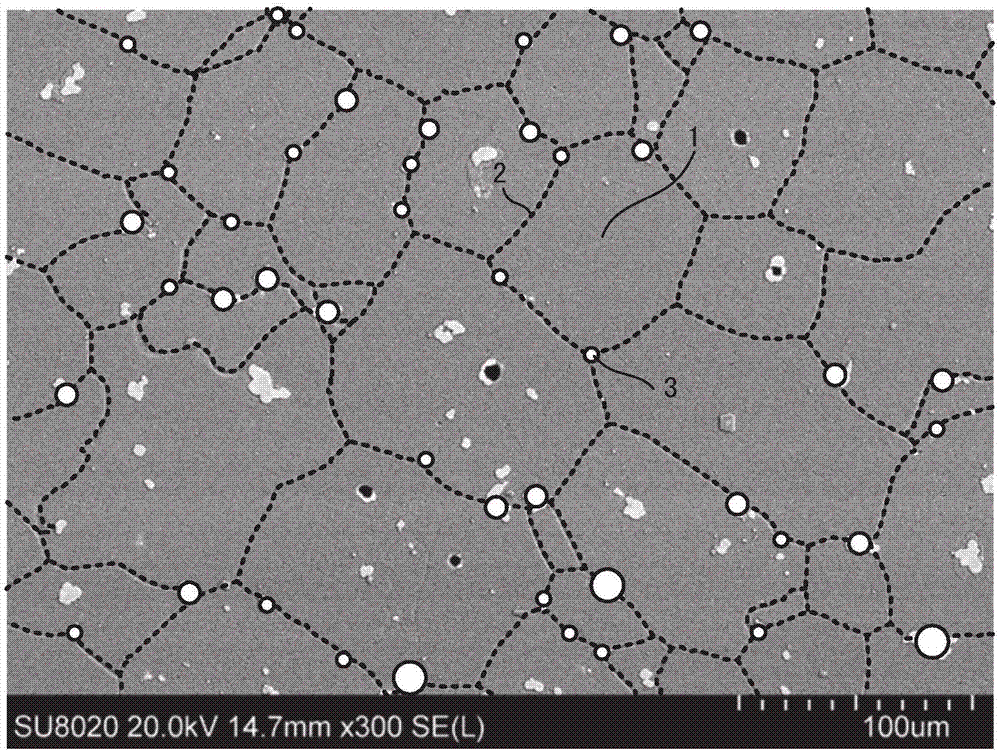
本发明实施方式涉及永久磁铁、旋转电机、以及车辆。
背景技术:
:作为高性能的永久磁铁的例子,已知sm-co系磁铁、nd-fe-b系磁铁等稀土类磁铁。现在量产的这些磁铁大量含有fe或co。fe或co有利于饱和磁化强度的增大。在混合动力汽车(hev)、电动汽车(ev)、或轨道车辆等车辆的驱动电动机中使用永久磁铁的情况下,对永久磁铁要求耐热性。在hev、ev、或轨道车辆等车辆的驱动电动机中,现使用例如用dy置换了nd-fe-b系磁铁的nd的一部分而提高了耐热性的永久磁铁。由于dy是稀有元素之一,正寻求不使用dy的永久磁铁。已知sm-co系磁铁以不使用dy的体系显示优异的耐热性,但与nd-fe-b系磁铁相比仍有最大磁能积(bh)max小的难点。作为决定永久磁铁的(bh)max的值的主要因素,可例举剩余磁化强度和矫顽力、矩形比。为了提高sm-co系磁铁的磁化强度,在用fe置换co的一部分的同时提高fe浓度是有效的。但是,在fe浓度高的组成范围内,容易难以在sm-co系磁铁中得到高的烧结体密度、或呈现优异的矩形比。于是,正寻求在高fe浓度的sm-co系磁铁中保持足够的矫顽力、同时实现高剩余磁化强度和高矩形比的技术。现有技术文献专利文献专利文献1:日本专利特开2014-192193号公报专利文献2:国际公开第2016/084118号技术实现要素:本发明所要解决的课题是提供一种提高了矫顽力、剩余磁化强度、以及矩形比的永久磁铁,和使用其的旋转电机以及车辆。实施方式的永久磁铁以组成式:rpfeqmrcutco100-p-q-r-t(式中,r为1种以上的稀土类元素,m为选自zr、ti、以及hf的至少一种元素,p为满足10.8≤p≤12.5原子%的数,q为满足28≤q≤40原子%的数,r为满足0.88≤r≤4.5原子%的数,t为满足3.5≤t≤13.5原子%的数)表示。永久磁铁具备烧结体,所述烧结体具备具有th2zn17型晶相的晶粒、和晶粒的晶界。烧结体中,在将r元素以及氧的浓度在85原子%以上的连续区域作为一个r元素的氧化物相时,存在于晶界的氧化物相的数量与晶粒的数量之比在1.1以下。附图说明图1是烧结体的剖面的一部分的sem图像。图2是烧结体的剖面的一部分的sem图像。图3是示出永久磁铁电动机的图。图4是示出可变磁通量电动机的图。图5是示出发电机的图。具体实施方式下面参照附图对实施方式进行说明。另外,附图是示意性的,例如厚度和平面尺寸的关系、各层厚度的比例等或与实物不同。此外,在实施方式中,对实质上相同的构成要素标注相同的符号且省略其说明。(第一实施方式)本实施方式的永久磁铁具有以组成式:rpfeqmrcutco100-p-q-r-t(式中,r为1种以上的稀土类元素,m为选自zr、ti、以及hf的至少一种元素,p为满足10.8≤p≤12.5原子%的数,q为满足28≤q≤40原子%的数,r为满足0.88≤r≤4.5原子%的数,t为满足3.5≤t≤13.5原子%的数)表示的组成。r元素给永久磁铁带来较大磁各向异性,赋予高矫顽力。作为r元素,使用1种以上的稀土类元素。作为r元素,更优选使用选自钇(y)、钐(sm)、铈(ce)、钕(nd)和镨(pr)的至少1种元素,特别优选使用sm。通过使r元素的50原子%以上为sm,可再现性良好地提高永久磁铁的性能、尤其是矫顽力。更优选r元素的70原子%以上、进一步优选90原子%以上为sm。r元素的含量例如在10.8原子%以上、12.5原子%以下。如果r元素的含量低于10.8原子%,则大量的α-fe相会析出而得不到足够的矫顽力。另一方面,如果r元素的含量超过12.5原子%,则饱和磁化强度的下降明显。r元素的含量更优选在10.9原子%以上12.0原子%以下,进一步优选在11.0原子%以上11.6原子%以下。