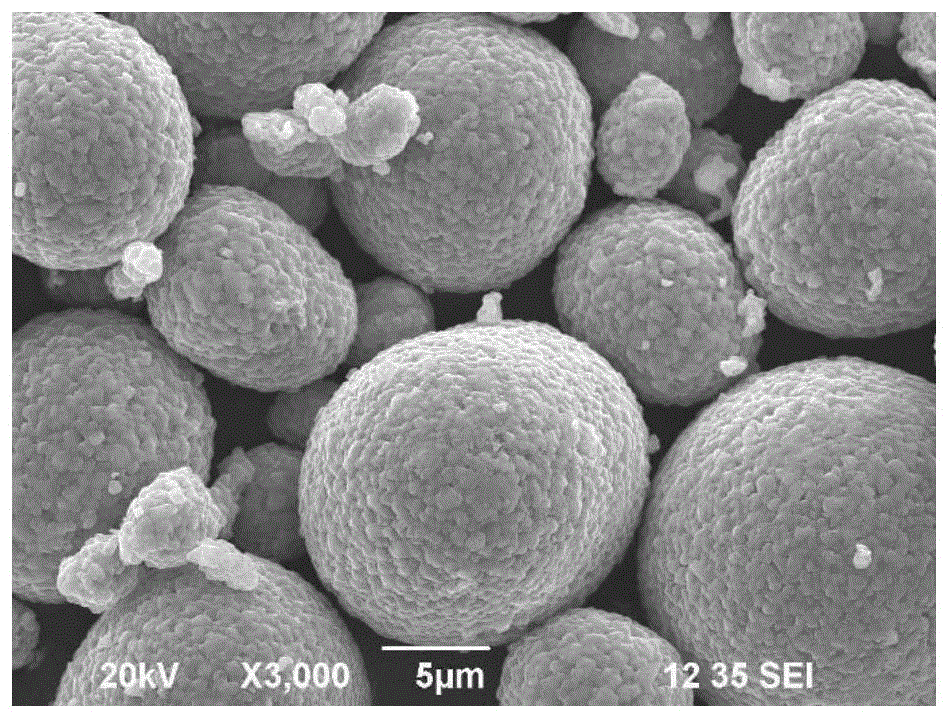
本发明涉及锂离子电池领域,主要涉及锂离子电池正极材料领域,具体涉及一种包覆有锆元素的锂离子电池正极材料及其制法和应用。
背景技术:
:目前常见的锂离子电池正极材料主要有钴酸锂、锰酸锂、镍钴锰酸锂和磷酸亚铁锂。研究表明,制备镍钴锰酸锂材料随着镍含量的上升对后续加工过程要求较为苛刻,通常镍含量越高,生产环境的水分及气氛控制非常重要,因此需要在加工过程中尽量在低水分下进行,为此需要对暴露于空气中比较长的工序进行分析,应当尽量缩短该工序的加工时间,在所有的加工工序中,材料的如过筛,包装等工序均是加工时间比较长的工序(瓶颈工序),上述工序影响材料加工性能的主要原因是高镍三元材料的流动性差。中国专利文献cn03816550.3公开了一种混入超细粉体中的流化添加剂,两步法制备锂离子电池正极材料的方法。将制备得到的镍钴铝氢氧化物ni0.80co0.15al0.05(oh)2粉末在空气中300℃/3~4h,自然冷却到室温,得到棒状氧化镍钴铝,再所得氧化镍钴铝、锂源和柠檬酸溶于水中,在室温下搅拌得到悬浊液,将此悬浊液于80~90℃水浴搅拌得到凝胶;将其干燥后研磨成粉末;再将粉末放置在空气中750℃/2~4h,自然冷却到室温,即得lini0.80co0.15al0.05o2。美国专利文献us5635548中公开了细粉涂料可以通过干法混入至少两种不同的添加物来提高其流动性能。这些无机添加物为:氧化铝、氢氧化铝、氧化钙、二氧化硅、氧化锌、氧化锆、三氧化钼、氧化铈,三氧化钨和硅酸铝。据发明者称,最有效的添加剂是氧化铝、氢氧化铝、硅酸铝和二氧化硅。这些添加剂都是通过实验确定的,没有理论依据。以上所列的添加剂,大部分是陶瓷或者矿物质,且对于锂电池材料而言,直接混合固然可以改善粉体的流动性,但锂电池制备除涉及粉体流动外,还涉及制浆及电化学性能,不能为仅改善粉体流动性能而牺牲其他性能尤其是锂电池的电化学性能。技术实现要素:本发明解决的技术问题是:现有的锂离子电池用高镍三元正极材料在使用过程中流动性不好,在使用过程中出现随机性堆积和结块,在制浆过程中容易凝胶,现有技术均就改善粉体材料的流动性提出了各自的解决方案,但对于应用于锂离子电池体系的正极材料而言,并不能兼顾粉体流动性能和电化学性能,人为添加助滤剂成份并不适用于电化学体系,因此从材料本身着手亟待开发一种新的简单可行的改进粉体流动性的正极材料和制备方法。为解决上述技术问题,本发明在分析高镍三元正极材料制备工艺后,最终发现加入不同种类锆源可以显著改善高镍正极材料的流动性能,同时不影响锂离子电池用正极材料的电化学性能,对于锂离子电池正极材料的应用具有重要意义。具体来说,针对现有技术的不足,本发明提供了如下技术方案:一种锂离子电池正极材料,其特征在于,含有化学式(i)所示组成的正极基础原料:lixniacobmco2,并掺杂有r元素,且包覆有锆元素;其中,0.95<x<1.15,0.55<a<0.95,0<b<0.2,0<c<0.25,0.98<a+b+c<1.05,m选自锰元素或铝元素,所述r元素选自钴、钛、钇或锆元素的一种或两种以上。所述化学式(i)为lixniacobmco2。优选的,上述正极材料中,所述正极材料的化学组成式为lixniacobmcrdzreo2,0≤d<0.1,0<e<0.1。优选的,上述正极材料中,所述r元素的质量占正极材料的200-5000ppm,优选为500-5000ppm,更优选为500-3500ppm。