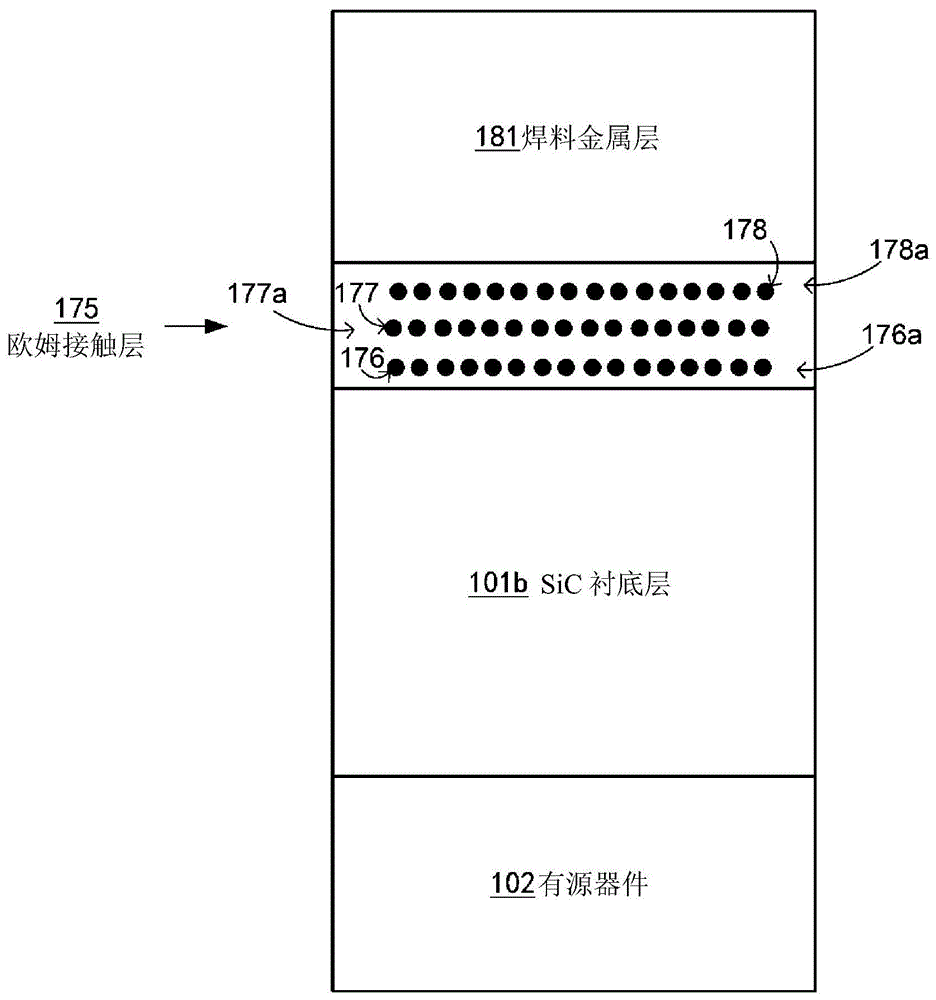
本说明书涉及碳化硅大功率半导体器件。
背景技术:
:碳化硅(sic)功率器件、特别是碳化硅大功率器件提供诸如高开关速度和低功率损耗的优点。高效sic功率器件的示例包括(但不限于)整流器、场效应晶体管(fet)和双极性结型晶体管(bjt)。多种物理特性引起了碳化硅大功率器件的各种优点,诸如其雪崩击穿的高临界场。因此,例如,800v与4500v之间的高电压可在例如大约4μm与35μm之间的极薄层内阻断。机械稳定性考虑因素在至少一些处理环境期间决定至少大约300至500μm之间的典型sic衬底厚度,但从电器件功能的角度来看,此类厚度可高于所需厚度。即,例如,过厚的衬底的电阻和热阻倾向于影响sic大功率器件的性能。为了减轻此类影响,可以对sic衬底的至少一部分执行减薄。正如刚才提及的,此类减薄的sic衬底在例如用于形成有源器件结构的顶侧半导体工艺期间可能不是优选或可行的。具体地讲,薄于大约280μm的150mm或更大sic衬底可能与晶圆制造环境中的前端sic器件处理不兼容。相反,可在顶侧有源结构完成(或几乎完成)的阶段执行晶圆减薄。因此,减薄后的晶圆工艺可限于特定操作,诸如欧姆接触形成,后接焊料金属的沉积。为实现所需欧姆行为和低接触电阻而对背侧接触的退火可在此类场景中使用脉冲能量源(诸如具有数纳秒到数百纳秒的脉冲持续时间的脉冲激光)进行。然后接触退火可后接焊料金属堆叠的沉积。sic的具体特征是欧姆接触形成通常需要大约850c与1050c之间的温度。这对于形成硅化镍(nisix)接触而言尤其如此,该硅化镍(nisix)接触提供低电阻率和良好工艺稳定性。能够以与在硅上形成硅化镍类似的方式,通过sic与金属镍的反应来在碳化硅上形成硅化镍。在碳化硅上,该反应伴随过量碳的释放,该碳的一部分被捕获在sic与nisix的分界面处,并且该碳的一部分扩散到硅化物中而在硅化物的本体中以及在硅化物的自由表面上形成碳团簇。俘获在sic/nisix分界面处的碳据报告具有多层石墨烯的结构,并且有利地形成具有对sic的低势垒的分界面。因此,碳对sic的该低势垒被认为会引起sic上的nisix接触的所需欧姆特性或与这些所需欧姆特性相关。然而,过量碳产生及其在硅化物内的分布可导致许多问题和困难。例如,此类问题和困难可包括由熔炉或由快速热处理(rtp)退火形成的接触的金属粘附不良(以及所得的接触缺乏稳定性)。技术实现要素:在以下公开内容中,公开了适用于利用减薄的sic衬底来实现sic功率器件的脉冲激光退火背侧接触层的可靠形成的技术。正如所述,适用性已例如通过对实际接触组成的研究以及对完全处理、切块且封装的sic功率器件的可靠性测试来验证。本公开描述了能够提供阻断电压与通态电阻的接近理论组合的器件。竖直非注入功率器件的通态比电阻rspon的限值由漂移区域的电阻设定。对于非穿通型器件而言,该数值是rspon=4bv2/(ε*μ*ec3),其中bv是击穿电压,ε是半导体的绝对电容率,μ是载流子迁移率,并且ec是雪崩击穿的临界场。因此大功率整流器可被理解为包括比电阻不超过rspon理论值10倍的器件。而具有较高比电阻的器件对大功率转换的使用可受到高度限制。比电阻rspon在其传统定义上应被理解为例如通态整流器或开关的微分电阻乘以有源器件面积(即,乘以器件单位单元的总面积)。就大功率应用而言,额定电流在此类场景中可限于约4a与10a之间的最小电流以上的域。可实现具有较低电流额定值的一些高电压整流器,但此类小面积功率器件通常是主流大功率器件的按比例缩小的型式。本公开还涉及额定值为至少约600v的高阻断电压的器件。根据一个一般方面,半导体功率器件可包括在其第一表面上形成有功率器件(诸如有源功率器件)的碳化硅(sic)层。半导体功率器件可包括在sic层的第二相对表面上形成的欧姆接触层。欧姆接触层可包括具有第一硅化物区域的硅化镍(nisix),该第一硅化物区域包含第一未反应的碳的析出物并且设置在sic层与第二硅化物区域之间。第二硅化物区域可设置在第一硅化物区域与第三硅化物区域之间,并且可包含第一难熔金属碳化物的析出物和第二未反应的碳的析出物的混合物。第三硅化物区域可包含第二难熔金属碳化物的析出物。半导体功率器件可包括在欧姆接触层上形成的至少一个焊料金属层,其中第三硅化物区域设置在第二硅化物区域与所述至少一个焊料金属层之间。在一些实施方式中,第三硅化物区域中的碳包含在第三硅化物区域与所述至少一个焊料金属层的至少百分之五十接触区域内的第二难熔金属碳化物的析出物内。在一个或多个此类半导体功率器件的一些实施方式中,第一未反应的碳的析出物和第二未反应的碳的析出物可包含在硅化形成nisix期间从sic层释放的碳。此外,第一难熔金属碳化物析出物和第二难熔金属碳化物析出物可包括在欧姆接触层的形成期间与镍包含在一起的第一难熔金属的析出物以及第二难熔金属的析出物。一个或多个实施方式的细节在附随附图和以下描述中阐明。其他特征将从说明书和附图中以及从权利要求书中显而易见。附图说明图1a是sic功率器件的示意性横截面。图1b是图1a的sic功率器件的半处理型式的第一示意性横截面。图1c是图1a的sic功率器件的半处理型式的第二示意性横截面。图1d是图1a的sic功率器件的半处理型式的第三示意性横截面。