作为m元素,使用选自钛(ti)、锆(zr)以及铪(hf)的至少一种元素。通过掺和m元素,可以高fe浓度的组成呈现大的矫顽力。m元素的含量在0.88原子%以上4.5原子%以下。在m元素的含量低于0.88原子%的情况下,提高fe浓度的效果小,在超过4.5原子%的情况下,生成过剩地含有m元素的相,磁特性变得容易下降。m元素的含量更优选在1.14原子%以上3.58原子%以下,进一步优选在1.55原子%以上2.23原子%以下。m元素可以是ti、zr、hf中的任意一种,优选至少含有zr。尤其是通过使m元素的50原子%以上为zr,可进一步提升提高永久磁铁的矫顽力的效果。另一方面,m元素中hf尤其昂贵,因此即使使用hf,也优选减少其用量。优选hf的含量不足m元素的20原子%。铜(cu)使永久磁铁呈现高矫顽力。cu的含量在3.5原子%以上13.5原子%以下。由于cu是非磁性元素,因此在超过13.5原子%的情况下,磁化强度的下降明显。在低于3.5原子%的情况下,难以得到高矫顽力。cu的含量优选在3.9原子%以上9.0原子%以下,进一步优选在4.3原子%以上5.8原子%以下。铁(fe)主要负责永久磁铁的磁化。通过大量含有fe,可提高永久磁铁的饱和磁化强度。但是,如果fe的含量过量,则会由于α-fe相的析出等而使矫顽力下降。fe的掺和量设在28原子%以上40原子%以下的范围。更优选在29原子%以上36原子%以下,进一步优选在30原子%以上33原子%以下。钴(co)是负责永久磁铁的磁化、并且用于呈现高矫顽力的必需元素。如果含co多,则居里温度会变高,永久磁铁的热稳定性也会提高。如果co的掺和量少,则这些效果减弱。但是,如果永久磁铁中含有过剩的co,则fe的含量会相对减少,因此,存在导致磁化强度下降之虞。co的含量(原子%)设为以p、q、r、t所规定的范围(100-p-q-r-t)。co的一部分可以被选自镍(ni)、钒(v)、铬(cr)、锰(mn)、铝(al)、硅(si)、镓(ga)、铌(nb)、钽(ta)和钨(w)中的至少一种元素a置换。这些置换元素有助于磁铁特性、例如矫顽力的提高。但是,用元素a过量置换co有导致磁化强度下降之虞,因此使元素a的置换量在co的20原子%以下的范围内。永久磁铁的组成例如通过高频电感耦合等离子体(inductivelycoupledplasma:icp)发射分光分析法、扫描电子显微镜-能量色散型x射线光谱法(sem-energydispersivex-rayspectroscopy:sem-edx)、透射电子显微镜-能量色散型x射线光谱法(transmissionelectronmicroscope-edx:tem-edx)等来测定。上述永久磁铁具备具有二维金属组织的烧结体,所述二维金属组织含有构成主相的多个晶粒、和晶粒的晶界(也称为晶界相)。主相由具有全部构成相的最大体积比的相来定义。主相的比例优选在全部构成相中的70体积%以上,进一步优选在90体积%以上。上述金属组织例如使用扫描电子显微镜(scanningelectronmicroscope:sem)来观察。晶粒具有六方晶系的th2zn17型晶相(2-17型晶相)。晶粒的粒径在10μm以上200μm以下。多个晶粒的平均粒径优选在60μm以上。th2zn17型晶相的c轴优选以与易磁化轴平行或大致平行的方式存在。大致平行包括自平行方向偏离-10度以上10度以下的方向。在包括th2zn17型晶相的c轴的剖面中,在晶粒内具有用由cacu5型晶相构成的胞壁相包围由th2zn17型晶相构成的晶胞相的晶胞结构。晶界相存在于晶粒的周围。晶界相的熔点比主相低。晶界相例如包括ce2ni7型晶相(2-7型晶相)和cacu5型晶相(1-5型晶相)等。晶界相还可含有比th2zn17型晶相更高浓度的cu以及m元素。