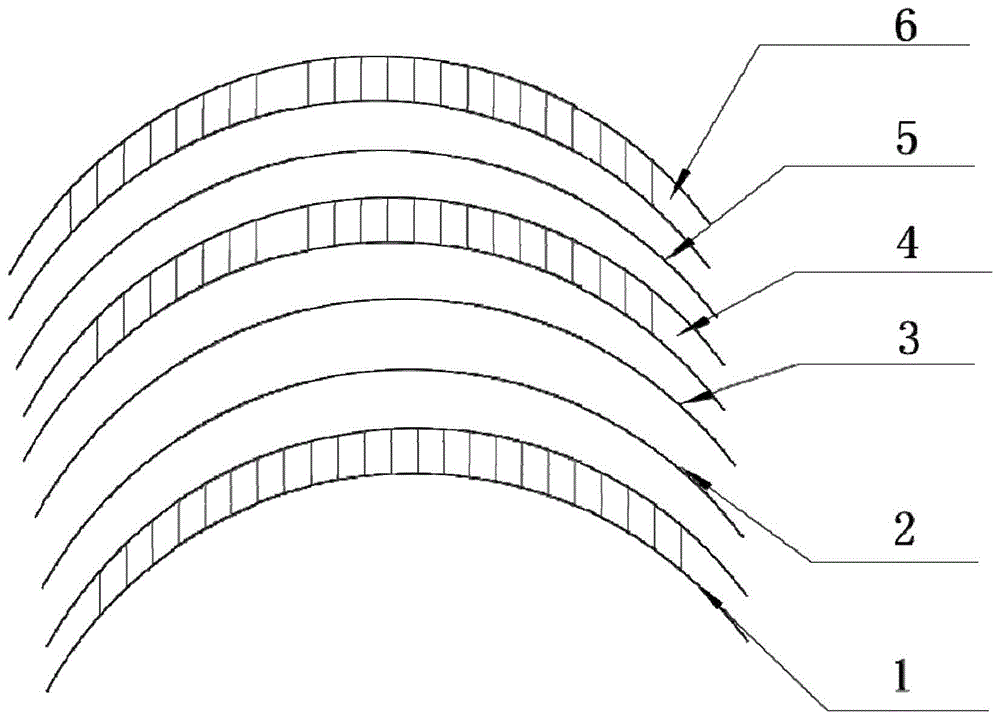
本公开涉及太阳能组件领域,具体地,涉及一种太阳能车辆组件和车辆。
背景技术:
:太阳能电池模组不需要消耗汽油、柴油等能源便可以将太阳能转化为电能。将太阳能电池组布置在车顶上,不仅能够帮助汽车降低汽油、柴油、天然气的消耗,减少二氧化碳的排放,改善空气质量,还可以延长充电式电动汽车的续航里程,提高电动汽车使用的便利性和灵活性,因此被广泛的应用在机动车等车辆中。目前,晶硅太阳能电池片或者大部分其他太阳能组件多为平面结构且偏刚性,如果想将太阳能电池模组应用在机动车上(比如车辆的车顶)时,一般要采取支架等结构进行固定,不但增加车身重量,而且会影响整车的美观性。此外还可以采取柔性太阳能薄膜标准组件以表面贴装形式进行安装,但现有的太阳能电池组不依据车身曲线设计,使其铺设受限,仅能铺设在如车顶及车身等相对较平面的位置;并且贴装后无法与车身紧密贴合,在高速驾驶时可能会脱落,存在一定安全隐患。技术实现要素:本公开的目的是提供一种太阳能车辆组件和车辆。为了实现上述目的,本公开第一方面:提供一种太阳能车辆组件,该组件包括由下向上依次叠置的车辆壳基体、固化的树脂基复合材料层、第一胶膜层、太阳能芯片组层、第二胶膜层和上封装层。可选地,所述车辆壳基体包括车顶基体、前顶盖基体、后顶盖基体、左车门基体和右车门基体中的一种或多种。可选地,所述树脂基复合材料层的厚度为0.2~0.6mm。可选地,所述太阳能芯片组层包括多个相互连接的子芯片,所述子芯片为铜铟镓硒薄膜太阳能电池、钙钛矿薄膜太阳能电池、有机半导体薄膜太阳能电池、GaAs化合物半导体薄膜太阳能电池或非晶硅异质结太阳能电池。可选地,所述第一胶膜层和第二胶膜层的厚度各自为0.1~1.5mm。可选地,所述上封装层的厚度为0.1~8mm。可选地,所述固化的树脂基复合材料层、第一胶膜层、太阳能芯片组层、第二胶膜层和上封装层的形状分别与所述车辆壳基体的形状相匹配。本公开第二方面:提供一种车辆,该车辆包括本公开第一方面所述的太阳能车辆组件。通过上述技术方案,本公开的太阳能车辆组件直接以车辆壳基体为下封装层,在其上设置包括树脂基复合材料层、太阳能芯片组层在内的多层结构,从而得到与车身形状相匹配的太阳能组件,无需对车体结构进行二次改造或额外使用固定结构,对车辆的轻量化效果显著,且不易脱落,安全性好。本公开的其他特征和优点将在随后的具体实施方式部分予以详细说明。附图说明附图是用来提供对本公开的进一步理解,并且构成说明书的一部分,与下面的具体实施方式一起用于解释本公开,但并不构成对本公开的限制。在附图中:图1是本公开提供的太阳能车辆组件的一种具体实施方式的结构示意图。附图标记说明1车辆壳基体2树脂基复合材料层3第一胶膜层4太阳能芯片组层5第二胶膜层6上封装层具体实施方式以下结合附图对本公开的具体实施方式进行详细说明。应当理解的是,此处所描述的具体实施方式仅用于说明和解释本公开,并不用于限制本公开。在本公开中,在未作相反说明的情况下,使用的方位词如“上、下”通常是指组件实际使用时的上或下,具体可参考图1的图面方向。本公开第一方面提供一种太阳能车辆组件,参考图1,该组件包括由下向上依次叠置的车辆壳基体1、树脂基复合材料层2、第一胶膜层3、太阳能芯片组层4、第二胶膜层5和上封装层6。