图1e是图1a的sic功率器件的半处理型式的第四示意性横截面。图1f是图1a的sic功率器件的半处理型式的第五示意性横截面。图1g是图1a的sic功率器件的半处理型式的第六示意性横截面。图2是曲线图,示出了随管芯数而变化的参考工艺的热机械循环之后的正向电压降漂移。图3是流程图,示出了用于形成图1a-1g的一个或多个半导体功率器件的第一示例性实施方案。图4是流程图,示出了用于形成图1a-1g的一个或多个半导体功率器件的第二示例性实施方案。图5是流程图,示出了用于形成图1a-1g的一个或多个半导体功率器件的第三示例性实施方案。图6示出了所研究的4个晶圆的平均bv对平均vf的相依性的趋势线。图7a示出了根据参考工艺形成的激光退火nisix接触的示意性横截面。图7b示出了图7a的根据参考工艺形成的激光退火nisix接触的电子显微照片。图7c示出了图7a的根据参考工艺形成的激光退火nisix接触的组成。图8a示出了根据一个示例性实施方案的使用碳吸除形成的激光退火nisix接触的电子显微照片。图8b示出了根据图8a的示例性实施方案的使用碳吸除形成的激光退火nisix接触的组成。图8c示出了对于图8a和图8b的示例性实施方案而言镍、碳、钒、硅和钛的硅化镍接触的元素对比扫描透射电子显微图像。图9示出了根据一个示例性实施方案的nisix接触的电子显微照片。图10示出了图9的实施方案的欧姆接触组成的高分辨率扫描。具体实施方式图1a是sic功率器件结构。在图1a中,sic衬底层101b被示出为在其第一表面上形成有有源器件102。如上文所提及并且如下文相对于图1b所描述和示出,sic层101b可表示初始较厚sic衬底层101a的减薄层。从术语上讲,其上形成有有源器件102的sic层101b的第一表面也可被称为前侧或顶侧表面。同时,在sic层101b的第二相对表面上形成欧姆接触层175,因此该第二相对表面可被称为背侧或底表面。如下文详细描述,背侧欧姆接触层175可表示在sic层101b上形成的硅化物,诸如硅化镍或硅化镍钒。如本文所述,使用来自sic层101b的硅形成这种硅化物通常也将伴随sic层101b中存在的碳的释放和潜在扩散。在图1a中,背侧欧姆接触层175被构造有第一硅化物区域176a,其中从sic层101b释放的碳析出物176位于sic与欧姆接触层175的硅化物的分界面附近(即,位于sic层101b的背侧表面附近)。如本文所述,第一硅化物区域的碳析出物176可采取石墨烯和/或石墨的形式,并且有利地用于降低sic层101b与背侧欧姆接触层175的硅化物之间的分界面处的接触电阻。在各种实施方式中,第一硅化物区域176a包含很少或不包含难熔金属碳化物析出物。此外,第二硅化物区域177a包含金属碳化物析出物和未反应的碳的附加析出物的混合物177。混合物177的金属碳化物析出物可通过难熔金属(诸如钛)与已从sic层101b扩散的碳的组合并通过第一硅化物区域176a来形成。在该上下文中,未反应的碳是指在硅化期间尚未与难熔金属反应的碳,并且也可被称为游离碳。进一步就背侧欧姆接触层175而言,第三硅化物区域178a被示出为与一个或多个焊料金属层181相邻并且电接触。如图所示,第三硅化物区域178a一般不应包含未反应的碳的析出物。具体地讲,第三硅化物区域178a可包含过量碳;然而,任何此类过量碳应完全结合或接近完全结合到接触区域的主要部分上的难熔金属碳化物析出物178中。例如,难熔金属碳化物析出物178可在至少百分之五十接触区域内出现。在其他实施方式中,该百分比可大于75%、90%或95%。类似地,在各种示例性实施方式中,具有游离碳(例如,未反应的碳的析出物)的接触区域的百分比可小于50%、20%、10%或5%。因此,第三硅化物区域178a提供具有相对于一个或多个焊料金属层181的优异粘附特性的表面。如下文详细描述,一个或多个可焊金属层因此能够承受高度的热应力和机械应力,同时保持与背侧欧姆接触层175的物理接触和电接触。从术语上讲,术语析出物应被理解为涉及并包括一种或多种相关材料的任何团簇、分散、微晶或非连续分布。例如,混合物177的金属碳化物析出物和金属碳化物析出物178可表示碳化钛(tic)的非连续分布,其由已与从sic层101b扩散并穿过第一硅化物区域176a进入第二硅化物区域177a和第三硅化物区域178a的碳发生反应的(至少部分)熔化的钛形成。因此,来自sic层101b的硅一般自由地或能够穿过第二硅化物区域177a移动到第三硅化物区域178a中,从而获得背侧欧姆接触层175的完全且高质量的硅化。包括图1a的目的是为了示出和描述本文描述并要求保护的sic半导体功率器件的一般结构和一些相关联的特征。应当理解,图1a并非旨在或表示对任何特定器件或器件类型或其部分按比例绘制。图1a的元件的相关尺寸、厚度和其他物理参数的具体示例在下文提供,或对于本领域技术人员而言将是显而易见的。因此,图1a的一般结构以及用于制备这种结构和相关结构的各种技术(其中一些技术在本文中有所描述)可用于例如任何相关功率sic器件。在本说明书(包括相对于以下图1b至图1g)中,在碳化硅肖特基二极管整流器的上下文中提供具体示例。因此,在图1b至图1g中,此类整流器可被理解为提供图1a的有源器件102的示例,该有源器件先形成在sic衬底101a的顶侧上,再对其进行减薄而获得sic衬底层101b。