金属组织有时还含有片晶相(日文:プレートレット相)、或r元素的氧化物相(主要为sm氧化物相)、含有m元素的偏析相(主要为zrc等的碳化物相)、ce2ni7型晶相等低熔点相。ce2ni7型晶相等低熔点相使晶界相大幅生长。因此,与th2zn17型晶相相比,cu或m元素的浓度容易变高。金属组织的各相的体积比率例如可并用由电子显微镜或光学显微镜来进行的观察和x线衍射等来综合判断,通过对永久磁铁的剖面拍摄出的电子显微镜照片的面积分析法来求出。作为永久磁铁的剖面,可采用试样的具有最大面积的表面的实质上中央部的剖面。本实施方式的永久磁铁可通过含有th2zn17型晶相和cacu5型晶相的相分离组织来呈现高矫顽力。相分离组织具有例如通过将胞壁相作为钉扎点起作用来抑制磁畴壁移动的、所谓的磁畴壁钉扎型的矫顽力结构。磁畴壁钉扎型的矫顽力结构中,即使产生作为磁化反转起点的磁化反转核,只要不施加超过钉扎势的外部场,就不会发生磁畴壁移动。因此,作为决定矫顽力大小的主要因素,相分离组织的结构是支配性的。为了提高r-co系永久磁铁的磁化强度,在用fe置换co的一部分的同时提高fe浓度是有效的。因此,本实施方式的永久磁铁含有28原子%以上40原子%以下的fe。但是,在fe浓度高的情况下,矫顽力难以呈现,容易产生磁化反转核,因此难以得到良好的矩形比,成为使永久磁铁的(bh)max下降的主要原因。磁化反转核容易在磁性弱的部分产生。宏观规模的磁性弱的部分例如为晶界相或非磁性相等的周边。在磁性弱的部分多的情况下,部分被磁化反转的区域通过外部场散逸。由此导致矩形比变差。作为非磁性相之一的r元素的氧化物相在晶粒内或晶界相内析出,成为磁化反转核的起点,因此使磁化强度等磁铁特性下降。r元素的氧化物相由于主相中主要的r元素(尤其是sm)与氧发生反应而析出。本实施方式的永久磁铁除了在可维持足够的烧结体密度的范围内减少r元素的氧化物相的析出量之外,还减少了晶界相中析出的上述氧化物相。藉此,可在高铁浓度组成范围内保持足够的矫顽力、同时实现优异的矩形比。如果r元素的氧化物相在晶界相析出,则容易发生磁化反转。与此相对,通过使r元素的氧化物相在不易磁反转的晶粒内析出,则可抑制非磁性相周边的磁化反转核产生概率。本实施方式的永久磁铁的烧结体中,存在于晶界相的r元素的氧化物的数量nb与晶粒的数量ng之比(nb/ng)优选在1.1以下(nb/ng≤1.1)。在nb/ng比1.1大情况下,存在于晶界相的r元素的氧化物相多。nb/ng更优选在1.0以下,进一步优选在0.8以下。通过抑制存在于晶界相的r元素的氧化物相的析出,能够在含有高浓度fe的r-co系磁铁中保持足够的矫顽力、同时呈现高剩余磁化强度和优异的矩形比。即,可使永久磁铁的(bh)max值提高,从而能够提供高性能的永久磁铁。nb/ng如下测定。通过sem-edx分析永久磁铁的组成。sem中,例如在倍率300倍下观察200μm×400μm以上300μm×500μm以下的区域。加速电压优选设为20kv。利用sem-edx来进行的分析中,对具有最大面积的面中最长边的中央部与边垂直(曲线的情况下与中央部的切线垂直)地切断出的剖面的表面部和内部进行组成测定。测定部位如下定义:在上述剖面上设置以各边的1/2的位置为起点、与边垂直地向内侧延伸至端部的第一基准线,和以各角部的中央为起点、在角部的内角的角度1/2位置向内侧延伸至端部的第二基准线,将从这些第一基准线以及第二基准线的起点起算的、基准线的长度的1%的位置定义为表面部,40%的位置定义为内部。另外,在角部因倒角等而具有曲率的情况下,将相邻的边延长而得的交点作为边的端部(角部的中央)。在该情况下,测定部位不是从交点起算的位置,而是从与基准线相接的部分起算的位置。通过如上设置测定部位,在例如剖面为四边形的情况下,第一基准线以及第二基准线各4根,基准线总计8根,测定部位是在表面部以及内部的各8处。