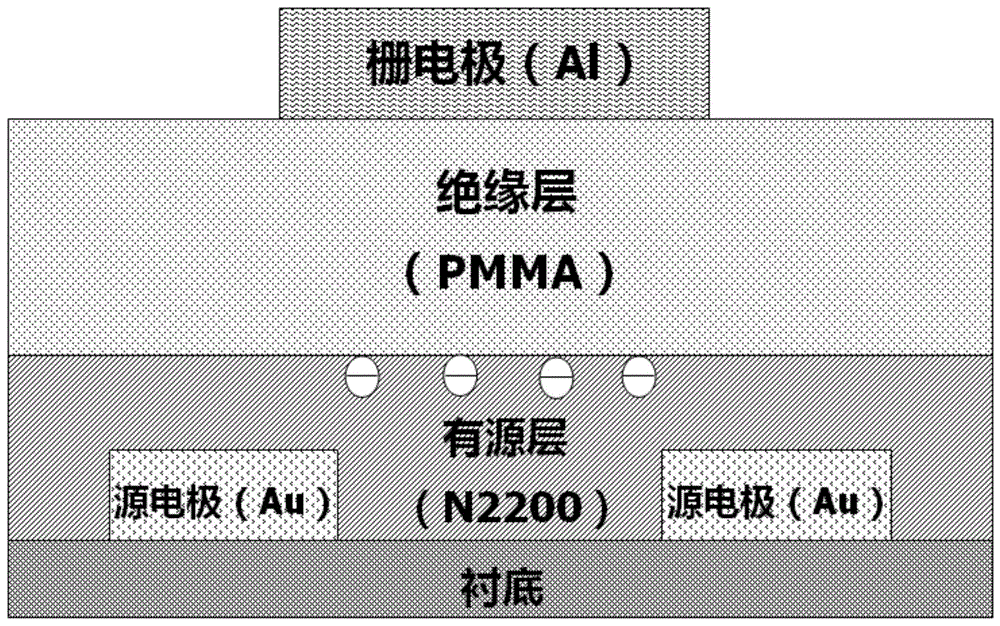
本发明涉及微电子材料与器件技术和信息显示等领域,尤其是一种铟掺杂N型有机薄膜晶体管及其制备方法。
背景技术:
:使用有机半导体作为薄膜晶体管中的有源层在近三十年来获了广泛的关注,以共轭聚合物、低聚合物和融合芳烃作为半导体材料的有机薄膜晶体管相对于采用无机半导体的场效应晶体管有特殊的优势,例如可用于大面积、柔性、低温加工(接近室温)、低成本和透明的新型薄膜晶体管的制作。有机薄膜晶体管可应用于有源矩阵平面显示、有机电致发光二极管和“电子纸”显示以及可贴式传感器、无线射频识别标签等领域。由于有机半导体材料电子难以注入,且极易受空气中水分和氧气的干扰,N型有机半导体材料的发展远落后于P型有机半导体材料。P型有机晶体管相较于N型有机晶体管,有更高的开关比与迁移率,以及更低的亚阈值摆幅、阈值电压和接触电阻。然而,具有高迁移率、空气稳定、可溶液法制备的N型半导体材料极为短缺,大大限制了以有机薄膜晶体管为基础的柔性电子器件及有机集成电路的发展。制备性能优良的N型有机薄膜晶体管是有机薄膜晶体管发展的至关重要的一步。国际上普遍采用对有机半导体材料进行分子结构改变或者化学元素替换的方法改善N型有机半导体的性能,这些方法能够使N型有机薄膜晶体管电学性能接近于P型有机薄膜晶体管电学性能,且工艺简单、成本低廉、适用性广泛,大大推动了N型有机薄膜晶体管的发展。技术实现要素:有鉴于此,本发明提供了一种铟掺杂N型有机薄膜晶体管及其制备方法。其制备方法适用的有机薄膜晶体管为顶栅底接触结构,晶体管由上至下依次是栅极、介电层、N型半导体有源层、源/漏电极以及衬底。该方法在有机薄膜晶体管制备源/漏电极完毕后,通过掩膜版对准方式,在源/漏电极表面形成一层掺杂层,通过该掺杂层对N型有机薄膜晶体管实现接触掺杂,提高了N型有机薄膜晶体管的电学性能。本发明提供的一种铟掺杂N型有机薄膜晶体管的制备方法,包括以下具体步骤:步骤1:溶液的制备A1:半导体溶液的配置将N型有机半导体材料与有机溶剂以8mg/ml的质量体积比进行配置;其中,所述N型有机半导体材料为:[N,N’-双(2-辛基十二烷基)-1,4,5,8-萘二酰亚胺-2,6-双基-并-5,5’-(2,2’-双噻吩)]聚合物(N2200);所述有机溶剂为氯苯或对二氯苯;A2:绝缘层溶液的配置将绝缘层材料与高溶解性的有机溶剂以80mg/ml的质量体积比进行配置;其中,所述绝缘层材料为高分子聚合物;所述高溶解性的有机溶剂为乙酸或乙酸甲酯;A3:溶液的溶解将配置的半导体溶液与绝缘层溶液分别放在加热板上60℃静置溶解24小时;步骤2:器件的制备B1:衬底的清洗选择绝缘衬底,将衬底依次放置于去离子水、丙酮、酒精中,分别用超声清洗机清洗10分钟,然后用氮气枪吹干;B2:源漏电极的制备采用真空热蒸发镀膜技术,在真空10-5~10-4Pa条件下,利用不锈钢掩膜版在衬底上蒸镀厚度为30纳米的金作为源漏电极;其中,热蒸镀电流为100-160A,速率为0.01-0.05nm/s;B3:掺杂层的制备采用真空热蒸发镀膜技术,在真空10-5~10-4Pa条件下,利用不锈钢掩膜版在源漏电极表面上蒸镀厚度为5~15纳米的铟作为掺杂层;其中,热蒸镀电流为60-100A,速率为0.01-0.02nm/s。