优选的,上述正极材料中,所述包覆的锆元素的质量占正极材料的200-2000ppm,优选为500-2000ppm。优选的,上述正极材料中,所述正极材料的中位粒径为5-15μm。优选的,上述正极材料中,r元素包含钴或钛;优选的,上述正极材料中,r元素包含钇和锆;优选的,上述正极材料中,r元素包含钴和钇。优选的,上述正极材料中,r元素包含钛和锆。优选的,上述正极材料的比表面积为0.2-5m2/g。本发明还提供上述正极材料的制备方法,其特征在于,包括下述步骤:(1)混合包括锂源、前驱体和r元素源的原料,在200-800℃下进行第一次烧结,其中,所述前驱体选自镍钴锰前驱体或镍钴铝前驱体;(2)将包括步骤(1)所得产物与锆源混合后,得到预包覆物;(3)将步骤(2)所得预包覆物在700-880℃下进行第二次烧结,得到所述正极材料。其中,所述步骤(1)中,所述锂源和前驱体共同构成正极基础材料的原料。优选的,上述制备方法中,所述锂源选自氢氧化锂、草酸锂、碳酸锂、硝酸锂、醋酸锂、氟化锂、氯化锂、叔丁醇锂或柠檬酸锂中的一种或两种以上。优选的,上述制备方法中,所述锆源选自含锆元素的可溶性盐或氧化物,所述r元素源选自含r元素的可溶性盐或氧化物。优选的,上述制备方法中,所述含锆元素的氧化物的中位粒径为20-3000nm。优选的,上述制备方法中,所述第一次焙烧的气氛为含氧空气,所述空气流量为150-600nm3/h,氧气体积含量为40-70%。优选的,上述制备方法中,所述第一次焙烧的氧气流量为100-500nm3/h。优选的,上述制备方法中,所述第二次焙烧的气氛为含氧空气,所述空气流量为200-600nm3/h,氧气体积含量为50-70%。优选的,上述制备方法中,所述第二次焙烧的氧气流量为100-500nm3/h。优选的,上述制备方法中,第一次焙烧过程的烧失率为25-45%,所述第二次焙烧过程的烧失率为0.5-10%。本发明还提供一种锂离子电池正极材料,其特征在于,由上所述方法制备得到。本发明还提供一种锂离子电池,其特征在于,包括上述正极材料。本发明还提供上述正极材料或上述锂离子电池在移动数码产品、电动汽车锂电池能源领域或储能领域的应用。本发明的优点是:本发明采用锆源来对高镍三元正极材料表面进行改进,通过锆源参与材料的表面的修饰进而改进粉体的流动性能,扩大高镍正极材料应用环境。该方法经济可行,适用性广泛,效果明显,具有较好的应用前景。附图说明图1为实施例4所得正极材料的扫描电镜图,放大倍数为3000倍。图2为对比例4所得正极材料的扫描电镜图,放大倍数为3000倍。图3为实施例6和对比例6的针刺试验电压及温升曲线图。具体实施方式鉴于目前锂离子电池用高镍正极材料对于加工条件敏感,易造成生产过程中瓶颈的问题,本发明提供一种制备流动性好的高镍正极材料及其制备方法,通过在包覆阶段添加锆源再经处理后即可得到流动性好的正极材料,有利于克服材料加工瓶颈,同时提升正极材料的物理及电化学性能。该工艺制备简单,经济可行,同时不影响锂离子电池用正极材料的电化学性能。。一种优选的实施方式中,本发明提供一种流动性好的锂离子电池用高镍三元正极材料,其特征在于,化学式为lixniacobmncrdzreo2其中,r为掺杂元素,0.95<x<1.15,0.55<a<0.85,0<b<0.2,0<c<0.2,0.98≤a+b+c≤1.00,0≤d<0.1,0<e<0.1;其中,所述镍元素占正极材料的质量分数>30%,优选为>40%,锰元素(mn)可以被铝(al)替代。优选的,上述流动性好的锂离子电池用高镍三元正极材料,其包括半成品制备过程中对材料颗粒表面锆处理过程部分,锆的含量在结构式中为0~0.1。