图1是烧结体的剖面的一部分的sem图像。图1示出的剖面具有晶粒1、晶界相2、和r元素的氧化物相3。r元素的氧化物相3由含有r元素以及氧、且r元素以及氧的浓度在85原子%以上的连续区域来定义。此外,r元素的氧化物相3的构成元素几乎为r元素和氧,r元素浓度在35原子%以上。晶粒1以及晶界相2例如通过对试样实施化学蚀刻或ar蚀刻来进行观察。化学蚀刻例如可采用奈塔尔硝酸乙醇腐蚀液(ナイタール)。接着,对sem图像中的晶粒1的数量(ng)和存在于晶界相2的r元素的氧化物相3的数量(nb)进行计数。存在于晶界(晶界相)的氧化物相定义为上述氧化物相的区域与晶界(晶界相)相接或交叉者。图2是包括表示图1所示出的晶界相2的虚线、和表示存在于晶界相2的r元素的氧化物相3的空心圆标记的sem图像。通过sem观察的r元素的氧化物相3如图1以及图2所示,具有直径为0.5~20μm左右的白色粒子形状。本实施方式中,优选表面部以及内部的各8处全部都在上述的nb/ng的范围内,但至少表面部以及内部的各4处以上在上述的范围内即可。在该情况下,不规定1根基准线上的表面部以及内部的关系。如此,对规定的烧结体内部的观察面进行研磨而使其平滑后进行观察。测定各测定部位内的nbtotal/ngtotal比,求出去除这些测定值中的最大值和最小值后的值的平均值,将该平均值作为nb/ng。本实施方式的永久磁铁中,烧结体的空孔率优选在2%以下,更优选在1.5%以下,进一步优选在1.1%以下。烧结磁铁的空孔率低即每单位体积的主相的比例高,意味着可得到高磁化强度。空孔导致磁化强度的下降,在空孔周边会产生反磁场,磁化强度以缺损的主相的比例以上的程度下降。通过使空孔率在2%以下,则可抑制空孔导致的磁化强度下降。空孔例如在图1所示出的sem图像中作为黑色的点状穴观察到。空孔率采用sem图像的面积(stotal)和穴面积总和(svacancy)、由svacancy/stotal×100来表示。矩形比如下评价。首先,通过直流b-h追踪装置测定室温下的直流磁化特性。接着,通过由测定结果得到的b-h曲线求出作为磁铁的基本特性的剩余磁化强度mr和矫顽力ihc以及最大磁能积(bh)max。此时,用mr由下式(1)求出理论最大值(bh)max。(bh)max(理论值)=mr2/4μ0…(1)矩形比的指标(α)通过测定得到的(bh)max与(bh)max(理论值)之比来评价,由下式(2)求出。(bh)max(实测值)/(bh)max(理论值)×100…(2)接着,对永久磁铁的制造方法例进行说明。首先,制备含有永久磁铁的合成所必需的规定元素的合金粉末。例如,可通过将由电弧熔化法或高频熔化法得到的熔液进行铸造得到合金铸锭,将该合金铸锭粉碎来制备合金粉末。合金粉末可将组成不同的多种粉末混合来制成所希望的组成。作为合金粉末的其他制备方法的例子,可例举机械合金法、机械研磨法、气体雾化法、还原扩散法等。通过使用薄带连铸法,可提高合金粉末的均匀性。而且,还能通过对合金粉末或粉碎前的合金材料实施热处理来使该材料均质化。例如,可使用喷磨机、球磨机等对材料进行粉碎。另外,通过在惰性气体气氛或有机溶剂中对材料进行粉碎,可防止粉末的氧化。粉碎后的粉末的平均粒径优选在5μm以上8μm以下。粉碎后的粉末的平均粒径更优选在5.5μm以上7.5μm以下,进一步优选在6μm以上7μm以下。通过将粒径1μm以下的粒子的比例设在1体积%以下,可抑制氧化物量。通过将粒径10μm以上的粒子的比例设在2体积%以下,可减少烧结后制造的烧结体的空孔率,实现足够的密度。粉末的平均粒径由通过激光衍射法等测定的粒度分布中累积分布达到50%的粒子径(中值粒径:d50)的值来定义。喷磨机适用于这样的粉末的制造。接着,向设置于电磁铁中的模具内填充合金粉末,一边施加磁场一边加压成形,藉此制造结晶轴取向了的压粉体。