在具体测试示例中,所得的二极管晶圆被机械地减薄到200μm或100μm的总sic晶体厚度。使用ni-v层及顶部上的ti层的沉积来执行晶圆背侧处的欧姆接触制备。使用波长为532nm的脉冲绿激光来使所得的背侧接触退火,之后沉积附加niv层并使之激光退火,从而得到具有所述硅化物区域176a-178a的欧姆接触层175。然后在欧姆接触金属的顶部上沉积焊料金属,该焊料金属表示一个或多个焊料金属层181的示例,并包含ti/ni/ag的堆叠。硅化镍组成的研究已表明形成了难熔金属碳化物177,以及在nisix与焊料金属的分界面附近(即,在第三硅化物区域178a中)不存在碳析出物。相比之下,激光烧结纯ni或镍-钒已显示出焊料金属对硅化镍的不合标准的粘附。例如,由于因nisix与焊料金属的分界面附近的过量碳含量所引起的焊料金属的剥离,故而发生了故障。因此,已展示了本文所述工艺和结构与参考工艺/结构的比较,从而显示出从所得sic功率器件的可靠性视角来看非常明显的优点。在图1a中,从电学角度来看最佳或优选的器件厚度在大约8μm与50μm之间,或在示例性实施方式中,不超过约280μm,这远小于sic衬底的厚度,可对该sic衬底加以处理而形成有源器件结构102。典型半导体制造工艺需要至少300至350μm厚的晶圆。附加sic材料厚度增加二极管通态电阻以及其热阻。如上文所提及,图1b是根据一个实施方案的半处理器件的示意性横截面。可向sic衬底层101a施加减薄工艺以去除不期望的sic厚度并获得sic层101b,如图1c所示。减薄工艺可为使用专用晶圆减薄工具的机械磨削。机械磨削应优选地用抛光完成以减少亚表面损伤并获得晶圆背侧的光滑表面。机械磨削通常受约100μm的临界厚度的限制,低于该厚度,可预计具有晶圆破损的某些问题,至少在现今的处理水平下是如此。机械减薄还可后接蚀刻。机械磨削与干法蚀刻的组合可实现比单独机械磨削可提供的晶圆厚度小得多的晶圆厚度。在一些示例中,晶圆被机械地减薄到大约50μm与100μm之间的厚度。机械减薄可导致一定量的亚表面损伤,即使在减薄工艺的最后阶段抛光晶圆背侧,晶圆背侧处仍可存在该亚表面损伤。例如在从载体去除衬底的阶段期间,该亚表面损伤可导致晶圆破损的高风险。因此可施加干法等离子体蚀刻以便通过从sic背侧去除至少5μm至15μm材料而使此类亚表面损伤最小化。至少最开始5μm的去除优选地在蚀刻工具中以中等功率电平进行,以便避免等离子体蚀刻期间晶圆处的热应力,该热应力可能增加晶圆中形成裂纹的概率。亚表面损伤的去除可促进sic功率器件衬底减薄到基本上低于100μm的厚度,而不会在晶圆中形成裂纹。如从图1a的上述讨论可以理解,有源器件102(例如,功率肖特基整流器晶圆)的制造可以通过形成背侧欧姆接触层175以及通过沉积管芯附接所需的焊料金属181来最终完成。因此,可将清洗的晶圆放在金属沉积工具中,其中沉积一个或多个金属层。例如,如图1d所示,镍层160可在生产磁控溅射工具中沉积,对于该工具而言,纯镍的铁磁特性可能成为一个问题。通常在添加较小百分比的钒的情况下能更方便沉积镍。其他金属层可在相同运行中潜在地沉积。将具有沉积的含镍层的晶圆转移到激光退火工具,其中该层由脉冲长度为约100ns的短脉冲170曝光。典型曝光能量可为例如绿(532nm)激光的约2j/cm2,该绿激光具有150ns的脉冲持续时间以及接近2j/cm2的脉冲能量。欧姆金属沉积和激光退火的步骤可重复一次或多次,并且第二(或更高)激光退火170可用不同激光脉冲能量进行。例如,可沉积钛层161(或其他难熔金属,如本文所述)并使之退火。在完成欧姆接触工艺之后,可沉积焊料金属堆叠。焊料金属堆叠可例如为ti/ni/ag,但可使用其他类型的焊料堆叠。图1c中示出了最终完成的器件结构的示意性横截面。在一个方面,激光辅助nisix形成的时间可少至介于数纳秒与100-200ns之间,该时间比rtp硅化工艺的典型持续时间短9个数量级。还可能出现不能通过直接读取来测量准确烧结温度的情况,因为温度的直接读取在纳秒时间标度下较困难。因此,激光退火的峰值温度的值一般对于典型制造工艺仍是未知的。可通过某些测量(诸如表面反射率与计算机模拟)的组合来估计峰值退火温度。硅晶圆上的峰值镍硅化温度可在约1400c(即,接近硅的熔点)以及比硅上ni的rtp硅化的温度(例如,介于400c与800c之间)高得多的温度下发生。对于碳化硅而言,镍的rtp硅化在比硅上ni的温度更高的温度下发生。一般而言,本文所公开的工艺的峰值温度可为至少1400c,并且可超过1600c,该温度约为ti的熔点(因此在如本文所述的那样处理时钛可被部分或完全液化)。另外,激光辅助工艺(包括化学反应和相位变换)可由激光刺激进一步增强。在另一个方面,根据本说明书的功率器件可为利用减薄的sic衬底的三端碳化硅功率器件。三端器件可例如为碳化硅场效应晶体管,例如,sicmosfet或sicjfet。另选地,三端器件可为双极性的,诸如bjt或igbt、或在sic中形成的晶闸管。所述三端sic功率器件的背侧接触的设计和工艺可与整流器的设计和工艺相同。对于本领域技术人员必须清楚的是,至三端器件的前侧接合线必须超过一个,并且所述接合线通常可超过两个,以便在没有过大寄生电阻的情况下适应所述功率器件的高通态电流以及使寄生引线电感最小化。