优选的,上述流动性好的锂离子电池用高镍三元正极材料,其特征在于:本体半成品制备过程部分中可以加入掺杂元素r,r的含量在结构式中为0~0.1。优选的,上述流动性好的锂离子电池用高镍三元正极材料,其特征在于:半成品制备过程部分中可以加入掺杂元素r,r为钴,钛,钇,锆等元素中的一种或者两种以上。另一种优选的实施方式中,本发明还提供上述锂离子电池用高镍三元正极材料的制备方法,其特征在于,包括下述步骤:将包括前驱体、锂源化合物、掺杂元素化合物和其他助剂原料按计量比混合后,经过烧结得到所述锂离子电池正极材料半成品;其中,所述前驱体化学式为niacobmncrd(oh)2,其中,r为掺杂元素,0.55<a<0.85,0<b<0.2,0<c<0.2,0.98<a+b+c<1.05,0≤d<0.1;所述正极材料化学式为lixniacobmncrdzreo2,其中,0.95<x<1.15,0<e<0.1。再将锂离子电池半成品与锆源按计量比加入溶剂或者是干态混合后进行脱水及热处理,得到锂离子电池正极材料。优选的,上述制备方法中,所述锂源化合物选自含氢氧化锂、草酸锂、碳酸锂、硝酸锂、醋酸锂、氟化锂、氯化锂、叔丁醇锂或柠檬酸锂中的一种或两种以上。优选的,上述制备方法中,所述锆源为锆的可溶解性盐类或者是氧化物及其组合物原料。优选的,上述制备方法中,所述锆氧化物的中位粒径为20-3000nm。优选的,上述制备方法中,所述热处理为焙烧过程,所述焙烧温度为700-880℃,烧结气氛为富氧空气,氧气体积含量为50-70%,焙烧时间为5-10小时,空气流量为200-600nm3/h。优选的,上述制备方法中,对于加入了水原料制备的混合物,在所述焙烧过程之前,还包括预烧的过程,所述预烧过程包括下述步骤:在200-800℃,氧气体积比为40%-70%的条件下,烧结5-20小时,空气流量为150-600nm3/h。优选的,上述掺杂工艺中,其中锂盐为碳酸锂,草酸锂,单水氢氧化锂,醋酸锂,氟化锂等的一种或多种,纯度为工业级或者是电池级,所述的目标掺杂物为钴、钛、钇、锆等具有一定粒度的氧化物,盐类,或者是氧氧化物中的一种或者是几种。本发明还提供高镍锂离子三元正极材料在制造锂离子二次电池、移动式存贮设备和储能电站中的应用。本发明还提供一种锂离子二次电池,其特征在于,包含上述的高镍锂离子电池用正极材料制成的正极。本发明还提供一种锂离子二次电池,其特征在于,所述高镍锂离子正极材料是通过上述的方法制备得到。下面通过具体实施例来进一步说明本发明所述包覆有锆元素的锂离子电池正极材料及其制法和应用。在下面的实施例中,所用的各试剂和仪器的信息如下:表1本发明实施例中所用试剂信息表2本发明实施例中所用设备信息实施例一流动性改善的锂离子电池正极材料的制备实施例1选用200l融合机,开启搅拌(500rpm),在搅拌情况下加入100kg的镍钴锰前驱体(ni0.69co0.14mn0.16(oh)2),再称取46.3kg单水氢氧化锂粉体加入到融合机中,再称取0.36kg碱式碳酸钴(钴含量按成品质量计为3300ppm),在搅拌情况下按80wt%固含量添加38.3kg去离子水,搅拌0.5h后进一步降低速度(50rpm)搅拌20min出料形成具有一定成型度的膏状物料备用。采用通气24m辊道窑。设置升温区温度为200℃,通入富氧空气(氧含量体积比为60%,气体输入量180nm3/h)条件下将上述膏状物料装入到陶瓷钵中进行第一次烧结,烧结时间为15h,将物料隔离空气冷却至常温,称取进出物料的重量,统计烧失率(第一次烧结粉料质量差与第一次烧结前粉料质量的比值)为31.6%。