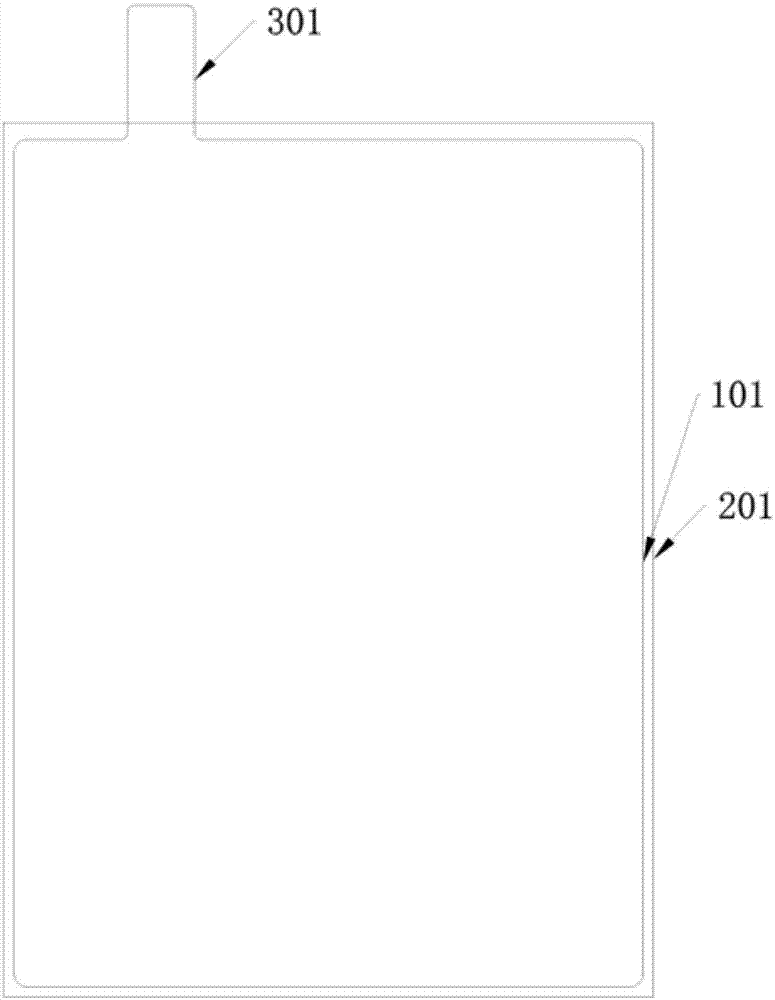
本发明涉及锂离子电池领域,特别设计一种适用于大容量电池的软包锂离子电池结构。
背景技术:
:随着环境保护的急迫需求,电动汽车的发展越来越得到人们的关注。大容量单体电池(50ah及以上)的应用越来越广。而电池越大,安全问题越突出,更需要重视和加强。技术实现要素:本发明实施例的目的之一在于提供一种软包锂离子电池,本技术方案应用于大容量电池,有利于提高电池的安全性。第一方面,本发明实施例提供的一种软包锂离子电池,包括:正对相互层叠的第一隔膜袋、第二隔膜袋,在各所述第一隔膜袋中分别封装有一正极片;在各所述第二隔膜袋中分别封装有一负极片;在任意相邻的正极片、负极片之间均间隔有两隔膜层。可选地,所述正极片的宽度窄于所述负极片的宽度。可选地,第一隔膜袋、第二隔膜袋的尺寸一致,层叠时各边缘均对齐。可选地,所述第一隔膜袋包括:所述第一隔膜层、第二隔膜层分别正对覆盖在所述正极片的顶面以及底面,仅所述正极片的极耳焊接从所述第一隔膜层、第二隔膜层的边缘伸出,其他部分覆盖在所述第一隔膜层、第二隔膜层之间;所述第一隔膜层、第二隔膜层、以及所述正极片分别面对面粘合在一起。可选地,在所述第一隔膜层与所述正极片之间,以及所述第二隔膜层与所述正极片之间还分别设置有一聚偏氟乙烯层,所述第一隔膜层、第二隔膜层、以及所述正极片分别通过各所述聚偏氟乙烯层粘合在一起。可选地,所述第二隔膜袋包括:所述第一隔膜层、第二隔膜层分别正对覆盖在所述负极片的顶面以及底面,仅所述负极片的极耳焊接从所述第一隔膜层、第二隔膜层的边缘伸出,其他部分覆盖在所述第一隔膜层、第二隔膜层之间;所述第一隔膜层、第二隔膜层、以及所述负极片分别面对面粘合在一起。可选地,在所述第一隔膜层与所述负极片之间,以及所述第二隔膜层与所述负极片之间还分别设置有一聚偏氟乙烯层,所述第一隔膜层、第二隔膜层、以及所述负极片分别通过各所述聚偏氟乙烯层粘合在一起。可选地,所述第一隔膜袋包括:第一隔膜层、第二隔膜层,所述第一隔膜层、第二隔膜层分别正对覆盖在所述正极片的顶面以及底面,仅所述正极片的极耳焊接从所述第一隔膜层、第二隔膜层的边缘伸出,其他部分均覆盖在所述第一隔膜层、第二隔膜层内;所述第一隔膜层、第二隔膜层超出所述正极片的边缘激光点焊连接在一起;可选地,所述第二隔膜袋包括:第一隔膜层、第二隔膜层,所述第一隔膜层、第二隔膜层分别正对覆盖在所述负极片的顶面以及底面,仅所述负极片的极耳焊接从所述第一隔膜层、第二隔膜层的边缘伸出,其他部分均覆盖在所述第一隔膜层、第二隔膜层内;所述第一隔膜层、第二隔膜层超出所述负极片的边缘激光点焊连接在一起。由上可见,采用本实施例技术方案,将每正极片、负极片分别置入第一隔膜袋、第二隔膜袋中,能有效避免极片移位导致的短路以及由于极片移位而导致正极片未能针对负极片,而导致正极片析锂而出现毛刺进而出现刺穿隔膜的不良现象。附图说明此处所说明的附图用来提供对本发明的进一步理解,构成本申请的一部分,并不构成对本发明的不当限定。图1为本发明实施例1提供的一种正极片与第一隔膜袋的装配透视结构示意图;图2为本发明实施例1提供的一种负极片与第二隔膜袋的装配透视结构示意图;图3为本发明实施例1提供的叠片体的装配透视结构示意图。附图标记:101:正极片;102:负极片;201:第一隔膜袋;202:第二隔膜袋;301、302:极耳焊接部。具体实施方式下面将结合附图以及具体实施例来详细说明本发明,在此本发明的示意性实施例以及说明用来解释本发明,但并不作为对本发明的限定。