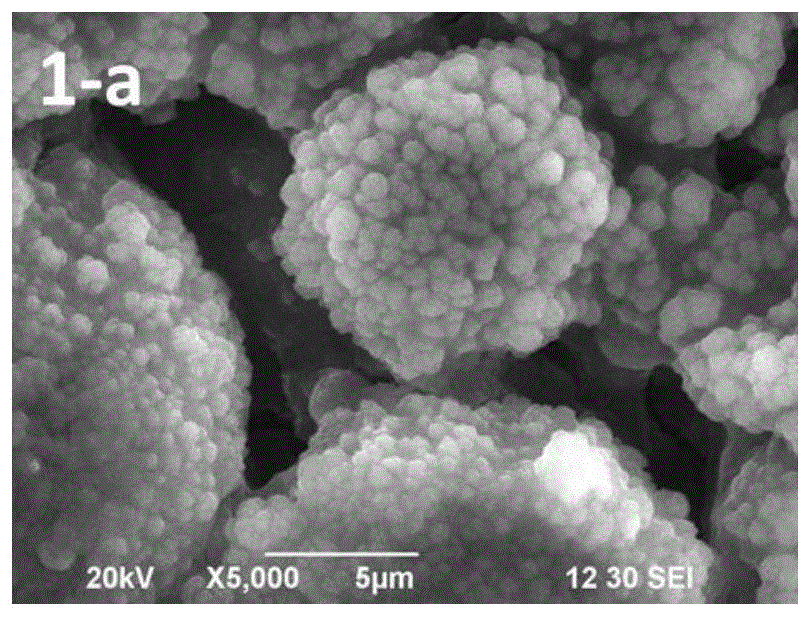
本发明涉及锂离子电池
技术领域:
,主要涉及锂离子电池正极材料领域,具体涉及一种球形二次结构锰酸锂正极材料及其制备方法。
背景技术:
:近年来随着新能源汽车,便携式电动工具,组合式储能电站的兴起,对其中使用的化学电源的动力能量密度及安全性的要求越来越高,目前常见的锂离子电池用正极材料主要有钴酸锂、锰酸锂、镍钴锰酸锂和磷酸亚铁锂。其中钴酸锂尽管能量密度高,但因钴储存量有限以及钴酸锂安全性差因而主要用于3c领域的小型锂离子电池中,锰酸锂及磷酸亚铁锂材料能量密度较低,有逐渐被镍钴锰酸锂和含钴低的高镍材料替代的趋势,尽管如此,受市场供需影响,以高安全性为代表的锰酸锂材料仍旧是一款类似“压舱石”的正极材料,仍旧具有较好的市场应用前景。锰酸锂正极材料通常包括尖晶石型锰酸锂(limn2o4)以及层状结构的锰酸锂(limno2),后者因知识产权主要在美国阿贡(argone)实验室,以及合成和电解质的匹配性问题目前研究集中于实验室阶段。尖晶石型锰酸锂limn2o4是hunter在1981年首先制得,晶体结构属于立方晶系,fd3m空间群,由于具有三维隧道结构,锂离子可以可逆快速地从尖晶石晶格中三维方向脱/嵌,不会引起结构的塌陷,因而具有优异的倍率性能、稳定性和安全性能。由于锰酸锂中只含有锂和锰两种有价元素,不涉及国内较为短缺的钴和镍元素。且来源广泛,因此在近年来正极材料市场价格涨跌中受市场影响较小,整体价格已接近铅酸电池的价格,且回收方便,是一种不可多得的绿色化工产品,因而是锂离子电池中代替铅酸系电池的最有力竞争者。目前市场上推出的锰酸锂材料主要用于功率型锂电池和动力型锂电池,以单独使用或者是与价格贵的高镍正极材料复配使用。锰酸锂相对钴酸锂,镍钴锰酸锂等层状结构商业应用材料而言,其劣势是能量密度低,尽管理论比容量为148mah/g,但实际发挥的比容量为80-90mah/g(钴酸锂为140-180mah/g),以及压实密度低(3.0-3.2g/cm3,钴酸锂为4.0-4.2g/cm3),此外因锰酸锂产品颗粒呈立方晶体状,棱角分明,因此在后期制备成极片辊压时,极易刺破薄的正极载体铝箔(通常厚度为8-20μm),因此无论是材料的比容量还是材料的重量及体积能量密度均较钴酸锂低,因此如何有效的提升锰酸锂的能量密度扩大其应用范围是解决锰酸锂应用的关键。cn201110056889.1公开了一种高温循环稳定的尖晶石锰酸锂合成方法,其特征在于,将原料锂化合物、锰化合物以及al2o3、mgo、tio2、cr2o3的一种或多种按照化学式li(1+x)mn(2-x-y)myo4(0<x<0.3,0<y<0.2,m为al、mg、ti、cr的一种或多种)均匀混合,然后在500~750℃下保温5~20h,冷却后的产物研磨后在800~1200℃下保温10~30h,冷却后的产物与一定量的钴、镍、锂化合物(钴、镍、锂和产物中的锰摩尔比为0.02~0.2)均匀混合,再于500~750℃下保温10~30h,最后产物经冷却后粉碎过筛得到成品。从最终制备物上看,似乎是一种锰酸锂掺杂的镍钴二元材料。cn201110327883.3公开了一种提高锰酸锂产能及锰酸锂电池中正极压实密度的方法,其特征将混合均匀的按配方混合的二氧化锰与碳酸锂与质量比为0.6~1.2wt%的有机粘结剂混匀;再将混合料装入压机的模具压制成锰酸锂原料团块;将压制好的锰酸锂团块放入烧结炉中烧结(温度为800~850℃,烧结时间为10~15h);将烧结好的锰酸锂团块破碎(粒度为dv50≤15μm),用325目振动筛筛分得到锰酸锂产品。