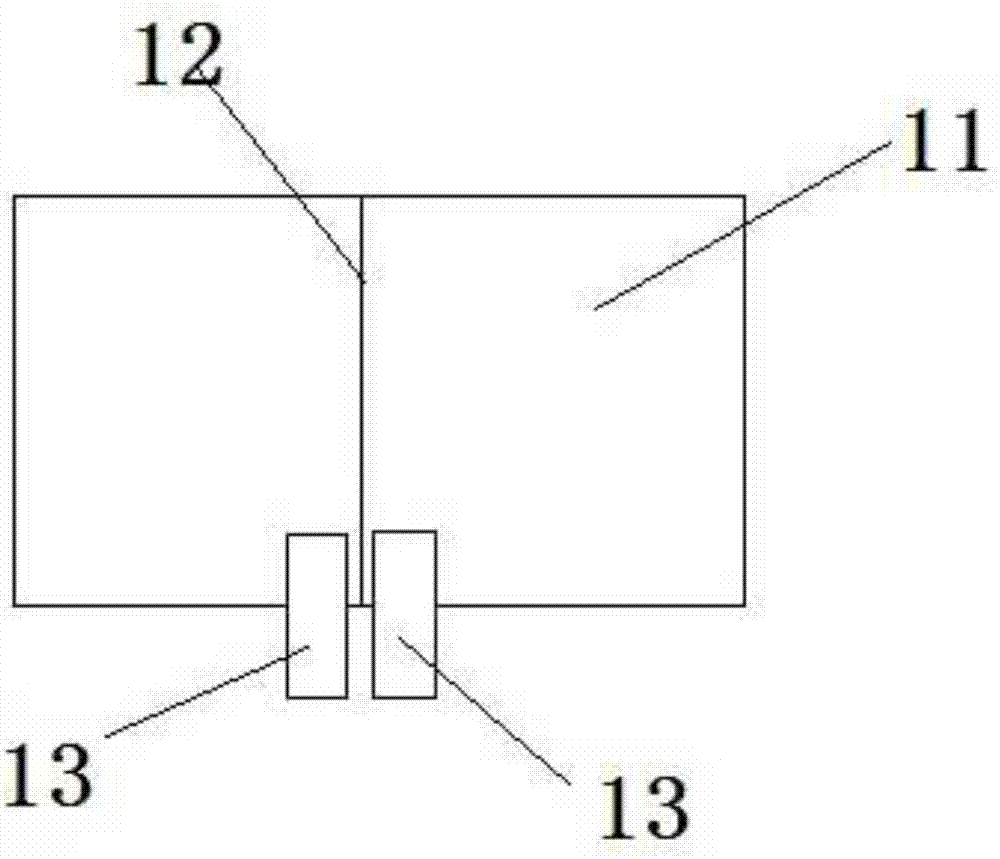
本发明涉及胶带
技术领域:
,具体地是涉及一种光伏组件背板用修补胶带贴合工艺及其应用。
背景技术:
:太阳能组件背板需具有可靠的绝缘性和阻水性,以保证组件的正常运行。目前,组件破损主要有两种,一种是组件在运输及安装过程中,部分组件背板会被破损划伤,导致组件运行时的安全性失效和功能失效;另一种是组件在户外使用一段时间后,背板会出现逐步老化开裂现象,达不到组件运行时的安规性要求。针对破损的背板只能进行组件的更换,若大批量更换则成本极高,旧组件回收难还造成环境污染大。鉴于此背景,开发出一种修补胶带可在现场施工、环保无废弃物、成本低廉,使破损的组件在质保期内能正常运转,具有深远意义。技术实现要素:鉴于上述现有技术中存在的缺陷,本发明的目的是提出一种光伏组件背板用修补胶带贴合工艺及其应用,当仅背板出现异常时,无需更换全部光伏组件,通过对背板的修补,能使破损的光伏组件在质保期内正常运行,有效地提升了光伏组件的价值,延长了光伏组件的使用寿命。为了实现上述目的,本发明采用了如下技术方案:一种光伏组件背板用修补胶带贴合工艺,包括以下步骤:步骤一:对光伏组件背板进行外观检查,并对外观检查结果有异常的光伏组件背板进行判断是需要局部修补还是全面修补;步骤二:对需修补的光伏组件背板进行清洁处理;步骤三:使用光伏组件背板用修补胶带对清洁处理后的光伏组件背板进行局部修补或全面修补的贴合;步骤四:检验修补效果。进一步的,所述步骤一中,对光伏组件背板进行湿漏电测试,检测其绝缘性以判断是需要修补,如组件面积大于0.1m2,测出的绝缘电阻数值乘以组件面积小于40mω·m2,则需进行全面修补;如组件面积大于0.1m2的组件,测出的绝缘电阻数值乘以组件面积大于等于40mω.m2,组件绝缘性测试通过,但外观仍有划伤则需要进行局部修补。进一步的,所述湿漏电测试包括以下步骤:步骤1)将光伏组件背板置于盛有介质溶液的浅槽中,浅槽的尺寸与光伏组件背板的尺寸相匹配,介质溶液至少覆盖光伏组件背板,介质溶液的电阻率小于等于3500ω·cm,表面张力小于等于3n·m-1,温度22℃±3℃;步骤2)将光伏组件背板上的输出端短路,连接到绝缘电阻测试仪的正极,使用金属导体将介质溶液连接到绝缘电阻测试仪的负极;步骤3)调节绝缘电阻测试仪的直流电压至1000v,维持此电压不少于60s后,测出光伏组件背板的绝缘电阻数值;步骤4)降低直流电压至0,将绝缘电阻测试仪的引出端短路,以释放光伏组件背板内部的电压;步骤5)若组件湿漏电测试未通过,需进行修补,则采用红外线辐射加热装置或热吹风机对组件背板进行加热,组件背板表面加热温度不超过80℃,以去除光伏组件背板中的微量水分,同时使用微型探针检查组件背板水分含量,要求不大于1000ppm。进一步的,所述步骤二具体包括如下:步骤1)将待修补的光伏组件背板面朝上地放置于工作平台上,用吸尘设备对光伏组件背板表面进行预吸尘处理;步骤2)用毛刷对光伏组件背板表面进行除尘处理;步骤3)用有机溶剂对光伏组件背板表面进行清洗;步骤4)用吸尘设备对光伏组件背板表面进行吸尘。进一步的,所述步骤三中的局部修补的贴合包括以下步骤:步骤1)根据组件背板划伤处面积进行定量化贴合修补,裁出修补胶带尺寸,其胶带外围距划伤边缘处距离大于等于5cm;步骤2)将裁片的修补胶带,撕开其离型材料层,粘贴于需修补处,同时使用压辊对其进行压实贴合。