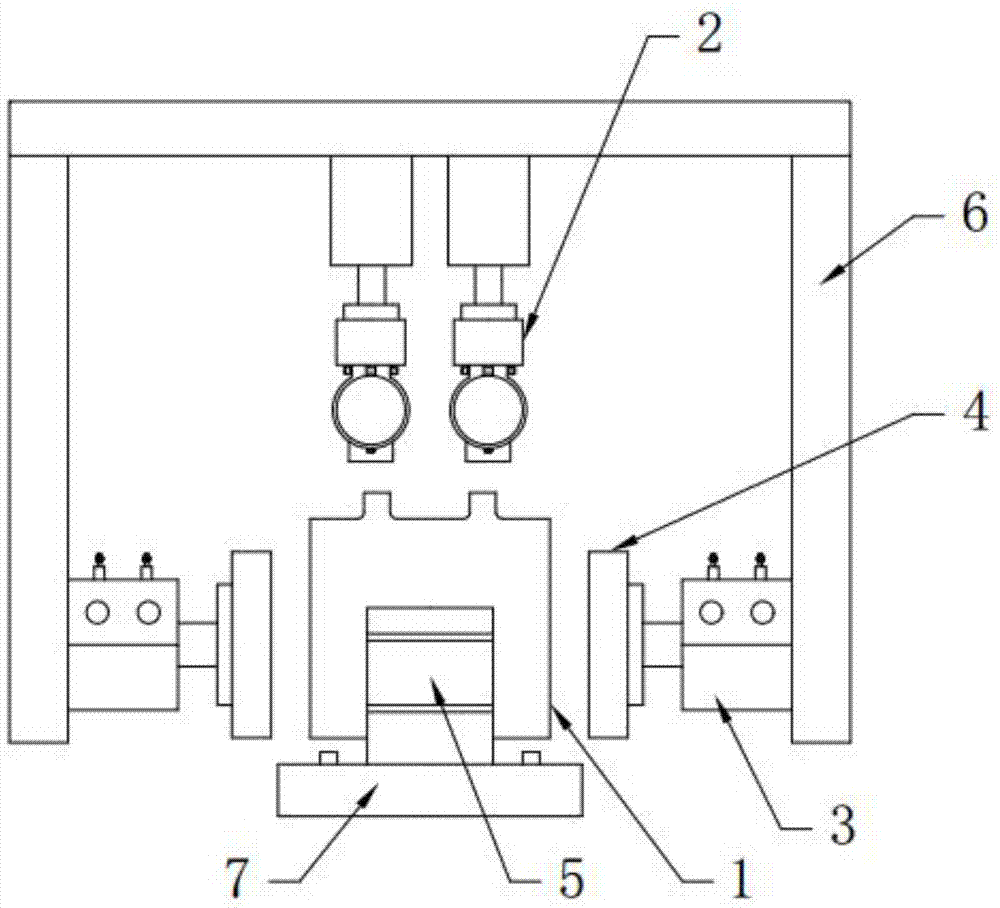
本实用新型属于铅蓄电池技术领域,具体涉及一种铅蓄电池自动折耳装置。
背景技术:
铅蓄电池在生产加工过程中,极板群为由多片极板并联组成的组件,极板群需要压实、组装、极耳焊接等,在极板群入槽焊接前,需要将位于两个侧边的两列极耳进行向内侧弯折一定的距离,否则在焊接后将无法合盖。目前上述步骤由人工手动操作完成,由于不同人的力度差异导致折耳的尺寸不一,而且人工操作效率低下、容易出现漏折、折的角度过大等,进而严重影响到产品的质量和浪费。
技术实现要素:
针对现有技术中的不足与难题,本实用新型旨在提供一种效率更高、准确性更强铅蓄电池自动折耳装置,极耳弯折的角度、尺寸保持一致。
本实用新型通过以下技术方案予以实现:
一种铅蓄电池自动折耳装置,包括工作架、固定挂在所述工作架顶板下表面的两组折耳组件、固定在所述工作架两侧板内壁上的两组定位气缸,所述工作架放置在用于自动运输极板群的传输链上方,两组所述定位气缸为相互对称并相对设置。所述折耳组件包括长形的吊座、安装在所述吊座上的两套电动伸缩轴、固定在所述电动伸缩轴末端的支撑板、并排固定在所述支撑板下表面的连接条与限位长杆、通过固定件安装在所述连接条末端的横向安置的微型气缸、设置在所述微型气缸活塞杆末端的压板,所述连接条与限位长杆并列固定在所述支撑板下表面,所述限位长杆在所述连接条与所述微型气缸内侧,所述限位长杆2长度高于所述连接条与所述微型气缸总长度,且限位长杆末端低于压板末端。
进一步地,所述定位气缸末端固定安装长方形的平板。
进一步地,所述压板为向内倾斜的斜板。
进一步地,所述固定件为卡箍,
进一步地,所述传输链上设置均匀分布的固定槽,所述固定槽由两个固定在所述传输链上的夹具组成,每个极板群置于固定槽内并由两个夹具分别对前后两面进行夹紧固定。
本实用新型工作原理:极板群放置在传输链上的两个夹具之间的固定槽内,通过夹具对首尾极板进行夹紧固定,防止在折耳过程中极板群前后晃动;在传输链移动下,带动极板群定点位移至工作架下方后停住,为防止极板群的极耳与工作架上的折耳组件的位置之间存在左右偏差或不同片的极板未对齐,由两组定位气缸活塞运动带动平板对极板群进行推压,使得其极耳同列对齐且位置对准折耳组件;校准后,由两组折耳组件分别对极板群两列的极耳进行内折,每组折耳组件设置一对微型气缸分别对同列的首尾极耳进行弯折,电动伸缩轴向下运动带动微型气缸与限位长杆活动至需弯折的极耳相应位置,微型气缸活位于首尾外侧的极耳外围,限位长杆位于同列极耳的间隙之间,微型气缸活动带动压板对外侧极耳向内压,限位长杆对极耳弯折的尺寸起到限制作用,防止弯折力度过大、不均等;极耳弯折完成后,传输链继续移动,带动下一组极板群传输至工作架下,并重复上述操作。