上述专利采用通过制备纳米级的锰酸锂来提高锰酸锂的性能,实际上是采用物理方法减少因颗粒大而带来的锂扩散困难来提升锰酸锂的比容量,由于锰酸锂的性能发挥与本体晶体大小、电解质、负极、电池结构等均相关,实际中仅通过减少颗粒大小来提升锰酸锂性能不太明显。cn102201572a公开了一种掺杂改性制备锰酸锂性能的合成方法。其化学式可以表述为limn(2-x)mxo4·ylialo2。m是mg,ca,co,ni,cr,zn,s中的一种或者几种化学元素的组合。x值范围为0≤x<0.1,0<y<0.5。将一定量的金属元素mn、m和al的复合氧化物前驱体与li2co3按照li:(mn+m)=0.5:1和li:al=1:1的摩尔比充分研磨混合,然后在高温下烧结而成。cn201310125371.8公开了一种掺杂锰酸锂前驱体的制备方法。先将合金前驱体粉碎,然后煅烧。粉碎、煅烧交替进行,直到合金全部氧化,然后将粉料烘干、筛分。再向粉碎的前驱体中加入摩尔比为45%-60%的锂盐,然后球磨(湿磨)烘干后,在马弗炉中先低温500℃-600℃锻烧1-10h,再高温700℃-900℃锻烧10-60h(温度高时间适当缩短),得到初始掺杂锰酸锂正极材料。对初始掺杂锰酸锂再粉碎,烘干,筛分,即得到所需掺杂锰酸锂正极材料。其振实密度可达≥2.6g/cm3(比化学法掺杂高15%),电极填充加工性能好。该产品制成的扣式电池检测,1c充放电,放电至2.4伏时,其可逆放电容量为175mah/g-260mah/g;放电至2.75v时,可逆放电容量为135mah/g~185mah/g,超出了现有尖晶石结构锰酸锂锂离子电池正极材料148mah/g的理论容量。但通常锂离子电池/组的工作电压为3.4v以上,仅通过调整工作电压范围尤其是下限阀值来提升比容量实际中并不可行,且不具有可比性。技术实现要素:本发明解决的技术问题是:现有的锂离子电池用锰酸锂正极材料在使用过程中能量密度较低,材料颗粒棱角分明导致极片压实密度不高,因此从材料本身着手亟待开发一种新的简单可行的改进方法。为解决上述技术问题,本发明在研究锰酸锂正极材料制备工艺后,发现加入少量钴源可以参与锰酸锂合成,钴化合物熔点低,可与锰酸锂晶体相互“熔解”,减少烧结料板结,最终制备出表面棱角不明显,且呈势能最低的球形颗粒粉体,生成表面圆润的球形锰酸锂材料,进而提升锰酸锂的压实密度等加工性能,以及制备的锂离子电池的电化学性能,对于锂离子电池正极材料的应用具有重要意义。具体来说,针对现有技术的不足,本发明提供一种球形度高的二次结构锰酸锂正极材料,其特征在于,该锰酸锂正极材料的化学式为li(1+x)mn2raob其中,r为至少含钴的掺杂元素,0.01<x<0.22,0.05<a≤0.25,4<b<4.6;优选地,0.02≤x≤0.2,还优选0.02≤x≤0.12,0.06≤a≤0.25,4.1≤b≤4.4;进一步优选地,其总游离锂含量处于0.01-0.04wt%范围内;还优选ph值处于10以内。优选的,上述正极其球形度为0.8-0.99,优选0.87-0.98。另外,本发明还提供如下技术方案。