在另一个方面,根据本说明书制造的碳化硅功率器件芯片可被安装为功率模块的部件。功率模块通常被组装在直接铜接合(dcb)衬底上,其中铜层被接合到绝缘陶瓷衬底。dcb衬底上装有所需的半导体芯片,这些半导体芯片可通过焊接或使用扩散焊接技术或通过另一种方法来附接到其顶部金属层。安装在模块中的该组半导体芯片可例如完全由根据本公开制造的减薄的碳化硅功率器件组成。另选地,碳化硅功率器件可与硅功率器件组合,以及与预期为功率模块的一部分的其他元件组合。顶侧功率器件端子进行线接合或由某种其他技术进行连接。然后使用硅橡胶或使用emc来灌封功率模块以将功率器件与环境效应隔离。功率模块还可用作功率转换器件的子电路。根据本说明书的减薄sic功率器件的背侧接触的改善完整性对器件可靠性将具有积极效果。在一些实施方式中,利用根据本发明的sic功率器件的低成本功率模块可被组装在不含陶瓷衬底的emc模具模块中。此类低成本功率器件模块中的半导体器件附接到引线框,并且该模块的所需部件的电绝缘由emc提供。在一个方面,通过由jedec(联合电子设备工程委员会)和/或由aec(汽车工程协会)设定的一组合格性测试来验证sic功率器件的sic功率器件适用性。所提及的组包括多个测试,其中与背侧接触完整性最相关的测试是热机械循环(tmcl),如上所提及。tmcl测试内容可依赖于封装类型。在其余的说明书中,参考工艺(被称为“por”)提供各种所公开的实施方案(诸如上述的那些)的一个或多个比较,以及以下图3至图5的更具体的示例性处理选项。更具体地讲,参考工艺(por)欧姆接触工艺包括单个循环的ni-v沉积和激光退火以实现硅化。下文例如相对于图7a至图7c描述和示出了por工艺的具体示例性结果。一般而言,已发现por工艺会引起通孔封装的tmcl测试失败,除非焊料金属的沉积之前有延长的预先溅射。焊料金属沉积之前对退火nisix表面的延长的预先溅射使得通孔封装未出现故障。然而,smt封装中安装的相同管芯未通过tmcl测试。在欧姆接触层中用纯ni替代ni-v未得到统计上显著的改善。图2示出了在预处理加上100个tmcl循环之后额定电流下二极管正向电压降(vf)的值的分布。还示出了测试之前的vf值以便进行比较。vf的所有值被绘制为样本数的函数。在图2中,四个不同曲线图对应于封装中采用的五种不同类型的emc。vf的明显变化指示从散热器的管芯分层的开始,这通过故障分析来验证。故障的量强烈地依赖于所施加的emc的类型;然而,77个部件的任何批次都不能成功通过前面有预处理的1000循环tmcl测试,而不论采用的是哪种类型的emc。执行故障分析以识别分层的准确位置,并且该故障分析指示恰好沿着nisix接触与焊料金属的分界面发生管芯分层,这通过分层后sic芯片上的残余物的x射线发射分析来确立。因此,该故障分析证实了上文相对于图1a的讨论,例如,nisix/焊料金属分界面附近存在游离碳会产生粗糙表面和不良粘附特性。图3是流程图,示出了根据本说明书的半导体制造工艺的第一选项。在图3中,顶侧功率器件结构(302)的形成后接晶圆减薄(304),如上所述。镍(或镍合金,诸如niv)的沉积(306)后接碳吸除材料(诸如难熔金属,例如钛)的沉积(308)。然后执行第一激光退火(310),后接第二镍层的沉积(312)。第二激光退火(314)后接一个或多个焊料金属的沉积(316)。然后可执行管芯切单(318),后接所形成的器件的合适封装(320)。作为图3的选项1的更具体示例,可通过在待激光退火的两个镍层之间沉积50nm钛层来形成欧姆接触。可将70nmni-v层和50nmti层沉积到被机械地减薄到100μm的sic功率整流器晶圆的背侧上。可使用绿(532nm)脉冲激光来执行该接触的激光退火,该激光具有约140ns的脉冲长度以及能量为2j/cm2的脉冲。在第一退火之后,可沉积附加70nm的ni-v,之后可执行第二激光退火。然后可向晶圆的背侧施加ti/ni/ag的焊料金属堆叠。使用根据选项1的设计和工艺的器件晶圆被切块,被封装在d2pack封装中,并且经受预处理以及从-55c到150c的1000个温度循环的热机械循环(tmcl)。测试条件和所测试的批量(77个器件)与向根据参考工艺(por)处理和测试的器件施加的那些相同。未观察到正向电压漂移或其他器件故障的情形,这明显不同于根据参考工艺的结果的测试结果(已相对于图2描述)。图4是流程图,示出了根据本说明书的半导体制造工艺的第二选项,在本文中被称为选项2。在选项2中,顶侧功率器件形成(402)、晶圆减薄(404)和镍沉积(406)直接后接第一激光退火(408)。然后,可进行碳吸除材料(诸如钛)的沉积(410),后接镍的第二沉积(412)和第二激光退火(414)。之后,与图3类似,图4的工艺可继续进行焊料金属堆叠的沉积(416)、管芯切单(418)和封装(420)。作为相对于图4的选项2的更具体示例,可通过在待激光退火的两个镍层之间沉积50nm钛层来形成欧姆接触。可将70nmni-v层沉积到被机械地减薄到100μm的sic功率整流器晶圆的背侧上。可使用绿(532nm)脉冲激光来执行该接触的激光退火,该激光具有约140ns的脉冲长度,该脉冲具有2j/cm2的能量。