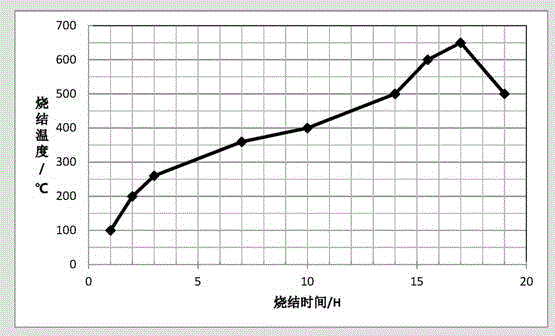
本发明涉及电机用电刷,特别是涉及一种节能型直流低压吸尘器电机用电刷及其制备方法,属于电机领域,并广泛使用在直流吸尘器、厨房电器用电机上。技术背景电刷是用于电机中与换向器或滑环接触而形成电连接的一种导电部件,作为导入导出电流的滑动接触体,其导电、导热及润滑性能良好,有一定的机械强度,具有抑制换向火花的本能。现代工业发展推动电机的种类和使用的工况条件越来越多样化,需要有各种不同类型的电刷来满足各类电机的要求,电刷的种类随着电机工业的发展越来越丰富。常规家用吸尘器电机一般连接市电,属于交流电机,其使用安全,吸力大,无需经常维护,且输出稳定。但随着社会的进步,机器的发明朝着解放双手的方向进行,设备无绳化趋势明显。低压直流吸尘器的发展是社会的需求,随着生活水平的提高以及锂电池的突破发展,低压直流吸尘器会遍布每个家庭。电机对电刷的要求有:1、在换向器或集电环表面,能形成适宜的由氧化亚铜、石墨和水分等组成的表面薄膜;2、电刷的使用寿命长,同时对换向器或集电环的磨损小;3、电刷导电性能好,过载能力强;4、电刷的电功率损耗和机械损耗小;5、电刷不出现对电机有危害的火花;6、电刷运行的噪声小。直流低压吸尘器因应用环境的需要,要求其电刷具备抑制火花能力好、寿命长、工作效率高等优点。然而,目前一般国产电刷运行效率较低、稳定性差、寿命短,国内电刷厂无法满足该类电机的需求。技术实现要素:本发明的首要目的是针对上述现有技术存在的问题提供一种节能型直流低压吸尘器电机用电刷,本发明的直流低压吸尘器电机用电刷材料电阻率低、换向性能好、耐磨性能好、火花等级低,更重要的是具有效率高、噪音低、产品稳定性好等特点。为实现本发明的目的,本发明提供了一种电机用电刷材料,包括炭素基体粉料,金属粉末与减摩材料,其中,所述金属粉末与所述减摩材料的重量份配比为:金属粉末10-40、所述减摩材料1-5。其中,所述炭素基体粉料与金属粉末、减摩材料的重量份配比为:炭素基体粉料40-95、金属粉末10-40、减磨材料1-5。特别是,所述炭素基体粉料、金属粉末和减磨材料的重量份配比为:炭素基体粉料60-95、金属粉末20-40、减磨材料2-4。尤其是,所述炭素基体粉料、金属粉末和减磨材料的重量份配比为:炭素基体粉料80-82、金属粉末28-32、减磨材料4。特别是,所述炭素基体粉料、金属粉末和减磨材料的重量份之比为(40-95):(10-40):(1-5),优选为(60-95):(20-40):(2-4),进一步优选为(80-82):(28-32):4。其中,炭素基体粉料包括原料天然石墨、合成石墨、沥青;所述金属粉末选自铜粉、银粉或锡粉中的一种或多种;所述减摩材料选择二硫化钼或/和二硫化钨。特别是,所述炭素基体粉料中原料的重量份配比为:天然石墨25-45,合成石墨10-25,沥青5-25。尤其是,所述天然石墨、合成石墨、沥青的重量份配比优选为:天然石墨35-45,合成石墨15-25,沥青10-25。特别是,所述炭素基体粉料中原料的重量份配比进一步优选为:天然石墨40-45,合成石墨15-20,沥青20-22。所述天然石墨选用t399.9,其鳞片结晶完整,片薄且韧性好,物理化学性能优异,具有良好的耐温性、自润滑性、传导性、抗热震性、耐腐蚀性等性能;所述人造石墨具有耐磨性能优良,能抑制电刷火花和提高电刷换向性能,其粒度为≤325目,含碳量≥99.9%,固定碳含量≥80%,水分≤0.5%,灰份≤0.5%;所述沥青选用软化点为95-110℃的煤沥青,结焦值≈55%,甲苯不溶物含量≈25%,灰分<0.5%。其中,所述金属粉末为铜粉和银粉的混合物。特别是,所述铜粉与银粉的重量比为3-6:1,优选为4-5:1,进一步优选为5:1。