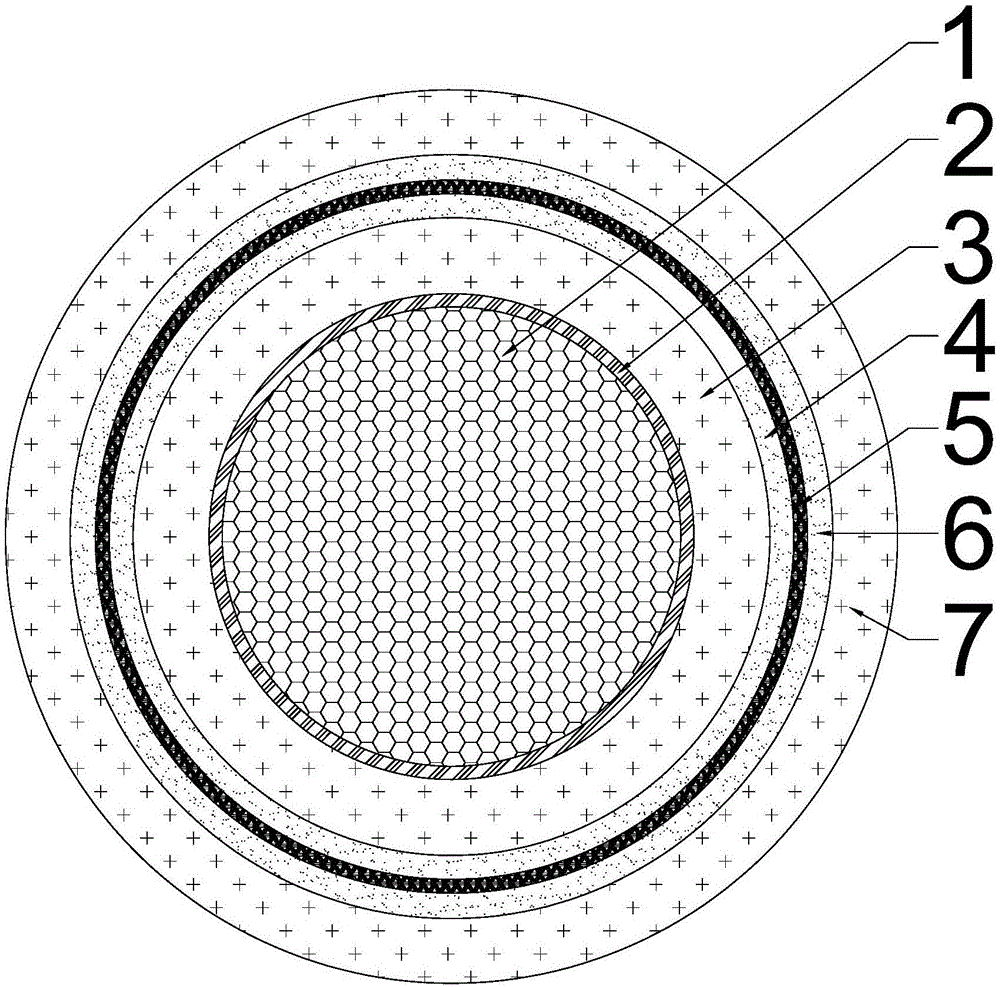
本发明涉及新能源汽车领域,尤其涉及新能源汽车用铝合金电缆及其生产工艺。
背景技术:
:新能源汽车是指采用非常规的车用燃料作为动力来源(或使用常规的车用燃料、采用新型车载动力装置),综合车辆的动力控制和驱动方面的先进技术,形成的技术原理先进、具有新技术、新结构的汽车。目前,国内新能源汽车用电缆产品主要以铜芯为导体材料,pvc为绝缘和护套材料为主,主要存在以下不足:导电芯和绝缘护套柔软度不高,导致电缆的弯曲性能差,易松散和断裂;pvc材料不耐高温且燃烧后会产生大量烟气和毒素,不环保;铜芯导体成本高、重量较重,不够经济。因此有必要设计一种新能源汽车用的耐热、非铜导体的电缆和其生产工艺。技术实现要素:本发明的目的是提供新能源汽车用铝合金电缆及其生产工艺。实现本发明目的的技术方案是:新能源汽车用铝合金电缆,包括导体以及由内到外依次包裹在导体外表面的无纺布绕包带、辐照氟橡胶绝缘层、第一铝塑复合带屏蔽层、镀锡铜丝编织屏蔽层、第二铝塑复合带屏蔽层和辐照氟橡胶护套层。所述导体为耐热铝合金束丝后绞合而成。所述耐热铝合金组分(以质量百分比表示为):zr0.1~1,cu0.1~2,mg0.1~05,fe0.1~0.6,稀土元素0.02~0.2。铝合金丝径在0.12~0.51mm之间,导体截面面积为1.5~150mm2,抗拉强度大于230mpa,导电率大于55%iacs,伸长率大于3.5%,加热230℃,1h或加热180℃,400h,高强耐热铝合金线强度残存率大于90%。所述无纺布绕包带厚度为0.08mm,宽度为30mm,搭盖率为15%~20%。所述辐照氟橡胶绝缘层的厚度为1.3~1.5mm。所述镀锡铜丝编织屏蔽层的丝径为0.12~0.18mm,编织密度≧85%。所述第一铝塑复合带屏蔽层和第二铝塑复合带屏蔽层的厚度为0.025~0.05mm,搭盖率为15%~30%。所述辐照氟橡胶护套层厚度为1.7~2.0mm。新能源汽车用铝合金电缆,其生产工艺包含以下步骤:s1:熔铸得到耐热铝合金。s2:拉丝。绞合。s3:在导体外绕包厚度为0.08mm,宽度为30mm的无纺布绕包带,搭盖率为15%~20%。s4:采用绝缘挤出工艺在导体挤出辐照氟橡胶绝缘层并辐照。s5:在辐照氟橡胶绝缘层外依次绕包第一铝塑复合带屏蔽层。所述镀锡铜丝编织屏蔽层和第二铝塑复合带屏蔽层。所述镀锡铜丝编织屏蔽层的丝径为0.12~0.18mm,编织密度≧85%。所述第一铝塑复合带屏蔽层和第二铝塑复合带屏蔽层的厚度为0.025~0.05mm,搭盖率为15%~30%。s6:在第二铝塑复合带屏蔽层外挤出辐照氟橡胶护套层并辐照。所述s1中,熔铸铝合金形成的铝水中加入组分(以质量百分比表示为):zr0.1~1,cu0.1~2,mg0.1~05,fe0.1~0.6,稀土元素0.02~0.2配成铝液。所述s2中,铝液经过810℃高温精炼,并静置30分钟后进行轧制,铝液在结晶温度前为720℃左右,铸锭温度为520℃,入轧温度500℃,经过轧制后铝杆温度为30℃左右,上盘,拉丝丝径控制在0.12~0.51mm之间。