作为成型方式,有以干法成型的方法和以湿法成型的方法。以干法成型的方法中,为了提高粉末的流动性和抗氧化,优选微量添加润滑剂。作为润滑剂,例如可例举硅油或矿物油等。接着,通过对上述压粉体在1180℃以上1250℃以下实施0.5小时以上15小时以下的热处理来进行烧结。在热处理温度低于1180℃情况下,烧结体的密度变得不足。在热处理温度超过1250℃的情况下,存在因粉末中的sm等r元素过多蒸发等而磁特性下降的情况。热处理温度例如优选在1180℃以上1220℃以下,更优选在1190℃以上1210℃以下。在热处理时间低于0.5小时的情况下,有不能得到足够的密度之虞。在热处理时间超过15小时的情况下,则粉末中的r元素的蒸发变得过多,有磁特性下降之虞。热处理时间优选在1小时以上10小时以下,进一步优选在1小时以上7小时以下。上述烧结中,为了抑制氧化,优选在真空中或氩气等惰性气氛中进行热处理。例如,维持真空直至接近保持温度,之后切换为氩气氛,等温保持,藉此可降低空孔率并提高烧结体密度。对得到的烧结体进行2阶段以上的热处理,热处理后以150℃/分钟以上的冷却速度进行急冷。第一阶段的热处理是在比烧结时的热处理温度略低的温度下长时间保持的高质化热处理。第二阶段的热处理是在比第一阶段的热处理更低的温度下进行的熔体化热处理。通过进行熔体化热处理,可使作为前体相的tbcu7型晶相(1-7相)单相化。另外,任一个热处理均优选在真空中或氩气等惰性气氛中进行。高质化热处理中,例如通过在比烧结时的热处理温度低10℃以上的温度下、且比熔体化热处理时的热处理温度高10℃以上的温度下保持4小时以上30小时以下来进行热处理。高质化热处理时的温度优选在1130℃以上1190℃以下。在比烧结时的热处理温度过高的情况下,会产生由液相生成的异相,存在使磁特性下降的情况,还存在导致r元素蒸发的情况。而且,在熔体化热处理中,温度低、元素扩散慢而不会充分地结晶生长。如果高质化热处理的时间少于4小时,则不会充分地进行结晶生长或元素扩散,会使晶粒内的氧化物的生成比例降低。如果高质化热处理的时间超过30小时,则有r元素蒸发之虞,还存在生产性下降的情况。高质化热处理的时间优选在12小时以上28小时以下,更优选在14小时以上24小时以下。熔体化热处理中,在比高质化热处理的温度低10℃以上的温度下进行热处理。熔体化热处理的温度优选在1100℃以上1180℃以下。在熔体化热处理的温度低于1100℃或超过1180℃的情况下,前体相以外的比例变小,有磁特性下降之虞。熔体化热处理的温度更优选例如在1110℃以上1170℃以下。熔体化热处理的时间优选在4小时以上30小时以下。在熔体化热处理的时间低于4小时的情况下,元素扩散不充分,构成相容易变得不均匀,有磁特性下降之虞。在熔体化热处理的时间超过30小时的情况下,烧结体中的r元素有蒸发之虞,还会生产性下降。熔体化热处理的时间更优选在4小时以上12小时以下。2阶段的热处理后进行将冷却速度设在150℃/分钟以上冷却至室温为止的急冷,藉此可使tbcu7型晶相稳定化,矫顽力容易呈现。在冷却速度低于150℃/分钟的情况下,在冷却中容易生成ce2ni7型晶相或th2zn17型晶相。接着,对熔体化热处理后的烧结体实施时效处理而形成相分离区域。时效处理中,优选在700℃以上900℃以下的温度下进行10小时以上100小时以下的热处理后,以0.1℃/分钟以上5℃/分钟以下的冷却速度缓慢冷却至20℃以上600℃以下的温度,之后,冷却至室温。通过在这样的条件下实施时效处理,能够提高具有相分离组织的永久磁铁的矫顽力等。为了防止氧化,时效处理优选在真空中或氩气等惰性气体气氛中进行。在时效处理的温度低于700℃或超过900℃的情况下,不能得到均质的晶胞相和胞壁相的混合组织,有永久磁铁的磁特性下降之虞。