尤其是,所述铜粉选用树枝状电解铜粉,纯度≥99.9%,松装比重为0.8-1.0g/cm3,粒度为-325目;所述银粉选用片状银粉,纯度99.9%,粉末粒度≤80nm;所述锡粉选用雾化球形锡粉,锡含量≥99.95%,颗粒度≤20μm。铜粉与银粉均具有良好的抗熔焊特性,且两种材料导电性、耐磨性优异,采用银粉与铜粉配合使用,是因为银更加低而稳定的接触电阻以及更加优良的温升特性。本发明中铜粉与银粉特定配比使用,既保证了本发明的电刷具有合适的电阻率、较低的摩擦系数,又使得本发明的电刷耐磨损特性优异。其中,所述减摩材料为二硫化钼和二硫化钨的混合物.特别是,所述二硫化钼和二硫化钨的重量比为3-5:1,优选为3:1。尤其是,所述减摩材料的二硫化钼、二硫化钨的粒度为3000-4000目,纯度为99%,其具有优良的润滑性能,摩擦系数低。二硫化钼是一种蓝银灰色粉末,具有很好的润滑性,摩擦系数低,耐磨性能好,二硫化钨是一种银灰色粉末,亦具有很有的润滑性,摩擦系数低,耐磨性能好,两种材料用于电刷中均可以提高电刷材料的耐磨性能。二硫化钼的抗氧化性较二硫化钨差,因此二硫化钨比二硫化钼化学性质更稳定,且二硫化钼属于天然形成的,二硫化钨属于人工合成的,二硫化钼摩擦系数稍低于二硫化钨,电阻率较二硫化钨高,二硫化钼和二硫化钨的配合使用能发挥两种成分更优良的效果,既考虑了电刷优良的导电性,又保证了低的摩擦系数,同时热稳定性更高。本发明中二硫化钼与二硫化钨特定配比配合使用时,电刷的摩擦系数低,更重要的是电刷的热稳定性高、且在电机换向器表面成膜性能更好,电刷运行火花更好、电刷磨损率更低。特别是,所述电刷材料还包括添加剂,其中所述添加剂的重量份配比为1-5,优选为2-5,进一步优选为3-4,更进一步优选为4。其中,所述添加剂为六方氮化硼和十八酸锌或氮化硼和十八酸钙的混合物,优选为氮化硼和和十八酸钙。特别是,所述添加剂中六方氮化硼和十八酸锌或氮化硼和十八酸钙的重量份配比为(1-5):1,优选为5:1。尤其是,所述六方氮化硼为一种白色松散状、质地柔软有光滑感的粉末,其纯度≥99%,粒度≤30μm,具有耐高温、耐腐蚀、高导热、润滑性能优良的特性;所述十八酸锌、十八酸钙作为润滑剂和脱模剂。十八酸锌为白色轻质细微粉末,有滑腻感,微具刺激性气味;密度为1.095g/cm3,熔点为118-125℃,在电刷材料中起到润滑剂和脱模剂的作用,增加电刷材料的稳定性、润滑性,以及机械加工性能。十八酸钙为白色粉末,密度为1.08g/cm3,熔点为145-160℃,,在电刷材料中起到润滑剂和脱模剂的作用,增加电刷材料的稳定性、润滑性,以及机械加工性能。其中,所述炭素基体粉料按照如下步骤制成:a)按照如下配比备料天然石墨25-45合成石墨10-25沥青5-25b)将原料天然石墨、合成石墨进行混合处理,制成石墨预混料;c)加热石墨预混料至温度升高至140±10℃时加入沥青,继续加热、混捏处理,直至温度升高至220±10℃;然后停止加热,边混捏处理边降温至温度≤100℃;d)卸出物料,待物料自然晾凉,即制得电刷炭素混合物;e)将电刷炭素混合物依次进行破碎处理、筛分处理,即得炭素基体粉料。特别是,步骤a)中所述天然石墨、合成石墨、煤沥青的重量份配比优选为:天然石墨35-45,合成石墨15-25,煤沥青10-25。尤其是,所述炭素基体粉料中原料的重量份配比进一步优选为:天然石墨40-45,合成石墨15-20,煤沥青20-22。其中,步骤b)中混合处理时间为1-1.5h;所述混合处理为采用将天然石墨和合成石墨置于混捏锅内进行混捏处理。特别是,步骤e)中所述筛分处理为破碎处理后的物料过120目筛,制得炭素基体粉料,其中所述炭素基体粉料的粒度≤120目。