然后用气旋涡流粉碎机进行粉碎,粉碎时控制环境空气的湿度≤2%,得到第一次烧结半成品。将半成品再次投入到融合机中,向其中加入0.13kg经去离子水溶解的五水硝酸锆(锆含量按成品质量计为250ppm),经混合0.5h后取出物料重新装入陶瓷匣钵中,采用通气24m辊道窑。设置升温区温度为700℃,通入富氧空气条件下(氧含量体积比为70%,气体输入量600nm3/h),烧结时间为8h,将物料隔离空气冷却至常温,称取进出物料的重量,统计烧失率(第二次烧结粉料质量差与第二次烧结前粉料质量的比值)为2.1%。然后用气旋涡流粉碎机进行粉碎,得到镍钴锰酸锂正极材料,材料的粒度(dv50)为7.0μm,比表面积为1.2m2/g。采用稀盐酸消解并经icp对正极材料的元素定量分析后结果核算发明物正极材料的化学式为li0.98ni0.69co0.14mn0.16zr0.0004o2,其中,掺杂元素为co,d为0.005。实施例2选用200l犁式混料机,开启搅拌(20rpm),在搅拌情况下加入100kg的镍钴锰前驱体(ni0.6co0.19mn0.21(oh)2),再称取41.8kg碳酸锂粉体加入到犁式混料机中,在搅拌情况下添加7.45kg钛酸四丁酯(工业级,纯度98.5%,浓度20wt%,钛含量以成品计为2000ppm),1.1kg去离子水,搅拌2h后进一步降低速度(3-5rpm)搅拌6h出料形成具有一定成型度的粉状物料备用。采用通气24m辊道窑。设置升温区温度为500℃,通入富氧空气(氧含量体积比为65%,气体输入量400nm3/h)条件下将上述膏状物料装入到陶瓷钵中进行第一次烧结,烧结时间为16h,将物料隔离空气冷却至常温,称取进出物料的重量,统计烧失率为28.9%。然后用气旋涡流粉碎机进行粉碎,粉碎时控制环境空气的湿度≤2%,得到第一次烧结半成品。将半成品再次投入到混合机中,向其中加入0.18kg纳米二氧化锆(按成品质量计锆元素含量为1300ppm),经混合3.0h后取出物料重新装入陶瓷匣钵中,采用通气24m辊道窑。设置升温区温度为880℃,通入富氧空气条件下(氧含量体积比为70%,气体输入量600nm3/h)将上述第一次烧结半成品粉料装入到陶瓷钵中进行烧结,烧结时间为8h,将物料隔离空气冷却至常温,称取进出物料的重量,统计烧失率为5.1%。然后用气旋涡流粉碎机进行粉碎,得到镍钴锰酸锂正极材料,材料的粒度(dv50)为8.5μm,比表面积为0.53m2/g。采用稀盐酸消解并经icp对正极材料的元素定量分析后结果核算发明物正极材料的化学式为li1.01ni0.60co0.19mn0.21zr0.001o2,其中,掺杂元素为ti,d为0.02。实施例3选用200l捏合机,开启搅拌(30rpm),在搅拌情况下加入100kg的镍钴锰前驱体(ni0.81co0.10mn0.11(oh)2),再称取57.9kg草酸锂粉体加入到捏合机中,称取0.067kg纳米三氧化二钇(陶瓷级,纯度98.5%,含量以成品计钇含量约为500ppm),0.19kg五水硝酸锆(工业级,纯度98.5%,含量以成品计锆含量约为400ppm)搅拌1h后进一步降低速度(10rpm)搅拌30min出料形成具有一定成型度的膏状物料备用。采用通气24m辊道窑。设置升温区温度为750℃,通入富氧空气条件下(氧含量体积比为70%,气体输入量600nm3/h)将上述膏状物料装入到陶瓷钵中进行烧结,烧结时间为8h,将物料隔离空气冷却至常温,称取进出物料的重量,统计烧失率为37.8%。然后用气旋涡流粉碎机进行粉碎,得到镍钴锰酸锂正极材料,材料的粒度(dv50)为16.0μm,比表面积为0.2m2/g。