B4:半导体薄膜的制备通过移液枪将已配置好的半导体溶液在衬底上表面铺满,采用旋涂仪在500rpm的转速下匀胶5秒,再在2000rpm的转速下匀胶40-80秒;在纯氩气环境下,将本步骤中旋涂半导体层完毕的样品放置于加热板上以110℃加热退火20分钟;制备的半导体薄膜厚度范围为35~45纳米,即为有源层。B5:绝缘层薄膜的制备通过移液枪将已配置好的绝缘层溶液在半导体薄膜上表面铺满,采用旋涂仪先在500rpm的转速下匀胶5秒,再在2000rpm的转速下匀胶60秒;在纯氩气环境下,将本步骤中旋涂绝缘层完毕的样品放置于加热板上以80℃加热退火2小时;B6:栅极的制备通过光学显微镜的校准,使不锈钢掩膜版的开口位置与源极和漏极之间的沟道对应,再利用真空热蒸发镀膜技术在绝缘层上表面制备厚度为60纳米的铝作为栅电极,得到所述铟掺杂N型有机薄膜晶体管。步骤A2中,所述高分子聚合物为聚甲基丙烯酸酯、聚苯乙烯或全氟(1-丁基乙烯醚)聚合物,与水具有至少90度接触角。步骤B1中,所述绝缘衬底为玻璃、二氧化硅或聚对苯二甲酸类塑料。该方法所制备的有机薄膜晶体管相较于传统有机薄膜晶体管,其器件开关比和载流子迁移率得到了明显的提升,器件的亚阈值摆幅和阈值电压大幅减小。本发明提升了顶栅底接触结构的N型有机薄膜晶体管的电学性能,具有成本低廉、工艺步骤简单以及广泛适用于N型有机薄膜晶体管的特点。附图说明图1为对比例N型有机薄膜晶体管的截面结构示意图;图2为本发明所述方法制备的铟掺杂N型有机薄膜晶体管的截面结构示意图;图3为未掺杂的传统方法以及本发明方法所制备的N型有机薄膜晶体管的转移特性曲线对比图。具体实施方式本发明通过传统电极制备工艺,在掩膜版的自对准下在电极的上表面制备出一层厚度可控且致密的铟掺杂层。铟因为其较低的功函数,能够有效地减小源漏电极与N型有机半导体接触形成的肖特基势垒高度,有利于电子在界面间的传输,且铟能够在不破坏半导体有源层分子结构的前提下,对半导体有源层进行电子掺杂,增大N型有机半导体薄膜的载流子浓度,从而使得有机薄膜晶体管的开关比、迁移率得到显著提高,且其亚阈值摆幅与阈值电压都显著减小。因此通过本发明,可使得N型有机薄膜晶体管的电学性能大幅提升。下面结合附图及实施例对本发明进一步说明。以下本发明提供优选实施例,但不应该被认为仅限于在此阐述的实施例,凡依本发明申请范围所做的均等变化与修饰,皆应属本发明的涵盖范围。图2是本发明的理想化实施例的示意图,本发明所示的实施例不应该被认为仅限于图中所示的区域的特定形状。在本实施例中均以矩形表示,图中的表示是示意性的,但这不应该被认为限制本发明的范围。