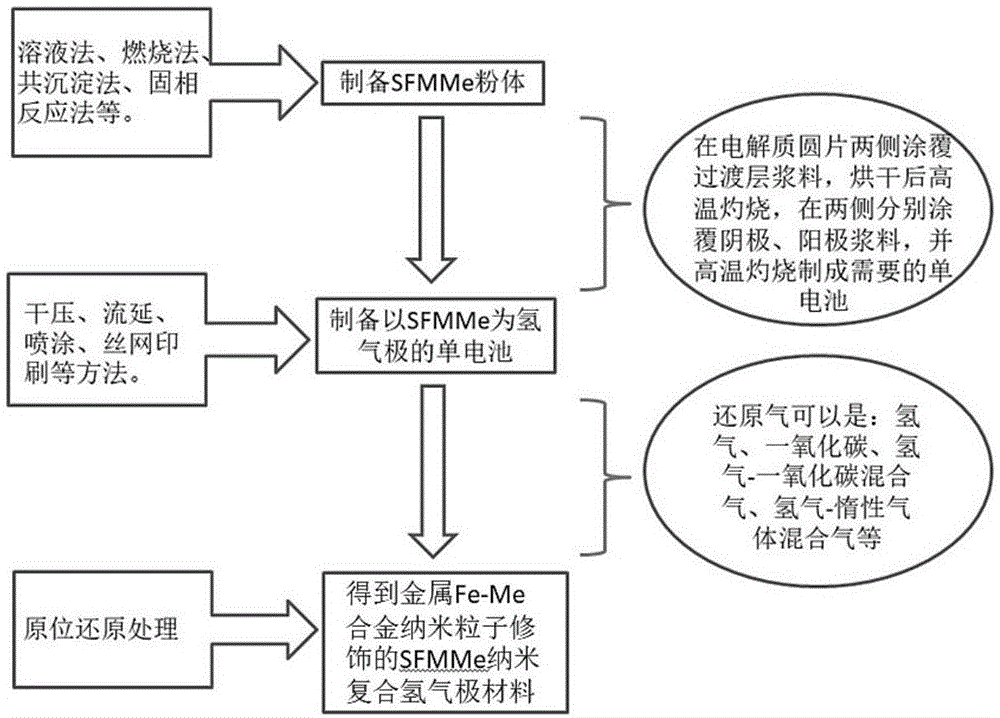
本发明涉及高温固体氧化物燃料电池及电解池领域,具体来说,涉及一种新型高温固体氧化物电池的氢气极材料及其制备方法。
背景技术:
目前人类活动所消耗的能源主要来自传统的化石能源——煤、石油和天然气等。面对巨大的能源需求和能源枯竭的矛盾,人们必须寻找可代替传统能源的更清洁的能源。氢能具有热值高、无污染、不产生温室气体、清洁、高效等优点,被公认为最有希望代替传统一次能源作为下一代的能源载体。目前,氢气的主要生产方式是天然气重整和电解水制氢。天然气重整制氢仍然要消耗一次能源(天然气),无法避免温室气体的产生,而电解水制氢过程是氢气与氧气燃烧生成水的逆过程,可利用其他形式能源产生的电能制取纯净氢气和氧气。在所有电解水制氢的形式中,固体氧化物电解池电解效率最高,有望实现环境友好且大规模低成本制氢的目标。
传统的纳米金属粒子修饰的纳米复合材料主要通过沉积的方法制备,如物理气相沉积法和化学溶液浸渍法,但是这些方法制备的材料难以控制纳米材料的颗粒尺寸、表面分布;同时支撑体骨架与纳米粒子的结合力较弱,制作过程繁复耗时,制作成本昂贵;再者,这种方法制备的纳米材料还容易引发催化活性衰减和碳沉积问题。因此,沉积方法制备的这类纳米复合材料在工作条件下易失活。新型原位还原技术制备的纳米催化剂材料不仅颗粒精细、分布均匀,还能有效避免繁琐的沉积过程,节约制备时间和成本;同时,将催化活性颗粒锚固在支撑体表面还可以延缓老化速度和抑制碳沉积现象;更为客观的是,由于原位还原技术制备的材料具有可逆性,即从支撑体骨架析出的纳米颗粒可以再次被氧化固溶到支撑体骨架中,从而可以避免因催化剂的颗粒长大而造成的电池的整体性能衰减,并有效地提高催化剂的使用寿命。
传统的金属-陶瓷复合电极催化活性高,但在高温高湿条件催化剂颗粒(如金属ni粒子)容易发生膨胀、被氧化等问题而使电池性能衰减。新型钙钛矿型基复合电极(如sr2fe1.5mo0.5o6-δ(sfm))具有极高的电化学性能和热稳定性,非常适合用作氢气极材料。然而与传统金属-陶瓷复合电极相比,金属氧化物基复合电极的电催化性能较低,为了进一步提高电极的电催化性能和电池的电化学性能,将金属元素(如ni)掺杂进入金属氧化物材料(如sfm)的晶格中形成sr2fe1.5-xmexmo0.5o6-δ(简写为sfmme,其中me为ni、co、cu、pt、ru等过渡金属元素),在工作条件下使材料晶格中的部分ni元素和fe元素还原出来并附着于基底材料的表面,形成纳米金属催化剂修饰的sfm材料(fe-ni@sfm)。
此类材料构建的复合氢气极用于高温电解水制氢时电化学性能经试验检测优异,可以为发展高效高稳定性的soec/sofc氢气极体系、推动高温电解水制氢技术的商业化应用提供实验和理论基础。
技术实现要素:
本发明所要解决的技术问题在于解决目前存在的金属-陶瓷基复合电极电化学性能优异而稳定性不足、金属氧化物基复合电极稳定性优异而电化学性能不足的特点,探索并发展原位还原法低成本制备纳米金属催化剂修饰的金属氧化物纳米复合材料用作固体氧化物电池氢气极。