一种球形度高的二次结构锰酸锂正极材料的制备方法,该锰酸锂正极材料的化学式为li(1+x)mn2raob其中,r为至少含钴的掺杂元素,0.01<x<0.22,0.05<a≤0.25,4<b<4.6,其特征在于该制备方法包括下述步骤:(a)将包括锰源前驱体、锂源化合物、掺杂元素化合物及助剂原料按计量比混合后,经过预烧脱水、粉碎后得到锂离子电池正极材料半成品1;(b)将步骤(a)得到的锂离子电池正极材料半成品1、钴源及助剂原料按计量比混合后,再将混合物放入到辊道窑或者回转窑中烧结合成,出窑炉后经粉碎得到锂离子电池正极材料成品;其中,步骤(a)中加入的掺杂元素化合物和步骤(b)中加入的钴源的量以钴元素计为能使得到的锰酸锂正极材料的化学式为li(1+x)mn2raob,其中,0.01<x<0.22,0.05<a≤0.25,4<b<4.6即可。根据上述制备方法,其中,锰源前驱体为由一次颗粒团聚而成的球形形貌四氧化三锰,优选其dv50:2-15μm,更优选球形度为0.3-0.99。根据上述制备方法,其中,锰源前驱体为由无定形一次颗粒组成的电解球形二氧化锰,优选其dv50:2-15μm,更优选球形度为0.3-0.99。根据上述制备方法,其中,锰源前驱体为由一次颗粒团聚而成的的球形形貌氢氧化锰,优选其dv50:2-15μm,更优选球形度为0.3-0.99。根据上述制备方法,其中,锂源化合物选自含单水氢氧化锂、氢氧化锂、草酸锂、碳酸锂、硝酸锂、醋酸锂、氟化锂、氯化锂、叔丁基锂和柠檬酸锂中的一种或两种以上。根据上述制备方法,其中,锂源化合物为固体物,优选其粒径dv50:0.1-200μm。根据上述制备方法,其中,所述r为掺杂元素,选自钴和铝、镁、锆、钛、钨、镧或钇中的一种或两种以上。根据上述制备方法,其中,掺杂元素化合物为固体物,优选其粒径dv50:0.1-200μm。根据上述制备方法,其中,所述钴源选自氢氧化亚钴,醋酸钴,碱式碳酸钴,四氧化三钴,钴酸锂,硫酸钴,氯化钴中的一种或一种以上。根据上述制备方法,其中,步骤(a)预烧脱水温度为200-800℃,优选气氛为富氧空气,更优选氧气体积比为45%-70%;进一步优选预烧时间为7-15小时,还进一步优选富氧空气流量为180-600nm3/h。根据上述制备方法,其中,步骤(b)的烧结温度为700-880℃,优选气氛为富氧空气,更优选氧气体积含量为60-80%;进一步优选烧结时间为6-16h,还进一步优选富氧空气流量为500-700nm3/h。本发明还提供一种球形度高的二次结构锰酸锂正极材料,其是由上述制备方法制备得到,其球形度为其球形度为0.8-0.99,优选0.87-0.98。其中,本发明的制备方法得到的所述二次结构锰酸锂正极材料,其粒度d50处于3.5-10.5μm范围内,比表面积为0.9-1.6m2/g范围内。本发明还提供一种锂离子电池,其包含上述锂离子电池正极材料。本发明的优点是:本发明采用添加钴源改进锰酸锂材料的形貌,降低制程过程中锰酸锂半成品的板结程度,提升锰酸钽正极材料的电化学性能,扩大了锰酸锂材料的应用环境。该方法经济可行,适用性广泛,效果非常明显,具有较好的应用前景。附图说明图1-a为实施例1电镜图,放大倍数5000倍。图1-b为对比例1电镜图,放大倍数5000倍。图1-c为实施例2电镜图,放大倍数3000倍。图1-d为对比例2电镜图,放大倍数3000倍。图2为实施例及对比例之55℃0.5c/0.5c循环图。具体实施方式鉴于目前锂离子电池用锰酸锂正极材料棱角分明球形度低在极片碾压过程中易损坏载体铝箔的问题,本发明提供一种制备含钴球形或类球形锰酸锂正极材料的方法,通过在制备过程中加入钴源再经处理后即可得到球形度高的锰酸锂正极材料,有利于提升锰酸锂正极材料的物理加工及电化学性能。该工艺制备简单,经济可行,同时不影响锂离子电池用正极材料的电化学性能。一种优选的实施方式中,本发明提供一种制备含钴二次球形结构锰酸锂正极材料的方法,最终形成目标产物含钴锰酸锂正极材料。