其中,在所述压制处理过程中控制电刷粗坯的体积密度为2.55-2.75g/cm3。压制是将电刷材料粉末通过一定的成型方式,采用相应的成型设备压成具有规定形状、尺寸和理化性能的生坯的工艺过程。成型工艺要达到两个目的:一是使制品具有一定的形状和规格;二是使制品密实,具有一定密度、强度。本发明控制电刷粗坯的体积密度在该款材料可控体积密度的上限,以期生坯材料的孔隙度尽量小而均匀,经焙烧后煤沥青焦化形成网状骨架碳结构,穿插包覆并粘结石墨等材料,使电刷材料致密,从而形成电刷的强度,本发明电刷制备过程中控制粗坯的体积密度是保证电刷制品的物理机械性能的充分条件,而保证电刷制品的物理机械性能,是其应用于特定工况类电机的首要条件。特别是,所述烧结处理包括2个处理阶段,首先对电刷粗坯升温烧结处理;然后再进行降温烧结处理。其中,所述升温烧结处理阶段的升温速率为10-120℃/h,优选为13.3-100℃/h;升温烧结时间为15-24h,优选为17h。特别是,所述电刷粗坯的升温烧结处理包括如下步骤:1)将电刷粗坯置于惰性气氛烧结炉内,以60-80℃/h(优选为75℃/h)的升温速率从室温(通常为15-35℃)升温至100℃;升温时间为0.9-1.3h(优选为1h);2)在温度升高至100℃后,以90-120℃/h(优选为100℃/h)的升温速率从100℃升温至200℃;升温时间为0.8-1.2h(优选为1h);3)在温度升高至200℃后,以50-80℃/h(优选为60℃/h)的升温速率从200℃升温至260℃;升温时间为0.7-1.2h(优选为1h);4)在温度升高至260℃后,以20-40℃/h(优选为25℃/h)的升温速率从260℃升温至360℃;升温时间为2.5-5h(优选为4h);5)在温度升高至360℃后,以10-30℃/h(优选为13.3℃/h)的升温速率从360℃升温至400℃;升温时间为1.5-4h(优选为3h);6)在温度升高至400℃后,以20-40℃/h(优选为25℃/h)的升温速率从400℃升温至500℃;升温时间为2.5-5h(优选为4h);7)在温度升高至500℃后,以50-80℃/h(优选为66.7℃/h)的升温速率从500℃升温至600℃;升温时间为1.2-2h(优选为1.5h);8)在温度升高至600℃后,以20-50℃/h(优选为33.3℃/h)的升温速率从600℃升温至650℃;升温时间为1-2.5h(优选为1.5h)。尤其是,升温烧结处理阶段步骤1)中所述室温温度为15-35℃;所述升温速率优选为75℃/h;升温时间优选为1h;步骤2)中所述升温速率优选为100℃/h;升温时间优选为1h;步骤3)中所述升温速率优选为60℃/h;升温时间优选为1h;步骤4)中所述升温速率优选为25℃/h;升温时间优选为4h;步骤5)中所述升温速率优选为13.3℃/h;升温时间优选为3h;步骤6)中所述升温速率优选为25℃/h;升温时间优选为4h;步骤7)中所述升温速率优选为66.7℃/h;升温时间优选为1.5h;步骤8)中所述升温速率优选为33.3℃/h;升温时间优选为1.5h。特别是,所述电刷粗坯的降温烧结处理包括如下步骤:1)在升温烧结处理的温度升高至650℃后,以50-100℃/h(优选为75℃/h)的降温速率从650℃降温至500℃;降温时间为1.5-3h(优选为2h);2)在温度降低至500℃后,进行自然冷却,直至温度降低至200℃以下,获得电刷熟坯。尤其是,降温烧结处理阶段,步骤1)中所述降温速率优选为75℃/h;降温时间优选为2h。特别是,所述的机械加工包括对电刷熟坯进行切割、磨床、钻孔、填线、点焊等加工。