时效处理的温度优选在750℃以上880℃以下,更优选在780℃以上850℃以下。在时效处理的时间低于10小时的情况下,有胞壁相尚未充分生成、或元素扩散不充分之虞。另一方面,在保持时间超过100小时的情况下,有因胞壁相变厚而晶胞相的体积分数下降、或因晶粒粗大化而不能得到良好的磁铁特性之虞。时效热处理时间更优选在10小时以上90小时以下,进一步优选在20小时以上80小时以下。在缓慢冷却时的冷却速度低于0.1℃/分的情况下,生产性下降,有成本增大之虞。在缓慢冷却时的冷却速度超过5℃/分钟的情况下,不能得到均质的晶胞相和胞壁相的混合组织,有永久磁铁的磁特性下降之虞。时效处理后的冷却速度优选在0.3℃/分钟以上4℃/分钟以下,更优选在0.5℃/分钟以上3℃/分钟以下。也可在上述时效处理之前进行在比时效热处理温度低的温度下进行热处理的预时效处理。预时效处理中,优选在500℃以上900℃以下的温度下进行0.5~10小时热处理后,以0.1℃/分钟以上5℃/分钟以下的冷却速度缓慢冷却至20℃以上450℃以下的温度。通过进行预时效处理,可提高磁特性的矩形比。(第二实施方式)第一实施方式的永久磁铁可用于汽车或轨道车辆等中所具备的各种电动机或发电机等旋转电机。此外,也能够作为可变磁通量电动机或可变磁通量发电机的固定磁铁、或可变磁铁使用。通过使用第一实施方式的永久磁铁,可构成各种电动机或发电机。在将第一实施方式的永久磁铁用于可变磁通量电动机的情况下,在可变磁通量电动机的结构或驱动系统中,可应用例如日本专利特开2008-29148号公报或日本专利特开2008-43172号公报中公开的技术。接着,参照附图,对具有上述永久磁铁的旋转电机进行说明。图3是示出本实施方式的永久磁铁电动机的图。图3所示出的永久磁铁电动机21中,在定子(固定子)22内配置有转子(旋转子)23。在转子23的铁芯24中,配置有作为第一实施方式的永久磁铁的永久磁铁25。通过使用第一实施方式的永久磁铁,基于各永久磁铁的特性等,可实现永久磁铁电动机21的高效化、小型化、低成本化等。图4是示出本实施方式的可变磁通量电动机的图。在图4所示出的可变磁通量电动机31中,在定子(固定子)32内配置有转子(旋转子)33。在转子33的铁芯34中,配置有第一实施方式的永久磁铁来作为固定磁铁35以及可变磁铁36。可变磁铁36的磁通量密度(磁通量的量)能够可变。可变磁铁36由于其磁化方向与q轴方向正交,因此不受q轴电流的影响,可通过d轴电流来磁化。转子33上设置有磁化绕组(未图示)。通过在该磁化绕组中流过来自磁化电路的电流,成为其磁场直接作用于可变磁铁36的结构。通过采用第一实施方式的永久磁铁,则可在固定磁铁35中得到合适的矫顽力。在将第一实施方式的永久磁铁用于可变磁铁36的情况下,只要通过变更前述的制造方法的各种条件(时效处理条件等)、例如将矫顽力控制在100ka/m以上500ka/m以下的范围内即可。另外,图4所示出的可变磁通量电动机31中,固定磁铁35以及可变磁铁36可以均使用第一实施方式的永久磁铁,但也可以任一方的磁铁使用第一实施方式的永久磁铁。由于可变磁通量电动机31能够以小装置尺寸输出大转矩,因此适合要求电动机高输出·小型化的混合动力汽车或电动汽车等车辆用的电动机。图5示出本实施方式的发电机。图5所示出的发电机41具有使用上述永久磁铁的定子(固定子)42。配置于定子(固定子)42内侧的转子(旋转子)43介由转轴45与设置于发电机41一端的涡轮44连接。涡轮44例如在从外部供给的流体的作用下旋转。另外,也能通过传递汽车等车辆的再生能量等动态旋转来代替在流体的作用下旋转的涡轮44,使转轴45旋转。定子42和转子43可采用各种公知的构成。转轴45与配置于相对于转子43在涡轮44的相反侧的整流子(未图示)接触,通过转子43的旋转而产生的电动势作为发电机41的输出,介由相分离母线以及主变压器(未图示)被升压为系统电压而进行供电。