其中,为清楚说明本公开的太阳能车辆组件的结构,图1中将上述各层间隔示出,而本领域技术人员可以知晓的是,在实际的组件产品中,上述各层是紧密贴合的。本公开直接以车辆壳基体为下封装层,在其上设置包括树脂基复合材料层、太阳能芯片组层在内的多层结构,从而得到与车身形状相匹配的太阳能组件,无需对车体结构进行二次改造或额外使用固定结构,对车辆的轻量化效果显著,且不易脱落,安全性好。根据本公开,所述车辆壳基体1可以为车辆上适于布置太阳能电池组的任意部位的基体(车辆外壳),例如可以包括车顶基体、前顶盖基体、后顶盖基体、左车门基体和右车门基体中的一种或多种。在本公开优选的实施方式中,所述车辆壳基体1为车顶基体。根据本公开,所述树脂基复合材料层2的厚度通常可以为0.2~0.6mm,其具有粘合密封,使组件免受湿气等侵蚀,以及提升组件机械强度的作用,可以是由一层或多层树脂基复合材料成型后形成的。具体地,所述树脂基复合材料层2可以包括树脂和纤维。其中,树脂的种类可在较大范围内选择,例如可以为环氧树脂、不饱和聚酯树脂、乙烯基树脂或聚氨酯树脂,其分子量没有特殊的限定;纤维可以为具有增强效果的任意种类,例如可以为玻璃纤维、碳纤维或芳纶纤维,纤维的具体形态没有特殊的限制,例如可以为短切纤维、长切纤维或连续纤维、中空纤维等。以所述树脂基复合材料层2的总重量为基准,所述树脂的含量可以为30~70重量%,所述纤维的含量可以为30~70重量%。为了进一步提高组件的机械强度和轻量化效果,在本公开的一种优选的实施方式中,所述树脂为环氧树脂,纤维为碳纤维;进一步地,以所述树脂基复合材料层2的总重量为基准,所述环氧树脂的含量为45~65重量%,所述碳纤维的含量为35~55重量%。根据本公开,所述太阳能芯片组层4可以包括多个相互连接的子芯片,该多个子芯片的连接和排列方式没有特殊的限制,可以通过本领域技术人员熟知的方式相互连接,例如并联、串联、串并联等,多个子芯片可上下叠置,也可平行并列设置,相邻子芯片之间可预留适当间隙(例如0~5mm)以避免短路。所述子芯片可以为各种常见的薄膜太阳能电池,如铜铟镓硒薄膜太阳能电池、钙钛矿薄膜太阳能电池、有机半导体薄膜太阳能电池、GaAs化合物半导体薄膜太阳能电池或非晶硅异质结太阳能电池。所述子芯片的数量和布置方式等均可根据实际需要(如根据车辆壳基体的形状、面积等)进行调整,实现较高的灵活度。所述子芯片均形成为整片,输出功率无损失。根据本公开,所述第一胶膜层3和第二胶膜层5的材料各自可以为乙烯-醋酸乙烯酯共聚物、聚乙烯醇缩丁醛树脂、聚烯烃、聚烯烃衍生物或有机硅硅,优选为聚烯烃或聚烯烃衍生物。所述第一胶膜层3和第二胶膜层5的材料可以相同,也可以不同。为进一步提高组件的性能,优选地,所述第一胶膜层3的材料和第二胶膜层5的材料的可见光透过率各自可以为大于85%,此外,还可具有足够低的水汽透过率(如低于10-1g/m2·d)。所述第一胶膜层3和第二胶膜层5的厚度各自可以为0.1~1.5mm。根据本公开,所述上封装层6的材料为本领域常规的可用于封装的高分子聚合物,例如可以为选自ETFE、EVOH、PET和PC中的一种或多种。进一步地,为了优化组件的性能,还可以将上述材料进行改性处理(如高阻隔改性处理、耐紫外改性处理、防刮伤改性处理等)后使用。