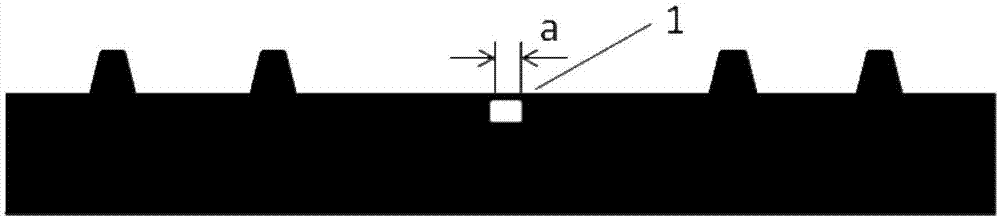
本发明涉及锂电池制作
技术领域:
,特别是一种杜绝锂电池卷芯隔膜黑点的方法。
背景技术:
锂电池的制作流程长,且工艺复杂,一般包含合浆、涂布、辊压分切、制片、卷绕、组装、激光焊、烘烤、注液、化成、分容等一系列工序。其中极片及隔膜在卷绕形成卷芯后,会采用高压短路测试仪或者高压内阻测试仪进行热压检测卷芯是否短路。由于锂电池所使用的材料均属于微米级,甚至纳米级,若制作过程控制不好,锂电池极片在卷绕断切的过程中极易掉粉,尤其是对于连续涂布的极片生产方式;掉落的粉尘由于静电作用,容易粘附在极片及隔膜表面,在短路检测时,短路测试仪产生的高电压击穿粉尘点,造成隔膜大面积高温碳化,产生黑点,引起锂电池卷芯内部短路,给后期电芯的使用带来较大的安全隐患。技术实现要素:本发明的目的在于提供一种杜绝锂电池卷芯隔膜黑点的方法,克服锂电池极片在卷绕断切过程中因掉粉现象,引起的高压短路检测中隔膜产生黑点问题。为实现上述目的,本发明采用了以下技术方案:一种杜绝锂电池卷芯隔膜黑点的方法,包括以下步骤:s1、在锂电池的制片过程中通过激光切割极片,形成用于标识极片断切位置的mark孔位;s2、在卷绕前,对mark孔位进行首次断切,然后将极片于断切位置处拉开距离b,并在拉开后的极片断切位置处,于极片双面对称贴保护胶带,使得断切后的极片继续连接为一体;s3、在卷绕时,对极片上的保护胶带位置进行二次断切,二次断切后的极片与隔膜卷绕形成卷芯,通过高压短路检测卷芯是否短路。优选的,所述mark孔的形状为椭圆形、矩形或者u形。优选的,所述s2中距离b满足:4mm≤b≤6mm。优选的,所述保护胶带的宽度c与mark孔位的纵向长度a及距离b满足以下关系:a+b<c≤(a+b+4)mm;所述保护胶带的长度e与极片的宽度d满足以下关系:d<e<隔膜宽度。优选的,所述高压短路的检测电压为300-500v,检测设备为高压短路测试仪或高压内阻测试仪。本发明具有的有益效果如下:本发明方法于卷绕前,对极片进行首次断切、拉开并贴胶,后在拉开的贴胶位置进行二次断切,二次断切时极片的断切位受保护胶带的防护,防止了断切部位掉粉被极片或隔膜吸附,保证了卷绕过程不会引入粉尘,从而杜绝了因掉粉导致短路测试产生隔膜黑点的问题,提升了锂电池的安全性能。附图说明图1是锂电池极片一次断切前的示意图;图2是锂电池极片一次断切后贴胶的示意图。图3是传统方法生产的卷芯隔膜上的黑点位置分布图。具体实施方式下面结合实施例对本发明做进一步说明:一种杜绝锂电池卷芯隔膜黑点的方法,包括以下步骤:首先,参照图1所示,在锂电池的制片过程中通过激光切割极片,形成用于标识极片断切位置的mark孔位1。本实施例中的mark孔位为矩形,实际也可以选择为椭圆形或u形。然后,参照图2所示,在卷绕前,对mark孔位1进行首次断切,然后将极片于断切位置处拉开距离b,并在拉开后的极片断切位置处,于极片双面对称贴保护胶带2,使得断切后的极片继续连接为一体。作为本实施例的优选实施方式,拉开的距离b满足:4mm≤b≤6mm。保护胶带2的宽度c与mark孔位1的纵向长度a及距离b满足以下关系:a+b<c≤(a+b+4)mm。保护胶带2的长度e与极片的宽度d满足以下关系:d<e<隔膜宽度。最后,在卷绕时,对极片上的保护胶带2位置进行二次断切,二次断切后的极片与隔膜卷绕形成卷芯,通过高压短路检测卷芯是否短路。通常的高压短路的检测电压为300-500v,检测设备可以采用高压短路测试仪或高压内阻测试仪。按照传统的锂电池极片无断切位拉开贴胶的模式进行连续生产,通过一段时间统计尺寸型号为18650的约20.4万只卷芯,对高压测短路后的653只短路卷芯拆解观察,按类型统计分析,得出隔膜黑点现象是导致电芯短路的主要问题。表1给出了对653只短路电芯的拆解数据统计分析。表1:统计短路总数隔膜黑点数隔膜黑点比例其它因素其它因素比例65351478.7%13921.3%进一步精准定位隔膜上黑点的位置分布后,确定黑点产生原因为极片断切掉料导致,具体如图3所示,给出了短路卷芯隔膜上黑点位置分布情况。而按照本发明方法进行锂电池连续生产,通过一段时间统计尺寸型号同样为18650的约51万只卷芯,对高压测短路后的392只短路卷芯拆解观察,按类型统计分析。表2给出了对392只短路电芯的拆解数据统计分析。表2:统计短路总数隔膜黑点数隔膜黑点比例其它因素其它因素比例39200%392100%通过表2和表1的对比,可以看出本发明方法有效的解决了因隔膜黑点导致的电芯短路问题,使得电芯制程合格率得到有效提升,同时提升了电芯使用安全性。以上所述的实施例仅仅是对本发明的优选实施方式进行描述,并非对本发明的范围进行限定,在不脱离本发明设计精神的前提下,本领域普通技术人员对本发明的技术方案作出的各种变形和改进,均应落入本发明权利要求书确定的保护范围内。当前第1页12