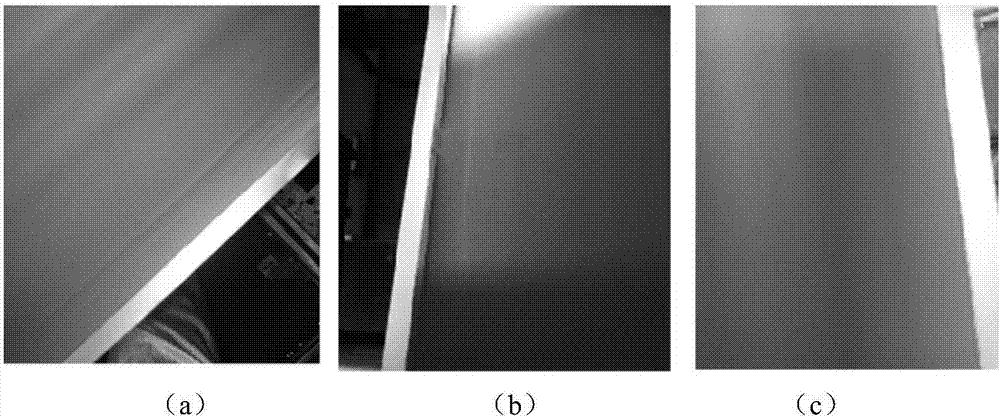
本发明涉及一种锂离子电池负极片的制备方法、锂离子电池负极片及锂离子电池,属于锂离子电池
技术领域:
。
背景技术:
:锂离子电池因为比能量高、循环寿命长等优点已经广泛应用于电动车、储能、数码电子产品等领域中,而且在这些领域中对电池的性能的要求也越来越高。随着电动车、储能等产业的快速发展,对锂离子电池的需求量也越来越大,对锂离子电池生产时的生产效率的要求越来越高。现有技术中,为了提高锂离子电池的生产效率,一般会提高极片的涂布速度同时提高极片烘干时的温度,这些操作非常容易导致极片上涂层开裂或卷边。特别是采用la133作为粘结剂的浆料,相比sbr,在涂布过程中更容易发生开裂或卷边现象。现有技术中为了克服极片开裂或卷边现象,一般采用调整干燥温度或者向合浆浆料中加入醇或醚等物质的方式。公开号为cn101420026a的中国发明专利公开了一种锂离子电池正极的制作方法,该方法将涂布后的正极片的干燥过程设置为三个阶段,并设置第一干燥阶段和第三干燥阶段的温度低于第二干燥阶段的温度,三个干燥阶段的温度分别设置为60-70℃、70-90℃和60-70℃。在此基础上,还可以向正极浆料中加入醇或醚作为表面张力调节剂。该方法可以减轻卷边现象。但是,该方法将干燥阶段分为三个阶段,工序较为复杂,大大降低了电池的生产效率,也增加了成本,不利于大规模、高效率的锂离子电池生产。而且,该方法针对锂离子电池正极,不能有效地解决配方体系与正极相差较大的负极的开裂和卷边现象。技术实现要素:本发明的目的在于提供一种效率高、成本低的锂离子电池负极片的制备方法。本发明的另一个目的在于提供一种上述方法制得的锂离子电池负极片及使用该负极片的锂离子电池。为实现上述目的,本发明的锂离子电池负极片的制备方法的技术方案是:一种锂离子电池负极片的制备方法,包括如下步骤:1)将负极材料与水混合均匀制得负极浆料;所述负极材料包括负极活性物质、导电剂、粘结剂、添加剂,所述负极活性物质、导电剂、粘结剂、添加剂的质量比为85.5-95.5:1-3:1.5-3.5:2-8;所述添加剂为碳酸乙烯酯、碳酸丙烯酯中的至少一种;2)将步骤1)制得的负极浆料涂布在负极集流体上,烘干,即得。本发明的锂离子电池负极片制备时,在负极浆料的合浆过程中添加了添加剂,该添加剂为碳酸乙烯酯、碳酸丙烯酯,在涂布时能够降低浆料表面张力,在烘干过程中,能够改变浆料凝固过程中溶剂挥发的动力学和热力学过程,减少由于极片不同区域烘干速度不同造成的张力不均,避免涂布烘干后极片产生开裂、卷边等问题。碳酸乙烯酯和碳酸丙烯酯性能稳定,不会与浆料的其他成分发生反应,不会导致电池的电化学性能下降。而且碳酸乙烯酯和碳酸丙烯酯作为锂离子电池电解液常用的溶剂,即使在极片涂层中有微量的残留,也不会影响电池的电化学性能。这些添加剂价格便宜,也不会过多的增加产品成本。所述粘结剂为la133或la133与sbr组成的混合粘结剂。所述la133为la133粘结剂或改进型的la133粘结剂。改进型的la133粘结剂为la133n。优选的,所述粘结剂为la133与sbr组成的混合粘结剂。la133与sbr的质量比为4-5:1。本发明的负极片的粘结剂包含la133,la133体系粘结剂与sbr(丁苯橡胶)一样,都属于水性粘结剂,大量运用在锂离子电池负极片制作中,但与sbr相比,la133的低温性能更好。