优选的,上述制备工艺中,其中锂盐为碳酸锂,草酸锂,单水氢氧化锂,氢氧化锂,醋酸锂,氟化锂等的一种或多种,纯度为工业级或者是电池级,所述的目标掺杂物必须有钴,其余的目标掺杂元素可以为镁、钛、铝、钇、锆、镧、钨等具有一定粒度的氧化物、盐、或其氧化物中的一种或者是几种,也可以只有钴,没有其他掺杂元素。在步骤(a)中加入的掺杂元素化合物中含有钴源,在步骤(b)中也加入有钴源,只要这两个步骤中加入的钴源物质中钴元素的总和符合目标产物的化学式即可,至于两个步骤中各加多少,则没有限制。本发明还提供锰酸锂锂离子正极材料在制造锂离子二次电池、移动式存贮设备和储能电站中的应用。本发明还提供一种锂离子二次电池,其特征在于,包含上述的锰酸锂锂离子电池用正极材料制成的正极。本发明还提供一种锂离子二次电池,其特征在于,所述锰酸锂锂离子正极材料是通过上述的方法制备得到。下面通过具体实施例来说明本发明所述锰酸锂正极材料及其制备方法和应用。下面实施例中所用到各试剂和仪器来源如表1及表2所示。表1本发明实施例中所用试剂信息表2本发明实施例中所用设备信息实施例1备料:选用500l融合机,开启搅拌(400rpm),在搅拌情况下加入76.5kg的四氧化三锰(dv50:10μm),再称取26.2kg单水氢氧化锂粉体加入到500l融合机中,再称取6.1kg纳米四氧化三钴,在搅拌情况下按80wt%固含量添加27.7kg去离子水,搅拌0.5h后进一步降低速度(50rpm)搅拌20min出料形成具有一定成型度的膏状物料备用。预烧脱水:采用通气24m辊道窑。设置升温区温度为200℃,通入富氧空气(氧含量体积比为60%,气体输入量180nm3/h)条件下将上述膏状物料装入到陶瓷匣钵中进行预烧结,烧结时间为7h,将物料隔离空气冷却至常温,称取进出物料的重量,统计烧失率(预烧结粉料质量差与预烧结前粉料质量的比值)为27.6%。然后用气漩涡流粉碎机进行粉碎,粉碎时控制环境空气的湿度≤2%,得到半成品1。复配烧结粉碎:将半成品1再次投入到500l融合机中,向其中加入10kg去离子水,称取2.0kg纳米四氧化三钴,经混合0.5h后取出物料重新装入陶瓷匣钵中,采用通气24m辊道窑。设置升温区温度为700℃,通入富氧空气条件下(氧含量体积比为70%,气体输入量600nm3/h)烧结16h,将物料隔离空气冷却至常温,称取进出物料的重量,统计烧失率(第二次烧结粉料质量差与第二次烧结前粉料质量的比值)为1.1%。然后用气漩涡流粉碎机进行粉碎,得到镍钴锰酸锂正极材料,材料的粒度(dv50)为10.2μm,比表面积为1.2m2/g。用icp对正极材料的元素定量分析后经核算结构式为:li1.2mn2co0.2o4.4。实施例2备料:选用500l犁刀式混料机,开启搅拌(主轴120rpm,侧刀速度1500rpm),在搅拌情况下加入85.4kg的电解二氧化锰((dv50:9μm)),再称取24.4kg碳酸锂粉体,加入0.25kg纳米氢氧化亚钴加入到500l犁刀式混料机中,在搅拌情况下添加用10kg去离子水溶解26.2kg五水硝酸锆溶液,搅拌2h后进一步降低速度(3-5rpm)搅拌6h出料形成具有一定成型度的粉状物料备用。预烧脱水:采用通气24m辊道窑。设置升温区温度为500℃,通入富氧空气(氧含量体积比为65%,气体输入量400nm3/h)条件下将上述膏状物料装入到陶瓷匣钵中进行预烧结,烧结时间为13h,将物料隔离空气冷却至常温,称取进出物料的重量,统计烧失率为31.9%。