理层的一面的相反面上按照干燥厚度达到4μm的方式涂饰第1粘接剂B-1,在40℃下利用干式层压法粘合第1基材材料A-1。之后,对所得层叠体进行40℃、7日的熟化。接着,在熟化后的层叠体的防腐蚀处理层一侧的面上按照干燥厚度达到3μm的方式涂饰粘接树脂G-1,在100℃下利用干式层压法粘合热熔融粘合树脂H-1,制作了外包装材料。(比较例3)在金属箔C-1的一个面上涂布处理剂D-1,实施烧结处理,形成干燥厚度为100nm的防腐蚀处理层。接着,在防腐蚀处理层上按照干燥厚度达到8μm的方式涂饰第2基材材料F-1。之后,进行40℃、7日的熟化,从而使第2基材层的固化剂交联。接着,在涂布有第2基材材料F-1的面上按照干燥厚度达到3μm的方式涂饰粘接树脂G-1,在100℃下利用干式层压法粘合热熔融粘合树脂H-1,制作了外包装材料。(比较例4)除了代替第2基材材料F-5而使用第2基材材料F-6以外,与比较例1同样地制作了外包装材料。[评价方法](耐热性)对实施例及比较例中制作的外包装材料在温度为190℃、面压为0.5MPa、时间为3秒的条件下进行加热加压,目视观察第2基材层的形状变化。另外,利用显微镜观察加热加压前后的外包装材料的截面,测定加热加压前后的第2基材层的膜厚。耐热性的评价根据以下的基准进行。另外,比较例2中由于未设置第2基材层,因此未作评价。将耐热性的评价结果示于表1。“优”:未见热熔融粘合导致的第2基材层的形状变化,且加热加压前后的第2基材层的膜厚变化小于10%。“良”:未见热熔融粘合导致的第2基材层的形状变化,且加热加压前后的第2基材层的膜厚变化为10%以上且小于20%。“好”:稍稍可见热熔融粘合导致的第2基材层的形状变化、或者加热加压前后的第2基材层的膜厚变化为20%以上且小于30%。“不好”:可见热熔融粘合导致的第2基材层的形状变化、或者加热加压前后的第2基材层的膜厚变化为30%以上。(成型深度)将实施例及比较例中制作的外包装材料剪切成150mm×190mm的形状,按照热熔融粘合树脂层朝上的方式配置在成型装置内。将成型装置的成型深度每隔1mm地设定为1~10mm,在室温为23℃、露点温度为-35℃的环境下对外包装材料进行冷成型,根据下述标准评价各成型深度下的成型性。其中,冲压金属模具使用具有100mm×150mm的长方形横截面、在底面具有0.75mm的冲压半径(RP)、在侧面具有1.5mm的冲压圆角半径(RCP)的模具。另外,冲模金属模具使用开口部上表面上具有0.75mm的模口圆角半径(RD)的模具。冲压金属模具与冲模金属模具之间的间隔为0.20mm。将成型深度的评价结果示于表1。“优”:在不发生断裂或裂纹的情况下能够进行成型深度为6mm以上的深拉深成型。“良”:在不发生断裂或裂纹的情况下能够进行成型深度为4mm以上且小于6mm的深拉深成型。“不好”:在成型深度小于4mm的深拉深成型中发生断裂或裂纹。(绝缘性)将实施例及比较例中制作的外包装材料剪切成240mm×70mm的形状。将所剪切的外包装材料在长边的中间处按照热熔融粘合树脂层相向的方式折回,在温度为190℃、面压为0.5MPa、时间为3秒的条件下对折回的长边2边的宽3mm的边缘进行加压热熔融粘合。之后从开口的短边侧注入3mg的电解液,该电解液是将把含有水分量抑制在20ppm以下的碳酸亚乙酯(EC)、碳酸二甲酯(DMC)及碳酸二乙酯(DEC)以EC:DMC:DEC=1:1:1(重量比)混合而成的。接着,对相向的短边在夹持铝制金属端子(厚度:50μm、宽:12mm、长:50mm)的状态下、在温度为190℃、面压为0.5MPa、时间为3秒的条件下进行宽度3mm的加压热熔融粘合,制作120mm×70mm形状的绝缘性评价用样品。利用检测器确认所制作的绝缘性评价用样品的金属端子与外包装材料的金属箔层之间有无短路,根据以下标准进行绝缘性的评价。将绝缘性的评价结果示于表1。“良”:20个样品中电阻值降低的样品和短路的样品为0个。“好”:20个样品中电阻值稍有降低的样品为1个以上、短路的样品为0个。“不好”:20个样品中短路的样品为1个以上。(成型加工后的翘曲)将实施例及比较例中制作的外包装材料剪切成120mm×260mm的坯料形状,按照热熔融粘合树脂层朝上的方式配置在成型装置内。