但la133体系浆料涂布时的一大问题就是烘干时边缘更容易开裂,而sbr不存在此种问题,所以,负极片制作中使用la133加sbr的混合粘结剂,则一定程度上可以改善la133体系极片的涂布开裂问题。所述负极材料还包括稳定剂,所述负极活性物质与稳定剂的质量比为85.5-95.5:0-1.5;所述稳定剂为cmc、hpmc、hpc中的一种。负极活性物质为本领域常用的负极活性物质,一般的,所述负极活性物质为天然石墨、人造石墨、无定形炭、中间相炭微球中的一种或几种。所述负极材料还包括导电剂,所述负极活性物质与导电剂的质量比为85.5-95.5:1-3;所述导电剂为导电炭黑、superp、ks6、碳纳米管中的一种或几种。烘干的温度以能够快速使溶剂及添加剂挥发但又不会因为温度太高而影响涂层其他成分性能为宜,一般的,步骤2)中烘干的温度为40-120℃。步骤1)中的加料顺序可视具体配方进行调整,一般的,为了得到方便涂布的负极浆料,可采用如下两种加料方式:步骤1)中将负极材料与水混合时,先将稳定剂或稳定剂和粘结剂与水混合均匀制成胶液,然后加入导电剂混合均匀,再加入负极活性物质混合均匀,再加入粘结剂和添加剂或添加剂混合均匀。步骤1)中将负极材料与水混合时,先将导电剂和负极活性物质干混得干混料;然后,将干混料加入由稳定剂和水制成的胶液中混合均匀,再依次加入粘结剂、添加剂混合均匀;或将干混料加入由稳定剂、粘结剂、水制成的胶液中混合均匀,再加入添加剂混合均匀;或将干混料加入由粘结剂和水制成的胶液中,再依次加入稳定剂、添加剂混合均匀。步骤1)中混合均匀时的搅拌速率为900-2500rpm。或者混合均匀时公转转速为15-25rpm,自转转速为900-2500rpm。本发明的锂离子电池负极片的技术方案是:一种采用上述的制备方法制得的锂离子电池负极片。本发明的锂离子电池的技术方案是:一种使用上述锂离子电池负极片的锂离子电池。本发明的有益效果是:本发明的锂离子电池负极片的制备方法在合浆过程中加入了添加剂,能够最大程度地减少涂布烘干过程中极片开裂、卷边等问题,大幅度提高了极片的合格率,减少了因为极片质量差导致的电池性能下降。附图说明图1为对比例1、实施例1和实施例2中不同配方浆料涂布时不同停机时长的极片边缘卷曲情况示意图;图2为对比例1、实施例1和实施例2中制得的锂离子电池负极片的开裂情况外观图。具体实施方式下面对本发明的具体实施方式作进一步说明。实施例1本实施例的锂离子电池负极片的制备方法包括如下步骤:1)将1.838kg粘结剂la133n2溶液与8kg去离子水加入30l的双行星搅拌机中,以2500rpm的转速搅拌2h,然后加入0.2kg导电剂sp,以2500rpm的转速搅拌2h,然后加入人造石墨15kg以2500rpm的转速搅拌2h;之后加入0.4kg添加剂ec,2500rpm的转速搅拌90min制得负极浆料,负极浆料的制备过程总时间约为8-12h;上述人造石墨、sp、la133n2、ec的质量比为92.82:1.27:3.41:2.50;制得的负极浆料的粘度为2000mpas,细度为20μm,固含量为55.82%;2)将步骤1)制得的负极浆料利用转移涂布机在厚度为9μm的铜箔集流体上涂布烘干,裁切加工即得。本实施例的锂离子电池负极片为上述方法制得的负极片。本实施例的锂离子电池的负极片为上述锂离子电池负极片,正极片为镍钴锰三元材料正极片,锂离子电池为按照现有技术中的方法制成的22ah的软包锂离子电池。