然后用气漩涡流粉碎机进行粉碎,粉碎时控制环境空气的湿度≤2%,得到预烧结半成品1。复配烧结粉碎:将半成品1再次投入到500l犁刀式混料机,开启搅拌,向其中加入0.22kg纳米氢氧化亚钴,经混合3.0h后取出物料重新装入陶瓷匣钵中,采用通气24m辊道窑。设置升温区温度为880℃,通入富氧空气条件下(氧含量体积比为70%,气体输入量600nm3/h)烧结6h,将物料隔离空气冷却至常温,称取进出物料的重量,统计烧失率为1.1%。然后用气漩涡流粉碎机进行粉碎,得到锰酸锂正极材料,材料的粒度(dv50)为9.5μm,比表面积为1.23m2/g,经核算结构式为:li1.02mn2co0.1zr0.15o4.14。实施例3备料:选用500l捏合机,开启搅拌(30rpm),在搅拌情况下加入94.3kg的氢氧化锰,再称取38.9kg草酸锂粉体加入到捏合机中,称取2kg碱式碳酸钴,34.6kg去离子水,搅拌1h后进一步降低速度(10rpm)搅拌30min出料形成具有一定成型度的膏状物料备用。预烧脱水:采用通气24m辊道窑。设置升温区温度为750℃,通入富氧空气条件下(氧含量体积比为70%,气体输入量500nm3/h)将上述膏状物料装入到陶瓷匣钵中进行烧结,烧结时间为8h,将物料隔离空气冷却至常温,称取进出物料的重量,统计烧失率为42.8%。然后用气漩涡流粉碎机进行粉碎,得到锰酸锂正极材料半成品1,材料的粒度(dv50)为11.0μm,比表面积为2.2m2/g。复配烧结粉碎:将半成品1再次投入到500l捏合机中,向其中加入去离子水10kg,3.3kg碱式碳酸钴,经混合1.0h后取出物料重新装入陶瓷匣钵中,采用通气24m辊道窑。设置升温区温度为880℃,通入富氧空气条件下(氧含量体积比为70%,气体输入量600nm3/h)烧结10h,将物料隔离空气冷却至常温,称取进出物料的重量,统计烧失率为1.7%。然后用气漩涡流粉碎机进行粉碎,得到锰酸锂正极材料,材料的粒度(dv50)为8.5μm,比表面积为0.98m2/g,经核算结构式为:li1.08mn2co0.08o4.16。实施例4备料:选用500l陶瓷球磨机。开启搅拌(30rpm,聚氨酯球料与原料重量比1.2:1),在搅拌情况下加入78.8kg的四氧化三锰(dv50:3.0μm),再称取16.9kg氢氧化锂粉体加入到500l陶瓷球磨机中,在搅拌情况下添加6.44kg乙醇钨,以及1.0kg醋酸钴,搅拌2h后进一步降低速度(10rpm)搅拌4h出料滤出聚氨酯球形成具有一定成型度的膏状物料备用。预烧脱水:采用通气24m辊道窑。设置升温区温度为800℃,通入富氧空气条件下(氧含量体积比为70%,气体输入量600nm3/h)将上述膏状物料装入到陶瓷匣钵中进行烧结,烧结时间为8h,将物料隔离空气冷却至常温,称取进出物料的重量,统计烧失率为35.3%。然后用气漩涡流粉碎机进行粉碎,得到锰酸锂正极材料半成品,材料的粒度(dv50)为6.0μm,比表面积为3.90m2/g。复配烧结粉碎:将半成品再次投入到500l陶瓷球磨机中,向其中加入用10kg去离子水溶解含有5.47kg醋酸钴的溶液,经混合6.0h后取出物料重新装入陶瓷匣钵中,采用通气24m辊道窑。设置升温区温度为880℃,通入富氧空气条件下(氧含量体积比为70%,气体输入量600nm3/h)烧结8h,将物料隔离空气冷却至常温,称取进出物料的重量,统计烧失率为5.1%。然后用气漩涡流粉碎机进行粉碎,得到锰酸锂正极材料,材料的粒度(dv50)为4.5μm,比表面积为1.53m2/g,经核算结构式为:li1.08mn2co0.08w0.02o4.20。