本发明的直流低压吸尘器电机用电刷具有以下优点:1、发明电刷材料组成合理,配方科学,制作的电刷耐磨性能优、噪音低、使用寿命长、且配方环保、且强度好,耐磨、耐压、稳定、润滑性好,易脱模,环境适应性高,机械加工性能好,导电性能、导热性能良好,并且具有良好的物理、力学、化学性能。2、本发明的电机用电刷材料中使用二硫化钼,电刷摩擦系数低,电机换向性能好,稳定性高,抗干扰强。3、本发明的直流低压吸尘器电机用电刷材料中使用天然石墨和合成石墨搭配,电刷运行过程中火花等级低,电机换向性能好,电刷的使用寿命长。4、本发明的直流低压吸尘器电机用电刷材料中使用铜粉和银粉,电刷具有更好的导电性和更低的温升,进而提高了电刷的耐磨性。5、本发明的直流低压吸尘器电机用电刷的制备方法简单,制备工艺科学,产品质量稳定。6、本发明的直流低压吸尘器电机用电刷材料适用于低压直流(dc0-50v)吸尘器电机电刷使用,亦可适用于直流厨房电器类电机。附图说明图1为本发明实施例1碳刷材料烧结曲线图。具体实施方式下面结合具体实施例来进一步描述本发明,本发明的优点和特点将会随着描述而更为清楚。但这些实施例仅是范例性的,并不对本发明的范围构成任何限制。本领域技术人员应该理解的是,在不偏离本发明的精神和范围下可以对本发明技术方案的细节和形式进行修改或替换,但这些修改和替换均落入本发明的保护范围内。实施例11)按照如下重量配比备料(份):其中,所述天然石墨选用t399.9;所述合成石墨粒度为≤325目,含碳量≥99.9%,固定碳含量≥80%,水分≤0.5%,灰份≤0.5%;所述沥青选用软化点为95-110℃的煤沥青,结焦值≈55%,甲苯不溶物含量≈25%,灰分<0.5%;所述金属粉末选用铜粉与银粉的混合物,其中铜粉与银粉的重量之比为5:1;其中所述铜粉选用树枝状电解铜粉,纯度≥99.9%,松装比重为0.8-1.0g/cm3,粒度为≤325目;所述银粉选用片状银粉,纯度99.9%,粉末粒度≤80nm;所述减磨材料选择二硫化钼和二硫化钨的混合物,其中二硫化钼和二硫化钨的重量之比为3:1;其中二硫化钼、二硫化钨的粒度为3000-4000目,纯度为99%;所述添加剂包括六方氮化硼和十八酸钙,其中六方氮化硼和十八酸钙的质量配比为5:1;2)将原料天然石墨、合成石墨置于混捏锅内,开启混捏锅,启动正转模式,室温条件下干粉混合1.5h(通常>1h,优选为1-1.5h),制得石墨预混料;3)将石墨预混料于混捏锅内边混捏边加热,直至温度升高至140±10℃时加入沥青,继续加热,以40℃/h(通常为30-50℃/h均适用于本发明)的升温速率升温220±10℃,升温时间为2h(通常为1.6-2.7h);然后停止加热,边混捏边自然降温至温度≤100℃;4)从混捏锅内卸出物料,待物料彻底自然晾凉,即制得电刷炭素混合物;5)将电刷炭素混合物进行破碎、筛分处理,破碎物料过120目筛,制得电刷材料炭素基体粉,电刷材料炭素基体粉粒度≤120目;6)将制备的电刷材料炭素基体粉,金属粉末、减磨材料、添加剂加入冷混锅内,于室温(25℃,通常为15-35℃)、相对湿度≤60%的条件下进行混合处理(3±0.5)h,得到电刷材料粉末,注意粉末存放时的防潮、防尘、防高温处理;7)将电刷材料粉末置于模具中,采用液压机进行压制处理即制得电机用电刷粗坯,其中电刷粗坯的体积密度达到2.65g/cm3(通常为2.55-2.75g/cm3);8)将电刷粗坯置于惰性气氛烧结炉中,按照图1所示的烧结曲线,制得烧结处理后的电刷熟坯;具体如下:8-1)烧结升温阶段(室温至650℃)第一升温阶段:(室温至100℃)将电刷粗坯置于惰性气氛烧结炉内,以75℃/h(通常为60-80℃/h均适用于本发明)的升温速率从室温(25℃,通常为15-35℃)升温至100℃;升温时间为1h(通常为0.9-1.3h);第二升温阶段:(100