且拉丝过程中由大拉机将9.5mm铝杆加工为2.6mm铝杆,由中拉机将2.6mm铝杆加工为1.0mm铝丝,由小拉机将1.0mm铝丝加工为0.12~0.51mm铝丝,其中小拉机拉丝前铝丝需经过200~300℃,1~2小时退火处理,确保铝丝伸长率,同时增加导体柔软度。导体采用3/51/0.15+6/51/0.15+12/51/0.15结构绞合。即51根0.15丝通过束丝成股后,再进行3股绞合作为中心层,6股按照51/0.15绞合作为复绞层,以12股按照51/0.15绞合作为最外层进行交合绞合,同时绞合时中间层采用右向,最外层采用左向绞合,确保导体不松散。经过束丝机绞合时其节距控制在15~30mm,复绞节距控制在50~80mm,绞合时紧压系数为0.8~0.9。所述s4和s6中,绝缘层挤出工艺,采用90挤出机生产厚度为1.3~1.5mm的辐照氟橡胶绝缘层和厚度为1.7~2.0mm的辐照氟橡胶护套层并辐照。挤出料筒宽度为1200-1600mm,挤出温度:一区120~145℃,二区165~175℃,三区168~180℃,机头170~180℃。绝缘料预烘干温度为65±5℃,时间为4h。生产速度为50~80m/min。辐照剂量为20-25mrad,辐照能量采用4.5mev,辐照圈数采用12道,辐照束流采用20-25ma,辐照束流比m/v/a=0.7-1.0,辐照1次确保产品耐油性能满足:耐柴油、机油:130±5℃,300h,外径变化率≦15%。所述s4和s6中,采用x-ray在线监测辐照氟橡胶绝缘层和辐照氟橡胶护套层的厚度。所述辐照氟橡胶绝缘层和辐照氟橡胶护套层组分(以质量百分比表示为):生胶60~70、mt炭黑15~20、taic5、过氧化物5、抗氧剂1~5、润滑剂1~5。采用连硫工艺,蒸汽压力在15公斤以上,挤出温度控制在50~80℃,材料阻燃性能测试指标符合ul94标准v-0等级燃烧。耐柴油、机油:130±5℃,300h,外径变化率≦15%,产品热老化性能达到200℃,3000h不开裂。通过搅拌机进行搅拌添加基材及母料进行混炼,其氟橡胶成品大大提高了材料性能,如高温永久变形性、耐热性和耐油性,其耐温等级-50~220℃,其中放入烘箱内长期老化满足200℃,3000h热老化,产品卷绕并浸质量浓度为3.0%的氯化钠溶液进行1.0kv/1min交流耐压测试,产品不开裂,不击穿。采用了上述技术方案,本发明具有以下的有益效果:(1)本发明的新能源汽车用铝合金电缆的导体由耐热铝合金束丝后绞合而成,抗拉强度大、导电率、伸长率、耐热性能均十分优良,绝缘层和护套层均采用氟橡胶材料,高温永久变形性、耐热性和耐油性较传统材料均有较大提升,降低了成本,大大提高了本发明的使用安全性和经济效益。(2)本发明的新能源汽车用铝合金电缆的生产工艺将耐热铝合金束丝后采用16/3/50/0.25+3/2/50/0.25结构绞合,逆向绞合,制成的导体铝合金丝径在0.12~0.51mm之间,导体截面面积为1.5~150mm2,抗拉强度大于230mpa,导电率大于55%iacs,伸长率大于3.5%,加热230℃,1h或加热180℃,400h,高强耐热铝合金线强度残存率大于90%。