实施例5备料:选用500l犁刀式混料机,开启搅拌(主轴130rpm,侧刀速度1450rpm),在搅拌情况下加入91.3kg的电解二氧化锰(dv50:3μm),再称取26.91kg单水氢氧化锂粉体,以及0.5kg纳米氢氧化亚钴粉体加入到500l犁刀式混料机中,在搅拌情况下添加3.34kg纳米二氧化钛,以及33.7kg去离子水,搅拌2h后进一步降低速度(3-5rpm)搅拌4h出料形成具有一定成型度的膏状物料备用。预烧脱水:采用通气24m辊道窑。设置升温区温度为400℃,通入富氧空气(氧含量体积比计为45%,气体输入量400nm3/h)条件下将上述膏状物料装入到陶瓷匣钵中进行预烧结,烧结时间为13h,将物料隔离空气冷却至常温,称取进出物料的重量,统计烧失率为34.1%。然后用气漩涡流粉碎机进行粉碎,粉碎时控制空气的湿度≤2%,得到预烧结半成品1。复配烧结粉碎:将半成品再次投入到500l犁刀式混料机中,向其中加入10kg去离子水,以及1.0kg纳米氢氧化亚钴,经混合6.0h后取出物料重新装入陶瓷匣钵中,采用通气24m辊道窑。设置升温区温度为700℃,通入富氧空气条件下(氧含量体积比计为70%,气体输入量600nm3/h)烧结12h,将物料隔离空气冷却至常温,称取进出物料的重量,统计烧失率为0.6%。然后用气漩涡流粉碎机进行粉碎,得到具有最终制备物锰酸锂正极材料,材料的粒度(dv50)为3.5μm,比表面积为1.35m2/g,经核算结构式为:li1.12mn2co0.02ti0.048o4.14。实施例6备料:选用500ly型混合机,开启搅拌(35rpm),在搅拌情况下加入81.43kg的四氧化三锰(dv50:4μm),再称取23.29kg碳酸锂粉体加入到500ly型混合机中,在搅拌情况下按80wt%固含量添加27kg去离子水,以及1.07kg纳米氧化镁,1.0kg无定形纳米四氧化三钴,搅拌2h后进一步降低速度(3-5转/min)搅拌2h出料形成具有一定成型度的膏状物料备用。预烧脱水:采用通气24m辊道窑。设置升温区温度为500℃,通入富氧空气(氧含量体积比计为45%,气体输入量400nm3/h)条件下将上述膏状物料装入到陶瓷匣钵中进行预烧结,烧结时间为15h,将物料隔离空气冷却至常温,称取进出物料的重量,统计烧失率为25.2%。然后用气漩涡流粉碎机进行粉碎,粉碎时控制空气的湿度≤2%,得到半成品1。复配烧结粉碎:将半成品1再次投入到500ly型混合机中,向其中加入1.14kg无定形纳米四氧化三钴,以及10kg去离子水,经混合6.0h后取出物料重新装入陶瓷匣钵中,采用通气24m辊道窑。设置升温区温度为700℃,通入富氧空气条件下(氧含量体积比计为70%,气体输入量600nm3/h)烧结10h,将物料隔离空气冷却至常温,称取进出物料的重量,统计烧失率为1.0%。然后用气漩涡流粉碎机进行粉碎,得到具有最终制备物锰酸锂正极材料,材料的粒度(dv50)为4.3μm,比表面积为1.47m2/g,经核算结构式为li1.06mn2co0.024mg0.04o4.13。对比例1对比例1与本发明实施例1类似,区别仅在于,在备料阶段加钴源过量为0.25,烧制过程中材料出现了严重的板结,最终制备的材料的粒度(dv50)为11.0μm,比表面积为5.78m2/g。对比例2对比例2与本发明实施例2类似,区别仅在于,在整个制备方法中未加钴源,烧制过程中材料出现了严重的板结,最终制备的材料的粒度(dv50)9.0μm,比表面积为4.29m2/g。