℃至20℃)在温度升高至100℃后,以100℃/h(通常为90-120℃/h均适用于本发明)的升温速率从100℃升温至200℃;升温时间为1h(通常为0.8-1.2h);第三升温阶段:(200℃至260℃)在温度升高至200℃后,以60℃/h(通常为50-80℃/h均适用于本发明)的升温速率从200℃升温至260℃;升温时间为1h(通常为0.7-1.2h);第四升温阶段:(260℃至360℃)在温度升高至260℃后,以25℃/h(通常为20-40℃/h均适用于本发明)的升温速率从260℃升温至360℃;升温时间为4h(通常为2.5-5h);第五升温阶段:(360℃至400℃)在温度升高至360℃后,以13.3℃/h(通常为10-30℃/h均适用于本发明)的升温速率从360℃升温至400℃;升温时间为3h(通常为1.5-4h);第六升温阶段:(400℃至500℃)在温度升高至400℃后,以25℃/h(通常为20-40℃/h均适用于本发明)的升温速率从400℃升温至500℃;升温时间为4h(通常为2.5-5h);第七升温阶段:(500℃至600℃)在温度升高至500℃后,以66.7℃/h(通常为50-80℃/h均适用于本发明)的升温速率从500℃升温至600℃;升温时间为1.5h(通常为1.2-2h);第八升温阶段:(500℃至600℃)在温度升高至600℃后,以33.3℃/h(通常为20-50℃/h均适用于本发明)的升温速率从600℃升温至650℃;升温时间为1.5h(通常为1-2.5h);8-2)烧结降温阶段(650至低于200℃)第一降温阶段:(650至500℃)在温度升高至650℃后,以75℃/h(通常为50-100℃/h均适用于本发明)的降温速率从650℃降温至500℃;降温时间为2h(通常为1.5-3h);粘结剂经高温烧结后变为粘结焦,起到粘结石墨与金属粉末等的作用,烧结降温阶段控制降温速度一方面避免了热震给坯料带来的破坏性伤害,同时使坯料的成焦率更稳定。第二降温阶段:(500℃至低于200℃)在温度降低至500℃后,进行自然冷却,直至温度降低至200℃以下,获得电刷烧结坯料剂电刷熟坯;在电刷坯料进行烧结处理过程中,沥青发生热解缩聚反应转变成粘结焦,沥青在烧结温度200℃以下,煤沥青首先熔融脱水且本身含有的轻质组分有少量的溢出,伴随轻微的热分解反应;在烧结温度260-500℃,热解缩聚反应急剧进行,其中在340-400℃挥发物大量排出,失重速率出现最大值,在260-360℃热分解反应随温度升高不断加剧,在360-500℃热分解反应逐渐减弱且缩聚反应逐渐占优势,煤沥青稠环芳烃分子量逐渐增大;在烧结温度在500-700℃,少量残留的低分子挥发分逸出,煤沥青炭化逐渐形成半焦。9)将电刷熟坯进行切割、磨床、钻孔、填线和与金属碳刷限位盒进行点焊等机械加工步骤后即得电机用电刷。按照jb/t8133.14-1999《电炭制品物理化学性能试验方法体积密度》的方法测定电刷的体积密度;按照jb/t8133.2-1999《电炭制品物理化学性能试验方法电阻率》的方法测定电刷的电阻率;采用hs-19ctv型硬度机测试电刷的肖氏硬度;按照jb/t8133.7-2013《电炭制品物理化学性能试验方法第7部分:抗折强度》的方法测定电刷的抗折强度,结果见表1。