(3)本发明的新能源汽车用铝合金电缆的生产工艺将生胶和mt炭黑等材料经搅拌机进行搅拌添加基材及母料进行混炼,采用连硫工艺,控制挤出温度,材料阻燃性能测试指标符合ul94标准v-0等级燃烧。耐柴油、机油:130±5℃,300h,外径变化率≦15%,产品热老化性能达到200℃,3000h不开裂。(4)本发明的新能源汽车用铝合金电缆的生产工艺中为了将伸长率较铜低的铝在导体绞合前对铝丝进行退火,确保铝丝伸长率,同时增加导体柔软度。(5)本发明的新能源汽车用铝合金电缆的生产工艺中对氟橡胶绝缘层和氟橡胶护套层进行辐照,增强耐柴油、机油性能,加强材料强度。附图说明为了使本发明的内容更容易被清楚地理解,下面根据具体实施例并结合附图,对本发明作进一步详细的说明,其中图1为本发明的结构示意图。附图中的标号为:导体1,无纺布绕包带2,辐照氟橡胶绝缘层3,第一铝塑复合带屏蔽层4,镀锡铜丝编织屏蔽层5,第二铝塑复合带屏蔽层6,辐照氟橡胶护套层7。具体实施方式见图1,本实施例的一种新能源汽车用铝合金电缆,包括导体1以及由内到外依次包裹在导体1外表面的无纺布绕包带2、辐照氟橡胶绝缘层3、第一铝塑复合带屏蔽层4、镀锡铜丝编织屏蔽层5、第二铝塑复合带屏蔽层6和辐照氟橡胶护套层7。导体1为耐热铝合金束丝后绞合而成。耐热铝合金组分(以质量百分比表示为):zr0.1~1,cu0.1~2,mg0.1~05,fe0.1~0.6,稀土元素0.02~0.2。铝合金丝径在0.12~0.51mm之间,导体1截面面积为1.5~150mm2,抗拉强度大于230mpa,导电率大于55%iacs,伸长率大于3.5%,加热230℃,1h或加热180℃,400h,高强耐热铝合金线强度残存率大于90%。无纺布绕包带2厚度为0.08mm,宽度为30mm,搭盖率为15%~20%。辐照氟橡胶绝缘层3的厚度为1.3~1.5mm。镀锡铜丝编织屏蔽层5的丝径为0.12~0.18mm,编织密度≧85%。第一铝塑复合带屏蔽层4和第二铝塑复合带屏蔽层6的厚度为0.025~0.05mm,搭盖率为15%~30%。辐照氟橡胶护套层7厚度为1.7~2.0mm。还包括新能源汽车用铝合金电缆的生产工艺,包含以下步骤:s1:熔铸得到耐热铝合金。s1中,熔铸铝合金形成的铝水中加入组分(以质量百分比表示为):zr0.1~1,cu0.1~2,mg0.1~05,fe0.1~0.6,稀土元素0.02~0.2配成铝液。s2:拉丝。绞合。铝液经过810℃高温精炼,并静置30分钟后进行轧制,铝液在结晶温度前为720℃左右,铸锭温度为520℃,入轧温度500℃,经过轧制后铝杆温度为30℃左右,上盘,拉丝丝径控制在0.12~0.51mm之间。且拉丝过程中由大拉机将9.5mm铝杆加工为2.6mm铝杆,由中拉机将2.6mm铝杆加工为1.0mm铝丝,由小拉机将1.0mm铝丝加工为0.12~0.51mm铝丝,其中小拉机拉丝前铝丝需经过200~300℃,1~2小时退火处理,确保铝丝伸长率,同时增加导体1柔软度。s2中导体1采用3/51/0.15+6/51/0.15+12/51/0.15结构绞合。