与现有技术相比,本实用新型有益效果包括:
(1)本实用新型设置限位长杆与微型气缸、压板配合使用,可保证极耳弯折的角度、尺寸保持一致。
(2)本实用新型为自动操作,无需人工手动,其效率更高、准确性更强。
(3)本实用新型设置微型气缸,其所需空间更小,其运动力度更加可控,可避免力度过大造成极耳变形。
(4)本实用新型设置夹具组成的固定槽、两组定位气缸,使得极耳进行弯折时定位更加准确、极板群更加稳固。
附图说明
图1为本实用新型的结构示意图。
图2为本实用新型的极板群结构示意图。
图3为本实用新型的折耳组件与极板群的侧视图。
图示说明:1-极板群,101-极板,102-极耳,2-折耳组件,201-吊座,202-电动伸缩轴,203-支撑板,204-连接条,205-微型气缸,206-固定件,207-压板,208-限位长杆, 3-定位气缸,4-平板,5-夹具,6-工作架,7-传输链。
在本实用新型的描述中,术语“上”、“下”、“左”、“右”、“内”、“外”等指示的方位或位置关系为基于附图所示的方位或位置关系,仅是为了便于描述本实用新型和简化描述,而不是指示或暗示所指的装置或元件必须具有特定的方位、以特定的方位构造和操作,因此不能理解为对本实用新型的限制。
在本实用新型的描述中,需要说明的是,除非另有明确的规定和限定,术语“安装”、“相连”、“连接”应做广义理解,例如,可以是固定连接、可拆卸连接、一体地连接;可以是机械连接、电连接;可以是直接相连、中间媒介间接相连,可以是两个元件内部的连通。对于本领域的普通技术人员而言可以具体情况理解上述术语在本实用新型中的具体含义。
具体实施方式
下面结合附图,对本实用新型作进一步地说明。
如图2所述,每组极板群1由多片极板101并联组成,两两极板101上的极耳102交错排列,相隔的极板101上极耳102在同一列,由此极板群1上形成了两列极耳,本实用新型将两列极耳首尾向内弯折。
如图1所述,一种铅蓄电池自动折耳装置,包括用于对极板群1极耳进行弯折的两组折耳组件2、用于将极板群1定位的两组定位气缸3。所述折耳组件2、定位气缸3固定在工作架6上,所述折耳组件2固定挂在所述工作架6顶板下表面,所述定位气缸3固定在所述工作架6两侧板内壁上,两组所述定位气缸3为相互对称并相对设置。定位气缸3作用是为防止极板群1的极耳102与工作架6上的折耳组件2的位置之间存在左右偏差或不同片的极板未对齐,由两组定位气缸3对极板群1进行推压,使得其极耳同列对齐且位置对准折耳组件2。所述定位气缸3末端固定安装长方形的平板4,使得在对极板群1定位时受力更加均匀、固定面积也更大。