在激光退火之后,可依次沉积附加50nm厚的ti层和70nm的ni-v,之后可重复激光退火。焊料金属堆叠可被实现为ti/ni/ag,然后可将其施加到晶圆的背侧。使用根据选项2的设计和工艺的器件晶圆被切块,被封装在d2pack封装中,并且经受预处理以及从-55c到150c的1000个温度循环的热机械循环(tmcl)。测试条件和所测试的批量(77个器件)与向根据参考工艺处理和测试的器件以及向使用工艺选项1的器件施加的那些相同。未观察到正向电压漂移或其他器件故障的情形。图5是流程图,示出了根据本说明书的半导体制造工艺的第三选项,在本文中被称为选项3。如所示和所述的,图5的选项3仅需要单个激光退火。具体地讲,顶侧功率器件结构形成(502)后接晶圆减薄(504),然后是镍沉积(506)和适当碳吸除材料的沉积(508)。然后,执行单个激光退火(510)。之后可进行焊料金属堆叠沉积(512)、管芯切单(514)和封装(516)。在图5的选项3的具体实施方式中,可使用金属沉积和激光退火的单个循环来形成欧姆接触,其中70nmni-v层和50nmti层依次沉积到被机械地减薄到100μm的sic功率整流器晶圆的背侧上。可使用绿(532nm)脉冲激光来执行该接触的激光退火,该激光具有约140ns的脉冲长度以及能量为2j/cm2的脉冲。然后可向晶圆的背侧施加ti/ni/ag的焊料金属堆叠。使用根据选项3的设计和工艺的器件晶圆被切块,被封装在d2pack封装中,并且经受预处理以及从-55c到150c的1000个温度循环的热机械循环(tmcl)。测试条件和所测试的批量(77个器件)与向根据参考工艺处理和测试的器件以及向使用工艺选项1或选项2的器件施加的那些相同。未观察到正向电压漂移或其他器件故障的情形。如上所述,执行至少一个激光退火可包括在沉积镍层和难熔金属层之后且在沉积第二镍层之前执行第一激光退火,以及在沉积第二镍层之后执行第二激光退火。在其他实施方式中,执行至少一个激光退火可包括在沉积镍层之后且在沉积难熔金属层和第二镍层之前执行第一激光退火,以及在沉积难熔金属层和第二镍层之后执行第二激光退火。因此,使用激光退火与碳吸除形成的硅化镍接触(诸如上文相对于图3至图5所述)可与焊料金属形成具有足够强的粘附的分界面以防止沿着焊料金属的分层。可施加两种类型的测试来验证这种焊料金属粘附,例如管芯剪切测试和胶带测试。在另外一个方面,利用与碳吸除层一起形成的激光退火背侧硅化镍的sic功率器件(如在图3至图5中)具有低接触电阻,这对通态电压降没有显著贡献。实现该目标所需的示例性比接触电阻优选地低于0.1mohm*cm2。因此,许多类型的sic器件对背侧接触的一个要求是低比接触电阻。例如,迄今为止,具有650v阻断电压额定值的sic整流器可具有低于1mohm*cm2的通态比电阻。0.1mohm*cm2的比接触电阻将引入超过10%的附加电阻,这是不期望的。而预计未来sic器件具有通态比电阻的较低值,这需要比电阻基本上低于0.1mohm*cm2的接触。表1示出了4个功率整流器晶圆的晶圆测试的结果。所有管芯具有10安培的标称通态电流和650v的标称阻断电压。实际阻断电压是更高的值以便提供所需的安全裕度。使用参考工艺(por)来制造晶圆w1和w2。晶圆w3使用图4的新工艺选项2进行,并且w4使用图3的新工艺选项1进行。整流器具有超过630a/cm2的高电流密度,这就是为什么在附加接触电阻基本上较高时其正向电压降一定会受到此类电阻的影响的原因。表1中提供了平均正向电压降和平均vf的值,并且图6中绘制了该趋势。表1。晶圆平均vf(v)平均bv(v)w11.349766w21.394819w31.357780w41.368784在图6中,4个晶圆的平均bv对平均vf的相依性的趋势线表明,所测试的所有4个晶圆的相依性大约落在平均击穿电压对平均正向电压降之间的相同折衷相依性上。因此,工艺修改对功率整流器的总电压降没有显著影响。任何工艺选项的0.1mohmcm2接触电阻将使630a/cm2额定电流密度下的正向偏压偏移63mv,图6中明显不存在从趋势线的该偏移。63mv的偏移将超过图6所示的曲线图的电压轴的整个跨度,情况明显不是这样。因此不同工艺选项的接触电阻基本上低于0.1mohmcm2。使用图5的选项3(即,金属沉积和激光退火的单个循环)形成的整流器器件的测试数据也指示与选项1相同的低正向电压降,就此而言欧姆接触的贡献不会影响整流器在约630a/cm2电流密度下的正向电压降。如上文所提及,图7a至图7c示出了扫描透射电子显微术(stem)分析的结果,执行该分析的目的是为了分析使用por工艺之一形成的sic功率器件的接触横截面702a–710a。具体地讲,图7a至图7c示出了激光退火nisix接触的示意性横截面(图7a)、电子显微照片(图7b)和组成(图7c)。如图7a所示,层702a是sic层,欧姆接触层704a是各处分散有碳的nisix层,并且层706a,708a,710a分别表示ti/niv/ag的焊料金属堆叠。对应附图标记702b-710b涉及对应stem图像。从图7b中可以看出,大量碳析出物存在于nisix欧姆接触金属704b的本体中。碳团簇或析出物存在于sic与nisix的分界面附近、nisix的本体中以及nisix的顶表面处,即与焊料金属的分界面附近。