实施例1参见图1-3所示,本实施例提供了一种适用于大倍率放电应用需求的软包锂离子电池,该电池主要包括:相互正对层叠的第一隔膜袋201、第二隔膜袋202。参见图1所示,在各第一隔膜袋201中分别封装有一正极片101,仅正极片101的极耳焊接部301从第一隔膜袋201的边缘伸出,正极片101的其他部分均覆盖在第一隔膜袋201内,而无法伸出。参见图2所示,在各第二隔膜袋202中分别封装有一负极片102,仅负极片102的极耳焊接部302从第二隔膜袋202的边缘伸出,负极片102的其他部分均覆盖在第二隔膜袋202内,而无法伸出。其制备工艺如下:按照图1、2的图示工艺,分别对正极片101、负极片102分别置入第一隔膜袋201、第二隔膜袋202中,在制袋工序完成后,然后按照叠片工艺,将第一隔膜袋201、第二隔膜袋202顺次层叠(也可以但不限于按第二隔膜袋202、第一隔膜袋201的顺序)即可得到图3所示的叠片锂离子电池,此时,各正极片101、负极片102除各自的极耳焊接部301、302外,分别限位在第一隔膜袋201、第二隔膜袋202中,在任意相邻的两正极片101、负极片102之间均间隔有两层隔膜层。由上可见,采用本实施例技术方案,将每正极片101、负极片102分别置入第一隔膜袋201、第二隔膜袋202中,能有效避免极片移位导致的短路以及由于极片移位而导致正极片101未能针对负极片102而导致正极片101析锂而出现毛刺进而出现刺穿隔膜的不良现象。作为本实施例的示意,优选将第一隔膜袋201、第二隔膜袋202的长度宽度设计成一样,使其在叠片时形成的叠片体的各侧边缘完全对齐,进一步有利于确保正极片101、负极片102的正对,有利于进一步避免极片移位,有利于提高软包电池的一致性。作为本实施例的示意,可以将本实施例的正极片101的宽度以及长度设置成略窄于负极片102的宽度以及长度,使在将尺寸一致的第一隔膜袋201、第二隔膜袋202正对层叠时,位于第二隔膜袋202中的负极片102过盈对正第一隔膜袋201中的正极片101,采用本实施例优选方案能进一步确保正极片101的每处涂覆层均能正对负极片102上的涂覆层,进一步避免析锂现象。作为本实施例的示意,本实施例的正极片101的制袋工艺如下:将两尺寸相同的隔膜层(记为第一隔膜层、第二隔膜层)分别覆盖在正极片101的顶面、底面,使仅正极片101的极耳焊接部301从第一隔膜层、第二隔膜层的边缘伸出,其他部分覆盖在第一隔膜层、第二隔膜层之间;然后将第一隔膜层、第二隔膜层、以及正极片101分别面对面粘合在一起即得到正极片101不可移动的第一隔膜袋201。作为本实施例的示意,也可以采用上述工艺进行负极片102制袋:将两尺寸相同的隔膜层(记为第一隔膜层、第二隔膜层)分别覆盖在负极片102的顶面、底面,使仅负极片102的极耳焊接部302从第一隔膜层、第二隔膜层的边缘伸出,其他部分覆盖在第一隔膜层、第二隔膜层之间;然后将第一隔膜层、第二隔膜层、以及负极片102分别面对面粘合在一起即得到负极片102不可移动的第一隔膜袋201。作为本实施例的示意之一,本发明人提供了在各隔膜袋的各隔膜层的顶面以及底面分别涂覆聚偏氟乙烯材料(polyvinylidenefluoride,简称pvdf),使在各隔膜层相对正极片101的面形成有pvdf层,然后通过热压,使热压温度达到预定的温度,使在压力以及温度下,各隔膜层的pvdf层在受热下软化(软化温度为112~145℃)从而与其相邻的正极片101(或负极片102)相互粘结在一起实现两隔膜层与其中间的正极片101(或负极片102)粘合在一起。采用上述的粘合制袋技术方案,有利于避免极片的移位,确保电池的安全性。