发电机41也可以是通常的发电机以及可变磁通量发电机中的任一种。另外,转子43上会产生来自涡轮44的静电和伴随发电产生的轴电流而发生的带电。因此,发电机41具备用于对转子43的带电进行放电的电刷46。如上,通过在发电机中采用上述永久磁铁,可得到高效化、小型化、低成本化等效果。实施例(实施例1、2)按照表1示出的组成秤量各原料后,通过高频熔化制成合金铸锭。将铸锭粗粉碎后,用喷磨机进行微粉碎而制成平均粒径为6μm的合金微粉末。在1.5t的磁场中以1t加压力对所得到的微粉末加压而制成压粉体。对所得到的压粉体进行烧结。在烧结中,在真空中使其升温至1175℃,保持30分钟后,导入ar,在ar气氛中使其升温至1210℃,保持3小时。接着,通过在ar气氛中在1180℃下保持14小时进行高质化热处理后,在1160℃下保持12小时进行熔体化热处理,以170℃/分钟的速度冷却至室温。接着,作为时效处理对熔体化热处理后的烧结体实施ar气氛中830℃、40小时的热处理,然后以0.7℃/分钟的冷却速度缓慢冷却至300℃,进一步冷却至室温。通过以上的工序得到烧结磁铁。进而,分别测定烧结磁铁的nb/ng、剩余磁化强度mr、矫顽力ihc、矩形比的指标α、以及空孔率。这些结果示于表2。(实施例3、4)按照表1示出的组成秤量各原料后,通过高频熔化制成合金铸锭。将合金铸锭粗粉碎后,用喷磨机进行微粉碎而制成平均粒径为7μm的合金微粉末。在1.5t的磁场中以2t加压力对合金粉末进行加压而制成压粉体。在真空中将压粉体升温至1180℃,保持1小时后在ar气氛中升温至1200℃,然后保持5小时进行烧结。接着,通过在ar气氛中在1160℃下保持20小时进行高质化热处理后,在1130℃下保持20小时进行熔体化热处理,以180℃/分钟的速度冷却至室温。接着,作为时效处理对熔体化热处理后的烧结体实施ar气氛中700℃下1小时的热处理,然后在850℃下实施50小时的热处理,以0.4℃/分钟的冷却速度缓慢冷却至500℃,进一步冷却至室温。通过以上的工序得到烧结磁铁。进而,分别测定烧结磁铁的nb/ng、剩余磁化强度mr、矫顽力ihc、矩形比的指标α、以及空孔率。这些结果示于表2。(比较例1)按照表1示出的组成秤量各原料后,在与实施例1相同的条件下制成压粉体。在真空中使压粉体升温至1175℃,保持30分钟后,导入ar,在ar气氛中使其升温至1210℃,保持3小时来进行烧结。接着,通过在ar气氛中在1180℃下保持4小时进行高质化热处理后,在1160℃下保持3小时进行熔体化热处理,以170℃/分钟的速度冷却至室温。接着,作为时效处理对熔体化热处理后的烧结体实施ar气氛中830℃、40小时的热处理,然后以0.7℃/分钟的冷却速度缓慢冷却至300℃,进一步冷却至室温。通过以上的工序得到烧结磁铁。进而,分别测定烧结磁铁的nb/ng、剩余磁化强度mr、矫顽力ihc、矩形比的指标α、以及空孔率。这些结果示于表2。(比较例2)按照表1示出的组成秤量各原料后,通过高频熔化制成合金铸锭。将铸锭粗粉碎后,用喷磨机进行微粉碎而制成平均粒径为3μm的合金微粉末。在1.5t的磁场中以1t加压力对所得到的微粉末进行加压而制成压粉体。在与实施例3相同的条件下对所得到的压粉体进行烧结而制成烧结体。接着,通过在ar气氛中在1160℃下保持20小时进行高质化热处理后,在1130℃下保持20小时进行熔体化热处理,以180℃/分钟的速度冷却至室温。接着,作为预时效处理对熔体化热处理后的烧结体在750℃下实施2小时的热处理,然后以1.5℃/分钟的冷却速度缓慢冷却至200℃。继而,作为时效处理在850℃下实施10小时的热处理后,以1℃/分钟的冷却速度缓慢冷却至600℃,进而冷却至室温。预时效处理以及时效处理均在ar气氛中实施。