进一步的,所述步骤三中的全面修补的贴合包括以下步骤:步骤1)将所述光伏组件背板用高性能修补胶带切割成若干个的第一片材,2个第二片材和1个第三片材,所述第一片材的离型材料层的中心线上设有切割线,所述切割线的两侧的离型材料层上分别设有第一撕手胶带,所述第二片材和所述第三片材的离型材料层上分别设有第二撕手胶带和第三撕手胶带;步骤2)所述光伏组件背板的一端安装有接线盒,将第1个所述第一片材贴合于所述光伏组件背板远离所述接线盒的一端,所述第一片材的短边沿所述光伏组件背板的长边铺平,所述第一片材的长边沿所述光伏组件背板的短边铺平,从所述第一片材的中间撕开所述离型材料层,同时用压辊或刮板贴合,使所述第一片材的半边的功能胶层贴于所述光伏组件背板上,并去除所述功能胶层与所述光伏组件背板之间的气泡,重复上述方法,完成所述第一片材的另半边贴合,从而完成第1个所述第一片材的贴合;步骤3)重复步骤2),依次贴合剩余的所述第一片材,直至贴合至所述接线盒的下边缘;步骤4)将2个所述第二片材一端的短边分别沿所述接线盒的左右两侧的边缘铺平,另一端的短边分别沿所述光伏组件背板的长边铺平,撕开其中一个所述第二片材的所述离型材料层,同时用压辊或刮板贴合,使所述功能胶层贴于所述光伏组件背板上,并去除所述功能胶层与所述光伏组件背板之间的气泡;重复上述方法,完成另一个所述第二片材的贴合;步骤5)将所述第三片材的长边分别沿所述接线盒的上边缘和所述光伏组件背板的短边铺平,撕开所述第三片材的所述离型材料层,将所述功能胶层贴于所述光伏组件背板上,同时用压辊或刮板贴合,使所述功能胶层贴于所述光伏组件背板上,并去除所述功能胶层与所述光伏组件背板之间的气泡;步骤6)在所述第一片材、第二片材和第三片材的边缘与平行相邻的所述光伏组件背板的边缘和所述接线盒的边缘之间进行密封;相邻的所述第一片材、第二片材和第三片材之间依次重叠贴合,重叠贴合宽度大于等于50mm。进一步的,所述步骤6)中通过硅胶或绝缘胶带进行密封。进一步的,所述第一片材、第二片材和第三片材的边缘与平行相邻的所述光伏组件背板的边缘和所述接线盒的边缘之间的距离小于等于1mm。进一步的,所述步骤四具体包括如下:步骤1)将修补好的光伏组件背板置于盛有介质溶液的浅槽中,浅槽的尺寸与光伏组件背板的尺寸相匹配,介质溶液至少覆盖光伏组件背板,介质溶液的电阻率小于等于3500ω·cm,表面张力小于等于3n.m,温度22℃±3℃;步骤2)将光伏组件背板上的输出端短路,连接到绝缘电阻测试仪的正极,使用金属导体将介质溶液连接到绝缘电阻测试仪的负极;步骤3)调节绝缘电阻测试仪的直流电压至1000v,维持此电压不少于60s后,测出光伏组件背板的绝缘电阻数值;步骤4)降低直流电压至0,将绝缘电阻测试仪的引出端短路,以释放光伏组件背板内部的电压。一种根据上述的任一种光伏组件背板用修补胶带贴合工艺的应用,用于光伏组件背板的现场修补。本发明的光伏组件背板用修补胶带贴合工艺的突出效果为:1.可在现场维修破损的光伏组件背板,不需要运输至工厂,节省劳力和运输费用,同时避免组件在运输时产生的引裂;2.可在短时间以内完成光伏组件背板的局部修补或全面修补,修补效率高;3.