实施例2本实施例的锂离子电池负极片的制备方法包括如下步骤:1)将1.838kg粘结剂la133n2溶液与8kg去离子水加入30l的双行星搅拌机中,以2500rpm的转速搅拌2h,然后加入0.20kg导电剂sp,以2500rpm的转速搅拌2h,然后加入15kg人造石墨以2500rpm的转速搅拌2h;之后加入0.83kg添加剂ec,2500rpm的转速搅拌90min制得负极浆料,负极浆料的制备过程总时间约为8-12h;上述人造石墨、sp、la133n2、ec的质量比为90.44:1.24:3.33:5.00;制得的负极浆料的粘度为1900mpas,细度为30μm,固含量为55.17%;2)将步骤1)制得的负极浆料利用转移涂布机在厚度为9μm的铜箔集流体上涂布烘干,裁切加工即得。本实施例的锂离子电池负极片为上述方法制得的负极片。本实施例的锂离子电池的负极片为上述锂离子电池负极片,正极片为镍钴锰三元材料正极片,锂离子电池为按照现有技术中的方法制成的22ah的软包锂离子电池。实施例3本实施例的锂离子电池负极片的制备方法包括如下步骤:1)将196kg的去离子水与2.3kg稳定剂cmc均匀混合制得胶液;在650l的双行星搅拌机中加入3.2kg导电剂sp和300kg的ft-1石墨,以公转速度为15rpm、自转速度为900rpm的转速搅拌15min,然后加入上述胶液,以公转25rpm的速度捏合90min,之后加入41.8kg的la133溶液和9.7kg的添加剂ec,以自转速度为1500rpm的转速搅拌2h,再加入sbr溶液以公转速度为12rpm、自转速度为800rpm的转速搅拌30min,制得负极浆料;所述ft-1石墨、sp、la133、cmc、sbr、ec的质量比为92.80:1:2:0.70:0.50:3.00;2)将步骤1)制得的负极浆料利用挤压涂布机涂布到厚度为9μm的铜箔集流体上,95℃下烘干,裁切加工即得。本实施例的锂离子电池负极片为上述方法制得的负极片。本实施例的锂离子电池的负极片为上述锂离子电池负极片,正极片为镍钴锰三元材料正极片,锂离子电池为按照现有技术中的方法制成的22ah的软包锂离子电池。实施例4本实施例的锂离子电池负极片的制备方法包括如下步骤:1)将211.2kg的去离子水与3.5kg的稳定剂cmc均匀混合制得cmc溶液,然后加入21.9kg的la133溶液制成复合溶胶;在650l的双行星搅拌机中加入4kg导电剂sp和375kg的ft-1石墨,以公转速度为15rpm、自转速度为900rpm的转速搅拌15min,然后加入上述胶液213kg,以公转25rpm的速度捏合90min,之后加入la133溶液46kg、去离子水68kg和8.04kg的添加剂ec,以自转速度为1500rpm的转速搅拌2h;最后加入70kg去离子水和sbr溶液,以公转速度为12rpm、自转速度为800rpm的转速搅拌30min制得负极浆料;所述ft-1石墨、sp、la133、cmc、sbr、ec的质量比为93.20:1:2.50:0.80:0.50:2.00;2)将步骤1)制得的负极浆料利用挤压涂布机涂布到厚度为9μm的铜箔集流体上,95℃下烘干,裁切加工即得。本实施例的锂离子电池负极片为上述方法制得的负极片。本实施例的锂离子电池的负极片为上述锂离子电池负极片,正极片为镍钴锰三元材料正极片,锂离子电池为按照现有技术中的方法制成的22ah的软包锂离子电池。