本发明的技术方案可以通过以下技术措施来实现:
一种新型氢气极材料,分子式为sr2fe2-x-ymexmoyo6-δ(sfmme),其中所述me为过渡金属元素,x=0~2,y=0~2-x。
优选地,所述me为ni、co、cu、pt、rh、ru、au、ag中的任一种或多种。
上述氢气极材料用于固体氧化物燃料电池及电解池的氢气极。
优选地,所述氢气极材料sfmme用于氢气极的过程包括:
步骤(1),制备sfmme初始粉体;
步骤(2),将sfmme初始粉体与氧离子导体材料混合均匀,加入粘结剂,充分研磨,制得sfmme基复合浆料;
步骤(3),将sfmme基复合浆料涂覆于电解质片一侧,制备得到以sfmme基复合浆料为氢气极的单电池;
步骤(4),在单电池氢气极工作条件下利用氢气极侧的还原性气体使sfmme粉体b位的金属元素me和fe从晶格位原位析出,得到金属fe-me合金纳米粒子修饰的sfmme纳米复合氢气极材料fe-me@sfmme。
优选地,步骤(2)所述的氧离子导体材料包括稳定的氧化锆(sz)、镧掺杂的氧化铈(dco)、稳定的氧化铋(sb)、氧化锶和氧化镁共掺杂的镓酸镧(lsgm)。
优选地,步骤(3)中单电池所用的电解质材料包括:稳定的氧化锆(sz)、镧掺杂的氧化铈(dco)、稳定的氧化铋(sb)、氧化锶和氧化镁共掺杂的镓酸镧(lsgm)。
优选地,单电池所用的电解质为lsgm或sz,在氢气极和电解质中间引入镧掺杂的氧化铈(dco)阻止电解质和氢气极发生反应生成惰性相。
优选地,步骤(3)中单电池所用的空气极包括:氧化锶掺杂锰酸镧(la1-xsrxmno3-δ,lsm)、钙钛矿型ln1-xaxme1-ybyo3-δ、层状钙钛矿型氧化物aa’bb’o6,其中,ln,a,a’=la,sr、pr、ba、sm;me,b,b’=fe、co、ni、y、zr、ta。
优选地,步骤(4)所述的还原性气体包括氢气、一氧化碳、氢气-一氧化碳混合气、氢气-惰性气体混合气。
本发明还公开了一种固体氧化物燃料电池,采用上述的氢气极材料作为氢气极或者采用上述方法利用所述氢气极材料制备得到固体氧化物燃料电池。
本发明还公开了一种固体氧化物电解池,采用上述的氢气极材料作为氢气极或者采用上述方法利用所述氢气极材料制备得到固体氧化物电解池。
与现有技术相比,本发明采用现有方法(固相合成法、溶液法、共沉淀法、燃烧法等)制成sfmme初始粉体材料,该材料用于氢气极时,氢气极侧工作时的还原性气体将sfmme中的的铁元素(fe)和me元素还原为fe-me合金催化颗粒,形成fe-me@sfmme纳米复合氢气极材料。与传统的ni基氢气极材料相比,本发明原位还原后得到的纳米复合氢气极材料具备更加优异的长期稳定性;与新型陶瓷氧化物氢气极材料(如氧化镧掺杂钛酸锶(la1-xsrxtio3±δ,lst)、氧化钼掺杂铁酸锶(sr2fe2-xmoxo6-δ,sfm)等)相比,本发明中原位还原后得到的纳米复合氢气极材料具备了更加优异的电化学性能;并且本发明氢气极材料不需要建立特殊的条件还原金属纳米催化颗粒,fe-me合金的还原是在氢气极工作条件下实现的,因此与传统的纳米复合氢气极材料制备方法(如溶液浸渍法)相比,本发明具有更加优异的经济性。