即51根0.15丝通过束丝成股后,再进行3股绞合作为中心层,6股按照51/0.15绞合作为复绞层,以12股按照51/0.15绞合作为最外层进行交合绞合,同时绞合时中间层采用右向,最外层采用左向绞合,确保导体1不松散。经过束丝机绞合时其节距控制在15~30mm,复绞节距控制在50~80mm,绞合时紧压系数为0.8~0.9。s3:在导体1外绕包厚度为0.08mm,宽度为30mm的无纺布绕包带2,搭盖率为15%~20%。s4:采用绝缘挤出工艺在导体1外挤出辐照氟橡胶绝缘层3并辐照。s5:在辐照氟橡胶绝缘层3外依次绕包第一铝塑复合带屏蔽层4,镀锡铜丝编织屏蔽层5和第二铝塑复合带屏蔽层6。镀锡铜丝编织屏蔽层和第二铝塑复合带屏蔽层。镀锡铜丝编织屏蔽层的丝径为0.12~0.18mm,编织密度≧85%。第一铝塑复合带屏蔽层和第二铝塑复合带屏蔽层的厚度为0.025~0.05mm,搭盖率为15%~30%。s6:在第二铝塑复合带屏蔽层6外挤出辐照氟橡胶护套层7并辐照。s4和s6中,绝缘层挤出工艺,采用90挤出机生产厚度为1.3~1.5mm的辐照氟橡胶绝缘层3和厚度为1.7~2.0mm的辐照氟橡胶护套层7并辐照。挤出料筒宽度为1200-1600mm,挤出温度:一区120~145℃,二区165~175℃,三区168~180℃,机头170~180℃。绝缘料预烘干温度为65±5℃,时间为4h。生产速度为50~80m/min。辐照剂量为20-25mrad,辐照能量采用4.5mev,辐照圈数采用12道,辐照束流采用20-25ma,辐照束流比m/v/a=0.7-1.0,辐照1次确保产品耐油性能满足:耐柴油、机油:130±5℃,300h,外径变化率≦15%。采用x-ray在线监测辐照氟橡胶绝缘层3和辐照氟橡胶护套层7的厚度。辐照氟橡胶绝缘层3和辐照氟橡胶护套层7组分(以质量百分比表示为):生胶60~70、mt炭黑15~20、taic5、过氧化物5、抗氧剂1~5、润滑剂1~5。采用连硫工艺,蒸汽压力在15公斤以上,挤出温度控制在50~80℃,材料阻燃性能测试指标符合ul94标准v-0等级燃烧。耐柴油、机油:130±5℃,300h,外径变化率≦15%。产品热老化性能达到200℃,3000h不开裂。通过搅拌机进行搅拌添加基材及母料进行混炼,其氟橡胶成品大大提高了材料性能,如高温永久变形性、耐热性和耐油性,其耐温等级-20~220℃,其中放入烘箱内长期老化满足200℃,3000h热老化,产品卷绕并浸质量浓度为3.0%的氯化钠溶液进行1.0kv/1min交流耐压测试,产品不开裂,不击穿。产品的各项性能见表1。表1.电缆的各项性能数据序号性能氟橡胶产品其他汽车线1耐油130℃500h20℃20h2耐老化200℃3000h120-175℃3000h3耐温200℃以上最大175℃4耐刮磨优175℃耐刮磨不好5耐酸碱优不良以上所述的具体实施例,对本发明的目的、技术方案和有益效果进行了进一步详细说明,所应理解的是,以上所述仅为本发明的具体实施例而已,并不用于限制本发明,凡在本发明的精神和原则之内,所做的任何修改、等同替换、改进等,均应包含在本发明的保护范围之内。当前第1页12