在室温为23℃、露点温度为-35℃的环境下,将成型深度设定为3mm,进行外包装材料的冷成型。其中,冲压金属模具使用具有70mm×80mm的长方形横截面、在底面具有0.75mm的冲压半径(RP)、在侧面具有1.5mm的冲压圆角半径(RCP)的模具。另外,冲模金属模具使用开口部上表面上具有0.75mm的模口圆角半径(RD)的模具。冲压金属模具与冲模金属模具之间的间隔为0.20mm。成型区域为所剪切的外包装材料长度方向的大致中央处分出的半面的大致中央,按照成型区域的3边距离所剪切的外包装材料的短方向两端及长度方向一端分别为25mm的位置的方式,配置成型区域。按照热熔融粘合树脂层朝下的方式将成型加工后的外包装材料静置在室温为23℃、露点温度为-35℃的环境下60分钟,测定未成型的区域侧的短边的翘曲量(短边中央与静置面的距离)。翘曲的评价根据以下标准进行。将成型加工后的翘曲的评价结果示于表1。“优”:翘曲量小于50mm。“良”:翘曲量为50mm以上且小于100mm。“不好”:翘曲量为100mm以上。(水蒸汽阻隔性)将实施例及比较例中制作的外包装材料剪切成240mm×70mm的形状,将所剪切的外包装材料在长边的中间处按照热熔融粘合树脂层相向的方式折回,在温度为190℃、面压为0.5MPa、时间为3秒的条件下对折回的长边2边的宽3mm的边缘进行加压热熔融粘合。之后从开口的短边侧注入3mg的电解液,该电解液是将把含有水分量抑制在20ppm以下的碳酸亚乙酯(EC)、碳酸二甲酯(DMC)及碳酸二乙酯(DEC)以EC:DMC:DEC=1:1:1(重量比)混合而成的。接着,对开口的短边的宽3mm的边缘在温度为190℃、面压为0.5MPa、时间为3秒的条件下进行加压热熔融粘合,制作120mm×70mm形状的水分透过测定用样品。将所制作的水分透过测定用样品在温度为60℃、湿度为90%的环境下保管4周。利用卡尔费休试验机测定保管后的电解液中的水分含量,算出以实施例1的水分含量为基准(100%)时的实施例及比较例的水分含量的值。水蒸汽阻隔性的评价根据以下标准进行。将水蒸汽阻隔性的评价结果示于表1。“良”:水分含量相对于实施例1小于110%。“不好”:水分含量相对于实施例1为110%以上。表1耐热性成型性绝缘性成型加工后的翘曲水蒸汽阻隔性实施例1优优良良良实施例2优优良良良实施例3优优良优良实施例4优优良优良实施例5优优良优良实施例6良优良优良实施例7好良好优良比较例1不好良不好良良比较例2-良不好不好良比较例3优不好良不好良比较例4优良良良不好实施例1~6及比较例3~4获得了良好的耐热性,而比较例1未获得充分的耐热性。比较例1中由于第2基材层不是由含有热固化性树脂的树脂组合物形成的,因此认为由于热熔融粘合,形状发生了大的变化。另外,实施例7中,由于第2基材层的熔点低,因此由于热熔融粘合,形状稍稍发生了变化,但判断其程度是可被允许的。另外,实施例1~7、比较例1~2及比较例4获得了充分的成型深度,而比较例3未获得充分的成型性。认为是比较例3中未设置第1基材层而未能保护金属箔层。另外,实施例1~6及比较例3~4获得了良好的绝缘性,而比较例1~2中未获得充分的绝缘性。比较例1中第2基材层不是由含有热固化性树脂的树脂组合物形成的,热熔融粘合时金属箔层内侧的层变薄,因此认为在金属端子与金属箔层之间发生了短路。比较例2中未设置第2基材层,热熔融粘合时金属箔层内侧的层变薄,因此认为金属端子与金属箔层之间发生了短路。另外,实施例7中,第2基材层的熔点低,热熔融粘合时金属箔层内侧的层稍稍变薄,因此电阻值降低了一部分,但是认为还不至于在金属端子与金属箔层之间发生短路。另外,实施例1~7、比较例1及比较例4中抑制了翘曲量,而比较例2及3中并未充分地抑制成型加工后的翘曲量。比较例2及3中相对于外包装材料的金属箔层仅在单侧层叠了基材层,因此认为在成型加工后发生了翘曲。另外,实施例1~7及比较例1~3中获得了高的水蒸汽阻隔性,而比较例4中未获得充分的水蒸汽阻隔性。比较例4中第2基材层厚、而且设有第2粘接剂层,因此认为自外包装材料端部的水蒸气侵入量增加。另外,对于除了未在金属箔C-1的一个面上涂布处理剂D-1(未形成防腐蚀处理层)以外与实施例1~7同样地制作的外包装材料,也获得了与对应的实施例相同的评价结果。当前第1页1 2 3