优选情况下,所述上封装层6的材料的可见光透过率可以为大于90%,此外,还可选择具有较优隔绝水汽(例如,水汽透过率低于10-3g/m2·d)、耐紫外等功效的材料作为所述上层封装。所述上封装层6的厚度可以为0.1~8mm。根据本公开,为了提高车辆的美观性,所述固化的树脂基复合材料层2、第一胶膜层3、太阳能芯片组层4、第二胶膜层5和上封装层6的形状可以分别与所述车辆壳基体1的形状相匹配,从而形成形状统一的一体式太阳能车辆组件。本公开所述的太阳能车辆组件的方法可以包括:S1、在车辆壳基体上依次铺设未完全固化的柔性树脂基复合材料、第一胶膜层的材料、太阳能芯片组、第二胶膜层的材料和上封装层的材料,得到预制体;S2、将步骤S1得到的所述预制体进行真空固化封装成型。根据本公开,步骤S1中,所述未完全固化的柔性树脂基复合材料、第一胶膜层的材料、太阳能芯片组、第二胶膜层的材料和上封装层的材料的铺设区域与所述车辆壳基体的形状相匹配,以最终形成符合车身形状的太阳能车辆组件。铺设完成后,可进行适当固定,避免预制体发生位移。根据本公开,步骤S1中,所述未完全固化的柔性树脂基复合材料为树脂完全固化前的阶段性中间产物,其具有一定的柔性,因此可适应车辆壳基体的形状,实现与车身的紧密贴合;同时,其可在步骤S2中继续熔融并交联固化,从而实现粘合密封,并达到使组件免受湿气等侵蚀,提升组件机械强度的效果。所述未完全固化的柔性树脂基复合材料的柔性程度和固化程度根据树脂的种类有所不同,本公开对其没有特殊的限制,只要能达到上述目的即可。例如,当该复合材料为环氧树脂基复合材料或聚氨酯基复合材料时,其可以为固化程度在50%左右的柔性半固化材料;当该复合材料为不饱和聚酯树脂基复合材料或乙烯基树脂基复合材料时,其可以为经过熟化处理得到的柔性半固化材料。根据本公开,步骤S2中,所述真空固化封装成型可以在本领域的常规封装设备中进行,如真空层压机。进一步地,所述真空封装成型可以包括:将所述预制体放入真空层压机的真空袋中,先在30~60℃下进行抽真空处理至真空度为80~100kPa并维持0.5~1h,然后将真空袋推入层压机,在温度为130~160℃,真空度为90~100kPa的条件下进行层压固化成型2~3h。上述条件有利于树脂基复合材料固化完全,达到粘合和结构增强的预期效果。该步骤中,第一胶膜层的材料、树脂基复合材料和第二胶膜层的材料充分融化和固化交联,填充车辆壳基体、太阳能芯片组、和下封装层之间的空隙,最终使三者粘结为一体。所述真空封装成型完成后,自然冷却至室温,得到太阳能车辆组件。上述方法直接依据车身形状在车辆壳基体上铺设预制体,然后一体化一次封装成型,制成太阳能车辆组件,生产效率高、成本低。本公开第二方面:提供一种车辆,该车辆包括本公开第一方面所述的太阳能车辆组件。以下通过实施例进一步说明本公开,但并不限定本公开。实施例中,太阳能车辆组件的树脂基复合材料层、第一胶膜层、第二胶膜层和上封装层的厚度采用螺旋测微器进行检测。粘合强度的测试方法为:裁切1cm宽度的组件,采用剥离力机以180°进行剥离测试。组件制备成本为组件及固定结构等相关辅料成本、人工成本与设备成本的总和。实施例1本实施例中,柔性树脂基复合材料为55重量%环氧树脂-45重量%碳纤维,第一胶膜层和第二胶膜层的材料均为聚烯烃(乙烯-辛烯共聚物,可见光透过率为89%),上封装层的材料为ETFE与PET的复合材料,太阳能芯片组是由50个子芯片(铜铟镓硒薄膜太阳能电池)串并联结合形成的。