碳含量的高峰值也可见于nisix与焊料金属的分界面附近的层组成的元素分布图,如图7c所示。正如所述,该峰值特别不可取,因为其意味着该分界面粗糙以及相关联的粘附力缺乏。以纯ni作为nisix形成的来源(而非niv)的por样本显示出类似的碳近分界面峰值以及类似的可靠性问题。nisix组成在这种情况下与约62/38成比例,这对应于大约ni3si2的nisix组成。相比之下,图8a是大体上对应于图1a的结构的stem图像。图8a对应于使用图3的选项1形成的结构,其中在第一激光退火之前提供ti的碳吸除层。图8b提供竖直方向上的元素组成的线扫描。图8a示出了与图1a的层175相对应的欧姆接触层875的硅化物。此外,碳析出物被示出为存在于区域876a中,该区域在nisix与sic的分界面附近,并且对应于图1的第一硅化物区域176a。较大碳析出物(或团簇)和未反应的碳的混合物形成于区域877a中,该区域高于区域876a并且对应于图1a的第二硅化物区域177a。更具体地讲,在该区域877a中,可存在游离或未反应的碳,但第二硅化物区域877a的本体硅化物内的此类碳一般对层875与焊料金属堆叠881a/b之间的分界面的接触和表面特性没有不利影响。在反差stem图像(其中较重元素显示较亮反差)诸如图8c中(其中对应元素符号包括在每幅图的右上角中),可以观察到碳的亮反差与ti的反差完全相关。在此类图像中,碳和钛的亮反差在区域877a中与镍和硅的暗反差相关,这指示ti和ni的聚集体是析出物。ti的亮反差也与钒的亮反差相关,但v的浓度低于ti。因此区域877a中的碳聚集体是钛的且部分为钒的碳化物的析出物。ti的连续层不再存在于区域877a中。这与如上所述ti的部分或完全熔化一致,和/或涉及ti的扩散与固态反应的组合。tic的形成还发生在与图1的第三硅化物区域178a相对应的区域878a中,其主要在图3的第二激光退火期间形成。然而,该区域中的平均tic粒度小于区域874a的平均tic粒度。如从上文所提及的反差stem图像的类型中可以观察到,钒的反差图案在整个区域877a和878a中密切遵循碳和钛的反差图案,这指示碳化钒的形成发生在与碳化钛的形成相同的位置中。然而,碳化钒的此类形成不足以通过使用附加碳吸除难熔金属(诸如钛)来解决和纠正本文所提出的稳定性和粘附问题。换句话说,第一难熔金属(诸如钒)与nisix层的镍包含在一起(例如,出于促进硅化处理的目的,如本文所提及)不足以形成本文所述的硅化物结构(包括第一硅化物区域、第二硅化物区域和第三硅化物区域),也不能解决本文所述的稳定性和粘附问题。然而,也如本文所述,以本文所述的方式包含第二难熔金属(诸如钛)足以在整个nisix层175/875中产生反应和未反应的碳的所述分布。富tic层880也存在于欧姆接触层875与sic衬底801b的分界面附近。该近分界面tic层可潜在地和/或部分地阻碍碳析出物层876a的形成,如图8a所示的横截面的右侧部分中可见。对界面碳析出物层876a的形成的此类阻碍是不可取的,因为这可增加接触电阻率,如上文相对于图1a所述。太厚的吸除ti层(例如,图1中的层161)的使用可因tic层880的早期形成而不合需要地使接触电阻劣化。为了减轻或避免该结果,可保持吸除层160的厚度小于或等于镍层160的厚度。此外,如果ni层160太薄,则可发生接触特性的相同劣化,从而导致在退火期间ti朝向sic衬底的过快迁移。可保持ni(或ni-v)的厚度超过大约20nm以避免欧姆接触电阻的增加。因此,区域876a中的碳浓度被设计为独立于ti的碳吸除层中包含的ti,该ti的碳吸除层初始放置在图3的第一镍层上。换句话讲,至少部分地引起欧姆接触层875的接触电阻的界面碳层876a可基本上如同不存在吸除层161那样形成,同时仍获得吸除层161的所有优点。最后就图8a和图8b而言,可以观察到由图3的工艺选项1得到的nisix组成对应于ni3si。por参考工艺的nisix组成是ni3si2。下文将更详细讨论nisix组成。图9示出了使用图4的选项2形成的nisix欧姆接触层975的横截面的stem图像。stem图像中标记了游离碳的析出物的位置(“c”)以及所测量的nisix组成(ni3si2)。该组成可与por(ni2si3)进行比较,并且不同于工艺选项1(ni3si)。游离碳存在于区域976a中的nisix层下部的层中。然而,在nisix层的较高区域977a,978a中,元素分辨stem图像显示出与碳、钛和钒的元素图像相关的亮反差,从而指示碳向碳化钛中且部分地向碳化钒中的吸除。在nisix与焊料金属981的分界面附近进行高分辨率扫描,并且在图10中示出这种扫描的示例。图10中的扫描的x坐标沿从欧姆金属接触层875到焊料金属881的方向增加。欧姆金属中的镍与硅的比率为大约3:2,这接近因por工艺而引起的ni/si比率。该分析中检查的焊料金属部分对应于ti,其是ti/ni/ag焊料金属堆叠的第一层。该扫描示出了该分界面附近的增加的碳含量,其中该碳结合到碳化物中,从图10中可以清楚看出该结合。碳含量保持低于ti的含量。另外,还在与碳浓度的峰值相同的位置处观察到钒的累积。