对比例未掺杂的传统有机薄膜晶体管制备A1:半导体溶液的配置将N型有机半导体材料与有机溶剂以8mg/ml的质量体积比进行配置;其中,所述N型有机半导体材料为:[N,N’-双(2-辛基十二烷基)-1,4,5,8-萘二酰亚胺-2,6-双基-并-5,5’-(2,2’-双噻吩)]聚合物(N2200);所述有机溶剂为氯苯;A2:绝缘层溶液的配置将绝缘层材料与高溶解性的有机溶剂以80mg/ml的质量体积比进行配置;其中,所述绝缘层材料为聚甲基丙烯酸酯(PMMA);所述高溶解性的有机溶剂为乙酸甲酯;A3:溶液的溶解将配置的半导体溶液与绝缘层溶液分别放在加热板上60℃静置溶解24小时;步骤2:器件的制备B1:衬底的清洗选择绝缘衬底,将衬底依次放置于去离子水、丙酮、酒精中,分别用超声清洗机清洗10分钟,然后用氮气枪吹干;B2:源漏电极的制备采用真空热蒸发镀膜技术,在真空条件下(10-4Pa)利用不锈钢掩膜版在衬底上蒸镀厚度为30纳米的金作为源漏电极;其中,热蒸镀电流为100-160A,速率为0.01-0.05nm/s;B3:半导体薄膜的制备通过移液枪将已配置好的半导体溶液在衬底上表面铺满,采用旋涂仪在500rpm的转速下匀胶5秒,再在2000rpm的转速下匀胶40-80秒;在纯氩气环境下,将本步骤中旋涂半导体层完毕的样品放置于加热板上以110℃加热退火20分钟;制备的半导体薄膜厚度范围为35~45纳米,即为有源层。B4:绝缘层薄膜的制备通过移液枪将已配置好的绝缘层溶液在半导体薄膜上表面铺满,采用旋涂仪先在500rpm的转速下匀胶5秒,再在2000rpm的转速下匀胶60秒;在纯氩气环境下,将本步骤中旋涂绝缘层完毕的样品放置于加热板上以80℃加热退火2小时;B5:栅极的制备通过光学显微镜的校准,使不锈钢掩膜版的开口位置与源极和漏极之间的沟道对应,再利用真空热蒸发镀膜技术在绝缘层上表面制备厚度为60纳米的铝作为栅电极,得到传统N型有机薄膜晶体管。如图1所示,图1为依照对比例制备的传统N型有机薄膜晶体管的截面结构示意图。实施例A1:半导体溶液的配置将N型有机半导体材料与有机溶剂以8mg/ml的质量体积比进行配置;其中,所述N型有机半导体材料为:[N,N’-双(2-辛基十二烷基)-1,4,5,8-萘二酰亚胺-2,6-双基-并-5,5’-(2,2’-双噻吩)]聚合物(N2200);所述有机溶剂为氯苯;A2:绝缘层溶液的配置将绝缘层材料与高溶解性的有机溶剂以80mg/ml的质量体积比进行配置;其中,所述绝缘层材料为聚甲基丙烯酸酯(PMMA);所述高溶解性的有机溶剂为乙酸甲酯;A3:溶液的溶解将配置的半导体溶液与绝缘层溶液分别放在加热板上60℃静置溶解24小时;步骤2:器件的制备B1:衬底的清洗选择绝缘衬底,将衬底依次放置于去离子水、丙酮、酒精中,分别用超声清洗机清洗10分钟,然后用氮气枪吹干;B2:源漏电极的制备采用真空热蒸发镀膜技术,在真空条件下(10-4Pa)利用不锈钢掩膜版在衬底上蒸镀厚度为30纳米的金作为源漏电极;其中,热蒸镀电流为100-160A,速率为0.01-0.05nm/s;B3:掺杂层的制备采用真空热蒸发镀膜技术,在真空条件下(10-4Pa)利用不锈钢掩膜版在源漏电极表面上蒸镀厚度为5~15纳米的铟作为掺杂层;其中,热蒸镀电流为60-100A,速率为0.01-0.02nm/s。