将半成品再次投入到混合机中,向其中加入经0.547kg正丙醇锆(按成品质量计锆元素含量为1000ppm),经混合3.0h后取出物料重新装入陶瓷匣钵中,采用通气24m辊道窑。设置升温区温度为880℃,通入富氧空气条件下(氧含量体积比为70%,气体输入量600nm3/h)将上述第一次烧结半成品粉料装入到陶瓷钵中进行烧结,烧结时间为8h,将物料隔离空气冷却至常温,称取进出物料的重量,统计烧失率为5.1%。然后用气旋涡流粉碎机进行粉碎,得到镍钴锰酸锂正极材料,材料的粒度(dv50)为8.5μm,比表面积为0.71m2/g。采用稀盐酸消解并经icp对正极材料的元素定量分析后结果核算发明物正极材料的化学式为li1.01ni0.81co0.10mn0.11y0.0006zr0.012o2,其中,掺杂元素为y,d为0.0006。实施例4选用500l陶瓷球磨机。开启搅拌(30rpm,聚氨酯球料与原料重量比1.3:1),在搅拌情况下加入100kg的镍钴铝前驱体(ni0.82co0.17al0.01(oh)2),再称取47.8kg单水氢氧化锂粉体加入到陶瓷球磨机中,在搅拌情况下添加0.16kg醋酸钴(钴含量以成品计钴含量为500ppm),以及0.42kg四水醋酸钇(钇含量以成品计钇含量为1100ppm),搅拌2h后进一步降低速度(10rpm)搅拌4h出料滤出聚氨酯球形成具有一定成型度的膏状物料备用。采用通气24m辊道窑。设置升温区温度为800℃,通入富氧空气条件下(氧含量体积比为70%,气体输入量600nm3/h)将上述膏状物料装入到陶瓷钵中进行烧结,烧结时间为8h,将物料隔离空气冷却至常温,称取进出物料的重量,统计烧失率为35.3%。然后用气旋涡流粉碎机进行粉碎,得到镍钴铝酸锂半成品正极材料,材料的粒度(dv50)为6.0μm,比表面积为0.61m2/g。将半成品再次投入到混合机中,向其中加入0.16kg经纳米氢氧化锆(按成品质量计锆元素含量为900ppm),经混合6.0h后取出物料重新装入陶瓷匣钵中,采用通气24m辊道窑。设置升温区温度为880℃,通入富氧空气条件下(氧含量体积比为70%,气体输入量600nm3/h)将上述第一次烧结半成品粉料装入到陶瓷钵中进行烧结,烧结时间为8h,将物料隔离空气冷却至常温,称取进出物料的重量,统计烧失率为5.1%。然后用气旋涡流粉碎机进行粉碎,得到镍钴铝酸锂正极材料,材料的粒度(dv50)为9.5μm,比表面积为0.93m2/g。采用稀盐酸消解并经icp对正极材料的元素定量分析后结果核算发明物正极材料的化学式为li1.02ni0.82co0.17al0.01y0.0005zr0.001o2,其中,掺杂元素为co和y,d为0.001。实施例5选用200l犁式混料机,开启搅拌(20rpm),在搅拌情况下加入100kg的镍钴锰前驱体(ni0.90co0.03mn0.07(oh)2),再称取44.8kg单水氢氧化锂粉体加入到犁式混料机中,在搅拌情况下添加0.09kg纳米二氧化钛溶液(钛含量以成品计钛含量为100ppm),以及0.09kg纳米氧化锆(锆含量以成品计锆含量为600ppm),搅拌2h后进一步降低速度(3-5rpm)搅拌4h出料形成具有一定成型度的膏状物料备用。采用通气24m辊道窑。设置升温区温度为400℃,通入富氧空气(氧含量体积比计为45%,气体输入量400nm3/h)条件下将上述膏状物料装入到陶瓷钵中进行第一次烧结,烧结时间为13h,将物料隔离空气冷却至常温,称取进出物料的重量,统计烧失率为39.1%。