采用本发明的贴合工艺贴合的背板,可以防止雨水的反渗透,片材胶带间的重叠贴合宽度大于等于50mm,以保证片材胶带间的防水性和绝缘性;4.使用压辊或刮板可以避免贴合气泡,保证贴合质量;5.修补后的光伏组件背板,其修补效果可通过湿漏电测试快速判断,保证了修补质量可控,检验方便。附图说明图1为本发明实施例的贴合工艺结构示意图;图2为本发明实施例的第一片材的离型材料层的结构示意图;图3为本发明实施例的第二片材的离型材料层的结构示意图;图4为本发明实施例的第三片材的离型材料层的结构示意图。具体实施方式下面将结合本发明实施例中的附图,对本发明实施例中的技术方案进行清楚、完整地描述,显然,所描述的实施例仅仅是本发明一部分实施例,而不是全部的实施例。实施例本实施例的一种光伏组件背板用修补胶带贴合工艺,包括以下步骤:步骤一:对光伏组件背板进行湿漏电测试,检测其绝缘性以判断是需要修补,如组件面积大于0.1m2,测出的绝缘电阻数值乘以组件面积小于40mω·m2,则需进行全面修补;如组件面积大于0.1m2的组件,测出的绝缘电阻数值乘以组件面积大于等于40mω·m2,组件绝缘性测试通过,但外观仍有划伤则需要进行局部修补;其中,湿漏电测试包括以下步骤:步骤1)将光伏组件背板置于盛有介质溶液的浅槽中,浅槽的尺寸与光伏组件背板的尺寸相匹配,介质溶液至少覆盖光伏组件背板,介质溶液的电阻率小于等于3500ω·cm,表面张力小于等于3n·m,温度22℃±3℃;步骤2)将光伏组件背板上的输出端短路,连接到绝缘电阻测试仪的正极,使用金属导体将介质溶液连接到绝缘电阻测试仪的负极;步骤3)调节绝缘电阻测试仪的直流电压至1000v,维持此电压不少于60s后,测出光伏组件背板的绝缘电阻数值;步骤4)降低直流电压至0,将绝缘电阻测试仪的引出端短路,以释放光伏组件背板内部的电压;步骤5)若组件湿漏电测试未通过,需进行修补,则采用红外线辐射加热装置或热吹风机对组件背板进行加热,组件背板表面加热温度不超过80℃,以去除光伏组件背板中的微量水分,同时使用微型探针检查组件背板水分含量,要求不大于1000ppm。步骤二:对需修补的光伏组件背板进行清洁处理,具体包括如下:步骤1)将待修补的光伏组件背板面朝上地放置于工作平台上,用吸尘设备对光伏组件背板表面进行预吸尘处理;步骤2)用毛刷对光伏组件背板表面进行除尘处理;步骤3)用有机溶剂对光伏组件背板表面进行清洗;步骤4)用吸尘设备对光伏组件背板表面进行吸尘。步骤三:使用光伏组件背板用修补胶带对清洁处理后的光伏组件背板进行局部修补或全面修补的贴合;局部修补的贴合包括以下步骤:步骤1)根据组件背板划伤处面积进行定量化贴合修补,裁出修补胶带尺寸,其胶带外围距划伤边缘处距离大于等于5cm;步骤2)将裁片的修补胶带,撕开其离型材料层,粘贴于需修补处,同时使用压辊对其进行压实贴合。