B4:半导体薄膜的制备通过移液枪将已配置好的半导体溶液在衬底上表面铺满,采用旋涂仪在500rpm的转速下匀胶5秒,再在2000rpm的转速下匀胶40-80秒;在纯氩气环境下,将本步骤中旋涂半导体层完毕的样品放置于加热板上以110℃加热退火20分钟;制备的半导体薄膜厚度范围为35~45纳米,即为有源层。B5:绝缘层薄膜的制备通过移液枪将已配置好的绝缘层溶液在半导体薄膜上表面铺满,采用旋涂仪先在500rpm的转速下匀胶5秒,再在2000rpm的转速下匀胶60秒;在纯氩气环境下,将本步骤中旋涂绝缘层完毕的样品放置于加热板上以80℃加热退火2小时;B6:栅极的制备通过光学显微镜的校准,使不锈钢掩膜版的开口位置与源极和漏极之间的沟道对应,再利用真空热蒸发镀膜技术在绝缘层上表面制备厚度为60纳米的铝作为栅电极,得到所述的铟掺杂N型有机薄膜晶体管。如图2所示,图2为本实施例制备的铟掺杂N型有机薄膜晶体管的截面结构示意图;图3为分别为对比例与实施例所得有机薄膜晶体管的饱和区转移特性曲线对比图。参阅图3可得,实施例制备的晶体管其饱和区转移特性曲线有非常大的改善。为详细统计其具体电学参数的改变,表1列出了两种器件的开关比、迁移率、亚阈值摆幅以及阈值电压等电学参数。对于未掺杂的传统有机薄膜晶体管,其开关比为104、迁移率为0.116平方厘米/(伏特·秒)、亚阈值摆幅为2.67伏特/单位数量级、阈值电压为7.25伏特,而对于掺杂后的有机薄膜晶体管,其开关比为2×105、迁移率为0.356平方厘米/(伏特·秒)、亚阈值摆幅为0.87伏特/单位数量级、阈值电压为0.18伏特。因此,从四个晶体管核心电学参数指标可以观察到,经本发明制备的N型有机薄膜晶体管的电学性能都得到了显著提升,对N型有机薄膜晶体管的进一步发展,有非常重要的意义。铟掺杂层对源/漏电极与N型半导体有源层的接触调节作用和对N型有机半导体的电子注入作用是促使晶体管性能优化的主要原因。实际上,具有高迁移率、空气稳定、可溶液法制备的N型半导体材料极为短缺,未掺杂的传统N型有机薄膜晶体管的性能明显落后于P型有机薄膜晶体管,大大限制了以有机薄膜晶体管为基础的柔性电子器件及有机集成电路的发展。而经过本发明方法掺杂后的N型有机薄膜晶体管,其电极表面功函数接近N型有机半导体的LUMO能级,从而降低了源漏电极与半导体间的肖特基势垒,有利于电子漂移;且铟对于半导体具有电子掺杂注入的作用,从而增大了沟道中的载流子浓度,使得N型有机薄膜晶体管的电学性能得到了显著的提升。参阅表1可得,通过本发明制备的晶体管开关比为传统方法制备的器件的20倍,载流子迁移率提高到传统器件的3倍,且其亚阈值摆幅与阈值电压都得到了明显的减小。因此,通过本发明,可以解决N型有机薄膜晶体管性能远落后于P型有机薄膜晶体管性能的问题,大幅度提升其各项电学性能,对实现有机薄膜晶体管的大规模商业应用,有非常重要的意义。表1有机薄膜晶体管电学参数掺杂前掺杂后开关比1042×105迁移率(平方厘米/(伏特·秒)0.1160.356亚阈值摆幅(伏特/单位数量级)2.670.87阈值电压(伏特)7.251.18当前第1页1 2 3