然后用气旋涡流粉碎机进行粉碎,粉碎时控制空气的湿度≤2%,得到第一次烧结半成品。将半成品再次投入到混合机中,向其中加入0.27kg磷酸锆(按成品质量计锆含量为850ppm),经混合6.0h后取出物料重新装入陶瓷匣钵中,采用通气24m辊道窑。设置升温区温度为700℃,通入富氧空气条件下(氧含量体积比计为70%,气体输入量200nm3/h)将上述第一次烧结半成品装入到陶瓷钵中进行第二次烧结,烧结时间为8h,将物料隔离空气冷却至常温,称取进出物料的重量,统计烧失率为3.6%。然后用气旋涡流粉碎机进行粉碎,得到具有最终制备物镍钴锰酸锂正极材料,材料的粒度(dv50)为13.0μm,比表面积为1.52m2/g。采用稀盐酸消解并经icp对正极材料的元素定量分析后结果核算发明物正极材料的化学式为li1.03ni0.90co0.03mn0.07ti0.0002zr0.001o2,其中,掺杂元素为ti和zr,d为0.0004。实施例6选用300ly型混合机,开启搅拌(35rpm),在搅拌情况下加入100kg的镍钴锰前驱体(ni0.80co0.11mn0.09(oh)2),再称取42.3kg碳酸锂粉体加入到混合机中,在搅拌情况下按80wt%固含量添加38kg去离子水,以及0.25kg氢氧化亚钴(含量以成品计钴含量为1500ppm),0.34kg四水醋酸钇(含量以成品计钇含量为850ppm),搅拌2h后进一步降低速度(3-5转/min)搅拌2h出料形成具有一定成型度的膏状物料备用。采用通气24m辊道窑。设置升温区温度为500℃,通入富氧空气(氧含量体积比计为45%,气体输入量400nm3/h)条件下将上述膏状物料装入到陶瓷钵中进行第一次烧结,烧结时间为15h,将物料隔离空气冷却至常温,称取进出物料的重量,统计烧失率为35.6%。然后用气旋涡流粉碎机进行粉碎,粉碎时控制空气的湿度为2%,得到第一次烧结半成品。将半成品再次投入到混合机中,向其中加入0.40kg五水硝酸锆(按成品质量计锆含量为830ppm),经混合6.0h后取出物料重新装入陶瓷匣钵中,采用通气24m辊道窑。设置升温区温度为700℃,通入富氧空气条件下(氧含量体积比计为50%,气体输入量600nm3/h)将上述第一次烧结半成品装入到陶瓷钵中进行第二次烧结,烧结时间为8h,将物料隔离空气冷却至常温,称取进出物料的重量,统计烧失率为2.9%。然后用气旋涡流粉碎机进行粉碎,得到具有最终制备物镍钴锰酸锂正极材料,材料的粒度(dv50)为10.0μm,比表面积为0.32m2/g。采用稀盐酸消解并经icp对正极材料的元素定量分析后结果核算发明物正极材料的化学式为li1.02ni0.80co0.11mn0.09y0.001zr0.001o2,其中,掺杂元素为co和y,d为0.003。实施例7物料混合:选用400l捏合机。开启搅拌(转速30rpm),在搅拌情况下加入100kg的镍钴铝前驱体ni0.80co0.15al0.04(oh)2(粒度dv50:8μm,有效物含量99.5%),再按li/(ni+co+al)摩尔比=1.06称取43.1kg碳酸锂粉体(粒度dv50:3.5μm,有效物含量99.8%),以及0.129kg醋酸钴(化学纯,纯度98.0%,含量以成品计钴含量为400ppm),搅拌50min后进一步降低速度(20rpm)搅拌20min出料密封备用。一次烧结:采用与实施例1相同的方法进行一次烧结,实施例7烧失率以原料计为33.8%。粉碎:用气旋涡流粉碎机进行粉碎(分级轮线速度为35m/s),得到具有一定晶体结构的第1次烧结半成品。将半成品再次投入到400l捏合机。