附图说明
利用附图对本发明作进一步说明,但附图中的实施例不构成对本发明的任何限制。
图1是本发明氢气极材料的制备及使用流程示意图;
图2为x=0和x=0.2时sfmnix粉体在1050℃煅烧5h后的xrd图谱,其中(a)为2θ为20-80o时的xrd图谱,(b)为2θ为40-50o时的xrd图谱;
图3为sfmni0.2粉体在800℃湿润h2下还原前后的xrd图谱,其中b1为还原后,b0为还原前;
图4为本发明实施例所得pbc-sdc|ldc|lsgm|ldc|sfmnix-sdc单电池在97%h2(g)-3%h2o(g)、1.3v电压下的阻抗谱,其中(a)为700℃测试条件下的阻抗谱,(b)为不同温度下电极界面极化电阻随ni掺杂量关系图。
具体实施方式
为使本发明更加容易理解,下面将进一步阐述本发明的具体实施例。
图1为本发明氢气极材料的制备及使用流程示意图,本发明实施例采用ni作为掺杂材料来进行说明,所使用的材料的制备方法如下:
1,sfmnix(sr2fe1.5-xnixmo0.5o6-δ)
按化学计量比依次称取(nh4)6mo7o24·4h2o、柠檬酸、sr(no3)2、fe(no3)3·9h2o、ni(no3)2·6h2o、甘氨酸,溶于400-500ml的除盐水中,溶解顺序与称量顺序一致,60-80℃混合2h使溶液充分络合。随后将溶液置于蒸发皿中加热使之先后成为溶胶、凝胶、干凝胶,直到发生自燃烧反应生成sfmni初始粉体。收集初始粉体并置于中温箱式炉中,煅烧获得立方钙钛矿结构的sfmni粉体。
2,sdc(sm0.2ce0.8o1.9)
将sm2o3和ce(no3)3按化学计量比称量后加入除盐水中溶解,再加入柠檬酸和硝酸溶液,得到无色溶液,其中sdc:柠檬酸的摩尔比为1:1.5,柠檬酸质量:硝酸体积比例为1:1;接着加入氨水调节ph值,在向无色溶液中缓慢加入氨水的过程中溶液中首先出现乳黄色沉淀,继续加氨水黄色沉淀会溶解,此时溶液的ph值约为7。将溶液加热并磁力搅拌,使之充分络合2h后,将其置于蒸发皿中,在300-400℃发生自燃烧反应生成sdc初始粉体。收集该初始粉体并在1000℃灼烧5h获得萤石结构的sdc粉体。
3,sfmnix-sdc复合电极浆料
按质量比1:1称量sfmnix和sdc粉体,将粉体转移到研钵中,加入无水乙醇充分研磨使之混合均匀;将上述粉体烘干,再加入粉体质量1.5倍的松油醇,充分研磨直至获得均匀胶状sfmnix-sdc复合电极浆料。
4,lsgm电解质圆片
称量lsgm、pvb粉体(质量比为1:0.05)并转移到研钵中,加入无水乙醇研磨直至混合均匀。将该粉体置于圆形磨具中,压成直径约为13mm、厚度约为0.7mm、质量约为0.3g的圆片。将圆片置于高温箱式炉中并于1400℃保温5h烧结成致密电解质片。
5,ldc过渡层浆料
按质量比1:1.5称取ldc粉体和松油醇,用球磨机充分研磨得到混合均匀的ldc过渡层浆料。