如图1-4所示,全面修补的贴合包括以下步骤:步骤1)将光伏组件背板7用高性能修补胶带切割成3个第一片材1,2,3,2个第二片材4,5和1个第三片材6,第一片材1,2,3的离型材料层11的中心线上设有切割线12,切割线12的两侧的离型材料层11上分别设有第一撕手胶带13,第二片材4,5和第三片材6的离型材料层14和15上分别设有第二撕手胶带16和第三撕手胶带17,其中设置切割线和撕手胶带的目的都是为了便于客户贴合修补胶带快速揭离离型材料层;步骤2)光伏组件背板7的一端安装有接线盒8,将第1个第一片材1贴合于光伏组件背板7远离接线盒8的一端,第一片材1的短边1a沿光伏组件背板7的长边7b铺平,第一片材1的长边1b沿光伏组件背板7的短边7a铺平,从第一片材1的中间撕开离型材料层,同时用压辊或刮板贴合,使第一片材1的半边的功能胶层贴于光伏组件背板7上,并去除功能胶层与光伏组件背板之间的气泡,重复上述方法,完成第一片材1的另半边贴合,从而完成第1个第一片材1的贴合;步骤3)重复步骤2),依次贴合第一片材2,3,直至贴合至接线盒8的下边缘8a;步骤4)将第二片材4,5一端的短边4a,5a分别沿接线盒8的左右两侧的边缘8c,8d铺平,另一端的短边4a,5a分别沿光伏组件背板的长边7b铺平,撕开第二片材4的离型材料层,同时用压辊或刮板贴合,使功能胶层贴于光伏组件背板7上,并去除功能胶层与光伏组件背板7之间的气泡;重复上述方法,完成第二片材5的贴合;步骤5)将第三片材6的长边6b分别沿接线盒8的上边缘8b和光伏组件背板7的短边7a铺平,撕开第三片材6的离型材料层,将功能胶层贴于光伏组件背板7上,同时用压辊或刮板贴合,使功能胶层贴于光伏组件背板7上,并去除功能胶层与光伏组件背板7之间的气泡;步骤6)在第一片材1,2,3,第二片材4,5和第三片材6的边缘与平行相邻的光伏组件背板7的边缘和接线盒8的边缘之间通过硅胶9或绝缘胶带9进行密封;第一片材1,2,3,第二片材4,5和第三片材6的边缘与平行相邻的光伏组件背板7的边缘和接线盒8的边缘之间的距离小于等于1mm,相邻的第一片材1,2,3,第二片材4,5和第三片材6之间依次重叠贴合(见图1中的重叠区域10),重叠贴合宽度大于等于50mm。步骤四:检验修补效果,具体包括如下:步骤1)将修补好的光伏组件背板置于盛有介质溶液的浅槽中,浅槽的尺寸与光伏组件背板的尺寸相匹配,介质溶液至少覆盖光伏组件背板,介质溶液的电阻率小于等于3500ω·cm,表面张力小于等于3n·m-1,温度22℃±3℃;步骤2)将光伏组件背板上的输出端短路,连接到绝缘电阻测试仪的正极,使用金属导体将介质溶液连接到绝缘电阻测试仪的负极;步骤3)调节绝缘电阻测试仪的直流电压至1000v,维持此电压不少于60s后,测出光伏组件背板的绝缘电阻数值;步骤4)降低直流电压至0,将绝缘电阻测试仪的引出端短路,以释放光伏组件背板内部的电压。一种上述光伏组件背板用修补胶带贴合工艺的应用,用于光伏组件背板的现场修补,当仅背板出现异常时,无需更换全部光伏组件。应用本实施例的光伏组件面积为1.63m2,用修补胶带贴合工艺,对5个存在破损的光伏组件背板1-5进行局部修补或全面修补,修补前后进行湿漏电测试的结果见表1:表1组别修补前绝缘电阻数值(mω)修补后绝缘电阻数值(mω)背板111241背板216186背板37173背板412285背板517272由此可见,破损背板使用修补胶带贴合后其绝缘性测试通过。以上所述,仅为本发明较佳的具体实施方式,但本发明的保护范围并不局限于此,任何熟悉本
技术领域:
的技术人员在本发明揭露的技术范围内,根据本发明的技术方案及其发明构思加以等同替换或改变,都应涵盖在本发明的保护范围之内。当前第1页12