开启搅拌(转速25rpm),在搅拌情况下加入0.074kg纳米氢氧化锆(陶瓷级,纯度98.0%,含量以成品计锆含量为400ppm)加入到捏合机中,充分搅拌后制备得到篷松的粉状物料。二次烧结:采用与实施例1相同的方法进行二次烧结,实施例7烧失率以原料计为0.9%。粉碎:用气旋涡流粉碎机进行粉碎(分级轮线速度为45m/s),得到锆包覆的镍钴铝酸锂正极材料。材料的粒度(dv50)为8.1μm,比表面积为2.3m2/g。采用稀盐酸消解并经icp检测核算得到发明物正极材料化学式为li1.06ni0.80co0.15al0.04zr0.04o2,其中,掺杂元素为co,d为0.001。对比例对比例1与本发明实施例1类似,区别仅在于,在第2次混过程中不添加五水硝酸锆,并按同样的步骤制备正极材料。对比例2与本发明实施例1类似,区别仅在于,在第2次混过程中不添加二氧化锆,并按同样的步骤制备正极材料。对比例3与本发明实施例3类似,区别仅在于,在第2次混过程中不添加正丙醇锆溶液,并按同样的步骤制备正极材料。对比例4与本发明实施例4类似,区别仅在于,在第2次混过程中不添加纳米氢氧化锆粉末,并按同样的步骤制备正极材料。对比例5与本发明实施例5类似,区别仅在于,在第2次混过程中不添加磷酸锆,并按同样的步骤制备正极材料。对比例6与本发明实施例6类似,区别仅在于,在第2次混过程中不添加五水硝酸锆,并按同样的步骤制备正极材料。对比例7与本发明实施例7类似,区别仅在于,在第2次混过程中不添加氢氧化锆,并按同样的步骤制备正极材料。对比例8与本发明实施例1类似,区别仅在于,在第2次混过程中不添加五水硝酸锆,而添加0.13kg的碱式碳酸钴,并按同样的步骤制备正极材料。实施例8扫描电镜sem图将上述实施例4,对比例4制备得到的正极材料粉体分别进行扫描电镜sem测试,得到图1,图2。由图1、图2可见,采用本发明技术制备的样品一次颗粒生长均匀(粒径约200-400nm),且二次颗粒球型度较好,表面干净光滑,表面锆元素与高镍三元材料结合紧密,锆元素均匀的包覆于材料表面,而对比例制备的材料小颗粒较多,且一次颗粒有大有小(600-800nm),有不少不规整的颗粒。实施例9堆积角检测取实施例和对比例制得的正极材料粉体各约200g,参考gbt6609.24-2004物理性能安息角的测定,采用ft-104a氧化铝/氟化铝安息角测定仪,在干燥房内,向不锈钢漏斗(上内径74mm、下料口内径6mm两档板间装有孔径为1mm的筛网)中倒入200g粉料。物料经漏斗口自然洒落在抛光电镀的底板上。通过测量堆积本的高度再经换算得到物料的堆积角(安息角)。上述实施例的堆积角结果如表3所示。表3实施例堆积角测试结果实施例放完时间(s)堆积角(°)堆垛形状实施例11333.22光滑锥形实施例21432.39光滑锥形实施例31233.23光滑锥形实施例41536.11光滑锥形实施例51535.05光滑锥形实施例61334.59光滑锥形实施例71535.79光滑锥形对比例12539.92不光滑锥形对比例22139.14不光滑锥形对比例32741.19不光滑锥形对比例42843.31不光滑锥形对比例52740.78不光滑锥形对比例62639.38不光滑锥形对比例72943.8不光滑锥形对比例81745.12不光滑锥形由表3可见,采用本发明制备的材料下料顺畅,下料时间较对比例短50%左右,堆积体外形为光滑的锥形,表明物料比较“滑爽”,对比例形成的锥体不光滑,物料在自然下落的过程中因为相互作用导致局部流动性不好出现堆积,且堆积角普遍较大,要保证这样的物料自然流动,则相应的罐体锥体部分需要加长加高,增加了设备成本和维护成本。