6,pbc(prbaco2o5+δ)
按化学计量比配制溶液,加氨水调节ph值至7左右,加热并磁力搅拌完成络合反应后再加热直到发生自燃烧,得到pbc初始粉体,高温煅烧获得双钙钛矿型pbc粉体。
7,pbc-sdc复合阳极浆料
按化学计量称量一定量的pbc和sdc(mpbc:msdc=1:1),与无水乙醇一起研磨直至混合均匀,再加入一定量的松油醇,其中pbc、sdc粉体和松油醇的质量比为1:1.5,充分研磨获得胶状pbc-sdc复合阳极浆料。
8,制备电解质支撑型soec单电池
在lsgm电解质圆片两侧涂覆ldc过渡层浆料,烘干后高温灼烧,然后在两侧分别涂覆pbc-sdc和sfmnix-sdc浆料,并高温灼烧制成需要的pbc-sdc|ldc|lsgm|ldc|sfmnix-sdc单电池,再在单电池两侧涂覆金浆用于集电。
实施例1
(1)制备单电池所需:sfm(sr2fe1.5mo0.5o6-δ,即sfmnix制备方法中,ni(no3)2·6h2o的化学计量比为0)、sfm-sdc、pbc-sdc、ldc、lsgm材料。
(2)称取0.7gsfm-sdc复合粉体用条状磨具压制成方形条状样品,将方形条状样品置于高温箱式炉中1300℃保温5h得到结构致密的sfm-sdc样品。
(3)采用直流四端子法测试步骤(2)所得sfm-sdc样品的电导率(σ)和表面氧交换系数(kchem)。
(4)利用阿伦尼乌斯(arrhenius)公式计算样品的活化能ea。其中σ—样品电导率,scm-1;l—样品两电压引线之间的距离,cm;r—样品电阻,ω;s—样品横截面积,cm2;t—样品测试温度,k;ea—活化能,ev;kb—波尔滋蔓常数,8.6173×10-5evk-1。
(5)制备pbc-sdc|ldc|lsgm|ldc|sfm-sdc单电池,根据其在97%h2-3%h2o、1.3v电压条件下阻抗谱得到电解池的极化电阻rp。
实验评价
测得10%h2-90%n2还原后的sfm-sdc在800℃时电导率(σ)为10.82s/cm,表面氧交换系数(kchem)为2.55×10-5cms-1,550-800℃时活化能为0.331ev。测得800℃条件下单电池极化电阻为0.210ωcm-2。
实施例2
(1)制备单电池所需:sfmni0.1(sr2fe1.4ni0.1mo0.5o6-δ)、sfmni0.1-sdc、pbc-sdc、ldc、lsgm材料。
(2)称取0.7gsfmni0.1-sdc用条状磨具压制成方形条状样品。将方形条状样品置于高温箱式炉中1300℃保温5h得到结构致密的sfmnix-gdc样品。
(3)采用直流四端子法测试步骤(2)中条形样品的电导率(σ)和表面氧交换系数(kchem)。
(4)利用阿伦尼乌斯(arrhenius)公式计算样品的活化能ea。
(5)制备sm0.2ce0.8o1.9(sdc)材料、sfm-sdc复合阴极浆料、prbaco2o5+δ(pbc)、pbc-sdc复合阳极浆料、lsgm电解质圆片、ldc过渡层浆料,制备pbc-sdc|ldc|lsgm|ldc|sfmni0.1-sdc单电池,测定电解池的极化电阻rp。