对比例3对比例3与本发明实施例3类似,区别仅在于,在制备过程中未加钴源,烧制过程中材料出现了严重的板结,烧制完成后混入按计量比加入的钴酸锂材料,最终制备的材料的粒度(dv50)为10.7μm,比表面积为1.62m2/g,评估备用。将上述实施例制备的正极材料进行下述表征。1.sem及球形度将上述实施例1,实施例2,对比例1,对比例2制备得到的正极材料粉体分别进行扫描电镜sem测试,得到图1-a(加速高压eht=15.00kv,工作距离wd=7.5mm,放大倍数mag=5.00kx,signala=inlens)、图1-b(加速高压eht=15.00kv,工作距离wd=7.5mm,放大倍数mag=5.00kx,signala=inlens)和图1-c(加速高压eht=15.00kv,工作距离wd=7.5mm,放大倍数mag=3.00kx,signala=inlens),图1-d(加速高压eht=15.00kv,工作距离wd=7.5mm,放大倍数mag=3.00kx,signala=inlens)的结果。同时采用马尔文公司产fpia3000型微粒分析仪对实施例1-6,对比例1-3粉体进行球形度测试,干法测试,ccd放大倍数:10倍,定时计数法,明光源检测。得到表3的结果。表3实施例及对比例球形度实施例球形度10.920.8730.9740.9650.9860.94对比例10.4对比例20.5对比例30.5由图1可见,采用本发明制备的锰酸锂样品球形度较好,颗粒表面比较光滑,球形度为0.87-0.98;对比例制备的样品呈非球形,且大小不一。对应检测的球形度(表3)也呈现相同的结果。2、游离锂及ph值取实施例1,实施例2,实施例3,对比例1,对比例2,对比例3各约200g,参考gb/t37202-2018镍锰酸锂物理性能游离锂的测定,采用滴定法及稀释法分别测得实施例及发明例的游离锂及ph值,得到表4所示结果。表4实施例游离锂含量及ph测试结果由表4可见,采用本发明制备的材料游离锂含量普遍比较低,总游离锂含量处于0.0177-0.0354wt%范围内,相应的ph在10以内,对应对比例的粉体的游离锂含量较高。游离锂含量高通常会吸收环境中的水分,导致溶剂n,n-甲基吡咯烷酮(nmp)对黏接剂聚偏氟乙烯(pvdf)的溶解能力下降,进而导致浆料黏度出现波动,在实际生产中需要尽力避免。3、粉体加工性能按实施例/对比例:nmp:pvdf=95:5:45的质量比(固含量70%)配制正极浆料,待浆料分散均匀后抽真空排除浆料中气体,按gbt2794-2013胶黏剂黏度的测定方法检测浆料的黏度。同时将浆料双面涂布(极片涂布平均重量为0.0260g/cm3)于铝箔(16μm)上,参考gbt26492.3-2011变形铝及铝合金铸锭及加工产品缺陷,采用辊压机辊压,并对辊压后的极片检测密度及极片柔软性,得到表5的实验结果。表5粉体制浆黏度及极片性能由表5可见,采用本发明制备的正极材料由于球形度较高,游离锂含量低,在后期加工过程中综合性能较好,浆料黏度低意味着可以适当减少溶剂的用量,降低有机物voc排放及回收,降低能耗,同时极片的压实密度尤其是极片压实密度得到一定程度的提升(可达3.4g/cm3),提升了锂电池的能量密度,且极片柔韧性较好,表现出优良的加工性能。4、全电池制备及循环性能将实施例2,实施例3及对比例2,对比例3制备得到的4个正极材料粉体作为正极活性物质按21700圆柱电池设计制备成容量为4.5-4.8ah左右动力电池,设计时以圆柱电池具有相同的容裕度为标准(即圆柱电池中有效物质占的体积与圆柱电池的总封闭有效容积百分比,通常为96%左右)。