通过堆积角的测量可明显发现掺锆的方式明显有利于粉体的流动性,有利于高镍三元正极材料的制备加工。实施例10全电池制备及性能评估将实施例5至实施例7,对比例5至对比例7制备得到的6个正极材料粉体作为正极活性物质按21700圆柱电池设计制备成容量为4.8-5.2ah左右动力电池,设计时以圆柱电池具有相同的容裕度为标准(即圆柱电池中有效物质占的体积与圆柱电池的总封闭有效容积百分比,通常为96%左右)。制作全电池主要用于考察高电压循环及安全性效果。其中所评估适用的品种为卷绕结构21700型钢壳电池,制作的电池直径为21mm,高度为70mm。正极极片制备通常由制备浆料,涂布及冷压,分切等工艺制成,极片中有效正极活性物质含量为97.5%,极片涂布平均重量为0.0260g/cm3,极片涂布宽度为62mm,极片活性物质总面积为937.4cm2,铝箔基材厚度为13μm,极片压实密度以活性物质计为3.2g/cm3。负极片的制备方法通常经由制备浆料,涂布,冷压,分切等工序制备。采用人造石墨作为负极活性物质时,制备后的极片有效负极活性物质(人造石墨)含量为96.0%,极片涂布重量为0.0164g/cm2,极片涂布宽度为63.5mm,极片活性物质总面积为1009.65cm2,铜箔基材厚度为9μm,极片压实密度以活性物质计为1.65g/cm3。将焊接有铝极耳的正极片,隔离膜(为经纳米氧化铝处理的厚度为16μm的pp/pe/pp复合隔离膜),焊接有镍极耳的负极片等按顺序卷绕制备成圆柱裸电芯,并将极耳套上绝缘环后入壳,采用激光焊接将镍极耳焊接在筒底部,然后经卷曲制备成具有凹槽的裸电芯,经干燥后冷却注液,并在将极耳依次焊接上cid,ptc及vent等保护构件,封装静置后在lip-10ahb06型高温化成机化成(化成电压0~4.2v,0.1c充电,0.2c放电,温度45℃±2℃),进行容量测试(测试电压3.0~4.2v,0.2c,0.5c),挑选质量合格的电芯用于后续性能评估。将上述锂电池按ul-1642进行侧压试验,先将锂电池满充至4.2v,测试开路电压及内阻,再将锂电池放置于两块平板之间开始以一定速度挤压电池直至压力传感器的上限值达到13kn为止,再松开压紧装置,测试锂电池因内短路引起的温升及其他结果,电池未出现冒烟,起火及电解质泄漏视为通过了挤压测试。将上述实施例进行测试得到如表4及图3所示的代表性结果。表4实施例及对比例钉刺结果由表4可见,实施例5,6通过了钉刺测试,实施例7及对比例5,对比例6,对比例7均发生了燃烧等现象,未通过钉刺测试,从概率上讲,实施例较对比例更易通过钉刺测试,其原因在于表面包覆了锆的高镍材缺陷较少,或者是以电解质的接触面比较友好,有利于抑制意外滥用情况下锂离子电池的安全性能,表明包覆了锆的高镍三元正极材料综合性能更好,达到了继提升高镍三元材料加工性能,又提升了高镍三元材料电化学性能的目的。以上通过实施例描述了本发明的具体实施方式,本领域技术人员应理解的是,上文实施例仅出于举例的目的,不应认为以此限定本发明之保护范围,本领域技术人员在不脱离本发明精神的前提下可以对其进行修改、变化或替换,但是,依照本发明所作的各种等同变化,仍属于本发明所涵盖的范围。综上所述,本发明所述高镍三元正极材料在添加锆源后在材料表面形成了稳定均一的体相掺杂层,可避免正极材料在后期使用过程中粉体出现团聚结块,从而有利于高镍三元正极材料的加工使用,同时提升了锂电池的安全性能。本发明所述制备方法经济可行,操作简单,效果明显,具有较好的应用前景。当前第1页12