在具体实施中,所述工作架6放置在用于自动运输极板群1的传输链7上方,所述传输链7从所述工作架6穿过,所述传输链7上设置均匀分布的固定槽,所述固定槽由两个固定在所述传输链7上的夹具5组成,每个极板群1置于固定槽内并由两个夹具5分别对前后两面进行夹紧固定,防止在折耳过程中极板群1前后晃动造成弯折效果不佳,两个夹具5组成的固定槽的尺寸与极板群1的厚度匹配。
如图3所示,所述折耳组件2包括长形的吊座201、安装在所述吊座201上的两套电动伸缩轴202、固定在所述电动伸缩轴202末端的支撑板203、并排固定在所述支撑板203 下表面的连接条204与限位长杆208、通过固定件206安装在所述连接条204末端的横向安置的微型气缸205、设置在所述微型气缸205活塞杆末端的压板207,所述连接条204 与限位长杆208并列固定在所述支撑板203下表面,所述限位长杆208在所述连接条204 与所述微型气缸205内侧,所述限位长杆208长度高于所述连接条204与所述微型气缸205 总长度,且限位长杆208末端低于压板207末端。所述压板207为向内倾斜的斜板,斜板设置使得折耳时极耳顶端优先内折,且受力更加均匀。由于相邻的极板101上极耳102在不同列,位于同一列的两两相邻的极耳102之间存在一个极板距离的空隙,在具体实施极耳弯折时,所述微型气缸205活塞杆推动压板207对首尾外侧的极耳向内折,所述电动伸缩轴202用于带动下方的微型气缸205与限位长杆208活动至需弯折的极耳102位置,所述限位长杆208移动至同列极耳102的间隙内,限位长杆208对极耳弯折的尺寸起到限制作用,可有效防止弯折力度过大、不均等。所述限位长杆208与微型气缸205、压板207 配合使用,可保证每个极板群1极耳102弯折的角度、力度一致。
所述固定件206为卡箍,卡箍为活动可调节式的固定件,便于对微型气缸205的夹紧、调节、更换、维护等。
在具体实施中,所述定位气缸3、微型气缸205、电动伸缩轴202、传输链7均由电机提供动力且由自动系统PLC进行联动控制操作,传输链7设置为周期性运动,配合折耳组件2、定位气缸3的工作来停启,上述设置为常规组件、连接与控制,在图中未标示,本实用新型不详细描述。
在具体实施中,各个组件的固定、安装等通过螺栓或铆钉或焊接等方式进行相互连接,动力、控制系统与相关组件电连接,在技术方案描述时与附图标示时,本实用新型对其连接部分不一一阐述。
以上所述仅表达了本实用新型的优选实施方式,其描述较为具体和详细,但并不能因此而理解为对本实用新型专利范围的限制。应当指出的是,对于本领域的普通技术人员来说,在不脱离本实用新型构思的前提下,还可以做出若干变形、改进及替代,这些都属于本实用新型的保护范围。因此,本实用新型专利的保护范围应以所附权利要求为准。