制作全电池主要用于考察高电压循环及安全性效果。其中所评估适用的品种为卷绕结构21700型钢壳电池,制作的电池直径为21mm,高度为70mm。正极极片制备通常由制备浆料,涂布及冷压,分切等工艺制成,极片中有效正极活性物质含量为97.5%,极片涂布平均重量为0.0260g/cm3,极片涂布宽度为62mm,极片活性物质总面积为937.4cm2,铝箔基材厚度为13μm,上述粉体加工性能中实施例2和实施3的粉体材料制备的极片压实密度以活性物质计为3.4g/cm3及3.3g/cm3,相应的对比例2和3粉体材料制备的极片压实密度以活性物质计为3.03g/cm3。负极片的制备方法通常经由制备浆料,涂布,冷压,分切等工序制备。采用人造石墨作为负极活性物质时,制备后的极片有效负极活性物质(人造石墨)含量为96.0%,极片涂布重量为0.0164g/cm2,极片涂布宽度为63.5mm,极片活性物质总面积为1009.65cm2,铜箔基材厚度为9μm,负极片压实密度以活性物质计为1.65g/cm3。将焊接有铝极耳的正极片,隔离膜(为经纳米氧化铝处理的厚度为16μm的pp/pe/pp复合隔离膜),焊接有镍极耳的负极片等按顺序卷绕制备成圆柱裸电芯,并将极耳套上绝缘环后入壳,采用激光焊接将镍极耳焊接在筒底部,然后经卷曲制备成具有凹槽的裸电芯,经干燥后冷却注液,并在将极耳依次焊接上cid,ptc及vent等保护构件,封装静置后在lip-10ahb06型高温化成机化成(化成电压0~4.2v,0.1c充电,0.2c放电,温度45℃±2℃),进行容量测试(测试电压3.0~4.2v,0.2c,0.5c),挑选质量合格的电芯用于后续性能评估。在制备工艺及条件相同的条件下,采用实施例3制备的锂电池的容量达到了3.6ah,对比例3制备的锂电池由于极片压实密度低,导致最终制备的锂电池容量为3.1ah,对比例3的容量较实施例容量低13.8%,可见采用本发明的方法制备的锰酸锂材料由于颗粒形貌较好,可以获得更高的压实密度,在其他电化学性能较好的情况下,可以有效提升锂离子电池的密度,有利于锰酸锂材料的推广应用。通常锰酸锂材料在高温下由于焦-汤效应导致锰的溶出,引起正极侧的结构崩塌,以及负极片侧锰的积聚,最终导致锰酸锂电池容量急速衰减。将实施例3,对比例3制备的锂电池放入55℃烘箱中,电极接入到在lip-10ahb06型高温化成机上进行1c/1c,3.0-4.2v循环检测,得到图2的高温循环结果。由图2可见,本发明例制备的锂离子电池循环性能优异,经100周循环容量保持率在96%以上,其中实施例1的容量保持率在120周循环大于98%,超过了常规锰酸锂材料制备的锂电池的检测结果。对比例2及对比例3制备的锂离子电池在循环过程中容量保持率逐步快速下降,表明未经处理的材料性能上尚有不足,且上述性能的提高不能仅依靠简单的混配就能达到相应的效果,相关的协同效应并不明显。以上通过实施例描述了本发明的具体实施方式,本领域技术人员应理解的是,上文实施例仅出于举例的目的,不应认为以此限定本发明之保护范围,本领域技术人员在不脱离本发明精神的前提下可以对其进行修改、变化或替换,但是,依照本发明所作的各种等同变化,仍属于本发明所涵盖的范围。综上所述,本发明所述锰酸锂正极材料通过加入钴参与合成改变了锰酸锂材料的形貌,最终制备出颗粒圆润的粉体,提高了极片的压实密度,进而提高了锰酸锂电池的能量密度,有利于扩大锰酸锂电池的应用场景,本发明所述制备方法经济可行,操作简单,效果明显,具有较好的应用前景。当前第1页12