实施例21)按照如下重量配比备料(份):其中,所述天然石墨选用t399.9;所述合成石墨粒度为≤325目,含碳量≥99.9%,固定碳含量≥80%,水分≤0.5%,灰份≤0.5%;所述沥青选用软化点为95-110℃的煤沥青,结焦值≈55%,甲苯不溶物含量≈25%,灰分<0.5%;所述金属粉末选用铜粉与银粉的混合物,其中铜粉与银粉的重量之比为5:1;其中所述铜粉选用树枝状电解铜粉,纯度≥99.9%,松装比重为0.8-1.0g/cm3,粒度为≤325目;所述银粉选用片状银粉,纯度99.9%,粉末粒度≤80nm;所述减磨材料选择二硫化钼和二硫化钨的混合物,其中二硫化钼和二硫化钨的重量之比为3:1;其中二硫化钼、二硫化钨的粒度为3000-4000目,纯度为99%;所述添加剂包括六方氮化硼和十八酸钙,其中六方氮化硼和十八酸钙的质量配比为5:1;2)将原料天然石墨、合成石墨置于混捏锅内,开启混捏锅,启动正转模式,室温条件下干粉混合1-1.5h(通常>1h,优选为1-1.5h),制得石墨预混料;3)将石墨预混料于混捏锅内边混捏边加热,直至温度升高至140±10℃时加入沥青,继续加热,以40℃/h(通常为30-50℃/h均适用于本发明)的升温速率升温220±10℃,升温时间为2h(通常为1.6-2.7h);然后停止加热,边混捏边自然降温至温度≤100℃;4)从混捏锅内卸出物料,待物料彻底晾凉,即制得电刷炭素混合物;5)将电刷炭素混合物进行破碎、筛分处理,破碎物料过120目筛,制得电刷材料炭素基体粉,电刷材料炭素基体粉粒度≤120目;6)将制备的电刷材料炭素基体粉,金属粉末、减磨材料、添加剂加入冷混锅于室温(25℃,通常为15-35℃)、相对湿度≤60%的条件下进行混合处理(3±0.5)h,得到电刷材料粉末,注意粉末存放时的防潮、防尘、防高温处理;7)将电刷材料粉末置于模具中,采用液压机进行压制处理即制得电机用电刷粗坯,其中电刷粗坯的体积密度达到2.65g/cm3(通常为2.55-2.75g/cm3);8)将电刷粗坯置于惰性气氛烧结炉中,按图1烧结曲线,制得烧结处理后的电刷熟坯;具体操作步骤与实施例1的步骤8)相同。9)将电刷熟坯进行切割、磨床、钻孔、填线和与金属碳刷限位盒进行点焊等机械加工步骤后即得电机用电刷。按照jb/t8133.14-1999《电炭制品物理化学性能试验方法体积密度》的方法测定电刷的体积密度;按照jb/t8133.2-1999《电炭制品物理化学性能试验方法电阻率》的方法测定电刷的电阻率;采用hs-19ctv型硬度机测试电刷的肖氏硬度;按照jb/t8133.7-2013《电炭制品物理化学性能试验方法第7部分:抗折强度》的方法测定电刷的抗折强度,结果见表1。对照例1以崇德批量产品a473电刷作为对照1,表1为电刷物理机械性能测试结果对照。表1电刷的物理机械性能测试结果试验例1电机用电刷磨损率、火花等级试验采用市售的直流吸尘器电机r545-130a(dc21.6v/130w)和cds*r545*mb021*04(dc28v/100w)作为试验电机进行电刷寿命、火花试验实测对照。采用直流稳压稳流电源负载耐久试验控制仪测试实施例1-2制得的电刷、对照例1进口电刷a473的磨损率、火花等级,试验结果见表2。表2电刷的磨损率试验结果由表2结果可知:本发明方法制备的电机用电刷的磨损率低,耐磨性能优异,与进口电刷a473相比,耐磨损性能更佳。火花等级在其中的r545-130a(dc21.6v/130w)机型上,本发明方法制备的电刷火花等级更低,火花等级降低了1个等级,抑制火花能力好,提高了使用安全性。其中,所述电刷火花等级说明如表3所示。表3电刷的火花等级试验例2电机用电刷效率试验参照国家标准《旋转电机(牵引电机除外)确定损耗和效率的试验方法(gb/t755.2-2003)》测试上述实施例1-2制得的电机用电刷的效率,以市售直流吸尘器电机r545-130a原装电刷a473作为对照例1,测试结果见表4。表4电刷的效率试验结果实施例1实施例2对照例效率26.5%26.8%26.1%由表4的测试结果可知:本发明的电机用电刷的效率较该对照例进口电刷高,为一种节能型电机用电刷。当前第1页12