对比例1本实施例的锂离子电池负极片的制备方法包括如下步骤:1)将0.13kg的稳定剂cmc与水加入30l的双行星搅拌机中,以2500rpm的转速搅拌2h制得固含量为1.2%的胶液,然后加入3.15kg的la133n2溶液,以2500rpm的转速搅拌2h,然后加入sp,以2500rpm的转速搅拌2h,然后加入人造石墨15kg以2500rpm的转速搅拌2h制得负极浆料,负极浆料的制备过程总时间约为8-12h;上述人造石墨、sp、cmc、la133n2的质量比为95.20:1.00:0.80:3.00;制得的负极浆料的粘度为1800mpas,细度为40μm,固含量为43.64%;2)将步骤1)制得的负极浆料利用转移涂布机在厚度为9μm的铜箔集流体上涂布烘干,裁切加工即得。本对比例的锂离子电池负极片为上述方法制得的负极片。本对比例的锂离子电池的负极片为上述锂离子电池负极片,正极片为镍钴锰三元材料正极片,锂离子电池为按照现有技术中的方法制成的22ah的软包锂离子电池。对比例2本实施例的锂离子电池负极片的制备方法包括如下步骤:1)将284.3kgl的去离子水与3.2kg的cmc混合均匀制得固含量为1.11%的胶液,然后加入80kg的粘结剂la133溶液均匀混合制得复合胶液;在650l的双行星搅拌机中加入导电剂sp和350kg的ft-1石墨,以公转速度为15rpm、自转速度为900rpm的转速搅拌15min;加入上述复合胶液156kg,以公转25rpm的速度捏合90min,之后加入复合胶液181.79kg、去离子水和添加剂ec,以自转速度为1500rpm的转速搅拌2h,制得负极浆料;所述ft-1石墨、sp、la133、cmc的质量比为95.20:1.00:3.00:0.80;2)将步骤1)制得的负极浆料利用挤压涂布机涂布到厚度为9μm的铜箔集流体上,95℃下烘干,裁切加工即得。本对比例的锂离子电池负极片为上述方法制得的负极片。本对比例的锂离子电池的负极片为上述锂离子电池负极片,正极片为镍钴锰三元材料正极片,锂离子电池为按照现有技术中的方法制成的22ah的软包锂离子电池。试验例1)停机卷边时间测试利用对比例1及实施例1、2中的方法制备的浆料进行涂布,并对涂布时转移涂布机上烘干时的停机卷边情况进行观测,停机卷边情况分别如图1(a)、图1(b)、图1(c)所示。可以看出随着停机时间的延长,涂布极片边缘的卷曲情况越严重。对比例1及实施例1、2中制得的锂离子电池负极片的开裂情况分别如图2(a)、图2(b)、图2(c)所示。由图1可知,实施例1、2中添加了ec后,停机卷边现象有明显的缓解。由图2可知,实施例1、2中添加了ec后,负极片边缘的开裂现象消失。2)tga测试对对比例2及实施例3、4中制得的锂离子电池负极片进行tga测试,测试结果如表1所示。表1对比例2及实施例3、4中制得的锂离子电池负极片进行tga测试结果样品160℃失重(%)160℃-260℃失重(%)对比例20.2320.089实施例30.1900.057实施例40.2140.058由表1可知,与对比例2相比,实施例3和4中的负极片加热到260℃也没有更多的失重。所以,可以判断,极片经过烘干后,添加剂都挥发了出去。3)电化学性能测试将对比例2及实施例3、4中的锂离子电池进行化成、容量测试和老化静置后,充满电后在2c和3c的倍率下进行放电测试其倍率性能,其容量保持率如表2所示。表2对比例2及实施例3、4中的锂离子电池倍率性能2c容量保持率3c容量保持率对比例298.3%98.1%实施例398.1%97.8%实施例498.5%97.8%由表2可以看出,实施例3和实施例4中添加ec后,对电池的倍率性能影响不大。当前第1页12