通过以上的工序得到烧结磁铁。进而,分别测定烧结磁铁的nb/ng、剩余磁化强度mr、矫顽力ihc、矩形比的指标α、以及空孔率。这些结果示于表2。(比较例3)按照表1示出的组成秤量各原料后,通过高频熔化制成合金铸锭。将铸锭粗粉碎后,用喷磨机进行微粉碎而制成平均粒径为10μm的合金微粉末。在1.5t的磁场中以1t加压力对所得到的微粉末进行加压而制成压粉体。在真空中使压粉体升温至1180℃,保持1小时后,导入ar,在ar气氛中使其升温至1210℃,保持5小时来进行烧结。接着,通过在ar气氛中在1170℃下保持40小时进行高质化热处理后,在1150℃下保持24小时进行熔体化热处理,以180℃/分钟的速度冷却至室温。接着,作为预时效处理对熔体化热处理后的烧结体在750℃下实施2小时的热处理,然后以1.5℃/分钟的冷却速度缓慢冷却至200℃。继而,作为时效处理在850℃下实施10小时的热处理后,以1℃/分钟的冷却速度缓慢冷却至600℃,进而冷却至室温。预时效处理以及时效处理均在ar气氛中实施。通过以上的工序得到烧结磁铁。进而,分别评价烧结磁铁的nb/ng、剩余磁化强度mr、矫顽力ihc、矩形比的指标α、以及空孔率。这些结果示于表2。(比较例4)按照表1示出的组成秤量各原料后,通过高频熔化制成合金铸锭。将铸锭粗粉碎后,用喷磨机进行微粉碎而制成平均粒径为4μm的合金微粉末。在1.5t的磁场中以1t加压力对所得到的微粉末进行加压而制成压粉体。在真空中使压粉体升温至1170℃,保持1小时后,导入ar,在ar气氛中使其升温至1200℃,保持5小时来进行烧结。接着,通过在ar气氛中在1170℃下保持48小时进行高质化热处理后,在1150℃下保持20小时进行熔体化热处理,以180℃/分钟的速度冷却至室温。接着,作为预时效处理对熔体化热处理后的烧结体在750℃下实施2小时的热处理,然后以1.5℃/分钟的冷却速度缓慢冷却至200℃。继而,作为时效处理在850℃下实施10小时的热处理后,以1℃/分钟的冷却速度缓慢冷却至600℃,进而冷却至室温。预时效处理以及时效处理均在ar气氛中实施。通过以上的工序得到烧结磁铁。进而,分别测定烧结磁铁的nb/ng、剩余磁化强度mr、矫顽力ihc、矩形比的指标α、以及空孔率。这些结果示于表2。[表1]磁铁组成(原子%)实施例1sm11.36fe30.14zr1.77cu5.32co51.41实施例2(sm0.9nd0.1)11.49fe30.09zr1.77cu4.43co52.22实施例3sm11.24fe31.07zr1.78cu5.33co50.58实施例4sm11.24fe31.07(zr0.7ti0.2hf0.1)1.78cu5.33co50.58比较例1sm11.36fe30.14zr1.77cu5.32co51.41比较例2sm11.24fe31.07zr1.78cu5.33co50.58比较例3sm11.36fe30.14zr1.77cu5.32co51.41比较例4sm11.36fe30.14zr1.77cu5.32co51.41[表2]sem观察的结果是,实施例1~4、比较例1~4的烧结磁铁都具备:具有构成主相的th2zn17型晶相的晶粒、晶粒的晶界、和r元素的氧化物相。此外,由表2明确可知,实施例1~4的烧结磁铁均在维持高剩余磁化强度和矫顽力的同时,还具有α超过92%的良好的矩形比。与此相对,比较例1~4的永久磁铁由于nb/ng高、r元素的氧化物相分散于晶界,因此矩形比差。说明了本发明的几个实施方式,但这些实施方式仅是作为例子而举出,并不是用来限定本发明的范围。这些新的实施方式能够以其他各种方式实施,在不脱离发明的技术思想的范围内可进行各种省略、置换、变更。这些实施方式及其变形都包括在发明的范围和技术思想内,也包括在与权利要求所记载的发明及其等同的范围内。当前第1页12