从nisix欧姆接触层175,875,975的结构研究得出的一个结论是例如140ns的短退火时间和大约或高于ti熔点的高温都不会给激光退火过程中过量碳的有效吸除带来障碍。另一个结论是对碳具有高亲和力的其他金属的添加可用于吸除与sic的nisix激光退火接触中的过量碳。钒表示这种金属的一个示例,如上所提及。也可使用其他金属,如w、mo或ta。此类金属的硅化物可潜在地用作纯金属的代用品。此外,所施加的难熔金属不一定必须限于重元素。例如,二硼化钛可用作碳吸除剂。硼也会与碳反应形成碳化硼b4c。在一个方面,如本文所述,退火硅化镍的顶表面应优选地不含任何游离碳,因为游离碳可能影响焊料金属粘附的可靠性。硅化镍接触的顶表面可具有增加的碳含量;然而,此类增加的碳应优选地结合到难熔金属碳化物中,正如选项1和2的组成分布图的示例的情况那样。未反应的碳的析出物(或团簇)实际上可存在于硅化镍接触层的本体中而对接触可靠性没有任何不利影响(例如,第二硅化物区域177a/877a),正如图4的选项2的情况那样。然而,根据选项2的硅化镍的结构不含与焊料金属相邻的第三硅化物区域178a/878a的未反应的碳的析出物,该相邻区域对于焊料金属的粘合特性最为关键。相邻区域178a/878a的厚度应为至少大约10nm以便提供硅化物的一些回蚀的可能性,但不会因这种回蚀而到达第二硅化物区域177a/877a内的未反应的碳的析出物。在一些情况下,硅化镍与焊料金属的分界面处的难熔金属碳化物层可不存在于根据一些实施方案的完成sic功率器件中。所述分界面处的这种界面碳化物层可例如在焊料金属堆叠沉积之前的原位回蚀期间至少部分地去除。有可能第二硅化物层177/877仅在其下部中包含游离碳的析出物,例如表示从第一硅化物区域876向第二硅化物区域877的转变(例如,如可在图3的选项1的情况下发生,如图8a/8c中表示)。换句话讲,从第一硅化物区域176/876向第二硅化物区域177/877的转变可能不一定具有尖锐边界,并且硅化镍本体中的碳析出物的某部分将属于第二硅化物层。在各种实施方式中,可存在碳吸除金属的优选量和/或激光退火之前这种金属的优选位置的边界。上文例如相对于与图3的工艺选项1相关的实施方案公开了这些边界中的一些边界。碳吸除金属应优选地不放置在与sic的分界面附近,这是由于有可能抑制sic表面附近的碳析出物形成,该抑制可增加接触电阻。一般而言,已经表明,利用纯镍接触的至重n掺杂sic衬底的欧姆接触具有低10至100倍的比电阻,这是由于形成了界面游离碳,该游离碳具有对n型sic的极低势垒高度。优选的是,吸除金属与sic表面由至少10nm至20nm的镍隔开。10%至15%以下的少量吸除金属仍可作为在激光退火之前沉积到sic表面上的ni层的添加物存在,该可能性由以上公开的3个工艺选项中的钒的作用证实。以上描述证实了由足够厚的镍层隔开吸除金属的意义。因此,太厚和/或放置得太靠近sic/nisix分界面的碳吸除材料可抑制界面碳团簇区域(176a,876a,976a)的形成,该界面碳团簇区域至少部分地引起该接触的欧姆特性。另一方面,吸除金属的量太低将使区域177a,877a,977a内以及nisix层与焊料金属层的分界面附近(即,区域178a,878a,978a)的游离碳太多。在后一种情况下,可从相对于先前实施方案公开的钒的作用中观察到吸除材料的量不足的影响。即,正如所提及的,通常在半导体制造中将钒添加到镍溅射靶以便避免纯镍的镍铁磁特性的影响,所述铁磁特性对于某些类型的金属溅射工具是不可取的。钒添加的典型浓度是7%,先前实施方案中所述的ni-v合金也是如此。然而,7%的该浓度不足以提供背侧接触堆叠的稳定性所需的水平的碳吸除。可估计欧姆金属堆叠(如图1中示意性地表示的层160和161)中的吸除金属量的下边界介于大约20%与25%之间。可使用化学计量规则来确定待激光退火的镍-难熔金属(rem)金属堆叠中存在的rem的最少量。rem的量应足以吸附由镍与sic的硅化所产生的碳,并且在硅化镍的顶侧处没有未反应的碳上的析出物的聚集。在激光退火之前沉积到sic上的几乎所有镍都将反应形成硅化镍;因此,每个ni原子平均将产生0.33至0.67个碳原子,具体取决于实际硅化镍组成,其可在ni3si至ni3si2的范围内变化。因此激光退火金属堆叠中的难熔金属的量应足以结合因从sic和ni形成硅化镍而产生的碳的至少约25%。如上文所提及,有可能所有或几乎所有沉积的镍都发生硅化,这是由于难熔金属被分散和/或是非连续的,故而难熔金属只能防止很少硅或不能防止硅扩散穿过镍层。所释放的碳的某部分仍能够以硅化物的本体中游离碳析出物的形式存在于该硅化镍中。这些析出物的一部分将位于硅化物与sic的分界面附近,而另一部分可能仍存在于硅化镍的本体中而不会到达顶部硅化物表面,如图9所示的选项2工艺的stem分析图像中证实。硅化镍本体中未反应的碳的部分可为因sic与镍反应而释放的总量的至多75%。所释放的碳的剩余至少25%可结合到难熔金属的碳化物以便避免硅化镍的顶表面处有未反应的碳。作为一个示例,工艺选项2中利用的50nm的ti理论上将消耗因镍与sic反应形成ni2si3而产生的碳的至多38%。38%的量考虑了沉积的ni-v层中的钒的7%分数,因为钒也参与了过量碳的吸除。难熔金属的准确最少所需量将取决于难熔金属所形成的碳化物的化学计量。