实验评价
测得10%h2-90%n2还原后的sfmni0.1-sdc在800℃时电导率(σ)为13.67s/cm,表面氧交换系数(kchem)为8.18×10-5cms-1,550-800℃时活化能为0.168ev。测得800℃条件下单电池极化电阻为0.185ωcm-2。
与实施例1相比,电导率、表面氧交换系数得到了提高,550-800℃时活化能、800℃时单电池极化电阻得到了降低。
实施例3
(1)制备单电池所需:sfmni0.2(sr2fe1.3ni0.2mo0.5o6-δ)、sfmni0.2-sdc、pbc-sdc、ldc、lsgm材料。
(2)按质量比1:1称取一定量的sfm和gdc粉体置于研钵中,加入无水乙醇研磨,得到充分混合的复合粉体,烘干后再加入该粉体质量5%的pvb(胶结剂),加无水乙醇研磨再次得到复合粉体。称取0.7g上述粉体用条状磨具压制成50粉体用条状磨具压方形条状样品。方形条状样品至于高温箱式炉中1300℃保温5h得到结构致密的sfmnix-gdc样品。
(3)采用直流四端子法测试步骤(2)中条形样品的电导率(σ)和表面氧交换系数(kchem)。
(4)利用阿伦尼乌斯(arrhenius)公式计算样品的活化能ea。
(5)制备sm0.2ce0.8o1.9(sdc)材料、sfm-sdc复合阴极浆料、prbaco2o5+δ(pbc)、pbc-sdc复合阳极浆料、lsgm电解质圆片、ldc过渡层浆料,制备pbc-sdc|ldc|lsgm|ldc|sfmni0.3-sdc单电池,测定电解池的极化电阻rp。
实验评价
测得10%h2-90%n2还原后的sfmni0.2-sdc在800℃时电导率(σ)为12.51s/cm,表面氧交换系数(kchem)为1.68×10-4cms-1,550-800℃时活化能为0.127ev。测得800℃条件下单电池极化电阻为0.109ωcm-2。
图2为x=0~0.3时sfmnix粉体在1050℃煅烧5h后的xrd图谱,其中(a)为2θ为20-80o时的xrd图谱,(b)为2θ为40-50o时的xrd图谱,从图2(a)中可以看出,经过1050℃煅烧,ni掺杂的sfmnix粉体呈现单一、稳定的钙钛矿型结构,与未掺杂的纯sfm粉体的晶型结构一致,表明ni掺杂并未改变sfm基材料的晶型结构。从图2(b)可以看出,随着ni掺杂量由0增加至0.3,衍射峰由46.4o向高角度偏移至46.5o。根据布拉格方程:2dsinθ=nλ,(其中,d为晶格间距;θ为衍射角度;n为第反射级数;λ为x射线波长,测试采用cu靶的kα波长为0.154178nm),可知衍射角越大对应晶胞尺寸d越小,因此,ni掺杂使得晶格收缩,且随着掺杂量的增加晶格收缩的程度越高。并可以得出ni2+半径为0.072nm,略小于fe2+的0.076nm。