在车顶基体上依次铺设上述柔性树脂基复合材料、第一胶膜层的材料、太阳能芯片组、第二胶膜层的材料和上封装层的材料,得到预制体;将其放入真空层压机的真空袋中,先在30℃下进行抽真空处理至真空度为100kPa并维持0.5h,然后将真空袋推入层压机,在温度为150℃,真空度为100kPa的条件下进行层压固化成型2h,推出层压机,自然冷却至室温,得到本实施例制备的太阳能车辆组件。经检测,该组件中树脂基复合材料层的厚度为0.5mm,第一胶膜层的厚度为0.4mm,第二胶膜层的厚度为0.4mm,上封装层的厚度为0.3mm,该组件的单位重量、粘合强度和制备成本数据列于表1。实施例2本实施例中,柔性树脂基复合材料为45重量%环氧树脂-55重量%玻璃纤维,第一胶膜层和第二胶膜层的材料均为乙烯-醋酸乙烯酯共聚物(可见光透过率为85%),上封装层的材料为改性PET复合材料,太阳能芯片组为由50个子芯片(铜铟镓硒薄膜太阳能电池)串并联结合形成的。在车顶基体上依次铺设上述柔性树脂基复合材料、第一胶膜层的材料、太阳能芯片组、第二胶膜层的材料和上封装层的材料,得到预制体;将其放入真空层压机的真空袋中,先在50℃下进行抽真空处理至真空度为90kPa并维持1h,然后将真空袋推入层压机,在温度为130℃,真空度为100kPa的条件下进行层压固化成型3h,推出层压机,自然冷却至室温,得到本实施例制备的太阳能车辆组件。经检测,该组件中树脂基复合材料层的厚度为0.6mm,第一胶膜层的厚度为0.5mm,第二胶膜层的厚度为0.5mm,上封装层的厚度为0.2mm,该组件的单位重量、粘合强度和制备成本数据列于表1。对比例1按照现有技术中的方法制备太阳能车辆组件,然后安装于车顶上。具体步骤为:a、支架结构设计:依据车顶结构设计支架结构,并加工成型;b、组件封装:依据薄膜太阳能电池需求的封装结构进行封装;c、组件安装:将薄膜太阳能电池安装于预先设计好的支架结构上,并将此结构整体焊接在车顶上。该组件(包括固定结构)的单位重量、粘合强度和制备成本数据列于表1。对比例2按照现有技术中的方法制备太阳能车辆组件,然后安装于车顶上。具体步骤为:a、组件封装:依据薄膜太阳能电池需求的封装结构进行封装;b、组件安装:将薄膜太阳能电池贴背胶,然后用背胶将组件安装于预铺的车顶上。该组件(包括固定结构)的单位重量、粘合强度和制备成本数据列于表1。表1单位重量,kg/m2粘合强度,N/m成本,元/瓦实施例12509.5实施例224510对比例110-27对比例23.52013.5由表1可见,相比传统方法,本公开的太阳能车辆组件具有较高的粘合强度,轻量化效果显著,且制造成本更低。以上结合附图详细描述了本公开的优选实施方式,但是,本公开并不限于上述实施方式中的具体细节,在本公开的技术构思范围内,可以对本公开的技术方案进行多种简单变型,这些简单变型均属于本公开的保护范围。另外需要说明的是,在上述具体实施方式中所描述的各个具体技术特征,在不矛盾的情况下,可以通过任何合适的方式进行组合,为了避免不必要的重复,本公开对各种可能的组合方式不再另行说明。此外,本公开的各种不同的实施方式之间也可以进行任意组合,只要其不违背本公开的思想,其同样应当视为本公开所公开的内容。当前第1页1 2 3