作为一个示例,就钛而言,化学计量系数是1,即,1个ti原子结合1个碳原子。如果难熔金属作为硅化物引入,则在对应化学计量计算中还应考虑因难熔金属碳化物形成而释放的硅。碳吸除金属的最少所需量可取决于激光退火金属堆叠的准确构型,如从选项1和2的比较中可以清楚看出。将吸除金属定位在sic表面附近(正如图3的选项1的情况那样)可促进难熔金属碳化物形成在sic表面附近。所述近界面金属碳化物层的示例在图8a中示出为层880。所述近界面难熔金属碳化物继而将促进ni3si的形成而非ni3si2的形成,在这种情况下,需要吸除较低量的碳。在一个方面,预计使背侧接触激光退火的工艺不能提供晶圆内的完美均匀性。作为一个示例,可用的激光不能提供以所需的密度级曝光整个晶圆背侧的可能性。激光束在晶圆区域内扫描,并且存在曝光区域的某些拼接。拼接区域可在偏离最适条件的条件下曝光,并且游离碳的完全吸除可能不一定发生在此类拼接区域中硅化物欧姆接触与焊料金属的分界面处。另一个可能的不规则性来源可能是金属沉积之前sic表面受污染,因为在晶圆减薄之后清洗背侧的例行程序可能未完全遵守与向前侧工艺施加的标准相同的标准。未在依照根据本说明书的选项1、2或3形成的样本中观察到焊料金属区域附近的此类未反应的碳的区域;然而,它们可潜在地出现于某些实施方式中。焊料金属粘附可能不会受到显著影响,前提条件是其分界面附近的界面碳被吸除而在器件区域的主要部分中形成难熔碳化物,在这种情况下,所得的sic器件基本上不会偏离本说明书中教导的sic器件。预计相对不良的可焊金属粘附的区域在其分数未超过总背侧接触区域的大约三分之一时会形成不连续网络,该数值设定了区域178a中有未吸除的碳的所述缺陷部分的分数的示例性上边界。不过优选的是,所述分数应保持尽可能低,优选地0.1或0.01,或被完全消除。使用波长为532nm的脉冲可见光激光来执行上述示例中公开的激光退火实施方案。选择该激光波长是出于sic工艺与用于硅器件处理的既有工艺的兼容性的考虑因素,但其他波长也可为合适的,例如在170nm与10微米之间。至sic的nisix欧姆接触的激光退火的先前公开内容受限于紫外(uv)激光的使用,所述激光具有大约360nm与240nm之间的波长。uv激光可能具有穿透暴露金属层的一部分的激光可能会被吸附在sic中的优点。然而,该要求不一定适用于至sic的nisix接触的激光退火。在利用背侧接触的可见光退火时确实在理论上有可能出现顶侧器件特征的激光损伤,因为sic能透过可见激光能量,如果退火的金属接触包含空隙,则该激光能量可能穿透到sic中。然而,对于sic肖特基二极管和sicmosfet工艺两者而言,可消除对所述顶侧器件图案的激光损伤。这通过标准半导体工艺控制的应用来实现以避免待激光退火的金属堆叠中的大空隙。同样可利用uv光的激光脉冲来执行本文所公开的至sic的nisix激光退火欧姆接触形成的碳吸除技术。还可以出于nisix欧姆接触退火的目的而利用脉冲红外(ir)激光。可例如在工艺稳定性不够好时使用uv激光退火以确保在晶圆背侧处形成连续金属膜,需要该连续金属膜来保护顶侧有源结构图案过度暴露于可见激光。使用可见光和ir激光系统的一个优点可能是其较低的设备成本,因为脉冲uv辐射通常通过ir或可见光的上转换来实现。应当理解,在前面的描述中,当元件诸如层、区域、衬底或部件被提及在另一个元件上,连接到另一个元件,电连接到另一个元件,耦接到另一个元件,或电耦接到另一个元件上时,该元件可直接在另一个元件上,连接或耦接到另一个元件上,或者可以存在一个或多个中间元件。相反,当元件被提及直接在另一个元件或层上、直接连接到另一个元件或层、或直接耦接到另一个元件或层时,不存在中间元件或层。虽然在整个详细描述中可能不会通篇使用术语直接在…上、直接连接到…、或直接耦接到…,但是被示为直接在元件上、直接连接或直接耦接的元件能以此类方式提及。本申请的权利要求书(如果存在的话)可被修订以叙述在说明书中描述或者在附图中示出的示例性关系。如在本说明书和权利要求书中所使用的,除非根据上下文明确地指出特定情况,否则单数形式可包括复数形式。除了附图中所示的取向之外,空间相对术语(例如,在…上方、在…上面、在…之上、在…下方、在…下面、在…之下、在…之以下等等)旨在涵盖器件在使用或操作中的不同取向。在一些实施方式中,在…上面和在…下面的相对术语可分别包括竖直地在…上面和竖直地在…下面。在一些实施方式中,术语邻近能包括横向邻近或水平邻近。一些实施方式可使用各种半导体处理和/或封装技术来实现。一些实施方式可使用与半导体衬底相关联的各种类型的半导体处理技术来实现,该半导体衬底包括但不限于,例如硅(si)、砷化镓(gaas)、氮化镓(gan)、碳化硅(sic)等。虽然所描述的实施方式的某些特征已经如本文所述进行了说明,但是本领域技术人员现在将想到许多修改形式、替代形式、变化形式和等同形式。因此,应当理解,所附权利要求书旨在涵盖落入实施方式的范围内的所有此类修改形式和变化形式。应当理解,这些修改形式和变化形式仅仅以示例的方式呈现,而不是限制,并且可以进行形式和细节上的各种改变。除了相互排斥的组合以外,本文所述的装置和/或方法的任何部分可以任意组合进行组合。本文所述的实施方式能包括所描述的不同实施方式的功能、部件和/或特征的各种组合和/或子组合。当前第1页1 2 3