图3为sfmni0.2粉体在800℃湿润h2下还原前后的xrd图谱,其中b1为还原后,b0为还原前,还原反应时间为2小时,h2流量为50ml/min。图中可以看出ni(x=0.2)掺杂后的sr2fe1.3ni0.2mo0.5o6-δ粉体呈现单一的钙钛矿结构,表明ni离子已经成功掺入sfm的晶格中。经过高温还原之后,原有sfm衍射花样的主要特征峰仍然存在,表明sfmni在还原性气氛下仍可维持稳定的钙钛矿结构。在43o、51o处观测到了ni-fe合金(pdf#47-1417)的特征衍射峰,表明采用原位还原法可以制备fe-ni修饰的钙钛矿sfm基材料。
实施例4
(1)制备单电池所需:sfmni0.3(sr2fe1.2ni0.3mo0.5o6-δ)、sfmni0.3-sdc、pbc-sdc、ldc、lsgm材料.
(2)按质量比1:1称取一定量的sfm和gdc粉体置于研钵中,加入无水乙醇研磨,得到充分混合的复合粉体,烘干后再加入该粉体质量5%的pvb(胶结剂),加无水乙醇研磨再次得到复合粉体。称取0.7g上述粉体用条状磨具压制成50粉体用条状磨具压方形条状样品。方形条状样品至于高温箱式炉中1300℃保温5h得到结构致密的sfmnix-gdc样品。
(3)采用直流四端子法测试步骤(2)中条形样品的电导率(σ)和表面氧交换系数(kchem)。
(4)利用阿伦尼乌斯(arrhenius)公式计算样品的活化能ea。
制备sm0.2ce0.8o1.9(sdc)材料、sfm-sdc复合阴极浆料、prbaco2o5+δ(pbc)、pbc-sdc复合阳极浆料、lsgm电解质圆片、ldc过渡层浆料,制备pbc-sdc|ldc|lsgm|ldc|sfmni0.4-sdc单电池,测定电解池的极化电阻rp。
实验评价
测得10%h2-90%n2还原后的sfmni0.3-sdc在800℃时电导率(σ)为15.06s/cm,表面氧交换系数(kchem)为5.87×10-5cms-1,550-800℃时活化能为0.150ev。
测得800℃条件下单电池极化电阻为0.118ωcm-2。
从上述实验评价可以看到,ni掺杂后,sr2fe1.5-xnixmo0.5o6-δ(sfmni0.2)的表面氧交换系数最大,550-800℃时活化能最低,ni掺杂后可以显著降低阴极的极化电阻rp,且当掺杂量x=0.2时rp最低。虽然电导率(σ)并不是最佳,但就材料的综合性能来看,当ni掺杂量为0.2时材料性能最佳。
图4为本发明实施例所得pbc-sdc|ldc|lsgm|ldc|sfmnix-sdc单电池在97%h2(g)-3%h2o(g)、1.3v电压下的阻抗谱,其中(a)为700℃测试条件下的阻抗谱,(b)为不同温度下电极界面极化电阻随ni掺杂量关系图。图中可以看出,ni掺杂显著降低电极的极化电阻rp,经过原位还原的sfmnix可以有效地提高电解池的电化学性能。
采用ni以外的co、fe、cu等几种金属也可以得到与ni掺杂的相似的效果。
最后所应当说明的是,以上实施例仅用以说明本发明的技术方案而非对本发明保护范围的限制,尽管参照较佳实施例对本发明作了详细说明,本领域的普通技术人员应当理解,可以对本发明的技术方案进行修改或者等同替换,而不脱离本发明技术方案的实质和范围。