作为本实施例的示意,第一隔膜袋201、第二隔膜袋202还可以采用以下技术方案实现:将第一隔膜层、第二隔膜层分别正对覆盖在正极片101(或负极片102)的顶面以及底面,仅正极片101(或负极片102)的极耳焊接从第一隔膜层、第二隔膜层的边缘伸出,其他部分均覆盖在第一隔膜层、第二隔膜层内;第一隔膜层、第二隔膜层超出正极片101(或负极片102)的边缘激光点焊连接在一起,即得正极片101(或负极片102)制袋。其中激光焊接可以采用间隔点焊的方式实现也可以采用线性焊接的方式实现。采用激光点焊对第一隔膜层、第二隔膜层进行连接成袋的技术方案,由于激光点焊可以使其点焊连接点小且精确,有利于提高隔膜袋中的正极片101的体积,有利于提高电池的容量,且采用该技术方案能够大大提高生产效率,且实现了对隔膜袋中的正极片101的定位,避免正极片101移位而导致锂离子电池电性能不佳甚至短路、引发安全隐患的问题。试验对比分析以下以制备50ah的单体电动汽车用软包装锂离子电池为示意对本发明实施例结构进行试验比对分析:对照例1:采用以下工艺制成:制备正极片,其中正极集流体采用铝箔,铝箔的规格为:长176mm宽80mm,正极材料为:li(nicomn)o2,涂覆厚度为:60um±5um;制备负极片,其中负极集流体采用铜箔,铜箔的规格为:长179mm宽82mm,负极材料为:c,涂覆厚度为:60um±5um;正极片入袋,将正极片置入隔膜袋中,其中隔膜袋采用三层pp/pe/pp隔膜制成,隔膜袋的规格为:长179mm宽82mm;叠片工艺,将置入正极片的隔膜袋、负极片进行层叠,得到叠片体;将叠片体进行铝塑膜封装,进行电解液灌注,即得本对照例的50ah的单体电动汽车用软包装锂离子电池。其中各工序的工艺可以但不限于采用现有技术实现。实施例1:本实施例的采用以下工艺制成:正极片、负极片、以及采用的隔膜、以及各工序中的工艺均与对照例相同,所不同之处仅在于:本实施例在制得正极片、负极片后,分别将正极片负极片入袋,其中用于置入正极片、负极片的隔膜袋的尺寸均为:长179mm宽82mm;在正负极片分别入袋后,其叠片工序具体是将已分别置入正极片、负极片的隔膜袋进行层叠,得到叠片体。同理后需要将叠片体进行铝塑膜封装,进行电解液灌注,得本实施例50ah的单体电动汽车用软包装锂离子电池。实施例1:本实施例的正极片、负极片、以及采用的隔膜、以及各工序中的工艺均与对照例相同,所不同之处仅在于:本实施例在制得正极片、负极片后,分别将正极片负极片入袋,使各正极片、负极片分别位于其对应的隔膜袋的中央,其中用于置入正极片、负极片的隔膜袋的尺寸均为:长179mm宽82mm;在正负极片分别入袋后,其叠片工序具体是将已分别置入正极片、负极片的隔膜袋进行层叠,得到叠片体,使各隔膜袋的边沿对齐。同理后需要将叠片体进行铝塑膜封装,进行电解液灌注,得本实施例50ah的单体电动汽车用软包装锂离子电池。实施例2:本实施例与实施例1所不同之处仅在于:本实施例的正极集流体的规格与负极集流体的规格长度一致均为:长179mm宽82mm。其他工艺以及工艺参数与实施例1相同。分别取对照例、实施例1、实施例2的软包锂离子电池进行短路及低压测试,对测试结果取平均数,得到以下试验数据表:实验数据对照表项目短路率低压率对照例0.82%2.23%实施例10.26%0.47%实施例20.56%1.67%以上所述的实施方式,并不构成对该技术方案保护范围的限定。任何在上述实施方式的精神和原则之内所作的修改、等同替换和改进等,均应包含在该技术方案的保护范围之内。当前第1页12